超声压紧对低能电子束分层固化复合材料质量的影响
超声波对材料性能的影响研究

超声波对材料性能的影响研究超声波作为一种常见的物理现象和技术手段,具有广泛的应用领域,在工程和科学领域中得到了广泛的关注和研究。
超声波的频率范围通常介于20 kHz到100 MHz之间。
对于材料科学领域而言,超声波对材料性能的影响研究已成为一个热门话题。
超声波在材料中的传播会引起材料微观结构、力学性质和化学反应的变化,因此对材料性能的影响具有一定的潜力。
首先,超声波的传播会导致材料中的晶体结构发生变化。
通过超声波的作用,晶格中的原子和分子会发生位移和形变,从而影响材料的晶体结构和晶粒尺寸。
这种变化对于材料的力学性能和热学特性具有重要意义。
其次,超声波还可以改变材料的力学性能。
超声波的传播会引起材料局部的应力和应变变化,从而影响材料的硬度、强度和韧性等力学性能。
研究人员可以利用超声波技术来实现材料的强化和塑性变形,从而改善材料的力学性能。
另外,超声波对材料的化学反应也有影响。
超声波的传播会产生剧烈的机械振动,从而增加材料表面和界面的活性。
这种机械振动可以促进化学反应的进行,提高反应速率和反应效率。
因此,超声波技术在催化剂制备、材料表面处理、有机合成等化学领域具有重要应用前景。
超声波对材料性能的影响还与超声波参数的选择密切相关。
首先,超声波的频率对材料的响应有着重要影响。
不同频率的超声波引起的材料性能变化也不同。
例如,低频超声波通常导致材料的塑性变形,而高频超声波更容易产生材料的热效应和化学反应。
其次,超声波的振幅和功率也对材料的影响有一定程度的影响。
过高的振幅或功率可能引起材料的破坏或不可逆变化。
因此,在超声波处理过程中需要根据具体的材料和应用需求选择合适的超声波参数。
在实际应用中,超声波技术已广泛应用于材料加工和改性领域。
例如,通过超声波振动可以实现金属焊接和合金熔化等加工过程,也可以用于纳米材料的制备和涂层的加工。
此外,超声波还可以用于材料的清洗、降解和改性。
通过超声波技术,可以提高材料的质量和性能,并实现材料在工程和科学领域中的创新应用。
超声振动对金属材料焊接质量的影响研究
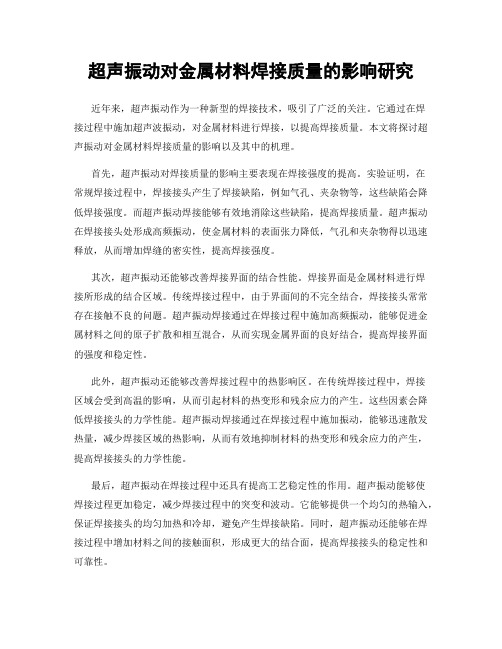
超声振动对金属材料焊接质量的影响研究近年来,超声振动作为一种新型的焊接技术,吸引了广泛的关注。
它通过在焊接过程中施加超声波振动,对金属材料进行焊接,以提高焊接质量。
本文将探讨超声振动对金属材料焊接质量的影响以及其中的机理。
首先,超声振动对焊接质量的影响主要表现在焊接强度的提高。
实验证明,在常规焊接过程中,焊接接头产生了焊接缺陷,例如气孔、夹杂物等,这些缺陷会降低焊接强度。
而超声振动焊接能够有效地消除这些缺陷,提高焊接质量。
超声振动在焊接接头处形成高频振动,使金属材料的表面张力降低,气孔和夹杂物得以迅速释放,从而增加焊缝的密实性,提高焊接强度。
其次,超声振动还能够改善焊接界面的结合性能。
焊接界面是金属材料进行焊接所形成的结合区域。
传统焊接过程中,由于界面间的不完全结合,焊接接头常常存在接触不良的问题。
超声振动焊接通过在焊接过程中施加高频振动,能够促进金属材料之间的原子扩散和相互混合,从而实现金属界面的良好结合,提高焊接界面的强度和稳定性。
此外,超声振动还能够改善焊接过程中的热影响区。
在传统焊接过程中,焊接区域会受到高温的影响,从而引起材料的热变形和残余应力的产生。
这些因素会降低焊接接头的力学性能。
超声振动焊接通过在焊接过程中施加振动,能够迅速散发热量,减少焊接区域的热影响,从而有效地抑制材料的热变形和残余应力的产生,提高焊接接头的力学性能。
最后,超声振动在焊接过程中还具有提高工艺稳定性的作用。
超声振动能够使焊接过程更加稳定,减少焊接过程中的突变和波动。
它能够提供一个均匀的热输入,保证焊接接头的均匀加热和冷却,避免产生焊接缺陷。
同时,超声振动还能够在焊接过程中增加材料之间的接触面积,形成更大的结合面,提高焊接接头的稳定性和可靠性。
综上所述,超声振动技术对金属材料焊接质量的影响主要体现在焊接强度的提高、焊接界面结合性能的改善、热影响区的改善以及工艺稳定性的提高。
超声振动焊接作为一种新型的焊接技术,在提高焊接质量方面具有巨大的潜力。
碳纤维复合材料缺陷的超声检测及材料力学性能仿真研究

生高频脉冲激励信号ꎬ将信号传输到超声换能器ꎬ再由换
博看网 . All Rights
Reserved.
能器的压电效应将脉冲激励信号转换成脉冲超声波ꎮ Nhomakorabea当
声波在换能器与工件之间的耦合介质内传输时ꎬ一部分声
波被工件表面反射ꎬ反射后由换能器接收ꎬ并转换成激励
信号传输到超声脉冲激励 / 接收单元ꎬ通过单元进行信号
合介质的界面发生强烈折射ꎬ并在界面处发生轴向聚焦ꎮ
透镜和样品之间的耦合介质主要用于传播超声波ꎮ 换能
器安装在 x、y、z 三轴移动平台上ꎬ可在三维空间范围内运
4K
图 3 复合材料内部缺陷建模
模型中界面层通过插入 Cohesive 内聚力单元来连接
两材料ꎬ并模拟裂纹产生和损伤演化ꎮ 基于胶合力学理论
ZHANG Quanli 1 ꎬ ZENG Jiaheng1 ꎬ YANG Zhen1 ꎬ GUO Nan1 ꎬ CHEN Zhengsheng2 ꎬ SU Honghua1
(1. College of Mechanical and Electronic Engineeringꎬ Nanjing University of Aeromautics and Astronauticsꎬ
时ꎬ其材料的抗拉强度下降 13. 2%ꎮ 王雪明等
[15]
对碳纤
维复合材料整体成型过程中温度对材料缺陷的影响进行
动ꎮ 为了防止检测过程中近表面产生扫描盲区问题ꎬ内部
平台采用有机玻璃ꎮ 探头与平台之间采用去离子水作为
检测耦合剂ꎬ探头下沉至水中ꎬ距离工件表面约1 cmꎮ采用
徕卡 DMC 4500 光学显微镜、科视达 KH- 7700 三维视屏
增强树脂基复合材料层压板进行分层缺陷检测ꎬ获得了复
低能电子束辐射固化涂料的研究
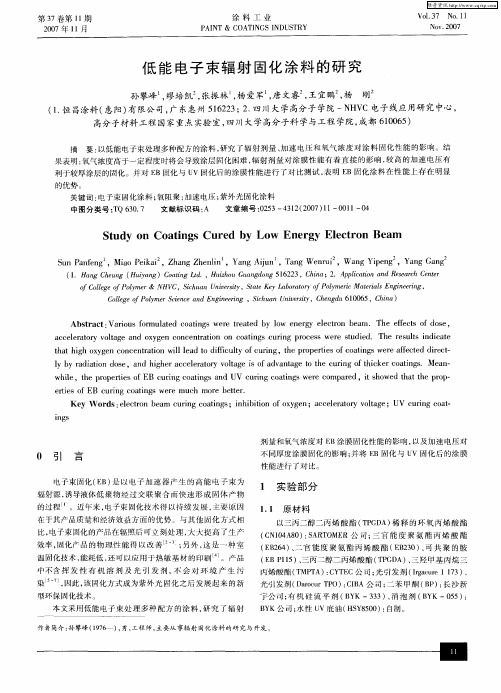
关键词 : 电子束 固化涂料 ; 氧阻聚 ; 加速 电压 ; 紫外光固化涂料
中 图 分 类 号 :Q6 32 20 ) 1 0 1 o 0 5 4 1( 0 7 l — 0 l— 4
S u y o a i g r d by Lo En r y El c r n Be m t d n Co tn s Cu e w e g e t o a
S nP ne g ,M a e a , h n h ni ,Y n i n , a gWe ri, n ieg , a gG n u afn i0P i i Z agZ e l agAj T n nu Wa gY pn Y n ag k n u
( .H n hug ( uyn )C ai t. H i o u nd n 2 3 hn ; .Api t na dR s r et 1 a gC en H i g ot gLd , u huG a g og5 6 2 ,C ia 2 pl a o n e ac Cne a n z 1 ci e h r
维普资讯
第3 7卷第 1 期 1
20 0 7年 1 月 1
涂 料 工 业
P NT & C T N ND T AI OA I GS I US RY
V 13 No 1 0. 7 .1
NO . 0 7 V20
低 能 电子 束 辐射 固化 涂 料 的研 究
Absr t Va iu o multd c ai g r r ae b o e e g l cr n b a t ac : ro s f r ae o t s we e te t d y l w n r y ee to e m. T fe t fdo e, n he e fc so s a c lr tr otg n x g n c n e ta in o o tn sc rn r c s r t did Th e u t n i ae c e ea oy v la e a d o y e o c n r t n c a i g u i g p o e s we e su e . o e r s ls i d c t t a ih o y e o c n r to l la o d f c lyo u n h th g x g n c n e ta in wil e d t i u t fc r g,t e p o e te fc ai g r fe td d rc — i i h r p ri so o tn swe e afc e ie t l y rdit n d s y b a a i o e,a d h g ra c l r tr ot g so d a t g o t e c rn ft i k rc a i g . Me n o n ihe c ee ao y v l e i fa v n a e t h u i g o h c e o tn s a a— wh l i e,t e p o e te fEB urn o tng n h r p ri so c i g c a i s a d UV urn o t swee c mp r d,i s o d t a h r p c igc ai r o ae ng t h we h tt e p o —
复合材料层板超声检测缺陷评定方法分析_王铮

第44卷增刊2012年4月 南 京 航 空 航 天 大 学 学 报Journal of Nanjing U niversity of Aeronautics &Astronautics V ol.44N o.S A pr.2012复合材料层板超声检测缺陷评定方法分析王 铮 梁 菁 史丽军 权 鹏(北京航空材料研究院,北京,100095)摘要:碳纤维增强树脂基复合材料的接触式超声检测,对大于探头直径的缺陷常采用半波高法评定大小,但各检测标准均没有对半波高法的基准波进行规定。
采用不同基准波评定缺陷可能会造成缺陷评定结果不同,从而直接影响制件验收。
本文采用理论分析与实际检测相结合的方法,对复合材料检测中常采用的以底面回波为基准波和以缺陷回波为基准波两种缺陷评定方法进行分析,比较了两种方法测量结果的差异,给出了复合材料层板接触式超声检测缺陷评定方法的建议。
关键词:复合材料;超声检测;缺陷评定中图分类号:T B5 文献标识码:A 文章编号:1005-2615(2012)S-0138-04 收稿日期:2011-10-16;修订日期:2012-01-30 通讯作者:王铮,女,工程师,E -mail :w angzhengnln @sina .co m .cn 。
Measurement for Ultrasonic Contact Inspection onDefect in Carbon Fiber -Reinforced CompositeW ang Zheng ,L iang J ing ,Shi L ij un ,Quan Peng(Beijing Instit ut e o f A ero naut ical M aterials ,Beijing ,100095,China )Abstract :W hen the carbon fiber -r einfo rced com posite is inspected by ultrasonic co ntact m ethod,the sizeof the defect is measur ed by the amplitude of the reflectio n echo .T he distance betw een the tw o points can be determined as the length o f the defect on one direction w hen the am plitude of the reflectio n echo co mes dow n to half of its max imum.T he reflection echo can be r eflected by the defect as w ell as by the botto m.T he effect of the cho ice of these tw o different reflection echo es on the measurement result is studied .The sug gestion o n ho w to measur e the defect is also g iven .Key words :composite;ultraso nic test;m easur e defect 复合材料以其优异的性能在航空工业领域得到越来越广泛的应用,无损检测技术作为复合材料制件质量控制的有效手段,也越来越发挥出重要作用。
复合材料层压结构超声相控阵检测的缺陷定量表征

复合材料层压结构超声相控阵检测的缺陷定量表征张继敏;周晖;刘奎;刘卫平【摘要】使用便携式超声相控阵设备及两个几何参数不同的线性阵列换能器对埋有ϕ6 mm和ϕ9 mm 人工缺陷的碳纤维复合材料层压板试块进行检测,分别进行了非聚焦线性扫查和聚焦线性扫查,并对 C 扫成像进行分析。
结果表明:在非聚焦线性扫查情况下,其扫查缺陷尺寸的准确性与换能器晶元长度和孔径长度有紧密关系,试验结果与理论分析一致;而在聚焦线性扫查情况下,其扫查缺陷尺寸的准确性不再受孔径数过大的影响。
%In this paper,a portable phased array ultrasonic device and two linear array transducers with different geometric parameters are utilized to detect the ϕ 6 mm and ϕ 9 mm defects in a carbon fiber composite laminate. Non-focusing linear scan and focusing linear scan are adopted,respectively,and C scan image is shown to study and analysis.The experiment reveals that in the case of non-focusing linear scan,the accuracy of the size of defects has a close relation with the lengths of the element and aperture.The experiment results show good agreements with theoretical analysis;but in the case of focusing linear scan,the accuracy of the defect size is not affected by the overlarge aperture.【期刊名称】《无损检测》【年(卷),期】2016(000)001【总页数】6页(P20-25)【关键词】超声相控阵;阵列换能器;尺寸定量【作者】张继敏;周晖;刘奎;刘卫平【作者单位】上海飞机制造有限公司航空制造技术研究所,上海 200436;上海飞机制造有限公司航空制造技术研究所,上海 200436;上海飞机制造有限公司航空制造技术研究所,上海 200436; 纤维材料改性国家重点实验室东华大学,上海200051;上海飞机制造有限公司航空制造技术研究所,上海 200436【正文语种】中文【中图分类】TG115.28在无损检测技术发展史中,超声相控阵技术凭借其快速,灵活,可进行复杂检测,可靠性强等特点在电力、石油化工、铁路、核工业、航空航天等领域发挥越来越重要的作用[1-6]。
复合材料层压板分层缺陷超声相控阵检测与评估

第49卷2021年2月第2期第149-157页材料工程J o u r n a l o fM a t e r i a l sE n g i n e e r i n gV o l.49F e b.2021N o.2p p.149-157复合材料层压板分层缺陷超声相控阵检测与评估D e l a m i n a t i o nd e f e c t s t e s t i n g a n d e v a l u a t i o no f c o m p o s i t e l a m i n a t e su s i n gp h a s e da r r a yu l t r a s o n i c t e c h n i q u e曹弘毅1,马蒙源1,丁国强1,姜明顺1,孙琳2,张雷1,贾磊1,田爱琴2,梁建英2(1山东大学控制科学与工程学院,济南250061;2中车青岛四方机车车辆股份有限公司,山东青岛266111)C A O H o n g-y i1,MA M e n g-y u a n1,D I N G G u o-q i a n g1,J I A N G M i n g-s h u n1,S U N L i n2,Z H A N GL e i1,J I A L e i1,T I A N A i-q i n2,L I A N GJ i a n-y i n g2(1S c h o o l o fC o n t r o l S c i e n c e a n dE n g i n e e r i n g,S h a n d o n gU n i v e r s i t y,J i n a n250061,C h i n a;2C R R CQ i n g d a oS i f a n gC o.,L t d.,Q i n g d a o266111,S h a n d o n g,C h i n a)摘要:针对碳纤维增强树脂基复合材料分层缺陷的无损检测与评估问题,通过制备预埋分层缺陷的标准试样,利用超声相控阵技术对缺陷进行无损检测与定量评估,并对测量误差进行分析㊂首先,在层压板铺层中间埋入聚酰亚胺薄膜制备分层缺陷试样;然后,对试样进行超声相控阵检测,通过超声S扫和C扫图像对缺陷进行定性分析与定量测量,并结合声场仿真对检测误差进行分析㊂结果表明:所制备试样内分层缺陷形状规则㊁埋深及大小与预设一致;超声相控阵步进方向检测尺寸比较准确,而扫查方向尺寸误差较大;超声相控阵技术能够准确识别分层缺陷的形状㊁尺寸及位置,具有很高的检测精度,对较小缺陷具有很好的检测效果㊂关键词:复合材料;分层缺陷;无损检测;超声;评估d o i:10.11868/j.i s s n.1001-4381.2020.000405中图分类号:T B553文献标识码:A 文章编号:1001-4381(2021)02-0149-09A b s t r a c t:C o m p o s i t em a t e r i a l sa r e p r o n e t od e l a m i n a t i o nd e f e c t sd u r i n g t h e p r e p a r a t i o n p r o c e s s.F o r t h en o n-d e s t r u c t i v e t e s t i n g a n de v a l u a t i o no fc a r b o nf i b e rr e i n f o r c e d p o l y m e r(C F R P)d e l a m i n a t i o n d e f e c t s,a s t a n d a r d s p e c i m e nw i t h e m b e d d e d d e l a m i n a t i o n d e f e c t sw a s p r e p a r e d,a n d t h e n p h a s e d a r r a y u l t r a s o n i cn o n-d e s t r u c t i v et e s t i n g t e c h n o l o g y w a s u s e d t o d e t e c tt h e d e l a m i n a t i o n d e f e c t s.T h e q u a l i t a t i v e a s s e s s m e n t a n d q u a n t i t a t i v e e v a l u a t i o no f d e l a m i n a t i o nd e f e c t sw e r e c a r r i e do u t.F i r s t,t h e d e l a m i n a t i o nd e f e c t s p e c i m e n w a s p r e p a r e dw i t ht h ea u t o c l a v e f o r m i n gp r o c e s s,a n d p o l y i m i d e f i l m s w e r e e m b e d d e d i n t h e s p e c i m e nb e f o r e p r o g r e s s;t h e n,t h e s p e c i m e nw a s i n s p e c t e du s i n gp h a s e d a r r a y u l t r a s o n i c t e c h n i q u e,q u a l i t a t i v ea n d q u a n t i t a t i v em e a s u r e m e n t o f d e l a m i n a t i o nd e f e c t sw e r ea n a l y z e d w i t hu l t r a s o n i cS-s c a na n dC-s c a n i m a g e,u n c e r t a i n t y a n a l y s i so f t e s t r e s u l t sw e r ea l s od i s c u s s e d i nc o m b i n a t i o nw i t ht h es o u n df i e l ds i m u l a t i o n.T h er e s u l t ss h o wt h a t t h es h a p e so f t h ede l a m i n a t i o nd e f e c t s i n t h e s a m p l e a r e r e g u l a r,t h e e m b e d m e n t d e p t ha n ds i z e a r e c o n s i s t e n tw i t ht h e p r e s e t.T h e i n d e xd i r e c t i o n s i z eo f t h ed e l a m i n a t i o nd e f e c t i sm o r ea c c u r a t e,a n dt h es c a nd i r e c t i o ns i z e i s l a r g e r t h a n t h ea c t u a ls i z e.P h a s e da r r a y u l t r a s o n i ct e c h n i q u ec a na c c u r a t e l y i d e n t i f y t h es h a p e,s i z ea n d p o s i t i o no f d e l a m i n a t i o nd e f e c t sw i t hh i g hd e t e c t i o na c c u r a c y a n ds t i l lh a s g o o dd e t e c t i o ne f f e c t s f o r s m a l l d e f e c t s.K e y w o r d s:c o m p o s i t e s;d e l a m i n a t i o nd e f e c t;n o n-d e s t r u c t i o n t e s t i n g;u l t r a s o n i c;e v a l u a t i o n材料工程2021年2月碳纤维增强树脂基复合材料(c a r b o nf i b e r r e i n f o r c e d p o l y m e r,C F R P)作为高性能结构材料,具有比强度高㊁比刚度大㊁耐腐蚀㊁可设计性好等优点,在航空航天㊁轨道交通和船舶等领域获得了广泛应用[1-2]㊂但由于复合材料的特殊制造工艺及其多铺层的特点,导致在制造过程中容易出现不稳定现象,伴随着某些制造缺陷的产生,常见的缺陷有分层㊁夹杂㊁脱粘㊁孔隙等,严重影响材料结构性能㊂并且缺陷在服役过程中由于应力作用不断扩展,大大降低结构件的残余强度,导致结构整体失效或其他灾难性后果[3]㊂因此,复合材料缺陷检测是复合材料制造过程中需要关注的焦点㊂复合材料具有各向异性及多铺层界面特性,导致其界面行为及缺陷信号特征复杂㊂而无损检测与评估技术能够提供复合材料内部损伤的基础信息,是缺陷定量评估及损伤行为分析的一种有效手段[4-6]㊂因此,很多学者对复合材料无损检测技术进行了广泛研究,常用无损检测技术包括超声[7]㊁L a m b波[8]㊁红外热成像[9-10]等㊂超声相控阵技术具有声束灵活可控㊁检测精度和灵敏度高㊁检测效率高等优势,被认为是一种非常有发展潜力的无损检测方法,在复合材料无损检测领域受到越来越多的关注[6]㊂N a g e s w a r a n等[11]通过在C F R P试样中预埋特氟龙薄膜制备分层缺陷,并使用超声相控阵技术对其检测,准确识别出预埋缺陷形状,但并未对缺陷进行定量评估;徐娜等[12]利用线型相控阵换能器对L型构件R区进行检测,通过对相控阵聚焦法则的优化设计,准确检测出R区分层缺陷形状及深度,但未对缺陷尺寸进行定量评估;张冬梅等[13]利用超声相控阵技术对复合材料R区分层缺陷进行检测,通过对线阵及弧阵相控阵探头的实验研究,对试样厚度及缺陷深度进行了定量测量,缺少对缺陷尺寸的定量分析;李健等[14]利用超声相控阵检测A扫数据,结合小波包与B P神经网络算法,对C F R P分层㊁夹杂和脱粘缺陷进行分类,有效提高了缺陷的检测效率,但是仅限对缺陷进行定性分析识别,未进行有效的定量评估;M e o l a等[15]利用超声相控阵技术对C F R P中预埋分层缺陷进行了检测,并和红外热成像技术进行对比,证明超声相控阵技术能够有效检测出预埋缺陷的形状㊁尺寸和深度,但其仅预埋一个直径20m m的圆形缺陷,数量较少且直径较大,不利于对超声相控阵技术检测能力进行充分评估;C a m i n e r 等[16]为充分评估超声相控阵技术对C F R P分层缺陷的检测能力,制备了预埋多种不同材质㊁形状㊁尺寸及埋深分层缺陷的试样,并对铺层方式及厚度对检测结果的影响做了研究,但其制作工艺及缺陷材质特性导致其预埋分层缺陷易产生变形,一定程度上影响对检测结果的定量评估,且缺陷尺寸较大(ȡ10m m)也不利于对超声相控阵检测能力的评估㊂上述研究中受限于分层试样的制作效果,对分层缺陷的检测误差分析较少;此外,预埋缺陷数量较少㊁直径较大,不能对超声相控阵检测能力进行很好的评估㊂针对上述问题,本工作首先制备含有不同埋深及尺寸分层缺陷的C F R P层压板试样;然后利用超声相控阵技术对其进行检测,通过S扫描与C扫描图像对检测结果进行分析与测量,并结合声场仿真对检测结果进行误差分析,实现了试样分层缺陷的可视化分析与定量评估㊂1实验材料及方法1.1分层缺陷试样超声信号在复合材料传播过程中,当内部存在损伤或缺陷时,由于声阻抗的不同,将会导致入射声波发生反射㊁衍射等行为㊂声波的反射强度(能量)与缺陷的物理性质(如密度㊁弹性常数)有关:R=νDρD-νCρCνDρD+νCρC(1)式中:R为入射声波在缺陷界面的声压反射系数;νD 为入射声波在缺陷中的传播速率;ρD为缺陷区密度;νC为入射声波在复合材料中的传播速率;ρC为复合材料的密度㊂R值越大,表明声波反射越强烈㊂因此,选择声阻抗与复合材料相近的聚酰亚胺薄膜作为分层缺陷,声波在缺陷处反射信号较弱,能够有效地评估超声相控阵对分层缺陷的检测能力,且聚酰亚胺耐高温可有效防止预埋缺陷在制备过程中的扭曲变形㊂分层缺陷试样尺寸为250m mˑ200m m,厚度为3.0m m㊂原材料为东丽T300编织碳纤维斜纹预浸布(F AW200/69),克重200g/m2,单层名义厚度0.25m m㊂试样铺层方式[90/0]7,共14层,其中0ʎ方向为长边方向㊂通过在铺层之间预埋聚酰亚胺薄膜制备分层缺陷,薄膜厚度为0.025m m㊂试样铺层及缺陷埋入方式如图1所示,预埋位置共3处,分别为浅层(第2,3铺层之间)㊁中间层(第7,8铺层之间)㊁深层(第11,12铺层之间),每层预埋4个圆形缺陷,直径分别为12,9,6,3m m㊂聚酰亚胺薄膜预埋入铺层时喷涂适量脱模剂,阻止其与预浸布铺层发生粘连,有效防止其在试样固化成型过程中发生扭曲变形㊂试样使用热压罐成型工艺制备,将铺叠后的试样毛坯密封于真空袋内,抽真空后放入热压罐中,按照预浸布固化工艺进行升温㊁升压㊁固化成型,固化温度与压力分别为130ħ,600k P a㊂051第49卷 第2期复合材料层压板分层缺陷超声相控阵检测与评估图1 试样尺寸及缺陷预埋方式F i g .1 S pe c i m e n s i z e a n dd e l a m i n a t i o nd ef e c t s e m b e d m e n tm e t h o d 铺叠后试样名义厚度为3.5m m ,但在试样制备过程中由于高温高压作用,试样成品最终厚度约为3m m ㊂假定固化过程中各铺层具有相同的压缩量,则各层分层缺陷预埋深度(d s )分别为浅层0.43m m ㊁中间层1.50m m ㊁深层2.34m m ㊂1.2 超声相控阵检测技术超声相控阵检测原理如图2所示,超声相控阵技术可以同时对阵列探头中的多个晶元进行激励,通过控制每个晶元的激发延迟时间,实现发射声束的自动偏转与聚焦;在反射信号处理过程中,对每个晶元接收到的反射信号进行时间延迟校准,然后进行叠加处理即可得到当前检测点的反射信号㊂检测过程中,通过对激发孔径和聚焦法则的设置,可以动态调整发射声束的偏转方向㊁聚焦深度和焦点大小㊂图2 超声相控阵检测原理F i g .2 P r i n c i p l e o f p h a s e da r r a y u l t r a s o n i c t e s t i n g相控阵探头接收到的原始信号以A 扫描的形式被记录,每一扫查点的入射波㊁缺陷波及底面波以幅值-时间(或厚度)曲线的形式显示㊂通过不同成像算法对A 扫信号进行处理,可得到超声S 扫与C 扫图像㊂超声相控阵检测视图如图3所示,对于线性聚焦扫查方式,超声S 扫描图像为横断面视图,由探头阵列方向的A 扫描信号处理后得到,能够提供缺陷深度信息及断面形状;超声C 扫描图像为平面视图,由扫查区域内所有A 扫信号处理后得到,包括幅值或深度两种不同的视图形式,能够提供缺陷平面形状及尺寸信息㊂图3 超声相控阵检测视图F i g.3 V i e w s o f p h a s e d a r r a y u l t r a s o n i c 超声相控阵检测系统如图4所示,主机为O m n i S c a n M X 2便携式超声相控阵探伤仪,相控阵探头选择线性阵列近壁探头(5L 64-NW 1),晶元数为64,晶元中心间距为1m m ,探头中心频率为5MH z ㊂为解决检测近表面盲区问题,使用高度为20m m 的有机玻璃楔块㊂在楔块与被检试样之间使用纯净水作为耦合剂,确保超声信号能够顺利经楔块射入试样,探头在扫查方向的行程位置通过E N C 1-2.5-D E 编码器获取㊂图4 超声相控阵检测实验装置F i g .4 E x p e r i m e n t a l s e t -u p o f p h a s e d a r r a y u l t r a s o n i c t e s t i n g相控阵探头聚焦法则选择线性聚焦方式,超声声束只聚焦不偏转㊂设置激活孔径为8,晶元步距为1,即每次通过软件控制激发8个晶元产生超声声束,然后从第1个晶元到第64个晶元依次移动激发㊂在不移动探头的情况下即可获取57(64-8+1)个扫查点,扫查宽度约为57m m ㊂采用单线扫查方式对试样进行检测,一次扫查可覆盖宽度为57m m ㊂因此,需要对试样进行3次单线扫查,每次扫查只检测同一埋深位置的分层缺陷㊂扫查方案如图5所示,单线扫查方151材料工程2021年2月向为试样长边方向,图中C F R P 板为分层缺陷试样实物㊂图5 扫查方案F i g.5 D e t a i l s o f s c a ns c h e m e 为准确获得缺陷深度信息,检测前需要对试样中的声速进行校准㊂试样厚度通过测量其4个边的中心位置厚度,然后取平均值得到㊂选择试样中无明显制造缺陷的位置进行声速校准,试样校准声速为2857.1m /s㊂2 实验结果与分析图6为单线扫查的结果图像,包含A 扫㊁S 扫和C扫视图,S 扫和C 扫图像均对A 扫信号幅值进行颜色编码,建立信号幅值与图像颜色的对应关系,信号幅值强度范围0%(白色)到100%(红色)㊂C 扫描成像结果与A 扫描图像中设定的闸门(G a t eA )范围和阈值紧密相关,当反射信号在闸门范围内且幅值大于设定阈值时,被识别为有效反射信号,因此需要准确设置闸门参数㊂检测前先对试样无缺陷区域进行扫查,分析其噪声信号幅值强度㊂扫查结果显示,试样噪声信号幅值均在15%以下㊂为保证成像效果,闸门阈值应稍高于噪声幅值,因此实验中设定闸门阈值为20%㊂图6 扫查结果视图 (a )A 扫;(b )S 扫;(c )C 扫F i g.6 V i e w s o f l i n e s c a n (a )A -s c a n ;(b )S -s c a n ;(c )C -s c a n 由于复合材料自身具有各向异性及多层界面特性,超声信号在其内部传播过程中衰减严重,深层反射信号较弱,导致深层缺陷检测尺寸偏小或出现漏检㊂而且试样中所预埋的聚酰亚胺缺陷声阻抗与复合材料相近,缺陷界面反射信号能力较弱,进一步减弱了深层反射信号强度㊂因此,在对分层缺陷试样进行超声相控阵检测时,使用时间校正增益技术增强反射信号[17],改善深层信号质量,提高检测精度㊂设定增益后,底部反射信号幅值与上表面反射信号幅值相同㊂2.1 C 扫描幅值图像分析图7为分层缺陷C 扫描幅值图像,可以看出,预埋的12个分层缺陷被全部检出,缺陷形状近似圆形,与预埋的圆形薄片基本一致,且缺陷圆形区域内颜色无明显差别,表明预埋薄膜未发生明显褶皱变形㊂图中分层缺陷与其他区域颜色差别较明显,图像颜色为红色或黄色,反射信号较强;其他区域图像颜色为蓝色,反射信号较弱㊂除缺陷外其他区域颜色均匀,试样无明显其他制备缺陷㊂图7(a )~(c)中同一埋深处分层缺陷图像颜色基本相同,反射信号强度相近㊂但仍然能够观察到随着缺陷直径的减小,缺陷颜色变浅,说明缺陷越小其反射信号能力越弱,越不容易被检测㊂图7(a ),251第49卷 第2期复合材料层压板分层缺陷超声相控阵检测与评估图7 分层缺陷C 扫描幅值图像(a )d s =0.43m m ;(b )d s =1.50m m ;(c )d s =2.34m m F i g .7 A m p l i t u d eC -s c a n i m a g e s o f d e l a m i n a t i o nd e f e c t s (a )d s =0.43m m ;(b )d s =1.50m m ;(c )d s =2.34m m (b)中缺陷中心在同一水平位置,与铺层时预埋位置一致,制备过程中未发生偏移;而图7(c)中3m m 缺陷中心位置相比其他3个缺陷有明显下移,说明此缺陷在制备过程中发生了移位㊂对比不同埋深分层缺陷图像颜色可知,随着缺陷埋深的增大,缺陷图像颜色由红变黄,反映出随着缺陷埋深的增加其反射信号越来越弱㊂为对分层缺陷尺寸进行定量评估,使用-6d B 方法[18-19]对超声相控阵检测结果进行定量测量,此方法中分层缺陷边界为信号幅值下降到缺陷区域内最大幅值的50%时位置㊂使用O m n i P C4.4软件的数据分析功能,首先利用数据光标定位缺陷内最大幅值点,获取缺陷内最大幅值,然后根据-6d B 方法确定缺陷边界,实现缺陷长度与宽度的测量,分层缺陷长度与宽度检测误差分别如图8(a ),(b)㊂可明显看出,超声相控阵检测结果比缺陷实际尺寸稍微偏大,长度测量值误差均比宽度测量值误差大,宽度测量值更接近缺陷实际直径㊂图8 分层缺陷检测误差 (a )长度误差;(b)宽度误差F i g .8 T e s t e r r o r s o f d e l a m i n a t i o nd e f e c t s (a )l e n gt he r r o r ;(b )w i d t he r r o r 351材料工程2021年2月由于线阵超声相控阵探头只能沿阵元宽度(步进方向)聚焦,对选定超声探头,聚焦声束焦斑尺寸是由激活孔径㊁聚焦深度决定㊂为对上述误差原因进行准确分析,建立基于瑞利积分的固固界面多点源三维声场模型,使用MA T L A B 对平行于试样平面方向超声声场进行仿真[20]㊂仿真中楔块密度为1.18g /c m3,纵波声速为2730m /s ,聚焦深度为3m m ,激活孔径为8㊂图9为聚焦点位置处平面声场仿真结果,能够直观观察到超声声束在步进方向聚焦效果较好,扫查方向上焦斑尺寸较大大,使用-6d B 方法测量聚焦声场在扫查方向与步进方向尺寸分别为5.7,1.9m m㊂图9 聚焦点位置声场仿真图像F i g.9 S i m u l a t i o n r e s u l t o f s o u n d f i l e d a t f o c u s p o i n t 根据上述仿真结果,当声束沿扫查方向向缺陷移动时,聚焦点中心到达缺陷边缘前已经产生较强缺陷反射信号(信号幅值大于设定闸门阈值)㊂在图7中可以发现,随着探头在扫查方向移动,反射信号逐渐增强,导致图像颜色逐渐变深;同样在探头远离缺陷时也会发生部分声束反射现象,反射信号逐渐变弱,图像颜色逐渐变浅㊂相控阵超声聚焦声场的不对称导致缺陷检测尺寸的不对称结果,在步进方向聚焦焦斑尺寸更小,检测结果更接近真实值㊂聚焦声束焦斑扫查方向与步进方向尺寸差值为4m m ,而缺陷检测结果在两个方向的误差差值约2m m ,为焦斑尺寸差值的一半㊂因此,在实际工程应用中,应该以步进方向检测结果为准,为准确检测缺陷长宽尺寸可对缺陷进行两次方向垂直的扫查㊂为验证上述分析的正确性,调整扫查方向为试样短边方向(与原扫查方向垂直),对不同埋深的3m m 缺陷进行单线扫查㊂扫查结果如图10所示,调整后缺陷扫查方向尺寸依然大于步进方向尺寸,验证了上述分析的正确性㊂综上,超声相控阵C 扫描幅值图像能够直观呈现分层缺陷沿铺层方向的形状,对最小直径3m m缺陷图10 3m m 缺陷C 扫幅值图像F i g.10 A m p l i t u d eC -s c a n i m a g e o f 3m md e f e c t s 依然有很好的检测效果㊂在对分层缺陷进行定量评估时,特别是对于小尺寸缺陷,应对缺陷进行两次不同方向扫查并以步进方向检测结果为准,以提高定量评估准确性㊂2.2 C 扫描深度图像分析C 扫描深度图像是利用闸门内A 扫描原始数据,根据超声信号渡越时间t 及声速c p ,计算每一扫查点反射信号的深度信息d t (d t =(c p ˑt )2),并以颜色编码的方式成像,深度范围为0m m (红色)到3m m (蓝色)㊂图11为分层缺陷C 扫描深度图像,图中同一埋深处缺陷深度颜色基本相同,说明缺陷埋深相同,与缺陷预埋在同一铺层一致;对比不同埋深缺陷图像,浅层㊁中层㊁深层缺陷图像颜色分别为黄色㊁绿色㊁蓝色,图像颜色所代表缺陷埋深基本与预设埋深d s 一致㊂图11 分层缺陷C 扫描深度图像(a )d s =0.43m m ;(b )d s =1.50m m ;(c )d s =2.34m m F i g .11 D e p t hC -s c a n i m a ge s of d e l a m i n a t i o nd e f e c t s (a )d s =0.43m m ;(b )d s =1.50m m ;(c )d s =2.34m m 为对缺陷深度进行定量评估,选取图像中缺陷中心位置深度作为检测深度(d t ),表1为缺陷深度检测451第49卷 第2期复合材料层压板分层缺陷超声相控阵检测与评估结果㊂中间层及底层缺陷埋深检测结果较准确,最大误差仅为0.04m m ;而浅层缺陷埋深检测结果误差相对较大,4处缺陷埋深误差均为0.11m m ㊂超声相控阵对分层缺陷深度检测精度较高,但对于近表层缺陷深度误差相对较大㊂表1 分层缺陷深度T a b l e 1 D e pt ho f t h e d e l a m i n a t i o nd e f e c t s d s /m m d t /m m ϕ12m m ϕ9m mϕ6m mϕ3m m0.430.540.540.540.541.501.541.521.501.502.342.362.342.332.312.3 S 扫描图像分析S 扫图像是基于信号渡越时间的试样断面深度图像,不同埋深分层缺陷中心位置S 扫描图像如图12所示,图中上表面波与底面波图像颜色为红色,表明信号在此处发生较强的界面(楔块-试样界面㊁试样-空气界面)反射,而缺陷图像颜色相比要浅很多,说明缺陷反射信号较弱;另外在缺陷下部均未发现明显声影,说明声波在遇到缺陷后大部分发生透射,与缺陷所用聚酰亚胺材质声阻抗特性一致㊂图中分层缺陷外其他位置能够明显观察到浅蓝色横向条纹,表明在铺层界面处发生了超声弱反射现象,说明超声相控阵技术具有很高的纵向分辨力㊂图12 分层缺陷S 扫描图像(a )d s =0.43m m ;(b )d s =1.50m m ;(c )d s =2.34m m F i g .12 S -s c a n i m a ge s of t h e d e l a m i n a t i o nd e f e c t s (a )d s =0.43m m ;(b )d s =1.50m m ;(c )d s =2.34m m 551材料工程2021年2月S扫图像能够反映试样整个厚度区间的断面信息,更加直观地观察到不同埋深缺陷在试样厚度方向上的位置及缺陷断面形状㊂并且能够实现对试样厚度㊁缺陷深度及缺陷断面尺寸的定量检测(详见图中标注尺寸)㊂图像上缺陷断面形状为直线,说明缺陷未发生扭曲变形㊂缺陷中心位置断面尺寸与通过C扫描测量的宽度信息基本一致,缺陷形状为圆形相符㊂3结论(1)实验所制备的分层缺陷标准试样效果较好,缺陷实际形状㊁深度及尺寸置信度较高,能够实现对超声相控阵检测能力的评估㊂(2)仿真结果显示,相控阵超声聚焦声束的不对称导致了检测结果的不对称,步进方向尺寸误差较小,在工程应用中对缺陷定量分析时应以此方向结果为准㊂(3)定量测量结果表明,超声相控阵技术能够准确识别分层缺陷形状㊁尺寸及位置,对不同深度及尺寸的分层缺陷均具有很好的检测效果,尺寸检测结果误差<1m m,深度检测结果误差<0.1m m㊂(4)超声相控阵C扫图像能够呈现缺陷形状及大小,S扫描图像能够揭示缺陷位置及断面形状,结合C 扫描图像与S扫描图像,可实现对分层缺陷的可视化检测分析,是对分层缺陷进行定性分析与定量检测的有效手段㊂参考文献[1]邢丽英,包建文,礼嵩明,等.先进树脂基复合材料发展现状和面临的挑战[J].复合材料学报,2016,33(7):1327-1338.X I N GLY,B A OJ W,L IS M,e t a l.D e v e l o p m e n t s t a t u sa n d f a-c i n g c h a l l e n g eo fad v a n ce d p o l y m e r m a t r i xc o m p o s i t e s[J].A c t aM a t e r i a eC o m p o s i t a eS i n i c a,2016,33(7):1327-1338. [2]顾善群,刘燕峰,李军,等.碳纤维/环氧树脂复合材料高速冲击性能[J].材料工程,2019,47(8):110-117.G USQ,L I U YF,L I J,e t a l.H i g h s p e e d i m p a c t p r o p e r t i e s o f c a r-b o n f i b e r/e p o x y r e s i nc o m p o s i t e s[J].J o u r n a lo f M a t e r i a l sE n g i-n e e r i n g,2019,47(8):110-117.[3]梁小林,许希武,林智育.复合材料层板低速冲击后疲劳性能实验研究[J].材料工程,2016,44(12):100-106.L I A N GXL,X U X W,L I NZY.F a t i g u e p e r f o r m a n c e o f c o m p o s-i t e l a m i n a t e sa f t e rl o w-v e l o c i t y i m p a c t[J].J o u r n a lo f M a t e r i a l sE n g i n e e r i n g,2016,44(12):100-106.[4]I B R A H I M M E.N o n d e s t r u c t i v ee v a l u a t i o no f t h i c k-s e c t i o nc o m-p o s i t e s a n ds a n d w i c hs t r u c t u r e s:ar e v i e w[J].C o m p o s i t e s:P a r t A,2014,64:36-48.[5] G H O L I Z A D E HS.Ar e v i e wo f n o n-d e s t r u c t i v e t e s t i n g m e t h o d s o fc o m p o s i t em a t e r i a l s[J].P r o c ed i aS t r u c t u r a l I n te g r i t y,2016,1:50-57.[6]刘松平,刘菲菲,李乐刚,等.航空复合材料无损检测与评估技术研究进展回顾[J].航空制造技术,2019,62(14):14-27.L I USP,L I U FF,L IL G,e t a l.R e v i e wo f r e s e a r c h p r o g r e s so n n o n d e s t r u c t i v e t e s t i n g a n d e v a l u a t i o n t e c h n i q u e s f o r a e r o-c o m p o s-i t e s[J].A e r o n M a n u fT e c h n o l,2019,62(14):14-27.[7] H A S S E N A A,T A H E R IH,V A I D Y A U K.N o n-d e s t r u c t i v e i n-v e s t i g a t i o no ft h e r m o p l a s t i cr e i n f o r c e dc o m p o s i t e s[J].C o m p o s-i t e s:P a r tB,2016,97:244-254.[8]S A E E D I F A R M,MA N S V E L D E R J,M O H AMMA D I R,e ta l.U s i n gp a s s i v e a n da c t i v ea c o u s t i cm e t h o d s f o r i m p a c t d a m a g ea s-s e s s m e n t o f c o m p o s i t e s t r u c t u r e s[J].C o m p o s i t e S t r u c t u r e s,2019, 226:111252.[9] M E O L AC,B O C C A R D IS,C A R L OMA G N O G M,e ta l.I m p a c td a m a g i n g o fc o m p o s i te st h r o u g ho n l i n e m o n i t o r i n g a n dn o n-d e-s t r u c t i v e e v a l u a t i o nw i t h i n f r a r e d t h e r m o g r a p h y[J].N D T&E I n-t e r n a t i o n a l,2017,85:34-42.[10] L IY,Z H A N G W,Y A N GZ W,e t a l.L o w-v e l o c i t y i m p a c t d a m-a g e c h a r a c t e r i z a t i o no fc a rb o nf i b e rr e i n f o rc ed p o l y me r(C F R P)u s i n g i n f r a r e d t h e r m o g r a p h y[J].I n f r a r e dP h y s i c s&T e c h n o l o-g y,2016,76:91-102.[11] N A G E S WA R A NC,B I R D C R,T A K A HA S H IR.P h a s e da r r a ys c a n n i n g o fa r t i f i c i a la n di m p a c td a m a g ei nc a r b o nf i b r er e i n-f o r c e d p l a s t i c(C F R P)[J].I n s igh t-N o n-D e s t r u c ti v eT e s t i n g a n dC o n d i t i o n M o n i t o r i n g,2006,48(3):155-159.[12]徐娜,周正干,刘卫平,等.L型构件R区的超声相控阵检测方法[J].航空学报,2013,34(2):419-425.X U N,Z H O UZG,L I U W P,e t a l.U l t r a s o n i c p h a s e da r r a y i n-s p e c t i o nm e t h o d f o r t h e c o r n e r o f L-s h a p e d c o m p o n e n t s[J].A c t aA e r o n a u t i c a e tA s t r o n a u t i c aS i n i c a,2013,34(2):419-425.[13]张冬梅,于光,周正干,等.复合材料构件R区的超声相控阵检测实验[J].北京航空航天大学学报,2013,39(5):688-692.Z H A N G D M,Y U G,Z H O UZG,e t a l.U l t r a s o n i c p h a s e da r r a yi n s p e c t i o n f o r t h e c o r n e r o f c o m p o s i t e c o m p o n e n t s[J].J o u r n a l o fB e i j i n g U n i v e r s i t y o fA e r o n a u t i c s a n dA s t r o n a u t i c s,2013,39(5):688-692.[14]李健,郭薇,杨晓霞,等.超声相控阵检测C F R P缺陷识别方法[J].天津大学学报(自然科学与工程技术版),2015,48(8):750-756.L I J,G U O W,Y A N GXX,e t a l.Af l a wc l a s s i f i c a t i o nm e t h o d f o r u l t r a s o n i c p h a s e d a r r a y i n s p e c t i o no fC F R P[J].J o u r n a l o fT i a n-j i nU n i v e r s i t y(S c i e n c e a n dT e c h n o l o g y),2015,48(8):750-756.[15] M E O L AC,B O C C A R D I S,C A R L OMA G N O G M,e t a l.N o n d e-s t r u c t i v ee v a l u a t i o no fc a r b o nf i b r er e i n f o r c e dc o m p o s i t e s w i t hi n f r a r e dt h e r m o g r a p h y a n d u l t r a s o n i c s[J].C o m p o s i t e S t r u c-t u r e s,2015,134:845-853.[16] C AM I N E R O M A,G A R C I A-M O R E N OI,R O D R I G U E Z G P,e t a l.I n t e r n a ld a m a g ee v a l u a t i o no fc o m p o s i t es t r u c t u r e su s i n gp h a s e da r r a y u l t r a s o n i c t e c h n i q u e:i m p a c t d a m a g e a s s e s s m e n t i nC F R Pa n d3D p r i n t e dr e i n f o r c e dc o m p o s i t e s[J].C o m p o s i t e s:P a r tB,2019,165:131-142.[17] S A D E G H IM Z,N I E N H E Y S E N P,A R S L A N S,e ta l.D a m a g ed e t e c t i o nb y d o u b l e-s i d e du l t r a s o n i ca s s e s s m e n t i nl o w-v e l o c i t y651第49卷第2期复合材料层压板分层缺陷超声相控阵检测与评估i m p a c t e dC F R P p l a t e s[J].C o m p o s i t eS t r u c t u r e s,2019,208:646-655.[18]S M I T H R.U l t r a s o n i cd e f e c ts i z i n g i nc a r b o n-f i b r ec o m p o s i t e s:a n i n i t i a ls t u d y[J].I n s i g h t(N o r t h a m p t o n),1994,36(8):595-605.[19]S M I T H RA,J O N E SLD,W I L L S H E RS J,e t a l.D i f f r a c t i o n a n ds h a d o w i n g e r r o r s i n-6d Bd e f e c t s i z i n g o f d e l a m i n a t i o n s[J].I n-s i g h t,1998,40(1):44-59.[20]曹弘毅,姜明顺,马蒙源,等.复合材料层压板分层缺陷相控阵超声检测参数优化方法[J].材料工程,2020,48(9):158-165.C A O H Y,J I A N G M S,MA M Y,e t a l.P a r a m e t e ro p t i m i z a t i o nm e t h o d f o r d e l a m i n a t i o nd e f e x t s d e t e c t i o no f c o m p o s i t e l a m i n a t eu s i n gp h a s e d a r r a y u l t r a s o n i c[J].J o u r n a l o fM a t e r i a l sE n g i n e e r-i n g,2020,48(9):158-165.基金项目:国家重点研发计划(2018Y F E0201302);国家自然科学基金(61873333);山东省重点研发计划(2019T S L H0301,2019G H Z004)收稿日期:2020-05-16;修订日期:2020-10-10通讯作者:姜明顺(1981-),男,教授,博士,研究方向为光电检测㊁故障检测与诊断㊁超声无损检测,联系地址:山东省济南市历下区经十路17923号山东大学千佛山校区控制科学与工程学院(250061),E-m a i l: j i a n g m i n g s h u n@s d u.e d u.c n(本文责编:解宏)751。
超声振动强化复合材料胶接技术

超声振动强化复合材料胶接技术
复合材料胶接技术是一种常见的加工方式,在航空、汽车、船舶等领域广泛应用。
然而,传统的复合材料胶接技术存在一些问题,例如接头强度低、胶层厚度不均匀等。
为了解决这些问题,近年来超声振动技术被引入到复合材料胶接中,可以有效地提高胶接质量和效率。
超声振动技术是利用高频振动使胶水分子产生摩擦热,从而提高胶接面的温度和粘结性能。
同时,超声振动还能够打破材料表面的氧化层,增强表面的附着力。
此外,超声振动还可以使胶水在接触面上均匀分布,减少气泡和缺陷的产生。
在实际应用中,超声振动的频率和振幅需要根据具体的胶水种类和材料性能进行调整。
同时,胶接面的准备、涂胶和压合等操作也需要注意一些细节,以确保胶接质量和效率。
总的来说,超声振动强化复合材料胶接技术具有操作简单、胶接质量高、生产效率高等优点,是一种非常实用的技术。
- 1 -。
- 1、下载文档前请自行甄别文档内容的完整性,平台不提供额外的编辑、内容补充、找答案等附加服务。
- 2、"仅部分预览"的文档,不可在线预览部分如存在完整性等问题,可反馈申请退款(可完整预览的文档不适用该条件!)。
- 3、如文档侵犯您的权益,请联系客服反馈,我们会尽快为您处理(人工客服工作时间:9:00-18:30)。
cure
content
iS reduced
to
1.80%.When
the
to
220 N,ILLS is
only improved by 3.64%and the void
increasing resin
gets under
to
2.62%.Larger amplitude and compacting force will induce
mE×12 mE×6
mE。层间剪切强度r
=3P/4bh,其中P是加载过程中的最大载荷(N),b 为试件宽度(ram),h为试件厚度(mm)。 1.5微观形貌及孔隙率观测 采用扫描电子显微镜S-3000N对复合材料层 压板层间剪切破坏形貌进行观察,利用美国 Sonoscan超声波无损检测设备D9500检测复合材 料孔隙缺陷,超声探头的频率为15 MHz。 1.6固化度测试 采用瑞士Mettler—Toledo差示扫描量热仪(型 号为DSCl)测试预浸带的固化度,测试温度范围为 一50~350℃,升温速率为20℃/min。
第49卷第4期 2015年4月
西
安
交
通
大
学
学
报
V01.49
NO.4
JOURNAL 0F XI’AN JIAOTONG UNIVERSITY
Apr.2015
DOI:10.7652/xjtuxb20 1 504022
超声压紧对低能电子束分层固化 复合材料质量的影响
张小辉,段玉岗,李超,张静静,赵新明
(西安交通大学机械工程学院,710049,西安)
收稿日期:2014—09—11。
作者简介:张小辉(1980一),男,博士生;段玉岗(通信作者),男,教授,博士生导师。
基金项目:
国家重大科技专项资金资助项目(2014ZX0400L091);国家“863计划”资助项目(2012AA040209);教育部新世纪优秀人才支持 计划资助项目(NCET-11—0419)。
2.1振幅对孔隙及ILsS的影响 在振幅分别为0、5、7.5、10肛m,压紧力为140 N,铺放夹角为90。和压头移动速度为10 mm/s的 工艺参数下,进行超声铺层实验,层压板的层间剪切 强度如图2所示。 由图2可知,随着超声振幅的增加,层压板层间 剪切强度呈现先增加后减小的趋势;当振幅达到 7.5肛m时,层压板的层间剪切强度值最大,相比不 采用超声振动的层压板(振幅为0“m),层间剪切强 度提高了约11.5%。图3是不同振幅所制备试件 的孔隙宏观分布图,其中黑色表示孔隙,孔隙最小测 量尺寸为0.13 mE。根据超声无损检测结果分析, 当振幅分别为0、5、7.5和10“m时,其孔隙率分别 为8.07%、5.39%、1.80%和7.65%(能量阀值为35,
http://WWW.jdxb.ca
万方数据
西安交通大学学报
第49卷
70
试件孔隙缺陷较多,出现了树脂与纤维局部分离的 破坏形式。因此,孔隙分布与ILSS测试结果相对
日65
塞60
趟
应,即孔隙率高的试件ILSS较低,反之亦然。 根据以上结果,超声振动压紧作用可有效消除 气泡,减少复合材料孔隙率,同时也发现超声振动热 效应非常明显。热效应作用使预浸带温度升高(图 6所示),从而使得树脂渗透性增强,其与超声的机 械作用共同使复合材料中树脂与纤维的界面结合程
http://zkxb.xjtu.edu.cn
压紧装置的工作原理是通过压头将超声振动传递到 预浸带铺层中,以消除孔隙、增强层间性能。 1.2原材料 电子束固化预浸带由北京航空材料研究院制 备,其中碳纤维采用东丽公司的T700,树脂采用北 京航空材料研究院研制的电子束固化树脂EB99—1。 复合材料预浸带厚度为0.125 mm,树脂质量分数 为(35±3)%。 1.3试件制备 首先,预浸带采用电子束双面辐照,然后通过超 声压紧装置将预浸带压紧并固化,经过逐层累加成
degree due
the rising temperature,resulting in lower resin permeability and ILSS.
Keywords:low—energy electron beam;ultrasonic compaction;composite;voids;ILSS
陵妻震纂◆剥
(b)5弘m (c)7.5肛m
图3
不同振幅制备试件的孔隙宏观分布网
(b)j pm
(c)7.j
J上m
罔4Biblioteka 不同振幅制备试件的孔隙微观SEM照片
(b)5 ptm 图5
(c)7.5
um
不同振幅制备试件分层断面SEM照片
http://WWW.Jdxb.cn
http://zkxb.xjtu.edu.cn
to
fabricate laminate with lOW—
to
energy electronic beam curing system,which transmits the energy of ultrasonic
the prepreg analyzed. ultrasonic
layers.The effects Experiments show
摘要:针对低能电子柬分层固化复合材料层间孔隙缺陷导致层间剪切强度较低的问题,设计了超 声压紧装置。该装置通过压头将超声波作用于预浸带铺层上,配合低能电子柬固化系统制作复合 材料层合板,并研究了超声压紧参数对复合材料质量的影响。实验结果表明,超声振动在压紧过程 中产生的机械效应和热效应可有效减少孔隙,增强纤维与树脂的界面结合性能,提高层间剪切强 度,从而改善复合材料试件质量。其中,振幅对复合材料孔隙率及层间剪切强度影响最大,当超声 振幅为7.5肚m时,试件致密性明显改善,孔隙率降至1.80%,层间剪切强度提高11.7%;压紧力影 响相对较小,当压紧力从100 N到220 N变化时,层间剪切强度只有3.64%的提高,孔隙率在 2.62%以下。过大的振幅与压紧力都会引起压紧过程中预浸带温度升高,导致树脂固化度提高,渗 透性变差,孔隙率增加,使复合材料质量降低。 关键词:低能电子束;超声压紧;复合材料;孔隙;层间剪切强度 中图分类号:TB332 文献标志码:A文章编号:0253—987X(2015)04—0134—06
of
ultrasonic
compaction effect
parameters and
on
voids
and
ILSS
are
that the
mechanical
heating effect
are
produced
in
compacting process,which eliminate interlaminar voids and enhance bonding strength of fibers and resin,then improve the quality of the
型,如图1所示。最后,固化成型后的复合材料层合 板在160℃恒温加热烘箱保温30 rain进行后固化 处理。低能电子束系统(型号为EB250—2DSF一150) 由美国AEB公司生产,电压为0~150 keV可调,束 流为O~25
mA。
l|
虱1
低能电子束分层制造_T艺流程图
1.4层间剪切强度测试 层间剪切强度根据ASTM D2344[15]进行测试, 实验设备为Instron4467,加载速率为1 mm/min,试 件尺寸为40
composite.When
the laminate layers
are
compacted
with 7.5弘m ultrasonic amplitude,the laminate’S ILSS is 1 1.7%higher than that of the laminate fabricated without ultrasonic compaction,and the void compacting force changes from 100 N
网络出版时间:2015—02—27
网络出版地址:http:∥WWW.cnki.net/kcms/detail/61.1069.T.20150227.0845.009.html
万方数据
第4期
张小辉,等:超声压紧对低能电子束分层固化复合材料质量的影响
碳纤维增强树脂基复合材料在航空航天、能源 装备、交通运输等领域的应用越来越广泛口、2],但是 传统的热压罐固化工艺周期长、能耗高、成本高,限 制了碳纤维增强树脂基复合材料的应用。近年来, 电子束固化逐渐成为树脂基复合材料固化工艺的一 个研究方向[3‘5]。其中,高能电子束固化研究开展较 早,工艺比较成熟,如加拿大航空公司利用高能电子 束固化技术修复了空客A320飞机整流罩[6];美国 军方采用高能电子束固化技术实现了导弹壳体、装 甲车侧板及全复合材料概念车等的制备[7];文献[8— 9]研究表明,电子柬固化复合材料具有优异的综合 性能。但是,高能电子束辐照强度大,屏蔽系统复 杂,成本较高,而低能电子束由于辐射强度小,成本 低的优势引起了研究者的兴趣。文献[10-11]将低 能电子束设备集成到自动铺带机上,制备出了宇航 飞机火箭助推器检修舱门蒙皮。文献E12J研究了低 能电子柬对复合材料冲击性能的影响。与热压罐固 化工艺中树脂因热压而产生流动以消除孔隙并获得 致密层压结构不同,低能电子束辐照固化温度较低, 树脂不能充分流动以填补制造过程中产生的空隙, 因而低能电子束分层固化复合材料构件层间孔隙较 多,层间剪切强度较低D3-14]。针对此问题,本文提出 了一种基于超声原理的压紧方法,以减少低能电子 束分层固化复合材料孔隙并提高层间剪切强度,为 低能电子束固化工艺的工程应用提供了参考。
振幅/Din
翼55 签50
嗵45