光学冷加工毕业设计
光学专业毕业设计:激光光斑尺寸的测量和研究.

激光光斑尺寸的测量和研究摘要激光光斑尺寸是标志激光器性能的重要参数,也是激光器在应用中的重要参量。
本文主要介绍了两种测量激光光斑尺寸的方法:刀口扫描法,CCD 法。
分析了利用刀口法测量高斯光束腰斑大小的测量实验装置,并阐述了具体的测量过程。
此方法对激光光斑大小测量是可行的。
实验装置简单实用。
CCD法是利用CCD作为探测传感器,可以更精确地测出激光器的光斑尺寸和束腰光斑尺寸,克服了传统测量的繁杂过程,并用计算机控制及数据处理,测量精度得到提高,为激光器性能研究和光信息处理提供了一种新的方法。
本文给出了这两种方法测得的数据及处理结果。
结果表明,刀口扫描法对高能量光束半径的测量特别实用,装置简单,可在普通实验室进行测量。
CCD法检测的直观性好,不需要辅助的逐行扫描机械移动,成像精度和检测精度高。
关键词激光光斑尺寸;Matlab;CCD传感器;刀口法The Measurement and Research of Laser SpotSizeAbstractThe size of Laser spot is not only one important parameter of laser performance, but also in laser application.This paper introduces two methods of measuring laser spot diameter: scanning method, CCD: knife method. We analyze of measurement is cut the size of the gaussian beam waist measurement device spot, and elaborates on process of the measurement. Using this method of laser spot size measurement is feasible. The experiment device is simple and practical. CCD method uses the CCD sensor as a detection can be more accurate to measure the size of the laser spot and waist size spot, overcoming traditional measurement process and using computer control to deal with data processing, and the measurement accuracy is improved, providing a new method for laser performance study and light information processing. At the same time, it gives two methods of measured data and processing results.The results show that the method of blade scanning is practical for high-energy beams radius’s measurement. Simple device can be operated in ordinary laboratory. CCD detection method is visually good, and do not need to manufacture progress ive-scan auxiliary of the machine movement, the imaging accuracy and precision is the higherKeywords Laser spot size; Matlab; CCD sensor; knife-edge method.哈尔滨理工大学学士学位论文目录摘要 (I)Abstract (II)第1章绪论 (4)1.1 课题背景 (4)1.2 国内外研究现状 (5)1.3 论文研究的内容 (7)第2章激光光斑测量方法探究 (8)2.1 刀口扫描法测激光光斑直径研究 (8)2.2 CCD测激光光斑直径方法 (12)2.3 本章小结 (20)第3章激光光斑尺寸的测量与数据分析 (21)3.1 刀口法测光斑直径 (21)3.1.1 90/10刀口法理论及方法 (21)3.1.2 计算理论 (23)3.1.3 实验数据处理 (23)3.1.4 实验分析 (25)3.2 CCD法测激光光斑方法 (25)3.2.1 用CCD拍摄光斑图像 (25)3.2.2 Matlab的图片处理 (26)3.2.3 图像处理结果 (26)3.2.4 实验分析 (29)3.3 本章小结 (30)结论 (31)致谢 (32)参考文献 (33)附录A 英文原文 (34)附录B 中文译文 (38)附录C Matlab程序 (42)第1章绪论1.1课题背景激光技术对国民经济及社会发展有着重要作用,激光技术是二十世纪与原子能、半导体及计算机齐名的四项重大发明之一。
光学冷加工工艺流程

光学冷加工工艺流程光学冷加工是一种利用激光技术进行加工的方法,它可以在材料表面形成微小的热效应区域,通过控制激光加热时间和能量密度,实现材料的冷加工。
光学冷加工广泛应用于精密加工、微纳加工和光学元件制备等领域,具有高效、高精度和无损伤等优点。
光学冷加工的工艺流程主要包括以下几个步骤:1. 材料准备:首先需要选择适合光学冷加工的材料,常见的材料有金属、陶瓷、玻璃等。
对于需要进行精密加工的材料,还需要进行表面处理,以消除材料的氧化层和污染物。
2. 激光加工参数设置:根据具体的加工要求,需要设置激光的加热时间和能量密度。
加热时间和能量密度的选择需要考虑材料的热导率、熔点和热膨胀系数等因素。
3. 激光加工设备调试:将激光加工设备进行调试,确保激光的功率和焦点等参数满足要求。
同时,还需要保证加工设备的稳定性和安全性,以防止意外事故的发生。
4. 加工操作:将待加工的材料放置在加工平台上,并通过光学系统将激光聚焦在材料表面。
激光加热后,材料会在短时间内形成微小的热效应区域。
在这个过程中,需要保持激光加工头与材料表面的距离恒定,并控制激光加热时间和能量密度,以控制热效应区域的形成和扩散。
5. 加工结果检验:完成加工后,需要对加工结果进行检验。
通常可以通过显微镜观察材料表面的形貌和微观结构变化,并使用精密测量仪器对加工尺寸进行测量。
如果加工结果符合要求,即可进行下一步的处理;如果加工结果不理想,可以调整加工参数进行再次加工。
光学冷加工工艺流程的关键在于控制激光加热时间和能量密度,以及保持激光加工头与材料表面的距离恒定。
这样可以控制材料的热效应区域,实现微小区域的冷加工。
同时,光学冷加工还可以利用光学系统的特性,实现对材料的精密加工和微纳加工。
光学冷加工具有高效、高精度和无损伤等优点,广泛应用于光学元件制备、微电子器件制备和材料表面处理等领域。
综上所述,光学冷加工工艺流程包括材料准备、激光加工参数设置、激光加工设备调试、加工操作和加工结果检验等步骤。
毕业设计光学设计软件OSLO的应用
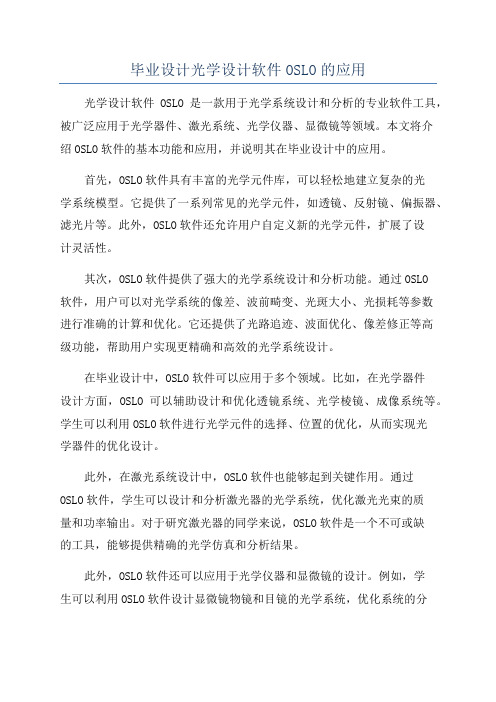
毕业设计光学设计软件OSLO的应用光学设计软件OSLO是一款用于光学系统设计和分析的专业软件工具,被广泛应用于光学器件、激光系统、光学仪器、显微镜等领域。
本文将介绍OSLO软件的基本功能和应用,并说明其在毕业设计中的应用。
首先,OSLO软件具有丰富的光学元件库,可以轻松地建立复杂的光学系统模型。
它提供了一系列常见的光学元件,如透镜、反射镜、偏振器、滤光片等。
此外,OSLO软件还允许用户自定义新的光学元件,扩展了设计灵活性。
其次,OSLO软件提供了强大的光学系统设计和分析功能。
通过OSLO软件,用户可以对光学系统的像差、波前畸变、光斑大小、光损耗等参数进行准确的计算和优化。
它还提供了光路追迹、波面优化、像差修正等高级功能,帮助用户实现更精确和高效的光学系统设计。
在毕业设计中,OSLO软件可以应用于多个领域。
比如,在光学器件设计方面,OSLO可以辅助设计和优化透镜系统、光学棱镜、成像系统等。
学生可以利用OSLO软件进行光学元件的选择、位置的优化,从而实现光学器件的优化设计。
此外,在激光系统设计中,OSLO软件也能够起到关键作用。
通过OSLO软件,学生可以设计和分析激光器的光学系统,优化激光光束的质量和功率输出。
对于研究激光器的同学来说,OSLO软件是一个不可或缺的工具,能够提供精确的光学仿真和分析结果。
此外,OSLO软件还可以应用于光学仪器和显微镜的设计。
例如,学生可以利用OSLO软件设计显微镜物镜和目镜的光学系统,优化系统的分辨率和放大倍数。
对于需要进行光学测量或观察的毕业设计项目来说,OSLO软件可以提供非常重要的帮助。
综上所述,光学设计软件OSLO在毕业设计中具有广泛的应用。
它提供了丰富的光学元件库和强大的设计分析功能,能够帮助学生进行复杂光学系统的设计和优化。
因此,对于从事光学相关领域的毕业设计项目来说,OSLO软件是必不可少的工具。
通过合理的使用OSLO软件,学生可以更好地完成光学器件、激光系统、光学仪器等方面的设计任务。
光学冷加工的工艺流程

光学冷加工的工艺流程光学冷加工是一种高精密度、高表面质量的精密加工技术。
它通过使用激光光束或电子束来对工件进行局部熔化或蒸发,然后再利用凝固后的残余热进行表面精密加工。
光学冷加工技术在微纳米加工领域具有广泛的应用,主要包括微纳米精密加工、微纳米表面处理和微纳米结构制备等方面。
光学冷加工的工艺流程可以分为以下几个步骤:首先是工件的装夹与定位。
在进行光学冷加工之前,需要将工件进行装夹,并对其进行精确定位,以保证加工的精度和稳定性。
其次是光源的选择和调节。
在光学冷加工中,通常会选择激光光束或电子束作为加工源,需要根据具体的加工任务选择合适的光源,并对其进行调节和优化。
接下来是能量传递和局部加热。
在光学冷加工中,光束或电子束会对工件表面进行局部加热,使其局部熔化或蒸发。
然后是凝固和形成残余热。
在加热后,工件表面会迅速凝固,形成残余热。
最后是残余热的利用和表面精密加工。
利用残余热对工件表面进行精密加工,例如去除表面残余材料、形成微纳米结构等。
总的来说,光学冷加工的工艺流程包括装夹定位、光源选择调节、能量传递局部加热、凝固形成残余热和残余热利用表面精密加工。
这个工艺流程是非常复杂的,需要对设备和工艺参数进行精确控制,以保证加工的精度和质量。
下面我们将从光学冷加工的原理、应用和发展趋势等几个方面对其进行更详细的介绍。
首先是光学冷加工的原理。
光学冷加工是基于光热效应的一种加工技术。
光热效应是指当光束或电子束照射到物体表面时,光能或电子能被吸收,导致局部温度的升高。
在光学冷加工中,光束或电子束通过对工件表面进行局部加热,使其局部熔化或蒸发,然后利用凝固后的残余热进行表面精密加工。
这种加工方式具有高精度、高表面质量和高加工效率的优点,特别适用于微纳米加工领域。
光学冷加工技术在微纳米加工领域具有广泛的应用。
它可以用于微纳米精密加工,例如微孔加工、微型器件加工等;还可以用于微纳米表面处理,例如表面改性、表面粗糙度调控等;还可以用于微纳米结构制备,例如微纳米结构的形成、微纳米光栅的制备等。
光学冷加工工艺流程

光学冷加工工艺流程
《光学冷加工工艺流程》
光学冷加工是一种高精度、高效率的先进加工工艺,它通过激光或光纤激光束来加工材料,可实现微米级甚至亚微米级的加工精度。
下面我们来介绍一下光学冷加工的工艺流程。
首先,工件的表面要进行预处理,包括清洗、除油等,以确保激光束能够顺利地照射到工件表面。
其次,选择合适的激光加工设备,根据工件的材料和加工要求来确定激光功率、频率、加工速度等参数。
然后,将工件放置在加工台上,调整激光束的焦距和聚焦点位置,使其能够准确地照射到工件表面。
接下来,启动激光加工设备,激光束照射到工件表面后,可以选择不同的加工模式,如脉冲激光加工、连续激光加工等,根据具体的加工要求进行调整。
在加工过程中,监控工件表面的温度和形变情况,及时调整激光参数,以确保加工的精度和质量。
最后,完成加工后,对工件表面进行清洗、除渣等处理,然后进行质量检测,确保加工的精度和质量达到要求。
总而言之,光学冷加工工艺流程包括预处理、选型、调整、加
工和后处理等多个环节,只有严格按照流程操作,才能实现高精度、高效率的加工。
希望通过不断的技术创新和工艺改进,光学冷加工能够在更广泛的领域得到应用,为制造业的发展贡献更大的力量。
光学冷加工抛光技术

光学冷加工抛光技术
光学冷加工抛光技术是一种利用光学原理进行表面修整和抛光的高精度加工方法。
相比传统的机械抛光,光学冷加工抛光技术具有以下优势:
1. 高精度: 光学冷加工抛光技术可以达到亚纳米级的表面精度,适用于高要求的光学元件和器件的加工。
2. 无接触: 光学冷加工抛光技术利用光束进行加工,不需要与
工件接触,避免了机械抛光可能带来的刮擦和损伤。
3. 无热效应: 光学冷加工抛光技术在抛光过程中不会产生热量,避免了传统热加工可能引起的热应力和热变形问题。
4. 高效率: 光学冷加工抛光技术可以同时对多个表面进行加工,提高了加工效率。
光学冷加工抛光技术的基本原理是利用光束的聚焦和控制来进行表面修整和抛光。
通过调整光束的聚焦参数,可以控制加工深度和加工形状,从而实现精确的表面加工。
光学冷加工抛光技术在光学器件制造、半导体加工、精密机械加工等领域有着广泛的应用。
它不仅可以提高光学元件和器件的质量和性能,还可以降低制造成本和提高生产效率。
光学设计论文
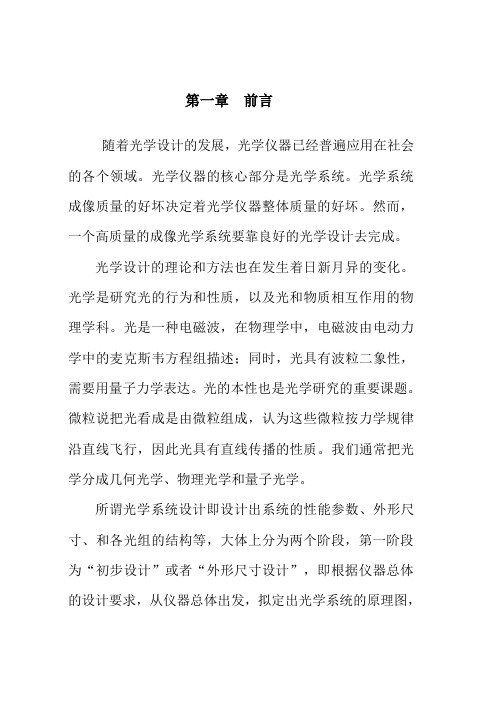
第一章前言随着光学设计的发展,光学仪器已经普遍应用在社会的各个领域。
光学仪器的核心部分是光学系统。
光学系统成像质量的好坏决定着光学仪器整体质量的好坏。
然而,一个高质量的成像光学系统要靠良好的光学设计去完成。
光学设计的理论和方法也在发生着日新月异的变化。
光学是研究光的行为和性质,以及光和物质相互作用的物理学科。
光是一种电磁波,在物理学中,电磁波由电动力学中的麦克斯韦方程组描述;同时,光具有波粒二象性,需要用量子力学表达。
光的本性也是光学研究的重要课题。
微粒说把光看成是由微粒组成,认为这些微粒按力学规律沿直线飞行,因此光具有直线传播的性质。
我们通常把光学分成几何光学、物理光学和量子光学。
所谓光学系统设计即设计出系统的性能参数、外形尺寸、和各光组的结构等,大体上分为两个阶段,第一阶段为“初步设计”或者“外形尺寸设计”,即根据仪器总体的设计要求,从仪器总体出发,拟定出光学系统的原理图,并初步计算系统的外形尺寸,以及系统中各部分要求的光学特性。
第二阶段称为“像差设计”,一般称为“光学设计”,即根据初步设计的结果,确定每个透镜的具体结构参数,以保证满足系统光学特性和成型质量成像质量的要求。
一个光学仪器工作性能的优劣,初步设计是关键,当然在初步设计合理的条件下,如果像差设计不当,同样也可能造成不良后果。
一个好的设计应该是在满足使用要求的情况下,结构设计最简单的系统。
光学设计是20世纪发展起来的一门学科,至今已经经历了一个漫长的过程。
光学系统设计的具体过程:制定合理的技术参数,光学系统总体设计和布局,光组的设计(包括选型,初始结构的计算,像差校正、平衡与像质评价),长光路的拼接与统算,绘制光学系统图、部件图和零件图,编写设计说明书,进行技术答辩。
光学设计的设计步骤为选择系统的类型,分配元件的光焦度,校正初始像差,减小残余像差(高级像差)。
重复以上步骤,最终会找到一个满意结果。
本次设计主要采用ZEMAX光学设计软件已经专门的绘图软件、撰写公式的软件。
光学冷加工抛光技术

光学冷加工抛光技术引言:光学冷加工抛光技术是一种先进的表面加工技术,可以在不增加材料温度的情况下,提高材料表面质量和精度。
本文将对光学冷加工抛光技术进行详细介绍,并探讨其在工业制造领域的应用前景。
一、光学冷加工抛光技术的原理光学冷加工抛光技术是利用激光在材料表面产生微观热效应,通过控制激光参数和加工条件,实现对材料表面的微观结构调控和去除。
具体来说,光学冷加工抛光技术利用高能激光束对材料表面进行扫描,产生微小的熔融区域和快速冷却,使材料表面的微观结构发生变化,从而实现抛光效果。
二、光学冷加工抛光技术的优势1. 高效性:光学冷加工抛光技术可以快速去除材料表面的缺陷和粗糙度,大大提高加工效率。
2. 精度高:光学冷加工抛光技术可以实现对材料表面微观结构的精细调控,从而获得高精度的表面质量。
3. 热影响小:光学冷加工抛光技术在加工过程中不会增加材料的温度,避免了热引起的变形和损伤。
4. 环保性:光学冷加工抛光技术不需要使用化学溶剂和磨料,减少了对环境的污染。
三、光学冷加工抛光技术的应用领域1. 光学元件制造:光学冷加工抛光技术可以用于制造光学镜面、透镜等光学元件,提高其表面质量和光学性能。
2. 精密机械制造:光学冷加工抛光技术可以应用于精密机械零件的加工,如航空航天器件、半导体器件等,提高其表面质量和加工精度。
3. 光纤通信:光学冷加工抛光技术可以用于光纤端面的加工,提高光纤的传输效率和信号质量。
4. 光学薄膜涂层:光学冷加工抛光技术可以用于光学薄膜涂层的制备,提高薄膜的平整度和光学性能。
四、光学冷加工抛光技术的发展趋势1. 多波长激光应用:将多种波长的激光进行组合,可以实现对不同材料的高效抛光。
2. 全自动化加工系统:引入机器视觉和自动控制技术,实现光学冷加工抛光技术的全自动化生产。
3. 远程加工能力:通过激光束传输技术,实现对远程材料的抛光加工,拓展了应用范围。
4. 材料适应性提高:研发新的材料适应性加工方法,扩大光学冷加工抛光技术的适用范围。
- 1、下载文档前请自行甄别文档内容的完整性,平台不提供额外的编辑、内容补充、找答案等附加服务。
- 2、"仅部分预览"的文档,不可在线预览部分如存在完整性等问题,可反馈申请退款(可完整预览的文档不适用该条件!)。
- 3、如文档侵犯您的权益,请联系客服反馈,我们会尽快为您处理(人工客服工作时间:9:00-18:30)。
河南工业职业技术学院 第 1 页 共 31 页 河 南 工 业 职 业 技 术 学 院 Henan Polytechnic Institute 毕业设计(论文)
题 目光学零件精磨加工工艺 班 级 精密 0601 姓 名 崔 四 海 指导教师
黄 长 春
河南工业职业技术学院
第 2 页 共 31 页 目录
摘要................................................................................................................................ 4 前言................................................................................................................................ 4 一 精磨的目的.............................................................................................................. 6 二 精磨的方法.............................................................................................................. 7 2.1散粒磨料精磨法...................................................................................................... 7 2.1.1精磨模的修整....................................................................................................... 7 2.1.2精磨工艺............................................................................................................... 8 2.1.3精磨机的精磨原理............................................................................................. 10 2.1.4 精磨的四大重点................................................................................................ 11 2.2金刚石磨具精磨.................................................................................................... 12 2.2.1金刚石磨具的制作............................................................................................. 13 3.1实际工作中精磨遇见的问题与解决方法............................................................ 16 四 冷却液.................................................................................................................... 17 五 金刚石精磨工艺因素的选择................................................................................ 18 六 面检........................................................................................................................ 19 6.1光圈概述................................................................................................................ 19 6.2光圈检验................................................................................................................ 19 6.2.1面本数与亚斯的计算方法................................................................................. 19 6.2.2原器检面注意事项............................................................................................. 19 6.3光圈的识别............................................................................................................ 19 6.4高低光圈的识别方法............................................................................................ 20 6.5光圈的度量............................................................................................................ 20 6.6 面形检测............................................................................................................... 20 七 精磨(抛光)检验................................................................................................ 22 7.1 线性尺寸检验....................................................................................................... 22 7.1.1 透镜中心厚度的检验........................................................................................ 22 7.1.2 棱镜理论高度................................................................................................... 22 河南工业职业技术学院 第 3 页 共 31 页 7.2 表面疵病检验...................................................................................................... 22 7.2.1 观察法................................................................................................................ 22 7.2.2 表面疵病的鉴别................................................................................................ 23 7.3光学零件的基本量测量..................................................................................... 23 7.3.1光学面形检测.................................................................................................. 23 7.3.2 曲率半径的测量............................................................................................. 23 八 模具检测与修整.................................................................................................. 24 8.1 精磨本体模凹模的检测和修整........................................................................... 24 九 任务书设计............................................................................................................ 25 1)精磨本体模的设计................................................................................................ 25 2)修模的设计............................................................................................................ 25 3)套圈的设计............................................................................................................ 25 4) 面本体的设计...................................................................................................... 25 5)面修模的设计........................................................................................................ 26 6) 面套圈的设计...................................................................................................... 26 结论.............................................................................................................................. 27 致谢.............................................................................................................................. 28 参考文献...................................................................................................................... 29