TEG脱水装置及汽提气回收装置工艺流程图
TEG脱水装置的设计
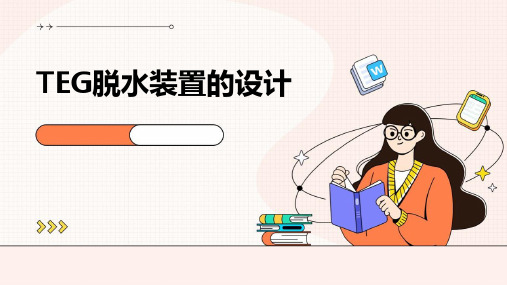
铸造工艺
对于大型结构件或复杂形状的零件,可以采用铸造工艺进行加工。铸造
工艺具有成本低、生产效率高等优点,但精度和表面质量相对较低。
02 03
机械加工工艺
对于精度要求高、形状复杂的零件,可以采用机械加工工艺进行加工。 机械加工工艺具有精度高、表面质量好等优点,但成本较高,生产效率 较低。
焊接工艺
对于大型结构件或需要拼接的零件,可以采用焊接工艺进行加工。焊接 工艺具有成本低、生产效率高等优点,但易产生焊接变形和应力集中。
连接部件
合理设计各部件的连接方 式,确保装置的气密性和 可靠性。
热能回收系统
热能收集
通过高效热能收集器,将 废气中的热能进行收集。
热能传递
利用导热性能良好的材料, 将收集的热能快速传递至 热交换器。
热能利用
将回收的热能用于加热进 入装置的空气或水,提高 能源利用效率。
冷凝系统
冷凝器
排水系统
设计高效冷凝器,将水蒸气冷凝成水。
材料选择
耐高温材料
由于TEG脱水装置需要在高温环境下工作,因此应选择具有良好 耐高温性能的材料,如不锈钢、钛合金等。
耐腐蚀材料
脱水装置在处理腐蚀性气体时,应选择具有良好耐腐蚀性能的材料, 如镍基合金、玻璃钢等。
高强度材料
为了确保装置的稳定性和安全性,应选择具有较高强度和刚度的材 料。
加工工艺
01
变化。
塞贝克效应
当两种不同导体组成闭合回路时, 如果两导体的两个接点温度不同, 就会在回路中产生电动势,这种
现象称为塞贝克效应。
皮尔兹效应
在一定条件下,半导体材料中产 生的热电势与温度梯度成正比,
这种现象称为皮尔兹效应。
脱水原理介绍
三甘醇_TEG_脱水系统的选材设计概要

第22卷第4期2008年8月全面腐蚀控制TOTAL CORROSION CONTROLVol.22 No.4Aug. 20081概述水是天然气从采出至消费的各个处理加工步骤中最常见的杂质组分,且其含量经常达到饱和。
冷凝水的局部积累将限制管道中天然气的流率,降低输气量,而且水的存在使输气过程增加了不必要的动力消耗;液相水与CO2或H2S接触后会生成具有腐蚀性的酸,H2S不仅导致常见的电化学腐蚀,它溶于水生成的HS-还会促使阴极放氢加快, HS-阻止原子氢结合为分子氢,从而造成大量原子态氢积聚在钢材表面,导致钢材氢鼓泡、氢脆及硫化合物应力腐蚀开裂(SSC;湿天然气中经常遇到的另一个麻烦问题是,其中所含水分和小分子气体及其混合物可在较高的压力和温度高于0℃的条件下,形成一种外观类似于冰的固体水合物。
因此,天然气一般都应先经脱水处理,使之达到规定的指标后才能进入输气干线。
我国强制性国家标准规定:在天然气交接点的温度和压力条件下,天然气的水露点应比最低环境温度低5℃。
在CO2或H2S存在的情况下,目前海洋工程设计过程中认为只有当水露点比最低操作温度低10℃时介质不具有腐蚀性。
甘醇类化合物具有很强的吸湿性,其水溶液冰点较低,故广泛应用于天然气脱水。
最初应用于工业的是二甘醇(DEG,上世纪50年代后主要采用三甘醇(TEG,其热稳定性更好,容易再生,蒸气压也更低,且相同质量浓度下TEG可达到更大的露点降,而且TEG的毒性很轻微,沸点较高,常温下基本不挥发,故使用时不会引起呼吸中毒,与皮肤接触也不会造成伤害。
因此,TEG 脱水方法是天然气工业中应用最普遍的方法。
2 TEG脱水系统的工艺流程如图1[1]所示,TEG脱水装置主要包括2部分:天然气在压力和常温下脱水;富TEG溶液在低压和高温下再生(提浓。
此图所示流程包括了若干优化操作方面的考虑,如以气体—TEG换热器调节吸收塔顶温度,以分流(或全部富液换热的方式控制进入闪蒸罐的富液温度,以干气汽提提高贫TEG的浓度,以及设置多种过滤器等。
天然气脱水工艺流程介绍(ppt 30页)
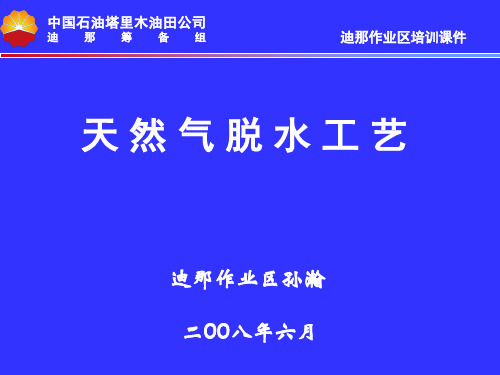
①工艺简单,操作容易,占地面积小;
②不需要额外加入溶剂,不需再生,无二次污染;
③可利用天然气本身的压力作为推动力,几乎没有压力损失;
④操作弹性大,可通过调节膜面积和工艺参数来适应处理量
的波动。
中国石油塔里木油田公司
迪那筹备组
讲座提 纲
一、脱水的原
因 二、脱水方法简
介 三、脱水工艺介
绍 四、各工艺的注意事
节流阀制冷
膨胀制冷
膨胀机制冷
低温分离法
丙烷制冷
热分离机制冷等
中国石油塔里木油田公司
迪那筹备组
脱水的方
法
• 溶剂吸收法:
利用某些液体物质不与天然气中的水分发 化学反应,只对水有很好的溶解能力且溶水 后蒸气压很低,可再生和循环使用的特点。 将天然气中水汽脱出。这样的物质有甲醇、 甘醇等。由于吸收剂可再生和循环使用,故 脱水成本低,已得到广泛使用。
油气田无自由压降可利用,满足 管输天然气水露点要求的场合。
1、脱水后干气中水含量可 低于1ppm,水露点可低于90℃; 2、对进料气体温度、压力 、流量变化不敏感; 3、操作简单,占地面积小 4、无严重腐蚀和发泡方面 的问题。
1、对于大装置,其设备投 资大,操作费用高; 2、气体压降大; 3、吸附剂使用寿命短,一 般三年需更换,增加成本; 4、耗能高,低处理量时更 明显;
• 牙哈320万方/日凝析气处理装置:设计处理天然 气320万方/天、凝析油产量为50万吨/年, 2000 年10月31日投产装置通过经J-T阀节流降温[加注 乙二醇防冻],脱除天然气中的水,并实现轻烃回 收。
中国石油塔里木油田公司
迪 三那 甘筹 醇备脱水组 工
艺
各工艺的注意 事项
TEG脱水的设计讲解

天然气的含水量及其露点
图3-1 天然气中的水含量及其露点
露点降及要求的脱水量
• 假定脱水装置操作压力为2.76MPa(表) • 进料气200C;含水7.34kg/104m3 • 脱水气-8.890C;含水1.09kg/104m3
露点降 = 20-(-8.89)=28.890C
脱水量 = 7.34 – 1.09 =6.25kg/104m3
5 与吸收塔组合(小型装置)
分离器截面积与允许流量的关系
•原料气相对密度 0.6 •操作压力 2.76MPa(表) •操作温度 21.110C •查表D.2
最大流量=0.89x106m3/d•m2
原料气分离器截面积的确定
• 截面积 Ac=Gs(实际流量)/Ga(允许) • 在0.6; 2.76MPa(表);21.110C下
实际流量为1x106m3/d
• Ac = 1/0.89 = 1.12m2 • 查表D.3
允许流量为0.89xm3/(d•m2)
分离器外径大致为1067mm(4.97MPa)
分离器设计的优化
•分离器可以与吸收塔组合一体 •组合工分离器直径一般与吸收塔相同 •(此时)最小直径应按吸收塔允许流速定 •以捕雾器除去直径大于10μm的液滴 •推荐使用过滤式分离器(除掉润滑油) •必要时储液部位设置回执盘管 •必要时在分离器前设置水冷器
C值的选择
设备与介质 板间距
46cm
61cm
75cm
油吸收塔
700
800
850
甘醇吸收塔
500
550
醇胺吸收塔
350
395
精馏塔
440
540
600
露点降与吸收塔实际板数(表D.5)
含硫天然气的TEG法脱水

含硫天然气的TEG法脱水在含硫气田的开发过程中,为防止集输过程中管线发生腐蚀,应把含硫天然气先脱水后再集输。
含硫天然气的TEG法脱水原则上是和一般气体同样操作,但也有其特殊的矛盾,现简要介绍如下。
1.富TEG溶液的汽提当含硫天然气与TEG溶液接触,H2S会溶解到TEG溶液中,其溶解量随分压增加而增加,随温度升高而减少(参阅图4-26)H2S溶解于TEG溶液后,不仅导致溶液PH植下降,而且也会与TEG反应而导致溶液变质。
鉴此,处理含硫天然气的装置,其流程与图4-15所示不同,应在富TEG溶液进再生塔前的位置上增设一个富液汽提塔[14],以不含硫的天然气或其它惰性气汽提(参阅图4-27)。
2.装置的防腐TEG脱水装置本身就存在腐蚀问题,处理含硫天然气的装置则腐蚀更为严重,必须充分重视。
纯净的TEG溶液本身对碳钢基本上不腐蚀,一般认为腐蚀的加速是由于存在其他化合物,他们主要来自TEG的热降解、氧化降解以及与H2S反应而产生的化学降解。
甘醇类化合物氧化而生成的有机酸以及从气流中吸收H2S和CO2是装置腐蚀的重要化学因素。
TEG脱水装置的防腐问题文献中已有较详细的介绍[11],其要点可大致归纳如下:(1)腐蚀严重的设备或部位采用耐腐蚀材料,如在吸收塔内采用不锈钢衬里、不锈钢板等等。
(2)采取工艺性的防腐措施,如加强分离和过滤措施,保持溶液清洁;用惰气保护溶剂储罐等设备,防止氧气进入系统;改进工艺设计,降低操作温度和流体流速等等。
(3)使用中和剂或缓蚀剂。
TEG装置的腐蚀与溶液的PH值密切有关,PH值降低则腐蚀加剧,因而可以在TEG溶液中注入中和剂或缓蚀剂,保持溶液PH值在7.3-8.5的范围内。
PH值也不宜过高,否则会增加溶液的发泡倾向。
常用的中和剂和缓蚀剂有硼砂、一乙醇胺、三乙醇胺、磷酸钾、β-巯基苯并噻唑钠盐时、苛性钠、碳酸钠。
使用β-巯基苯并噻唑钠盐时,可将它配成45%的水溶液,直接加到甘醇储罐中,控制其在TEG溶液中的浓度为1%。
第5章 天然气脱水第3节ppt课件
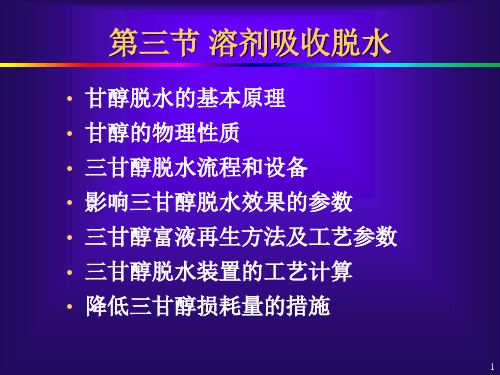
量、塔径、塔结构等影响气、液两相接触时间 的因素。一般可取t=8~11C。
34
(2)贫甘醇溶液用量
甘醇溶液用量超过某一值后曲线趋于平缓, 再增加三甘醇溶液用量,获得的露点降变化不大。 根据经验,每吸收1kg水所需三甘醇为0.025~ 0.06m3。天然气脱水设计规范(SY/T0076—2003) 推荐为每吸收1kg水所需甘醇量,三甘醇为 0.02~0.03m3;二甘醇为0.04~0.1m3。
37
(3)吸收塔塔板数的确定
yN1y1 AN1A yN1y0 AN11
yN+1—进吸收塔湿原料气中水的摩尔分数; y1—离开吸收塔干气中水的摩尔分数; y0—当离塔干气与进塔贫三甘醇溶液处于平衡时,
干气中水的摩尔分数; N—吸收塔理论塔板数; A—吸收因子。
38
(3)吸收塔塔板数的确定
A L KV
18
甘醇循环量与露点降关系图(c)
19
循环量、浓度与塔板数的相互关系
• 循环量和塔板数固定时,三甘醇浓度愈高则露 点降愈大;
• 循环量和三甘醇浓度固定时,塔板数愈多则露 点降愈大,但一般都不超过10块实际塔板;
• 塔板数和三甘醇浓度固定时,循环量愈大则露 点降愈大,但循环量升到一定程度后,露点降 的增加值明显减少,而且循环量过大会导致重 沸器超负荷,动力消耗过大,故最高不应超过 33L/kg水。
在各级塔板上,甘醇并没有都达到平衡 状态。通常用25%的塔板效率作设计。在泡 罩式塔内,相邻塔板的间隔一般为610mm。
14
3. 三甘醇浓度和温度
• 气体露点随三甘醇浓度增加有显著的下降。因此, 降低出塔干气露点的主要途径是提高三甘醇贫液 浓度。
天然气脱水方法

天然气脱水方法作者:佚名文章来源:自动化论坛点击数:37 更新时间:2009-7-201、溶剂吸收法利用适当的液体吸收剂以除去气体混合物中的一部分水份,对吸收后的贫溶剂进行脱吸,使溶剂再生循环使用。
常用的脱水剂有二甘醇、三甘醇等。
2 、固体干燥剂吸附法利用气体在固体表面上积聚的特性,使某些气体组分吸附在固体吸附剂表面,进行脱除。
气体组分不同,在固体吸附剂上的吸附能力也有差异,因而可用吸附方法对气体混合物进行净化。
工业上常用的固体吸附剂有硅胶、活性氧化铝和分子筛。
吸附是在固体表面张力作用下进行的,根据表面张力的性质可将吸附过程分为物理吸附和化学吸附。
物理吸附是可逆过程,可用改变温度和压力的方法改变平衡方向,达到吸附剂的再生。
目前广泛采用的用分子筛作吸附剂脱除天然气中水分的过程就是物理吸附过程。
3、冷冻分离法将一定温度的混合气体在一定压力下通过干燥的、最低温度可达- 20 ℃以下的冷凝器,使混合气体中的水气变成液滴后分离。
常用的设备有冷冻干燥器。
4、脱水剂4.1、三甘醇( TEG) 脱水剂甘醇类化合物具有很强的吸水性,其溶液水点较低,沸点高,毒性小,常温下基本不挥发,所以广泛应用于天然气脱水。
最先用于天然气脱水的是二甘醇,50 年代后TEG 以良好的性能逐步取代了二甘醇成为最主要的脱水溶剂。
TEG 热稳定性好,易于再生,蒸汽压低,携带损失量小,露点降通常为33 - 47 ℃。
4.2、分子筛吸附剂分子筛具有均一微孔结构,能将不同大小的分子分离的一种高效、高选择性的固体吸附剂。
分子筛是一种人工合成的无机吸附剂,天然气脱水常用的是4A 和5A ,它是具有骨架结构的碱金属或碱土金属的硅铝酸盐晶体,其分子式为:M2/ nO·Al2O3·xSiO2·yH2O式中:M —某些碱金属或碱土金属离子, 如Li ,Na ,Mg ,Ca 等;n —M 的价数;x —SiO2 的分子数;y —H2O 的分子数。
天然气脱水工艺流程演示文稿

天然气脱水工艺流程演示文稿一、引言天然气是一种重要的清洁能源,然而,在天然气的生产和运输过程中,常常伴随着大量的水分存在。
为了提高天然气的热值和减少管道的腐蚀,需要对天然气进行脱水处理。
二、脱水工艺流程1.提高压力天然气从井口出来时的压力一般比较低,需要通过增压设备将其压力提高到一定程度,以便后续步骤的进行。
2.初级脱水初级脱水是将天然气中的大部分水分去除的工艺步骤。
通常采用的方法是使用吸附剂或干燥剂来吸附天然气中的水分。
常用的吸附剂有硅胶和分子筛等,常用的干燥剂有石油醚等。
天然气经过初级脱水后,水分含量明显降低。
3.残余水分的除去初级脱水后,天然气中仍然会残留一部分水分。
为了进一步降低水分含量,需要使用高效脱水设备进行二次脱水。
常用的高效脱水设备有膜分离器和冷凝器等。
膜分离器通过半透膜的作用将天然气中的水分分离出来,冷凝器则利用冷凝原理将天然气中的水分冷凝成液体。
4.脱水后处理脱水后的天然气含有少量的脱水剂残留物和其他杂质。
为了提高天然气的纯净度,需要经过一系列的后处理步骤。
常用的后处理设备有过滤器和除尘器等。
三、工艺流程的示意图(在演示文稿中插入一张天然气脱水工艺流程示意图,并进行详细解释)四、设备介绍1.增压设备增压设备用于将天然气的压力提高到一定程度。
一般采用的设备有压缩机和泵等。
2.初级脱水设备初级脱水设备主要是吸附剂和干燥剂。
吸附剂常用的有硅胶和分子筛,干燥剂常用的有石油醚等。
3.高效脱水设备高效脱水设备有膜分离器和冷凝器。
膜分离器通过半透膜的作用将水分分离出来,冷凝器通过冷凝原理将水分冷凝成液体。
4.后处理设备后处理设备有过滤器和除尘器。
过滤器用于去除脱水后残留的脱水剂残留物和其他杂质,除尘器用于去除天然气中的颗粒物。
五、总结。