重点解读SCR脱硝系统喷氨优化调整试验
电站燃煤锅炉SCR烟气脱硝喷氨优化控制分析

电站燃煤锅炉 SCR烟气脱硝喷氨优化控制分析摘要:污染是一个全球问题,它会导致温室效应,破坏臭氧层和形成酸雨。
我们国家对的排放做出了严格的限制。
另一方面脱硝所用液氨的价格较贵,给对电厂的经济运行带来了挑战。
锅炉脱硝系统的正常运行对于整个发电厂的环保和经济运行都有着非常重要的影响。
本文通过对发电厂脱硝系统运行中存在的问题进行总结与分析,提出了一些有效的优化调整措施,希望在满足严苛环保要求下保持脱硝系统的经济运行。
关键词:脱硝系统;超净排放;精准喷氨引言为达到国家环保超净排放标准的严格要求(30万千瓦及以上公用燃煤发电机组大气污染物排放浓度基本达到燃气轮机组排放限值的环保指标,即在基准氧含量6%条件下,氮氧化物排放浓度分别不高于50毫克/立方米),华能井冈山电厂一期两台30万千瓦燃煤机组采用选择性催化还原(SCR)工艺烟气脱硝系统,锅炉配置2台SCR反应器,采用纯度为99.6%的液氨做为脱硝系统的反应剂。
SCR反应器布置在省煤器与空预器之间的高含尘区域。
脱硝系统在机组并网运行期间保持连续运行,运行人员既要确保脱硝系统出口浓度在标准要求之内,又要满足脱硝系统节约经济运行的要求。
所以要对机组脱硝喷氨进行优化控制,实现精准喷氨,既满足于严苛的环保要求,又能节约液氨消耗的成本,助力我厂实现绿色节能型电厂的建设。
一SCR脱硝系统简介我厂一期锅炉烟气脱硝装置布置在炉外,呈露天布置,采用高粉尘布置的SCR工艺,即将SCR反应器布置在省煤器之后、空预器和电除尘之前。
脱硝系统布置有三台稀释风机,一台运行,两台备用。
氨气与空气混合后被喷入反应器中,与反应器中的氮氧化物发生反应。
烟气中所含的全部飞灰和均通过催化剂反应器,的去除率可达到80%~85%。
每台锅炉配置两台SCR反应器,采用蜂窝式催化剂,按“2+1”模式布置三层催化剂。
SCR的化学反应机理比较复杂,催化剂选择性主要是指在有的条件下被氧化,而不是被氧化,SCR反应是选择性反应生成,而非其他的含氮氧化物。
燃煤电厂600MW机组SCR脱硝系统优化调整研究

燃煤电厂600MW机组SCR脱硝系统优化调整研究摘要:目前,我国经济建设极快发展,人们环境保护的意识在不断增强。
在燃煤电厂600MW机组中,加强对SCR脱硝系统的优化研究,符合节能减排的相关要求,也是燃煤电厂可持续发展的要求,应予以重视,本文就此展开了探讨。
关键词:燃煤电厂;600MW机组;SCR脱硝系统1 前言随着环保部门对 NO x 排放限制水平的日益严格,烟气脱硝技术被普遍应用于燃煤电站.选择性催化还原(SCR )技术由于脱硝效率高且技术成熟,已成为国内燃煤电站应用最为广泛的烟气脱硝技术。
2 项目介绍脱硝采用选择性催化还原法(SCR)脱硝装置,在设计煤种及校核煤种、锅炉最大连续出力工况(BMCR)、处理100%烟气量时保证条件下脱硝效率按80%设计,催化剂按照“2+1”布置模式设计,现役催化剂采用蜂窝式催化剂,分别于2013年7月、2013年12月投运。
目前,1、2号炉已完成超低排放改造,NOx排放浓度满足小于50mg/Nm3的要求。
根据1号炉引风机2016年更换滑块后运行两年再次损坏,原因与叶片积垢有关,另外发现超低排放改造后锅炉尾部烟道硫酸氢氨含量较多,且电厂NOx含量以及氨逃逸热工测点代表性不足,长期运行对空预器、引风机等造成不利影响,严重时引起堵塞,叶片卡涩风机轮毂损坏等,影响设备的安全运行。
故需要进行喷氨格栅优化调整试验。
合理分配各格栅喷氨量,保证供氨均匀,在保证脱硝效率的同时,降低脱硝装置的运行成本,提高氨的使用率,避免反应器出口截面局部区域氨逃逸浓度过高,减轻对下游设备的腐蚀堵塞,保证脱硝装置及机组的安全稳定运行。
3 试验内容及测点布置3.1 试验内容SCR脱硝装置的喷氨优化调整试验主要在机组常规高负荷进行,并在高、中、低负荷下进行验证和微调。
试验过程如下:1)预备试验:实测反应器进出口NOX浓度,氨逃逸等,为正式试验做准备。
机组运行人员稳定锅炉运行氧量、磨投运组合方式等,减少脱硝装置入口NOX的波动。
300_MW燃煤机组SCR脱硝喷氨格栅改造及优化调整

山 西 电 力
2023 年第 6 期
195~220 mg/m3之间,平均质量浓度205.09 mg/m3, 相对标准偏差4.38 ;B侧SCR进口NOx质量浓度在 185~215 mg/m3之间,平均质量浓度201.83 mg/m3,相 对标准偏差4.55 ,如图4(b)所示。改造后SCR 进口NOx质量浓度及其均匀性与改造前相比均没有 明显变化,表明喷氨格栅改造并未对烟气流场产生 不利影响。
3.2 改造前出口NO 质量浓度和氨逃逸 x
改造前A侧SCR出口NOx质量浓度控制在39 ~52 mg/m3之间,平均质量浓度45.74 mg/m3,相对 标准偏差11.72 ;B侧SCR出口NOx质量浓度控制在 37~53 mg/m3之间,平均质量浓度44.99 mg/m3,相 对标准偏差11.06 。改造前SCR出口NOx质量浓度 如图5所示。由图5(a)可知,在将SCR出口NOx平 均质量浓度保持在45 mg/m3左右的前提下,NOx质 量浓度的相对标准偏差远高于5 ,且部分区域实 测质量浓度超过了超低排放要求的50 mg/m3,说明 出口NOx分布非常不均匀。由于SCR进口的NOx分布 是较为均为的,由此可以判断该机组的问题主要在 于氨气与烟气混合效果差,导致局部脱硝反应进行 的不充分,应对喷氨格栅进行优化改造。
2023 年 12 月
赵玉东:300 MW燃煤机组SCR脱硝喷氨格栅改造及优化调整
˄≘䘳䙨˅˄/g/ ˅
排放质量浓度相对标准偏差达到5 的优化调整目
标。改造后SCR出口NOx质量浓度如图6所示。
由图6(b)可知,A侧SCR出口氨逃逸体积分
ü$˗חü%חDŽ
数在1.85~2.15 μL/L之间,平均为2.01 μL/L,相
脱硝系统运行喷氨量优化调整
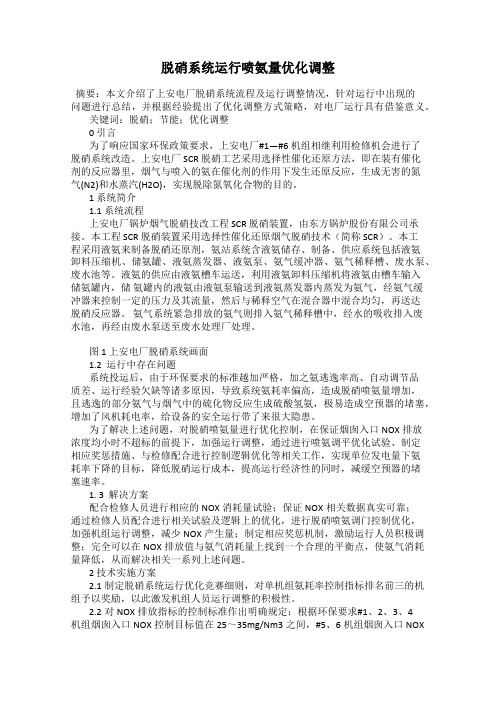
脱硝系统运行喷氨量优化调整摘要:本文介绍了上安电厂脱硝系统流程及运行调整情况,针对运行中出现的问题进行总结,并根据经验提出了优化调整方式策略,对电厂运行具有借鉴意义。
关键词:脱硝;节能;优化调整0 引言为了响应国家环保政策要求,上安电厂#1—#6机组相继利用检修机会进行了脱硝系统改造。
上安电厂SCR 脱硝工艺采用选择性催化还原方法,即在装有催化剂的反应器里,烟气与喷入的氨在催化剂的作用下发生还原反应,生成无害的氮气(N2)和水蒸汽(H2O),实现脱除氮氧化合物的目的。
1 系统简介1.1 系统流程上安电厂锅炉烟气脱硝技改工程 SCR 脱硝装置,由东方锅炉股份有限公司承接。
本工程 SCR 脱硝装置采用选择性催化还原烟气脱硝技术(简称 SCR)。
本工程采用液氨来制备脱硝还原剂,氨站系统含液氨储存、制备、供应系统包括液氨卸料压缩机、储氨罐、液氨蒸发器、液氨泵、氨气缓冲器、氨气稀释槽、废水泵、废水池等。
液氨的供应由液氨槽车运送,利用液氨卸料压缩机将液氨由槽车输入储氨罐内,储氨罐内的液氨由液氨泵输送到液氨蒸发器内蒸发为氨气,经氨气缓冲器来控制一定的压力及其流量,然后与稀释空气在混合器中混合均匀,再送达脱硝反应器。
氨气系统紧急排放的氨气则排入氨气稀释槽中,经水的吸收排入废水池,再经由废水泵送至废水处理厂处理。
图 1 上安电厂脱硝系统画面1.2 运行中存在问题系统投运后,由于环保要求的标准越加严格,加之氨逃逸率高、自动调节品质差、运行经验欠缺等诸多原因,导致系统氨耗率偏高,造成脱硝喷氨量增加,且逃逸的部分氨气与烟气中的硫化物反应生成硫酸氢氨,极易造成空预器的堵塞,增加了风机耗电率,给设备的安全运行带了来很大隐患。
为了解决上述问题,对脱硝喷氨量进行优化控制,在保证烟囱入口NOX排放浓度均小时不超标的前提下,加强运行调整,通过进行喷氨调平优化试验、制定相应奖惩措施、与检修配合进行控制逻辑优化等相关工作,实现单位发电量下氨耗率下降的目标,降低脱硝运行成本,提高运行经济性的同时,减缓空预器的堵塞速率。
SCR烟气脱硝喷氨自动控制分析及优化

SCR烟气脱硝喷氨自动控制分析及优化摘要:随着我国环境保护法律、法规和标准的日趋严格及执法力度的加大,电厂先后进行了燃烧器低碳改造和脱硝装置加装。
其中,大型电站主要主要烟气脱硝技术为选择性催化还原法(SCR),通过化学反应降低NOx排放。
本文主要分析了SCR烟气脱硝喷氨自动控制分析及优化策略。
有不对之处,请批评指正。
关键字:SCR;烟气脱硝;自动控制;优化NOx被证明是引起酸雨、诱发光化学烟雾、温室效应及光化学反应主要物质之一。
根据《火电厂大气污染物排放标准》,降低燃煤电站污染物NOx排放浓度限值,提供清洁能源,建设绿色环保电厂已势在必行。
我国目前新建大型火力发电机组大多采用SCR,选择性催化还原法方法,SCR法一般是将氨类等还原剂喷入烟气中,利用催化剂将烟气中的NOx转化为N2和H2O。
为了确保烟气脱硝效率,增强脱硝系统的可靠性、连续性以及经济性,需要配置可靠性较高的自动调节系统。
笔者结合实际经验,探讨了SCR烟气脱硝喷氨自动控制及优化方法。
1 SCR工作原理及流程SCR工艺是在催化剂作用下以液氨为介质,通过化学反应使NOx转化为N2和H2O。
SCR系统一般由液氨存储系统、氨/空气喷射系统及催化反应器系统组。
首先,将液氨槽车内液氨卸入液氨储槽,然后进入氨气蒸发器将液氨加热蒸发成氨气,再经过气液分离器后氨气调压至所需压力进入氨气缓冲罐,送出气化站供后续使用。
氨气进入SCR区后一般分为两路,反应器内烟气浓度等经DCS计算后通过调节阀调节气氨的流量后进入氨/空气混合器使空气和氨气以文丘里管喷射的方式在混合器内进行混合后送至分配总管,由总管通过每个支管的流量调节进入喷氨格栅,继而进入SCR反应器中与NOx进行催化反应。
2 SCR脱硝控制系统特性分析控制系统对象的动态特性取决于结构特性,SCR脱硝控制系统具有其特殊性,从脱硝系统的工艺流程可看到,氨喷射格栅至SCR反应器上游的位置是氨气与烟气的混合区域,虽然已经喷氨,但由于最终过程是一个化学反应,进入反应器催化剂层前,化学反应没有产生,所以调节不会影响到控制对象。
电站锅炉烟气脱硝系统优化调整试验

电站锅炉烟气脱硝系统优化调整试验摘要:采用 SCR 脱硝装置,在进行脱硝装置设计时,必须充分考虑该装置对锅炉尾部受热面(主要是空气预热器)的堵塞和腐蚀可通过限制氨逃逸量及催化剂的SO2∕SO3氧化率加以控制;对引风机的影响 ( 即锅炉烟气阻力的增加 ) 可通过合理设计烟道形状、合理选取烟气流速、加装导流装置、缩短烟道长度等加以控制。
在进行脱硝装置设计时;对锅炉运行的影响,并应进行技术经济评价,以保证锅炉安全经济运行。
关键词:电站锅炉;烟气脱硝;系统优化;调整试验1导言随着国家对污染物排放标准越来越严格,燃煤电厂烟气脱硝改造势在必行。
对于一些老机组,设备老化,改造难度较大,脱硝技术对于不同电厂出现不同问题,很难达到理想脱硝效率。
2设备概述辽化热电厂7台蒸发量410t/h锅炉。
锅炉的基本型式是:自然循环汽包炉、Π型布置、单炉膛、燃烧器四角布置,切圆燃烧、固态排渣、采用管式空气预热器、钢构架。
设计煤种为铁厂沟露天煤矿,校核煤种为硫磺沟露天矿煤,设计煤种和校核煤种均属于中等结渣特性的烟煤。
锅炉正常运行时 NOx 排放浓度最高超过 600mg/m 3 ,无法满足《火电厂大气污染物排放标准》(GB13223-2011)要求的在 2014 年 7月 1 日前 NOx 排放浓度控制在 100mg/m 3 以内的排放限值要求。
在2013 年至 2015年辽化热电厂分别对 7台机组进行了低氮燃烧器改造和在锅炉尾部烟道低温省煤器前加装烟气脱硝装置。
3脱硝装置投运后对锅炉运行的影响3.1低氮燃烧器对锅炉的影响低氮燃烧器改造后,通过试验调整,在保证锅炉燃烧稳定以及锅炉安全经济运行的情况下,改造效果明显,NOx 排放量大幅降低,锅炉效率不发生变化,能够达到原锅炉运行效率。
3.2 SCR 对锅炉各设备的影响1、对空气预热器的影响。
安装高温高尘型 SCR 装置后,在烟气脱硝过程中所产生的硫酸氢胺将对空气预热器的运行带来较大的负面影响,硫酸氢胺牢固黏附在空气预热器传热元件表面,使传热元件发生强烈腐蚀、积灰。
深度调峰下脱硝系统喷氨优化试验
深度调峰下脱硝系统喷氨优化试验杨宇【摘要】针对燃煤机组在深度调峰低负荷运行工况下选择性催化还原法(SCR)脱硝装置喷氨量大、不均匀、反应器出口NOx质量浓度分布与DL/T 260-2012《燃煤电厂烟气脱硝装置性能验收试验规范》相对标准偏差率(CV)值高等特点.通过对低负荷下SCR脱硝装置的性能进行喷氨优化调整试验,改善其运行状况.经优化调整后,机组在120 MW低负荷下运行时,A侧SCR反应器出口截面NOx质量浓度分布CV值分别由51.7%和28%降低至8.4%、9.8%,平均氨逃逸浓度分别由3.1×10-6和2.1×10-6降为1.8×10-6和0.3×10-6,且SCR反应器出口NOx质量浓度分布均匀性明显改善,局部氨逃逸体积分数峰值明显降低.【期刊名称】《吉林电力》【年(卷),期】2019(047)002【总页数】5页(P52-56)【关键词】脱硝系统;深度调峰;选择性催化还原法;优化调整【作者】杨宇【作者单位】白山热电有限责任公司,吉林白山 134300【正文语种】中文【中图分类】TK223.71;X511近年来,我国风电、光伏发电等清洁能源装机容量迅猛增长[1-2],为了消纳这部分清洁电力,国家能源局出台了一系列相关文件,要求燃煤火电机组作为当前电网调峰的主力军,进一步提高燃煤火电机组的调峰能力和调峰深度,提升我国燃煤火电机组的运行灵活性[3]。
当燃煤火电机组长期参与深度调峰,锅炉处于低负荷下运行时,机组将面临一系列问题[4-5],其中,脱硝系统的安全高效投运是关注的重点之一。
当机组在低负荷下运行时,由于选择性催化还原法(SCR)脱硝装置远远偏离了其设计工况,需要采取宽负荷脱硝技术提升烟温,且低负荷下SCR入口喷氨量一般都偏大,运行成本较高[6]。
对于含硫量较高的机组,低负荷下运行一段时间后,空气预热器被硫酸氢铵严重堵塞[7-8],严重时可能引起炉膛负压的剧烈波动,引发不必要的损失。
2号炉脱硝系统优化调整措施
2号炉脱硝系统优化措施为防止2号炉脱硝系统喷氨量偏大、氨逃逸偏高,导致布袋除尘器差压高影响机组带负荷能力及机组安全性,采取应对措施如下:(一)优化燃烧调整,降低脱硝入口NOx含量1.在保持锅炉燃烧稳定和不结焦的情况下,适当降低运行燃烧器二次风量,增加燃烬风量,保持锅炉氧量不变。
尽量降低SCR入口NOx浓度在300mg/Nm3以下。
2.在正常运行时,运行燃烧器的燃料风门控制在20%-40%,相邻辅助风门控制在20%-45%,但最上层与最下层辅助风门开度不低于40%;停运的制粉系统对应燃烧器相邻辅助风门控制在15%,燃料风门开至10%,冷却燃烧器喷口。
3.在保证运行磨煤机出力的情况下,尽量减少一次风量,降低煤粉燃烧初期的空气量,限制NOx形成。
4.锅炉应急减负荷时,应控制减负荷幅度,尽量保持在不需要投入等离子进行稳燃的负荷以上运行。
若必须投入等离子进行稳燃时,应及时调整好燃烧,在燃烧稳定后尽早退出等离子运行。
5.锅炉低负荷运行时,应通过抬高燃烧器摆角,来提高炉膛火焰中心位置,同时投入脱硝宽负荷烟气旁路,尽量提高脱硝入口烟气温度,保持催化剂活性。
同时避免因脱硝SCR入口烟温低,引起脱硝SCR系统退出运行的事件发生。
6.若给煤机发生断煤或给煤机煤量异常需紧急停运给煤机时,应根据磨煤机出口温度变化情况及时减少一次风量,避免因一次风量过大,燃烧区氧量增加过多,造成脱硝SCR入口NOx急剧上升。
7.燃烧调整控制NOx的生成,应遵循的原则:a.降低燃烧区域的平均温度和峰值温度。
b.减少燃料周围的氧浓度。
c.尽量延长燃料在低氧环境下燃烧的时间。
8.运行中要注意脱硝SCR系统各参数变化情况,发现有表计指示不准时,及时联系检修人员处理,尤其是脱硝SCR入口烟温、NOx含量、氧量等重要表计。
9.当机组增、减负荷或需要调整燃料量、风量时,应缓慢进行调整,防止SCR入口NOx大幅波动。
(二)按工作任务分解表对脱硝设施设备进行检查用机组停备机会,脱硝设施按工作任务分解表(详见附表)进行全面检查,发现问题及时优化整改,以减少喷氨量、降低氨逃逸率。
烟气脱硝SCR氨喷射系统调整效果评估
烟气脱硝SCR氨喷射系统调整效果评估以某火电厂氨喷射系统(AIG)改造为例,通过数值模拟计算,对AIG调整方案的效果开展了评估.结果说明将AIG改为具备双向调节功能后,有利于氨的均匀分配,对于烟气流速不均具有更好的适应性.脱硝反应器出口截面NOx分布相对标准偏差由40%降低至15%以内.可改善脱硝装置喷氨合理性,一定程度上延长催化剂使用寿命,消除反应器出口氨逃逸浓度局部过高的现象,降低了下游空气预热器硫酸氢铵(ABS)腐蚀的风险,对火电厂实现NOx超低排放具有一定奉献.SCR脱硝技术的核心是催化剂和氨喷射混合系统.氨喷射混合系统设计的优劣和实际运行中喷氨的合理性对脱硝装置的运行效果影响明显。
催化剂入口截面的NH3/NO摩尔比及其分布.决定了反应器出口的NOx和氨逃逸浓度分布,并影响到整体脱硝效率和下游设备的硫酸氢铵堵塞程度。
NOx与NH3在顶层催化剂入口的分布均匀性,取决于喷氨格栅上游的NOx分布、烟气流速分布、喷氨流量分配、静态混合器的烟气扰动强度及混合距离等。
常见的氨喷射系统(AIG)氨喷射与混合装置主要有3类:格栅式AIG、混合型AIG及涡流型AIG,这3类氨喷射系统各具优势和适应范围。
对于脱硝工程中氨/烟气混合距离足够长时,几种氨喷射技术均能满足要求。
SCR装置在设计阶段通过CFD数值模拟.对反应器入口烟道、导流板、喷氨格栅、静态混合器及整流装置等开展整体优化设计,最终使进入顶层催化剂的烟气流场到达均匀分布的要求。
由于CFD数值模拟的边界条件是假设进入AIG上游脱硝入口烟气参数分布均匀.而脱硝装置实际运行中AIG上游烟气参数分布受锅炉运行方式及烟道走向等因素影响.与实际运行时的烟气分布存在偏差.需在运行过程中通过氨喷射系统支管上手动阀调整,开展喷氨流量分配的优化调节.但前提是氨喷射系统本身需具有良好的设计性能.满足分区双向调节功能。
1设备概况某火电厂1000MW机组的烟气脱硝SCR装置随锅炉同期建设,现有氨喷射系统采用混合型AIG,每个反应器的AIG 在入口竖直段烟道内沿炉宽方向设19只喷氨支管.每根支管上设置4个喷嘴,相应支管设有手动蝶阀以调节氨喷射流量,实现整个烟道截面上宽度方向的氨喷射流量分配,如图1。
火电厂scr脱硝系统喷氨自动优化
自动化应用 2019.28电子乐园316 火电厂SCR 脱硝系统喷氨自动优化焉建东 孙福杰 葛胜玉 徐明军 房高超 华能威海发电有限责任公司, 山东威海 264205摘要:针对680MW 燃煤机组脱硝系统运行中的一些问题,进行控制系统优化后的系统不仅满足环保排放要求,同时其可靠性及经济性得到提高。
本文基于某直流燃煤锅炉的实例详细介绍了火电厂SCR 脱硝系统喷氨自动控制优化调整过程。
通过优化调整,有效降低了喷氨量,提高自动控制水平,调节效果明显。
关键词:脱硝; 控制系统 ; 优化前言某厂#5锅炉为超超临界一次中间再热、变压运行单炉膛燃煤直流炉,采用MPS 中速磨煤机,直吹式制粉系统、CUF 墙式切圆喷燃、平衡通风、露天布置、固态连续排渣、全钢构架、全悬吊结构Π型锅炉。
采用以五氧化二钒和二氧化钛为催化剂的SCR烟气脱硝。
SCR脱硝系统投运之后,在实际生产过程中发现较多问题。
本文分为五部分,第一部分介绍了SCR脱硝控制系统现状及主要问题,第二部分针对存在的问题进行了分析,第三部分详细介绍了自动优化过程,第四部分对优化后的成果进行了估算。
一、SCR 脱硝控制系统现状及主要问题从现已投运的SCR 脱硝系统的实际运行情况看,控制效果不理想,甚至喷氨自动控制不能正常投入,严重影响脱硝系统的正常运行。
主要表现为以下方面:1) 无法将机组排放净烟气NOx 控制在理想范围内,不能长时间稳定达到环保要求;2) 在机组升降负荷或制粉系统启动、停止时,机组排放净烟气NOx 大幅度波动。
由于控制不稳定,部分电厂采用增加喷氨量的方式来保证机组排放净烟气NOx 的稳定。
此种方法带来的弊端也很明显:喷氨量增大,增加了生产成本且造成NH3的二次污染。
据调查【1】,我国燃煤电站锅炉的NOx 排放量普遍超标,按照目前的排放控制水平,2020 年中国NOX 排放量将达到2900万吨左右,电力行业排放量约占1/2。
过量排放到大气中的氮氧化物对酸雨和光化学烟雾的形成,以及地球臭氧层的破坏有直接的影响。
- 1、下载文档前请自行甄别文档内容的完整性,平台不提供额外的编辑、内容补充、找答案等附加服务。
- 2、"仅部分预览"的文档,不可在线预览部分如存在完整性等问题,可反馈申请退款(可完整预览的文档不适用该条件!)。
- 3、如文档侵犯您的权益,请联系客服反馈,我们会尽快为您处理(人工客服工作时间:9:00-18:30)。
SCR脱硝系统喷氨优化调整试验为了调高脱硝系统效率,在满足环保超低排放标准的前提下,减少喷氨量、降低氨逃逸率、降低空预器堵塞风险,对某电厂超临界2×700MW燃煤机组脱硝系统进行喷氨优化调整试验。
通过调整喷氨手动门开度,合理调节SCR喷氨量,使SCR脱硝系统出口氮氧化物浓度分布的均匀性得到改善,降低了局部氨逃逸峰值,降低了空预器堵塞的风险。
随着火电厂最新大气污染排放标准的颁布及煤电节能减排升级与改造行动计划的实施,燃煤电厂必须更加严格地控制烟气中NO x的排放量。
选择性催化还原(SCR)脱硝技术因脱硝效率高且运行稳定可靠,而被广泛应用于燃煤电厂。
脱硝效率、喷氨量大小和氨气逃逸率是衡量SCR脱硝系统运行是否良好的重要依据。
电厂在实际运行过程中,由于负荷、锅炉燃烧工况、煤种、喷氨格栅阀门开度、烟道流场均匀性、吹扫间隔时间等因素均会影响SCR脱硝效率和氨逃逸率。
逃逸氨在空预器中会生成黏性的硫酸铵或硫酸氢铵,减小空预器流通截面,造成空预器堵灰。
空预器堵灰不仅影响锅炉运行的经济性而且显著降低锅炉安全性,严重影响脱硝机组的安全稳定运行。
目前燃煤电厂可以选择新型的SCR脱硝系统喷氨格栅类型、布置方式及改造喷氨管,调整喷氨量和喷复均匀性,改进催化剂入口氨氮比,优化烟气导流板布置、烟气流速的均布性,或研发与应用烟气脱硝系统自动控制技术。
通过提升自控系统稳定性和可靠性等措施,可提高SCR脱硝系统出口NO x分布均匀性,防止局部氨选逸超标,减轻空预器堵灰、腐蚀、运行阻力等问题。
某厂由于投产时间早,投产时由于国家环保要求不高,脱硝系统按出口氮氧化物排污浓度200mg/m3设计。
随着国家环保要求的提升,为满足发改能源〔2014〕2093号文件《煤电节能减排升级与改造行动计划(2014—2020年)》的要求,该厂将氮氧化物排放浓度稳定的控制到50mg/m3以下,该厂进行了SCR烟气脱硝提效改造,主要是加装5号炉第三层及6号炉第二层催化剂来达到NO x浓度超低排放。
通过上述改造措施,能够将氮氧化物浓度控制到50mg/m3以下,但运行过程中存在局部氨逃逸偏大,自动跟踪系统满足不了运行要求等问题,导致还原剂耗量高、空预器阻力上升较快等问题。
因脱销系统投产时SCR烟气脱硝系统采用传统的线性控制式喷氨格栅技术。
而目前脱硝系统新型结构改造经济成本高、周期长,在现有SCR脱硝系统中开展喷氨优化调整试验,是目前提高氨利用率、减少NO x污染物排放的主要手段,调节SCR脱硝系统喷氨量,改善SCR脱硝系统出口NO x分布均匀性和氨利用率。
1试验对象及参数该厂700MW超临界燃煤5、6号机组的烟气脱硝系统采用选择性催化还原法(SCR)脱硝工艺和板式催化剂,催化剂按“2+1"模式布置,选用二氧化钛、钒化合物作为催化剂,采用液氨制备脱硝还原剂。
SCR烟气脱硝系统采用线性控制式喷氨格栅技术。
喷氨格栅中各组喷嘴之间的气氨喷射具有较强的独立性。
SCR脱硝系统入口每侧布置3层上下交错的喷氨格栅,21支控制喷氨量分配的喷氨手动门。
每个手动门控制3根支管。
每组3个手动门分别对应烟道截面前后部分喷氨。
1.1试验仪器及调整方法SCR脱硝系统喷氨优化试验是根据GB/T16157—1996《固定污染源排气中颗粒物测定与气态污染物采样方法》,DL/T335—2010《火电厂烟气脱硝(SCR)装置运行技术规范》开展的。
根据测定的SCR脱硝系统出口NO x浓度分布情况,调整手动阀门开度,对应调节喷氨流量。
试验时要保证煤质负荷及配风方式等条件的稳定。
由于锅炉炉型、燃烧方式、燃用煤种的限制,目前的设备状况决定了该厂5、6号锅炉炉膛出口氮氧化物已经没有明显改进空间,故在设备不进行改造的情况下无法通过燃烧调整显著降低SCR入口的NO x产生浓度。
同时,由于5、6号锅炉炉膛较宽,炉膛出口氮氧化物浓度分布均匀性偏差较大。
根据投运磨组合方式、机组运行负荷、煤质等的不同,锅炉炉膛出口NO x浓度分布均匀性偏差较大。
目前炉膛出口NO x浓度大小相差约±50mg/m3,环保政策超低排放限制要求烟囱入口NO x浓度低于50mg/m3,为保证NO x 浓度不超标,实际运行时一般都要求控制NO x浓度低于40mg/m3,此种情况下,容易出现局部位置的入口NH3/NO x摩尔比超过1.0,造成局部氨逃逸过大,进而引发局部氨逃逸过大导致的空预器阻力快速上升问题。
为此,通过进行喷氨调整试验来评估现有流场和氨混合系统能够满足超低排放需要,并决定是否需要进一步改造。
1.2测试内容和方法SCR脱硝装置的喷氨优化调整试验主要在机组常规高负荷(100%负荷)进行,并在高、中、低负荷(100%、75%、50%)下进行验证和微调。
根据现场条件和测试要求,试验过程如下:预备与摸底试验:在100%负荷下实测反应器进、出口NO x浓度、氨逃逸等,分别与在线CEMS分析仪表的DCS显示值进行比较,为正式试验做准备。
机组运行稳定,锅炉运行氧量、磨投运组合方式等情况下,减少脱硝装置入口NO x的波动。
喷氨优化调整:在机组100%(负荷稳定)负荷下,根据SCR反应器出口截面的NO x浓度分布,对反应器入口水平烟道上的AIG喷氨格栅的手动阀门开度进行调节,最大限度提高反应器出口的NO x分布均匀性。
AIG优化校核试验:在机组100%、75%、50%负荷下,在设计脱硝效率下测量反应器进出口的NO x浓度分布和氨逃逸,评估优化结果,并根据结果对AIG手动调阀进行微调。
在SCR反应器的进口和出口烟道截面,分别采用等截面网格法布置烟气取样点。
在反应器平台布置一套TESTO350型烟气分析仪,烟气经不锈钢管引出至烟道外,再经过除尘、除湿、冷却等处理后,最后接入烟气分析仪进行分析。
利用烟气分析仪,在反应器的进出口逐点切换采集烟气样品,分析烟气中的NO与O2含量,可获得烟道截面的NO x浓度分布。
取反应器进、出口的NO x浓度的算术平均值计算脱硝效率。
根据反应器出口截面的NO浓度分布,每台反应器选取6个代表点作为NH3取样点。
1.3摸底试验根据测试,5、6号机组在负荷稳定时目前脱硝装置入口NO x浓度在约300mg/m3左右,此入口NO x浓度低于原设计的NO x。
5号机组负荷680MWA、B、C、D、E、F磨煤机投运,SCR 投入自动控制前提下,进行摸底测试,作为喷氨优化调整前基准工况。
6号机组负荷620MWA、B、C、D、E、F磨煤机投运,SCR投入手动控制前提下,进行对比测试。
试验过程中,同步在每台反应器进、出口测量NO x浓度,同时在反应器出口采集氨逃逸样品,用于计算脱硝效率与氨逃逸,初步评估脱硝装置的效率和氨喷射流量分配状况。
测试结果(表1)表明,喷氨优化调整试验前,5号炉脱硝装置A、B两侧脱硝效率分别为69.6%、87.2%,A、B两侧烟道截面平均氨逃逸浓度分别为1.7μL/L、5.2μL/L,A、B侧单点最大氨逃逸分别为2.4μL/L、12.7μL/L;6号炉脱硝装置A、B两侧脱硝效率分别为76.2%、84.7%,A、B两侧烟道截面平均氨逃逸浓度分别为1.2μL/L、0.9μL/L,A、B 侧单点最大氨逃逸分别为2.3μL/L、1.6μL/L。
表1优化调整前的脱硝效率、氨逃逸分析对比5号机组脱硝反应器出口NO x分布结果见图1、2。
摸底试验工况下A、B侧脱硝反应器入口NO x分布相对偏差在10%以内,说明入口NO x分布相对较为均匀。
A侧喷氨量65kg/h,B侧喷氨量75.18kg/h。
实测A侧入口NO x浓度263.8mg/m3,B侧入口NO x浓度274.5mg/m3;DCS显示A侧入口NO x浓度263.1mg/m3,B侧入口NO x浓度296.5mg/m3。
实测A侧出口NO x浓度80.3mg/m3,NO x浓度最大值为134.0mg/m3,最小值为47.8mg/m3。
B侧出口NO x浓度35mg/m3,NO x浓度最大值为67.2mg/m3,最小值为16.7mg/m3;DCS显示A侧出口NO x浓度87.8mg/m3,B侧出口NO x浓度68.3mg/m3。
图15号炉脱硝反应图1 5号炉脱硝反应器出口NO x分布图图2 5号炉摸底试验反应器出口测孔内NO x及氨逃逸分布A侧反应器出口截面NO x浓度分布相对标准偏差为27.0%,初步计算第一层催化剂入口NH3/NO摩尔比偏差为8.2%;B侧反应器出口截面NO x浓度分布相对标准偏差为5.0%。
从图2可以看出,摸底试验表现出A侧靠近中心线位置处存在单点过大的情况,但整体NO x浓度分布无明显规律。
根据实测值与表盘氨气用量,B侧由于喷氨量高于A侧,导致B侧的氮氧化物较A侧低,且B侧由于喷氨不均,出现了氨逃逸超过3μL/L的点,意味着B侧空预器堵塞的风险较A 侧高,烟风系统也显示B侧空预器阻力高于A侧约300Pa,反映出现场实测数据无误。
对比6号机组脱硝反应器出口NO x分布结果(图3和图4):摸底试验工况下A、B侧脱硝反应器入口NO x分布相对偏差在10%以内,说明入口NO x分布相对较为均匀。
A侧喷氨量75.6kg/h,B侧喷氨量78.1kg/h。
实测A侧入口NO x浓度291.5mg/m3,B侧入口NO x浓度261.5mg/m3;DCS显示A侧入口NO x浓度342.5mg/m3,B侧入口NO x浓度310.6mg/m3。
实测A侧出口NO x浓度69.4mg/m3,NO x浓度最大值为143.3mg/m3,最小值为15.1mg/m3。
B侧出口NO x浓度40mg/m3,NO x浓度最大值为114.5mg/m3,最小值为15.5mg/m3;DCS显示A侧出口NO x浓度51.1mg/m3,B侧出口NO x浓度42.7mg/m3。
A侧反应器出口截面NO x浓度分布相对标准偏差为44.7%,初步计算第一层催化剂入口NH3/NO摩尔比偏差为10.6%;B侧反应器出口截面NO x浓度分布相对标准偏差为9.6%。
从图3可以看出,摸底试验中反应器出口整体NO x浓度分布无明显规律。
对比摸底试验5、6号机组的测试数据,6号机NO x浓度分布相对偏差较小,由于两台炉导流板、喷氨系统设计均相同,主要在于锅炉燃烧和喷氨支管阀门开度不一致。
因此,6号机只需对部分喷氨支管阀门开度进行微调。
由于5号机NO x浓度分布相对偏差较大,此次试验重点是对5号机进行调整。
图3 6号炉脱硝反应器出口NO x分布图图4 6号炉摸底试验反应器出口测孔内NO x及氨逃逸分布1.4验证试验在5号机组600~680MW稳定负荷条件下,根据摸底测试测得SCR反应器出口截面的NO x浓度分布结果,对反应器入口竖直烟道上喷氨格栅不同支管的手动阀开度进行调节,经过多次调整格栅开度,两个反应器出口截面的NO x分布均匀性均有一定改善。