甲基乙烯基硅橡胶混炼胶压缩永久变形性能的改善 2
硅橡胶

硅橡胶(SiliconeRubber)是一种兼具无机和有机性质的高分子弹性材料,其分子主链由硅原子和氧原子交替组成(—Si—O—Si—),侧链是与硅原子相连接的碳氢或取代碳氢有机基团,这种基团可以是甲基、不饱和乙烯基(摩尔分数一般不超过01005)或其它有机基团,这种低不饱和度的分子结构使硅橡胶具有优良的耐热老化性和耐候老化性,耐紫外线和臭氧侵蚀。
分子链的柔韧性大,分子链之间的相互作用力弱,这些结构特征使硫化胶柔软而富有弹性,但物理性能较差。
硅橡胶发展于20世纪40年代,国外最早研究的品种是二甲基硅橡胶。
1944年前后由美国DowCorning公司和GeneralElectric公司各自投入生产。
我国在60年代初期研究成功并投入工业化生产。
现在生产硅橡胶的国家除我国外,还有美国、英国、日本、前苏联和德国等,品种牌号有1000多种。
1 硅橡胶的分类和特性1.1 分类硅橡胶按其硫化机理不同可分为热硫化型、室温硫化型和加成反应型三大类。
1.2 特性(1)耐高、低温性在所有橡胶中,硅橡胶的工作温度范围最广阔(-100~350℃)。
例如,经过适当配合的乙烯基硅橡胶或低苯基硅橡胶,经250℃数千小时或300℃数百小时热空气老化后仍能保持弹性;低苯基硅橡胶硫化胶经350℃数十小时热空气老化后仍能保持弹性,它的玻璃化温度为-140℃,其硫化胶在-70~100℃的温度下仍具有弹性。
硅橡胶用于火箭喷管内壁防热涂层时,能耐瞬时数千度的高温。
硅橡胶在高温下连续使用寿命见表1。
(2)耐臭氧老化、耐氧老化、耐光老化和耐候老化性能硅橡胶硫化胶在自由状态下置于室外曝晒数年后,性能无显著变化。
硅橡胶与其它橡胶的耐臭氧老化性能比较见表2。
(3)电绝缘性能硅橡胶硫化胶的电绝缘性能在受潮、频率变化或温度升高时变化较小,燃烧后生成的二氧化硅仍为绝缘体。
此外,硅橡胶分子结构中碳原子少,而且不用炭黑作填料,因此在电弧放电时不易发生焦烧,在高压场合使用十分可靠。
各种橡胶基本特性精
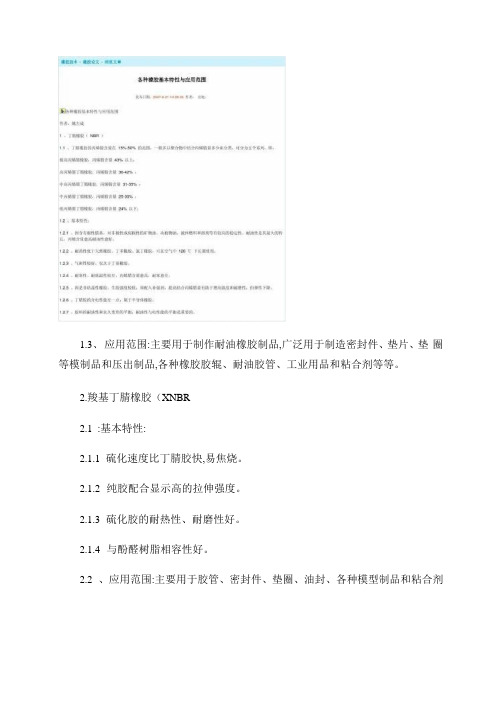
1.3、应用范围:主要用于制作耐油橡胶制品,广泛用于制造密封件、垫片、垫圈等模制品和压出制品,各种橡胶胶辊、耐油胶管、工业用品和粘合剂等等。
2.羧基丁腈橡胶(XNBR2.1:基本特性:2.1.1硫化速度比丁腈胶快,易焦烧。
2.1.2纯胶配合显示高的拉伸强度。
2.1.3硫化胶的耐热性、耐磨性好。
2.1.4与酚醛树脂相容性好。
2.2、应用范围:主要用于胶管、密封件、垫圈、油封、各种模型制品和粘合剂3、丁腈橡胶-聚氯乙烯共混胶(NBR/PVC3.1、基本特性:3.1.1耐臭氧和耐天候老化性能比通常丁腈橡胶显著提高。
3.1.2比通常丁腈橡胶提高了耐燃性。
3.1.3耐磨耗、耐油性、耐化学药品等性能比通常丁腈橡胶有所改善。
3.1.4提高了压出、压延工艺性能。
3.1.5可任意着色制作艳色制品。
3.1.6低温特性、弹性降低,压缩变形增大。
3.1.7比通常的聚氯乙烯改善了低温特性、耐油性、伸长率等。
3.2应用范围:主要用于电线电缆护套,油管和燃油管外层胶,皮辊和皮圈,汽车模压零件,微孔海绵,发泡绝热层,安全靴和防护涂层等。
4、氢化丁腈橡胶(HNBR4.1、基本特性4.1.1氢化丁腈橡胶虽经氢化饱和,但仍然保持原丁腈的特性。
具有拉伸结晶性, 因而强度较高。
4.1.2有良好的耐热和耐臭氧、耐天候老化性能以及耐化学酸碱性能。
4.1.3良好的耐技术液体(包括含腐蚀添加物的油类的溶胀性能。
4.1.4良好的机械性能,即使在温升条件下仍保持相当水平。
4.1.5在极有害的条件下,有显著的耐磨耗性能。
4.1.6硫化胶的拉伸强度比丁腈橡胶,氯丁橡胶更高,接近高于羧基丁腈橡胶。
4.1.7优异的耐酸(硫化氢环境和耐胺/油混合物性能,以及耐氧化燃料和润滑油性能。
4.1.8玻璃化温度Tg随氢化程度在-15- -40 ℃之间,脆性温度-50 ℃。
4.2、应用范围:由于具有独特的性能,因此广用于油田工业、汽车工业、飞机制造工业和建筑工业等领域的制品,如制造钻井管、钻井管保护层、蓄压器、汽车燃料和润滑系统、发动机使用垫圈,O型圈、密封件等。
硅橡胶指标

110甲基乙烯基硅橡胶甲基乙烯基硅橡胶是以优质硅氧烷并引入乙烯基合成的高分子量聚硅氧烷化合物,添加补强剂(二氧化硅)和硫化剂后,在高温下可交联成弹性体。
该系列胶以分子端基不同可分为甲基封端和乙烯基封端两大类。
型号中带"S"的为乙烯基封端的甲基乙烯基聚硅氧烷。
110系列硅橡胶可用于制造模压胶、挤出胶、电绝缘胶、阻燃胶等各类混炼胶。
除下表中所列标准系列外,亦可生产高分子量(70~80万)、高乙烯基含量(≥1%)和低挥发份 < 1%)产品,满足市场需要。
分子量 乙烯基含量 挥发分(104)(%) (%)乙烯基封端胶 110-8 50~700.04~0.06 ≤2.5甲基封端胶 110-150~700.07~0.12乙烯基封端胶 110-1S 甲基封端胶 110-245~700.13~0.20乙烯基封端胶 110-2S 甲基封端胶 110-345~700.21~0.24乙烯基封端胶 110-3S 甲基封端胶 110-450~700.25~0.35 乙烯基封端胶 110-4S 乙烯基封端胶 110-5S 50~60 0.60~0.70 乙烯基封端胶 110-6S 50~600.90~1.10注:指标不在上表所列范围的特殊要求的产品,以合同形式约定。
一般模压胶该产品具有良好的物理机械性能,适合生产普通硅橡胶制品和杂件,普通硅橡胶按键,尤其适用于加颜色制品,模压工艺生产。
一般模压胶性能表NE-5130 NE-5140 NE-5150 NE-5160 NE-5170 NE-5180外观乳白色,淡黄,淡灰色密度 g/cm3 1.09±0.05 1.13±0.05 1.15±0.05 1.18±0.05 1.21±0.05 1.25±0.05硬度邵氏A度30±3 40±3 50±3 60±3 70±3 80±3拉伸强度 MPa≥ 5.0 6.0 7.0 7.0 6.5 6.0扯断伸长率 %≥440 380 320 280 200 150扯断永久变形 %≤8 9 10 10 9 8撕裂强度 kN/m≥15 16 18 18 16 15试片一次硫化条件:175℃×5min硫化剂:活性含量80%的“双-2,5”,加入量0.65%食品型模压胶该产品硫化后透明度好,物理机械性能高,抗黄变性能强。
硅胶的特性解读
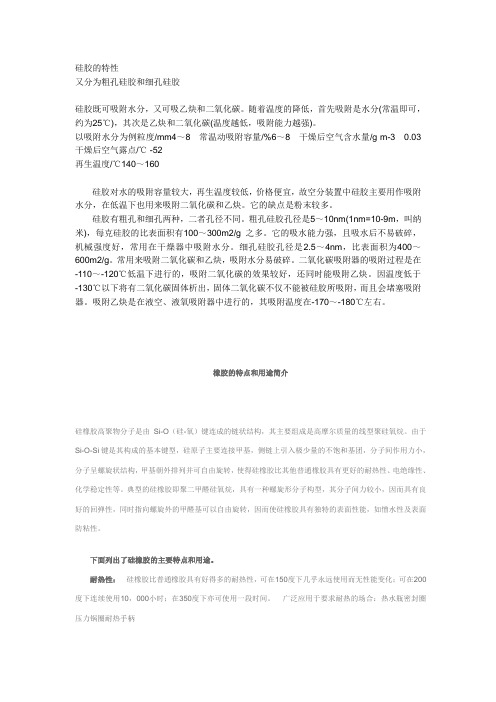
硅胶的特性又分为粗孔硅胶和细孔硅胶硅胶既可吸附水分,又可吸乙炔和二氧化碳。
随着温度的降低,首先吸附是水分(常温即可,约为25℃),其次是乙炔和二氧化碳(温度越低,吸附能力越强)。
以吸附水分为例粒度/mm4~8 常温动吸附容量/%6~8 干燥后空气含水量/g·m-3 0.03 干燥后空气露点/℃ -52再生温度/℃140~160硅胶对水的吸附容量较大,再生温度较低,价格便宜,故空分装置中硅胶主要用作吸附水分,在低温下也用来吸附二氧化碳和乙炔。
它的缺点是粉末较多。
硅胶有粗孔和细孔两种,二者孔径不同。
粗孔硅胶孔径是5~10nm(1nm=10-9m,叫纳米),每克硅胶的比表面积有100~300m2/g之多。
它的吸水能力强,且吸水后不易破碎,机械强度好,常用在干燥器中吸附水分。
细孔硅胶孔径是2.5~4nm,比表面积为400~600m2/g。
常用来吸附二氧化碳和乙炔,吸附水分易破碎。
二氧化碳吸附器的吸附过程是在-110~-120℃低温下进行的,吸附二氧化碳的效果较好,还同时能吸附乙炔。
因温度低于-130℃以下将有二氧化碳固体析出,固体二氧化碳不仅不能被硅胶所吸附,而且会堵塞吸附器。
吸附乙炔是在液空、液氧吸附器中进行的,其吸附温度在-170~-180℃左右。
橡胶的特点和用途简介硅橡胶高聚物分子是由Si-O(硅-氧)键连成的链状结构,其主要组成是高摩尔质量的线型聚硅氧烷。
由于Si-O-Si键是其构成的基本键型,硅原子主要连接甲基,侧链上引入极少量的不饱和基团,分子间作用力小,分子呈螺旋状结构,甲基朝外排列并可自由旋转,使得硅橡胶比其他普通橡胶具有更好的耐热性、电绝缘性、化学稳定性等。
典型的硅橡胶即聚二甲醛硅氧烷,具有一种螺旋形分子构型,其分子间力较小,因而具有良好的回弹性,同时指向螺旋外的甲醛基可以自由旋转,因而使硅橡胶具有独特的表面性能,如憎水性及表面防粘性。
下面列出了硅橡胶的主要特点和用途。
耐热性:硅橡胶比普通橡胶具有好得多的耐热性,可在150度下几乎永远使用而无性能变化;可在200度下连续使用10,000小时;在350度下亦可使用一段时间。
彩色橡胶制品高弹性和低压变研制(附带案例配方-天然、丁腈、乙丙橡胶三个)

彩色橡胶制品高弹性和低压变研制(附带案例配方-天然、丁腈、乙丙橡胶三个)彩色橡胶常出现的问题1、混炼胶料中的颜料分散不均出现色差;吃料慢,难分散;混炼密炼升温快易焦烧(死胶);2、硫化硫化速度慢制品高温色变;制品容易黏磨;出磨热撕性差;飞胶边厚,难修边;3、成品橡胶成品弹性差、压缩变形大;橡胶成品时间长出现色差、黄变现象;橡胶成品停放厚容易出现喷霜。
影响高弹和压变:1.橡胶的种类弹性取决于橡胶分子链的内旋转难易,分子问作用力的大小。
如天然胶、顺丁胶、丁基胶、硅橡胶等被认为足弹性好的橡胶。
2.分子量的大小影响分子链的卷曲程度、无用未端的数量。
分子量大,弹性较好。
3.共聚橡胶的化学组成及结构本文来自橡胶信息网丁苯胶、丁腈胶中随苯乙烯和丙烯腈含量的增加弹性变差。
乙丙橡胶中,丙烯的含量为4O~5O%时弹性最好,这时形成的共聚物是无规共聚物,如果乙烯含量超过7O%,形成较长的乙烯嵌段,长乙烯嵌段易形成结品而使乙丙胶失去弹性。
二、补强填充剂对硫化胶弹性的影响非炭黑补强填充剂会损害橡胶的弹性,增大压缩永久变形。
这与在应力作用下,橡胶分子在非活性填充剂表面滑动,除去应力以后,又阻碍分子键的恢复有关。
偶联荆的应用可以大大地改善非补强填充剂对硫化胶弹性的影响(改善填充荆的分敝性和表面活性)大多文献资料中都说,随着炭黑粒径的增大,硫化胶的弹性增强,但往往忽略了填充量对硫化橡胶弹性的影响。
实际上各种橡胶产品都有一定的硬度和强度要求,如单一地使用低补强性炭黑时,用量需要增大,这样同样会损害橡胶的弹性和恢复。
在一定变形量的硫化橡胶中,填充的橡胶分子链的变形量要比实际变形量大,扩大的数值与填充量成比例。
变形量的增大同样会影响橡胶分子链的位移位置和恢复,增大永久变形。
采用适当地补强剂并用和适当地混合工艺,使混炼胶获得理想的结构形态,可以得到高弹性的硫化橡胶。
本文来自橡胶信息网三、软化荆和增塑荆软化荆通常指与橡胶桕容性火是很好的汕类或树脂,增塑荆指与橡胶桕容性好的油或树脂。
110 甲基乙烯基硅橡胶 生产工艺
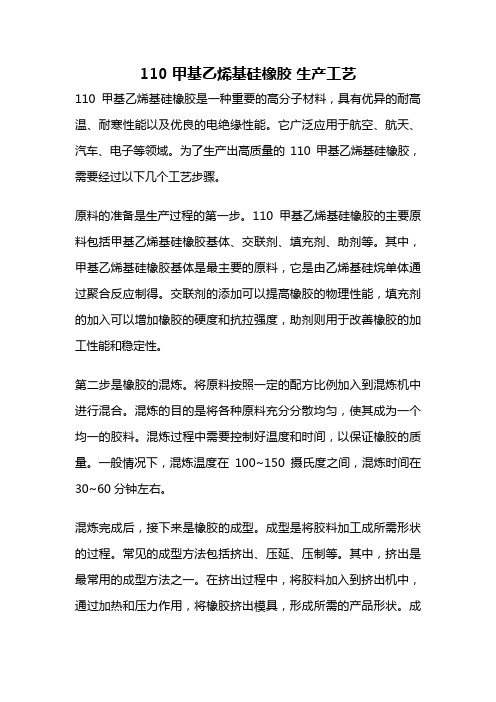
110 甲基乙烯基硅橡胶生产工艺110甲基乙烯基硅橡胶是一种重要的高分子材料,具有优异的耐高温、耐寒性能以及优良的电绝缘性能。
它广泛应用于航空、航天、汽车、电子等领域。
为了生产出高质量的110甲基乙烯基硅橡胶,需要经过以下几个工艺步骤。
原料的准备是生产过程的第一步。
110甲基乙烯基硅橡胶的主要原料包括甲基乙烯基硅橡胶基体、交联剂、填充剂、助剂等。
其中,甲基乙烯基硅橡胶基体是最主要的原料,它是由乙烯基硅烷单体通过聚合反应制得。
交联剂的添加可以提高橡胶的物理性能,填充剂的加入可以增加橡胶的硬度和抗拉强度,助剂则用于改善橡胶的加工性能和稳定性。
第二步是橡胶的混炼。
将原料按照一定的配方比例加入到混炼机中进行混合。
混炼的目的是将各种原料充分分散均匀,使其成为一个均一的胶料。
混炼过程中需要控制好温度和时间,以保证橡胶的质量。
一般情况下,混炼温度在100~150摄氏度之间,混炼时间在30~60分钟左右。
混炼完成后,接下来是橡胶的成型。
成型是将胶料加工成所需形状的过程。
常见的成型方法包括挤出、压延、压制等。
其中,挤出是最常用的成型方法之一。
在挤出过程中,将胶料加入到挤出机中,通过加热和压力作用,将橡胶挤出模具,形成所需的产品形状。
成型温度和压力的控制是保证成型质量的关键。
成型完成后,还需要对橡胶进行硫化处理。
硫化是将橡胶中的硫和交联剂反应,形成硫化交联网络的过程。
硫化可以提高橡胶的强度、耐磨性和耐温性能。
常用的硫化方法有热硫化和加热硫化两种。
热硫化是将成型的橡胶制品放入硫化炉中,在一定的温度下进行硫化。
加热硫化是将成型的橡胶制品放入加热板中,通过加热板的加热作用,使橡胶硫化。
经过硫化处理的橡胶制品需要进行后处理。
后处理的目的是去除硫化产物和改善橡胶的表面性能。
常见的后处理方法有洗涤、除臭、热处理等。
洗涤是将橡胶制品放入洗涤机中,用清洁剂进行清洗,去除硫化产物。
除臭是通过加热处理橡胶制品,使其产生挥发性物质,从而去除橡胶的异味。
211064797_MVQ_与AEM_共混胶胶料性能的研究

MVQ与AEM共混胶胶料性能的研究陈国栋上海锐巴新材料科技有限公司55中国橡胶应用技术APPLIED TECHNOLOGY邦公司;其他原材料全部由上海品盛化工有限公司提供。
2.配方AEM 混炼胶:AEM 100,SA 1,N550 55,防445 1,654 1,DCP 5。
MVQ 混炼胶:MVQ 100,白炭黑 40,TAIC 1,DCP 1。
3.主要仪器和设备X (K )-160开炼机,上海橡胶机械厂;电加热平板硫化机HS100T-FTMO-90,佳鑫电子设备科技(深圳)有限公司;AI-8000S 电子拉力机,台湾高铁科技股份有限公司;邵氏硬度计、老化试验箱,上海实验仪器总厂;MV2000型门尼粘度仪,美国阿尔法科技公司;热失重分析仪209F1,德国NETZSCH 公司;老化试验箱401A 型,上海实验仪器厂有限公司;橡塑低温脆性试验仪 MZ-4068,江都市明珠试验机机械厂;242型动态分析仪,德国NETZSCH 公司。
4.试样制备(1)MVQ 混炼胶制备硅橡胶→塑炼→加入各种助剂小料→混炼→加入硫化剂DCP →混炼→薄通6~8次→下片→备用(2)AEM 橡胶制备乙烯丙烯酸酯橡胶→塑炼→下片→备用(AEM 母炼胶需在炼胶房内加入白炭黑、硫化剂、小料后打三角包5次,混炼均匀后,下片,停放待用。
)(3)MVQ 橡胶与AEM 橡胶共混工艺AEM 母炼胶→塑炼包辊→逐渐加入MVQ 胶片→混炼→加入硫化剂→混炼→薄通6次→下片→停放24h →待用(4)硫化执行标准按照GB 6038-2006,参考标准ISO/DIS2393-2014。
裁出拉伸、撕裂、回弹、压缩永久变形所需胶片。
其中拉伸片的宽度方向与压延方向一致,撕裂片的宽度方向与压延方向相垂直。
胶料的硫化条件为:硫化温度为170℃,硫化压力均10MPa ,硫化时间为硫化仪所测定的各试样的理论正硫化时间t c90。
硫化后的试样,在室温下停放10h 后,进行性能测试。
有机硅名词:高温胶室温胶

室温胶 RTV-1与RTV-2
RTV-1
RTV-2
引发剂 空气中水分 催化剂
特点
使用方便, 但深部固化 速度较困难
固化时不放热, 收缩率很小,不膨胀,无内应 力,可在内部和表面同时进行,深部硫化。具 有优良的电气绝缘性、耐电弧、电晕、耐水、 耐臭氧、耐气候老化、耐高低温性能,同时具 有优异的脱模性。
主要高温胶品种
苯基硅橡胶
随着苯基含量的增加,分子链的刚性增大,其结晶温度反而上升。 苯基含量(苯基与硅原子之比)在5~10%时称低苯基硅橡胶,在70~-100℃仍能保持橡胶的弹性,是所有橡胶中低温性能最好的一 种。苯基含量20~40%时称中苯基硅橡胶,它具有卓越的耐燃特性, 一旦着火可以自熄。苯基含量在40~50%时称高苯基硅橡胶,它具 有优异的耐辐射性能。
阻燃型 :添加含卤或铂化合物作阻燃剂,具有良好的抗 燃性。
导电硅橡胶 :以乙炔炭黑或金属粉末作填料,选择高温 硫化或加成型硫化方法,可得到体积电阻系数为2.0~ 102Ω·cm的硅橡胶。
热收缩型 :乙烯基硅橡胶中加入具有一定熔融温度或软 化温度的热塑性材料,成品热收缩率可达35 % ~50%。
高强度型 :采用乙烯基硅橡胶或低苯基硅橡胶,以高比表 面积或处理型的白炭黑作补强剂,配合其他技术改进措施, 改进交联结构,提高撕裂强度。
耐高温型: 采用乙烯基硅橡胶或低苯基硅橡胶,适当选择 补强剂和耐热添加剂,可制得耐300~350℃高温的硅橡胶。
低温型 :主要采用低苯基硅橡胶,脆性温度达-120℃,在 -90℃时不丧失弹性。
RTV-1是以羟基封端的聚二甲基硅氧烷为基础胶料, 配以补强填料、交联剂、催化剂,经特殊配制而成。 在大气中交联时脱除低分子物质,根据脱除物的种类, 单组份又分为脱酸型、脱酮肟型、脱醇型、脱酰胺型 和脱酮型等类型,其中以前三种用途最为广泛。
- 1、下载文档前请自行甄别文档内容的完整性,平台不提供额外的编辑、内容补充、找答案等附加服务。
- 2、"仅部分预览"的文档,不可在线预览部分如存在完整性等问题,可反馈申请退款(可完整预览的文档不适用该条件!)。
- 3、如文档侵犯您的权益,请联系客服反馈,我们会尽快为您处理(人工客服工作时间:9:00-18:30)。
1
甲基乙烯基硅橡胶混炼胶压缩永久变形性能的改善
甲基乙烯基硅橡胶是以硅-氧键为主链的有机硅化合物,侧基由甲基、乙烯基取代基构
成。它的分子主链是由硅原子和氧原子交替组成(-si-o-si-)的硅氧键,其键能达
370kJ/mol,比一般橡胶的碳碳结合键能(240kJ/mol)要大很多,因此其结构决定了硅橡胶有
具有很好热稳定性及绝缘、耐天候老化性。这是硅橡胶广泛地应用在电力、电气、
汽车、机械及其他行业中。
目前国内大多数橡胶加工企业都使用预混炼胶来制作橡胶制品,这种生产方式改进了传
统的开炼机混炼工艺,降低了劳动强度,提高了劳动效率,同时避免了因白炭
黑飞扬而造成的环境污染,但硅橡胶混炼胶的压缩永久变形性能较差,在密封制品领域内很
难大规模应用,为了拓宽混炼胶的使用范围,需改善其力学性能,尤其是压缩永
久变形性能,我们对此进行了一些技术改进。
1 实验部分
1.1 原材料
硅橡胶预混胶,南京产;甲基乙烯基硅橡胶110-2,吉化公司合成橡胶厂;氧化铁130,
市售;硫化剂DCP,双-2,5,市售;常用助剂,市售。
1.2 主要设备及仪器
XK-160型双辊筒开炼机,广东湛江机械厂;50t平板硫化机,湖州橡胶机械厂生产;
ZMGL250拉力实验机,江都明珠试验机厂生产;401A型老化实验箱,大连干燥箱厂生产。
1.3 试样制备
胶料在开炼机上进行混炼,基本工艺:硅橡胶混炼胶→硅橡胶110-2→氧化铁→硫化剂
→耐热添加剂,混炼均匀,薄通后下片,停放至少24h后硫化试样。
胶料在平板硫化机上硫化。试片硫化条件:160℃×10min,压力10-12MPa;试样(Φ10
×10)硫化条件:160℃×15min,压力10-12MPa。
二段硫化在老化试验箱中进行。常温→150℃×1h→(1h)→200℃×4h,鼓风。
1.4 性能测试
按GB/T 528-1998,GB/T 531-1999测量硫化硅橡胶试样的物理机械性能;按GB/T
7759-1987测量试样的压缩永久变形性能;按GB/T3512-2001测量其热空气老化性能;抗撕
裂性能按GB/T 529-1999测试,采用直角型试样。
2 结果与讨论
2.1 不同硫化剂的影响
2
从硅橡胶热老化过程的规律出发,提高硅橡胶热稳定性即提高硅橡胶的抗氧化降解能
力,可从生胶结构和混炼胶配合两方面考虑,主要途径有:①防止硅橡胶有机侧基的氧化分
解引起交联和降解,改变侧基钓结构,如引入苯基等;②防止主链环化解聚引起降解,主链
中引人大体积链段,如碳硼烷基、苯撑基、苯醚撑基、环二硅氮烷基等;③防止硫化胶中交
联链断裂,使硫化胶中含有比C-C键更高热氧化稳定性的交联键;④添加耐热添加剂防止
侧链氧化交联和主链环化解聚,如Fe2O-3,CeO2等,提高硅橡胶侧基的热氧化稳定性,六
苯基环三硅氧烷、硅氮橡胶等可以防止主链的环化解聚。
使用2种不同硫化剂的硅橡胶胶料的性能对照,见表1。
表1 2种不同硫化剂的硅橡胶性能表
硫化剂 邵尔A硬度 拉伸强度,MPa 拉断伸长率,% 拉断变形,% 撕裂强度,
Mpa 压变,%(200℃×48h,30%) 250℃×72h老化后 邵尔A硬度,度 拉断伸长
率,%
双-2,5 48 7 400 5 14
65 40 360
DCP 50 6 330 8 21
56 432 250
试验配方;预混胶,100;Fe2O3,5:硫化剂,1.0。
从表1可以看出,DCP硫化的硅橡胶压缩永久变形和抗撕裂性能较用双-2,5硫化的硅
橡胶的性能优,其他性能大致相当。压缩永久变形性能较优,表明该胶料在高温下的抗氧化
能力强,故试验胶料硫化剂选用DCP。
为了进一步改善混炼胶的压缩永久变形性能,从增加生胶用量,选择合适的硫化剂用量
以及添加耐热助剂上着手,以提高胶料在高温下抗氧化降解能力。
叶定雷
2014年2月28日