钻杆螺纹断裂失效分析
钻杆失效分析
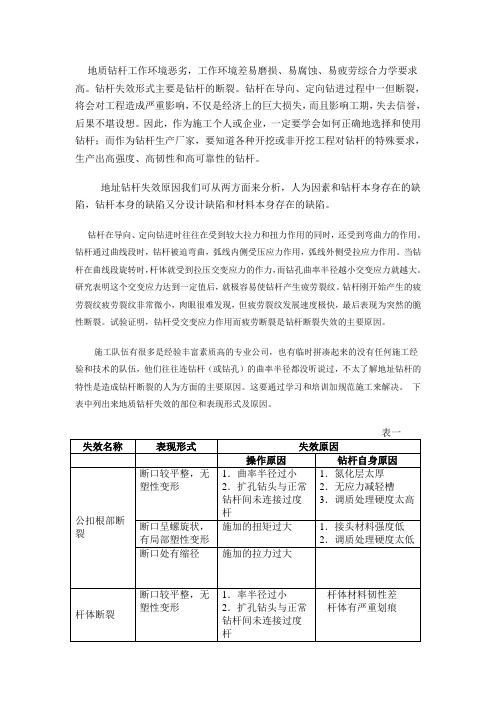
三、避免钻杆非正常失效的措施钻杆的基本力学工况钻杆在内外充满钻井液的狭长井眼里工作,通常承受压、弯、扭、液力等载荷。
如果钻杆所受应力小于每平方米206.8牛顿时,钻杆虽经过无数次的弯曲,也不会产生疲劳裂纹。
钻井时钻杆承受弯曲、扭转和拉伸应力组成的复合应力很大,特别是在大位移定向井及水平井中扭矩极大,钻杆在100万次弯曲次数时便产生疲劳微裂纹;微裂纹产生后便不断扩大延伸,此时如果具有腐蚀作用的高压钻井液进入微裂纹中,就会加速裂纹扩展,最终导致钻井液刺穿钻杆的失效事故。
刺穿发展的结果,使钻杆有效断面不断缩小,刺孔加裂纹的总长度超过其临界裂纹尺寸时,即发生断裂。
除旋转向下的运动,同时还有钻杆的各种振动和涡动。
根据钻杆的失效原因分析,钻杆除正常磨损而失效外,钻杆的非正常失效原因可分为为两个方面:工人操作原因和钻杆自身质量原因。
因此,我们可以从提高钻杆质量和规范操作两方面来避免钻杆非正常失效。
1.提高钻杆质量(1)钻杆材料选择:为适应钻杆的受力分析,钻杆杆体应有较高的抗拉强度、较好抗弯性能和较好的冲击韧性。
杆体材料应选择中碳合金结构无缝钢管,合金元素中应含有较多的Cr、Mo等元素以提高材料的抗拉强度和冲击韧性,含有Mn、Si等元素以提高材料的弹性(即抗弯性能)。
有时还含有微量的B、V等元素以提高材料的淬透性。
常用的杆体材料有:36Mn2V、35CrMo、42MnMo7、35CrMnSi、45MnMoB等。
用于杆体的无缝钢管的壁厚均匀度和轧制缺陷也是影响钻杆质量的重要因素。
如轧制的钢管壁厚均匀情况严重,当钻杆较大的扭力作用时,容易在壁厚较薄处纵向裂开。
有的钢管有重皮、气孔等缺陷,钻杆易从此处产生应力集中断裂或刺漏。
钻杆接头受力最为复杂,接头材料须有很高综合机械性能。
钻杆接头多采用35CrMo或42CrMo.30CrMnSiA棒料制造,但经过锻造的接头材料能大大提高其综合机械性能。
(2)加工工艺选择:目前国内钻杆从加工工艺分主要有整体锻造钻杆(简称整体钻杆)、镦粗+摩擦焊钻杆(简称镦焊钻杆)和单纯摩擦焊钻杆(简称摩擦焊钻杆)。
某51/2FH双台肩钻杆内螺纹接头断裂原因分析

F r a c t u r e Ca u s e An a l y s i s o f a 5— — 1 / 2 F H Bo x J o i n t o f Dr i l l P i p e
ZH ANG Xi n s he ng L I U Zha n y e
使用 时发生断裂 。
间以后重新对焊 了新钻 杆接头 , 断裂的 即为新换钻 杆接 头, 扣型为双 台肩 5 1 / 2 F H 。
钻井液 中含砂量 0 . 1 5 %, p H值为 1 0 , 钻井参数 如表
1 所示 。 表 1 钻进参数
据送样者所提供现 场资料显示 , 此钻杆 内螺 纹接头 断裂事故经过如下 : 2 0 1 0年 1月 2 1日早 上 6 : 3 0 , 在下套 管 到底后 , 上提距离井底 2 . 7 m循 环 , 上提最 大钩载 1 5 5 吨, 提到 3 3 3 5 m静 止进行 循环 , 泵冲为 4 0冲/ 分, 泵压
・
5 0・
石油 管材 与仪 器 P E T RO L E U M T U B UL A R Goo DS& I N S T R U ME NT S
2 0 1 5年 4月
・
失效分 析及 预 防 ・
某5 1 / 2 F H双 台 肩钻 杆 内螺 纹 接 头 断 裂 原 因分 析
c r e a s e d , t h e n f a t i g u e c r a c k w a s o c c u r r e d i f r s l t y a t t h e t h r e a d r o o t o f t h e d r i l l p i p e t h r e a d e d j o i n t , a l l o f t h e s e l e a d t o f a t i g u e f a i l u r e .
钻具失效断裂浅谈
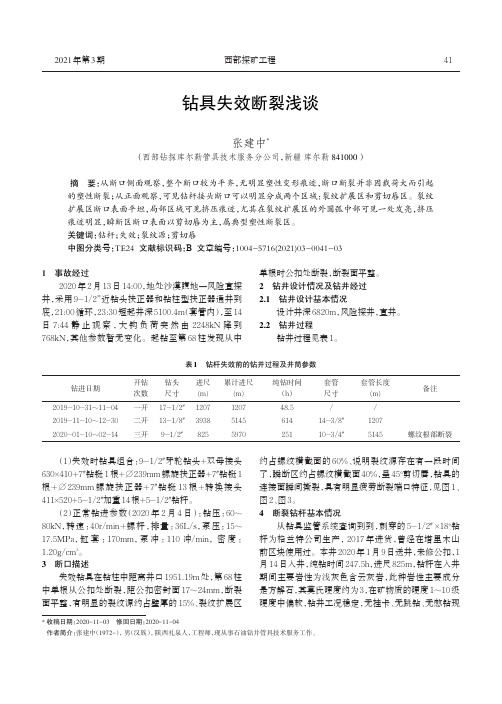
杆为格兰特公司生产,2017 年进货,曾经在塔里木山
1.20g/cm 。
前区块使用过。本井 2020 年 1 月 9 日送井,未修公扣,1
3
月 14 日入井,纯钻时间 247.5h,进尺 825m,钻杆在入井
3
断口描述
失效钻具在钻柱中距离井口 1951.19m 处,第 68 柱
期间主要岩性为浅灰色含云灰岩,此种岩性主要成分
图 3,且表面疲劳台阶明显;瞬断区断口表面以剪切唇
为主,属典型塑性断裂区。根据钻杆接头以上断口特
征,该钻杆接头根部断裂应为典型的疲劳断裂。
(4)接头断裂部位位于螺纹根部,从断口表面裂纹
源区域可以看到,该区域断口颜色发亮,与附近端 5 口
表面颜色明显不同,且该区域挤压痕迹明显,见图 3。
根据裂纹源处的宏观特征,和该钻具入井时间和钻井
设计井深 6820m,风险探井,
直井。
2.2
768kN,其他参数暂无变化。起钻至第 68 柱发现从中
表1
钻井设计情况及钻井经过
钻井过程
钻井过程见表 1。
钻杆失效前的钻井过程及井筒参数
开钻
钻头
进尺
累计进尺
纯钻时间
套管
套管长度
次数
尺寸
(m)
(m)
(h)
尺寸
(m)
2019-10-31~11-04
一开
17-1/2″
液沉淀浓度(0.1~0.4mL/100mL)配合连续法加电同
时施加配置好的磁悬液,尤其适应于钻具公螺纹表面
和近表面的缺陷检测。
7 预防措施
钻具公扣螺纹根部为应力集中区,应力得不到及
时释放加之复杂工况下的拉应力和弯曲应力交变,容
钻杆接头失效分析

前言2007年1月底,井下作业公司在用φ127(接头NC50)钻杆发生失效,失效形式为螺纹缺损,粘着以及接头密封台肩面撕裂性缺损。
委托方提供的钻杆工作参数为:进尺1243m,钻压4~6T,泵压10Mpa,转速80r/min。
据委托方说明该批钻杆为新产品,第一次使用。
事故发生后,该批钻杆集中放置于井下作业工司油管厂场地,经查看125根钻杆中有9组接头存在损伤,其中严重损伤2组,呈现螺纹被冲刺缺损,而且其中1组有螺纹粘着、撕毁现象;其余7组存在不同程度的接头密封台肩面黏着撕裂性缺损现象。
一、外观形貌分析1严重失效2组钻杆外观形貌如图1~4所示。
螺纹粘着、撕毁图1第1组外螺纹接头外观形貌螺纹粘着、撕毁图2第1组内螺纹接头外观形貌冲击起始区图3第2组内螺纹接头外观形貌图4第2组内螺纹接头外观形貌如图所示:第一组钻杆失效形式为螺纹缺损,粘扣。
从缺损形貌可见,图示内外钻杆接头对应部位同时存在对应的螺纹缺损和黏着形貌,因此图示内外钻杆接头为工作时对接的接头。
外螺纹接头自密封面起第6、7、8扣粘结,内螺纹自密封面起第4、5、6扣粘结;从螺纹缺损形貌分析,可以断定螺纹缺损由高压钻井液冲刺造成。
第一组钻杆失效形式为螺纹缺损,从螺纹缺损形貌分析,可以断定螺纹缺损由高压钻井液冲刺造成。
2接头密封面损伤接头密封面损伤外观形貌如图5~6所示。
7组接头密封面存在图示的撕脱性损伤。
撕脱性损伤图5密封面撕脱性损伤一撕脱性损伤图6密封面撕脱性损伤二自图1所示的接头,按照《SY/T5290-2000石油钻杆接头》之规定,采取材质、机械性能、硬度及金相试样,逐个进行实验。
二、材质分析按照《SY/T5290-2000石油钻杆接头》取样后经直读光谱分析结果如下表1:《SY/T5290-2000石油钻杆接头》规定接头材质为合金钢,且对S,P作出规定,含量不超过0.030%,从检测结果看来,符合标准要求。
三、机械性能按照《SY/T5290-2000石油钻杆接头》取样后,依据《GB/T228金属拉伸试验法》进行试验测得结果如表2。
_127mmS135钻杆接头外螺纹断裂失效分析

失效钻杆接头 的冲击 功和硬度符合 SY /T S29 " 一
2010 年第 3 期
西部探矿工程 流预防钻具事故好的经验和做法 , 特别要做好钻具使用 中后期的腐蚀应力疲劳失效的预防工作 "
参考文献 :
+ 10 1. 11
+ 10 1. 85 + 10 2. 51
50 85
50 95
貌 " 在接头瞬断区可见明显 的剪切唇形貌 " 从宏观形 貌分析判断 , 裂纹起源于接头密封 台肩面根部外表 面 , 由外 向内扩展 , 最终导致接头发生断裂失效 "
2.2 微观 断 口分析
口井 , 在挂曰177.st m 尾管时发生一起必 127m m S135 n 斜台肩内涂层钻杆接头外螺纹断裂 "该井为一 口直井 , 发生事故是实钻井深 6262.o o m " 必 17 7 .sm m 尾管下 深 6259. 28m , 球 座 位 置 6202. 64m , 悬 挂 器 位 置
钻柱是快速优质钻井的重要工具和手段 , 是联通地
承受复杂的应力载荷 , 接头密封 台肩面根部是应力集中 部位 , 同时也是易产生加工缺陷的部位 , 是钻杆接头事 故的多发处 , 裂纹易在此处萌生 "
3 .2 此次 断裂 事故 的结论
面与井下的枢纽 " 在转盘钻井 时依靠 它来传递破碎岩 石所需的能量 , 给井底施加钻压 , 以及 向井 内输送钻井 液等 "在井下动力钻井时 , 井底动力机是用钻柱送到井 底 , 同时动力钻具所需 的液体能量也是通过钻柱输送到 井底的 "在钻井过程中 , 钻头的工作 , 井眼的状况 , 甚至 地层的各种变化 , 往往是通过钻柱及各种仪表才能反映 到地面上来 "合理的钻井参数和其他的技术措施 , 也只 能在正确使用钻柱的条件下才能实现 "
Ф127mmS135钻杆接头外螺纹断裂失效分析

此 次外螺 纹断裂 的钻 杆为 中石化 20 06年集 中采 购
的 1 7 2 mm9 1 S 3 . 9 1 5斜 台肩 内涂 层钻 杆 , 外螺 纹 接 内、
头体 各加 长 5.mm, 08 外螺 纹 接头水 眼 为 8. mm。 26 该批钻 杆共 到货 60根 ,0 7年 到货 后 , 具 公 司 2 20 管 按标 准对该批 钻杆 进行 了抽 检 , 检结果 符合 相关 的标 抽
准要 求 。
20 08年 7月配 套 井 队使 用 , 生 断 裂 时 为 该 批 钻 发 杆承钻 的第一 口井 。
2 断 裂失效 分析 2 1 宏 观断 口分析 .
断裂失 效 钻杆断 裂 位 置为 钻 杆 接 头外 螺 纹 台肩 面 根部 。 观察钻 杆接 头断 口形貌 可 以看 出 , 口表面 存在多 断 个裂 纹源 区 , 主裂 纹源 区及大 部分 扩展 区受 到严重 的钻
图 1 断 口表面能谱分析
2 3 金 相组织 分析 .
井液冲蚀 , 已无法观察到原始形貌 , 但后期产生的裂纹 及扩 展 区形 貌清 晰可见 , 这些 裂纹 源 区都紧靠 接头 密封
在 失效 钻杆 接头 的断 口附近 取 样 进行 金 相 组 织 分 析 , 析结果 见 表 1 示 。断 口附近 组织 与基体 组织基 分 所
2 4 下 降 至 1 8 后 反 弹 回 2 6 , 断 未 坐 挂 。 上 提 1t 7t 0 t判 1 5 . m 过 程 中 , 重上 升 至 2 2 , . ~2 0 悬 1 t 钻具 震 动 , 重 悬
下降 至 14, 0 t判断 钻杆 断裂 。2 5日起 钻 完 , 现 钻杆 外 发 螺纹根 部断裂 , 鱼顶 2 1 . 3 9 5 1 m。
钻杆及其接头的早期失效分析与措施研究
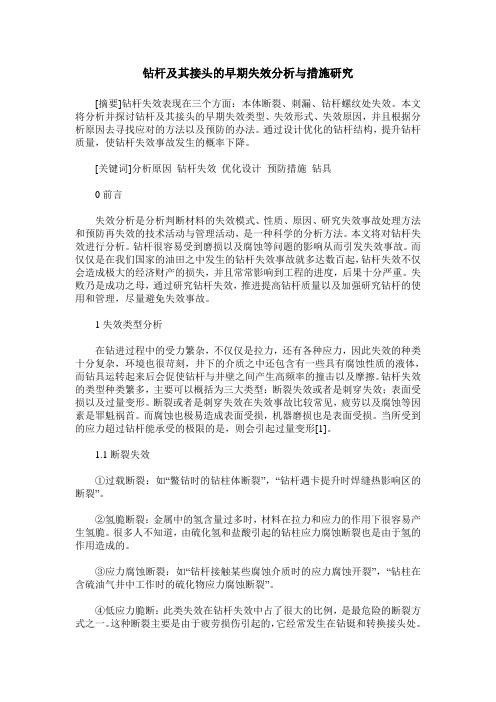
钻杆及其接头的早期失效分析与措施研究[摘要]钻杆失效表现在三个方面:本体断裂、刺漏、钻杆螺纹处失效。
本文将分析并探讨钻杆及其接头的早期失效类型、失效形式、失效原因,并且根据分析原因去寻找应对的方法以及预防的办法。
通过设计优化的钻杆结构,提升钻杆质量,使钻杆失效事故发生的概率下降。
[关键词]分析原因钻杆失效优化设计预防措施钻具0前言失效分析是分析判断材料的失效模式、性质、原因、研究失效事故处理方法和预防再失效的技术活动与管理活动,是一种科学的分析方法。
本文将对钻杆失效进行分析。
钻杆很容易受到磨损以及腐蚀等问题的影响从而引发失效事故。
而仅仅是在我们国家的油田之中发生的钻杆失效事故就多达数百起,钻杆失效不仅会造成极大的经济财产的损失,并且常常影响到工程的进度,后果十分严重。
失败乃是成功之母,通过研究钻杆失效,推进提高钻杆质量以及加强研究钻杆的使用和管理,尽量避免失效事故。
1失效类型分析在钻进过程中的受力繁杂,不仅仅是拉力,还有各种应力,因此失效的种类十分复杂,环境也很苛刻,井下的介质之中还包含有一些具有腐蚀性质的液体,而钻具运转起来后会促使钻杆与井壁之间产生高频率的撞击以及摩擦。
钻杆失效的类型种类繁多,主要可以概括为三大类型:断裂失效或者是刺穿失效;表面受损以及过量变形。
断裂或者是刺穿失效在失效事故比较常见,疲劳以及腐蚀等因素是罪魁祸首。
而腐蚀也极易造成表面受损,机器磨损也是表面受损。
当所受到的应力超过钻杆能承受的极限的是,则会引起过量变形[1]。
1.1断裂失效①过载断裂:如“鳖钻时的钻柱体断裂”,“钻杆遇卡提升时焊缝热影响区的断裂”。
②氢脆断裂:金属中的氢含量过多时,材料在拉力和应力的作用下很容易产生氢脆。
很多人不知道,由硫化氢和盐酸引起的钻柱应力腐蚀断裂也是由于氢的作用造成的。
③应力腐蚀断裂:如“钻杆接触某些腐蚀介质时的应力腐蚀开裂”,“钻柱在含硫油气井中工作时的硫化物应力腐蚀断裂”。
④低应力脆断:此类失效在钻杆失效中占了很大的比例,是最危险的断裂方式之一。
工程用钻杆螺纹断裂失效研究

z,膨ed“,以er 0ctu以埘D庙如础.胃缸ed o儿n,l眈眈mem肘e£危Dd,fk cDn6∞£疗n娩e如,聊眦,∞deZ o厂dr珊i粥
p咖e tIIlre以^璐6een esta6倦k正而r中42 d棚p咖e,琥e sfre耐括虢奶就正A如。加幻g呷Ill记肌d砒碰一 如卿^如e翮i,刎幻n,cD,,妒o,暑e,啪,r圮仍ure,,lem∞以,i掰西圮ss,,le∞Mre,,lem^伽e 6ee,l c∞7诒d o以on£7le 帆咖括旷砒扰耽昭p咖e啦re以孤e陀su凰s危伽t砌矗妣r£^rend s£陀ss埘耐i瑚£玉以渺讯冼e km
图7断件微观形貌
图8断件微观腐蚀坑
安全系数为1.32,仍然偏低。 4.4失效原因分析
通过对钻杆螺纹进行强度分析和材质分析,找出钻杆螺纹失 效原因如下。 4.4.1应力集中
根据钻杆接头螺纹原始模型有限元分析结果表明,在公扣第 一螺纹牙处根部受到严重的应力集中,极容易引起疲劳破坏。 4.4.2热处理工艺不稳定
152 文章编号:100l一3997(2009)12.0152-03
机械设计与制造
Machinery De《gn & Manufacture
第12期 2009年12月
工程用钻杆螺纹断裂失效研究
管朝晖杨斌 (重庆钢铁股份有限公司,重庆400082) Fracture fajIure anaIysis 0f the dri¨ing pipe thread used in enginee ring
2石晓兵,施太和.一种新璋!钻柱稳定器连接螺纹减应力区的研究[J].天然 气工业,2002,22(2):48巧O
- 1、下载文档前请自行甄别文档内容的完整性,平台不提供额外的编辑、内容补充、找答案等附加服务。
- 2、"仅部分预览"的文档,不可在线预览部分如存在完整性等问题,可反馈申请退款(可完整预览的文档不适用该条件!)。
- 3、如文档侵犯您的权益,请联系客服反馈,我们会尽快为您处理(人工客服工作时间:9:00-18:30)。
钻杆螺纹断裂失效分析
鲍洪峰刘道喜
(无锡双马钻探工具有限公司技术研发中心 江苏 无锡 214000)
江苏钻通生产的X320型钻机中钻杆在使用一段时间,在钻杆螺纹处断裂。
为查明原因进行失效分析。
钻杆材料为42MnMo7,化学成分由厂家提供,有待进行复验。
钻杆规格:¢73*8*3000mm。
技术要求:钻杆整体进行调制处理,硬度30~35HRC。
抗拉强度:≧965Mpa,
屈服强度:≧865Mpa
钻杆结构及断裂位置如图1所示。
(图1)钻杆结构及断裂位置示意图
1、宏观分析
送检式样的宏观形貌如图2所示。
(图2)试样宏观形貌
从图2中看到断口在螺纹的第三级上,断口基本齐平与轴向垂直,无明显塑性形变痕迹,断口形貌如图3所示。
从图3中看到,断口的外圈有一个平台区,平台上可看到明显的贝纹线,这是疲劳裂纹扩展留下的痕迹,也是裂纹扩展时停歇后留下的痕迹,所以根据典型的贝纹线形貌可以确定,断口的断裂类型为疲劳断裂。
断裂过程为:在螺纹根部的一周都有疲劳裂纹源,一周的裂纹同时向轴心扩展,根据受力的大小反应出扩展的快慢,从图3看到,右侧的受力要偏大于左侧,因平面区域大,且疲劳扩展的贝纹线清晰可见。
当剩余直径的截面积承受不了工作载荷后,即发生最后的瞬时断裂,因为受到的是扭力,所以最后断裂区与轴向呈45度,并且断口粗糙。
各区的放大形貌如图4所示。
(图3)断口宏观形貌
从图3中可以看出公扣的牙底部份的储油空
(a)疲劳扩展区右侧
(b)疲劳扩展区左侧
(图4)断口局部放大形貌
2、显微分析
在图4a中红框位置取样,沿纵截面按照常规制样方法制样,进行显微组织分析。
式样的纵截面上即可看到其他螺纹根部也有宏观裂纹产生,如图5所示。
宏观裂纹长度大约为2~3mm。
从截取的试样上看到,断口处的螺纹顶部已被挤压磨损掉了,如图6所示。
(图5)螺纹根部宏观裂纹形貌
(图6)螺纹顶部磨损形貌
观察试样心部及表层显微组织均为回火索氏体组织,组织分布均匀,如图7所示。
心部组织形貌
表层组织形貌
(图7)试样显微组织形貌
(图8)微裂纹形貌
从图8中看到,微裂纹深度大致相同,深度在100微米左右,都是浅层裂纹,较深的裂纹是受力后扩展后造成的。
3、硬度试验
对试样进行洛氏硬度测试,测试结果见表1.
表1 洛氏硬度测试结果HRC
根据以上硬度测试结果,说明心部硬度符合技术要求,螺纹顶部表面的硬度有所升高说明螺纹处可能进行了表面处理。
4、综合分析
根据以上测试结果,可以得出零件的断裂类型为疲劳断裂,疲劳裂纹源产生在螺纹根部,显微分析证实在螺纹上有多处微裂纹,这些裂纹都可以形成疲劳源,或断裂的起点,只是根据微裂纹产生的位置是否受力大小而变化,如微裂纹处不受力,裂纹不会扩展;如微裂纹受力,当受力比较小时,就会产生疲劳裂纹扩展,直到剩余截面不能承受工作载荷时才会发生最后的一次性断裂。
如微裂纹处受力过大,超出零件的承受工作应力,微裂纹就会快速扩展发生一次性的过载断裂。
显而易见,本次零件的断裂为疲劳断裂,由此说明零件的工作应力不是很大的,只是当疲劳裂纹扩展一定截面后,剩余截面不能承受工作载荷时才发生了最后的断裂。
由此微裂纹的产生原因是本次疲劳断裂的主要因素,从图8的微裂纹形貌看应该为应力集中区形成的裂纹扩展,所有在螺纹根部的裂纹在受力后都有所扩展,因在螺纹侧面上的裂纹不受力,所以都没有扩展。
结论
(1)零件的断裂类型为疲劳断裂。
(2)公口螺纹根部往往是应力集中区,特别是根部螺纹小径处应力不易释放最终导至形成裂纹。
使用具有较好抗疲劳强度的材质;同时在螺纹根部设计应力减轻槽才是解决问题的关键。