汽车动力传动系统参数优化匹配方法.
新能源车辆动力系统的建模、仿真及优化算法

新能源车辆动力系统的建模、仿真及优化算法新能源车辆动力系统建模、仿真及优化算法是新能源汽车领域的关键问题之一。
该问题主要涉及到电池、电机、控制器等多个方面,需要对各个部件进行系统建模与分析,并提出相应的优化算法,以提高新能源车的整体性能。
建模方面,根据新能源车辆的实际情况和工作原理,可采用不同的建模方法,如基于物理原理的建模、基于统计学模型的建模、基于神经网络的建模等。
其中,基于物理原理的建模是一种较为常用的方法,能够准确地描述电池、电机、传动系统等部件的物理特性,并利用物理公式对其进行计算模拟。
仿真方面,通过对建立的模型进行仿真,可以得到部件的工作性能、功率输出、能量转换效率等参数,并得到整车的动力性能、能耗性能等指标,从而为新能源车辆的设计和优化提供有效的依据。
优化算法方面,目前广泛应用的算法包括PID控制算法、模型预测控制算法、基于遗传算法的优化算法等。
其中,基于遗传算法的优化算法是一种较为有效的方法,能够对多个参数进行优化,并考虑到不同变量之间的相互影响。
综上所述,新能源车辆动力系统建模、仿真及优化算法是新能源汽车领域中的重要问题,其研究将为新能源车的设计和优化提供有效的理论依据,同时也有助于推动新能源汽车产业的发展。
一、新能源车背景概述(一)新能源车的定义新能源车是指以新型能源为动力的汽车,它采用的能源比传统燃油车更加环保、经济、节能,包括电动汽车、混合动力汽车、燃料电池汽车等。
(二)新能源车的发展历程新能源汽车的概念和技术在上世纪就已经开始研究,但直到21世纪,随着环境污染和能源危机的凸显,新能源汽车才开始大力推广。
国内外政府涌现出一系列鼓励新能源汽车发展的政策。
中国政府发布了一系列《新能源汽车产业发展规划》,并出台多项补贴政策,促进新能源汽车市场增长。
(三)新能源车的发展现状随着新能源汽车技术的日益成熟,越来越多的新能源车型开始进入市场。
截至2021年,我国新能源汽车保有量已超过500万辆,市场规模不断扩大。
汽车动力传动系统匹配研究

圈 1
发 动机 外 特性
1 12 动 办 洼 目标 函 数 ..
1 优化 目标 函数 模 型 的 建立
11 动力性 目标 函数建 立 . 11 1 发 动机数 学模 型建 立 ..
相对 其 他 评价 指 标 而 言 , 车原 地起 步 加速 时 汽 间能反 映汽 车动力 性 全 貌 . 因此本 文选 用 汽 车原 地 起 步加 速时 间作 为汽 车动力性 目标 函数 . 由汽车行 驶方 程 可得 :
≤ 0. 9
收 稿 日期 :04I.9 修 订 日期 :050 -4 20 -11; 2O.20
【( _ !』
一G + (×
)。 】 一
() 3
作者简 介 : 文孝霞(97)女 , 17. , 贵州遵义人 , 硕士 , 助教 , 从事车辆设计方 法与理论 研究 .
维普资讯
Q1=
×, + —
式 中 ,p t—— 发动 机最 大功 率对应 转速 n 决 定 的最 , 高车 速(n ) k h . 3 直接 档 动力性 要 求 : )
\ ( 一1 / ≥ o m ,… G Da 2d c1 /声 | '5, o a I l x
.
因 : 阻= × F
A t
o = T + 一 o
,
型 —
一
×( 一 )
() 1 () 2 厶,
×
am
G×
一 0 37× 7
:
.
r
式 中 , —— 发 动机 有 效 扭 矩 ( I)Me N. ; 一— — 发 n 动机 最大 有效扭 矩 ( m) — — 发 动 机最 大 功 率 N. ;
性、 经济性均得到一定 的提高 . 关 键 词: 汽车; 动力 ; 传动 系; 匹配 文献标识码 : A 文章编号 :0 1 1X{060-18 4 10. 6 20 )1 3 - 7 0 0 中图分 类号 : 443 U 6 .2
基于CRUISE的某轻型载货汽车动力性优化匹配设计

摘
要
汽车 动 力性 能在 整 车性 能 中 , 占有 非 常 重要 的位 置 , 动 力链 匹配的 优 劣直接
决定 了整 车的动 力性 能 。本 文基 于 C RUI S E软件 , 通过 对 某轻 型载货 汽车 动 力链
进 行 匹配 分析 , 优 化 了动 力链 匹配 , 提 高 了整 车动 力性 能。
0 - 1 0 0 k m / h起 步 加 速 时间 ( 5 6 . 7
S )
5 6 . 2
5 8 . 6
6 0 - 3
5 7 . 9
主 减速 比
5 . 3 7 5
轮 胎规 格
7 . o 0 — 1 6
6 0 — 1 0 0 k m/ h 最高 档 加速 时 间 ( 3 6 . 7
轻 型汽 车技 术
2 0 1 3 ( 9) 总2 8 9
表3 某车型动力性试验结果
车 型代 号 最 高 车速 Y 5
1 08
1 7
1 0 9
1 8
I 】 0
2 4
1 l 0
均值
1 09
整备质量 ( k g )
总质 量 ( k g )
2 5 6 0
对整车的动力性进行计算分析。
3 整车主要技术参数
目标 车型是 某厂 家全新 开发 的新 一代 轻 型载
货汽车产品中的一款 6 t 车型 , 其主要技术参数及
8 技 术纵横
表 1 整 车主 要 技 术参 数
整 车外 形 尺 寸 ( 长 ×宽 X高 )( m m) 5 9 9 5 X2 0 3 0X 2 3 3 0
轻型 汽 车技 术
汽车传动系选型匹配与参数优化设计软件研制
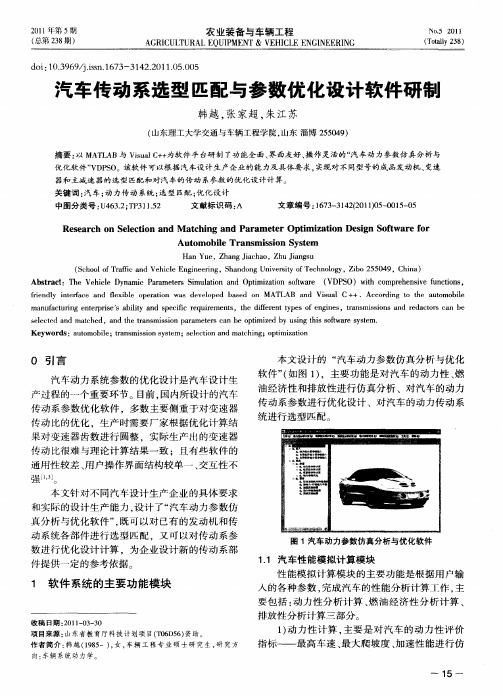
d i 1 .9 9 jin 1 7 —3 4 .0 10 .0 o : 03 6 / .s .6 3 1 22 1 .50 5 s
汽 车传 动 系选 型 匹配 与参 数 优 化 设 计 软件 研 制
韩 越 , 家 超 , 江 苏 张 朱
( 东 理 工 大 学 交 通 与 车辆 工 程 学 院 , 东 淄 博 2 5 4 ) 山 山 5 0 9 摘 要 : MA L 以 T AB与 Vsa c + i l + 为软 件 平 台研 制 了功 能全 面 、 面友 好 、 作 灵 活 的 “ 车 动 力 参数 仿 真 分析 与 u 界 操 汽 优 化软 件 ” D S V P O。该软 件 可 以根 据 汽 车设 计 生产 企 业 的能 力及 具体 要 求 , 对 不 同型号 的 成 品发 动 机 、 实现 变速 器和 主减 速 器 的选 型 匹配和 对 汽 车 的传 动 系参数 的 优 化设 计 计 算 。
产过程 的一 个重 要 环节 。目前 . 国内所 设计 的汽 车 传动 系参 数优 化 软件 ,多 数 主要 侧 重 于对 变速 器 传 动 比 的优化 ,生 产 时需 要 厂家 根据 优 化计 算 结 果对变 速 器齿 数进 行 圆整 .实 际生产 出的变 速 器 传 动 比很 难 与理论 计 算结 果 一致 :且 有 些软 件 的 通 用性 较差 、 户操 作 界 面结 构较 单 一 、 用 交互 性 不
Abtat h eil D n mc P r t sSm l i n pi ztn sf ae ( D S src:T eV h e y a i a me r i ua o ad O t ai ot r V P O)wt o rh ni u ci s c a e tn mi o w i cmpe es efnt n , h v o
新能源汽车动力系统优化设计与性能分析

新能源汽车动力系统优化设计与性能分析随着环境保护意识的增强和能源危机的威胁,新能源汽车成为了当前汽车行业的研发热点。
而新能源汽车的核心就是动力系统的设计与性能分析。
本文将围绕新能源汽车动力系统的优化设计和性能分析展开讨论,旨在为读者提供一些有关新能源汽车动力系统的信息。
一、新能源汽车动力系统的优化设计1.1 动力系统结构设计新能源汽车的动力系统一般由电池组、电机和控制器组成,并通过变速器将动力传递到车轮。
在设计动力系统结构时,需要考虑电池容量、电机功率和变速器的匹配关系,以及整个系统的重量分布、空间利用率等因素。
1.2 动力系统参数优化为了提高新能源汽车的性能和续航里程,动力系统的参数优化至关重要。
例如,电池的能量密度和功率密度、电机的效率和输出扭矩等都是需要优化的参数。
通过合理选择和调整这些参数,可以提高新能源汽车的动力性能和节能性能。
1.3 系统能量管理策略新能源汽车的能量管理策略是指如何合理地分配和利用电池的能量,以实现对电机的供能控制。
常见的能量管理策略包括最大能量采集控制策略、最大效率控制策略和最大续航里程控制策略等。
根据车辆使用场景和驾驶需求,可以选择合适的能量管理策略以优化动力系统的性能。
二、新能源汽车动力系统性能分析2.1 能量效率分析新能源汽车的能量效率是指在行驶过程中将电池储存的能量转化为车辆动力输出的效率。
通过对动力系统的能量转换过程进行分析,可以计算出能量转化的损失和效率,进而评估系统的能源利用效率。
2.2 动力性能分析新能源汽车的动力性能包括加速性能和最高速度等指标。
通过对动力系统的输出功率、扭矩和转速等参数进行分析,可以评估新能源汽车在不同工况下的动力性能表现。
2.3 续航里程分析续航里程是评估新能源汽车电池性能的重要指标。
通过对电池组的能量密度、电机的能量消耗率以及车辆质量等因素进行分析,可以预测新能源汽车在不同驾驶工况下的续航里程。
综上所述,新能源汽车动力系统的优化设计和性能分析是实现新能源汽车高效、可靠运行的重要环节。
不确定汽车动力传动系统低频NVH性能分析与优化

不确定汽车动力传动系统低频NVH性能分析与优化动力传动系统是整车最重要的振动、噪声源之一,其NVH(振动、噪声和声振粗糙度)性能主要包括扭振、颤振、轰鸣噪声、敲击、啸叫等内容。
其中,扭振、颤振、轰鸣噪声主要作用在低频范围内,这些低频性能指标对整车起步、全油门加速等工况下的NVH性能有着决定性的影响。
因此,分析和控制动力传动系统低频NVH性能,对于提高整车NVH水平具有非常重要的意义。
目前,动力传动系统低频NVH性能的开发主要基于确定性系统参数,并借助CAE(计算机辅助工程)技术进行求解。
然而,在工程实际问题中,由于制造、装配和测量误差的影响,激励和边界条件的变化,外部环境的不可预测等因素的影响,动力传动系统的不确定性无法避免。
这些不确定性互相影响和耦合,导致动力传动系统的实际性能相对于设计性能出现较大偏差,可能造成产品性能一致性差、仿真模型与测试结果对标困难、优化方案实际效果不明显等一系列问题。
针对目前动力传动系统低频NVH开发中存在的问题,本文在这一过程中引入了不确定理论和算法,对不确定条件下动力传动系统扭振、颤振、轰鸣噪声性能的开发和扭转动力吸振器的设计进行了研究。
建立了各项性能的仿真分析模型,提出了各项性能的评价指标;针对各项性能指标的特点,采用不同的不确定性模型和数值计算方法,以预测由不确定因素引起的动力传动系统低频NVH性能波动;建立了动力传动系统的不确定优化模型,以实现其低频NVH性能的优化设计。
论文完成的工作主要包括:(1)建立了新的动力传动系统-后桥耦合扭转振动模型(DRCTVM),该模型将主减速器输入轴和差速器搭载在后桥桥壳上,考虑了扭转振动中动力传动系统与后桥之间的耦合关系,试验结果显示,相对于没有考虑后桥耦合关系的传统模型,该模型可以更准确的模拟动力传动系统的扭转振动性能。
提出了不确定动力传动系统的扭振分析和优化方法,该方法以扭转模态频率和扭振响应峰值的期望和标准差作为输出响应,采用截断概率模型描述模型参数的不确定性,同时考虑了参数的概率分布特性和边界特性,数值算例结果显示,该方法可以大幅度降低动力传动系统扭振响应的均值和标准差,收窄扭振响应的上、下界范围,有效的提升动力传动系统扭振性能的稳健性。
汽车传动系参数与使用工况匹配设计

汽 车传动 系统 与发动机合理 匹配 的程度决定 拟合公式的系数 。 了汽车 的动力性 、燃油经济性和排放特性 的好坏 表
嘲
。
1 拟合公式 系数
而汽车传 动系参数 的优化设计 是在 汽车总质
量 、载荷分配 、空气 阻力和滚动阻力等参数确定 的情况 下 ,合 理的设计 和选择传 动系参数来提 高
动 进取 型 。车轮 半径 为 :
1 6 X 25 . 4=4 06 . 4mm
O s , :
兰 坐 !L / l o ? : 1 1 4 2 L 1 0 0 /  ̄ v n
.
= ( 4 0 6 . 4 + 1 2 3 X 2 ) = 3 2 6 . 2 m m 取车轮半径 r r 为0 . 3 3 m .
3 . 8 6 × 6 , 3 6
『 j :4 . 1 4 , b ” / h / I }
1 汽 车模 型的数字化
1 . 1 汽 车参数 的数 字化
发 动 机 发 出 的 功 率 为 : : 1 ( G .  ̄ l a l + 磊 ) 将
相关数据代入上式 ,解得 , = 0 . 2 8 又因为
‘ 1 . O 2 × 4 . 1 4 x 7 . 0 6
表2 I 挡各车速下的等速百公 里油耗计算结果
1 . 2 发 动机 万有 特性 的数 字化
下面计算该车各挡等速百公里 油耗 。表 1 为
收谢 1 3期 :2 0 1 3 — 3 — 2 5 作者简介 :魏泽川 ( 1 9 5 4 一) ,男 ,工程师 。
匹配后 汽 车动力 性 、燃 料经 济性 和排 放特性 。
对传动系 的参数进行优化设计 ,首要任务是 确定 与传动系匹配的评价指标 。 目前 ,多数学者 采用 动力性指标 、经济性指标 和多工况循环试验
动力总成匹配试验测试方法

动力总成匹配试验测试方法一、引言动力总成是指由发动机、传动系统和相关控制系统组成的汽车动力装置。
为了确保动力总成的性能和可靠性,需要进行匹配试验测试。
本文将介绍动力总成匹配试验测试的方法和步骤。
二、试验前准备1. 确定试验目的:根据动力总成的设计要求和使用条件,确定试验目的和要求,包括动力输出、燃油消耗、排放等方面的指标。
2. 确定试验条件:根据动力总成的设计参数和使用条件,确定试验条件,包括环境温度、湿度、海拔高度等。
3. 准备试验设备:包括发动机试验台、传动系统试验台、测量仪器等。
三、试验步骤1. 发动机试验:首先进行发动机试验,包括动力输出、燃油消耗、排放等方面的测试。
通过改变发动机工况和负荷,测试发动机在不同工况下的性能指标。
2. 传动系统试验:然后进行传动系统试验,包括传动效率、换挡平顺性、噪声振动等方面的测试。
通过模拟实际驾驶情况,测试传动系统在不同工况下的性能指标。
3. 整车试验:最后进行整车试验,将发动机和传动系统安装到实际车辆上,测试整车的性能和可靠性。
包括加速性能、制动性能、悬挂系统等方面的测试。
四、试验参数和指标1. 动力输出:包括最大功率、最大扭矩等指标,用于评估动力总成的动力性能。
2. 燃油消耗:包括燃油经济性和排放指标,用于评估动力总成的燃油效率和环保性能。
3. 传动效率:用于评估传动系统的能量传输效率,包括传动损失和能量转换效率等指标。
4. 换挡平顺性:评估传动系统换挡的舒适性和平顺性,包括换挡时间、换挡冲击等指标。
5. 噪声振动:评估传动系统和整车的噪声和振动水平,包括噪声强度、振动幅值等指标。
6. 加速性能:评估整车的加速性能,包括0-100km/h加速时间等指标。
7. 制动性能:评估整车的制动性能,包括制动距离、制动稳定性等指标。
8. 悬挂系统:评估整车的悬挂系统性能,包括悬挂刚度、减震效果等指标。
五、试验数据处理与分析1. 试验数据采集:通过测量仪器和传感器,采集试验过程中的各项数据,包括转速、扭矩、温度、压力等。
- 1、下载文档前请自行甄别文档内容的完整性,平台不提供额外的编辑、内容补充、找答案等附加服务。
- 2、"仅部分预览"的文档,不可在线预览部分如存在完整性等问题,可反馈申请退款(可完整预览的文档不适用该条件!)。
- 3、如文档侵犯您的权益,请联系客服反馈,我们会尽快为您处理(人工客服工作时间:9:00-18:30)。
机械传动汽车动力传动系统参数的优化通常包括发动机性能指标的优选,机械变速器传动比的优化和驱动桥速比的优化,以下分别阐述。 7.1汽车发动机性能指标的优选方法 在汽车设计中,发动机的初选通常有两种方法: 一种是从保持预期的最高车速初步选择发动机应有功率来选择的,发动机功率应大体上等于且不小于以最高车速行驶时行驶阻力功率之和;一种是根据现有的汽车统计数据初步估计汽车比功率来确定发动机应有的功率。 在初步选定发动机功率之后,还需要进一步分析计算汽车动力性和燃料经济性,最终确定发动机性能指标(如发动机最大转矩,最大转矩点转速等)。 通常在给定汽车底盘参数、整车性能要求(如最大爬坡度imax,最高车速Vmax,正常行驶车速下百公里油耗Q,原地起步加速时间t等),以及车辆经常运行工况条件下,就可以选择发动机的最大转矩Temax,及其转矩nM,最大功率Pemax及其转速nP,发动机最低油耗率gemin和发动机排量Vh。 在优选发动机时常常遇到两种情况:一种情况是有几个类型的发动机可供选择,在整车底盘参数和车辆经常行驶工况条件确定时,这属于车辆动力传动系合理匹配问题,可用汽车动力传动系统最优匹配评价指标来处理。 第二种情况是根据整车性能要求和汽车经常行驶工况条件来对发动机性能提出要求,作为发动机选型或设计的依据,而这时发动机性能是未知的。 对于计划研制或未知性能特性指标的发动机性能可看作为发动机设计参数和运行参数的函数,此时,外特性和单位小时燃油消耗率可利用表示发动机的简化模型。 优选汽车发动机参数的方法: (1) 目标函数F(x) 目标函数为汽车行驶的能量效率最高。 (2) 设计变量X X [Tem,Pemax,np,nM,Vh] (3) 约束条件 1) 发动机性能指标的要求 发动机转矩适应性要求: 1.1≤Tem/TP≤1.3 转矩适应性系数也可参考同级发动机试验值选取。 发动机转速适应性要求: 1.4≤np/nM≤2.0 如果nM取值过高,使np/nM<1.4,则可能使直接档稳定车速偏高,汽车低速行驶稳定性变差,换档次数增多。 2) 汽车动力性要求 最大爬坡度要求: TeM≥Grk(f⋅cosαmax+sinαmax) ig1i0ηt 最高车速要求: Vamax/Vp=1.0~1.1,即 Vamaxi0i高档1.0≤≤1.1 0.377nprk 直接档动力性要求: Temi0ηtCDAVa2-≥Domax rkG21.15G 汽车加速性能的要求: 原地起步连续换档加速时间不得大于要求值t0 t≤t0 3) 汽车燃料经济性要求: 直接档在常用车速下行驶的百公里油耗不得超过其限制值Q0 Qs≤Q0 发动机排量的要求: P1式中,Ph、P1——分别为发动机升功率的统计上、下限值,kW/L。 根据上述建立的优化模型,即可优选出最优发动机参数,并选择发动机型号。 发动机简化模型 发动机性能特性可看作是发动机性能指标和运行参数的函数,此时,外特性可表示为: Te=Tm-Tm-Tp (np-nm)2⋅(nm-ne)2 式中,Tm——发动机最大有效转矩,N·m; Tp——发动机最大功率对应的转矩,N·m; nm——发动机最大有效转矩对应的转速,r/min np——发动机最大功率对应的转速,r/min。 发动机单位时间的油耗量可以表示为: Gt=ne⋅(Gox+ro⋅Te)⋅Vh 式中,Gt——发动机每分钟消耗的燃油量,g/min; Gox——发动机怠速时单位排量每转燃油消耗量,g/(r·L); N·m ·r·L); ro——发动机单位排量单位转矩每转燃油消耗量提高系数g/( Vh——发动机的排量,L。 根据研究,汽油机和柴油机的的Gox和ro值范围如下表所示。 汽油机和柴油机的的Gox和ro值
7.2汽车变速器速比的优化方法 汽车传动系参数优化是以汽车动力性与燃料经济性模拟计算为基础,以汽车 动力性要求为约束条件,多工况燃料经济性为目标函数进行优化。 汽车变速器速比优化最终目的是使汽车在满足动力性要求前提下,在常用行驶工况下燃料经济性最佳。 设计变量取变速器各档速比,表示为x(i),i=1,kn(kn为前进档位数)。 目标函数一般为汽车多工况循环模式的燃油消耗量Qs。 约束条件主要包括:汽车的动力性要求和变速器各档速比间隔的要求。 在选择传动系参数时,应考虑汽车具有足够的动力性能,即应有足够的直接档动力因数Domax和I档最大动力因数Dimax,同时需校核I档最大驱动力时附着条 件。 Tem⋅I0⋅ηtCD⋅A0.377⋅nem⋅rk2-⨯()rk21.15I0=G 式中, Tem——发动机最大有D0max 效转矩,N.m ηt——传动系效率 rk——车轮滚动半径,m CD——汽车空气阻力系数 A——汽车前迎风面积,m2 nem——发动机最大转矩点所对应的转速,rpm; G——汽车总重力,N。 则直接档最大动力因数的约束条件应为 Dol式中,Dol,Doh——分别为不同车型汽车直接档最大动力因数要求的上下限。 I档最大动力因数反映了汽车最大爬坡能力,其计算式如下: Tem⋅I0⋅I1⋅ηtCD⋅A⎛0.377⋅nem⋅rk-⨯ rk21.15 I0⋅I1⎝=g⋅M⎫⎪⎪⎭2DImax 同上,I档最大动力因数的约束条件为 D1L式中 D1L,D1h ——分别为不同车型汽车I档最大动力因数要求的上下限值。 在确定I档动力因数后还应该按以下条件校核附着条件,即最大牵引力必须 小于或等于汽车在地面上的附着力: Tem⋅I0⋅I1⋅ηt≤Zϕ⋅ϕ Rk 式中 ϕ ——道路附着系数; Zϕ——驱动轮上的法向反作用力,N。 同样也可以汽车最大爬坡度要求代替动力因数作为约束条件。 变速器相邻档位的速比比值影响着变速器的使用性能,比值过大会造成换档 困难。根据统计,一般在1.4~1.8之间。考虑到换档过程,外界道路阻力总是 造成车速下降,换档时车速越高,换档过程的速度下降就越多,所以随着档位的 提高,相邻两档的速比比值应逐渐降低。据此对相邻档位的速比比值要求如下: IlX(i+1)X(i)< X(i+2)X(i+1) 式中,Il,Ih——分别为相邻速比间隔的下限和上限值。 此外,汽车最高车速,汽车原地起步连续换档加速时间限制也作为约束条件。 以上构成了汽车变速器速比的一般优化模型。 7.3汽车主传动比优化方法 汽车主传动比对汽车动力性燃料经济性影响很大。主减速比增大,可以增加汽车 的后备功率,提高汽车加速性能,但也会使汽车燃料经济性下降。因此,主传动 比的选择,应保证汽车的动力够用,又有最佳的燃料经济性。 对于某一特定的车辆,当汽车总重、重量分配和发动机等已确定后,如何合 理的选择传动系参数,按传统的做法,需要进行大量的汽车动力性和燃料经济性 计算和实验工作,而且由于各种条件限制,往往不能获得最理想的结果。 汽车主传动比的优化最终目的是使汽车在满足动力性要求下,在常用行驶工 况燃料经济性最佳。 在选择传动系参数要求时,应考虑汽车具有足够的动力性能,即应有足够的直接档动力因数D0max 。直接档动力因数表示汽车在正常情况下行驶所具有的上 坡和加速能力。 TeMioηtCDA0.377neMrk-⨯()221.15I0 D0max=rk G 汽车最高设计车速,原地起步连续换档加速时间和最大爬坡度要求也作为约束条件。 7.4汽车传动系统参数的区间优化方法 如前所述,传动系参数中齿轮齿数和模数为离散变量,而采用以上优化方法获得的速比值是一个确定的最优值,不一定满足生产厂家的实际生产需要,存在着变速器齿轮配齿的问题。 为此我们提出了汽车传动系参数的区间优化模型。在这一模型里,不追求变量的确定优化值,只是在保证一定的优化效果的前提下,求设计变量的最大可行区间,这样就可以扩大传动系参数的选择范围,并可以解决变速器齿轮配齿问题。 用区间数表示需要共享的实际变量,则确定汽车传动系参数最大可行区间的问题可以表述为扩大设计变量区间数的宽度问题。令Xi为共享设计变量,则求最大共享区间问题的数学模型,即是求最大可行区间问题的数学模型,即是求最大可行区间宽度的优化问题。在一定的约束条件下,其数学模型为: maxω=∑αiωi(Xi) i=1l 满足约束条件 F(X1,X2, ,Xl)≤c 2, ,l Xi⊆Xi'i=1, 其中,F( )为约束区间函数,c为约束区间函数的限制值,αi为权系数,l为区间变量总数,ωi(Xi)为第i个区间数的区间宽度,Xi'可行区间变量Xi的约束区间数,Xi'=[Xi',Xi']。 上述模型描述的是区间扩张的逆问题,及规定函数的值域区间求定义域区间 的问题,在约束函数为凸函数时,有确定的解。 求解上述模型得到的可行区间宽度有时较窄,为了改善效果,引入“条件预优概念及方法”,也就是把影响实值函数F(x1,x2, ,xl,xl+1, ,xn)的变量及参数分为两类,其中x1,x2, ,xl为一类,叫做关键变量,我们关心这些变量的可行变化区间[Xi,Xi],而不关心它们取什么确定值;此外,我们把影响目标函数值的其他变量及参数在一定的范围内变动,这些扩大的变量称作为条件变量。 我们采用对条件变量优选的方法,即求xl+1,xl+2, ,xn使 minF(x1,x2, ,xl,xl+1, ,xn) 求解模型时,对应于每一组z=[x1,x2, ,xl]T时,有一组对应的最优变量 *Ty*=[xl*+1,xl*+2, ,xn],我们把y*称为预优条件变量,把这一类运算成为“条件 预优运算”。通过条件预优运算,能明显地提高与改善优化效果,即 *F(x1,x2, ,xl,xl*+1, ,xn)≤F(x1,x2, ,xl,xl+1, ,xn) 若我们把上述预优概念引入模型 ,那末就可以扩大关键变量允许选取的范围,改善最大可行区间的求解效果。也就是说,在满足性能要求的前提下,扩大关键变量的区域。这样可导出改进的模型如下: 求z=[x1,x2, ,xl]T使 maxω=∑αiωi(Xi) i=1l *T求y*=[xl*+1,xl*+2, ,xn]使 minF(x1,x2, ,xl,xl+1, ,xn)≤c 2, ,l xi⊆Xi'i=1, ,n Xj⊆X'jj=l+1,l+2, 其中X'j为条件变量的约束区间数,X'j=[X'j,X'j];n为变量总数(包括关键变量和条件变量)。 在具体计算传动系参数最大可行区间问题时,我们以多工况模式的燃油百公 里油耗Qs为目标区间函数,以满足汽车动力性要求为约束条件。为了简化计算,以传统的按等比级数q来分配变速器各档速比,最高档为直接档;同时取驱动桥速比I0为另一约束区间数,故约束区间函数可表示为QS(q,I0)≤c。