斜齿轮插齿刀齿形误差的测量
关于插齿刀齿形误差传递结果的探讨

其 法 向误 差 珐一Afcs o 口
式 中:a 一 r 径 处 插 齿 刀 齿 形 的压 力 角 ;a一 r 径 处 标 准 齿 形 的压 力 角 ; 半 , 半
u 一
插 齿 刀 基 圆柱 螺 旋 角 ; 除 与 r 径 有 关 外 ,还 与 半
分 析 上 式 可 以看 出 :当插 齿 刀 的 前 、 后 角 已 定 的情 况 下 ,
插齿 刀 的齿 形 角 有 关 .当 a =2 "0 1" ,得 到 的齿 顶 和齿 根 误 差 都 属 正 误 差 ,分 布 在 理 0 1' 5 时 论 渐 开 线 的 外 侧 ( 厚 增 加 ) 齿 . 2 齿 形 角 修 正 后 的齿 形 误 差 传 递 分 析 因插 齿 刀 相 当 于 变 位 齿 轮 ,根 据 渐 开 线 齿 轮 啮 合 原理 ,插 齿 刀
为减 小 齿 形 误 差 , 采用 修 正 插 齿 刀齿 形 角 的 办法 , 即修 正 齿
形 表 面 ( 开 螺 旋 面 ) 端 面 齿 形 角 . 插 齿 刀 的齿 形 角 a 渐 的 使 和齿
轮 分 圆压 力 角 n不 等 .
具 体 方 法是 : 刀具 切 削 刃投 影 在分 圆处 的切 线 和 理 论 渐 开 使 线 的切线 重 合 . 样 推 导 出刀 具 齿 面 的原 始 齿 形 角 n 这 的计 算 公
0 引言
插 齿 刀 由于 有 了前 角 和后 角 ,使 刀 刃在 切 削 运 动 中形 成 的 产 形 表 面 偏 离 了 渐 开 线 齿 面 , 引起 了齿 形 误 差 , 由于 标 准插 齿 刀 采 用 的前 刀 面 ( 锥 面 和 平 面 ) 和 后 刀 面 ( 开 螺 旋 面 ) 圆 渐 在 工 艺上 有 很 多 优 点 ,不 宜 轻 易变 动 .因而 ,为 使 齿 形 误 差 得 以修 正 , 目前 我 国采 用 的标 准 插 齿 刀一 律 把 齿 形 角 n 做 成 2 。01 .使 刀 刃 的投 影 齿 形 在 分 圆 处 和 标 准 齿 形 相 切 , 即分 01
斜齿轮螺旋线偏差测量误差分析

斜齿轮螺旋线偏差测量误差分析
斜齿轮螺旋线偏差测量误差分析涉及到机械工程领域的研究和实践,具体内容如下:
1. 测量方法的选择:选择合适的测量设备和测量方法来获取螺旋线偏差数据。
常用的方法包括齿间差法、螺纹测微仪法、投影法等。
2. 测量数据的处理:将螺旋线偏差的测量数据进行整理和统计分析。
包括计算平均值、最大值和最小值,计算标准偏差等。
3. 误差来源的分析:分析影响螺旋线偏差测量误差的各种因素,包括测量设备的精度、人为操作误差、环境条件等。
4. 误差的修正和补偿:根据误差来源进行误差修正或者补偿,以提高测量精度。
5. 统计分析和评估:利用统计学方法对测量数据进行分析和评估,例如建立测量误差模型,计算测量误差的置信区间等。
需要注意的是,具体的测量误差分析涉及到专业领域的知识,建议在实际操作中咨询专业工程师或者相关领域的专家。
插齿刀的结构及检测0

10.内支撑面对外支撑面的平行度误差(盘、碗形) 11.前角误差 12.顶刃后角误差 13.侧刃后角误差 14.前斜角误差(斜插齿刀)
2012-6-13
27
2012-6-13
28
2012-6-13
14
锥柄插齿刀(Ⅲ型)主要用于加工内齿轮,公称分度 圆直径有25mm、38mm两种。
说明:盘形、碗形内孔直径一般为Ф 31.743,也可以为Ф 44.443。 锥柄:锥部:莫氏2#(Ф 25),3# (Ф 38)。
2012-6-13
15
2.硬质合金插齿刀 用于硬质合金面插齿,适用于淬火后外、内齿 轮,双联或多联齿轮齿面半加工。
2012-6-13 17
斜齿插齿刀使用条件,在斜齿插齿机上使用
刀具的导程必须与机床的导程相同; 刀具的旋向必须与机床导轨的旋向相同; 被加工工件旋向与刀具的旋向相反; 刀具的螺旋角等于被加工齿轮的螺旋角。
2012-6-13
18
斜齿插齿刀的刀齿相对于其轴线是倾斜的,所以 两侧刃的切削角相差很大,一侧为锐角(称锐 侧),另一侧为钝角(称钝侧),切削条件差, 为了使两侧刃的工作条件大致相同,它的前面 采用特殊的刃磨方法,将刀齿前面刃磨成垂直 于其齿向方向的平面。 斜齿插齿刀可以做成锥柄:公称分度圆直径 Ф 38 锥柄莫氏3# 也可以做成盘形:公称分度圆直径Ф 100孔径 Ф 31.743。
2012-6-13
16
3.斜面插齿刀 斜面插齿刀用来加工内、外啮合的斜齿圆柱齿 轮,也可以加工人字齿轮,根据刃磨方法不同, 斜齿插齿刀有两种型式: ⑴ 费罗型斜齿插齿刀(一般称斜齿插齿刀)用 于加工普通的斜齿轮。 ⑵ 赛克斯型斜齿插齿刀主要用于加工人字齿轮, 也称人字齿轮插齿刀,这种插齿刀要成队使用, 一为左旋,一为右旋。
齿轮误差测量

二、不同场合的要求
1、精密机床、仪表的读数齿轮 2、低速重载(起重机、矿山机械)齿轮 3、高速重载(气轮机减速器) 4、正反转齿轮
资讯
1、传递运动准确性 2、传动平稳性 3、载荷分布均匀
资讯
1、载荷分布均匀性 2、侧隙要合理
资讯
1、传递运动的准确性 2、传动平稳性 3、载荷分布均匀性
要控制齿侧间隙
资讯
三、 单个齿轮的精度指标
(一)误差的产生
1、机床制造误差 2、刀具误差 3、齿坯加工、安装误差
1、几何偏心
2、运动偏心 3、机床传动链的短周期误差
(二)影响传递运动准确性的误差参数及测量
检测仪器
① 将被测齿轮安装在仪器上,松紧合适,即轴向不能窜 动,转动自如。
② 根据被测齿轮的模数选择测头,将它装在千分表上, 再将千分表装入仪器的表架上并锁紧。
③ 移动被测齿轮的位置,使测头处于齿宽中部。
④ 松开立柱6后的紧定螺钉,转动调节螺母7,使测头处 于齿槽内,并压表0.2—0.3mm左右,锁紧螺钉,将表针调 为0,开始记录数据。
(2)误差产生的原因:机床分度蜗轮偏心,使齿坯 转速不均匀,引起齿面左右切削不均匀所造成的齿轮 切向长周期误差
(3)影响:齿轮传递运动不准确
(4)公法线长度测量步骤
1)根据被测齿轮参数,计算(或查表)公法线公称值和跨 齿数
2)校对公法线千分尺零位值。
3)根据右图形式,依次测量 齿轮公法线长度值(测量全 齿圈),记下读数
(1)定义:齿轮端截面上,齿形工作部分内(齿顶倒棱部 分除外),包容实际齿形的两条设计齿形间的法向距离。
齿轮齿厚偏差测量
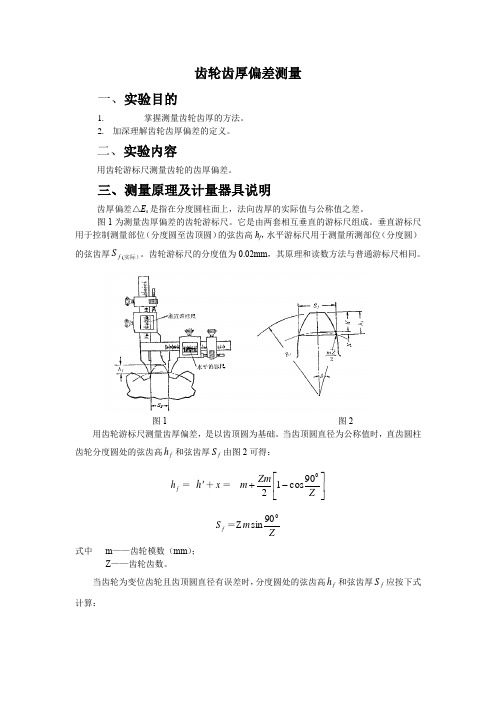
齿轮齿厚偏差测量一、实验目的1. 掌握测量齿轮齿厚的方法。
2. 加深理解齿轮齿厚偏差的定义。
二、实验内容用齿轮游标尺测量齿轮的齿厚偏差。
三、测量原理及计量器具说明齿厚偏差△E s 是指在分度圆柱面上,法向齿厚的实际值与公称值之差。
图1为测量齿厚偏差的齿轮游标尺。
它是由两套相互垂直的游标尺组成。
垂直游标尺用于控制测量部位(分度圆至齿顶圆)的弦齿高h f ,水平游标尺用于测量所测部位(分度圆)的弦齿厚实际)(f S 。
齿轮游标尺的分度值为0.02mm ,其原理和读数方法与普通游标尺相同。
图1 图2用齿轮游标尺测量齿厚偏差,是以齿顶圆为基础。
当齿顶圆直径为公称值时,直齿圆柱齿轮分度圆处的弦齿高f h 和弦齿厚f S 由图2可得:f h =h '+x =⎥⎦⎤⎢⎣⎡-+Z Zm m 090cos 12f S =Z Zm 090sin 式中 m ——齿轮模数(mm ); Z ——齿轮齿数。
当齿轮为变位齿轮且齿顶圆直径有误差时,分度圆处的弦齿高f h 和弦齿厚f S 应按下式计算:f h =)()24cos(12'--⎥⎦⎤⎢⎣⎡+-+e e f R R Ztg Zm m αξπf S =⎥⎦⎤⎢⎣⎡+Z Zm f2sin 4sin αξπ 式中ξ——移距系数;f α——齿形角;e R ——齿顶圆半径的公称值;'e R ——齿顶圆半径的实际值。
四、测量步骤1. 用外径千分尺测量齿顶圆的实际直径。
2. 计算分度圆处弦齿高f h 和弦齿厚f S (可从表1查出)。
3. 按f h 值调整齿轮游标尺的垂直游标尺。
4. 将齿轮游标尺置于被测齿轮上,使垂直游标尺的高度尺与齿顶相接触。
然后,移动水平游标尺的卡脚,使卡脚靠紧齿廓。
从水平游标尺上读出弦齿厚的实际尺寸(用透光法判断接触情况)。
5. 分别在圆周上间隔相同的几个轮齿上进行测量。
6. 按齿轮图样标注的技术要求,确定齿厚上偏差E sns 和下偏差E sni ,判断被测齿厚的适用性。
齿轮 齿形齿向测量说明书
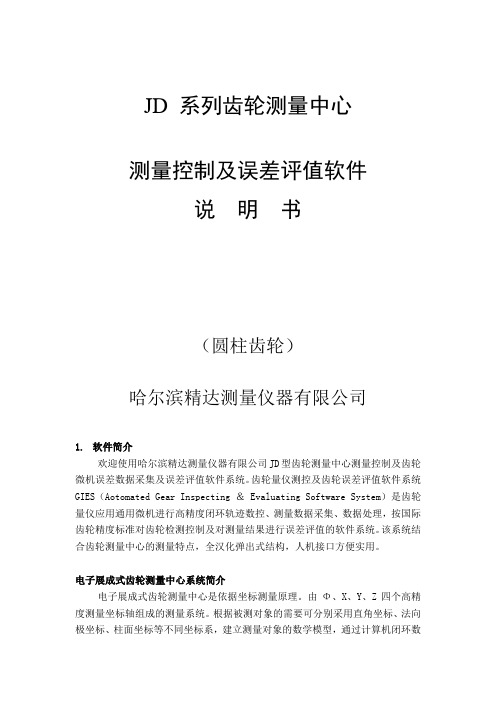
JD 系列齿轮测量中心测量控制及误差评值软件说明书(圆柱齿轮)哈尔滨精达测量仪器有限公司1.软件简介欢迎使用哈尔滨精达测量仪器有限公司JD型齿轮测量中心测量控制及齿轮微机误差数据采集及误差评值软件系统。
齿轮量仪测控及齿轮误差评值软件系统GIES(Aotomated Gear Inspecting & Evaluating Software System)是齿轮量仪应用通用微机进行高精度闭环轨迹数控、测量数据采集、数据处理,按国际齿轮精度标准对齿轮检测控制及对测量结果进行误差评值的软件系统。
该系统结合齿轮测量中心的测量特点,全汉化弹出式结构,人机接口方便实用。
电子展成式齿轮测量中心系统简介电子展成式齿轮测量中心是依据坐标测量原理。
由Φ、X、Y、Z四个高精度测量坐标轴组成的测量系统。
根据被测对象的需要可分别采用直角坐标、法向极坐标、柱面坐标等不同坐标系,建立测量对象的数学模型,通过计算机闭环数字控制,插补实现测量头的空间轨迹,由测微式测量头测量被测参数的实际误差、高速测量数据采集,并由计算机测量软件完成测量数据分析,按照齿轮误差理论及齿轮精度标准对测量数据进行误差评值、生成测量报告、输出测量结果,对齿轮加工机床进行调整或对齿轮质量进行验收。
图1-1是齿轮测量中心系统组成1、测量主机2、计算机系统3、打印机4、微机工作台GIES软件系统的特点1)全自动控制仪器测量动作、数据采集、误差补偿、测量结果误差评值及测量结果输出等功能;2)通用弹出式菜单完成测量参数输入、测量方式设置、误差评值标准选择,测量数据存盘等功能,屏幕显示彩色测量报告单;3)根据输入齿轮基本参数(齿数、模数、压力角、变位系数等)自动计算出测量评定长度等测量数据、可自动和人工选择长度和误差放大比;4)手工选齿、四分或三分左右面测量及测量结果存盘、打印;按GB10095-2001标准、ISO标准、或其他可选的齿轮标准(如DIN、ANSI/AGMA等)对凸形、修缘等设计齿形、齿向、齿距进行误差评值;具有齿廓、螺旋线修缘量及修缘长度评定功能;5)可对被测齿轮的受检范围精确确定,微机自动确定起测、起评、终评、终测四点位置,其中齿形测量起评位置按标准齿条啮合确定,并且误差评定范围可由用户根据图纸或测量要求在菜单上改变;6)齿廓、螺旋线误差测量结果评定位置(起评、终评点)可以在屏幕上方便改变,重新设定;7)具有“K”形框图误差评定功能;8)具有“三压力角”误差评定功能;9)精度等级评定按照 GB10095-2001标准、ISO标准,预先确定精度等级,对超差误差项目作出标记;10)激光打印机输出测量结果(误差曲线及数值),可选择输出各种国际通用格式或用户要求格式的齿轮测量报告单;11)按用户要求特殊提供测量软件输出格式(如在测量报告单上输出用户方厂名、名标及产品编号、日期、检验员签字等);硬件组成:1)精密测量主机(圆回转转台及X、Y、Z直线坐标舟);2)测微式测量传感器、高精度光栅编码;3)CNC闭环数控系统;4)系统微机及激光针打印机;5)数据采集电路(光栅记数、A/D转换、接口);软件功能齿轮:齿廓(Fα、ffα、fHα、Cα)、螺旋线(Fβ、ffβ、fHβ、Cβ)、齿距(fpt、fu、Fp)、径跳(Fr);2.软件结构分类.软件系统所要求的软、硬件环境:JD型齿轮测量软件系统所要求的硬件环境为 PII、128M内存以上的微机系统,软件应采用MS-DOS 以上版本。
插齿时产生误差的原因与消除方法

2)刀具本身制造误差和安装偏心或倾斜
3)径向进刀机构不稳
4)工作台的摆动及让刀不稳定
修理刀架系统,使其恢复原有精度。修理径向进刀机构。调整工作台让刀机构及检查刀具安装情况
1)工件定位心轴须与工作台旋转中心重合
2)工件孔与工件定位心轴的配合要适合,不能太松
3)工件的两端面须平行,安装时工件端面须与安装孔垂直
4)工件垫的两平面须平行,不得有铁屑污物粘着,检查工件定位心轴的精度,并加以修正或更换新件
工件齿面的表面粗糙度变粗
1)机床传动链的精度不高或磨损后间隙过大,某些环节在运动中出现振动或冲击以致影响机床传动平稳性
调整工作台或刀架体的分度蜗杆。正确安装工件和刀具,并准确调整工作台主轴和主轴孔的配合
齿形误差
1)插齿刀刃磨不好,存在齿形误差和前角偏差
2)分度蜗杆轴向窜动过大或其他传动链零件精度太低,造成运动误差
3)工作台有较大的径向圆跳动
4)插齿刀主轴端面圆跳动(安装插齿刀部分)超差5)插齿刀安装后有径向与端面圆跳动
2)工作台主轴配合面接触情况不好,接触过紧,工作台转动沉重,磨擦发热,运转时产生振动;接触松,运转时工作台游动
3)分度蜗杆的轴向窜动或分度蜗杆蜗轮的啮合间隙过大,运转中产生振动
4)让刀机构工作不正常,回程时刮伤工件齿面
5)插齿刀刃磨不好或切削刃磨钝,使齿面有撕裂现象
6)进给量太大
7)工件和刀具安装不紧,切削时产生振动
插齿时产生误差的原因与消除方法
误差项目
1)工作台或刀架蜗杆副中蜗杆的轴向齿距误差相安装偏心,分度蜗杆轮的周节偏差
2)插齿刀的齿距偏差
3)工件和刀具的安装偏心
4)刀架体固定导轨和滑动导轨由于磨损不均匀,致使插齿刀运动轨迹不正确
齿轮齿形齿向测量说明书

齿轮齿形齿向测量说明书-CAL-FENGHAI.-(YICAI)-Company One1JD 系列齿轮测量中心测量控制及误差评值软件说明书(圆柱齿轮)哈尔滨精达测量仪器有限公司1.软件简介欢迎使用哈尔滨精达测量仪器有限公司JD型齿轮测量中心测量控制及齿轮微机误差数据采集及误差评值软件系统。
齿轮量仪测控及齿轮误差评值软件系统GIES(Aotomated Gear Inspecting & Evaluating Software System)是齿轮量仪应用通用微机进行高精度闭环轨迹数控、测量数据采集、数据处理,按国际齿轮精度标准对齿轮检测控制及对测量结果进行误差评值的软件系统。
该系统结合齿轮测量中心的测量特点,全汉化弹出式结构,人机接口方便实用。
电子展成式齿轮测量中心系统简介电子展成式齿轮测量中心是依据坐标测量原理。
由Φ、X、Y、Z四个高精度测量坐标轴组成的测量系统。
根据被测对象的需要可分别采用直角坐标、法向极坐标、柱面坐标等不同坐标系,建立测量对象的数学模型,通过计算机闭环数字控制,插补实现测量头的空间轨迹,由测微式测量头测量被测参数的实际误差、高速测量数据采集,并由计算机测量软件完成测量数据分析,按照齿轮误差理论及齿轮精度标准对测量数据进行误差评值、生成测量报告、输出测量结果,对齿轮加工机床进行调整或对齿轮质量进行验收。
图1-1是齿轮测量中心系统组成1、测量主机2、计算机系统3、打印机4、微机工作台GIES软件系统的特点1)全自动控制仪器测量动作、数据采集、误差补偿、测量结果误差评值及测量结果输出等功能;2)通用弹出式菜单完成测量参数输入、测量方式设置、误差评值标准选择,测量数据存盘等功能,屏幕显示彩色测量报告单;3)根据输入齿轮基本参数(齿数、模数、压力角、变位系数等)自动计算出测量评定长度等测量数据、可自动和人工选择长度和误差放大比;4)手工选齿、四分或三分左右面测量及测量结果存盘、打印;按GB10095-2001标准、ISO标准、或其他可选的齿轮标准(如DIN、ANSI/AGMA等)对凸形、修缘等设计齿形、齿向、齿距进行误差评值;具有齿廓、螺旋线修缘量及修缘长度评定功能;5)可对被测齿轮的受检范围精确确定,微机自动确定起测、起评、终评、终测四点位置,其中齿形测量起评位置按标准齿条啮合确定,并且误差评定范围可由用户根据图纸或测量要求在菜单上改变;6)齿廓、螺旋线误差测量结果评定位置(起评、终评点)可以在屏幕上方便改变,重新设定;7)具有“K”形框图误差评定功能;8)具有“三压力角”误差评定功能;9)精度等级评定按照 GB10095-2001标准、ISO标准,预先确定精度等级,对超差误差项目作出标记;10)激光打印机输出测量结果(误差曲线及数值),可选择输出各种国际通用格式或用户要求格式的齿轮测量报告单;11)按用户要求特殊提供测量软件输出格式(如在测量报告单上输出用户方厂名、名标及产品编号、日期、检验员签字等);硬件组成:1)精密测量主机(圆回转转台及X、Y、Z直线坐标舟);2)测微式测量传感器、高精度光栅编码;3)CNC闭环数控系统;4)系统微机及激光针打印机;5)数据采集电路(光栅记数、A/D转换、接口);软件功能齿轮:齿廓(Fα、f fα、f Hα、Cα)、螺旋线(Fβ、f fβ、f Hβ、Cβ)、齿距(fpt、fu、Fp)、径跳(Fr);2.软件结构分类.软件系统所要求的软、硬件环境:JD型齿轮测量软件系统所要求的硬件环境为 PII、128M内存以上的微机系统,软件应采用MS-DOS 以上版本。