射线检测技术对焊缝缺陷深度的判断效果
(整理)TOFD技术与射线技术在焊接接头检测中的对比.

TOFD检测技术和RT检测技术在焊接接头检测中的对比实验徐生东1 张鹏林2(1.兰州石化公司建设公司甘肃兰州730060;2.兰州理工大学材料工程学院甘肃兰州 730060)摘要:本文介绍了TOFD 技术的基本概念、原理、特点,以及TOFD与RT技术对比试验结果等,并提出承压设备焊接检测工作使用TOFD 技术替代射线方法的新局面。
关键词:TOFD技术标准射线检测检测能力对比试验应用效果TOFD detection and RT detection technology in thewelding experiments of joint detectionXu Shengdong 1 Zhang Penglin 2(1 Petrochemical Industries Co of Lanzhou construction company Gansu Lanzhou730060; 2College of materials engineering Lanzhou University ofTechnology Gansu Lanzhou 730060)Abstract: This paper introduces the basic concepts of TOFD technology, principle, characteristics, and the TOFD and RT technology in comparison to the experimental results, and proposes the bearing pressure equipment welding inspection work using TOFD technology instead of X-ray method a new situation.Key words: TOFD technology standard ray detection ability contrast experiment and application effects1 概述由于TOFD的缺陷高检出率和缺陷深度定位的准确性以及检测的高效率,TOFD技术在国内已用于天然气管道、加氢反应器等焊缝的检测。
射线检测质量分级

射线检测质量分级焊缝质量按缺欠性质、长度、数量分为四个级别;其中I级最佳,□级、川级依次降低,超过川级为W级。
裂纹是焊缝中危害性大的缺陷,应评为W级。
14.2缺欠的分级1421圆形缺欠的分级a)长宽比小于或等于3的缺欠定义为圆形缺欠。
他们可以是圆形、椭圆形、锥形或带有尾巴(在测定尺寸时应包括尾部)等不规则形状,包括气孔、夹渣和夹钨。
b)圆形缺欠用评定区进行评定,评定区域的大小见表7。
评定区框线的长边要与焊缝平行。
框线内必须包含最严重区域内的主要缺欠。
与框线外切的不计点数,相割的计入点数。
表缺欠评定区c )评定圆形缺欠时,应将缺欠尺寸按表8换算成缺欠占数表缺欠点数换算表d )不记点数的缺欠尺寸见表9表9不记点数的缺欠尺寸e )圆形缺欠的分级见表 10表10圆形缺欠的分级(1)长宽比小于或等于3的气孔、夹渣和夹钨统称圆形缺欠。
(2 )圆形缺欠应用评定区进行评定。
评定区框线的放置是引起圆形缺欠评级争议的关键。
本标准参照GB3323-87 的使用说明,从正文中明确了评定区的框线的放置要求。
即:评定区的框线必须放在焊缝内缺欠最严重的区域,框线内必须完整的包括严重区域的主要缺欠,框线的长边与焊缝平行。
与框线外切的不计点数,相割的计入点数,如图05所示。
图05圆形评定区框放置(3)表7、表&表9及表10与原标准相同,只不过表10的评定区10 mx 20 mm,对应的母材厚度由原来的>25〜30 mm,变为>25〜50mm。
(4)对圆形缺欠各国评定不一:ASME和API std 1104都是用标准图来表示合格与否的。
我国焊缝射线检测标准都是分级的,合格级别在相应的标准或设计图样中明确,这与日本JIS3104的评定方法相一f )圆形缺欠长径大于T/2时,评为W级。
圆形缺欠长径超过1/2壁厚评为W级与原标准相同,这与我国的锅炉压力容器标准的规定是一致的。
GB3323-87规定“I 级焊缝或母材厚度小于或等于5 mm的口级焊缝内不计点数的圆形缺陷,在评定区内不得多于10点,否则应降一级”,此条规定不是说I 级焊缝在评定区内 不计点数的缺欠超过 10点就评为不合格而可以评为H 级; 母材厚度小于或等于 5伽的□级焊缝内不计点数的圆形缺欠 超过10点,不能评为□级而评为川级。
焊缝检测报告

焊缝检测报告一、引言焊接作为一种常见的连接工艺,在各个领域都有着广泛的应用。
而焊缝作为焊接的关键部位,其质量直接影响着焊接件的强度和性能。
因此,焊缝的检测是确保焊接质量的重要环节。
本报告旨在对焊缝的检测方法和结果进行详细的介绍和分析。
二、焊缝检测方法常用的焊缝检测方法主要包括目视检测、超声波检测、X射线检测和磁粉检测等。
每种方法都有其适用的场景和优势。
1. 目视检测目视检测是最简单、最常用的一种焊缝检测方法。
通过肉眼观察焊缝表面的形态、气孔、裂纹等缺陷,来判断焊缝的质量。
目视检测操作简便、成本低廉,适用于一些简单结构和表面质量要求不高的焊接件。
然而,目视检测的主观性较强,对于微小缺陷的检测效果有限。
2. 超声波检测超声波检测利用超声波在不同介质中传播的原理,通过对焊缝进行超声波的传播和反射,来检测焊缝内部的缺陷。
超声波检测具有无损、高灵敏度、定量化等优点,适用于对焊缝内部缺陷的检测。
然而,超声波检测的设备和操作较为复杂,对操作人员的技术要求较高。
3. X射线检测X射线检测利用射线在物体中的吸收和散射特性,通过对焊缝进行X射线的照射和接收,来获得焊缝内部的信息。
X射线检测具有穿透力强、分辨率高等优点,适用于对焊缝内部的缺陷、结构等进行检测。
然而,X射线检测对设备的要求较高,操作时需要注意辐射防护。
4. 磁粉检测磁粉检测是一种利用磁场和磁性粉末的特性,检测焊缝表面和近表面缺陷的方法。
通过对焊缝表面施加磁场,再撒布磁性粉末,通过观察磁粉在缺陷处的聚集情况,来判断焊缝的质量。
磁粉检测具有操作简便、效果直观等优点,适用于对焊缝表面缺陷的检测。
然而,磁粉检测只能检测表面和近表面缺陷,对于焊缝内部的缺陷无法进行检测。
三、焊缝检测结果根据以上的检测方法,我们对焊缝进行了全面的检测,并得到了以下的结果:1. 目视检测结果通过目视检测,我们观察到了焊缝表面的形态和缺陷情况。
经过仔细观察,我们发现焊缝表面存在少量气孔和夹渣现象。
射线检测-焊缝缺陷图谱

1.外部缺陷在焊缝的表面,用肉眼或低倍放大镜就可看到,如咬边,焊瘤,弧坑,表面气孔和裂纹等。
2.内部缺陷位于焊缝内部,必须通过各种无损检测方法或破坏性试验才能发现。
内部缺陷有未焊透,未熔合,夹渣,气孔,裂纹等,这些缺陷是我们无损检测人员检查的主要对象。
焊缝缺陷的危害性:1、由于缺陷的存在,减少了焊缝的承载截面积,削弱了静力拉伸强度。
2、由于缺陷形成缺口,缺口尖端会发生应力集中和脆化现象,容易产生裂纹并扩展。
3、缺陷可能穿透焊缝,发生泄漏,影响致密性。
焊缝纵向裂纹示意图一、焊缝纵向裂纹X光底片焊缝纵向裂纹1 焊缝纵向裂纹2焊缝纵向裂纹3 焊缝纵向裂纹4焊缝纵向裂纹5 焊缝纵向裂纹6焊缝纵向裂纹7 焊缝纵向裂纹8焊缝纵向裂纹9 焊缝纵向裂纹10焊缝纵向裂纹11 焊缝纵向裂纹12焊缝纵向裂纹13 焊缝纵向裂纹14焊缝纵向裂纹15 焊缝纵向裂纹16焊缝纵向裂纹17 焊缝纵向裂纹18焊缝纵向裂纹19 焊缝纵向裂纹20 纵向裂纹的表面特征是沿焊缝长度方向出现的黑线,它既可以是连续线条,也可以是间断线条。
纵向裂纹影像产生的原因是沿焊缝长度破裂而导致的不连续黑线。
二、热影响区纵向裂纹X光底片热影响区纵裂1 热影响区纵裂2 热影响区撕裂呈线性黑色锯齿状,平行于熔合线,穿晶扩展,表面无明显氧化色彩,属脆性断口的延迟裂纹。
焊缝横向裂纹示意图三、焊缝横向裂纹X光底片焊缝横向裂纹1 焊缝横向裂纹25焊缝横向裂纹3 焊缝横向裂纹4焊缝横向裂纹的表征是横在焊接影像上的一根细小黑线(直线或曲线),它产生的原因是由焊缝上的金属破裂引起的。
当焊接应力为拉应力并与氢的析集和淬火脆化同时发生时,极易产生冷裂纹。
四、母材裂纹X光底片母材裂纹1 母材裂纹2裂纹:材料局部断裂形成的缺陷。
裂纹的分类方法:按延伸方向可分为纵向裂纹、横向裂纹、辐射状裂纹;按发生部位可分为焊缝裂纹、热影响区裂纹、熔合区裂纹、焊趾裂纹、弧坑裂纹、母材裂纹;按发生条件和时机可分为热裂纹、冷裂纹、再热裂纹。
不等厚对接管道焊缝射线检测技术总结

不等厚对接管道焊缝射线检测技术总结本文通过对福清核电站一期中GPV系统不等厚对接管道焊接接头的射线照相检测,试验证明,选用合适的透照工艺以及使用双胶片法可使射线照相得到较高的对比灵敏度、合适的黑度等,满足了工程及相关技术标准的要求。
标签:射线检测;双胶片法;GPV系统;不等厚对接管道1 透照工艺试验研究针对以上分析,提高射线照相的对比度和保证黑度是不等厚管道焊缝透照工艺的关键。
认真分析影响射线照相灵敏度和缺陷检出率的各种因素,并排除选择余地少或对射线照相灵敏度影响小的因素,选择以下几个因素进行透照工艺的试验研究。
根据现场的实际情况,不等厚管道射线检测可以采取三种方法:双胶片法、放射源偏心法和高电压法。
1.1 放射源不等厚管道的规格626×33/614×25mm余高为2mm,部分不等厚管道留了射线曝光孔,因此透照方式可以采用选择单壁内透和双壁单影两种方法。
为保证射线照相的对比度、清晰度和颗粒度,直接关系到射线照相的灵敏度,为提高射线照相的灵敏度,根据DL821-2002的要求对于透照厚度差较大的工件,当透照厚度(TA)大于或等于10mm时,采用适宜的γ射线源透照,可获得较大的检测范围,所以放射源选用Ir92,焦点尺寸尽量小。
X射线机选择上方公司的型号为3505。
1.2 底片黑度DL821-2002标准规定X射线底片黑度为 1.5-3.5,γ射线的底片黑度为1.8-3.5。
由于不等厚管道管径不同,存在厚度差,导致底片一半黑一半白,底片黑度无法满足要求,采用了双胶片法、放射源偏心法及高电压法,使底片黑度达到要求。
1.3 像质计的选择及放置图像质量必须能使规定直径的金属丝在底片上清楚的显示出来。
像质计的选择按照表1所示。
像质计应放在被检部位射线源侧,当无法在源侧放置像质计时,可放在胶片侧的工件表面上,此时应在像质计附近附加“F”铅示标记以示区别,像质计灵敏度应该提高一级或通过对比试验使底片的质量达到规定的要求。
角焊缝探伤检测方法

角焊缝探伤检测方法?一、角焊缝探伤检测方法?步骤/方式1射线探伤方法(RT)目前应用较广泛的射线探伤方法是利用(X、γ)射线源发出的贯穿辐射线穿透焊缝后使胶片感光,焊缝中的缺陷影像便显示在经过处理后的射线照相底片上,能发现焊缝内部气孔、夹渣、裂纹及未焊透等缺陷。
步骤/方式2超声波探伤(UT)超声波比射线探伤灵敏度高,灵活方便,周期短、成本低、效率高、对人体无害,但显示缺陷不直观,对缺陷判断不精确,受探伤人员经验和技术熟练程度影响较大。
步骤/方式3磁性探伤(MT)磁性探伤主要用于检查表面及近表面缺陷。
该方法与渗透探伤方法比较,不但探伤灵敏度高、速度快,而且能探查表面一定深度下缺陷。
步骤/方式4渗透探伤(PT)液体渗透探伤主要用于检查坡口表面、碳弧气刨清根后或焊缝缺陷清除后的刨槽表面、工卡具铲除的表面二、超声波探伤仪探头的介绍超声波探伤仪探头目前最多常见的是德国KK的产品,由于德国KK被美国GE收购以后,所以现在这类探头也叫美国GE德国KK探头。
主要应用于一般焊缝检测,大尺寸,厚部件的检测。
三、什么情况下使用超声波探伤?它与射线探伤有何区别?在不能破坏加工表面的要求下可以使用超声波仪器或设备来进行检测。
一、方式不同1、超声波探伤:是利用超声能透入金属材料的深处,并由一截面进入另一截面时,在界面边缘发生反射的特点来检查零件缺陷的一种方法。
2、射线探伤:是利用某种射线来检查焊缝内部缺陷的一种方法。
二、原理不同1、超声波探伤:波束自零件表面由探头通至金属内部,遇到缺陷与零件底面时就分别发生反射波,在荧光屏上形成脉冲波形,根据这些脉冲波形来判断缺陷位置和大小。
2、射线探伤:射线通过被检查的焊缝时,因焊缝缺陷对射线的吸收能力不同,使射线落在胶片上的强度不一样,胶片感光程度也不一样,这样就能准确、可靠、非破坏性地显示缺陷的形状、位置和大小。
三、优缺点不同1、超声波探伤:穿透能力强,探测深度可达数米,要由有经验的人员谨慎操作。
焊缝质量检测方法

焊缝质量检测方法1.目测检测方法目测是最简单常用的焊缝质量检测方法之一、通过肉眼直接观察焊缝外观,检查有无裂纹、孔洞、咬边等缺陷。
目测检测可以快速判断焊缝的表面质量和形状。
2.放射检测方法放射检测是利用放射性同位素或X射线对焊缝进行检测。
放射检测分为射线摄影和射线透射两种。
射线摄影通过将射线照射到焊缝上,然后在感光材料上观察形成的曝光图像,根据图像的密度和缺陷形态来判断焊缝的质量。
射线透射是将射线穿过焊缝,通过检测器接收射线,根据接收到的射线强度来判断焊缝的质量。
3.超声波检测方法超声波检测是利用超声波在材料中传播的特性,来进行焊缝质量检测。
超声波的传播速度和焊接缺陷之间存在关联,当焊接缺陷存在时,超声波的传播速度会发生变化。
通过超声波传感器的发射和接收,可以检测焊缝中的缺陷,如裂纹、孔洞、夹杂物等。
4.磁粉检测方法磁粉检测是利用液体磁粉或磁性颗粒在磁场作用下在焊缝表面产生磁化,然后观察磁粉或磁性颗粒的分布情况,从而检测焊缝中的裂纹、疲劳断裂等表面缺陷。
5.渗透检测方法渗透检测是通过将渗透剂涂在焊缝表面,然后在一定时间后将渗透剂清洗掉。
如果焊缝有裂纹或其他缺陷,渗透剂会渗入缺陷处,形成可见的痕迹。
通过观察渗透剂的渗透情况,可以判断焊缝的质量。
以上方法是常用的焊缝质量检测方法,不同的方法适用于不同的焊接方法和焊缝类型。
在进行具体的焊缝质量检测时,需要根据实际情况选择合适的方法,并进行相应的测试和分析。
同时,为了保证焊缝质量的可靠性,应该配合使用多种检测方法进行综合评估和判定。
射线底片未焊透与未熔合缺陷影像的识别
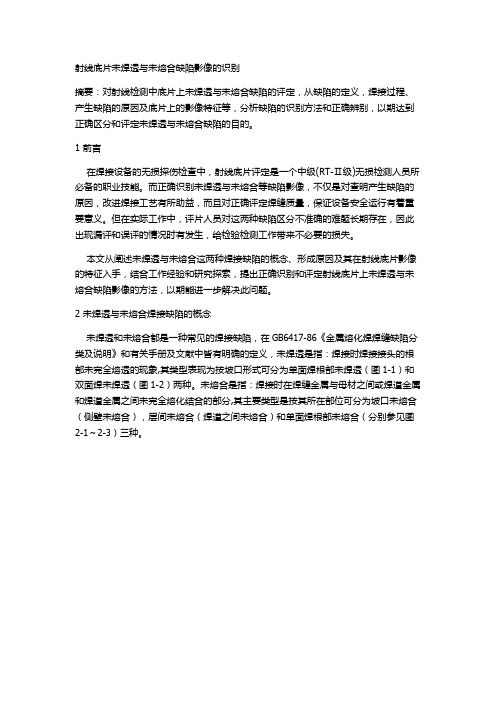
射线底片未焊透与未熔合缺陷影像的识别摘要:对射线检测中底片上未焊透与未熔合缺陷的评定,从缺陷的定义,焊接过程、产生缺陷的原因及底片上的影像特征等,分析缺陷的识别方法和正确辨别,以期达到正确区分和评定未焊透与未熔合缺陷的目的。
1 前言在焊接设备的无损探伤检查中,射线底片评定是一个中级(RT-Ⅱ级)无损检测人员所必备的职业技能。
而正确识别未焊透与未熔合等缺陷影像,不仅是对查明产生缺陷的原因,改进焊接工艺有所助益,而且对正确评定焊缝质量,保证设备安全运行有着重要意义。
但在实际工作中,评片人员对这两种缺陷区分不准确的难题长期存在,因此出现漏评和误评的情况时有发生,给检验检测工作带来不必要的损失。
本文从阐述未焊透与未熔合这两种焊接缺陷的概念、形成原因及其在射线底片影像的特征入手,结合工作经验和研究探索,提出正确识别和评定射线底片上未焊透与未熔合缺陷影像的方法,以期能进一步解决此问题。
2 未焊透与未熔合焊接缺陷的概念未焊透和未熔合都是一种常见的焊接缺陷,在GB6417-86《金属熔化焊焊缝缺陷分类及说明》和有关手册及文献中皆有明确的定义,未焊透是指:焊接时焊接接头的根部未完全熔透的现象,其类型表现为按坡口形式可分为单面焊根部未焊透(图1-1)和双面焊未焊透(图1-2)两种。
未熔合是指:焊接时在焊缝金属与母材之间或焊道金属和焊道金属之间未完全熔化结合的部分,其主要类型是按其所在部位可分为坡口未熔合(侧壁未熔合),层间未熔合(焊道之间未熔合)和单面焊根部未熔合(分别参见图2-1~2-3)三种。
.3未焊透与未熔合的产生原因3.1未焊透的产生原因未焊透的产生原因是焊接参数选择不当而引起,如焊接电流太小、运条速度太快、焊条角度不当或电弧发生偏吹以及坡口角度或焊接间隙太小等,它与焊接冶金因素关系不大。
有时焊工操作失误也会产生未焊透缺陷,如在不开坡口的双面埋弧自动焊中,也会由于两面焊接时中心对偏而形成未焊透。
3.2未熔合的产生原因未熔合的产生原因有焊接参数选择不当,如焊接线能量过小、电弧偏吹和焊条药皮偏心等;也有因焊工操作失误方面的原因,如坡口不够清洁、电弧离坡口过远、运条不当、摆动时在两端停留时间过短以及焊条直径或种类不对和焊丝倾角不合适等;因此使得母材或焊缝层间金属在未得到充分熔化前就被填充金属覆盖而造成未熔合缺陷。