大型机床床身铸造工艺研究
机床床身铸造加工工艺流程
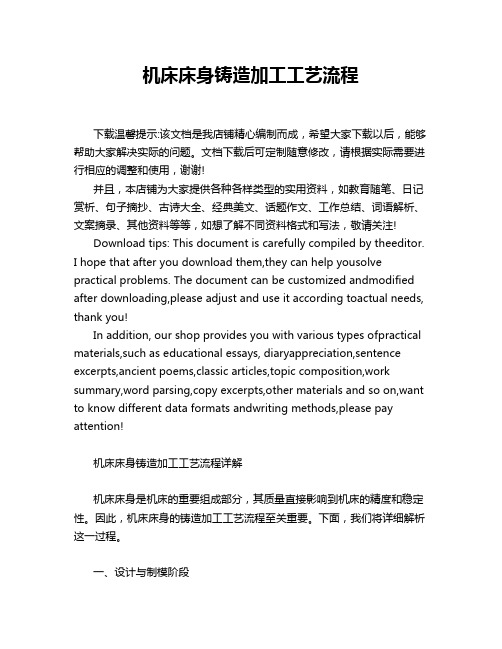
机床床身铸造加工工艺流程下载温馨提示:该文档是我店铺精心编制而成,希望大家下载以后,能够帮助大家解决实际的问题。
文档下载后可定制随意修改,请根据实际需要进行相应的调整和使用,谢谢!并且,本店铺为大家提供各种各样类型的实用资料,如教育随笔、日记赏析、句子摘抄、古诗大全、经典美文、话题作文、工作总结、词语解析、文案摘录、其他资料等等,如想了解不同资料格式和写法,敬请关注!Download tips: This document is carefully compiled by theeditor.I hope that after you download them,they can help yousolve practical problems. The document can be customized andmodified after downloading,please adjust and use it according toactual needs, thank you!In addition, our shop provides you with various types ofpractical materials,such as educational essays, diaryappreciation,sentence excerpts,ancient poems,classic articles,topic composition,work summary,word parsing,copy excerpts,other materials and so on,want to know different data formats andwriting methods,please pay attention!机床床身铸造加工工艺流程详解机床床身是机床的重要组成部分,其质量直接影响到机床的精度和稳定性。
大型机床床身铸造工艺设计研究

大型机床床身铸造工艺研究摘要:简述大型机床床身的特点、要求及铸造难度;阐述该类铸件的造型方法,工艺参数的选取,浇注系统设计、熔炼浇注工艺;介绍了一种简易的组箱组芯铸造工艺;对容易产生的导轨变形、砂芯漂芯、组织疏松、硬度低、硬质点及淬火问题等重点缺陷进行了原因分析并提出了防止措施。
关键词:大型机床床身,组箱组芯,铸造缺陷,铸造工艺目前国产大型机床包括车床、铣床、刨床、磨床、数控机床等各类机床床身铸件的壁厚一般在20~40mm,属于中厚壁铸件,重量一般在5~50t,材质为HT250或HT300。
该类铸件的最大特点是导轨较长,一般在几米甚至十几米,非常容易产生弯曲变形,且导轨非常厚大,一般在40~100mm,导轨容易产生组织缺陷,特别是10m长的导轨要保证无任何气孔砂眼也是较困难的。
该类铸件往往是单件小批量生产,没有现成的工装砂箱,投资较大,特别是数控机床床身,结构形状比较复杂,在模样制作、砂芯紧固、等造型操作方面存在较大难度;其材质要求具有良好的精度稳定性、抗压强度和减震性,良好的切削性能和铸造性能,其硬度要求180~241HB,硬度差△HB≤35[1],有些采用淬火硬化的机床导轨要求HT300以上牌号,易产生组织疏松、硬度低、硬质点及淬火效果差等缺陷,一旦因为这些问题导致铸件报废,损失非常惨重,因此很有必要进行专门研究。
1造型工艺1.1造型方法的选择首先要生产该类件需有专用工装,一般铸造厂无此专用工装,而且该类件往往都是定单制作,批量不大,没有规模效益。
所以要生产该类件所投工装砂箱费用比铸件的价值还要大,一旦导轨等重要部位出现重大缺陷造成废品,那损失更是不可估量。
因此铸造厂做此类铸件有时得不偿失,而且10m多长的铸件需要10m多长的砂箱,对整铸式砂箱的强度和刚度要求也相当高,如果在吊装过程中发生折断砂箱的情况,造成人员伤亡,那更是雪上加霜。
因此如何生产此类铸件,非常值得探讨。
一般厂家采用地坑造型,但对于紧张的造型面积,地坑造型不是很合适,而采用简易的组箱组芯法较好地解决了这一问题,它可以有效利用车间面积。
高质量机床球铁铸件关键铸造工艺及应用

高质量机床球铁铸件关键铸造工艺及应用高质量机床球铁铸件是机床制造中重要的组成部分,其关键性能及应用需要通过精细的铸造工艺来保证。
本文将介绍机床球铁铸件的关键铸造工艺及其应用。
机床球铁铸件是机床的重要零部件,通常用于支撑机床的重要结构和机械传动部件。
这类铸件要求具有高韧性、高强度和高耐磨性能,以确保机床的稳定性和可靠性。
关键的铸造工艺之一是选择合适的球墨铸铁材料。
球墨铸铁是一种具有球状石墨微观结构的铸铁,具有良好的韧性和强度,适合用于机床铸件的制造。
在选择球墨铸铁材料时,需要考虑其热处理性能、可焊性和耐磨性等指标,以满足机床工作的要求。
关键的铸造工艺之一是铸件的液态铸造过程控制。
机床球铁铸件的制造通常采用砂模铸造工艺,其关键是控制铁液的浇注温度、浇注速度和冷却速度等参数。
适当的浇注温度能够保证铸件内部组织的致密性和均匀性,而适当的浇注速度和冷却速度能够控制铸件的凝固过程,避免铁液凝固时引起的缺陷和内部应力。
关键的铸造工艺还包括熔炼和浇注过程中的流动控制和铁液凝固过程的温度控制。
熔炼过程中,需要控制铁液中的杂质含量和化学成分,以确保铸件的组织和性能。
浇注过程中,需要通过适当的浇注口设计和浇注系统排气,避免铁液的气体夹杂和热震裂纹的产生。
凝固过程中,需要通过合理的冷却系统和完整的降温曲线,控制铸件的凝固收缩和铸件缺陷。
机床球铁铸件的应用广泛,涵盖了各种机床类型和工作环境。
机床床身和底座等结构件,需要具有高强度和高刚性,以承受机床的工作负荷。
机床的传动部件,如滚珠丝杠、导轨和工作台等,需要具有高韧性和耐磨性,以确保机床的运动精度和寿命。
机床球铁铸件还可以用于机床附件和变速箱等重要部件的制造。
高质量机床球铁铸件的关键铸造工艺包括合适的材料选择、液态铸造过程控制和流动控制等。
这些工艺的合理应用能够保证铸件的性能和质量,满足机床的工作要求。
机床球铁铸件的应用范围广泛,可应用于各种机床类型和工作环境。
在今后的机床制造中,铸造工艺的持续优化和高质量球铁铸件的制造将会成为关键的发展方向。
M224磨床大箱体铸件的铸造工艺探索
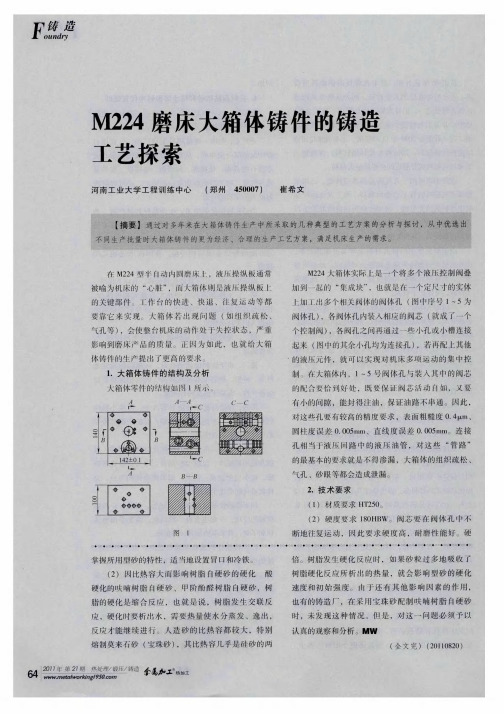
口颈在保 证 充分 的外 部 补 缩 的同 时 又 能在 适 当 的时 候及 时地 闸死 ,这 样 就 更 有 利 于铸 件 内石 墨 化 膨 胀 压 力 的 建 立 ,提 高 自补 缩 效 果 。正 是 这 种 自补 缩 , 使 用 较小 直 径 的 冒 口 ( 9 m  ̄ 0 m×12 m 冒 口两个 ) 5m , 即可保证 铸 件 不 产 生 缩 孔 缺 陷 。 冒 口离 开 热 节 又 靠 近 热节 ,充分 利 用 石 墨 化 膨 胀 增 加 铸 件 的 致 密 度 。 补 缩特 点 :① 依 靠 自身 补 缩 。 ②依 靠 冒 口 内金 属 液
以防造 成压力 油泄 漏 。
个 ,即可保证铸件不产生缩孔缺陷。此工艺最大的 优点是 冒口离开热节 ,但又靠近热节。同时 由于边
冒 口的 冒 口颈 窄 长 ,接 触 热 节 减 小 , 由 冒 口的 热 影
基 于此 ,大 阀体 铸 件 的铸 造 看 似 简 单 ,实 则 质 量 很难 控制 。 多年 来 ,我 们 在 大 阀体 的铸 造 工 艺 方 面进行 了大量 的探 索 ,取得 了较为 明显 的效果 。 l 上 — — Nhomakorabeaf 下
幽
3
1 ,冒口 2 .冒口颈
3 直浇道 4 横浇道 . .
方 案三 :应用 均 衡 凝 固理 论 ,采 用 热 飞 边 冒 口 工艺 。如 图 4 示 ,一坯 5 ,一 型两坯 铸造 ,在两 所 件
型腔之 间设 置浇 口 ,金 属 液 通 过 浇 口 、冒 口引 入 铸
图 2
件 ,与 方案 二不 同的是 :金 属液是 通过厚 6~8 m 的 m 飞边 冒 口进 入型 腔 ,冒 口距铸 件 l m O m左 右 。飞边 冒
高质量机床球铁铸件关键铸造工艺及应用

高质量机床球铁铸件关键铸造工艺及应用机床球铁铸件是机床行业中常见的零部件之一,其质量的优劣直接影响机床的性能和使用寿命。
本文将重点介绍高质量机床球铁铸件的关键铸造工艺及其应用。
一、关键铸造工艺1. 铸型设计铸型具有直接影响铸件质量的作用,合理的铸型设计能够提高铸件的成型性和凝固组织性,同时减少缺陷的产生。
在机床球铁铸件的铸型设计中,应根据零件的结构特点和使用条件合理确定孔洞、浇口和浇注系统等参数,并利用通风道和管道等布局优化砂芯的插入和气体的排除。
2. 铸型材料选择铸型材料的选择直接关系到铸件的表面质量和机械性能。
对于机床球铁铸件来说,一般采用石膏砂、湿型砂或酚醛砂等有机砂作为铸型材料,其具有良好的透气性和破碎性能,能够满足零件结构的需求。
3. 熔炼工艺控制熔炼工艺控制是保证铸件质量的重要环节。
在机床球铁铸件的铸造过程中,应控制铁水的温度、凝固时间和浇注速度等参数,尽可能减少合金元素的氧化和碳化,避免缺陷的产生。
同时还应对铁水进行脱气处理,降低氧含量和气孔率,提高铸件的强度和抗疲劳性能。
4. 凝固过程控制凝固过程控制对于机床球铁铸件的显微组织和性能具有重要影响。
在凝固过程中,应控制铸件的冷却速度和冷却方向,以避免铸件出现贝氏体组织、球墨铸铁中间铁相和残余渗碳体等不利于零件使用的组织结构。
5. 热处理技术对于机床球铁铸件来说,热处理是提高其性能的重要工艺。
一般采用正火、表面渗碳和淬火等热处理工艺,通过控制温度和时间,使铸件的硬度、强度和韧性达到设计要求。
6. 清理和表面处理清理和表面处理对机床球铁铸件的外观质量和耐腐蚀性能有直接影响。
在清理过程中,应去除铸件表面的氧化皮、油污和砂粒等杂质,保证铸件的光洁度和完整性。
同时还可以采用喷砂、镀镍和喷漆等表面处理工艺,提高铸件的表面硬度和耐腐蚀性。
二、应用领域机床球铁铸件广泛应用于各类机床设备中,如铣床、车床、磨床和钻床等。
其主要作用是支撑和定位机床的运动部件,保证机床的精度、稳定性和可靠性。
机床床身的铸造方法
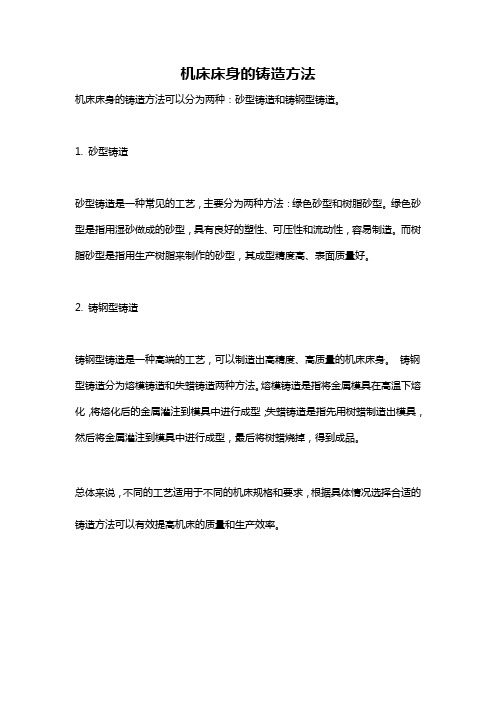
机床床身的铸造方法
机床床身的铸造方法可以分为两种:砂型铸造和铸钢型铸造。
1. 砂型铸造
砂型铸造是一种常见的工艺,主要分为两种方法:绿色砂型和树脂砂型。
绿色砂型是指用湿砂做成的砂型,具有良好的塑性、可压性和流动性,容易制造。
而树脂砂型是指用生产树脂来制作的砂型,其成型精度高、表面质量好。
2. 铸钢型铸造
铸钢型铸造是一种高端的工艺,可以制造出高精度、高质量的机床床身。
铸钢型铸造分为熔模铸造和失蜡铸造两种方法。
熔模铸造是指将金属模具在高温下熔化,将熔化后的金属灌注到模具中进行成型;失蜡铸造是指先用树蜡制造出模具,然后将金属灌注到模具中进行成型,最后将树蜡烧掉,得到成品。
总体来说,不同的工艺适用于不同的机床规格和要求,根据具体情况选择合适的铸造方法可以有效提高机床的质量和生产效率。
高质量机床球铁铸件关键铸造工艺及应用
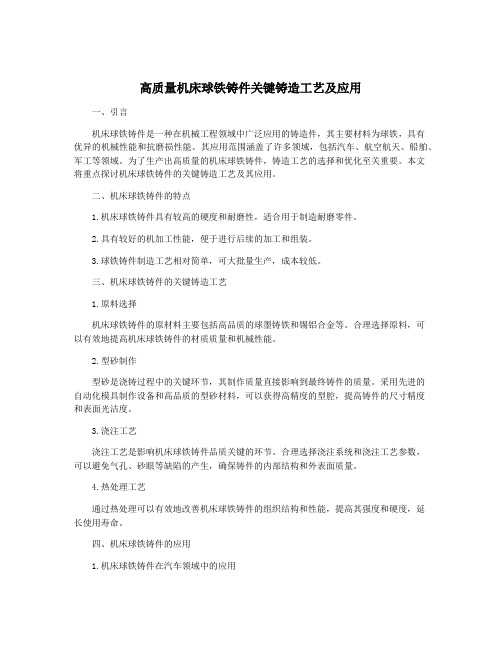
高质量机床球铁铸件关键铸造工艺及应用一、引言机床球铁铸件是一种在机械工程领域中广泛应用的铸造件,其主要材料为球铁,具有优异的机械性能和抗磨损性能。
其应用范围涵盖了许多领域,包括汽车、航空航天、船舶、军工等领域。
为了生产出高质量的机床球铁铸件,铸造工艺的选择和优化至关重要。
本文将重点探讨机床球铁铸件的关键铸造工艺及其应用。
二、机床球铁铸件的特点1.机床球铁铸件具有较高的硬度和耐磨性,适合用于制造耐磨零件。
2.具有较好的机加工性能,便于进行后续的加工和组装。
3.球铁铸件制造工艺相对简单,可大批量生产,成本较低。
三、机床球铁铸件的关键铸造工艺1.原料选择机床球铁铸件的原材料主要包括高品质的球墨铸铁和锡铝合金等。
合理选择原料,可以有效地提高机床球铁铸件的材质质量和机械性能。
2.型砂制作型砂是浇铸过程中的关键环节,其制作质量直接影响到最终铸件的质量。
采用先进的自动化模具制作设备和高品质的型砂材料,可以获得高精度的型腔,提高铸件的尺寸精度和表面光洁度。
3.浇注工艺浇注工艺是影响机床球铁铸件品质关键的环节。
合理选择浇注系统和浇注工艺参数,可以避免气孔、砂眼等缺陷的产生,确保铸件的内部结构和外表面质量。
4.热处理工艺通过热处理可以有效地改善机床球铁铸件的组织结构和性能,提高其强度和硬度,延长使用寿命。
四、机床球铁铸件的应用1.机床球铁铸件在汽车领域中的应用机床球铁铸件在汽车发动机缸体、缸盖、曲轴箱等关键零部件中得到广泛应用。
由于机床球铁铸件具有良好的机械性能和耐腐蚀性能,可以保证汽车发动机的高性能和长寿命。
2.机床球铁铸件在机械设备领域中的应用机床球铁铸件还广泛应用于各种机械设备,如数控机床、冲床、车床等。
机床球铁铸件能够提高这些设备的工作精度和稳定性,保证生产效率和产品质量。
3.机床球铁铸件在船舶和航空航天领域中的应用由于机床球铁铸件具有较高的硬度和耐磨性,能够满足船舶和航空航天领域对于耐磨零件的需求,如船舶发动机零部件、飞机发动机零部件等。
采用消失模铸造机床床身铸件的工艺探讨
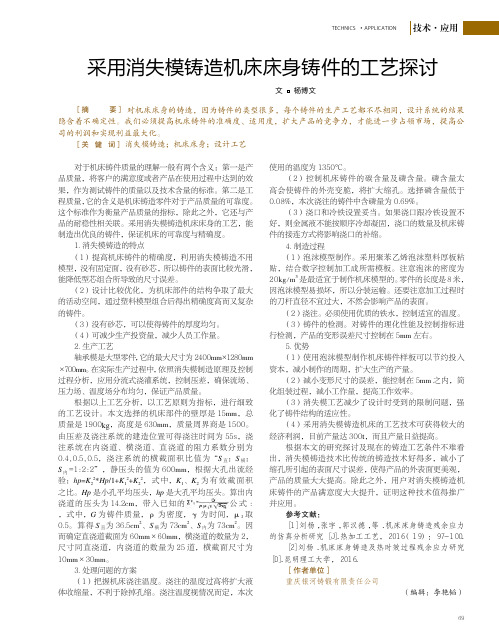
TECHNICS ·APPLICATION技术·应用文 杨博文采用消失模铸造机床床身铸件的工艺探讨对于机床铸件质量的理解一般有两个含义:第一是产品质量,将客户的满意度或者产品在使用过程中达到的效果,作为测试铸件的质量以及技术含量的标准。
第二是工程质量,它的含义是机床铸造零件对于产品质量的可靠度。
这个标准作为衡量产品质量的指标,除此之外,它还与产品的耐稳性相关联。
采用消失模铸造机床床身的工艺,能制造出优良的铸件,保证机床的可靠度与精确度。
1.消失模铸造的特点(1)提高机床铸件的精确度,利用消失模铸造不用模型,没有固定面,没有砂芯,所以铸件的表面比较光滑,能降低型芯组合所导致的尺寸误差。
(2)设计比较优化,为机床部件的结构争取了最大的活动空间,通过塑料模型组合后得出精确度高而又复杂的铸件。
(3)没有砂芯,可以使得铸件的厚度均匀。
(4)可减少生产投资量,减少人员工作量。
2.生产工艺轴承模是大型零件,它的最大尺寸为2400mm×1280mm ×700mm。
在实际生产过程中,依照消失模制造原理及控制过程分析,应用分流式浇灌系统,控制压差,确保流场、压力场、温度场分布均匀,保证产品质量。
根据以上工艺分析,以工艺原则为指标,进行细致的工艺设计。
本文选择的机床部件的壁厚是15mm,总质量是1900kg,高度是630mm,质量周界商是1500。
由压差及浇注系统的建造位置可得浇注时间为55s,浇注系统在内浇道、横浇道、直浇道的阻力系数分别为0.4,0.5,0.5,浇注系统的横截面积比值为“S直:S横:S内=1:2:2”,静压头的值为600mm,根据大孔出流经验:hp=K22*Hp/1+K12+K22,式中,K1、K2为有效截面积之比。
Hp是小孔平均压头,hp是大孔平均压头。
算出内浇道的压头为14.2cm,带入已知的公式: ,式中,G为铸件质量,ρ为密度,γ为时间,μ3取0.5。
- 1、下载文档前请自行甄别文档内容的完整性,平台不提供额外的编辑、内容补充、找答案等附加服务。
- 2、"仅部分预览"的文档,不可在线预览部分如存在完整性等问题,可反馈申请退款(可完整预览的文档不适用该条件!)。
- 3、如文档侵犯您的权益,请联系客服反馈,我们会尽快为您处理(人工客服工作时间:9:00-18:30)。
大型机床床身铸造工艺研究摘要:简述大型机床床身的特点、要求及铸造难度;阐述该类铸件的造型方法,工艺参数的选取,浇注系统设计、熔炼浇注工艺;介绍了一种简易的组箱组芯铸造工艺;对容易产生的导轨变形、砂芯漂芯、组织疏松、硬度低、硬质点及淬火问题等重点缺陷进行了原因分析并提出了防止措施。
关键词:大型机床床身,组箱组芯,铸造缺陷,铸造工艺目前国产大型机床包括车床、铣床、刨床、磨床、数控机床等各类机床床身铸件的壁厚一般在20~40mm,属于中厚壁铸件,重量一般在5~50t,材质为HT250或HT300。
该类铸件的最大特点是导轨较长,一般在几米甚至十几米,非常容易产生弯曲变形,且导轨非常厚大,一般在40~100mm,导轨容易产生组织缺陷,特别是10m长的导轨要保证无任何气孔砂眼也是较困难的。
该类铸件往往是单件小批量生产,没有现成的工装砂箱,投资较大,特别是数控机床床身,结构形状比较复杂,在模样制作、砂芯紧固、等造型操作方面存在较大难度;其材质要求具有良好的精度稳定性、抗压强度和减震性,良好的切削性能和铸造性能,其硬度要求180~241HB,硬度差△HB≤35[1],有些采用淬火硬化的机床导轨要求HT300以上牌号,易产生组织疏松、硬度低、硬质点及淬火效果差等缺陷,一旦因为这些问题导致铸件报废,损失非常惨重,因此很有必要进行专门研究。
1造型工艺1.1造型方法的选择首先要生产该类件需有专用工装,一般铸造厂无此专用工装,而且该类件往往都是定单制作,批量不大,没有规模效益。
所以要生产该类件所投工装砂箱费用比铸件的价值还要大,一旦导轨等重要部位出现重大缺陷造成废品,那损失更是不可估量。
因此铸造厂做此类铸件有时得不偿失,而且10m多长的铸件需要10m多长的砂箱,对整铸式砂箱的强度和刚度要求也相当高,如果在吊装过程中发生折断砂箱的情况,造成人员伤亡,那更是雪上加霜。
因此如何生产此类铸件,非常值得探讨。
一般厂家采用地坑造型,但对于紧张的造型面积,地坑造型不是很合适,而采用简易的组箱组芯法较好地解决了这一问题,它可以有效利用车间面积。
1.2组箱组芯法简介该工艺区别于传统的组箱组芯法(劈模造型)。
传统的劈模造型是将模样根据各个面的形状分成几部分,然后将这几部分固定在模板上,再用专用砂箱舂箱,舂完箱再将各面砂箱组起来,用螺栓紧固好,空腔用砂芯组合。
而新型组箱组芯法不用外模样,不用模板,直接将分段砂箱组合起来,在组合好后的砂箱内用砂芯直接组出铸件结构形状。
采用组箱组芯法制作专用工装,铸件结构形状全部用砂芯组合,重点要解决好砂箱组合起来的刚度问题,所以必须用螺栓连接,这是该件能够投产的前提条件。
对于分成若干段的总共长达十几米的砂箱,重点保证砂箱的强度和刚度的连续性,要求混砂速度快,舂砂也要跟上出砂的节奏,否则易出现砂型隔层裂纹等缺陷。
1.3该工艺的优缺点该工艺把砂箱做成不同规格( 1m、1.5m、2m、3m等)不同数量的几段,然后拼凑起各种长度和宽度不同的砂箱框,各段砂箱间用螺栓联结,满足不同长度和宽度的铸件需求,通用性强,一套工装可满足几种铸件的生产,工装费用大大降低,适用范围广,且操作方便,对砂箱的尺寸精度要求低。
该工艺将长达十几米的砂箱分成几段,减小每块砂箱的重量和尺寸大小,降低在行车吊装过程的危险性,可成功地避免这方面的安全事故,因为曾经发生几米长的砂箱在吊装过程中折断而发生危险的事情。
表1是组箱组芯法与传统方法的比较。
该方法缺点是要求操作人员的素质较高,操作过程尺寸精度的控制很大程度上依赖于操作人员的把握。
表1.组箱组芯法与传统方法的比较2工艺设计及过程控制2.1反变形量导轨面上留凸起的反变形量5~25mm不等,根据导轨长度确定:床身长度<5m,每1m铸件留1~2mm反变形量;床身长度>5m,每1m铸件留反变形量1.5~2.5mm;地脚面也要随形做出反变形量;有些结构很不均匀的床身,可能还会出现侧弯曲,这样也当需要在导轨侧面甚至整个床身侧面都要留反变形量。
2.2加工余量一般在反变形量基础上再留10~20mm加工余量,余量也不用太大,否则加工完后会出现硬度不够的现象。
2.3收缩率一般长度方向取1.0%,宽度方向取0.8%,高度方向取0.5%。
考虑胀箱等因素,宽度方向可不留缩尺,甚至考虑将模样尺寸人为减小,以保证出件后铸件的净尺寸符合要求。
2.4工艺补正量为防止加工后导轨因变形而变薄,导轨及地脚背面可留3~5mm工艺补正量。
2.5浇注系统设计浇注位置当然是将导轨放在下面,一般从床身两端由导轨进入铁液;特别长的导轨可采用底返雨淋浇注系统,这种浇注系统可保证铁液流程不要太长,有效防止出现冷隔及导轨掉渣、气孔缺陷,使铁液杂质上浮。
浇注系统全部采用耐火瓷管,造型时预埋于砂型中。
根据床身长度、浇注重量、导轨及床身与立柱结合面位于下型的特点,选择两端座包浇注,且采用底返雨淋及由“平、V”导轨两端同时进入铁液,总体上两层阶梯浇注方式,这样内浇道多点分散注入,两部行车同时浇注,充分考虑铁液流程,避免产生冷隔、浇不足、气孔等缺陷。
导轨中间采用集渣包,分散引流等方式将冷铁液转移走,避免导轨中间出现气孔针孔等缺陷,从而达到保证导轨铸造无缺陷的目标实现。
浇注时间要尽量短,依据浇注重量,一般在3~5min内浇注完。
2.6冒口设计多采用耳冒口形式,厚大部位用冷铁包敷;冒口放置位置避开厚大部位,防止形成接触热节。
2.7砂芯设计在保证操作方便的情况下,尽量将各砂芯连在一起,以增大自重抵消铁液浮力。
另外要用紧固螺栓把砂芯固定在底箱上,紧固螺栓可以穿透一层甚至几层砂芯,另外导轨芯也要根据长度分成好几段。
2.8模板设计较长的床身,模板可做成2~3段,段与段之间用燕尾销连接;若不用外模,纯粹用砂芯组合起来,那么形成外型的砂芯也要人为分成几段,以便制芯和下芯操作。
2.9冷却措施对于比较厚大的导轨,可在导轨底面敷以冷铁激冷,冷铁材质最好采用石墨块,也可以采用铸铁冷铁,当然必须烘干水分,防止呛火,特别在冬季要注意避免温差太大,因此放置铸铁冷铁要慎用。
2.10尺寸精度控制底箱首先要铺平,要用水平仪或拉线找平;导轨芯也要注意以水平线找正,其高度尺寸定位也要充考虑反变形量和加工余量。
2.11熔炼浇注工艺采用高Si/C灰铸铁在CE=3.4%~3.8%条件下,适当增加废钢加入量,将Si/C从0.4~0.5提高到0.7~0.8,将铁液出炉温度提高到1450℃以上,抗拉强度可提高20~30MPa,铸件具有较小的变形倾向;但对于机床这类壁较厚的铸件,提高Si/C比会增加厚断面处的铁素体含量,反而会使硬度降低,此时加入Cr合金元素,提高机床厚断面处的珠光体含量,减少断面硬度差,增加机床的精度稳定性。
另外, Mn量稍高于Si量的灰铸铁具有良好的性能:收缩小,不易产生缩孔、缩松,切削性能好,是一种提高强度,弹性模量和耐磨性、减少铸件变形的良好材质。
[2]值得一提的是,机床导轨表面经常采用淬火热处理,淬火后的表面能获得马氏体+石墨的组织,珠光体基体淬火后表面硬度可达50HRC左右,因普通灰铸铁含Si高,淬透性差,添加少量Ni、Cr、Mo能改善其淬透性。
采用炉前孕育和浇注时瞬时孕育相结合的方法,一般浇注采用两包同时浇注。
要调整好铁液成分,保证铁液温度。
我厂采用的HT250、HT300的化学成分见表2。
表2 HT250、HT300的化学成分( wt%)3重点缺陷防止3.1变形问题对于分导轨水平方向和床身侧面方向的变形问题,解决的措施:一是上述已提到的做反变形量;二是根据铸件结构,在铸件抗弯薄弱的地方适当做拉筋。
3.2砂芯漂芯最主要的是将导轨芯及上层砂芯用长螺栓紧固于下箱,若无法紧固,则应将各个独立的砂块用外力将它们联系起来,以抵消浮力的冲击。
3.3组织疏松硬度低经常在床身导轨面加工后出现弥散分布的细孔,这就是组织疏松,这是由于其金相组织中片状石墨粗大,即组织异常造成的缺陷,表现出很低的硬度。
其形成原因主要是对应于铸件壁厚部位,碳当量过高,片状石墨粗大是根本原因;熔炼温度低,铁液过热度小,铁液中有未完全熔解的石墨片,易使片状石墨粗大;冲天炉熔炼过程中,铁液增碳过多。
其防止措施:根据铸件壁厚,确定合理的碳当量,以获得细片状石墨和以珠光体为主的金相组织;铸件化学成分中添加适量的合金元素,如B、Mn等;提高铁液过热度,加强孕育处理,降低浇注温度,提高铸件厚壁部分的冷却速度,如放外冷铁等。
3.4硬质点及淬火效果差主要是由于含Si量高,组织中含有未充分扩散的局部的硅富集区,富集区中的Si同铁液中的C形成硬度很高的非金属夹杂物SiC晶体[3]造成加工硬点;另外由于含Si量高,组织中有铁素体存在,使得淬火硬度和深度受到影响,因为铁素体组织的淬透性远比珠光体差。
因此,对于要求导轨表面淬火的机床床身,成份选取时应控制较低的含Si 量,一般在1.2%~1.6%Si之间,对于原始组织中有铁素体存在需要表面淬火的灰铸铁件,则进行一次正火处理,能保证随后的淬火效果。
4应用效果( 1)采取以上工艺措施已成功为上海、威海、济南、沈阳等地生产数件机床床身,他们对我厂生产的铸件给予充分肯定和高度评价。
( 2)该工艺成功应用于M7150×3m、M7150×5m、M7150×6.6m、M7150×8.6m, M7150×12.6m、M8463×6.6m、M8463×8.6m、M8040×6.6m、M8048×8.6m等几种大型磨床床身及桂林重达15t的工作台及本公司大型铸铁平台的生产,不仅操作安全方便,而且经济适用,效果很好,相比劈模造型而言,生产以上铸件可节约工装费用100余万元。
( 3)应用组箱组芯法生产大型机床床身,具有经济适用,操作安全性高的优点,很适合铸造厂手工造型。
应用此工艺方法,从理论上讲,无论多长的铸件都能够生产,从而扩大了我厂的生产能力,拓宽了市场领域。
( 4)充分考虑机床床身铸件本身的结构特点,正确选取各项工艺参数,合理调整铁液成分,保证铁液温度,做好各类缺陷的防止措施,就能够成功铸造大型机床床身。