EB-PVD制备热障涂层完整介绍
一种热障涂层及其制备方法

一种热障涂层及其制备方法简介热障涂层是一种用于保护高温工作环境下金属材料的表面涂层。
热障涂层具有优良的隔热性能和耐高温性能,广泛应用于航空航天、能源等领域。
本文介绍了一种新型的热障涂层及其制备方法。
热障涂层制备方法原材料准备制备该热障涂层的原材料主要包括氧化铝粉末、稳定剂、粘结剂和溶剂。
其中,氧化铝粉末作为主要成分,具有优异的隔热性能和耐高温性能。
涂料的制备首先,将氧化铝粉末与稳定剂按一定比例混合,通过高能球磨机进行混合研磨,使其达到均匀的颗粒分布。
然后,将粘结剂和溶剂加入混合好的氧化铝粉末中,通过搅拌机进行搅拌,保证其成为均匀的涂料。
涂层的制备首先,需要将待涂层的金属基材表面进行喷砂处理,以提高涂层与基材的附着力。
然后,将制备好的涂料通过喷涂技术喷涂在金属基材表面,形成一层均匀的涂层。
喷涂过程中,需要保持适当的喷涂速度和喷涂厚度,以确保涂层质量。
热处理喷涂完成之后,将涂层烘干,以去除涂料中的溶剂。
然后,将含有涂层的金属基材进行高温热处理。
在高温环境下,涂料中的氧化铝粉末会发生热化学反应,生成具有良好结晶性和致密度的氧化铝涂层。
热处理过程中,需要控制温度和时间,以保证涂层的性能。
热障涂层的特点该热障涂层具有以下特点:1. 优异的隔热性能:热障涂层可有效减少热量传导,降低金属基材温度,提高工作环境下的工作效率。
2. 耐高温性能:热障涂层能够在高温环境下保持稳定,同时具有良好的抗氧化性能。
3. 良好的附着力:该涂层与金属基材的附着力强,不易脱落,具有较长的使用寿命。
应用前景这种热障涂层可以广泛应用于航空航天、能源等行业。
在航空航天领域,可以应用于发动机燃烧室内的金属壁面保护,提高发动机的工作效率和寿命;在能源领域,可以应用于燃煤电厂锅炉中的金属表面保护,减少能源损失,提高发电效率。
结论通过本文介绍的制备方法,我们可以制备一种新型的热障涂层。
这种热障涂层具有优异的隔热性能和耐高温性能,具有良好的应用前景。
新型热障涂层的制备与应用研究
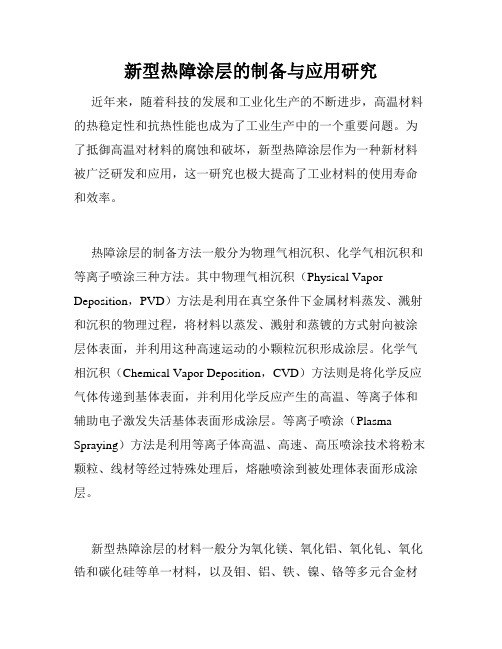
新型热障涂层的制备与应用研究近年来,随着科技的发展和工业化生产的不断进步,高温材料的热稳定性和抗热性能也成为了工业生产中的一个重要问题。
为了抵御高温对材料的腐蚀和破坏,新型热障涂层作为一种新材料被广泛研发和应用,这一研究也极大提高了工业材料的使用寿命和效率。
热障涂层的制备方法一般分为物理气相沉积、化学气相沉积和等离子喷涂三种方法。
其中物理气相沉积(Physical Vapor Deposition,PVD)方法是利用在真空条件下金属材料蒸发、溅射和沉积的物理过程,将材料以蒸发、溅射和蒸镀的方式射向被涂层体表面,并利用这种高速运动的小颗粒沉积形成涂层。
化学气相沉积(Chemical Vapor Deposition,CVD)方法则是将化学反应气体传递到基体表面,并利用化学反应产生的高温、等离子体和辅助电子激发失活基体表面形成涂层。
等离子喷涂(Plasma Spraying)方法是利用等离子体高温、高速、高压喷涂技术将粉末颗粒、线材等经过特殊处理后,熔融喷涂到被处理体表面形成涂层。
新型热障涂层的材料一般分为氧化镁、氧化铝、氧化钆、氧化锆和碳化硅等单一材料,以及钼、铝、铁、镍、铬等多元合金材料。
其中,单一氧化物涂层由于其良好的热稳定性能、化学稳定性和热导率低等特性,成为了热障涂层中最为常见的材料。
在应用方面,新型热障涂层被广泛应用于航空引擎、燃气轮机、锅炉、船舶等各个领域。
在航空制造业中,热障涂层可根据材料的性能分为多层涂层和单层涂层。
多层涂层包括有刚性涂层和热障涂层,根据应力分布可分为TBC层和MBC层。
刚性涂层是一种底层涂层,主要是增加涂层的黏着力和提高表面的硬度,同时可降低涂层与基体之间的热应力。
热障涂层的作用则主要是在飞行过程中起到隔热和保护的作用,减小温度对叶片等部件的影响,降低机械强度的丧失。
在燃气轮机中,热障涂层则被应用于燃气轮机的叶片、燃烧室、涡轮、导叶等部件表面,并具有延长使用寿命、提高效率、减少故障等优点。
EB-PVD热障涂层对IC10合金高温持久性能的影响

层 的过 程 中 , 用 E型 电 子枪 所 产生 的高 温 电子 束 采
流将 Y Z进 行 蒸 发 , 其 沉 积 在 试 样 上 , 蒸 镀 的 S 使 在
更小 的表面粗 糙 度 , 制 备 热 障 涂层 的最 佳 工 艺 技 是 术 。本 试验 采用 E -V 工 艺制 备 热 障 涂 层 , BP D 研
究 了沉 积 热 障涂 层 的 I 1 C 0合 金 在 9 0《下 的高 温 8a = 持 久性 能及 断 口形 貌 和组 织 变 化 , 为带 有 热 障涂 层 的 II C O合 金在 航空 发 动机上 的实际 应用 提供 依据 。
层 的使 用 可 以延 长发动 机使 用 寿命 和提 高发 动机 效 率, 由于 热 障涂层 与基 体合 金性 能相 差 很大 , 必须 采 取合 适 的制备 工 艺 , 热 障涂 层 在 起 到 隔 热 和 延 寿 使 的 同时 不影 响基 体 合 金 的力 学 性 能 。E .V B P D热 障
材料用 于 更 高推 重 比航 空 发动 机 成 为 可能¨ 。 川 试 样 所使 用 的 基体 材 料 为 金 属 间化 合 物 I I C O, 北京 航 空材 料研 究 院 自制 , 定 向凝 固的 I 1 将 C 0合金
试 棒加 工 成 尺寸 为  ̄ m ×2 m 的 台阶 圆柱 形 高 b m 5 5m 温 持久 试样 。热 障涂 层 的粘 结 层 为 N C AY i 属 ir 1 S 金 包 覆 型涂 层 , 厚 度 大 约 为 3 m, 用 电 弧 离 子 镀 其 0 采
随 着航空 发 动 机 向高 推 重 比方 向发 展 , 轮 进 涡 口温 度不 断提 高 , 即使 采用 先进 的气 膜冷 却 技术 , 叶
热障涂层隔热性能研究
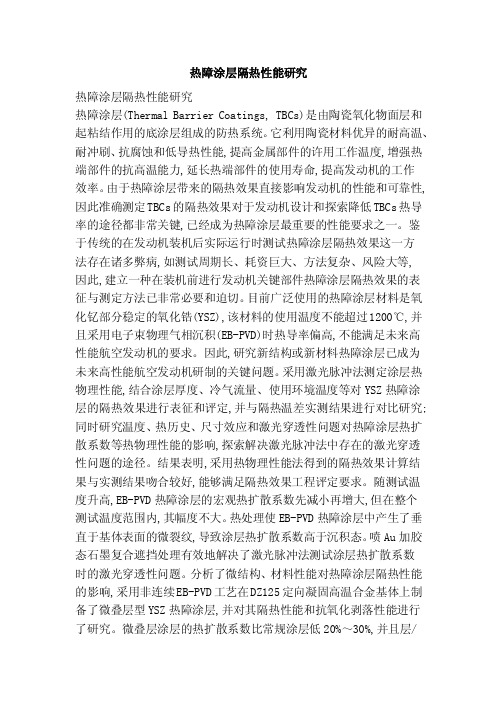
热障涂层隔热性能研究热障涂层隔热性能研究热障涂层(Thermal Barrier Coatings, TBCs)是由陶瓷氧化物面层和起粘结作用的底涂层组成的防热系统。
它利用陶瓷材料优异的耐高温、耐冲刷、抗腐蚀和低导热性能,提高金属部件的许用工作温度,增强热端部件的抗高温能力,延长热端部件的使用寿命,提高发动机的工作效率。
由于热障涂层带来的隔热效果直接影响发动机的性能和可靠性,因此准确测定TBCs的隔热效果对于发动机设计和探索降低TBCs热导率的途径都非常关键,已经成为热障涂层最重要的性能要求之一。
鉴于传统的在发动机装机后实际运行时测试热障涂层隔热效果这一方法存在诸多弊病,如测试周期长、耗资巨大、方法复杂、风险大等,因此,建立一种在装机前进行发动机关键部件热障涂层隔热效果的表征与测定方法已非常必要和迫切。
目前广泛使用的热障涂层材料是氧化钇部分稳定的氧化锆(YSZ),该材料的使用温度不能超过1200℃,并且采用电子束物理气相沉积(EB-PVD)时热导率偏高,不能满足未来高性能航空发动机的要求。
因此,研究新结构或新材料热障涂层已成为未来高性能航空发动机研制的关键问题。
采用激光脉冲法测定涂层热物理性能,结合涂层厚度、冷气流量、使用环境温度等对YSZ热障涂层的隔热效果进行表征和评定,并与隔热温差实测结果进行对比研究;同时研究温度、热历史、尺寸效应和激光穿透性问题对热障涂层热扩散系数等热物理性能的影响,探索解决激光脉冲法中存在的激光穿透性问题的途径。
结果表明,采用热物理性能法得到的隔热效果计算结果与实测结果吻合较好,能够满足隔热效果工程评定要求。
随测试温度升高,EB-PVD热障涂层的宏观热扩散系数先减小再增大,但在整个测试温度范围内,其幅度不大。
热处理使EB-PVD热障涂层中产生了垂直于基体表面的微裂纹,导致涂层热扩散系数高于沉积态。
喷Au加胶态石墨复合遮挡处理有效地解决了激光脉冲法测试涂层热扩散系数时的激光穿透性问题。
PVD

PVD(Physical Vapor Deposition),指利用物理过程实现物质转移,在真空的条件下,将原子或分子由源转移到基材表面上的过程。
它的作用是可以是某些有特殊性能(强度高、耐磨性、散热性、耐腐性等)的微粒喷涂在性能较低的母体上,使得母体具有更好的性能!基本方法:真空蒸发、溅射、离子镀(空心阴极离子镀、热阴极离子镀、电弧离子镀、活性反应离子镀、射频离子镀、直流放电离子镀溅射、离子镀。
)最初运用于高速钢刀具涂层,现在发展到硬质合金,陶瓷刀具的涂层运用,与CVD工艺相比,PVD工艺处理温度低,在600℃以下的低温时对刀具材料的抗弯强度无影响;薄膜内部应力状态为压应力,更适于对硬质合金精密复杂刀具的涂层。
尽管目前国内刀具涂层技术与国际先进水平相比存在较大差距, 普通的TiAlN 涂层技术也还不成熟, 但巨大的应用市场及国家对创新、绿色制造技术日益迫切的要求, 已经推动了国内刀具涂层技术的创新发展。
刀具涂层技术在国内掀起了第二次开发热潮, 纳米超硬膜技术已成为涂层领域研究开发的热点。
薄膜的生长工艺受如下几组相互依赖的因素影响: ( 1) 蒸汽源参数, ( 2) 等离子及迁移参数, ( 3)粒子动能( 冲击) 参数, ( 4) 基体参数。
这些参数分为宏观参数( 如蒸汽源功率、反应室总气压、靶源与基体间的距离等)和微观参数( 如在基体表面的离子和中性粒子流通量、能量)在国际上,除制备涂层外,EB-PVD (电子束物理气相沉)技术在新型复合材料制备、零件修复、难加工材料的净成形等制造领域也具有巨大的发展前景。
随着EB-PVD 技术的发展,尤其是离子束辅助EB-PVD 技术的出现,给其他各种涂层的制备带来了广阔的发展空间。
将EB-PVD 技术应用到微电子、光学等行业。
在航空方面相对于传统的,利用EB-PVD 制备热障涂层,是实现高推比发动机的一。
PVD法在多组分薄膜研制上取得重大进展, 象TiN/VN 和TiN/NbN 等氮化物的纳米尺度超晶格薄膜在强度和硬度等方面与立方氮化硼(已知第二最硬材料) 相当, 许多过渡金属多组分多层体系或梯度材料,如钛基材料TiAl-N.TiHf-N、TiZr-N 等和铬基材料CrAl-N 等多组分超硬薄膜是很好的刀具薄膜候选材料.1.国内PVD技术应用与研究现状.2007年第41卷I6 33 四川大学梁红樱,赵海波2.EB_PVD及其制备功能涂层的研究进展 2007 年增刊 1 哈尔滨工业大学复合材料与结构研究所滕敏,孙跃3.低温PVD 法制备多组分超硬薄膜研究 2003 第21卷第一期清华大学新型陶瓷与精细工艺国家重点实验室彭志坚, 齐龙浩4.对我国刀具涂层技术现状及发展趋势的认识 2009年第9期技术平台科技经济市场包头铝业有限公司,内蒙古包头赵晓燕5.PVD溅射技术在MEMS器件制作中的应用 2006年十月第19卷第五期传感技术学报国防科技大学机电工程与自动化学院王雄吴学忠。
热障涂层制备方法的研究现状

当等离子射流中高速(600 -800 m/s)运动的 熔融或者半熔融粉体垂直撞向基底表面时,速 度瞬间降为0,同时在冷却系统的作用下,粉 体和基底温度迅速冷却,发生塑性变形,同时 粘结在基底表面,重复喷涂次数,直到达到要 求厚度。喷涂主要参数包括喷涂功率、送粉速 率、氢气速率、喷涂距离、工件温度。
大气等离子喷涂具有以下优点:大气等离 子喷涂制备的涂层孔隙率较高 ,呈层状结构, 隔热性能良好;大气等离子喷涂制备涂层的粉 体范围广泛,从低熔点的电解质到高熔点的氧 化错都可以进行大气等离子喷涂;设备采用智 能机器人控制,制备精度高,受外界条件影响 小;点火起弧较容易,电极寿命较长,使用性能 稳定。缺点是:对喷涂工件的尺寸及材质有一 定要求(工件内孔必须满足火焰和喷枪能正常 工作的最小距离),材质必须耐一定的工作温 度,对粉体材料的利用率不高。
2.2 电子束物理气相沉积
电子束物理气相沉积(EB -PVD)技术是 利用高能电子束加热陶瓷原料,使陶瓷原料以 气态原子的形式产生原子蒸气,然后沉积到基 底表面形成涂层⑼。EB - PVD制备的热障涂 层呈柱状结构,致密度高,可以通过调控电子 束能量密度来制备平缓过渡梯度涂层,涂层的 抗热震性能良好何。但是,其对工件的尺寸 有严格要求、设备昂贵、沉积效率低等限制了 其进一步地大规模应用。
先进热障涂层的概述
六铝酸盐等离子喷涂涂层能产生分割裂纹网络(见图3),这增加 了涂层的应变公差进而产生了一个热冲击抗力,在TBC应用中这是很有 利的。当把它用作双层TBC系统的顶层材料时,在高达1350℃的热梯 度燃烧室测试中它表现出很不错的寿命。
图3 1200℃等温热处理后镧-锂-六铝酸盐大气等离子喷 涂涂层的典型分割裂纹的显微图像
Байду номын сангаас 背景
随着航空业的发展,对热障涂层的要求越来越高。为了达到降低燃烧 室内金属基体的温度提高使用寿命,提高涡轮发动机的点火温度来 提高它的工作效率这样的目的。我们研究了许多种热障涂层材料, 其中使用最 广泛的应该就是YSZ。但是YSZ也存在一些不足,由EB-PVD 和APS方法加工的YSZ含有亚稳态的T`相。长时间处于高温状态下,它能 够分解成高氧化钇相和低氧化钇相。后者在冷却过程中将会转变成为 单斜晶并伴随较大的体积增加,这将导致TBC的失效。公认的上限温 度是1200℃。另外,由于有限的相稳定性将导致涂层应变公差减小, 从而降低了它的高温性能,因此涂层会过早的失效。
总结
我们研究了很多不同的TBC材料,其热导率和热膨胀系数 在图5中有所标示。很明显,烧绿石材料占据着最令人关注 的区域 (低热导率及高膨胀系数)。这些材料在加工过程 中也没有出现很严重的问题,这表明就目前而言,这些材 料是比较合适的TBC材料。
图5 新型TBC材料的热导率和热膨胀系数分布图
尽管钙钛矿的整体特性很不错,但是它的韧性不如YSZ。在大气 等离子喷涂过程中,由于氧化物蒸汽压的不同导致组成锆酸盐中的非 氧化锆成分以及复杂钙钛矿中的氧化镁先蒸发。这种效应会导致不利 于涂层性能的非化学计量相的沉积。最近的研究表明,通过优化等离 子喷涂参数来缩短粒子在等离子焰流中的时间能够使这种效应最小化。
热障涂层技术在航空发动机上的应用与发展
Application and Development of Thermal Barrier Coatings on Aero Engines
MU Ren-de,LU Feng,HE Li-min,HE Shi-mei,HUANG Guang-hong
(Beijing Institute of Aeronautical Materials,Beijing 100095,China)
要求,P&W 公司又成功地开发了第 3 代涡轮叶片 EB-PVD 热障涂层——PWA266。该涂层采用EB-PVD 制备 7YSZ 陶瓷面层、低压等离子喷涂(LPPS)的 NiCoCrAlY 金属粘结层,该涂层消除了叶片蠕变疲 劳、断裂和叶型表面抗氧化陶瓷的剥落,使其寿命 比未喷涂该涂层叶片的寿命延长了 3 倍。PWA266 以其极好的耐久性、抗热剥落性能和耐热性,在 JT9D 和 PW2000 发动机上得到成功验证之后,于 1989 年首先应用到 PW2000 发动机涡轮叶片上,之 后又应用至 JT9D-7R4、V2500、F100-PW-229 和 F119 等发动机涡轮叶片上。应用该涂层后,F119 发动机高压涡轮工作叶片工作温度比未喷涂该涂 层叶片的可提高 150K 左右。除此之外,PW 公司 在 JT3D 和 JT38D 发动机的风扇叶片、压气机叶片、 燃烧室、涡轮叶片等处均用了热障涂层。
EB-PVD热障涂层微观损伤行为
EB-PVD热障涂层微观损伤行为姜涛;刘德林;刘洲;牟仁德;何利民【摘要】针对EB-PVD制备的热障涂层,通过对拉伸、疲劳、持久、撞击、慢速压缩、三点弯曲、振动等单一条件下,以及热循环、热冲击、超温等复合条件下涂层微观损伤特点进行观察,结合机械应力、热应力特点以及涂层氧化损伤过程,对热障涂层微观损伤类型进行划分.总结归纳出陶瓷层晶簇间垂直裂纹、陶瓷层水平台阶裂纹、陶瓷层V形崩裂、柱状晶弯折、柱状晶簇崩落、等轴晶区水平裂纹、陶瓷层水平撕裂、陶瓷层微鼓分离、氧化层破碎、粘结层内氧化、粘结层垂直裂纹、粘结层裂纹钝化、粘结层皱曲等13种损伤形式,这些基本损伤构型的归纳总结有助于对热障涂层复杂环境下失效行为的深入研究.【期刊名称】《失效分析与预防》【年(卷),期】2018(013)004【总页数】7页(P261-267)【关键词】热障涂层;典型条件;微观损伤行为;应力;氧化;裂纹;损伤形式【作者】姜涛;刘德林;刘洲;牟仁德;何利民【作者单位】中国航发北京航空材料研究院, 北京100095;航空工业失效分析中心, 北京100095;航空材料检测与评价北京市重点实验室, 北京100095;材料检测与评价航空科技重点实验室, 北京100095;中国航发北京航空材料研究院, 北京100095;中国航发北京航空材料研究院, 北京100095;中国航发北京航空材料研究院, 北京100095;中国航发北京航空材料研究院, 北京100095【正文语种】中文【中图分类】V261.930 引言为了满足航空发动机涡轮叶片等热端部件材料更加苛刻的服役环境要求,热障涂层(TBCs)技术得到了广泛重视,涂层失效及寿命是热障涂层研究和能否实现工程应用首先需要关注的问题[1-2]。
热障涂层的失效涉及多因素耦合作用,其失效行为和机理异常复杂。
例如陶瓷涂层与基体之间热膨胀系数差异产生的热应力、粘结层氧化导致TGO层增厚产生的应力、YSZ相变应力、YSZ陶瓷层的烧结收缩应力以及熔盐沉积带来的热腐蚀破坏等等。
- 1、下载文档前请自行甄别文档内容的完整性,平台不提供额外的编辑、内容补充、找答案等附加服务。
- 2、"仅部分预览"的文档,不可在线预览部分如存在完整性等问题,可反馈申请退款(可完整预览的文档不适用该条件!)。
- 3、如文档侵犯您的权益,请联系客服反馈,我们会尽快为您处理(人工客服工作时间:9:00-18:30)。
电子束物理气相沉积(EB-PVD)技术制备热障涂层技术黄升摘要:本文介绍电子束物理气相沉积(EB-PVD)制备热障涂层技术,结合发展历程综述其技术原理、设备构造及工艺特点。
关键词:电子束物理气相沉积(EB-PVD)热障涂层1 引言当今航空涡扇发动机正朝高流量比、高推重比和高涡轮进口温度方向发展,这就使得发动机叶片所承受温度不断升高,据报道目前商用飞机燃气温度达1500 °C、军用飞机燃气温度高达1700 °C[1]。
而当前所使用镍基高温合金最高工作温度只能达到1200 °C,并几乎已达到其使用温度上限,提升空间极其有限。
面对发动机使用的高温障碍,降低发动机叶片温度就成了极其关键的任务。
热障涂层就是一种降温的有效途径(见图1),自20世纪70年代初问世以来[2],受到广泛重视并迅速发展成为高温涂层研究的热点[3-8]。
图1 涡轮叶片承温能力所谓热障涂层(Thermal Barrier Coatings, TBCs)是指由金属缓冲层或者黏结层和耐热性好、隔热性好的陶瓷热保护功能层组成的层合型金属陶瓷复合涂层系统[9]。
一般由具有一定厚度和耐久性的陶瓷涂层、金属粘结层和承受机械载荷的合金组成。
目前根据不同设计要求热障涂层具有如图2所示双层、多层、梯度系统三种结构形式。
图2 热障涂层结构示意图而电子束物理气相沉积(Electron bean-physical vapor deposition EB-PVD)制备热障涂层(TBCs)是在20世纪80年代开发,近年来不断发展成熟起来的新技术,其使用高能电子束加热并汽化陶瓷源,陶瓷蒸汽以原子形式沉积到基体上而形成涂层。
EB-PVD法制备的TBCs涂层表面光洁,有良好的动力学性能;涂层/基体的界面以冶金结合为主,结合力强,稳定性好。
特别是其制备涂层组织为垂直基体表面柱状晶结构,具有很高的应变容限,较热喷涂制备涂层热循环寿命提升巨大。
另外EB-PVD工艺技术精密,具有良好的可重复性。
简而言之,EB-PVD法制备热障涂层是兼具优良性能和巨大应用潜力的前沿技术。
2 EB-PVD技术发展历程EB-PVD技术是伴随着电子束与物理气相沉积技术的发展而发展。
直到上世纪中叶,电子束与物理气相沉积技术结合并成功地用于材料焊接及镀膜(或涂层)的制备。
20世纪80年代,美国、德国等西方国家开始利用EB-PVD工艺制备热障涂层,但由于该设备在西方国家价格昂贵,且制备成本高,这使得对EB-PVD 技术的开发曾经一度停止[10, 11]。
20世纪50年代,前苏联对EB-PVD设备和工艺的投入全部集中在乌克兰巴顿焊接研究所,该所设计制造了30多台各种类型的EB-PVD设备。
前苏联解体后,在科学院院士B A Movchen的领导下,乌克兰巴顿焊接研究所成立了电子束国际中心(International Center for Electron Beam Technologies, ICEBT),并将EB-PVD设备的成本降低到接近西方国家同类设备的1/5。
该中心成功地在叶片上制备出热障涂层,现已得到应用。
到了上世纪九十年代中期,随着乌克兰巴顿焊接研究所研制的低成本的EB-PVD设备在世界各国的推广,从而掀起了EB-PVD技术的开发的新热潮[12-14]。
鉴于等离子喷涂(APS)涂层表面粗糙度大、孔隙多,难以适应气动性要求高的飞行器发动机涡轮转子叶片,加之APS涂层热稳定性和抗热冲击、热腐蚀性差。
因此自20世纪70年代开始国外对EB-PVD制备TBCs开展了大量研究,自20世纪80年代美国、德国均获得可成功的应用[15]。
由于EB-PVD TBCs柱状组织结构,能非常牢固地粘接在金属基体上,当基体受热膨胀时,柱状陶瓷晶体在水平方向具有大膨胀系数与基体匹配,在平面内的杨氏模量较低,可更多地释放热应力,具有较好的抗热冲击性。
正是这种高应力容限,使这种TBCs 在高应力发动机上成功工作而不致剥落。
这种特性是等离子喷涂TBCs不具备的。
EB-PVD制备的TBCs在航空航天领域得到了广泛应用并发挥了巨大作用,正常情况下,TBCs可降低金属表面温度50~80 °C,个别高温点降温可达140 °C。
以EB-PVD技术在梯度热障涂层的研究历程中起的作用为例,为了解决金属与陶瓷热膨胀系数不匹配造成陶瓷层过早剥落现象,德国和加拿大研究人员最先提出了梯度热障涂层的设想。
梯度热障涂层(图3)顶层YSZ(Yttria Stabilized Zironia)陶瓷层,底层为NiCoCrAlY金属粘接层,在二者之间引入了Al2O3-YSZ 梯度过渡层[16, 17]。
该系统中金属粘接层到陶瓷层为连续过渡,消除了层状结构的明显层间界面,使涂层力学性能由基体向陶瓷层连续过渡。
B A Movchan等人[18]选用Al-Al2O3-YSZ作为梯度过渡材料,利用EB-PVD采用单源多组分蒸发技术制备梯度热障涂层。
采用EB-PVD方法制备梯度热障涂层,将在YSZ陶瓷层内形成柱状晶结构,极大地提高陶瓷层的容应变能力。
当Al2O3和ZrO2共同蒸发时,将在基体上得到具有微观多孔结构的Al2O3-YSZ混合层,可以降低材料的热导率。
EB-PVD制备梯度TBC 的抗热震性能得到了提高,在1135 °C (24 h)风冷至50 °C的热循环试验条件下,涂层能持续1500 h。
图3 梯度系统结构3 EB-PVD技术原理、设备结构及工艺特点3.1 EB-PVD技术原理电子束物理气相沉积(EB-PVD)技术是电子束技术与物理气相沉积技术相结合的产物。
它是在真空环境下,利用高能量密度的电子束加热放入水冷坩埚中的被蒸发材料,使其达到熔融气化状态,并在基板上凝结成膜的技术。
其物理过程如下:被蒸发材料(固态)→金属熔融物和蒸气(气态)→涂层(固态)3.2 EB-PVD设备结构图4为乌克兰GEKONT公司研制的L5型EB-PVD设备[19]。
该设备为工业型电子束设备,全长近9 m,总功率为280 kW,由容积为116 m3和位于主真空两侧的1至2个预真空室组成。
图4 EB-PVD设备工作原理图配备8把电子枪,4个电子枪可分别或同时蒸发对应的4个锭料,2个电子枪用于从下方对基板进行加热,另外2个电子枪用于从上方对基板进行加热。
每个电子枪的功率为60 kW,电子枪主要有直式皮尔斯枪和电磁偏转式枪。
该设备采用的是直式皮尔斯枪,该枪具有结构简单,价格低廉和能量密度低等优点。
聚焦电压为25 kV,电子束流2~3 A。
3.3 EB-PVD工艺特点如前所述,电子束物理气相沉积法是以电子束为热源的一种蒸镀方法,在真空环境下(一般为0~10-2 Pa),利用高能密度的电子束轰击蒸镀材料(金属、陶瓷等)使之熔化、气化、蒸发,在基板上沉积形成涂层。
其工艺具有以下特点[20]:(1)在真空条件下着沉积涂层,有利于避免基板和涂层之间污染和氧化,便于获得质量较高的涂层;(2)电子束功率易于调节,束斑尺寸和位置易于控制,有利于精确控制涂层厚度;(3)选择适当的工艺参数,可得到与被蒸镀材料的成分相同,元素含量基本一致的涂层;(4)与其他蒸镀方法比,蒸发速率和沉积速率高(分别可达10~15 kg/h和100~150μm/min)工艺重复性好;(5)电子束所具有的高能量密度可以熔化、蒸发一些难熔材料物质,即使蒸气压较低的元素(如Mo、Nb等)也能利用该工艺蒸发;(6)基体与涂层之间有较高的结合力。
3.4 EB-PVD工艺参数由于电子束物理气相沉积(EB-PVD)是一个真空沉积过程,从蒸发材料表面的蒸汽流直接传输到基体上,沉积物达到基板的表面可能以几种状态存在:与基体完全粘结,扩散进入基体;与基体反应或不与基体反应。
而这些均可以通过改变基板的条件或调整气液相的冷却速率来控制。
许多制备工艺参数都会影响到EB-PVD涂层的组织结构和性能,如受到残余气体压强、蒸发材料的性质、电子束的特性以及基板温度等一系列因素的影响[21]。
3.4.1 蒸发温度蒸发温度直接影响沉积速率和质量,通常将蒸发物质加热,使其平衡蒸气压达到几帕以上,这时的温度定义为蒸发温度。
根据热力学理论,材料蒸气压p与温度T之间的关系可以近似表示为:(1)式中:A、B分别为与材料性质相关的常数(可以直接由实验确定或查阅相关文献获得);T 为热力学温度,单位为K;p为材料的蒸气压,单位为mmHg。
3.4.2 气体压强的影响为保持蒸气流和电子束可以畅通无阻的传输,必须使真空室的压强保持足够低。
如果残余气体粒子密度处于较低的水平,那么就可以忽略蒸气粒子与电子和残余气体粒子相互碰撞的影响。
但是蒸发表面附近,高的蒸气密度使蒸气与电子束束流发生相互作用,碰撞使蒸气粒子和电子偏离其原有的轨道,从而降低材料的利用率和能量的利用率,由碰撞引起的电子能量损失伴随着蒸气的激发和电离。
对于压强为0.01 Pa的残余气体来说,蒸气流和电子流之间的相互作用都可以忽略不计;在气体压强为0.01~1 Pa时,与气体的相互作用非常显著,必须考虑电子与蒸气之间的相互作用。
3.4.3 蒸发和凝聚的作用若用单位时间内从单位面积蒸发的质量即质量蒸发速率N m来表示蒸发速率,考虑到碰撞到液面或固面的分子只有部分凝聚,引入系数α(α<1),则:(2)引入气体状态方程p=nkT后,代入常数项,得(3)式(3)说明蒸发速率与蒸气压和温度之间密切相关,蒸发物质的饱和蒸气压和蒸气压随温度的变化呈指数变化,当温度变化10%时,饱和蒸气压要变化大约1个数量级。
因此,控制蒸发速率的关键在于精确控制蒸发温度。
当两种组元的凝聚系数都接近1时(即沉积层中B组元的含量X B4与蒸气中的含量X B3),蒸发参数与X B3之间的关系是(4)组元含量按重量百分比给出,并且X A3+X B3=100。
F A和F B是蒸气发射表面面积。
假定:整个蒸发容器表面上的蒸发速率是相同的,并且F B/F A是一个常数。
于是在多源蒸发共沉积时,沉积层中组元B的含量X B4可以通过改变各个坩埚的温度T A和T B来调节。
工业应用的沉积层要求组分恒定,沉积工艺必须在稳定状态进行。
这种状态要求单位时间供给熔池内的蒸发物料的数量正好等于单位时间内被蒸发掉的;并且蒸发物料的组分必须精确的与沉积层的相同。
当熔池中易挥发的组分消耗到某种程度时,蒸气的成分到达沉积的要求,即达到稳定的工作状态。
建立稳定态所需的时间,亦即熔池达到所需成分的时间称为过渡时间,它主要取决于涂层组元的性质、熔池体积、蒸气发射面积及发射表面温度[22]。
3.4.4 基板加热温度许多制备工艺参数都会影响到EB-PVD涂层的结构与性能,但其中最主要的是基片加热温度T s的选择。