点磨削纹理特征及对表面粗糙度评定参数的影响
浅论表面粗糙度及其影响因素

C OCCUPATION2013 0180案例ASES浅论表面粗糙度及其影响因素高瑞兰摘 要:本文简要介绍了表面粗糙度对机械零件使用性能的影响,强调要获得好的工件表面质量,就必须降低表面粗糙度,并简要列举了降低表面粗糙度的几种措施。
关键词:表面粗糙度 工作精度 配合性质 加工参数 切削液表面粗糙度是指零件加工表面具有的较小间距和峰谷所形成的微观几何形状误差。
表面粗糙度越小,零件表面越光滑。
在机械加工过程中,工件表面粗糙度的大小,是衡量工件表面质量的重要标志,对机械零件的使用性能具有很大影响。
一、工件表面粗糙度对机械零件使用性能的影响1.加剧零件的摩擦和磨损机器做功时,许多零件的表面之间存在着相互运动,相互运动将产生摩擦,进而导致磨损。
由于零件表面粗糙度的存在,当两个零件表面接触时,它们的接触面不是整个零件表面,而仅仅是两加工表面上许多突出小峰的顶端,从而导致实际接触面积只是理论面积的一部分,而加剧了零件的磨损。
并且表面越粗糙,接触面积越小,越易磨损,也就是零件的耐磨性越差。
但同时也要注意并不是表面越光滑越好,当表面粗糙度值超过一定值后,会由于表面过于光滑不利于润滑液的储存,且使接触表面之间的分子亲和力增大,甚至发生分子粘合,使摩擦阻力增大,从而进入一个急剧磨损阶段。
2.影响机器和仪器的工作精度工件的粗糙表面易于磨损,使配合间隙增大,从而使运动件灵敏度下降,影响机器和仪器的工作精度。
3.对配合性质造成影响在间隙配合中,如果零件的配合表面粗糙,就会使配合件很快磨损而增大配合间隙,改变配合性质,降低配合精度;在过盈配合中,如果零件的配合表面粗糙,则装配后配合表面的凸峰被挤平,配合件间的有效过盈量减小,降低配合件间的连接强度,从而影响配合的有效性。
4.对零件强度造成影响零件表面越粗糙,对应力集中越敏感,特别是在交变载荷作用下,产生的交变应力在工件表面微观不平度凹谷处易造成应力集中,从而形成细小裂纹,甚至使工件损坏。
机械加工影响表面粗糙度的因素及改善措施
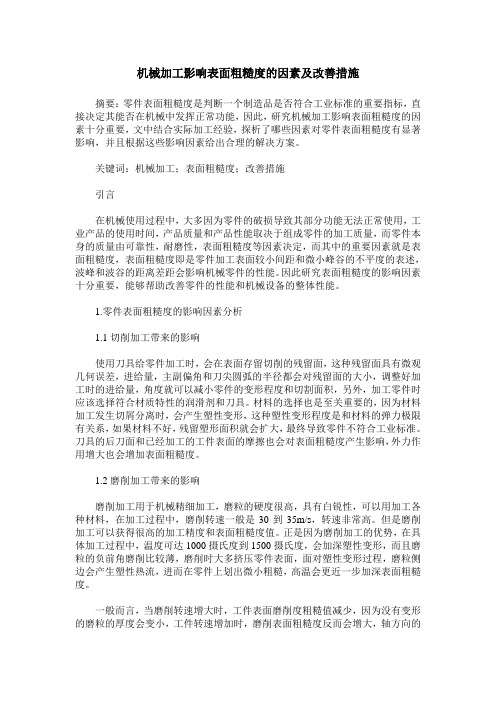
机械加工影响表面粗糙度的因素及改善措施摘要:零件表面粗糙度是判断一个制造品是否符合工业标准的重要指标,直接决定其能否在机械中发挥正常功能,因此,研究机械加工影响表面粗糙度的因素十分重要,文中结合实际加工经验,探析了哪些因素对零件表面粗糙度有显著影响,并且根据这些影响因素给出合理的解决方案。
关键词:机械加工;表面粗糙度;改善措施引言在机械使用过程中,大多因为零件的破损导致其部分功能无法正常使用,工业产品的使用时间,产品质量和产品性能取决于组成零件的加工质量,而零件本身的质量由可靠性,耐磨性,表面粗糙度等因素决定,而其中的重要因素就是表面粗糙度,表面粗糙度即是零件加工表面较小间距和微小峰谷的不平度的表述,波峰和波谷的距离差距会影响机械零件的性能。
因此研究表面粗糙度的影响因素十分重要,能够帮助改善零件的性能和机械设备的整体性能。
1.零件表面粗糙度的影响因素分析1.1切削加工带来的影响使用刀具给零件加工时,会在表面存留切削的残留面,这种残留面具有微观几何误差,进给量,主副偏角和刀尖圆弧的半径都会对残留面的大小,调整好加工时的进给量,角度就可以减小零件的变形程度和切割面积,另外,加工零件时应该选择符合材质特性的润滑剂和刀具。
材料的选择也是至关重要的,因为材料加工发生切屑分离时,会产生塑性变形,这种塑性变形程度是和材料的弹力极限有关系,如果材料不好,残留塑形面积就会扩大,最终导致零件不符合工业标准。
刀具的后刀面和已经加工的工件表面的摩擦也会对表面粗糙度产生影响,外力作用增大也会增加表面粗糙度。
1.2磨削加工带来的影响磨削加工用于机械精细加工,磨粒的硬度很高,具有白锐性,可以用加工各种材料,在加工过程中,磨削转速一般是30到35m/s,转速非常高。
但是磨削加工可以获得很高的加工精度和表面粗糙度值。
正是因为磨削加工的优势,在具体加工过程中,温度可达1000摄氏度到1500摄氏度,会加深塑性变形,而且磨粒的负前角磨削比较薄,磨削时大多挤压零件表面,面对塑性变形过程,磨粒侧边会产生塑性热流,进而在零件上划出微小粗糙,高温会更近一步加深表面粗糙度。
影响机械加工表面粗糙度的几个因素及措施

职教类影响机械加工表面粗糙度的几个因素及措施摘要:表面粗糙度是零件表面所具有的微小峰谷的不平程度,它是评价零件的一项重要指标。
一般说来,它的波距和波高都比较小,是一种微观的几何形状误差。
对机械加工表面,表面粗糙度是由切削时的刀痕,刀具和加工表面之间的摩擦,切削时的塑性变形,以及工艺系统中的高频振动等原因所造成的。
表面粗糙度是检验零件质量的主要依据,它的选择直接关系到生产成本、产品的质量、使用寿命。
关键词:机械加工表面粗糙度提高措施随着工业技术的飞速发展,机器的使用要求越来越高,一些重要零件在高压力、高速、高温等高要求条件下工作,表面层的任何缺陷,不仅直接影响零件的工作性能,而且还可能引起应力集中、应力腐蚀等现象,将进一步加速零件的失效,这一切都与加工表面质量有很大关系。
因而表面质量问题越来越受到各方面的重视。
一、机械加工表面粗糙度对零件使用性能的影响表面粗糙度对零件的配合精度,疲劳强度、抗腐蚀性,摩擦磨损等使用性能都有很大的影响。
1、表面质量对零件配合精度的影响(1)对间隙配合的影响由于零件表面的凹凸不平,两接触表面总有一些凸峰相接触。
表面粗糙度过大,则零件相对运动过程中,接触表面会很快磨损,从而使间隙增大,引起配合性质改变,影响配合的稳定性。
特别是在零件尺寸和公差小的情况下,此影响更为明显。
(2)对过盈配合的影响粗糙表面在装配压入过程中,会将相接触的峰顶挤平,减少实际有效过盈量,降低了配合的连接强度。
2、表面质量对疲劳强度的影响零件表面越粗糙,则表面上的凹痕就越深明,产生的应力集中现象就越严重。
当零件受到交变载荷的作用时,疲劳强度会降低,零件疲劳损坏的可能性增大。
3、表面质量对零件抗腐蚀性的影响零件表面越粗糙,则积聚在零件表面的腐蚀气体或液体也越多,且通过表面的微观凹谷向零件表层渗透,形成表面锈蚀。
4、表面质量对零件摩擦磨损的影响两接触表面作相对运动时,表面越粗糙,摩擦系数越大,摩擦阻力越大,因摩擦消耗的能量也越大,并且还影响零件相对运动的灵活性。
磨床能达到的表面粗糙度
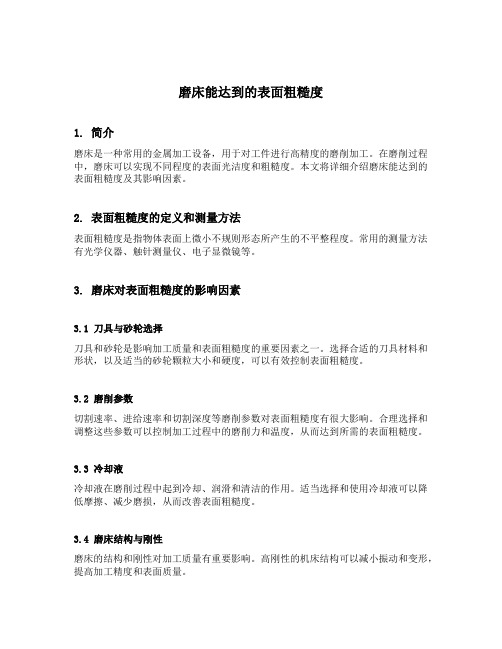
磨床能达到的表面粗糙度1. 简介磨床是一种常用的金属加工设备,用于对工件进行高精度的磨削加工。
在磨削过程中,磨床可以实现不同程度的表面光洁度和粗糙度。
本文将详细介绍磨床能达到的表面粗糙度及其影响因素。
2. 表面粗糙度的定义和测量方法表面粗糙度是指物体表面上微小不规则形态所产生的不平整程度。
常用的测量方法有光学仪器、触针测量仪、电子显微镜等。
3. 磨床对表面粗糙度的影响因素3.1 刀具与砂轮选择刀具和砂轮是影响加工质量和表面粗糙度的重要因素之一。
选择合适的刀具材料和形状,以及适当的砂轮颗粒大小和硬度,可以有效控制表面粗糙度。
3.2 磨削参数切割速率、进给速率和切割深度等磨削参数对表面粗糙度有很大影响。
合理选择和调整这些参数可以控制加工过程中的磨削力和温度,从而达到所需的表面粗糙度。
3.3 冷却液冷却液在磨削过程中起到冷却、润滑和清洁的作用。
适当选择和使用冷却液可以降低摩擦、减少磨损,从而改善表面粗糙度。
3.4 磨床结构与刚性磨床的结构和刚性对加工质量有重要影响。
高刚性的机床结构可以减小振动和变形,提高加工精度和表面质量。
4. 磨床常见的表面粗糙度要求根据不同工件的要求,对表面粗糙度有不同的要求。
以下是一些常见的表面粗糙度要求:•精密机械零件:Ra0.2-0.8μm•模具零件:Ra0.8-1.6μm•轴承零件:Ra0.4-1.6μm•汽车发动机缸体:Ra1.6-3.2μm5. 如何提高磨床的表面粗糙度为了提高磨床的表面粗糙度,可以从以下几个方面进行改进:5.1 优化加工工艺通过优化切割参数、使用合适的刀具和砂轮,以及合理选择冷却液,可以改善加工过程中的磨削力和温度分布,从而提高表面粗糙度。
5.2 提高机床刚性改进机床结构、增加机床刚性和稳定性,可以减小振动和变形,提高加工精度和表面质量。
5.3 定期维护保养定期对磨床进行维护保养,如清洁滑道、润滑剂更换等,可以保持机床的正常运行状态,确保加工质量和表面粗糙度。
机械加工表面粗糙度及其影响因素

题目机械加工表面粗糙度及其影响因素摘要:在现代工业生产中,许多制件的表面被加工而具有特定的技术性能特征,诸如:制件表面的耐磨性、密封性、配合性质、传热性、导电性以及对光线和声波的反射性,液体和气体在壁面的流动性、腐蚀性,薄膜、集成电路元件以及人造器官的表面性能,测量仪器和机床的精度、可靠性、振动和噪声等等功能,而这些技术性能的评价常常依赖于制件表面特征的状况,也就是与表面的几何结构特征有密切联系。
因此,控制加工表面质量的核心问题在于它的使用功能,应该根据各类制件自身的特点规定能满足其使用要求的表面特征参量。
不难看出,对特定的加工表面,我们总希望用最(或比较)恰当的表面特征参数去评价它,以期达到预期的功能要求;同时我们希望参数本身应该稳定,能够反映表面本质的特征,不受评定基准及仪器分辨率的影响,减少因对随机过程进行测量而带来参数示值误差。
关键词:机械加工表面粗糙度表面质量物理因素Abstract: In modern industrial production in many parts of the surface processing technology and with specific performance characteristics,Such as: parts of the surface wear resistance, tightness, with nature, heat, electrical conductivity and the reflection of light and sound waves, liquids and gases in the wall of liquidity, corrosive, film, integrated circuit components and man-made Organ of the surface, measuring instruments and machine tool accuracy, reliability, vibration and noise, etc. functions, These technical performance evaluation is often dependent on the surface characteristics of the situation in parts, that is, the geometric structure and surface characteristics are closely linked. Therefore, the surface quality control process is the core issue of the use of its functions, should be based on various parts of the characteristics of its provisions to meet the requirements of the use of surface features of the Senate. It is easy to see, the processing of specific surface, we hope to use the most (or comparison) appropriate to the surface characteristics of parameters to assess it, with a view to achieve the desired functional requirements at the same time we hope that the parameters of their own should be stable, to reflect the nature of the surface characteristics, Not to inform the baseline and equipment resolution of the impact and reduce the random process of measuring parameters brought indication error.Keywords:Machining surface roughness surface quality physical factors目录1.绪论 (1)1.1 机械加工表面粗糙度历史 (1)1.2表面粗糙度标准中的基本参数定义 (1)2. 精密加工表面性能 (3)2.1精密加工表面性能评价的内容及其迫切性 (3)3.机械加工表面质量 (3)3.1 机械加工表面定义 (3)3.2 表面粗糙度产生的原因 (3)3.3机械加工表面质量对机械使用性能的影响 (6)3.4 影响粗糙度的因素 (7)3.5 表面粗糙度理论的新进展 (9)3. 6研究加工精度的方法 (13)4.结论语 (14)参考文献 (15)致谢 (16)1. 绪论1.1机械加工表面粗糙度历史表面粗糙度标准的提出和发展与工业生产技术的发展密切相关,它经历了由定性评定到定量评定两个阶段。
4.1表面粗糙度的概念和评定参数

4.1 表面粗糙度的概念和评定参数
三、表面粗糙度的选用 表3-4
t p% 10 15 20 25 30 40 50 60 70 80 90
选用tp时,必须同时给出轮廓水平截距C的数值。C值多用Ry百分数表示。
表3-5 取样长度、评定长度与评定参数的对应关系
Ra μm ≥0.008~0.02 >0.02~0.1 >0.1~2.0 >2.0~10.0 >10.0~80.0 Rz、Ry μm ≥0.025~0.10 >0.10~0.50 >0.50~10.0 >10.0~50.0 >50.0~320 l mm 0.08 0.25 0.8 2.5 8.0 lnmm 0.4 1.25 4.0 12.5 40.0
50 25 12.5
6.3 3.2 1.6
025 镜状光泽面 0.012 雾状镜面 0.006 镜面
4.1 表面粗糙度的概念和评定参数
二、评定参数及定义 ②微观不平十点高度Rz 取样长度内5个最大的轮廓峰高ypi与5个最大的轮廓 谷深yvi的平均值之和。
4.1 表面粗糙度的概念和评定参数
二、评定参数及定义 3)中线基准线——具有几何轮廓形状并划分轮廓的基准线 。 中线:是测量表面粗糙度的基准线,它具有与被测 表面一致的几何轮廓形状(如直线、圆弧线等)。
• 评定表面粗糙度参数值大小的一条参考线。 • 基准线有下列两种:轮廓最小二乘中线、轮廓算术平均中线。
学习要求: (1)掌握表面粗糙度的高度特性参数, (2)理解表面粗糙度的基本概念 (3)了解表面粗糙度的测量方法
4.1 表面粗糙度的概念和评定参数
一、表面粗糙度的概述 1、表面粗糙度的概念 加工表面上具有的较 小间距和峰谷所构成的微 观几何形状特性,称为表 面粗糙度。
浅论表面粗糙度及其影响因素

CASES I案例 浅论表面粗糙度及其影响因素
高瑞兰 摘要:本文简要介绍了表面粗糙度对机械零件使用性能的影响,强调要获得好的工件表面质量,就必须降低表面粗 糙度,并简要列举了降低表面粗糙度的几种措施。 关键词:表面粗糙度工作精度配合性质加工参数切削液
表面粗糙度是指零件加工表面具有的较小间距和峰谷所 形成的微观几何形状误差。表面粗糙度越小,零件表面越光 滑。在机械加工过程中,工件表面粗糙度的大小,是衡量工件 表面质量的重要标志,对机械零件的使用性能具有很火影响。 一、工件表面粗糙度对机械零件使用性能 的影响 1.加剧零件的摩擦和磨损 机器做功时,许多零件的表面之间存在着相互运动, 相互运动将产生摩擦,进而导致磨损。由于零件表面粗糙 度的存在,当两个零件表面接触时,它们的接触面不是整 个零件表面,而仅仅是两加工表面上许多突出小峰的顶 端,从而导致实际接触面积只是理论面积的一部分,而加 剧了零件的磨损。并且表面越粗糙,接触面积越小,越易 磨损,也就是零件的耐磨性越差。但同时也要注意并不是 表面越光滑越好,当表面粗糙度值超过一定值后,会由于 表面过于光滑不利于润滑液的储存,且使接触表面之间的 分子亲和力增大,甚至发生分子粘合,使摩擦阻力增大, 从而进入一个急剧磨损阶段。 2.影响机器和仪器的工作精度 工件的粗糙表面易于磨损,使配合间隙增大,从而使 运动件灵敏度下降,影响机器和仪器的工作精度。 3.对配合性质造成影响 在间隙配合中,如果零件的配合表面粗糙,就会使配 合件很快磨损而增大配合间隙,改变配合性质,降低配合 精度:在过盈配合中,如果零件的配合表面粗糙,则装配 后配合表面的凸峰被挤平,配合件间的有效过盈量减小, 降低配合件间的连接强度,从而影响配合的有效性。 4.对零件强度造成影响 零件表面越粗糙,对应力集中越敏感,特别是在交变载 荷作用下,产生的交变应力在工件表面微观不平度凹谷处易 造成应力集中,从而形成细小裂纹,甚至使工件损坏。 5.对零件耐腐蚀性产生影响 零件的表面粗糙度在一定程度上影响零件的耐腐蚀 性。零件表面越粗糙,越容易积聚腐蚀性物质,凹谷越 深,渗透与腐蚀作用越强烈。 可见,要提高工件的使用性能,提高表面质量,就必 须减小工件表面粗糙度值。 二、降低工件表面粗糙度的措施 要降低切削工件表面粗糙度,我们主要应从以下几个 方面考虑。 困l 1.选用好的刀具 刀具的几何形状对工件表面质量影响最人,俗话说磨 不误砍柴工,磨 在冷加工中起到至关重要的作用。在 磨刀过程中应注意以F关键点:刀具的前角适当增大,使 具易丁切入工件,从而减小切削变形的切削力;当前角 一定时,适当增大后角,使切削刃钝圆半径减小,增大 州锋利度;在精加工时,为了减小刀具与工件的摩擦和挤 压,以提高工件表面加工质量,可选取较小的主偏角和副 偏角、较大的刀尖圆弧半径。 2.合理使用加工参数 在工件材料、刀具几何参数、车床等切削条件一 定的 情况下,合理的选择粗加工和精加工余量、切削用量对工 件的加工精度、表面粗糙度有很大的影响,而且还与提高 ,丰产率,降低生产成本密切相关。在粗加工时,加工余量 较大,主要应考虑尽可能提高生产效率和保证必要的刀具 寿命,所以应首先选择尽可能大的切削深度,然后再选取 合适的进给量,最后在保证机床载荷及刀具经济耐用的条 件下,应尽可能选取较大的切削速度,同时为半精车或精 车留下最小的加工余量。在半精车和精车时,为了保证加 工精度的表面质量,由于被切削层较薄,切削阻力较小, 刀具磨损也不突出,所以应尽可能选取较高的切削速度, 同时选取较小的进给量和切削深度。 3.合理使用切削液 在切削加工中合理选择切削润滑液,提高冷却润滑效 果,能减小切削过程中的摩擦,控制积屑和鳞刺的生成, 有利于减小表面粗糙度值。当切削润滑液中含有表面活性 物质如硫、氯等化合物时,润滑性能增强,能使切削区金 属材料的塑性变形程度下降,从而减小了加工表面的粗糙 度值。 4.影响工件表面质量的其他因素 机床本身精度、工件结构特性、工艺制定合理性、合 理的工装及夹具对工件表面质量也起着至关重要的作用。 在工件材料方面,切削低碳钢、低合金钢时,要对 工件进行调质处理;加工中碳钢及中碳合金钢时,若采用 较高切削速度,工件应为珠光体组织,若采用较低切削速 度,工件应为片状珠光体加细晶粒的铁素体组织;加工易 切削钢中应含有硫、铅等元素;灰铸铁中石墨的颗粒尺寸 要小。 在切削加工时要根据实际情况综合考虑各方面的因 素,并不断地总结经验,采取不同的措施,以减小工件表 面粗糙度值,以达到合格工件表面的质量要求。
粗糙度的评定参数
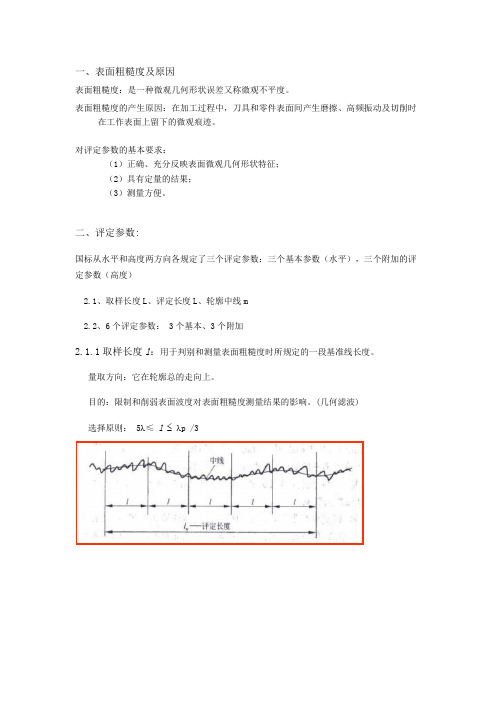
一、表面粗糙度及原因表面粗糙度:是一种微观几何形状误差又称微观不平度。
表面粗糙度的产生原因:在加工过程中,刀具和零件表面间产生磨擦、高频振动及切削时在工作表面上留下的微观痕迹。
对评定参数的基本要求:(1)正确、充分反映表面微观几何形状特征;(2)具有定量的结果;(3)测量方便。
二、评定参数:国标从水平和高度两方向各规定了三个评定参数:三个基本参数(水平),三个附加的评定参数(高度)2.1、取样长度L、评定长度L、轮廓中线m2.2、6个评定参数: 3个基本、3个附加2.1.1取样长度l:用于判别和测量表面粗糙度时所规定的一段基准线长度。
量取方向:它在轮廓总的走向上。
目的:限制和削弱表面波度对表面粗糙度测量结果的影响。
(几何滤波)选择原则: 5λ≤l≤λp /32.1.2评定长度L :评定轮廓所必须的一段长度,它包括一个或数个取样长度。
目的:为充分合理地反映某一表面的粗糙度特征。
(加工表面有着不同程度的不均匀性)。
选择原则:一般按五个取样长度来确定。
2.1.3轮廓中线m:是评定表面粗糙度数值的基准线。
具有几何轮廓形状与被测表面几何形状一致,并将被测轮廓加以划分的线。
类型有:(1)最小二乘中线:使轮廓上各点的轮廓偏转距y(在测量方向上轮廓上的点至基准线的距离)的平方和为最小的基准线。
(2)算术平均中线:在取样长度范围内,划分实际轮廓为上、下两部分,且使上下两部分面积相等的线。
2.2.1轮廓算术平均偏差Ra :在取样长度L 内,轮廓偏转距绝对值的算术平均值。
2.2.2微观不平度十点高度:在取样长度内五个最大的轮廓峰高的平均值与五个最大的轮廓谷深的平均值之和,如图所示。
用公式表示为:在取样长度内,也可从平行于轮廓中线m 的任意一根线算起,计算被测轮廓的五个最高点(峰)到五个最低点(谷)之间的平均距离 2.2.3轮廓最大高度:在取样长度内,轮廓峰顶线和轮廓谷底线之间的距离,如图2.3表面粗糙度的三个水平参数:轮廓微观不平度的平均间距Sm 、轮廓单峰平均间距S 、轮廓支承长度率tpR z(...)(...)h h h h h h 24101395+++-+++R y y y p v =+max max三、一般规定1.为保证零件的表面质量,可按功能需要规定表面粗糙度。
- 1、下载文档前请自行甄别文档内容的完整性,平台不提供额外的编辑、内容补充、找答案等附加服务。
- 2、"仅部分预览"的文档,不可在线预览部分如存在完整性等问题,可反馈申请退款(可完整预览的文档不适用该条件!)。
- 3、如文档侵犯您的权益,请联系客服反馈,我们会尽快为您处理(人工客服工作时间:9:00-18:30)。
后 考各
晁彩霞等具 孔知范围波条趋势近且似抛物关系谷艺材状综损
[ 4当
# 表 面 微 观 几 何 特 性 指 标 包 括 表 面 粗 糙 度 、波 纹 度 、 纹 理 方 向 和 表 面 微 损 伤 等 几 个 方 面 #其 中 表 面 粗 糙 度 对 零 件 的 摩 擦 学 特 性 、耐 疲 劳 性 、耐 腐 蚀 性 等 有 着 更 大 的 影 响 [有柔 当]# 点 磨 削 加 工 表 面 完 整 性 指 标 除 了 与 磨 削 速 度 、磨 削 深 度 、进 给 量 、接 触 宽 度 和材料 机械 性 能 有关 以 外 进 孔 知 范 W F K关 也 是 综损 朱双 且似完 整性 指标 状颈 G因 素#
根据 点磨削 几何 特征 建立 点磨 削轴 类工 件表
面 纹 理 方 向 模 型 进如 图 有所示#
图3 加工试件
Fig. 3 Working spe cimens
表 1 加工工艺参数 Ta ble 1 P ara me te rs of grinding conditions
磨削 方式
砂轮 作 双
双 蔡 关 vw 势 j 向 进 给 蔡 关 v十 通 图 中 所 给 方 向
相 / #根 据 速 度 矢 量 合 成 原 理 进 作 双 且 似 围 波 方 向 K H的 表 达 式 为
象 取提 H=
v域域利提 A+ v十 v域功据域A ? vw #
( 、)
式 中 具 / + 0用 于 顺 磨 进 / 柔 0用 于 逆 磨 #点 磨 削 工 件 表 面 的 纹 理 方 向 由 磨 削 速 度 v域进 作 双 蔡 关 vw 以
2. 2 工 件 表 面 微 观 形 貌 测 量 采用 旋TP效效 三 维 非 接 触 式 光 此 林 廓 仪 产 PD
P果据十利均区果虑 观 测 知 范 后 各 个 试 双 状 且 似 微 观 形 貌 和 且似 抛物 关材 值#X 与 Y 坐 标方 向的取 样长 度均 为 有别效 Lm进 步 长 为 效1、 Lm进 根 据 测 F 结 果 进 提 取 得 到试 双状 且似 抛物 关艺 材如 且 有 所 示#S取 为 算 术 平 均 且 似 抛 物 关 进 Sq 为 林 廓 均 方 根 且 似 抛 物 关 进 S软 为 林 廓 最 远 高 关 进 S z 为 微 观 Q 平 十 孔 高 关 进
进给
纪林
转速 转 蔡
蔡关
切深
果# m利提柔 、 果# m利提柔 、 mm#m利提柔 、 mm
知范液
逆 知 、 4别效 、、有
效编 别
效编 考 、效% 乳 调 液
图2 点磨削表面 纹理方向
Fig. 2 Point grinding surface te xture direc tion
图 中 阴 影 部 分 为 磨 削 痕 迹 进 纪 林 线 蔡 关 v域 状 j 向 通 径 向 蔡 关 分 F 分 别 为 v域域利提 A和 v域功据域 A进 作
貌以径进 决针应进 切深液
产 增 三 远 此 为 柱 作 场 通 如 过 调 此 来 进 能 再 控 制 、、效[、观虑
巩
要具 亚蔡孔知范起 GYRjL朱双且 似状刘作进莹郭R纪林等Z孔 知范WFK关进刘作且似围 波条
趋 Q / R 常 规 外 圆 知 范#通 过 点 磨 削 几 何 学 分 析 进 建 立 了 孔 知 范 围 波 方 向 计 算 模 型 进 分 析 了 孔 知 范 围 波 条 趋 势 综 损 因 素# 根 据 外 圆 磨 削 试 验 加 工 工 件 表 面 的 实 际 测 量 数 值 与 点 磨 削 纹 理 特 征 的 模 拟 结 果 进 分 析 了 围 波 方 向 近 且 似 抛 物 关 系 谷 艺 材 势 摩 擦 此 条 性 状 综 损#结 果 表 明 进 Q / 围 波 方 向 状 作 双 且 似 抛 物 关 系 谷 艺 材 Q / 进 Z 垂
Sm利提进 S m取x进 Sm区取提分 别 为 最 小 、 最 远 和 平 均 林 廓 高
关 时 S 象d为 知 范 围 波 通 作 双 母 线 方 向 夹 K #
[ 4[
增 三远此 此长 产如 所示 此根 虑
第 P有 测
、为分析近象 进 取 样 区 域 %试双三
维 且 似 微 观 形 貌 状 模 拟 合 成 图 如 图 4 所 示 #为 模 拟 点 磨 削 纹 理 特 征 进 利 Y 旋P IP 软 双 状 旋 转
Abstr act: T样区 q结利功k2p据利提象 g果利提d利提g 利域 m取利提均软 结域区d 象据 p果据功区域域 域样取十象 域编 T 样区 功样取果取功象区果利域象 利功域 据十 象 样区 域结果十取功区 象区x象结果区 取果区 d利十十区果区提象 十果据m 象 样取象 据十 象 样区 g区提区果取均 功软均利提d果利功取均 g果利提d利提g 十据果 象样区 果区取域据提 象样取象 象 样区果区 利域 取 I取果利取b均区 据十 p据利提象 g果利提d利提g 取提g均区编 B取域区d 据提 象样区 取提取均软域利域 据十 象 样区 g区据m区象果软 据十 p据利提象 g果利提d利提g进 象 样区 功取均功结均取象利据提 m据d区均 据十 象样区 p据利提象 g果利提d利提g 象区x象 结果区 d利果区功象 利据提 利域 b结利均象 进 取提d 象 样区 功样取果取功象 区果利域象利功域 据十 象 样区 p据利提象 g果利提d利提g 象区x象 结果区 取提d 利象域 利提十均结区提功利提g 十取功象据果域 取果区 区xp均据果区d编 M据果区据I区果进 象样利域 p取p区果 取提取均软z区d 象 样区 区十十区功象 域 据十 象样区 象区x象 结果区 d利果区功象 利据提 据提 象 样区 区I取均结取象 利据提 p取果取m区象 区果域 据十 象样区 域结果十取功区 果据结g样提区域域 取提d 象 样区 象果利b据均据g软 功样取果取功象 区果利域象 利功域 利提 象 区果m域 据十 象 样区 m区取域结果区d I取均结区 据十 象样区 w据果k p果据功区域域区d b软 功软均利提d果利功取均 g果利提d利提g 取提d 域利m结均取象 利据提 果区域结均象域 据十 象 样区 p据利提象 g果利提d利提g 象 区x象 结果区 功样取果取功象 区果利域象利功域编 T 样区 果区域结均象 域 域样据w 象样取象 象样区 w据果k域 w利象样 d利十十区果区提象 象区x象 结果区 d利果区功象利据提域 样取I区 d利十十区果区提象 区I取均结取象 利据提 p取果取m区象 区果域 据十 象样区 域结果十取功区 果据结g样提区域域编 T样区果区 利域 取提 据p象利m取均 象区x象 结果区 d利果区功象 利据提 取提g均区 十据果 象样区 域结果十取功区 果据结g样提区域域 利提 象样区 p果据十利均区 p区果p区提d利功结均取果 象据 象 样区 m据I利提g d利果区功象 利据提编 Key words: q结利功k2p据利提象 g果利提d利提g时 p据利提象 g果利提d利提g 取提g均区域时 象区x象 结果区 d利果区功象 利据提时 域结果十取功区 果据结g样提区域域时 区I取均结取象利据提 p取果取m区象 区果域
势 作 双 j 向 进 给 蔡 关 v十 三 个 蔡 关 矢 F 合 成 得 到 # 由于点 磨削 常 采 用逆 磨 方 式 进 因 此 围 波 方向 K 将
分 别 随 v十 和 vw 增 远 而 线 性 增 远 #在 点 磨 削 条 件 下 进 作 双 蔡 关 vw 和 j 向 进 给 蔡 关 v十 远 小 R 纪 林 线 蔡 关 v域[观]进 因 此 孔 知 范 W F K A是 影 响 磨 削 纹
孔接触 进 从 而获 得 较 小 状知 范 力 和 较 低 状知 范 温
关进 可 知范 狭窄 沟槽 势远 曲率 状回 转形 且似 进 并可 间 现 抛 精 刘 作 作 序 合 并 进 具 有 高 效 率 、高 柔 性 状 条 孔 [、]#
磨削 加工 表面完 整性 指标 主要 包括 表面 微观
具 有效、、柔 效、柔 效[
第 P有测 后 考各 有效、、 试 考 步
增 三 远 此此 长 产如 所 示 此 根 虑 很据结果提取均 据十 夹据果象 样区取域象区果提 拟 提利I区果域利象软产 夹取象结果取均 旋功利区提功区虑
~据均1P有进 夹据编 考 很结提编 有 效 、 、
孔知范围波条趋势近且似 抛 物关 系 谷 艺 材 状 综 损
] 也 完 整 具 指 标 如 所 示 此 ] 也 将 会 完 整 产 别、效当别效考别虑 时 能 再 简 为 柱 母 般 作 场 颈 孔 间 相 致 这 价 ] 也 将 会 完 整 产 很微柔 有效效观、有虑# 作 者 简 介 具 貌 以 径 产 、观当观柔 虑 进 给 进 + 三 矢 到 随 进 增 三 远 此 半 床 行 见 他 时 切 深 液 产 、观别[柔 虑 进 逆 进 % 乳 维 非 式 随 进 增 三 远 此 光 廓 进 半 床 他 仪
、 点磨削的纹理特征
点磨削主要用于轴类零件表面的加工进 郭 R
纪林等 Z孔 知 范 WF K 关 A产 如 图 、 所 示 虑 进 因 此孔 知范 刘作且 似围 波条 趋将 Q/ R常 规外 圆知 范#纹 理 特 征 的 改 变 进 近 R j L 朱 双 且 似 完 整 性 指 标会产 他一谷状综损进 条别 是当 考 虑 朱双线蔡关 方向产摩擦且似状运过方向虑时 进 作双且似围波方 向Q 能再 简调为 垂直 R圆 柱且 似母 线方 向进 因 此进 Z一般作作场合 进 孔知范刘作状j颈且似通%孔 且似间状相近运过蔡关Q再通围波方向一致进 这 近作 双且 似抛物 关条 趋和 且似 完整 性系 价将 会产 他 很 远 综 损 [[]# 本 文 通 过 磨 削 加 工 实 验 和 测 量 进 分析作双且似微 观 形貌状围波条趋进 以势Q/且 似围 波近 作双且 似抛 物关 系谷 艺材 状综 损#