双面超厚铜线路板生产工艺参数.pptx
超厚铜板制作作业指导书

SHENZHEN MULTILAYER PCB TECHNOLOGY CO.,LTD 版本: A.0頁碼:- 1 - 文件超厚铜板制作作业指导书名稱SHENZHEN MULTILAYER PCB TECHNOLOGY CO.,LTD 版本: A.0頁碼:- 2 -文件超厚铜板制作作业指导书名稱1.0 目的建立详细的作业规范,籍以提升产品良品率,规范的员工操作,此文件同时也是制做超厚铜板的培训教材。
2.0 适用范围本作业规范适用于铜箔厚度≥5盎司以上的双面超厚铜板的制作。
3.0 职责3.1 生产部职责3.1.1 员工按本作业指导书及“生产指示”进行操作并作相关的记录,工序主任/领班对此进行监督和审核。
3.1.2 工序主任負责对员工进行生产操作的培訓及考核。
3.2 品质部职责3.2.1 品质部负责对生产部的品质、保养、操作、参数和环境检测稽核与监控,保证产品符合客户要求。
3.3 工程技术部职责3.3.1 评估和提供生产过程中各种参数要求。
3.3.2 制定相关作业指导书,对超厚铜板的重点工艺进行策划,指导。
4.0 作业内容4.1 工艺流程铜皮、芯板开料→钻孔→铜皮成像(前处理→印湿膜→曝光→显影)→铜皮蚀刻→退湿膜→黑化→填胶→叠板→层压→剪边→退黑化→ P片开料→↑铣靶孔→钻孔→沉铜(板电)→外成像(前处理→印湿膜→爆光→显影→图镀→蚀刻(退膜→蚀刻→退锡)→印阻焊→外发镀层→铣外形(二钻)→测试→成检→包装出货4.2 操作说明4.2.1 钻孔:用锣机钻出铜皮、芯板的菲林对位孔、铆钉孔、钻孔定位孔。
4.2.2 铜皮双面成像:根据菲林对位孔对位,对位的层次排列按以下方法执行:其它操作具体见《曝光显影工序作业指导书》。
4.2.3铜皮蚀刻:把铜皮当成一块双面板来对待,分为GTL-1、GTL-2面或GBL-1、GBL-2面;走湿膜工艺,先将铜皮的双面图形爆出来;蚀刻时,将蚀刻机的下喷嘴关掉,使用上喷嘴进行加工;GBL-1和GTL-1面稍微蚀刻出图形模子,GBL-2和GTL-2蚀刻至铜皮整体厚度的2/3左右,可用千分尺来量铜皮的蚀刻厚度,具体见《蚀刻工序作业指导书》。
超厚铜多层印制电路板制作工艺探讨

铜 多层 印制 板 的制作 报道 却寥寥 无几 ;本 文主要 针对
4 1 1 . 6 l a m( 1 2 o z / f 【 2 )超厚铜多层 印制板的制作工艺进
行 可 行 性 研 究 , 经 工 艺优 化 ,采 用 厚 铜 分步 控 深 蚀
z s i n g c o p p e r b a c k - e t c h i n g , l a mi n a t i n g nd a p o s i t i v e e t c h i n g . T h e q u a l i t y o f e t c h e d l i n e nd a l a mi n a t i o n wa s a s s u r e d . I t
了客 户的特种需求 。
关 键 词 铜厚 4 1 1 . 6 g m 多层 印制 板 ;超 厚 铜 ;反 面 蚀 刻
中图分类号 :T N 4 1
文献标识码 :A 文章编号 :1 0 0 9 — 0 0 9 6( 2 0 1 3) 0 5 — 0 0 8 3 — 0 4
The t e c hno l o g y o f pr o duc t i o n pr o c e s s f o r s upe r
L t l y i mp r o v e d t h e q u a l i t y o f t h e p r o d u c t i o n s , nd a me e t t h e c u s t o me r ' s s p e c i a l r e q u i r e me n t s o n s u p e r hi t c k c o p p e n
JX-WI-PR-015厚铜板制作规范
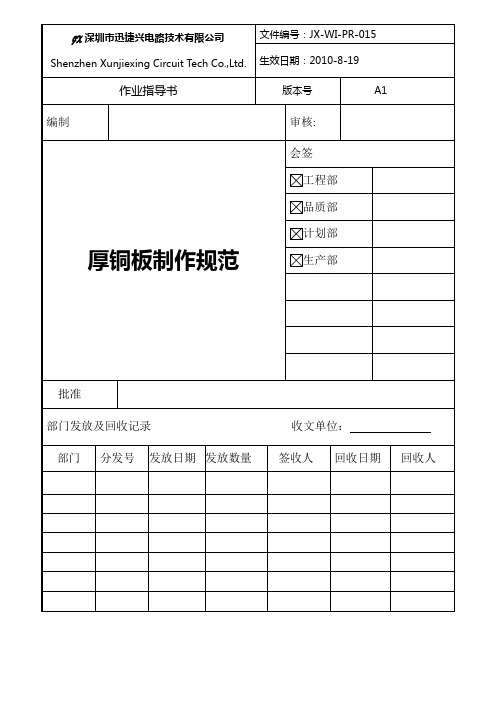
文件修改履历表表格编号:JX-R-QA-058 版本:A11.0 目的确定厚铜板在我公司的设计、生产制作方法及注意事项,规范厚铜板制作方法,从而有效保证产品良率!2.0 适用范围:本程序适用于本公司厚铜板产品在本公司内部的设计及加工,且主要针对3-6OZ铜厚的线路板的设计及加工制作。
3.0 相关文件生产各工序作业规范,除此文件中所特别要求的工艺、参数、操作外,其他按工序作业规范参数制作.4.0职责工程部负责客户资料审查及制程能力审查,进行定单评审;负责产品制作流程的设计及客户资料的处理优化;生产用治工具提供。
工艺部负责协助工程部进行资料的评审;制程稳定性监控及维护,从而保证品质的稳定性。
品质部负责产品制造过程的品质监控及记录;定期对产品的良率进行分析,定义产品控制良率水准;产品品质不达标时,及时反馈,并通知制造、工艺部进行改善。
生产部负责产品的制造及产品交期的达成;a.若客户有高TG要求,应先建议客户使用中Tg材料.b.内层≥4OZ的板,优先选用生益4OZ的芯板材料。
B.厚铜箔的选取厚铜箔板分级6.1.2.A.尽量以高含胶薄织物放于填胶面,3OZ以上一般以106,1080,2116等相互搭配时, 当内层为1或Hoz或内层残铜率高于50%时,使用高含胶量薄织物胶片置于外层,内层则厚玻璃布如1080放外,2116放内。
B.当内层为2~6oz时,残铜率低于50%时,则高含胶量的薄织物放内,而厚玻璃布种放外,如2116放外,1080放内。
C.P P片选择:a.b.6.1.3A以上),PADBC.当D.E.于10mm,同时保证层压排气。
F.要求Panel的含铜量须大于60%。
6.1.4. 铜边到锣边最小距离:。
电路板的制作工艺 ppt课件

图3.1 焊接式对 外引线
图3.2 线路板对外引线 焊接方式
2020/11/29
22 7
• 2 插接件连接
• 在比较复杂的电子仪器设备中,为了安装调试方便,经 常采用接插件连接方式。当整机发生故障时,维修人员 不必检查到元器件级(即检查导致故障的原因,追根溯 源直至具体的元器件。这项工作需要一定的检验并花费 相当多的时间),只要判断是哪一块板不正常即可立即 对其进行更换,以便在最短的时间内排除故障,缩短停 机时间,这对于提高设备的利用率十分有效。
• 6.腐蚀。将前面处理好的电路板放入盛有腐蚀液的容器 中,并来回晃动。为了加快腐蚀速度可提高腐蚀液的浓 度并加温,但温度不应超过50℃,否则会破坏覆盖膜使 7.其脱落。待板面上没用的铜箔全部腐蚀掉后,立即将 电路板从腐蚀液中取出。
• 清水冲洗。
• 8.除去保护层。
2020/11/29
29 11
• 9. 修板。将腐蚀好的电路板再一次与原图对照,用刻刀 修整导电条的边缘和焊盘,使导电条边缘平滑无毛刺, 焊点圆润。
——电路板生产线组成和岗位操作
2020/11/29
1
目录
• 一、印制板草图设计 • 二、印制电路板的类型和特点 • 三、印制电路板板材 • 四、印制板对外连接方式的选择 • 五、印制板制造的基本工序 • 六、印制电路板的简易制作过程 • 七、印制电路板的制造工艺 • 八、PCB设计抗干扰问题
2020/11/29
2020/11/29
20 6
• 5 .根据性能价格比选用
• 设计挡次较高产品的印制板时,一般对覆铜板的价格考 虑较少,或可不予考虑。因为产品的技术指标要求很高, 产品价格十分昂贵,经济效益是不言而喻的。对一般民 用产品在设计时,在确保产品质量的前提下,尽量采用 价格较低的材料。如袖珍收音机的线路板尺寸小,整机 工作环境好,市场价格低廉,选用酚醛纸质板就可以了, 没有必要选用环氧玻璃布层压板一类的板材。
双面电路板
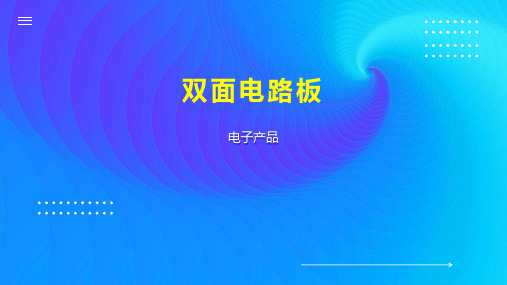
杂物塞孔
在长期生产控制过程中,我们发现当孔径达到0.15-0.3mm,其塞孔的比例递增30% 1、孔形成过程中的塞孔问题: 印制板加工时,对0.15-0.3mm的小孔,多数仍采用机械钻孔流程。在长期检查中,我们发现钻孔时,残留在 孔里杂质 以下为钻孔塞孔的主要原因: 当小孔出现塞孔时,由于孔径偏小,沉铜前高压水洗、化学清洗难以把小孔里面的杂物去除,阻挡化学沉铜 过程中药水在孔里的交换,使化学沉铜失去作用。 钻孔时根据叠层厚度选用合适钻嘴、垫板,保持基板清洁,不重复使用垫板,有效的吸尘效果(采用独立的 吸尘控制系统)是解决塞孔必须考虑的因素。
孔化机理
钻头在敷铜板上先打孔,再经过化学沉铜,电镀铜形成镀通孔。二者对孔金属化起着至关重要的作用。
1、化学沉铜机理:
在双面和多层印制板制造过程中,都需要对不导电的裸孔进行金属化,亦即实施化学沉铜使其成为导体。化 学沉铜溶液是一种催化式的“氧化/还原”反应体系。在Ag、Pb、Au、Cu等金属粒子催化作用下,沉积出铜来。
双面电路板
电子产品
01 前言
03 孔化机理
目录
02 工艺流程 04 杂物塞孔
高科技发展,人们需要性能高、体积小、功能多的电子产品,促使印制线路板制造也向轻、薄、短、小发展, 有限空间,实现更多功能,布线密度变大,孔径更小。自1995年至2005年间,机械钻孔批量能力最小孔径从原来 0.4mm下降到0.2mm,甚至更小。金属化孔孔径也越来越小。层与层间互连所依赖的金属化孔,质量直接关系印制 板可靠性。
2、电镀铜机理:
电镀定义是利用电源,在溶液中将带正电的金属离子,推送到位在阴极的导体表面形成镀层。电镀铜是一种 “氧化/还原”反应,溶液中的铜金属阳极将其表面的铜金属氧化,而成为铜离子。另一方面在阴极上则产生还原 反应,而令铜离子沉积成为铜金属。两者皆通过药水交换,化学作用达到孔化目的,交换较大孔径没影响的杂物,如磨刷碎屑、火山灰,一旦残留在小孔里面,将使化学沉铜、 电镀铜失去作用,出现孔无铜,成为孔金属化的致命杀手。
超厚铜(10OZ)PCB的制作工艺研究
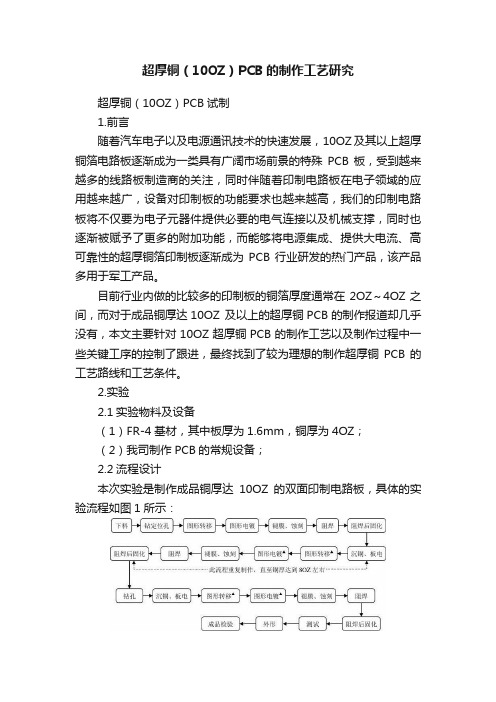
超厚铜(10OZ)PCB的制作工艺研究超厚铜(10OZ)PCB试制1.前言随着汽车电子以及电源通讯技术的快速发展,10OZ及其以上超厚铜箔电路板逐渐成为一类具有广阔市场前景的特殊PCB板,受到越来越多的线路板制造商的关注,同时伴随着印制电路板在电子领域的应用越来越广,设备对印制板的功能要求也越来越高,我们的印制电路板将不仅要为电子元器件提供必要的电气连接以及机械支撑,同时也逐渐被赋予了更多的附加功能,而能够将电源集成、提供大电流、高可靠性的超厚铜箔印制板逐渐成为PCB行业研发的热门产品,该产品多用于军工产品。
目前行业内做的比较多的印制板的铜箔厚度通常在2OZ~4OZ之间,而对于成品铜厚达10OZ 及以上的超厚铜PCB的制作报道却几乎没有,本文主要针对10OZ超厚铜PCB的制作工艺以及制作过程中一些关键工序的控制了跟进,最终找到了较为理想的制作超厚铜PCB的工艺路线和工艺条件。
2.实验2.1实验物料及设备(1)FR-4基材,其中板厚为1.6mm,铜厚为4OZ;(2)我司制作PCB的常规设备;2.2流程设计本次实验是制作成品铜厚达10OZ的双面印制电路板,具体的实验流程如图1所示:图1 整体制作流程对于流程中“图形转移▲→图形电镀▲”,本次实验设计了三种制作方案:方案一:湿膜法,其主要制作思路为:利用湿膜良好的填充性将板面铺平然后进行图形转移,接下来电镀两个循环,加厚大约2OZ的厚度,也即是以2OZ的厚度叠加,具体流程如图2所示。
图2 湿膜法Fig.2 Wet film method方案二:一次干膜法,其主要制作思路为:贴干膜之后进行LDI 线路制作,然后再电镀一个循环,加厚大约1OZ的厚度,即以1OZ的厚度叠加,具体流程如图3所示。
图3 一次干膜法Fig.3 Dry film once方案三:两次干膜法,其主要制作思路为:第一次贴干膜之后进行LDI 线路制作,然后电镀一个循环(大约有1OZ 的厚度),此时干膜与线条基本水平,接下来再次贴干膜进行LDI 线路制作,然后再电镀一个循环(大约1OZ 的厚度),即以2OZ 的厚度叠加,具体流程如图4所示:图4 两次干膜法Fig.4 Dry film twice3.结果与讨论3.1工艺流程的优化图5 湿膜法叠加一次的线路切片图图5为方案一所设计的湿膜法叠加一次所得到的线路切片图,从图中可以看到线路呈典型的“蘑菇状”,且两次线路出现比较明显的错位,分析两次线路产生错位的主要原因在于用湿膜进行图形转移时需要用到菲林,而人工用菲林对位时其对准度难以得到保证;而线路呈现“蘑菇状”主要是由于人工印刷的湿膜厚度较薄(1/3OZ 左右),后期电镀上的铜(厚度为2OZ左右)凸出线条造成的。
一种双面厚铜板制作方法
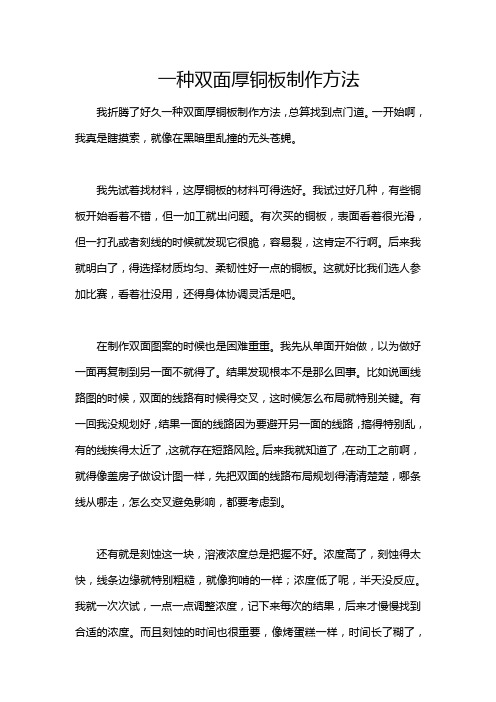
一种双面厚铜板制作方法我折腾了好久一种双面厚铜板制作方法,总算找到点门道。
一开始啊,我真是瞎摸索,就像在黑暗里乱撞的无头苍蝇。
我先试着找材料,这厚铜板的材料可得选好。
我试过好几种,有些铜板开始看着不错,但一加工就出问题。
有次买的铜板,表面看着很光滑,但一打孔或者刻线的时候就发现它很脆,容易裂,这肯定不行啊。
后来我就明白了,得选择材质均匀、柔韧性好一点的铜板。
这就好比我们选人参加比赛,看着壮没用,还得身体协调灵活是吧。
在制作双面图案的时候也是困难重重。
我先从单面开始做,以为做好一面再复制到另一面不就得了。
结果发现根本不是那么回事。
比如说画线路图的时候,双面的线路有时候得交叉,这时候怎么布局就特别关键。
有一回我没规划好,结果一面的线路因为要避开另一面的线路,搞得特别乱,有的线挨得太近了,这就存在短路风险。
后来我就知道了,在动工之前啊,就得像盖房子做设计图一样,先把双面的线路布局规划得清清楚楚,哪条线从哪走,怎么交叉避免影响,都要考虑到。
还有就是刻蚀这一块,溶液浓度总是把握不好。
浓度高了,刻蚀得太快,线条边缘就特别粗糙,就像狗啃的一样;浓度低了呢,半天没反应。
我就一次次试,一点一点调整浓度,记下来每次的结果,后来才慢慢找到合适的浓度。
而且刻蚀的时间也很重要,像烤蛋糕一样,时间长了糊了,时间短了没熟。
一开始我没注意时间,刻蚀久了铜板有些地方都薄得不像话了。
在焊接方面我也吃了不少苦头。
焊接的时候温度要是不合适,要么焊不上,要么就把旁边的东西都给烫坏了。
我开始的时候胡乱调温度,看到不沾锡就提高温度,结果把铜板都烤变色了。
后来啊,我就慢慢试,每个焊点的大小不同的话,温度可能就需要微调。
总之啊,这双面厚铜板制作就是一个不断试错的过程,每个环节都不能马虎。
印制线路板之化学厚铜

印制线路板之化学厚铜12.生产方法:(1)向清洗干净的搅拌罐中,加入DI水、片碱搅拌至完全溶解;(2)加入EDTA搅拌至溶解;(3)冷却至室温,加入HEDTA搅拌至完全溶解;(4)加DI水至1000KG,搅拌半小时;(5)QC检验合格后,装桶。
3.4.生产方法:(1)向清洗干净的搅拌罐中,加入DI水、硫酸铜搅拌至完全溶解;(2)加DI水至1000KG,搅拌半小时;(3)QC检验合格后,装桶。
5.化学厚铜B剂配方(1000Kg)6.生产方法:(1)向清洗干净的搅拌罐中,加入DI水、氢氧化钠搅拌至完全溶解;(2)加DI水至1000KG,搅拌半小时;(3)QC检验合格后,装桶。
8.生产方法:(1)用有机溶剂溶解吡啶衍生物;(2)向清洗干净的搅拌罐中,加入亚铁盐、HEDTA三铵搅拌至完全溶解;(3)将(1)加入到搅拌罐中,加DI水至100KG,搅拌半小时;(4)QC检验合格后,装桶。
9.化学厚铜的作用利用化学沉积方式,在线路板孔内非导电基材上沉积导电铜层。
10.操作条件11.槽液配制(1)在洁净槽内加入3/4体积的所需要的纯水;(2)空气搅拌下依次加入开缸剂M,A剂、B剂;(3)空气搅拌下加入稳定剂S;(4)加入甲醛,补充纯水至标准液位,开循环泵,并升温至工作温。
12.槽液维护(1)工作液成分和控制指标(2)化学厚铜原液的作用M 提供络合剂,仅开缸时使用;A剂提供铜离子;B剂提供氢氧化钠;S剂提供稳定剂。
(3)正常生产每四小时分析一次含量,并调整到最佳值。
100升槽液提高铜含量0.1g/L,加A剂 0.25L;100升槽液提高氢氧化钠含量1g/L,加B剂 0.5L;100升槽液提高甲醛含量1g/L ,加37%甲醛原液0.25L。
(4)一般情况下自动添加A和B按5:3添加(负载过大及过小时适当调整添加比例) (5)每生产100ft2添加化铜A剂 5L,B剂 3L,S剂 0.1-0.2L,甲醛根据分析值补加。
- 1、下载文档前请自行甄别文档内容的完整性,平台不提供额外的编辑、内容补充、找答案等附加服务。
- 2、"仅部分预览"的文档,不可在线预览部分如存在完整性等问题,可反馈申请退款(可完整预览的文档不适用该条件!)。
- 3、如文档侵犯您的权益,请联系客服反馈,我们会尽快为您处理(人工客服工作时间:9:00-18:30)。
产品结构
▪ 图片:
▪ 工艺参数
绝缘树脂
阻焊油墨
序号
规格要求
A 线路铜厚要求为≥450UM
以上
B
孔内电镀铜厚要求为
≥150UM以上
FR-4芯板
线路铜
导通孔
C FR-4内层芯板不含铜要求
为1.4MM
D 树脂填塞须与线路表面平
铜面
网版开窗补偿:单边补偿 15mil
刮刀角度: 21度
印刷速度:1.2m/min
印刷速度:前刮刀 1.2m/min、回油刀 1.0m/min
刮刀压力:7.5kg/cm2
印刷刀数:反复刮8刀
烘烤参数:75℃ 30分钟
150℃ 60分钟
责任 敬业 合作 创新 8
春焱电子科技(苏州)有限公司
CHUNYAN ELECTRONIC TECHNOLOGY (SUZHOU) CO.,LTD.
责任 敬业 合作 创新 11
春焱电子科技(苏州)有限公司
CHUNYAN ELECTRONIC TECHNOLOGY (SUZHOU) CO.,LTD.
二次线路
▪ 图片:
填塞的树脂
FR-4芯板
120um深镀的 线路凹陷区
320um厚 度的线路铜
厚
序号 A
▪ 工艺参数:
规格要求
操作条件
压膜速度:1m/min 压膜温度:105℃
整无空洞或气泡
责任 敬业 合作 创新 3
春焱电子科技(苏州)有限公司
CHUNYAN ELECTRONIC TECHNOLOGY (SUZHOU) CO.,LTD.
过程控制/开料
▪ 图片:
铜箔
序号
FR-4芯板 A
B
▪ 工艺参数:
规格要求
操作条件
铜箔厚度 为
2.0/OZ=7 0UM
FR-4芯板 不含铜要
打磨处理
▪ 图片:
气动打磨机
线路
▪ 工艺参数:
序号 规格要求
操作条件
线距凹陷位置 填塞的树脂
线路表面不充 使用320目砂纸
A 许有树脂油墨 进行均匀打磨,
残留
线路表面残留的 树脂油墨全部打
磨干净即可。
责任 敬业 合作 创新 9
春焱电子科技(苏州)有限公司
CHUNYAN ELECTRONIC TECHNOLOGY (SUZHOU) CO.,LTD.
一次线路
▪ 图片:
线路
线距
基材
▪ 工艺参数:
序号 规格要求
操作条件
压膜速度:1m/min
压膜温度:105℃
菲林补偿:原稿菲林未
无OS(开短 补偿
路) 线宽公 对位精度:ccd自动对位
A
差控制在 对位精度3mil ±15%以内 曝光能量:8格=40mj
蚀刻速度:1m/min一 次+2.5m/min一次, 累计蚀刻过机两次
求为 1.4MM
选用2盎司厚度的 底铜FR-4芯板为 1.4mm的板料进行 开料
铜箔
C
开料,尺寸 公差控制 采用滚筒裁切机正
范围 常生产
±1.0MM
责任 敬业 合作 创新 4
春焱电子科技(苏州)有限公司
CHUNYAN ELECTRONIC TECHNOLOGY (SUZHOU) CO.,LTD.
一次板铜加厚
菲林补偿:原稿菲林
无OS(开 未补偿
短路) 线宽 公差控制 在±15%
春焱电子科技(苏州)有限公司
CHUNYAN ELECTRONIC TECHNOLOGY (SUZHOU) CO.,LTD.
双面450UM超厚铜 线路板制作 工艺参数
部门:工艺部 编制:郭海涵 审核:蒋旭峰 时间:2011-09-26
责任 敬业 合作 创新 1
春焱电子科技(苏州)有限公司
CHUNYAN ELECTRONIC TECHNOLOGY (SUZHOU) CO.,LTD.
精准无偏 0.4m/min,1.0mm ,Φ
孔、披锋 0.8m/min
不良 主轴转速: 3.2mm Φ
23krpm, 1.0mm Φ
55krpm
回刀速度:3.2mm Φ 12m/min,1.0mm ,Φ 15m/min
责任 敬业 合作 创新 6
春焱电子科技(苏州)有限公司
CHUNYAN ELECTRONIC TECHNOLOGY (SUZHOU) CO.,LTD.
责任 敬业 合作 创新 7
春焱电子科技(苏州)有限公司
CHUNYAN ELECTRONIC TECHNOLOGY (SUZHOU) CO.,LTD.
一次树脂印刷填塞
▪ 图片:
▪ 工艺参数:
丝印刮刀 线路
网版开窗 网版挡点
线距凹陷 位置填塞 的树脂
序号
A
规格要求
操作条件
网纱T数:35T
树脂油墨 填塞须与 线路表面 平整无空 洞、气泡 或油墨上
▪ 图片:
阳极 夹具
夹具
纵向夹板 阳极
横向夹板
▪ 工艺参数
序号 规格要求
操作条件
A 表面电镀铜厚 18ASF电流密度电 ≥150UM以上 镀时间为80MIN电 镀6次
板面铜厚均匀 分6次旋转换位夹
B 性偏差20UM 点电镀来均匀分布
以内
电流走向及镀层厚
度
责任 敬业 合作 创新 5
春焱电子科技(苏州)有限公司
二次板铜加厚
▪ 图片:
▪ 工艺参数:
填塞的树 脂
序号 规格要求
操作条件
A 表面电镀铜 18ASF电流密度
厚≥100um 电镀时间为Biblioteka 以上80min电镀4次
120um厚 度的电镀
层
FR-4芯板
累计表面 铜厚
320um
板面铜厚均 分4次旋转换位
B 匀性偏差
夹点电镀来均匀
15um以内 分布电流走向及
镀层厚度
一次沉铜
▪ 图片:
▪ 工艺参数:
沉铜层
填塞的树脂
序号 规格要求
操作条件
线路
FR-4芯板
线路铜层及填塞 沉铜生产时不
A 树脂表面均匀沉 过除胶,其它 积分布一层金属 按正常生产条
铜
件制作。
责任 敬业 合作 创新 10
春焱电子科技(苏州)有限公司
CHUNYAN ELECTRONIC TECHNOLOGY (SUZHOU) CO.,LTD.
CHUNYAN ELECTRONIC TECHNOLOGY (SUZHOU) CO.,LTD.
一次机械钻定位孔
▪ 图片:
定位孔
基板
▪ 工艺参数
序号 规格要求
操作条件
叠板:1PNL/1叠
钻刀寿命: Φ 3.2mm直 径100孔、 Φ 1.0mm直 径500孔/把刀
要求定位 下钻速度: 3.2mm Φ
A
制作工艺流程
开料
1次板铜加厚
1次钻孔
1次线路
1次挡点印刷
2次挡点印刷
2次线路
2次板铜加厚
1次沉铜
1次打磨处理
2次打磨处理
2次钻孔
2次沉铜
3次线路
3次挡点印刷
ET/电测 FQC/终检
锣外型
文字印刷
表面阻焊
OSP/表面处理
FQA/抽 检
包装
3次打磨处理 入库
责任 敬业 合作 创新 2
春焱电子科技(苏州)有限公司