高炉强化冶炼汇总
高炉强化冶炼资料重点

是:燃烧产物煤气量增加;喷吹煤粉气
“高”指入炉矿石含 铁品位要高,焦炭、 烧结矿和球团矿强度 要高,烧结矿的碱度 要高。
王瑞祥
高炉炼铁知识9
6.2 精料
入炉矿含铁品位提高1%,炼铁燃料比降低 2%,产量提高3%,渣量减少30kg/t,允许 多喷煤15 kg/t。
原燃料转鼓强度要高。大高炉对原燃料 的质量要求是高于中小高炉。如宝钢要求 焦炭M40为大于88%,M10为小于6.5%,。
2020年10月28日星期三
王瑞祥
高炉炼铁知识2
6、高炉强化冶炼
在高炉冶炼的诸多矛盾中,炉料和煤气
的相向运动是主要的矛盾,炉料和煤气
的相向运动的存在和发展,影响着其他
矛盾的存在和发展,因此,处理好料和
煤气的矛盾,也就是要调整好料和风的
关系。实践证明,通过改善料柱透气性,
改善煤气流分布,从而降低料柱压差,
保证炉况顺行,是使此矛盾相统一的关
键。由此,普遍采用的高炉强化冶炼的
主要措施有:精料、高风温、富氧鼓风、
喷吹燃料、低硅生铁冶炼以及高寿命炉
衬等。 2020年10月28日星期三
王瑞祥
高炉炼铁知识3
6.1 提高冶炼强度
√
2020年10月28日星期三
王瑞祥
高炉炼铁知识4
6.1 提高冶炼强度
2020年10月28日星期三
王瑞祥
高炉炼铁知识26
6.5 喷吹燃料
2020年10月28日星期三
王瑞祥
高炉炼铁知识27
6.5 喷吹燃料
2020年10月28日星期三
王瑞祥
高炉炼铁知识28
6.5 喷吹燃料
2020年10月28日星期三
王瑞祥
高炉强化冶炼
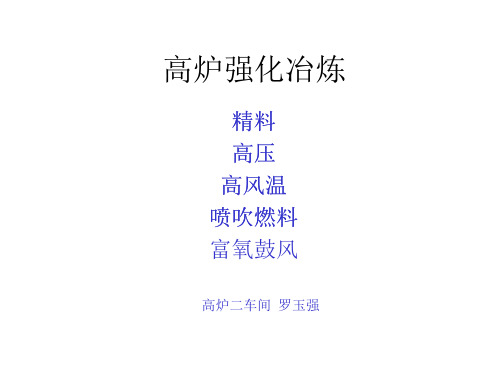
3.提高风温还可加快风口前焦炭的燃烧速度,提高T理,热 量更集中干炉缸,使高温区域下移,中温区域扩大,有利间 接还原发展,直接还原度rd降低。 4.风温的改变也是调剂炉况的重要手段之一。
高炉接受高风温的条件 凡是能降低炉缸燃烧温度和改善料柱透气性的措施,都 有利高炉接受高风温。 1.改善原燃料条件精料是高炉接受高风温的基本条件。只 有原料强度好,粒度组成均匀、粉未少,才能在高温条件下 保持顺行。 2.喷吹的燃料在风口前燃烧时分解、吸热,使理论燃烧温 度降低,高炉容易接受高风温。为了维持风口燃烧区域具有 足够的温度,需要提高风温进行补偿。 3.加湿鼓风时.因水分解吸热要降低理论燃烧温度,相应提 高风温进行热补偿。 4.搞好上下部调剂。保证高炉顺行的情况下才可提高风温。
• • • • • • • • •
(2)高还原性:低FeO、多气孔低温固结型烧结矿 FeO↓1%——K↓1.5%——产量↑1.5% (3)焦炭固定碳含量高:CS = 100 – A – V A↓——焦炭热值↑——渣量↓ (4)熔剂CaO含量高:CaO有效 = CaO – R×SiO2 (5)高强度:冷态强度——转鼓指数 热态强度——烧结矿低温还原粉化RDI 球团矿还原膨胀RSI 焦炭反应性↓ C + CO2 = CO
• (3) 煤气停留时间延长 • 提高炉顶压力,煤气在炉内停留时间延长,有利于还原反 应进行,也有利于焦比降低。 • (4) 有利稳定顺行 • 提高炉顶压力,由于压头损失降低,流速减慢,作用于炉 料的浮力也相应降低,炉料比较容易下降,因而有利于炉 况稳定顺行。 • (5) 除尘器瓦斯灰量减少 • 炉顶压力由常压转为0.08MPa时,炉尘量降了20%~50%, 现代高炉炉顶压力提高到 0.15 ~ 0.25MPa ,炉尘量常低于 10/kg/t。
高炉炼铁技术项目12任务12.1高炉强化冶炼的基本途径.ppt
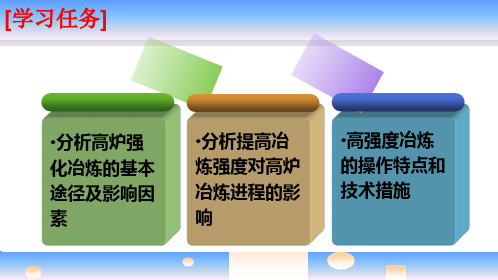
• 提要:高炉利用系数 I K
• √1、高炉强化冶炼两种途径: 1)提高冶炼强度, 2)降低焦比。
• √ 2、强化冶炼的基本方针:高产、优质、低耗、长寿、安 全与环保
各类因素之间关系的分析
1、 产量和消耗之间的关系 2、 产量与高炉寿命、效益之间的关系 3、产量与质量之间的关系
4
为了使高炉产量↑有4种途径: ηv = I / K
• (3)加大燃烧强度。燃烧强度是指每小时每平 方米炉缸截面积燃烧的焦炭量。
提高冶炼强度对高炉冶炼进程的影响
I适是随冶炼条件的改善不断增大的
1
焦
2 3
冶炼条件改善
比
4
5
适宜的 冶炼强度
冶炼强度和焦比之间的关系
焦比
Ima 产
产量
x
量
焦
比
I适
I
对一个实际高炉而言 存在与最低焦比相适宜的冶炼强度I适
高强度冶炼的操作特点和技术措施
3、产量与质量之间的关系
铁水质量的主要指标 • 铁水含硫 • 铁水温度
I过高时,炉料停留时间↓
脱硫反应能力↓ 加热不充分
[S] ↑ T铁↓
8
提高冶炼强度
• (1)增加入炉风量。增加高炉每分钟鼓入的风 量,高炉燃烧焦炭越多,即冶炼强度越高。
• (2)增加下料速度。下料速度加快,单位时间 内燃烧的焦炭增多。
14
[课堂小结]
1、高炉强化冶炼的基本途径和方针; 2、高炉强化冶炼的主要措施;
☆ I不变,K↓ ☆ K不变,I↑ ☆ 随I↑,K有所↓ ☆ 随I↑,K有所↑之间的关系
产量↑↑,意味着冶炼强度 I ↑↑ 高炉设备的寿命↓ → 修理费用↑ → 效益↓
故提高一代高炉寿命是很重要的
高炉强化冶炼的手段
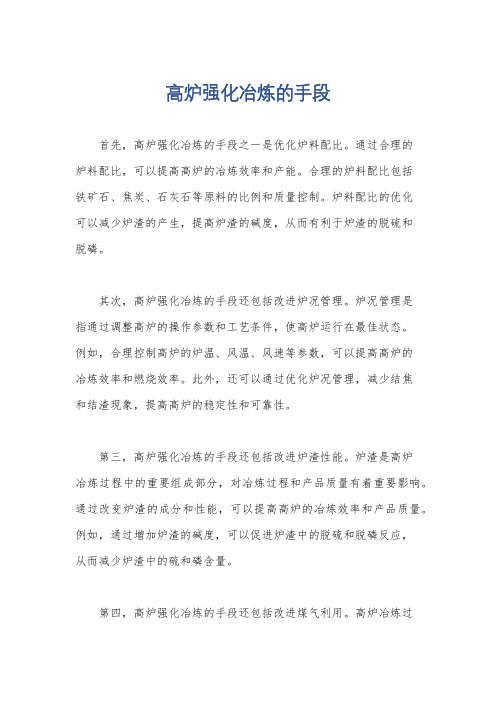
高炉强化冶炼的手段首先,高炉强化冶炼的手段之一是优化炉料配比。
通过合理的炉料配比,可以提高高炉的冶炼效率和产能。
合理的炉料配比包括铁矿石、焦炭、石灰石等原料的比例和质量控制。
炉料配比的优化可以减少炉渣的产生,提高炉渣的碱度,从而有利于炉渣的脱硫和脱磷。
其次,高炉强化冶炼的手段还包括改进炉况管理。
炉况管理是指通过调整高炉的操作参数和工艺条件,使高炉运行在最佳状态。
例如,合理控制高炉的炉温、风温、风速等参数,可以提高高炉的冶炼效率和燃烧效率。
此外,还可以通过优化炉况管理,减少结焦和结渣现象,提高高炉的稳定性和可靠性。
第三,高炉强化冶炼的手段还包括改进炉渣性能。
炉渣是高炉冶炼过程中的重要组成部分,对冶炼过程和产品质量有着重要影响。
通过改变炉渣的成分和性能,可以提高高炉的冶炼效率和产品质量。
例如,通过增加炉渣的碱度,可以促进炉渣中的脱硫和脱磷反应,从而减少炉渣中的硫和磷含量。
第四,高炉强化冶炼的手段还包括改进煤气利用。
高炉冶炼过程中产生的煤气含有可利用的热能和化学能。
通过改进煤气的利用方式,可以提高高炉的能源利用效率。
例如,可以采用煤气发电、煤气热解等技术,将煤气中的能源转化为电能或其他形式的能源,提高能源利用效率。
最后,高炉强化冶炼的手段还包括改进炉外工艺。
炉外工艺是指高炉冶炼过程中与高炉相配套的其他工艺环节。
通过改进炉外工艺,可以提高高炉的冶炼效率和产品质量。
例如,可以改进铁矿石的预处理工艺,提高铁矿石的还原性能;可以改进炼铁工艺,提高铁水的质量和纯度。
综上所述,高炉强化冶炼的手段包括优化炉料配比、改进炉况管理、改进炉渣性能、改进煤气利用和改进炉外工艺等多个方面。
这些手段可以提高高炉的冶炼效率和产品质量,实现高炉的强化冶炼。
高炉强化冶炼
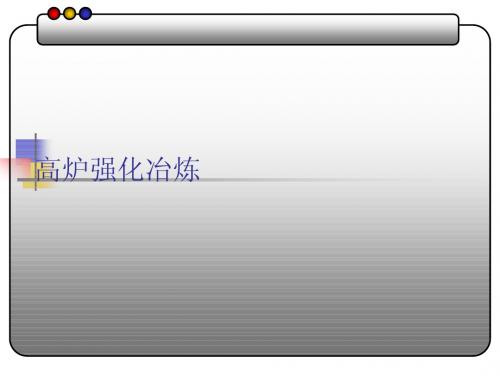
高炉强化冶炼
3、提高热风温度 、
提高热风温度是降低焦比和强化高炉冶炼的重要措施。 采用喷吹技术之后,使用高风温更为迫切。高风温能为提高 喷吹量和喷吹效率创造条件。据统计,风温在950~1350℃ 之间,每提高100 ℃可降低焦比8~20kg ,增加产量2~3%。 当前我国大高炉平均风温在1050~1100 ℃ ,先进高炉可 达1200 ℃,国外高炉风温水平达1300~1350 ℃,日本高炉 1200 1300 1350 的燃料比,1955~1979年间降低了 253kg/t,其中提高风温 的因素占31%。据资料,风温由1000℃提高到1250 ℃ ,焦 比降低22. 5kg/t,增产12.5%。 目前采用高风温已经不是高炉能否接受的问题,而是如何 能提供更高的风温。
“稳” 是指各种原料的化学成分稳定、波 高炉强化冶炼 动小。这是稳定炉况、实现自动控制的先 决条件。
“熟” 是指高炉全部装入烧结矿和球团矿, 熟料率达到100%,尽量不加石灰石入炉。 “小、匀、净” 是对原料的粒度而言。 综上所述,精料对矿石来说,关键是要使
高炉强化冶炼
2、高压操作
提高炉顶煤气压力的操作称为高压操作, 是相对于常压操作而言的。一般常压高 炉炉顶压力(表压)低于30kPa,凡炉顶压 力超过此值者,均为高压操作。它是通 过安装在高炉煤气除尘系统管道上的高 压调节阀组,改变煤气通道截面积,使 其比常压时为小,从而提高炉顶煤气压 力的。由于炉顶压力提高,高炉内部各
高炉强化冶炼
高压操作使炉尘吹出量显著减少, 单位矿石消耗降低,实际焦炭负荷得到 保证,批料出铁量增加,铁的回收率提 高,焦比应有所降低。实践证明,实行 高压操作,不断提高炉顶压力水平,是 强化高炉冶炼,增产节能的一条重要途 径。根据国内外经验,1000m3级高炉, 炉顶压力应达到120kPa左右;2000m3级 高炉,应达到150kPa以上; 3000m3级 高炉,应达到200kPa左右;4000m3级以
高炉强化冶炼

当冶炼强度过小,边缘气 流很强,中心气流很弱, 煤气热能和化学能得不到 充分利用,焦比升高,这 种情况往往出现在原料条 件很差的情况下。随着原 料条件改善,高炉料柱透 气性变好,随冶炼强度升
高,煤气在高炉内分布趋于均匀,煤气热能和化学能利用改 善,焦比降低。当冶炼强度过高时,冶炼周期明显减小,料 速过快,铁矿石间接还原不充分,直接还原度升高,焦比升 高。 随着原、燃料条件的改善,特别是铁矿石还原性提高, 基础焦比降低,在同样间接还原度下,铁矿石需要的还原时 间减少,冶炼周期可以缩短,焦比最低点的冶炼强度也可以 增加。
• 2)稳 • (1)烧结矿TFe波动↓,R波动↓ • TFe波动从1%↘0.5%—产量↑1.5~2.0%—焦比↓ • 1~1.5% • (2)焦炭水份、固定碳含量稳定 • 3)熟 • 提高熟料率:高炉使用人造富矿(烧结矿和球团矿) • (1)熟矿气孔率高,还原性好,低温还原粉化率低; • (2)熟矿化学成分稳定,且可以调整; • (3)熟矿硫含量低; • (4)熟矿可以减少高炉石灰石用量; • (5)高炉操作稳定,炉缸热量充沛。
5)矮胖高炉与超高冶强 vu
I
首钢4# 首钢3# 首钢1#
1726 1200 2536 2536 2000 2516 4063 4063
Hu/D
2.495 2.635 1.985 1.985 2.678 2.521 2.2 2.2
IΣ
1.427 1.465 1.426 1.430 0.975 1.025 1.032 1.139
6.2 高冶炼强度
1)高炉利用系数
I 高炉每天烧掉的焦炭量 u K Vu K 每天送入高炉的风量( 1440 Q0) 高炉每天烧掉的焦炭量 每吨焦炭需要的风量q C 22.4 q C 1000 C S /(0.21 0.29 f ) 2500 ~ 3000 m 3 / t 24
5-高炉炼铁工艺6高炉强化冶炼技术
大批重 小批重
一般情况下 大矿批压中心;小矿批压边缘。
25
③ 装料顺序
定义:炉料中矿石和焦炭装入高炉内的先后次 序称为装料顺序。
一般而言,先入炉的料首先在炉墙边沿较多堆 积到一定程度后才滚向中心。
26
装料顺序对布料的影响图示
正装—先装矿石, 后装焦炭;
倒装—先装焦炭, 后装矿石;
同装—矿石和焦炭 一起装入炉内;
16
高炉炉顶装料设备
钟式炉顶
无钟炉顶
17
影响炉顶装料状况的因素
固定因素 布料设备参数 1、布料器形式 2、炉喉高度和直径 3、大钟与炉喉间隙 4、大钟倾角及速度 5、无钟炉顶参数 炉料特性
堆比重、堆角、粒度、外形
可变因素 布料器工作参数 料线高度 料批大小 装料顺序
18
可变因素 炉料装入炉内方式的总称
8
适宜冶炼强度和焦比的关系
高炉适宜的I适和Kmin取决于冶炼条件,随着高炉冶炼条件 的改善,I适不断升高,而Kmin不断下降,使ηv不断增大。
9
(2)效益与产量、消耗之间的关系
P>P0,单位成本在 P>P0附近,升高幅度 很小;单位生铁利润(C一 S)减少的幅度小于产量 (P)增加的幅度;A=P (C一S)仍可达到最大。
(4)调节的原则是早动、少动,以保持炉况的 长期稳定顺行。因此,对炉况的发展趋势和变 化幅度要有预见性,避免根据出渣出铁的状态 再进行调节,这种滞后调节会造成炉况周期性 的波动。
39
(3)造渣制度
★控制炉渣各种理化性能的总称
包括
熔化温度、熔化性温度、粘度、 炉渣成分、熔化滴落区间、 脱硫性、排碱性、表面性能等
正常生产时高炉两尺相差应小于 500mm。
高炉炼铁工艺及强化操作
高炉炼铁工艺及强化操作高炉炼铁是指利用高炉将铁矿石还原成铁的工艺。
下面将介绍高炉炼铁的工艺流程和强化操作。
首先是炉料准备。
炉料是指进入高炉的原料,主要包括铁矿石、燃料和熔剂。
铁矿石是炼铁的主要原料,有各种类型,如富含铁的赤铁矿、磁铁矿等。
燃料主要是焦炭,用于提供炉内的热量。
熔剂主要是石灰石,用于与铁矿石中的杂质产生反应,形成易于熔融的铁渣。
然后是炉顶喂料。
炉顶喂料是将炉料逐层从高炉顶部加入,以保持炉内的物料平衡。
铁矿石、焦炭和石灰石按照一定比例加入到高炉顶部,同时还需要加入一定量的还原剂、燃料和助熔剂。
炉料从高炉顶部逐层往下加入,以确保炉内的物料层结构稳定。
然后是高炉操作。
高炉操作是指控制高炉正常运行的一系列操作。
首先是通风。
高炉顶部设有风管,通过风管送入燃料燃烧所需的氧气,维持炉内的高温。
其次是给料。
在正常运行过程中,需要不断地给炉料补料,保持高炉内的物料平衡。
还有是温度和压力的控制。
高炉内的温度和压力需要进行实时监测,以保持高炉内部的平衡状态。
接下来是铁渣处理。
高炉炼铁过程中,铁矿石中的杂质会与熔剂反应形成铁渣。
铁渣是高炉炼铁的副产物,需要进行处理。
铁渣处理主要包括根据铁渣的性质进行分选和利用。
铁渣中的铁石可以回收利用,用于生产水泥等建筑材料。
而其他杂质则需要通过石灰石的熔融和化学反应,形成不溶于炉渣的物质,进一步净化炉渣。
最后是产品收得。
通过高炉炼铁,最终产生的产品是生铁。
生铁是铁矿石还原后的产物,含有较高的碳含量和一些杂质。
生铁需要进行进一步的加工和处理,使其达到市场上的要求。
加工过程中,可以采用转炉炼钢或电炉炼钢技术,将生铁中的杂质进一步去除,得到优质的钢铁产品。
为了提高高炉炼铁的效率和质量,还有一些强化操作可以应用。
比如,在炉料准备过程中,可以根据铁矿石的性质进行选矿和破碎处理,以提高炉内的还原反应速率。
另外,可以在炉顶喂料过程中,适当控制喂料速度和炉料的层次,以保持高炉内的平衡状态。
高炉强化冶炼1
高风温与降低焦比的关系
高风温降低焦比的原因 (1)风温带入的物理热,减少了作为发热 剂所消耗的焦炭,因而可使焦比降低。 (2)风温提高后焦比降低,使单位生铁生 成的煤气量减少,炉顶煤气温度降低,煤气 带走的热量减少,因而可使焦比进一步降低。 (3)提高风温后,因焦比降低煤气量减少, 高温区下移,中温区扩大、增加间接还原, 减少直接还原,有利于焦比降低。
我国高炉炼铁在近几年来取得了很大的进步, 冶炼强度在中小型高炉上超过了1.5 t/(m3d),大高炉上也达到了 1.1t/(m3d)以上,利用系数相应达到 3.5 t/(m3d)以上和2.3 t/(m3d)以 上,燃料比降到530 kg/t和500 kg/t左 右。这是由于采取了所谓强化高炉冶炼技术 的结果。这些技术包括精料技术、高风温技 术、高压操作技术、喷吹燃料技术、富氧大 喷煤技术、先进的计算机控制技术等。
鼓风含氧按下式计算: 鼓风含氧=大气中含氧+富氧率 式中,鼓风含氧的单位为%;大气中含氧一 般取21%;富氧率按下式计算: 富氧率=富氧量/(风量+富氧量) 式中,富氧率的单位为%;富氧量的单位为 m3/min;风量的单位为m3/min,或以 吨铁所用的风量和吨铁耗的氧气量为单位计 算。
高风温与降பைடு நூலகம்焦比的关系
高风温降低焦比的原因 (4)由于风温提高焦比降低,产量相应提 高,单位生铁热损失减少。 (5)风温升高,炉缸温度升高,炉缸热量 收入增多,可以加大喷吹燃料数量,更有利 于降低焦比。
高风温与降低焦比的关系
高风温降低焦比的效果 风温水平不同,提高风温的节焦效果也不相 同。风温愈低,降低焦比的效果愈明显,相 反,风温水平愈高,增加相同的风温所节约 的焦炭减少。 对于焦比高、风温偏低的高炉,提高风温后 其效果更大。风温水平已经较高 (1200℃~1300 ℃)时,再提高风温的作 用减小。
高炉强化冶炼的手段 -回复
高炉强化冶炼的手段-回复高炉强化冶炼的手段是通过改进和优化高炉冶炼过程,提高炉内矿石的还原和熔化能力,提高产量和质量的一系列措施。
本文将详细介绍高炉强化冶炼的手段,并逐步回答相关问题。
一、高炉强化冶炼的背景和意义高炉是冶炼的核心设备之一,具有熔化矿石、还原金属氧化物、脱硫以及合金添加等多种功能。
强化冶炼手段旨在提高高炉的冶炼效率和产量,降低能耗和环境污染。
这对于钢铁工业的可持续发展和资源节约具有重要意义。
二、高炉强化冶炼的主要手段1. 提高炉料品位高炉强化冶炼的第一步是提高炉料品位。
通过选用高品位的矿石和燃料,减少杂质含量,可以提高高炉的冶炼效率和产量。
2. 优化炉料配比炉料配比是指矿石、焦炭和烧结矿在高炉中的加入比例。
通过合理的炉料配比,可以控制炉内反应的平衡,提高冶炼效果。
优化炉料配比需要根据炉料的化学成分、物理性质和炉渣特性进行科学的设计。
3. 改进炉渣配方炉渣是高炉冶炼过程中的重要组成部分,具有液相和固相两个组成部分。
通过改进炉渣配方,可以提高炉渣的脱硫和吸附能力,减少冶炼过程中的杂质含量。
4. 加强高炉控制高炉控制是高炉强化冶炼的重要环节。
通过采用先进的控制系统和自动化设备,可以实现对高炉冶炼过程的实时监测和精确控制,提高冶炼效率和产品质量。
5. 引入先进技术高炉强化冶炼的另一个重要手段是引入先进的技术和设备。
例如,通过喷吹装置引入高温燃烧气体,可以提高高炉的冶炼温度和热效率;通过炉内预处理,可以改变炉料的物相结构,提高冶炼效果。
三、高炉强化冶炼手段的优势和挑战1. 优势高炉强化冶炼手段可以提高冶炼效率和产量,降低能耗和环境污染。
这可以帮助钢铁企业提高竞争力,降低生产成本,实现可持续发展。
2. 挑战高炉强化冶炼手段的实施面临着技术和经济上的挑战。
从技术上讲,高炉是一个复杂的系统,受多种因素的影响,优化和改进手段需要综合考虑。
从经济上讲,高炉改造需要投入大量资金,并且可能需要长时间才能回收投资。
- 1、下载文档前请自行甄别文档内容的完整性,平台不提供额外的编辑、内容补充、找答案等附加服务。
- 2、"仅部分预览"的文档,不可在线预览部分如存在完整性等问题,可反馈申请退款(可完整预览的文档不适用该条件!)。
- 3、如文档侵犯您的权益,请联系客服反馈,我们会尽快为您处理(人工客服工作时间:9:00-18:30)。
高炉强化冶炼技术及其进步高炉炼铁生产的原则高炉冶炼生产的目标是在较长的一代炉龄(例如5年或更长)内生产出尽可能多的生铁,而且消耗要低,生铁质量要好,经济效益要高,概括起来就是“优质,低耗,高产,长寿,高效益” 以来,我国乃至。
长期世界各国的炼铁工作者对如何处理这五者间的关系进行过,而且还在进行着讨论,讨论的焦点是如何提高产量及焦比与产量的关系。
众所周知,表明高炉冶炼产量与消耗的三个重要指标一有效容积利用系数O Y)、冶炼强度(I)和焦比(K)之间有着如下的关系: “Y = I/K显然,利用系数的提高,也即高炉产量的增加,存在着四种途径: ⑴冶炼强度保持不变,不断地降低焦比;⑵焦比保持不变,冶炼强度逐步提高;⑶随着冶炼强度的逐步提高,焦比有所降低;⑷随着冶炼强度的提高,焦比也有所上升,但焦比上升的幅度不如冶炼强度增长的幅度大。
在高炉炼铁的发展史上,这四种途径都被应用过,应当指出在最后一种情况下,产量增长很少,而且是在牺牲昂贵的焦炭的消耗中取得的,一旦在冶炼强度提高的过程中,焦比升高的速率超过冶炼强度提高的速率,贝y产量不但得不到增加,反而会降低。
因此,冶炼强度对焦比的影响,成为高炉冶炼增产的关键。
在高炉冶炼的技术发展过程中,人们通过研究总结出冶炼强度与焦比的关系如图1所示。
0.90.80.3 0-5 05 0.9 1J 13Z/(MTi^ d')a (-pg •忙kO0.94 18000.92 17000.901500 Wo5 t097/(t m d*')1600a 美国资料,b 一原西德资料, c一前苏联资料图1冶炼强度与产量(I)和焦比(K)的关系a 美国资料,b 一原西德资料, c一前苏联资料在一定的冶炼条件下,存在着一个与最低焦比相对应的最适宜的冶炼强度I 适。
当冶炼强度低于或高于I 适时,焦比将升高,而产量稍迟后,开始逐渐降低。
这种规律反映了高炉内煤气和炉料两流股间的复杂传热、传质现象。
在冶炼强度很低时,风量及相应产生的煤气量均小,流速低,动压头很小,造成煤气沿炉子截面分布极不均匀,表现为边缘气流过分发展,煤气与矿石不能很好地接触,CO,结果煤气的热能和化学能不能得到充分利用,炉顶煤气中含量低,温度高,而进入高温区的炉料因还原不充分,直接还原发展,消耗了大量宝贵的高温热量,因此焦比很高。
随着冶炼强度的提高,风量、煤气量相应增加,煤气的速度也增大,从而改变了煤气流的流动状态,由层流转为湍流,风口前循环区的出现,大大改善了煤气流分布和煤气与炉料之间的接触,煤气流的热能和化学能利用改善,间接还原的发展减少了下部高温区热量的消耗,从而焦比明显下降,直到与最适宜冶炼强度儿相对应的最低焦比值。
之后冶炼强度继续提高,煤气量的增加进一步提高了煤气流速,这将带来叠加性的煤气流分布,导致中心过吹或管道行程,在煤气流速过大时,它的压头损失可变得与炉料的有效质量相等或超过有效质量,炉料就停止下降而出现悬料。
所有这些将引起还原过程恶化,炉顶煤气温度升高,炉况恶化,最终表现为焦比升高。
高炉炼铁工作者应该掌握这种客观规律,并应用它来指导生产,即针对具体生产条件,确定与最低焦比相适应的冶炼强度,使高炉顺行,稳定地高产。
然而高炉的冶炼条件是可以改变的,随着技术的进步,例如加强原料准备,采取合理的炉料结构,提高炉顶煤气压力,使用综合鼓风,改造设备等,高炉操作条件大大改善。
与改善了的条件相应的冶炼强度可以进一步提高,而焦比不会提高,相反与之相对应的最低焦比也进一步下降,这就是世界各国几年来冶炼强度不断提高,焦比也降低的原因,见图2。
但是,在任何生产技术水平上,当冶炼条件一定时,冶炼强度I与焦比K之间始终保持着极值关系,决不可以得出产量是与冶炼强度成正比地增长的简单结论,而盲目追求高冶炼强度。
超越冶炼条件允许的过高冶炼强度将使焦比大幅度上升。
上述有关咼炉冶炼重要技术指标、I、K之间的关系还未解决经济效益最佳的冶炼强度问题。
在对钢铁的需求大于供给的条件F,实践表明,尽管焦比的消耗对生铁成本有着很大影响,但在定的操作情况下,产品的最低成本并不是在最低焦比相对应的冶炼强度下,而是在略高的情况下取得的。
所以出现这种情况,是因为最高产量是在比最低焦比相对应的冶炼强度稍高的情况下达到的(图1)。
随着产量的提高,单位生铁成本中不随时间变化的费用总和不断降低。
在K=f(l)曲线的最低值附近,随着冶炼强度的提高,焦比上升得较缓慢,在这个区域内多消耗焦炭的费用能被节省下的加工费用全部补偿,而且还有多余。
实践还证明,经济上最合算的产量,并不是生铁成本最低时的产量,而是略高于这个最低产量。
(I)与焦比(K)的关系,I〜5示意冶炼条件不断改善图3日产量(P)对产品成本(S)和生产盈利性的影响(C 一出厂价格)K图2不同冶炼条件下的冶炼强度炼铁厂(或车间)经济上最合算的产量是在所具有的设备上,于单位时间内达到最高利润总和时的产量,如图3所示,在生铁成本为产量的函数S=f (P)曲线上,生铁最低成本是在P0产量下获得,而且在最低处附近,生铁成本升高较慢,使得生铁出厂价与成本的差值(C-S)减小的幅度比产量增加的幅度小,所以在某种P> P0的情况下经济效益户(C-S)的乘积达到最大,这就是我国众多厂家追求的产量指标。
最后,应当指出的是在我国随着产量和效益的提咼,咼炉设备,特别是高炉本体的寿命越来越短,大修和中修费用不断增加,有可能影响到增产的效益。
这个问题的严重性已引起人们重视,开始研究提咼咼炉寿命的有效措施,例如米用咼质量碳砖,碳化硅砖,改进高炉冷却(炉底水冷,炉身软水密闭循环冷却)以及钒钛炉渣护炉等。
高炉长寿技术的开发和实现将促使高炉生产实现高产、低耗、优质,高效益。
目前世界各国已把高炉长寿看作炼铁技术的个重要组成部分和发展的标志。
高炉强化冶炼工艺操作技术我国高炉炼铁在近几年来取得了很大的进步,冶炼强度在中小・d)以上,型高炉上超过了1.5 tJ(m3d),大高炉上也达到了 1.1t/(m3利用系数相应达到 3.5 t/(m3 <d)以上和2.3 t/(m \d)以上,燃料比降到530 kg/t和500 kg/t左右。
这是由于采取了所谓强化高炉冶炼技术的结果。
这些技术包括精料技术、高风温技术、高压操作技术、喷吹燃料技术、富氧大喷煤技术、先进的计算机控制技术等。
精料是高炉强化冶炼的基础高炉强化冶炼以后,一方面单位时间内产生的煤气量增加,煤气在炉内的流速增大,煤气穿过料柱上升的阻力也P上升;另一方面炉料下降速度加快,炉料在炉内停留时间缩短,也就是冶炼周期缩短,这样煤气与矿石接触的时间缩短,不利于间接还原的进行。
为保持强化冶炼后炉况顺行、煤气利用好、产量高、燃料比低,原燃料质量成为决定性的因素。
首先是矿石的人炉晶位和焦炭灰分及含硫量,它们决定着渣量。
人们普遍认为,渣量不低于300 kg/t,要实现喷吹燃料200 kg/t以上,燃料比500 kg/t是困难的,甚至是不可能的;另外渣量也是煤气顺利穿过滴落带的决定性因素。
其次,原料的粒度组成、高温强度和造渣特性是影响料柱透气性和高炉顺行的决定性因素。
均匀的粒度组成和较好的高温强度是保证块状带料柱透气性的基本条件,而良好的造渣性能是降低软熔带和滴落带煤气运动阻力的基本条件。
第三,原料的还原性是影响高炉内铁的直接还原度的决定性因素,只有原料具有良好的还原性(如烧结矿、球团矿或粒度小而均匀的天然赤铁矿和褐铁矿矿石),才能保证炉料在进入高温区以前充分还原,从而降低焦比。
第四,焦炭的强度特别是高温强度是软熔带焦窗和滴落带焦床透气性和透液性的决定性因素,所以降低焦炭的灰分、反应性是分重要的。
由此可见,要想高炉强化冶炼并获得良好的高炉生产指标,必须抓好原燃料,改善原燃料质量,使原料具有品位高、粒度均匀、 强度好、还原和造渣特性优良等条件,使焦炭具有灰分低、硫低、 强度高、反应性低等优良条件。
我国精料技术取进步和发展方织生产者的重视,精料技术取得了相当大的进步,具体表现为:(1) 入炉品位显著提高。
由于认识到入炉品位的高低是决定渣量和冶炼过程热量消耗的决定性因素之一,在原来入炉品位较低 为 50%左右 ) 时,提高矿石晶位 1%,可降低燃料比 2%,提高产量3%。
因此各厂都把提高人炉晶位作为提高冶炼强度和降低燃料消的人炉品位已在 60 %以上,绝大部分企业的人炉品位在58.5%以 。
入炉晶位提高的措施是:利用两种资源,适量使用进口富矿, 淘汰国产劣质矿;改进选矿技术,使精矿粉的品位由原来的~63%提高到 66% ~68%等。
(2) 做好入炉料成分稳定工作。
生产实践使人们认识到,原料成分 的不稳定是引起高炉炉况波动的重要原因。
为防止炉况失常,生产 中常被迫维持较高的炉温,这就无形中增加了燃料消耗,这就是很多高炉尤其是中小型高炉炼钢生铁中的 [Si ]降不下来的原因。
例如炼钢要求生铁中[Si ]在0.4%即可,但生产者考虑烧结矿中 度m cao /m siO2的波动,[Si ]迫维持在0.6%,甚至0.8%,而[Si ]每增 加 0.1%焦比要上升 4 kg/t 。
为使原料成分稳定,就要加强中和混匀近年来, 料的重要性已深入炼铁工作者的心中,受到各级组 精料仃Fe 约 耗最积极、最有效的措施。
我国宝钢、三明、杭钢等10 余家企业60%T Fe 和碱工作,很多厂包括地方骨干中型企业建成了中和混匀料场,取得了 很好的效果。
(3) 优化入炉料的粒度组成,这是改善料柱透气性和强化冶炼过程 的重要影响因素。
现在广泛地强化了筛分工作,不仅在烧结厂、球 团厂进行, 还普遍地在高炉槽下进行, 筛去粒度小于 5 mm 的粉末, 与此同时,还限制烧结矿粒度的上限为 40~50 mm 。
(4)采用低温烧结法生产高碱度低 F eO 高还原性的烧结矿,并向低 SiO 2 发展,这是提高烧结矿冶金性能的重要措施。
我国宝钢烧结矿 中的SiO 2含量降到4.5 %左右,达到世界先进水平,现在已逐步推 广。
(5)发展球团矿生产,为合理炉料结构提供优质酸性料。
我国铁矿资 源主要是贫矿,通过磁选得到磁精粉,本应用它来生产球团矿,但走的却是生产烧结矿的道路,球团矿生产一直没有得到重视。
随着料,开始得到发展。
近年来,一些厂都新建了球团车间以满足高炉炉料结构的要求。
虽然这些球团生产设备绝大部分是竖炉 球团矿的质量还不是太好,很难满足大型高炉对球团矿质量的要求,但为炉料结构的优化还是做出了贡献。
现在首钢迁安矿山公司正在建设200万t/年的新球团设备。
(6)焦炭质量不断提高。
我国已有两家焦化厂生产出灰分为 右的优质焦炭,达到国际上要求的一级焦炭。
有 10 余家生产的焦 炭的灰分已降到12 %以下,达到11.2 %〜11.5 %。