民用飞机先进制造技术的发展趋势
法国飞机发展现状及未来趋势分析
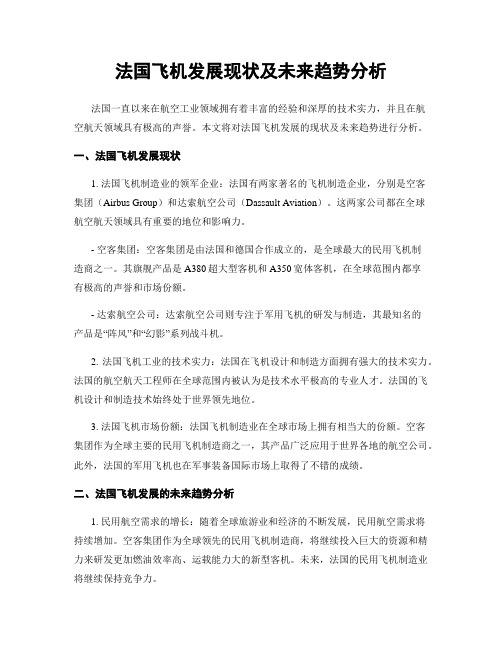
法国飞机发展现状及未来趋势分析法国一直以来在航空工业领域拥有着丰富的经验和深厚的技术实力,并且在航空航天领域具有极高的声誉。
本文将对法国飞机发展的现状及未来趋势进行分析。
一、法国飞机发展现状1. 法国飞机制造业的领军企业:法国有两家著名的飞机制造企业,分别是空客集团(Airbus Group)和达索航空公司(Dassault Aviation)。
这两家公司都在全球航空航天领域具有重要的地位和影响力。
- 空客集团:空客集团是由法国和德国合作成立的,是全球最大的民用飞机制造商之一。
其旗舰产品是A380超大型客机和A350宽体客机,在全球范围内都享有极高的声誉和市场份额。
- 达索航空公司:达索航空公司则专注于军用飞机的研发与制造,其最知名的产品是“阵风”和“幻影”系列战斗机。
2. 法国飞机工业的技术实力:法国在飞机设计和制造方面拥有强大的技术实力。
法国的航空航天工程师在全球范围内被认为是技术水平极高的专业人才。
法国的飞机设计和制造技术始终处于世界领先地位。
3. 法国飞机市场份额:法国飞机制造业在全球市场上拥有相当大的份额。
空客集团作为全球主要的民用飞机制造商之一,其产品广泛应用于世界各地的航空公司。
此外,法国的军用飞机也在军事装备国际市场上取得了不错的成绩。
二、法国飞机发展的未来趋势分析1. 民用航空需求的增长:随着全球旅游业和经济的不断发展,民用航空需求将持续增加。
空客集团作为全球领先的民用飞机制造商,将继续投入巨大的资源和精力来研发更加燃油效率高、运载能力大的新型客机。
未来,法国的民用飞机制造业将继续保持竞争力。
2. 绿色航空技术的推动:在全球环境保护日益重视的背景下,绿色航空技术将成为未来发展的重点。
法国航空工业在研发绿色航空技术方面具有优势,将会加大对可再生燃料、低碳排放等技术的研究和应用,以减少飞机对环境的影响。
3. 军事飞机技术的提升:在军事装备领域,法国一直是世界重要的参与者之一。
未来,随着军事技术的不断进步和军事需求的变化,法国将继续投入更多资源来提升军用飞机的性能,并发展更加智能化和多用途的战斗机、侦察机和无人机等。
航空航天技术的发展现状与未来趋势展望
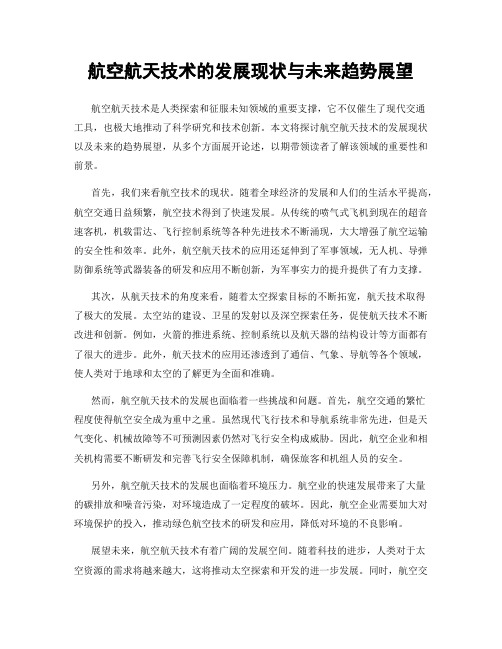
航空航天技术的发展现状与未来趋势展望航空航天技术是人类探索和征服未知领域的重要支撑,它不仅催生了现代交通工具,也极大地推动了科学研究和技术创新。
本文将探讨航空航天技术的发展现状以及未来的趋势展望,从多个方面展开论述,以期带领读者了解该领域的重要性和前景。
首先,我们来看航空技术的现状。
随着全球经济的发展和人们的生活水平提高,航空交通日益频繁,航空技术得到了快速发展。
从传统的喷气式飞机到现在的超音速客机,机载雷达、飞行控制系统等各种先进技术不断涌现,大大增强了航空运输的安全性和效率。
此外,航空航天技术的应用还延伸到了军事领域,无人机、导弹防御系统等武器装备的研发和应用不断创新,为军事实力的提升提供了有力支撑。
其次,从航天技术的角度来看,随着太空探索目标的不断拓宽,航天技术取得了极大的发展。
太空站的建设、卫星的发射以及深空探索任务,促使航天技术不断改进和创新。
例如,火箭的推进系统、控制系统以及航天器的结构设计等方面都有了很大的进步。
此外,航天技术的应用还渗透到了通信、气象、导航等各个领域,使人类对于地球和太空的了解更为全面和准确。
然而,航空航天技术的发展也面临着一些挑战和问题。
首先,航空交通的繁忙程度使得航空安全成为重中之重。
虽然现代飞行技术和导航系统非常先进,但是天气变化、机械故障等不可预测因素仍然对飞行安全构成威胁。
因此,航空企业和相关机构需要不断研发和完善飞行安全保障机制,确保旅客和机组人员的安全。
另外,航空航天技术的发展也面临着环境压力。
航空业的快速发展带来了大量的碳排放和噪音污染,对环境造成了一定程度的破坏。
因此,航空企业需要加大对环境保护的投入,推动绿色航空技术的研发和应用,降低对环境的不良影响。
展望未来,航空航天技术有着广阔的发展空间。
随着科技的进步,人类对于太空资源的需求将越来越大,这将推动太空探索和开发的进一步发展。
同时,航空交通工具的研发也将继续创新,未来可能会出现更高效、更环保的飞行器。
航空技术现状及未来发展趋势
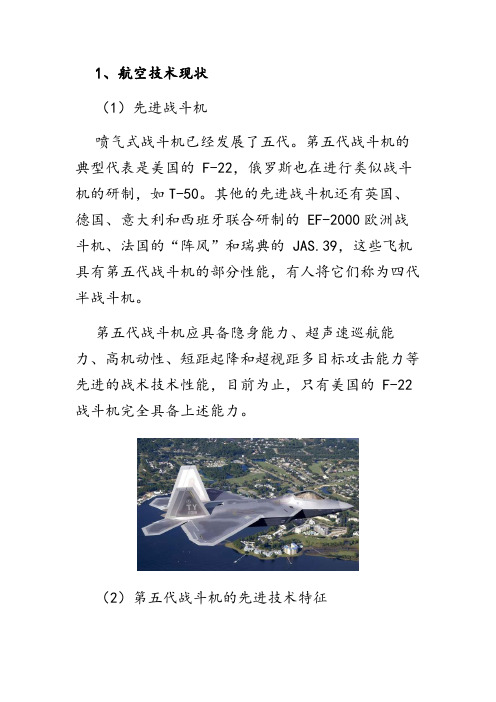
1、航空技术现状(1)先进战斗机喷气式战斗机已经发展了五代。
第五代战斗机的典型代表是美国的 F-22,俄罗斯也在进行类似战斗机的研制,如T-50。
其他的先进战斗机还有英国、德国、意大利和西班牙联合研制的 EF-2000欧洲战斗机、法国的“阵风”和瑞典的 JAS.39,这些飞机具有第五代战斗机的部分性能,有人将它们称为四代半战斗机。
第五代战斗机应具备隐身能力、超声速巡航能力、高机动性、短距起降和超视距多目标攻击能力等先进的战术技术性能,目前为止,只有美国的 F-22战斗机完全具备上述能力。
(2)第五代战斗机的先进技术特征隐身技术,又称低可探测技术或目标特征探测技术,主要有五个方面:第一,降低雷达波特征;第二,降低红外辐射特征;第三,降低可见光特征;第四,降低声学特征;第五,降低电子探测特征.具有超声速巡航能力:前提是飞机在正常起飞条件下具有超过 1.1的起飞推力重量比,即要求飞机安装推力大,重量轻的先进发动机.第五代战斗机具有比第四代战斗机更高的机动性。
短距起降是指飞机能以比较短的地面滑跑距离便可起飞或降落,通常认为飞机起飞或着陆滑跑距离在500m以内算作具有短距起降能力.先进战斗机的全环境作战能力除要求全天候和全空域 (全部适合空战的空域 )作战外,还要求飞机具有多目标跟踪/攻击和超视距作战能力(3)隐身飞机飞机的隐身能力是指飞机在飞行中具有不易被敌方探测器发现的能力,即飞机具有不易被雷达、红外、可见光和声波等探测到的能力;目前雷达探测手段对飞机的威胁约占各种探测手段的 60%左右,红外探测威胁约占 30%左右,所以飞机主要是雷达隐身和红外隐身。
雷达隐身的措施主要包括外形隐身和应用吸波材料,以减小雷达波回波散射,即降低RCS。
红外隐身的主要措施有:采用矩形二元喷管,使尾喷流火舌变平;飞机在飞行时尽量不要开加力燃烧室;把发动机布置在机身或机翼上面,利用机翼或尾翼等部件进行遮挡或隐蔽。
国外把隐身飞机的发展分为五代:第一代是洛克希德·马丁“臭鼬”工程队的 SR-7l战略侦察机;第二代为“海弗兰”原型机,即 F-117的原型机;第三代是洛克希德·马丁公司的 F-117战斗轰炸机;第四代是诺斯罗普·格鲁曼公司的 B-2战略轰炸机;而洛克希德·马丁/波音联合研制的 F-22战斗机为第五代隐身飞机。
年中 国航空航天产业发展现状及前景分析报告

年中国航空航天产业发展现状及前景分析报告航空航天产业作为现代科技的前沿领域,一直以来都备受关注。
在过去的几年里,中国航空航天产业取得了举世瞩目的成就,不仅在技术创新方面不断突破,还在产业规模和国际影响力上逐步提升。
一、发展现状1、技术创新成果显著中国在航空航天领域的技术创新不断涌现。
在航空方面,自主研发的大飞机 C919 成功首飞并逐步投入商业运营,标志着我国在民用航空领域迈出了重要的一步。
此外,新型战斗机、直升机等航空器的研发也取得了重要进展。
在航天领域,嫦娥五号成功实现月球采样返回,天问一号火星探测器成功着陆火星,北斗卫星导航系统全面建成并投入使用,这些都彰显了我国在航天技术方面的强大实力。
2、产业规模持续扩大随着技术的不断进步和市场需求的增加,中国航空航天产业的规模持续扩大。
航空产业方面,国内航空公司的机队规模不断增长,民用航空市场需求旺盛。
同时,航空制造业的产业链不断完善,涵盖了飞机设计、制造、维修等多个环节。
航天产业方面,卫星发射数量逐年增加,商业航天市场逐渐兴起,为产业发展注入了新的活力。
3、人才队伍不断壮大为了支持航空航天产业的发展,我国加大了人才培养和引进的力度。
众多高校和科研机构开设了相关专业,培养了大量的专业人才。
同时,通过引进海外高端人才和加强国际合作,进一步提升了人才队伍的素质和水平。
4、政策支持力度加大国家出台了一系列支持航空航天产业发展的政策,包括财政补贴、税收优惠、科研项目支持等。
这些政策为产业的发展提供了有力的保障,促进了企业的创新和发展。
二、面临的挑战1、核心技术仍存在差距尽管我国在航空航天领域取得了很多成果,但在一些核心技术方面,如航空发动机、高端材料等,与国际先进水平仍存在一定差距。
这些差距限制了我国航空航天产业的进一步发展,需要加大研发投入和技术创新力度来缩小差距。
2、产业配套体系有待完善航空航天产业的发展需要完善的配套体系支持,包括零部件供应商、检测认证机构等。
航空航天技术的发展现状和未来趋势展望

航空航天技术的发展现状和未来趋势展望航空航天技术是近代科技领域中最引人注目的领域之一,它对现代社会的发展和进步起到了重要的推动作用。
从最早的飞行机制到如今的宇宙探索,航空航天技术在各个方面都取得了显著的进展。
首先,让我们来看一下航空领域的发展现状。
随着技术的不断进步,飞机的性能和安全性得到了极大的提升。
如今的大型客机拥有更高的载客量和航程,同时也具备更高的燃油效率和更低的废气排放。
此外,无人机技术的快速发展也为航空领域带来了巨大的机会。
无人机在农业、环境监测和物流方面的应用越来越广泛,为人们的生活带来了便利。
然而,航空领域的发展并不仅仅局限于飞机和无人机。
航天技术的进步也为人类的探索和认识宇宙提供了巨大的机遇。
近年来,中国已经实现了多项太空探索的重要里程碑,包括成功发射载人飞船和月球探测器。
这些成就不仅向世界展示了中国航空航天技术的实力,也为未来的航天探索奠定了坚实的基础。
未来,航空航天技术有着广阔的发展前景。
在航空领域,随着燃料和能源成本的上升,航空公司正在探索更环保和节能的解决方案。
一种被广泛关注的技术是电动飞机。
虽然目前电动飞机的飞行时间和载重能力还受到限制,但随着电池技术和电动机技术的不断进步,电动飞机将成为未来航空领域的重要发展方向。
在航天领域,人类对宇宙的探索充满了无限的遐想。
火星、月球和外太空都成为人们研究和探索的热点。
未来,我们有望见证人类首次登陆火星的时刻,同时也将继续探索太阳系中更多的行星和卫星。
此外,航天技术还有望为人类解决诸如太空垃圾清理和地球环境监测等问题提供解决方案。
当然,随着航空航天技术的发展,也存在一些挑战和问题。
例如,航空领域的碳排放问题已经引起了全球范围内的关注。
解决这一问题需要航空公司和科研机构共同努力,推动绿色航空技术的发展。
在航天领域,太空探索的成本和安全性也是令人担忧的问题。
未来,我们需要寻求更加可持续和经济高效的解决方案,以确保航天探索的顺利进行。
综上所述,航空航天技术的发展正在以巨大的步伐向前推进。
飞行器制造行业发展现状与未来趋势
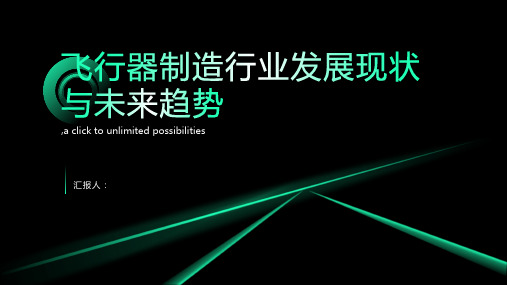
PART SIX
政策扶持:国家出台了一系列政策,鼓励飞行器制造行业的发展,包括财政补贴、税收优惠 等。
科技创新:国家鼓励企业加大科技创新投入,提高飞行器制造的核心技术水平。
市场拓展:国家支持企业拓展国内外市场,推动飞行器制造行业国际化发展。
人才培养:国家重视飞行器制造行业的人才培养,推动产学研用深度融合。
添加标题
在飞行器制造领域的应用:采用 绿色制造技术,如轻质材料、可 再生能源、高效制造工艺等,可 有效降低飞行器的能耗和排放, 提高其环保性能。
添加标题
前景展望:随着环保意识的提高 和技术的不断进步,绿色制造技 术在飞行器制造领域的应用将越 来越广泛,未来将有更多的创新 技术和产品出现。
添加标题
行业影响:绿色制造技术的应用 将推动飞行器制造行业的技术进 步和产业升级,促进其可持续发 展,对整个行业产生积极的影响。
,a click to unlimited possibilities
汇报人:
CONTENTS
PART ONE
PART TWO
定义:飞行器制造行业是指从事各类飞行器的设计、制造、试验、维修等业务的产业 分类:按照飞行器类型可分为固定翼飞机、旋翼机、无人机等;按照用途可分为军用、民用、商用等
起步阶段:20世纪初,飞行器制造行业开始起步,主要集中在欧美国家。 快速发展阶段:二战后,随着军事需求的增加,飞行器制造行业快速发展。 商业化阶段:20世纪80年代,随着航空工业的商业化,飞行器制造行业逐渐走向市场化。 高科技化阶段:近年来,随着科技的不断进步,飞行器制造行业不断涌现出新的技术和产品。
PART FIVE
绿色环保:随着环保意识的提高,未 来飞行器制造将更加注重环保和可持 续发展,采用更环保的材料和能源, 降低碳排放。
飞机数字化装配技术的发展与应用
飞机数字化装配技术的发展与应用随着科技的不断进步和飞机制造业的快速发展,飞机数字化装配技术在航空制造领域中扮演着越来越重要的角色。
数字化装配技术通过将传统的手工装配过程转变为数字化、智能化的方式,使得飞机制造过程更加高效、精准和安全。
本文将探讨飞机数字化装配技术的发展现状以及其在飞机制造领域的应用情况。
一、飞机数字化装配技术的发展历程飞机数字化装配技术的发展经历了多个阶段,从最初的CAD/CAM技术到如今的虚拟现实技术,每一个阶段的发展都极大地促进了飞机制造工艺的进步和效率提升。
1. CAD/CAM技术计算机辅助设计(CAD)和计算机辅助制造(CAM)技术是飞机数字化装配技术发展的最初阶段。
通过CAD软件,设计师可以将飞机的整体结构、零部件和装配工艺进行数字化设计,实现了设计部门和制造部门之间的无缝衔接。
而CAM技术则可以根据CAD设计的参数,实现数控机床的智能化加工,提高零部件的加工精度和效率。
2. 数字化装配技术数字化装配技术是在CAD/CAM技术的基础上发展而来的,它将CAD设计的数字模型和装配工艺与实际装配过程进行了深度融合。
通过数字化装配技术,制造工程师可以在计算机上模拟飞机的装配过程,发现和解决装配中可能存在的问题,提前预防装配差错,确保零部件的精准度和装配质量。
3. 虚拟现实技术随着虚拟现实技术的发展,飞机数字化装配技术又迈入了新的阶段。
利用虚拟现实技术,制造工程师可以在虚拟环境中进行飞机装配的实时模拟,不仅可以更真实地还原实际装配场景,还可以进行全方位的体验和调试。
这种虚拟装配技术大大提高了装配工程师的工作效率,减少了实际试装过程中的错误和浪费。
二、飞机数字化装配技术的应用领域飞机数字化装配技术的应用领域非常广泛,涵盖了飞机设计、制造、测试和维护等多个环节。
1. 飞机设计在飞机设计阶段,数字化装配技术可以帮助设计师实时模拟飞机的装配过程,发现和解决设计中可能存在的问题。
通过数字化装配技术,设计师可以更加直观地了解不同零部件之间的装配关系,优化零部件的结构和安装方式,提高整体飞机的装配效率和性能。
飞机制造的技术和工艺
飞机制造的技术和工艺随着科技的不断进步,飞机的制造技术和工艺也在不断变化和提升。
从最早的飞机制造到现代高科技飞机制造,专业人员在技术方面做出了令人瞩目的进步和贡献。
一、制造流程飞机制造是一项极其复杂的工作。
其制造流程包括设计、制造、装配和测试这几个环节。
其中,设计过程是非常重要的环节,设计师必须能够将飞机的设计理念、材料和性能相结合,才能保证飞机的飞行安全和性能达成预期效果。
制造飞机的主要材料包括金属材料、复合材料等。
与传统的金属材料相比,复合材料具有高强度、高刚度、轻重量等特点,能够有效地减轻飞机的重量。
随着复合材料的广泛应用,使得飞机的性能得到大大提高。
装配是飞机制造过程中的关键环节。
由于飞机部件的要求比较高,装配前必须要进行多次精细的加工和检验。
其中,金属件通常采用机加工和冷成形等方式加工,而复合材料则采用顶尖技术加工和成型,以保证飞机的性能。
测试环节也是飞机制造中最重要的环节之一。
测试过程中,必须进行全面的性能检测,包括飞机静态测试、飞行测试、负载测试等。
测试结果将直接影响到飞机的飞行性能和安全性。
二、新技术随着科技的不断进步,飞机制造的新技术也在不断涌现。
例如,3D打印技术、机器学习技术、大数据处理技术等,这些新技术的应用将大大提高飞机制造的效率和质量。
3D打印技术可以将数字模型直接转化为实体零件,使得飞机零部件的制造更加精确和快速。
机器学习技术可以通过对飞机数据进行分析,提高飞机的使用寿命和性能。
大数据处理技术可以直接对飞机数据进行监控和分析,提高飞机的运行效率和安全性。
三、展望未来的飞机制造将更加注重智能化、无人化和可持续性,这也是飞机制造技术和工艺发展的方向和目标。
未来的飞机将具备更高的自动化和智能化水平,具有更强的飞行能力和安全性。
同时,未来飞机制造将更加注重生态环保和可持续性。
随着社会对环境保护意识的日益加强,飞机制造将更加注重环保和节能,减少对环境造成的负面影响。
总之,飞机制造的技术和工艺是一个不断进步的过程,随着技术的发展和进步,未来的飞机将变得更加智能、高效和环保。
航空航天科技的发展趋势和未来方向
航空航天科技的发展趋势和未来方向近年来,随着科技的飞速发展,航空航天科技也日新月异。
无论是民用航空还是军事领域,各方都在探索新的发展方向,以满足不断增长的需求。
接下来,我将重点探讨航空航天科技的发展趋势和未来的方向。
首先,航空航天科技的未来将更加注重环保可持续发展。
近年来,随着气候变化的日益加剧,环保已成为世界范围内的共识。
航空业也在积极响应环保政策,推进绿色技术的研究与应用。
例如,欧洲航天局正在开发利用水分解产生氢燃料的发动机模型,这种燃料不仅能降低排放,更能减少对有限石油的依赖。
另外,无人机技术的应用也被视为未来的热点。
随着无人机技术不断完善,越来越多的领域开始采用无人机,例如配送、安防、搜救等。
在航空领域,无人机可以用于航空摄影、航空检测等。
未来,我们还可以期待无人机实现自主飞行,进一步提升其应用价值。
除此之外,未来航空航天科技还将加强与人工智能的深度融合。
人工智能的应用可以优化飞行控制和数据处理,提高飞行的安全性和效率。
大数据技术也可以作为分析和推断飞行数据的重要手段,帮助飞行员做出正确决策。
当然,未来还有更加遥远的目标,如太空旅游、探索其他星球等。
此类科技依然处于初期阶段,需要不断的研究和探索。
在航空航天科技的发展中,我认为需要注意以下几个方面。
首先,应该注重技术的可靠性和安全性。
虽然科技的创新能够带来新的发展机遇,但也必须确保技术的稳定性和可控性。
其次,科技研发应该注重现实应用与市场需求之间的平衡。
只有在满足市场需求的基础上,才能真正实现科技的价值和应用。
最后,科技发展需要全球合作,分享资源与经验,在这个全球化时代,航空航天科技的发展也需要跨越国界,携手前行。
总之,航空航天科技是一个充满潜力的领域,未来的发展前景十分广阔。
我们期待着更多的科技成果能够改变我们生活,满足我们的需求,创造出更加美好的未来。
航空航天技术的发展现状及未来趋势分析
航空航天技术的发展现状及未来趋势分析航空航天技术一直以来都是人们对科技进步的体现,它在不断推动人类文明的进步之中起着举足轻重的作用。
本文将对航空航天技术的发展现状及未来趋势进行分析。
一、航空航天技术的发展现状航空航天技术的发展经历了漫长而曲折的历程。
20世纪初,著名的莱特兄弟成功发明了第一架飞机,开创了人类航空领域的新时代。
此后,航空技术不断创新,飞机的速度、高度、载重能力都有了巨大的提高,民航运输事业也取得了长足的发展。
同时,在航天领域,人类还实现了从地球进入太空的壮举,载人航天器成为了航空航天技术的重要里程碑。
目前,航空航天技术在世界各地取得了重大突破。
航空方面,随着燃油效率的不断提高,飞机的燃油消耗大幅降低,环境友好的新型喷气式客机逐渐投入运营,这为航空业的可持续发展提供了保障。
航天方面,国际空间站的建设和运行为人类深入研究太空提供了有效平台。
此外,商业航天也逐渐兴起,私人公司参与航天事业,推动了航天技术的进一步发展。
二、航空航天技术的未来趋势分析1. 绿色航空环保意识的提高推动了航空航天技术向绿色化的方向发展。
未来,人们对飞行器燃油效率的要求将不断提高,同时也会对飞机排放的二氧化碳和噪音水平提出更高要求。
航空航天技术将致力于开发更节能、更环保的航空器,以减少对环境的影响。
2. 自动化与智能化航空航天技术的自动化发展势必是未来的趋势之一。
自动驾驶技术在航空领域也将得到广泛应用,这不仅能提高飞行安全性,还能减轻飞行员的工作负担。
同时,人工智能的快速发展将为航空航天技术带来更大的创新空间,例如机器人在航天领域的应用,将大大提高任务的效率和安全性。
3. 太空旅游与探索未来,太空旅游将从梦想变为现实。
随着航天技术的不断进步,普通人将有机会亲身体验太空之旅,探索太空的奥秘。
同时,人类对宇宙的探索也将日益深入,例如对其他星球的探测以及可能的移民。
这将成为航空航天技术未来最为激动人心的发展方向之一。
4. 航空航天与其他领域的融合航空航天技术的发展将与其他领域的融合不断加深。
- 1、下载文档前请自行甄别文档内容的完整性,平台不提供额外的编辑、内容补充、找答案等附加服务。
- 2、"仅部分预览"的文档,不可在线预览部分如存在完整性等问题,可反馈申请退款(可完整预览的文档不适用该条件!)。
- 3、如文档侵犯您的权益,请联系客服反馈,我们会尽快为您处理(人工客服工作时间:9:00-18:30)。
科技信息工程技术
1.引言近年来,飞机制造技术朝着整体结构轻量化、隐身、高可靠性,长寿命、短周期、低成本及绿色先进制造技术方向发展[1]。以B777、B737–800、A320和A380为代表的机型集中反映了大型客机制造技术的现状,而正在研制发展的A350、波音787更多地采用了先进制造工艺和材料技术以提高飞机的市场竞争力。数字化、自动化、柔性化、精确化制造技术,以及先进材料技术在这些机型中的应用和实践,将整个飞机制造技术水平提高到了一个新的境界。2.国外民机先进制造技术及发展趋势民机研制在欧、美、俄等发达国家已有近半个世纪的历史,制造技术已经从经验依赖型转向过程模拟、仿真、实时监控、智能化方向发展。尤其是近二十年的发展迅猛,其发展趋势以提高生产率,更快、更好且低成本为目标。2.1数字化装配技术飞机数字化装配技术涉及飞机设计、零部件制造、装配工艺规划、互换协调技术、数字化测量系统、自动控制和计算机软件等众多先进技术。飞机的装配过程是一项复杂的系统工程,涉及飞机设计、工艺计划、零件生产、部件装配和全机对接总装的全部过程。据统计,飞机装配成本在产品总成本中的比重可达40%,装配工作量一般约占全机工作量的一半。近年来,国外飞机装配技术发展迅速,以A380、B787为代表的大型飞机装配中,采用数字量尺寸协调体系和装配设计技术,通过装配虚拟仿真技术实现装配过程优化,应用柔性装配型架和自动化装配技术实现飞机结构的高质量、高效率和长寿命的装配。大型飞机自动化装配技术已从由单台数控自动钻铆机和数控托架组成的自动钻铆系统向由柔性装配工装、模块化加工单元、数控定位系统(包括机器人)、自动送料系统和数字化检测系统等组成的自动化装配系统发展,大部分基于CATIA平台设计,保证了装配系统与飞机产品的数字化协调。目前国外发展的自动化装配系统主要有柔性机翼壁板装配系统、柔性翼梁装配系统、机身壁板集成单元、机身环铆装配系统和机器人自动化装配系统等。图1为柔性轨道制孔系统。图1柔性轨道制孔系统2.2复合材料结构制造技术先进复合材料具有高比强、高比模、多功能、各向异性和可设计性、材料与结构的同一性等优异性能。自20世纪60年代问世以来,先进复合材料被广泛应用于民用飞机的各类结构,且应用比例还在不断提高,如图2所示。可以说当今先进的复合材料结构占飞机结构总量比重的多少,在某种程度上成为评价该飞机性能的重要技术指标,也标志着该飞机设计制造厂家(国家)工业技术的先进程度和实力[2]。2.2.1复合材料整体结构成型技术由于零件数量、紧固件数量和协调/连接装配工作量的减少,同时由于相应钉孔数量下降导致结构承载能力的改善,复合材料结构的减重效果可随整体化程度的提高而显著上升,同时结构成本可大幅度下降。采用整体成型技术还可以减少分段、对接、间隙和台阶,使机体表面光滑完整,整体成型技术使高度翼身融合的结构总体布局实现成为可能。共固化、共胶接和二次胶接是整体结构成型首先要研究发展的最基本、最常用的技术。
图2新一代大型民机复合材料应用情况2.2.2复合材料结构低成本制造技术复合材料结构的应用在带来性能极大提高的同时,也伴随着制造成本上升的高昂代价。为此,降低制造成本已成为促进先进复合材料结构应用发展的决定因素。低成本成型技术主要的发展趋势是液体成型技术、数字化与自动化生产技术以及制造工艺模拟与优化技术。20世纪80年代以后,随着低粘度热固性树脂材料和树脂转移技术的完善,形成了以树脂转移模塑(RTM)工艺为代表的液体成型制造技术体系。RTM工艺方法适合制造梁、肋、框等小型构件。由于RTM技术还存在缺点,因此,近年来又开发了真空辅助树脂注塑成型技术(VARI)。辅助树脂被织物吸收,不仅可降低孔隙率,使预成形纤维更紧密,而且由真空形成的负压,可使树脂沿着真空通路沿预成形体各层面流动,从而充分浸渍纤维,并使纤维/树脂分布均匀。该技术适用于中小尺寸、形状复杂的产品,如A380前后机身部分组件及襟副翼部分肋与铰链,波音787起落架支架[3]。90年代,出现了树脂膜熔融浸渍(RFI)成型方法,该工艺免去了RTM工艺所需的树脂计量注射设备及双面模具的加工,在制造出优异的制品的同时大大降低了成本。图3是采用RFI工艺制造的机身后压力框。
图3RFI成型的机身后压力框2.2.3复合材料结构三维增强技术目前航空复合材料结构上大量使用二维增强的层压复合材料。由于基体树脂的脆性和材料厚度方向性能的薄弱状态,此类结构存在抗冲击性能低弱和损伤容限问题,不能满足新型飞机的高性能要求。解决此类问题应从两方面入手,一是开发应用高韧性基体树脂来改善复合材料结构的抗冲击性能,二是通过三维编织、缝合技术或纵向加强技术(Z-pining)在Z向引入增强纤维来实现。三维编织法采用纺织技术将增强纤维制成三维预成型体,然后通过树脂转移方法成型构件,克服了二维编织厚度方向强度低的问题。缝合技术是在制造过程中,将未浸渍树脂的平面织物铺叠后采用特殊的缝合设备按工艺参数进行缝合,然后通过树脂转移方法成型复合材料结构,A380后机身压力隔框采用的就是该技术[3]。
民用飞机先进制造技术的发展趋势上海飞机设计研究院石霞琳[摘要]本文论述了国外民用飞机制造业在数字化装配技术、复合材料结构制造技术、大型整体结构件制造技术、精密钣金成形技术及焊接技术方面的发展趋势,并对我国民机制造业的发展提出了合理化建议。[关键词]民用飞机制造发展趋势
——348科技信息工程技术
2.2.4制造工艺模拟与优化技术对复合材料构件的制造工艺进行准确的模拟、评估和优化是获得合理工艺、高质量产品和降低制造成本的一个关键因素。传统的生产方式在进行这项工作时采用以大量材料、设备和工时耗费为代价的工艺试验作为评估依据,这不能满足复合材料低成本、高效率的制造要求。国内外在这方面开展了大量卓有成效的研究工作,研发出具有工程实用价值的计算机软件用于工艺的模拟、评估和优化,如用于模拟、评估液体成型工艺的RTM-Worx和PAM-RTM,用于设计和生产可行性评估的FiberSIM,洛克希德—马丁公司开发的能对复合材料热压罐固化工艺进行优化的COBRA,由美国辛辛那提机器公司开发的用于纤维铺放的Acraplace等。2.2.5复合材料纤维缠绕/铺放成型技术缠绕/铺放成型技术是在缠绕成型技术与铺叠成型技术的基础上发展起来的。缠绕成型技术限于回转体结构的制造,不适合航空工业通常的板壳构型。纤维铺叠则限于类似飞机机翼蒙皮一类单曲面结构。缠绕成型是复合材料构件最主要的成型工艺方法之一,缠绕成型技术的主要实施范围是具有筒、罐、管、球、锥及盒状几何外形的复合材料构件,并可根据结构需要实现环向的局部增厚、增强。而铺叠成型技术可在闭曲面的结构中实现纵向或子母线方向的增厚、增强。因此,为实现复杂型面结构的制造,就要将缠绕成型技术与铺叠成型技术相结合。当今在航空工业比较发达的国家随着近年来多轴联动缠绕设备、自动铺带设备、纤维丝束铺放设备等设备的不断进步,缠绕/铺放成型技术在以空客A380和波音787为代表的新型飞机上获得了大量应用。2.3大型整体结构件制造技术整体化结构具有诸多优点,如减少紧固件数量、降低重量及加工成本等。大型整体结构件的数控加工和成形技术在国外先进民机上有大量成功应用的案例,如大型机翼整体壁板、大型复合材料构件、大型整体框与结构等。图4为某机型机翼用3万转高速铣切设备加工成型的超薄巨型翼肋。图4机翼超薄巨型翼肋2.4精密钣金成形技术精密钣金成形技术的核心是简化设计、提高质量、缩短周期、降低成本。充分利用材料的最佳成形性能,发掘新的成形工艺与方法,预测成形缺陷、检测和控制成形过程是成形技术的发展趋势[4]。整体壁板的成形技术是制造机体结构的关键技术之一。波音707~777和空客A310~340等大中型民用客机都采用数控喷丸成形方法成形机翼整体壁板。近年来,随着新型可时效强化铝合金在机翼壁板结构中的应用以及焊接整体壁板的出现,整体壁板时效成形技术得到了空客、波音等公司的重视和发展,从而出现了喷丸成形与时效成形技术并存的局面,如空客A330、A340的上蒙皮壁板和A321下翼面蒙皮。2.5焊接技术目前,A380、B777、Eclipse-500及ERJ145等飞机制造中,都相继采用焊接技术作为飞机结构的连接方法。焊接技术也由小零件的制造发展到了大型部件和整体机身的组装焊接。先进焊接技术不仅使焊接质量较弧焊工艺有了飞跃性发展,而且生产效率较弧焊提高了5~20倍[5]。电子束焊接技术(EBW),激光束焊接技术(LBW)和搅拌摩擦焊技术(FSW),就是最具代表性的三种先进焊接技术。电子束焊接技术主要应用于钛合金材料,如波音的起落架和空客A380的发动机机架等。激光束焊接适合制造单曲度和双曲度壁板,空客正在将激光焊接技术用于支架接头、起落架舱区域压力隔框的制造上。A380飞机采用激光束焊接技术取代下机身壁板桁条的铆接工艺,使机身壁板结构从过去的“装配式结构”概念改变成“整体式结构”概念。搅拌摩擦焊接是一种完全不同于上述两种焊接技术的固相连接方法,目前,在世界范围内公认搅拌摩擦焊是最具潜力和最有应用前景的新型连接方法。这种方法可能成为今后中、薄板(包括有色金属和黑色金属)的重要连接方法,主要应用于机身纵向焊缝的连接及飞机大部件之间的连接。进入二十一世纪以来,欧洲航空工业正在掀起搅拌摩擦焊的技术研究和推广应用高潮,开展了多项针对飞机结构搅拌摩擦焊技术研究的欧盟框架计划项目,深入系统地研究了搅拌摩擦焊技术及其在飞机结构应用上的安全性和可靠性。Eclipse-500型商务飞机的机身和机翼等大量采用了该项技术,号称全搅拌摩擦焊飞机,如图5所示。空客公司也已经致力于将搅拌摩擦焊技术引入到A340飞机的制造中,并大规模应用于A350的制造,将机身面板从8块减少到4块,不仅可以减轻重量,而且提高了飞机的使用寿命[5]。
图5全搅拌摩擦焊飞机Eclipse-5003.对我国民机制造技术发展的几点建议
我国现有的民机制造体系以MD82/90的制造技术和管理技术为基础,同时在转包生产中吸收了一些波音、空客的先进技术。部分航空企业应用了计算机局域网络、信息集成技术、异地无纸设计制造及并行工程等先进技术,在航空零组件制造方面已有长足的发展。但是,我国的飞机装配技术、复合材料结构制造技术、关键成形技术、焊接技术等技术与国外发达国家相比还存在很大差距,在以下方面亟待重点突破:(1)基于精益制造理念,发展大型飞机数字化装配线及其模式、壁板件柔性装配系统、大型壁板自动钻铆系统、大部件对接系统、大型飞机部件精准对接系统、大型飞机部件的转运与装配、飞机装配工装快速设计、电磁铆接等新型连接工艺;(2)发展复合材料结构设计制造一体化、数字化设计和模拟、大型复合材料构件整体成型技术、复合材料构件的无损检测和修补技术等,进一步探索低成本制造技术;(3)发展大型机翼整体壁板成形技术、大型整体框锻造与轻合金结构件铸造技术、大型壁板多级化铣技术,大型双曲蒙皮数控加工成形技术等;(4)系统研究时效成形等新的钣金成形技术,发展数字化钣金制造技术,建立钣金柔性生产单元,钣金成形工艺过程模拟专家系统等;(5)提高焊接设备硬件水平,研究电子束、激光束焊接和搅拌摩擦焊接的基础工艺,建立完善的无损检测体系。4.结束语