3_4讲陶瓷基复合材料的界面设计说明
合集下载
陶瓷基复合材料(CMC

特点: 低密度,2.0-2.8g/cm3 高弹性模量(80-140GPa)和弯曲强度
(70-350MPa)
7
第三节 陶瓷粉末的烧结
粉末状物料在压制成型后,含有大量气孔,颗粒 之间接触面积较小,强度也比较低。经过高温作 用后,坯体中颗粒相互烧结,界面逐渐扩大成为 晶界,最后数个晶粒结合在一起,产生再结晶与 聚集再结晶,使晶粒长大。气孔体积缩小,大部 分甚至全部从体坯中排出,体收缩而致密,强度 增加,成坚固整体。上述整个过程叫烧结过程。
10
烧结作用力分析
表面张力产生的作用于ABCD表面上切线方向的力, 可由表面张力定义求出
11
由表可以看出,曲面压力随颗粒半径之降低而 增加,随曲面圆内角θ之减小而降低,亦即随 烧结之进行而降低。所以颗粒越细,曲面压力 越大,颈部成长越快。颈部长大表面积减小, 表面能也降低。
12
三、烧结机理
(一)颗粒的粘附作用
(7)氮化硅的电绝缘性也很好
5
三、碳化硅陶瓷
由反应烧结法(α-SiC+C粉 烧结)和 热压烧结(SiC+促进剂)法制备 特点: 较高的高温强度 较高的热导率 较好的热稳定性、耐磨性、耐腐蚀性和 抗蠕变性
6
四、玻璃陶瓷
含有大量微晶体的玻璃称为微晶玻璃或 玻璃陶瓷。常用的玻璃陶瓷有锂铝硅 (Al2LOi23O-S-iAOl22O,3M-SAiOS)2两,L个AS体)系和。镁铝硅(MgO-
39
模量
40
断裂韧性
没有增强时,断裂韧性随温度升高而降低,有晶须 增强后,因纤维拔出,在高温随温度升高而增大 41
2.蠕变
在高温或高应力的作用下,玻璃发生粘性流动, 应变急剧增大 42
3.热冲击性(热震性)
(70-350MPa)
7
第三节 陶瓷粉末的烧结
粉末状物料在压制成型后,含有大量气孔,颗粒 之间接触面积较小,强度也比较低。经过高温作 用后,坯体中颗粒相互烧结,界面逐渐扩大成为 晶界,最后数个晶粒结合在一起,产生再结晶与 聚集再结晶,使晶粒长大。气孔体积缩小,大部 分甚至全部从体坯中排出,体收缩而致密,强度 增加,成坚固整体。上述整个过程叫烧结过程。
10
烧结作用力分析
表面张力产生的作用于ABCD表面上切线方向的力, 可由表面张力定义求出
11
由表可以看出,曲面压力随颗粒半径之降低而 增加,随曲面圆内角θ之减小而降低,亦即随 烧结之进行而降低。所以颗粒越细,曲面压力 越大,颈部成长越快。颈部长大表面积减小, 表面能也降低。
12
三、烧结机理
(一)颗粒的粘附作用
(7)氮化硅的电绝缘性也很好
5
三、碳化硅陶瓷
由反应烧结法(α-SiC+C粉 烧结)和 热压烧结(SiC+促进剂)法制备 特点: 较高的高温强度 较高的热导率 较好的热稳定性、耐磨性、耐腐蚀性和 抗蠕变性
6
四、玻璃陶瓷
含有大量微晶体的玻璃称为微晶玻璃或 玻璃陶瓷。常用的玻璃陶瓷有锂铝硅 (Al2LOi23O-S-iAOl22O,3M-SAiOS)2两,L个AS体)系和。镁铝硅(MgO-
39
模量
40
断裂韧性
没有增强时,断裂韧性随温度升高而降低,有晶须 增强后,因纤维拔出,在高温随温度升高而增大 41
2.蠕变
在高温或高应力的作用下,玻璃发生粘性流动, 应变急剧增大 42
3.热冲击性(热震性)
陶瓷基复合材料

Ceramic-matrix
注意事项 : (1)料浆应能与纤维表面保持良好润湿。料浆中包括:陶瓷基体粉末、 载液(通常是蒸馏水)和有机粘接剂,有时还加入某些促进剂和基体润湿 剂。为使纤维表面均匀粘附料浆,要求陶瓷粉体粒径小于纤维直径,并 能悬浮于载液和粘接剂混合的溶液中。 (2)纤维应选用容易分散的、捻数低的丝束,保持其表面清洁无污染。 在操作过程中尽量避免纤维损伤,并注意排除气泡。 (3)热压烧结应按预定规律(即热压制度)升温和加压。在热压过程中, 将发生基体颗粒重新分布、烧结和在外压作用下的粘性流动等过程,最 终获得致密化的陶瓷基复合材料。很多陶瓷基复合材料体系在热压过程 中往往没有直接发生化学反应,主要通过系统表面能减少的驱动,使疏 松粉体熔结而致密化。 存在的问题: (1)纤维和陶瓷粉末不容易复合成型。 (2)烧结时由于基体收缩或热压烧结时无粘性流动,会使颗粒和纤维 之间的机械作用而损伤纤维。 (3)目前,直径小于0.1微米-1微米的粉末很难买到。并且,其中的夹 杂物不易排除。同时,细的粉末在制造复合材料过程中又不易分散。 (4)在热压时会损伤纤维结构。
Ceramic-matrix
注意事项:
(1)与高聚物先驱体转化法不同的是,溶胶—凝胶工艺的先驱体是在溶液浸 进纤维编织坯件后在原位合成的。 (2)采用溶胶—凝胶法制备复合材料可以先制备复合凝胶体,即将复合的各 相以原子或分子级进行均匀混合形成复合溶胶和凝胶化,得到高纯、超细、均 相、分子级或包裹式的复合陶瓷粉末,再经成型、烧结而形成复合材料的基体 或者通过控制溶剂的蒸发速度将复合的溶胶凝胶化后,直接烧结成陶瓷基复合 材料。 (3)如果第二相是粉末或纤维,则可浸在适当的溶液中,通过形核和成长, 使溶液形成溶胶,均匀包围粉末和纤维,经凝胶化处理和热解后即形成陶瓷基 复合材料的基体。 (4)溶胶—凝胶法制备陶瓷基复合材料的质量保证关键主要有:选择合适的 先驱体反应物,控制溶液的浓度和pH值、气氛、分散剂、选用胶溶剂、去除 团聚以及使各相处于良好的分散状态等。
第七章陶瓷基复合材料

• 陶瓷基复合材料的性能除于基体和增强材料的种类有关外, 也与增强材料的加入量有较大关系,特别是晶须材料,加 入太少时,增强效果小,加入太多时,由于晶须的顶立和 架桥左右,使得复合材料的致密化困难,导致复合材料的 强度降低。
• 7.1.4陶瓷基复合材料的界面强韧化机理 • 偏转、拔出、脱粘、桥联
• 7.2.1纤维增强陶瓷基复合材料的制备 1.泥浆浇铸法
• 在泥浆中把纤维分散,然后浇铸到石膏模具中一定时间后 脱模,修坯干燥后烧成。
• 工艺简单、生产成本低,产品性能不是很好。
2.热压烧结法 • 将纤维切短后,与基体粉末混合均匀,再用热压或无压烧
结的方法制得高性能的复合材料。 • 产品性能较好,难于制备形状复杂的产品,生产成本较高。
• 2.多向排列纤维复合材料
• 二维多向排列,复合材料在二维方向上性 能比较一致;
• 三维多向排列,复合材料在三维方向上性 能接近。
• 多向排列纤维复合材料的增韧机理与单向 排列相同。
• 7.1.3晶须和颗粒增强陶瓷基复合材料 • 晶须尺寸较小,宏观上与粉末相似,在制备复合材料时,
只需将晶须或颗粒增强材料与基体材料的粉末混合均匀, 然后进行热压或无压烧结,即可得到比较致密的陶瓷基复 合材料。
氮化物陶瓷(氮化硅、氮化铝、氮化硼等); 碳化物陶瓷(碳化硅、碳化钛、碳化硼等)。
• 2.增强材料
• 性状:长、短纤维、晶须、颗粒材料。
• 纤维材料:碳纤维、玻璃纤维、硼纤维等。
• 晶须材料:氧化铝、碳化硅、氮化硅、碳化硼、石墨等。
• 颗粒材料:等积形颗粒,一般直径为几微米左右,材质 以碳化硅、氮化硅为多,颗粒增强效果不如晶须或纤维, 但其加入比例可达到较大值,故对复合材料的性能的改 变也较大。
• 7.1.4陶瓷基复合材料的界面强韧化机理 • 偏转、拔出、脱粘、桥联
• 7.2.1纤维增强陶瓷基复合材料的制备 1.泥浆浇铸法
• 在泥浆中把纤维分散,然后浇铸到石膏模具中一定时间后 脱模,修坯干燥后烧成。
• 工艺简单、生产成本低,产品性能不是很好。
2.热压烧结法 • 将纤维切短后,与基体粉末混合均匀,再用热压或无压烧
结的方法制得高性能的复合材料。 • 产品性能较好,难于制备形状复杂的产品,生产成本较高。
• 2.多向排列纤维复合材料
• 二维多向排列,复合材料在二维方向上性 能比较一致;
• 三维多向排列,复合材料在三维方向上性 能接近。
• 多向排列纤维复合材料的增韧机理与单向 排列相同。
• 7.1.3晶须和颗粒增强陶瓷基复合材料 • 晶须尺寸较小,宏观上与粉末相似,在制备复合材料时,
只需将晶须或颗粒增强材料与基体材料的粉末混合均匀, 然后进行热压或无压烧结,即可得到比较致密的陶瓷基复 合材料。
氮化物陶瓷(氮化硅、氮化铝、氮化硼等); 碳化物陶瓷(碳化硅、碳化钛、碳化硼等)。
• 2.增强材料
• 性状:长、短纤维、晶须、颗粒材料。
• 纤维材料:碳纤维、玻璃纤维、硼纤维等。
• 晶须材料:氧化铝、碳化硅、氮化硅、碳化硼、石墨等。
• 颗粒材料:等积形颗粒,一般直径为几微米左右,材质 以碳化硅、氮化硅为多,颗粒增强效果不如晶须或纤维, 但其加入比例可达到较大值,故对复合材料的性能的改 变也较大。
2、3讲陶瓷基复合材料的强韧化机理课件

陶瓷的强韧化
• 脆性是陶瓷材料的致命弱点,其来源于高键能引起的缺陷敏感 性,陶瓷材料的强韧化本质上就是降低其对缺陷的敏感性。
陶瓷材料缺陷敏感性存在着显著的尺寸效应,即块体材料的尺 寸越大,缺陷数量越多。根据统计学原理,缺陷数量越多,缺 陷的概率尺寸越大。
陶瓷材料的强度和韧性具有“最弱连接”特征,即取决于缺陷 的最大尺寸而不是数量,实际上,陶瓷基复合材料的强韧化就 是利用了缺陷的尺寸效应。(掺杂改性)
2 韧化机理
• 径向微开裂容易导致微裂纹连通,对材料强度不利;
• 切向微开裂使颗粒与基体脱开,相当于形成一个颗粒尺寸大小 的孔洞,同样对材料强度不利。
• 所以在采用第二相颗粒补强增韧时,一般要求颗粒的直径小于 导致自发微开裂的临界颗粒直径dc。
√ 应力诱导微开裂增韧(dmin<d<dc)
• 当p>m,d<dc时,宏观裂纹的尖端由于外加应力的作用会出现 一个微开裂过程区,如图所示。
无限大基体中球形颗粒引 起的残余应力场
2) 韧化机理
• 当p>m 时,压力p>0,径向>0,切向t<0,即第二相颗粒 处于拉应力状态,而基体径向处于拉伸状态,切向处于压缩 状态,这时裂纹倾向绕过颗粒继续扩展,如图所示;
• 当p<m 时,压力p<0,径向<0,切向t >0,即第二相颗 粒处于压应力状态,而基体径向受压应力,切向受到拉应力 ,这时裂纹倾向于在颗粒处钉扎或穿过颗粒。
• Faber等证实了应力诱导微开裂增韧机理的存在。增加第二相颗 粒的体积含量和直径可以提高应力诱导微开裂的增韧效果,但 过分增加容易导致微裂纹的连通,对材料的强度也不利。
√ 残余应力增韧
• 当第二相颗粒的直径小于dmin时,在裂纹尖端不能诱发微开裂,但裂 纹尖端将与颗粒周围应力场相互作用,其裂纹扩展的微观过程应是 如图所示的裂纹偏转,这种由于裂纹与颗粒周围应力场相互作用所 导致的微裂纹偏转与裂纹直接和颗粒相互作用(不考虑颗粒周围的 应力场)所导致的裂纹偏转不同。
复合材料界面与设计

将纤维与基体压出,暴露出纤维与基体形貌,脱粘发生 在C层与反应层之间,可以看到碎片
图 高模量碳纤维复合材料 拉伸破坏断口侧壁SEM照片
图 高模量碳纤维复合材料 拉伸破坏的断口SEM图片 图中深色部分为纤维拔 出后留下的空洞
碳纤维水泥状态
玻璃纤维热塑性复合材料
复合材料界面SEM图
TEM是研究陶瓷基复合材料界面微观结构
玻纤单丝从PP基体中的拔出剪切强度测试
4、临界纤维长度试验法
将单丝纤维埋人基体制成哑铃状试样,拉伸使纤维断裂成一段
段的残片,测量残片长度,可得到残片的长度分布图,统计出 残片平均长度L,临界纤维长度Lc与平均长度L的关系为:
临界剪切强度为:
5、界面粘接能测试法
在试样中埋人纤维单丝,试样尺寸30mm×10mm×10mm, 试样中间开一直径1.5MM小孔,使小孔穿过纤维。对试 样施加压应力,由于纤维与基体压缩模量不同,界面 产生剪应力,载荷足够大时,纤维在小孔
复合材料界面分析表征 提 纲
界面形貌结构分析表征 增强材料表面化学表征 界面力学性能分析表征
一、界面形貌结构分析表征
界面结合强弱与与界面区域的微观结构密切相关; 复合材料的结构缺陷常常集中于界面区域; 制造与使用过程中,界面的结构前景都吸引人们
?界面结构的最重要的手段是temsemafm和拉曼光谱技术也为人们重视1纤维表面处理形态表征低温等离子处理热处理电晕和低温等离子处理植物纤维2纤维表面接枝聚合物形态碳纤维接枝聚苯乙烯碳纤维接枝3复合材料界面状态纤维拔出状态cc复合材料拉伸破坏断裂面脱粘没有导致表面和内壁任何损伤可以判定纤维与基体之间只有松散结合不存在确定厚度的界面层cc复合材料横断面semcc复合材料界面结构与先驱体种类和热处理形式有关以上显示纤维相同基体及处理不同界面状况不同26显示sicsic复合材料受压力破坏后显示复合材料几乎所有破坏形式27显示纤维拉出和断裂破坏界面结合弱碳化硅增强某种钛合金复合材料a纤维表面有一层碳b纤维表面未覆盖c反应层有明显区别
复合材料界面课件

汽车工业领域应用案例
碳纤维复合材料
在汽车工业领域,碳纤维复合材料被用于制 造高性能跑车的车身和车架。例如,兰博基 尼Aventador使用了碳纤维复合材料制造车 身,具有较高的强度和刚度,同时减轻了车 身重量,提高了车辆性能。
玻璃纤维复合材料
玻璃纤维复合材料在汽车工业中也被广泛应 用。例如,汽车保险杠、车门等部件使用了 玻璃纤维复合材料,具有较高的强度和刚度, 能够承受碰撞时的冲击合材料被用于制造桥梁、高速公路等基础设施的结构件。例如, 美国加州长滩大桥使用了碳纤维复合材料制造桥梁结构件,具有较高的强度和刚度,能
够承受车辆和自然灾害的荷载。
玻璃纤维复合材料
玻璃纤维复合材料在建筑领域也得到了广泛应用。例如,建筑外墙板、保温材料等使用 了玻璃纤维复合材料,具有较好的保温性能和耐候性能,能够提高建筑物的使用寿命和
界面材料匹配
通过合理的界面材料匹配,提高界面结合强度,降低界面应力集中,提高复合材料的整体性能。
制备工艺优化策略
制备工艺流程优化
通过优化制备工艺流程,减少生产过程中的能耗和污染,提高生产效率。
制备工艺参数优化
通过调整制备工艺参数,如温度、压力、时间等,提高复合材料的整体性能和稳定性。
06
复合材料界面应用案例分 析
复合材料界面课件
• 复合材料概述 • 界面基本概念与分类 • 复合材料界面研究方法 • 复合材料界面性能影响因素 • 复合材料界面优化设计策略 • 复合材料界面应用案例分析
01
复合材料概述
定义与分类
定义
复合材料是由两种或两种以上不同性质的材料,通过物理或化学的方法,在宏观 上组成具有新性能的材料。
用。
04
复合材料界面性能影响因 素
第4章复合材料的界面
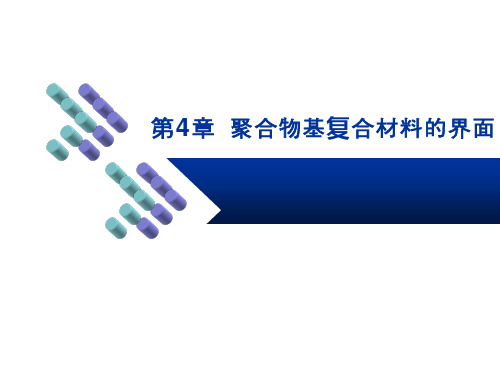
• 物理效应,引起各组分间相互浸润、扩散、相溶性、界面吉布斯自 由能等变化; • 化学效应,导致界面上的化学反应,形成新的界面层结构; • 力学效应,引起界面上的应力分布。具有弱界面的复合材料有较低 的强度和刚度,但它的断裂抗力较高;具有强界面的复合材料有较高 的强度和刚度,但非常脆。
界面的基本概念
界面的形成与作用机理
§界面的作用机理
(七)优先吸附理论
树脂胶液中,各组分在玻璃纤维上的吸附能力各不相同,纤维表面优 先吸附基体体系中的助剂。例如胺类固化环氧树脂,优先吸附胺类,使界 面层基体内分布为一梯度,有利于消除应力,改善复合材料的力学性能。
界面的破坏机理
§影响界面黏结强度的因素
(1)纤维表面晶体大小及比表面积
碳纤维复合材料的界面黏结强度随纤维表面晶体尺寸增大而下降。 纤维的比表面积大,黏结的物理界面大,粘结强度高。但对于不同的 纤维和不同的表面处理,应该具体问题具体分析。 (2)浸润性 界面的黏结强度随浸润性增加而增大,随空隙率的上升而下降。 (3)界面反应性 界面黏结强度随界面反应性的增大而增大,界面的反应性大小与复合 材料层剪强度紧密相关。制备复合材料时要尽可能多地向界面引入反应基 团,增加界面化学键合比例,提高复合材料性能。
第4 章 聚合物基复 合材料的界面
本章主要内容
1 2 3 4 5
第一节 界面的基本概念 第二节 界面的形成与作用机理 第三节 界面的破坏机理 第四节 纤维的表面处理
第五节 复合材料界面的研究
界面的基本概念
• 界面——纤维复合材料中增强纤维和基体之间
共有的接触面。 • 聚合物基复合材料的三要素:界面、纤维和基 体。 • 影响复合材料性能的因素:①增强材料的性能, 如纤维的形状、排列等;②基体的性能;③复 合材料的结构及成型技术;④复合材料中纤维 和基体界面的结合状态,即界面层的性能。
界面的基本概念
界面的形成与作用机理
§界面的作用机理
(七)优先吸附理论
树脂胶液中,各组分在玻璃纤维上的吸附能力各不相同,纤维表面优 先吸附基体体系中的助剂。例如胺类固化环氧树脂,优先吸附胺类,使界 面层基体内分布为一梯度,有利于消除应力,改善复合材料的力学性能。
界面的破坏机理
§影响界面黏结强度的因素
(1)纤维表面晶体大小及比表面积
碳纤维复合材料的界面黏结强度随纤维表面晶体尺寸增大而下降。 纤维的比表面积大,黏结的物理界面大,粘结强度高。但对于不同的 纤维和不同的表面处理,应该具体问题具体分析。 (2)浸润性 界面的黏结强度随浸润性增加而增大,随空隙率的上升而下降。 (3)界面反应性 界面黏结强度随界面反应性的增大而增大,界面的反应性大小与复合 材料层剪强度紧密相关。制备复合材料时要尽可能多地向界面引入反应基 团,增加界面化学键合比例,提高复合材料性能。
第4 章 聚合物基复 合材料的界面
本章主要内容
1 2 3 4 5
第一节 界面的基本概念 第二节 界面的形成与作用机理 第三节 界面的破坏机理 第四节 纤维的表面处理
第五节 复合材料界面的研究
界面的基本概念
• 界面——纤维复合材料中增强纤维和基体之间
共有的接触面。 • 聚合物基复合材料的三要素:界面、纤维和基 体。 • 影响复合材料性能的因素:①增强材料的性能, 如纤维的形状、排列等;②基体的性能;③复 合材料的结构及成型技术;④复合材料中纤维 和基体界面的结合状态,即界面层的性能。
第四章复合材料界面

浸润性仅仅表示了液体与固体发生接触时的 情况,而并不能表示界面的粘结性能。一种 体系的两个组元可能有极好的浸润性,但它 们之间的结合可能很弱,如范德华物理键合。 因此润湿是组分良好粘结的必要条件,并非 充分条件。
第四章复合材料界面
二、机械作用理论 : ➢ 当两个表面相互接触后,由于表面粗糙不
平将发生机械互锁。
• 因此,在研究和设计界面时,不应只追求 界面结合而应考虑到最优化和最佳综合性 能。
第四章复合材料界面
五、复合材料组分的相容性
• 物理相容性: 1. 是指基体应具有足够的韧性和强度,能够将外部
载荷均匀地传递到增强剂上,而不会有明显的不 连续现象。 2. 由于裂纹或位错移动,在基体上产生的局部应力 不应在增强剂上形成高的局部应力。 3. 另一个重要的物理关系是热膨胀系数。基体与增 强相热膨胀系数的差异对复合材料的界面结合产 生重要的影响,从而影响材料的各类性能。
第四章复合材料界面
• (5)诱导效应:一种物质(通常是增强剂) 的表面结构使另一种(通常是聚合物基体) 与之接触的物质的结构由于诱导作用而发生 改变,由此产生一些现象,如强弹性、低膨 胀性、耐热性和冲击性等。
第四章复合材料界面
诱导效应
HH
聚合物表面
R
R
R
Si
Si
Si
H O
H2O O
O H
HH
O
O
第四章复合材料界面
4.2 复合材料的界面理论
• 一、界面润湿理论 : ➢ 界面润湿理论是基于液态树脂对纤维表面
的浸润亲和,即物理和化学吸附作用。液 态树脂对纤维表面的良好浸润是十分重要 的。浸润不良会在界面上产生空隙,导致 界面缺陷和应力集中,使界面强度下降。 良好的或完全浸润将使界面强度大大提高, 甚至优于基体本身的内聚强度。