胶管冷喂料螺杆挤出机机头结构浅析
SHJ型双螺杆挤压机的结构及其特点剖析

杆、 机筒 、 传动系统及控制系统的结构特点 ; 指出 S H J 型双螺杆挤压机与单螺杆挤压机相比具 有很好 的混炼 、 输送 、 自洁性能 , 单位产量耗能低的特点; S HJ 双螺杆挤压机设有真空排气装置 、 液压换 网装 置等 , 运转平稳 、 安全可靠 。
设 备 与 控 制
C 合 H I N 成 A 纤 S Y N 维 T H E 工 T I C 业 F , I 2 B 0 E 1 R 4 , 3 I N 7 D ( U 1 S ) T : R 6 Y 6
S HJ型 双 螺 杆 挤 压 机 的结构 及 其特 点 剖析
姜 海 峰
( 中国石油化工股份有限公司天津分公司 , 天津 3 0 0 2 7 0 )
旋转 挤压 机 的螺杆 几何 外形 能得 到高度 的正 向位 移 输送特 性 , 形成 了强制 进 料 。
1 . 3 转 速控 制
单 螺杆 挤压 机 因物料是 直接 通过 料斗 加到 螺 杆 和料 筒之 间 的 , 进 料 速 度 与 螺 杆 的转 速 有 直 接 关系 , 同时 也 与原 料外 形 、 密度 、 表 面 物 理性 质 有 关, 粉 状 的物料 、 密度 小 的物料 、 物料 不光 滑 、 活动 阻力 大 的物料 都会 使 进 料 速 度 变慢 , 有 时还 轻 易 产生 架桥 阻止 进料 。单 螺杆挤 压机 螺杆 的转 速直
在 单螺 杆 挤 压 机 中 , 物料传送是 拖曳 型的。 固体输 送段 中为摩 擦 拖 曳 , 熔 体 输送 段 中为 粘 性 拖 曳 。 固体 物料 的摩擦 性 能和熔 融 物料 的粘性 决
原来橡胶挤出机的机构、原理、工艺是这样的?

原来橡胶挤出机的机构、原理、工艺是这样的?橡胶挤出机挤出机的规格用螺杆的外径表示,并在前面冠以“SJ”或“XJ”,S表示塑料;X表示橡胶;J表示挤出机。
如SJ-90表示螺杆外径为90mm的塑料挤出机;而XJ-200表示螺杆外径为200mm的橡胶挤出机。
一.挤出机结构挤出机结构通常由机筒、螺杆、加料装置、机头(口型)、加热冷却装置、传动系统等部分组成。
挤出机的主要技术参数有:螺杆直径、长径比、压缩比、转速范围、螺杆结构、生产能力、功率等。
1.机筒机筒在工作中与螺杆相配合,使胶料受到机筒内壁和转动螺杆的相互作用,以保证胶料在压力下移动和混合,通常它还起热交换的作用。
为了使胶料沿螺槽推进,必须使胶料与螺杆和胶料与机筒间的摩擦系数尽可能悬殊,机筒壁表面应尽可能粗糙,以增大摩擦力,而螺杆表面则力求光滑,以减小摩擦系数和摩擦力。
否则,胶料将紧包螺杆,而无法推向前进。
(1)机筒的结构形式按结构可分为整体式和组合式两种。
(2)喂料口与旁压辊喂料口的结构与尺寸对喂料影响很大,而喂料情况往往影响挤出产量。
在喂料口侧壁螺杆的一旁加一压辊构成旁压辊喂料,此种结构供胶均匀,无堆料现象,半成品质地致密,能提高生产能力,但功率消耗增加。
2.螺杆螺杆是挤出机的主要工作部件。
它在工作中产生足够的压力使胶料克服流动阻力而被挤出,同时使胶料塑化、混合、压缩,从而获得致密均匀的半成品。
螺杆的分类:按螺纹头数分:单头、双头、三头和复合螺纹螺杆。
双头螺纹螺杆用于压型挤出;单头螺纹螺杆多用于滤胶;复合螺纹螺杆多用于塑炼等。
按螺纹方向分:有左旋和右旋两种,橡胶挤出机多用右旋螺纹螺杆。
按螺杆外型分:有圆柱形、圆锥形、圆柱圆锥复合形螺杆。
圆柱形螺杆多用于压型和滤胶;圆锥形螺杆多用于压片和造粒;复合形螺杆多用于塑炼。
按螺纹的结构形式分:普通型(如等深变距型或等距变深型),分流型(如销钉型),分离型(如副螺纹型)和复合型螺杆等。
螺杆的结构:螺杆的结构分工作部分(指螺纹部和头部)和连接部分(指尾部),工作部分直接完成挤出作业,尾部起支持和传动作用。
挤出成型:单螺杆挤出机的基本结构、成型原理、工艺与流程[专业参考]
![挤出成型:单螺杆挤出机的基本结构、成型原理、工艺与流程[专业参考]](https://img.taocdn.com/s3/m/9f17c9dd804d2b160b4ec0c7.png)
专业参考
18
机头是口模与料筒的过渡连接部分,口模是制品 的成型部件,通常机头和口模是一个整体,习惯 上统称为机头。
机头的作用为:口模为具有一定截面形状的通道. 塑料熔体在口模中流动时取得所需形状并被模外 的定型装置和冷却装置冷却硬化而成型.
机头和口模包括过滤网、多孔板、分流器、模芯、 口模、机颈
压缩比
指螺杆加料段第一个螺槽的容积与均化段最后一 个螺槽的容积之比, 表示塑料通过螺杆的全过程 被压缩的程度。
压缩比愈大,塑料受到挤压的作用也就愈大。
专业参考
12
螺槽深度h
h小,产生较高的剪切速率,有利于传 热和塑化,但挤出生产率低;
热敏性塑料(如PVC)宜用深槽螺杆 熔体粘度低和热稳定性较高的塑料(如PA
专业参考
37
熔体在均化段的流动包括四种主要形式:
(1)正流 是物料沿螺槽方向(z方向)向机头的流动, 这是均化段熔体的主流,是拖电流动,它起挤出 物料的作用;
(2)逆流 沿螺槽与正流方内相反(—z方向)的流动, 它是由机头口模、过滤网等对料流的阻碍所引起 的反压流动,它将引起挤出生产能力的损失
正流和逆流的综合称为净流,是汇流和逆流的种速 度的代数和
固体床沿挤出方向逐渐减小。
从上述的熔化实验研究可知:
(1)塑料的整个熔化过程是在螺杆熔融区进行的
(2)沿挤出方向固体床宽度逐渐减小直到为零,其减小部分被熔融所占 有
(3)沿挤出方向固体床厚度逐渐减小直到为零,其减小部分形成熔膜
(4)熔化作用发生在熔膜和固体床的界面上,有一部分发生在固相与熔
池的迁移面.
足够厚、刚度、内壁光滑、有时也刻有沟槽、 有加热装置、冷却装置、温度显示和控制装置, 一般是、电磁震荡控制
螺杆挤出机的结构和工作原理
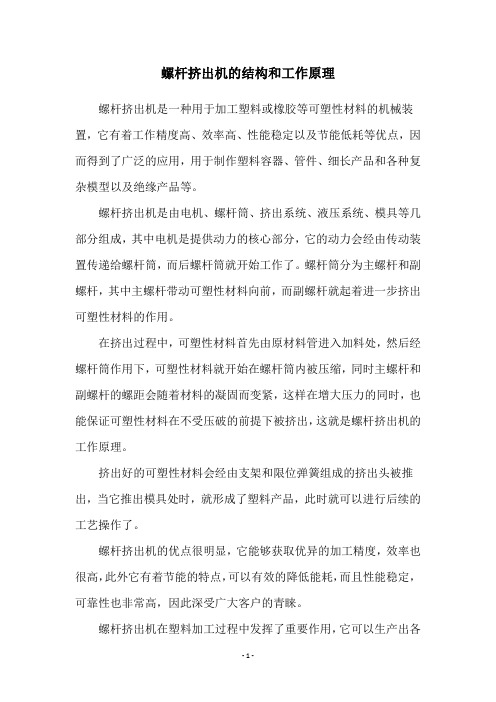
螺杆挤出机的结构和工作原理
螺杆挤出机是一种用于加工塑料或橡胶等可塑性材料的机械装置,它有着工作精度高、效率高、性能稳定以及节能低耗等优点,因而得到了广泛的应用,用于制作塑料容器、管件、细长产品和各种复杂模型以及绝缘产品等。
螺杆挤出机是由电机、螺杆筒、挤出系统、液压系统、模具等几部分组成,其中电机是提供动力的核心部分,它的动力会经由传动装置传递给螺杆筒,而后螺杆筒就开始工作了。
螺杆筒分为主螺杆和副螺杆,其中主螺杆带动可塑性材料向前,而副螺杆就起着进一步挤出可塑性材料的作用。
在挤出过程中,可塑性材料首先由原材料管进入加料处,然后经螺杆筒作用下,可塑性材料就开始在螺杆筒内被压缩,同时主螺杆和副螺杆的螺距会随着材料的凝固而变紧,这样在增大压力的同时,也能保证可塑性材料在不受压破的前提下被挤出,这就是螺杆挤出机的工作原理。
挤出好的可塑性材料会经由支架和限位弹簧组成的挤出头被推出,当它推出模具处时,就形成了塑料产品,此时就可以进行后续的工艺操作了。
螺杆挤出机的优点很明显,它能够获取优异的加工精度,效率也很高,此外它有着节能的特点,可以有效的降低能耗,而且性能稳定,可靠性也非常高,因此深受广大客户的青睐。
螺杆挤出机在塑料加工过程中发挥了重要作用,它可以生产出各
种各样形状复杂的塑料产品,并且可以满足不同强度要求,对于高强度及复杂结构的塑料产品来说,螺杆挤出机更加适用,因此在塑料加工行业中得到了广泛的应用。
总之,螺杆挤出机有着众多优点,因此越来越多的人开始使用它,未来的发展也是值得期待的。
单、双螺杆挤出机结构特点和工作原理的差异

单、双螺杆挤出机结构特点和工作原理的差异挤出成型工艺是聚合物加工领域中生产品种最多、变化最多、生产率高、适应性强、用途广泛、产量所占比重最大的成型加工方法。
挤出成型是使高聚物的熔体(或粘性流体)在挤出机螺杆的挤压作用下通过一定外形的口模成型,制品为具有恒定断面外形的连续型材。
挤出成型工艺适合于所有的高分子材料。
几乎能成型所有的热塑性塑料,也可用于热固性塑料,但仅限于酚醛等少数几种热固性塑料。
塑料挤出的制品有管材、板材、棒材、片材、薄膜、单丝、线缆包覆层、各种异型材以及塑料与其它材料的复合物等。
目前约5 0 %的热塑性塑料制品是通过挤出成型的。
此外挤出工艺也常用于塑料的着色、混炼、塑化、造粒及塑料的共混改性等,以挤出成型为基础,配合吹胀、拉伸等技术,又发展为挤出一吹塑成型和挤出拉幅成型制造中空吹塑和双轴拉伸薄膜等制品。
可见挤出成型是聚合物成型中最重要的方法。
挤出设备有螺杆挤出机和柱塞式挤出机两大类,前者为连续式挤出,后者为间歇式挤出,主要用于高粘度的物料成型,如聚四氟乙烯、超高分子量聚乙烯。
螺杆挤出机可分为单螺杆挤出机和多螺杆挤出机。
单螺杆挤出机是生产上最基本的挤出机。
多螺杆挤出机中双螺杆挤出机近年来发展最快,其应用日渐广泛。
目前,在PVC塑料门窗型材的加工中,双螺杆挤出机已成为主要生产设备,单螺杆挤出机将被逐步淘汰。
但在其它聚合物的挤出加工中,单螺杆挤出机仍占主导地位。
二者有各白的特点:单螺杆挤出机:■结构简单,价格低。
•适合聚合物的塑化挤出,适合颗粒料的挤出加工。
对聚合物的剪切降解小,但物料在挤出机中停留时间长。
■操纵轻易,工艺控制简单。
双螺杆挤出机:•结构复杂,价格高。
有很好的混炼塑化能力,物料在挤出机中停留时间短,适合粉料加工■产量大,挤出速度快,单位产量耗能低。
在PVC塑料门窗型材生产中,采用双螺杆挤出机与单螺杆挤出机的生产工艺为见页下):可以看出,单螺杆挤出机适合粒料加工,使用的原料是经造粒后的颗粒或经粉碎的颗粒料。
塑料挤出机机头结构设计

塑料挤出机机头结构设计摘要:挤出成型方法广泛应用于管材、棒材、异型材、中空制品以及单丝等产品的生产。
挤出机同时还可以对塑料进行混合、塑化、脱水、造粒、和喂料等准备工序或半成品加工。
因此挤出成型已成为最普遍的塑料成形加工方法之一。
挤出成型是在挤出机中通过加热、加压而使物料以流动状态连续通过口模成型的方法,是一种技术要求较高的成型方法。
挤出模的设计要求设计者对塑料特性的完全掌握和对挤出模具设计具有的丰富经验。
单螺杆挤出机做为应用范围最广泛的挤出机,而在设计过程中,实际遇到的问题很复杂,由于塑料的种类不同,它们的剪切速度、表面粘度不同,以及润滑剂、填充剂由于种类和配量的不同,其流动性也不同。
故挤出模的结构设计仍以实际经验为主,多数采用最终试模的方式确定其形状。
本设计中主要设计的是挤出模中各零件的工作面尺寸、外形尺寸、整体结构形式,由于塑料材质特性对于挤出模的要求非常的高,所以进行了主要零件的加工制造工艺的设计,还进行了机头和挤出主机的连接方式的设计。
关键词:挤出机;挤出模;硬质PVC;1绪论1.1挤出机的发展历程自第一台挤出机问世以来,挤出技术得到的良好快速的发展。
从开始的柱塞式到更为先进的螺杆式,从原始的手动操作到完全的自动控制,从产品单一到产品的多元化,挤出成型技术正逐渐成熟。
如今,挤出成型具有生产效率高,制造方便,可以连续化生产等特点,他、它在塑料成型加工工业中占有很重要的地位。
半个世纪以来,我国的塑料工业经历了从无到有,从小到大的发展过程,尤其是改革开放二十年来得到高速发展,已初步形成了部类齐全的工业体系,从产量上已跻身于世界先进行列。
塑料机械行业是为塑料工业提供技术装备的行业,强劲的市场需求促进塑料机械工业的发展。
挤出成型技术得到了很好的发展。
1.2挤出机的分类及挤出制品用途1.2.1 挤出机分类塑料挤出机按其螺杆数量分为单螺杆、双螺杆和多螺杆挤出机。
目前以单螺杆挤出机应用最为广泛,适宜于一般材料的挤出加工。
螺杆挤出机

一、单螺杆挤出机纳基本结构在塑料挤出机中,最基本和最通用的是单螺杆挤出机。
其基本结构如图6—1所示。
主要包:低传动、加料装盟、料筒、照扦、机头与口模等五部分。
(一)传动部分通常由电动机、减速箱和抽承等组成。
在挤出过稍中,要求螺杆转速稳定,不随螺杆负荷的变化而变化,以保证制品质量均匀一致。
但在不向的场合下,又要求螺杆能变速,以达到一台设备能适应挤出不同塑料或不同制品的要求。
为此,传动部分一殷采用交流整流子电动机、直流电动机等装置,以达无级变速,一舶绍杆转速为10一100转/分。
(二)加料装置供料一般多采用粒料,也可采用带状料或粉料。
装料设备通常都使用锥形加料斗,其容积至少应能容纳一小时的用料。
料斗底部有截断装置,以便调整和切断料流,料斗侧面有视孔和标定计量的装置。
有些料斗并带有可防止原料从空气中吸收水分朗真空(减压)装置或加热装置,有些料斗有搅拌器,并能自动上料或加料。
(三)料简为一金属圆筒,一般用耐温耐压强度较高、坚固耐磨、耐腐的合余钢或内衬合金钢的复合钢管制成。
一般料筒的长度为其直径的15—30倍,其长度以使物料得到充分加热和塑化均匀为原则。
料筒应有足够厚度、刚度。
内壁应光滑,有些料简则刻有各种沟槽,以增大与塑料的摩擦力。
在料筒外部附有用电阻、电感或其它方式加热的加热器、温度自控装置及冷却(风冷或水冷等)系统。
(四)螺杆螺杆是挤出机最主要部件,它直接关系到挤出机的应用范围和生产率。
通过螺杆的转动对塑料产生挤压作用,塑料在料简中才能产生移动、增压和从摩擦取得部分热量,塑料在移动过程中并得到混合和塑化,粘流态的熔体在被压实而流经口模时,取得所需形状而成型。
与料筒一样,螺杆也是用高强度、耐热和耐腐蚀的合金钢制成。
由于塑料品种很多,性质各异;因此为适应加工不同塑料的需要,螺杆种类很多,结构上也有些差别,以便能对塑料产生较大的输送、挤压、混合和塑化作用。
困6—2为几种较常螺杆。
表示螺杆结构特征的基本参数有直径、长径比、压缩比、螺距、螺槽深度、螺旋角、螺杆与料筒的间隙等。
塑料型材挤出螺杆、螺筒介绍

%
200
150
100
50
0 -4
侧角
-2 0 2 4 6 8 10 支承面 % 螺纹宽度 % 磨损率%
被动式螺杆温度控制系统 热传导原理
液体介质 的蒸发
能量传导通过液 体介质的蒸发和 冷凝实现
冷凝为液体
以水为主的液体介质的 热传导原理
主动式螺杆温度控制系统(油介质)
螺杆的油封
•油封部分为陶瓷涂覆 保证了密封系统的工 作寿命.
出。 2、另一种是位置一直在型材的下表面断续线装或云纹
状,这主要原因是: (1)随着运行周期的加长,造成的螺杆和螺筒磨损严重,这
时要进行抛光和间隙重新调整,严重时要更换; (2)原料润滑系统失衡,可以切换成后期外润滑(如PE等)或适
当加大用量; (3)适当增加稳定剂的量。
目前我公司产生型材黑线的挤出机主要有两种情况: 由于计量段螺杆、螺筒磨损严重,螺棱表面的硬质镀层