机械可靠性设计分析
机械设计中的可靠性分析与评估
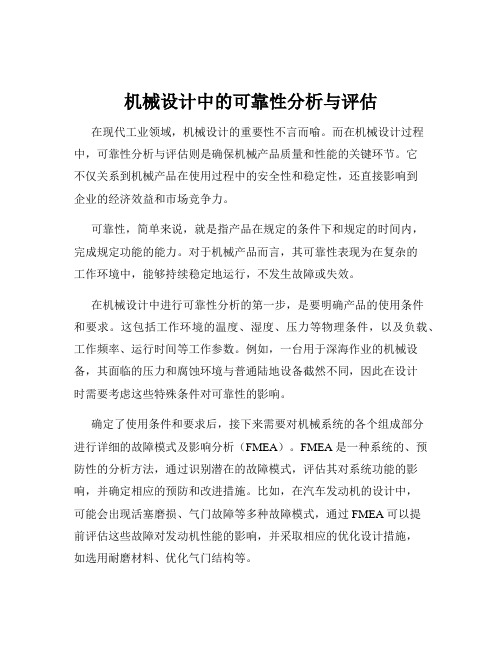
机械设计中的可靠性分析与评估在现代工业领域,机械设计的重要性不言而喻。
而在机械设计过程中,可靠性分析与评估则是确保机械产品质量和性能的关键环节。
它不仅关系到机械产品在使用过程中的安全性和稳定性,还直接影响到企业的经济效益和市场竞争力。
可靠性,简单来说,就是指产品在规定的条件下和规定的时间内,完成规定功能的能力。
对于机械产品而言,其可靠性表现为在复杂的工作环境中,能够持续稳定地运行,不发生故障或失效。
在机械设计中进行可靠性分析的第一步,是要明确产品的使用条件和要求。
这包括工作环境的温度、湿度、压力等物理条件,以及负载、工作频率、运行时间等工作参数。
例如,一台用于深海作业的机械设备,其面临的压力和腐蚀环境与普通陆地设备截然不同,因此在设计时需要考虑这些特殊条件对可靠性的影响。
确定了使用条件和要求后,接下来需要对机械系统的各个组成部分进行详细的故障模式及影响分析(FMEA)。
FMEA 是一种系统的、预防性的分析方法,通过识别潜在的故障模式,评估其对系统功能的影响,并确定相应的预防和改进措施。
比如,在汽车发动机的设计中,可能会出现活塞磨损、气门故障等多种故障模式,通过 FMEA 可以提前评估这些故障对发动机性能的影响,并采取相应的优化设计措施,如选用耐磨材料、优化气门结构等。
在可靠性分析中,概率统计方法也发挥着重要的作用。
通过收集和分析大量的现场数据或实验数据,可以确定各种故障模式的发生概率和故障间隔时间。
这些数据为评估机械产品的可靠性提供了定量的依据。
以数控机床为例,通过对其关键零部件的故障数据进行统计分析,可以计算出平均故障间隔时间(MTBF),从而评估机床的可靠性水平,并为后续的维护和改进提供参考。
除了上述方法,可靠性仿真技术也是近年来在机械设计中得到广泛应用的手段之一。
利用计算机仿真软件,可以模拟机械系统在各种工况下的运行情况,预测可能出现的故障,并评估不同设计方案的可靠性。
例如,在航空发动机的设计中,可以通过仿真分析叶片在高速旋转时的应力分布和疲劳寿命,从而优化叶片的形状和材料,提高发动机的可靠性。
机械工程的可靠性优化设计分析
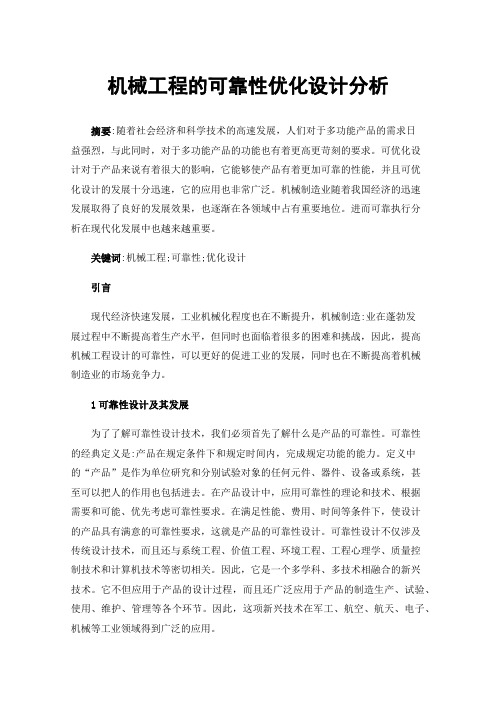
机械工程的可靠性优化设计分析摘要:随着社会经济和科学技术的高速发展,人们对于多功能产品的需求日益强烈,与此同时,对于多功能产品的功能也有着更高更苛刻的要求。
可优化设计对于产品来说有着很大的影响,它能够使产品有着更加可靠的性能,并且可优化设计的发展十分迅速,它的应用也非常广泛。
机械制造业随着我国经济的迅速发展取得了良好的发展效果,也逐渐在各领域中占有重要地位。
进而可靠执行分析在现代化发展中也越来越重要。
关键词:机械工程;可靠性;优化设计引言现代经济快速发展,工业机械化程度也在不断提升,机械制造:业在蓬勃发展过程中不断提高着生产水平,但同时也面临着很多的困难和挑战,因此,提高机械工程设计的可靠性,可以更好的促进工业的发展,同时也在不断提高着机械制造业的市场竞争力。
1可靠性设计及其发展为了了解可靠性设计技术,我们必须首先了解什么是产品的可靠性。
可靠性的经典定义是:产品在规定条件下和规定时间内,完成规定功能的能力。
定义中的“产品”是作为单位研究和分别试验对象的任何元件、器件、设备或系统,甚至可以把人的作用也包括进去。
在产品设计中,应用可靠性的理论和技术、根据需要和可能、优先考虑可靠性要求。
在满足性能、费用、时间等条件下,使设计的产品具有满意的可靠性要求,这就是产品的可靠性设计。
可靠性设计不仅涉及传统设计技术,而且还与系统工程、价值工程、环境工程、工程心理学、质量控制技术和计算机技术等密切相关。
因此,它是一个多学科、多技术相融合的新兴技术。
它不但应用于产品的设计过程,而且还广泛应用于产品的制造生产、试验、使用、维护、管理等各个环节。
因此,这项新兴技术在军工、航空、航天、电子、机械等工业领域得到广泛的应用。
2机械制造工艺可靠性的分析方法2.1管理工艺环节一个行业能否有效运行,关键点是不能离开其合理性与高效性,从机械制造行业的角度探寻问题,我们能够了解正常的运行也要讲求科学与合理,通过合理化的经营管理,能提升整个工艺流程。
机械零件的可靠性设计

3
加强维护
定期维护和保养机械零件,延长其寿命并提高可靠性。
可靠性测试和验证
测试方法
使用可靠性测试方法来验证零件的寿命和性能。
验证过程
验证设计的可靠性,确保其在实际使用中能够达到 预期要求。
案例研究和实践经验
1
汽车发动机设计
通过可靠性改进措施和测试验证,成功提高了发动机的可靠性和性能。
2
航空航天器零件
可靠性评估方法
故障模式与影响分析 (FMEA)
通过识别故障模式和评估其影响,确定潜在故障并采取措施预防。
可靠性指标计算
计算关键零件的故障率、平均寿命等指标,用于评估系统的可靠性水平。
可靠性改进措施
1
优化设计
通过改善设计来减少潜在的故障点,提高分析、可靠性预测等工具来预防和诊断故障。
在航空航天工程中,可靠性设计是确保安全和可靠运行的核心要素。
3
电力设备
在电力行业,可靠性设计是保障稳定供电和电网安全的关键。
机械零件的可靠性设计
在机械工程中,可靠性设计至关重要。本演示将介绍可靠性设计的基本原则, 影响因素和评估方法,以及可靠性改进和测试验证的案例研究和实践经验。
机械零件的可靠性设计的意义
1 保证性能
可靠性设计确保机械零件在使用期间保持良好性能,降低故障率,以满足用户需求。
2 成本节约
通过提前识别和解决潜在问题,可靠性设计可以减少维修和更换零件的成本。
可靠性设计的基本原则
设计简化
简化设计可以减少故障点,提 高系统的可靠性。
材料选择
选择适当的材料可以提高零件 的耐用性和抗腐蚀性。
质量控制
严格控制零件生产过程中的质 量,可以降低缺陷率。
机械设计中的可靠性设计与分析方法
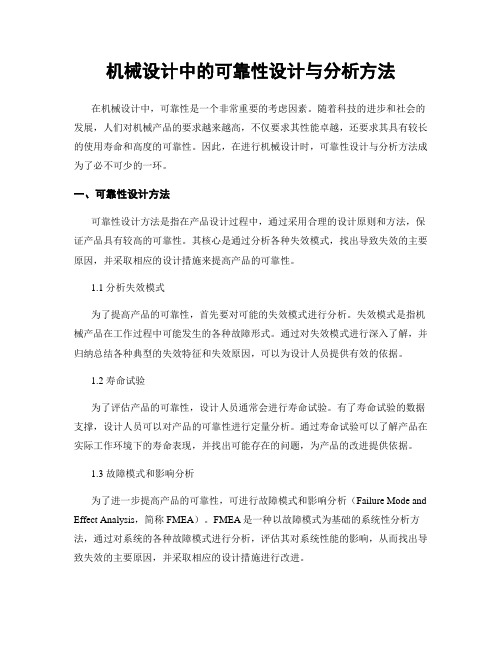
机械设计中的可靠性设计与分析方法在机械设计中,可靠性是一个非常重要的考虑因素。
随着科技的进步和社会的发展,人们对机械产品的要求越来越高,不仅要求其性能卓越,还要求其具有较长的使用寿命和高度的可靠性。
因此,在进行机械设计时,可靠性设计与分析方法成为了必不可少的一环。
一、可靠性设计方法可靠性设计方法是指在产品设计过程中,通过采用合理的设计原则和方法,保证产品具有较高的可靠性。
其核心是通过分析各种失效模式,找出导致失效的主要原因,并采取相应的设计措施来提高产品的可靠性。
1.1 分析失效模式为了提高产品的可靠性,首先要对可能的失效模式进行分析。
失效模式是指机械产品在工作过程中可能发生的各种故障形式。
通过对失效模式进行深入了解,并归纳总结各种典型的失效特征和失效原因,可以为设计人员提供有效的依据。
1.2 寿命试验为了评估产品的可靠性,设计人员通常会进行寿命试验。
有了寿命试验的数据支撑,设计人员可以对产品的可靠性进行定量分析。
通过寿命试验可以了解产品在实际工作环境下的寿命表现,并找出可能存在的问题,为产品的改进提供依据。
1.3 故障模式和影响分析为了进一步提高产品的可靠性,可进行故障模式和影响分析(Failure Mode and Effect Analysis,简称FMEA)。
FMEA是一种以故障模式为基础的系统性分析方法,通过对系统的各种故障模式进行分析,评估其对系统性能的影响,从而找出导致失效的主要原因,并采取相应的设计措施进行改进。
二、可靠性分析方法在机械设计中,可靠性分析方法主要是为了评估设计方案的可靠性,并选择出最佳的设计方案。
2.1 可靠性数学模型可靠性数学模型是一种通过数学方法对产品可靠性进行量化评估的工具。
通过建立合适的可靠性数学模型,可以对产品的失效概率、失效密度、可靠度等进行定量分析,为设计人员提供科学的依据。
2.2 误差拟合法误差拟合法是一种常用的可靠性分析方法。
它通过将实测数据与某一分布函数进行比较,从而找出最佳的分布函数,并利用该分布函数进行概率推断。
机械设计中的可靠性与安全性分析
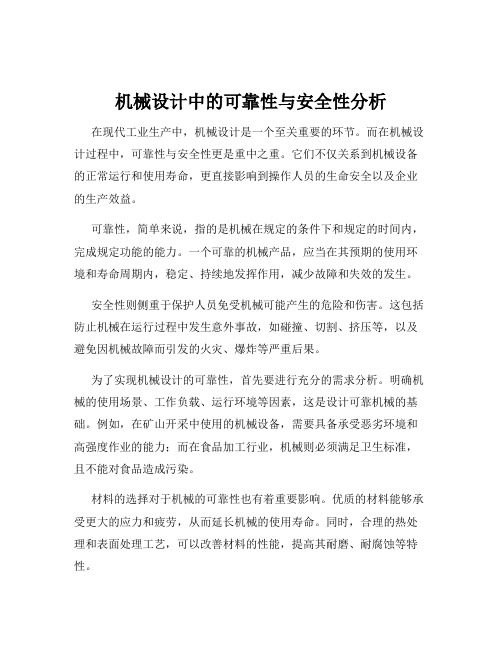
机械设计中的可靠性与安全性分析在现代工业生产中,机械设计是一个至关重要的环节。
而在机械设计过程中,可靠性与安全性更是重中之重。
它们不仅关系到机械设备的正常运行和使用寿命,更直接影响到操作人员的生命安全以及企业的生产效益。
可靠性,简单来说,指的是机械在规定的条件下和规定的时间内,完成规定功能的能力。
一个可靠的机械产品,应当在其预期的使用环境和寿命周期内,稳定、持续地发挥作用,减少故障和失效的发生。
安全性则侧重于保护人员免受机械可能产生的危险和伤害。
这包括防止机械在运行过程中发生意外事故,如碰撞、切割、挤压等,以及避免因机械故障而引发的火灾、爆炸等严重后果。
为了实现机械设计的可靠性,首先要进行充分的需求分析。
明确机械的使用场景、工作负载、运行环境等因素,这是设计可靠机械的基础。
例如,在矿山开采中使用的机械设备,需要具备承受恶劣环境和高强度作业的能力;而在食品加工行业,机械则必须满足卫生标准,且不能对食品造成污染。
材料的选择对于机械的可靠性也有着重要影响。
优质的材料能够承受更大的应力和疲劳,从而延长机械的使用寿命。
同时,合理的热处理和表面处理工艺,可以改善材料的性能,提高其耐磨、耐腐蚀等特性。
在设计过程中,运用先进的设计方法和工具也是必不可少的。
例如,有限元分析可以帮助设计师预测机械结构在不同载荷下的应力分布,从而优化结构设计,减少薄弱环节。
此外,可靠性设计方法,如故障模式与影响分析(FMEA),能够提前识别潜在的故障模式,并采取相应的预防措施。
机械的制造和装配质量同样会影响其可靠性。
严格的制造工艺和质量控制体系,能够确保零件的精度和一致性,从而保证机械的整体性能。
装配过程中的正确操作和调试,能够避免因安装不当而导致的故障。
而对于机械设计的安全性,首要的任务是识别潜在的危险因素。
这需要对机械的工作原理、运动方式、能量传递等进行深入的分析。
比如,旋转部件可能会造成缠绕危险,高压系统可能存在爆炸风险,锋利的边缘可能导致切割伤害。
FMEA在机械设计中的可靠性分析

FMEA在机械设计中的可靠性分析简介在机械设计领域中,可靠性是一个至关重要的指标,决定了产品在使用过程中的稳定性和安全性。
为了评估和提高机械产品的可靠性,工程师们通常会采用FMEA(Failure Mode and Effects Analysis)分析方法。
什么是FMEAFMEA是一种系统性的分析方法,旨在识别产品或系统可能存在的潜在故障模式和故障对系统功能的影响。
通过对潜在故障模式的识别和评估,可以帮助设计团队在设计阶段识别和消除设计缺陷,从而提高产品的可靠性。
FMEA的工作原理FMEA分析通常分为三个关键步骤:识别潜在故障模式、评估潜在故障的影响和严重性、确定并实施改进措施。
在识别潜在故障模式阶段,团队会收集和整理可能的故障模式,包括设备失效、材料损坏、操作错误等。
接着进行评估,根据潜在故障的影响和严重性对它们进行排序,并确定优先处理的故障。
最后,设计团队根据评估结果提出改进和预防措施,避免潜在故障的发生。
FMEA在机械设计中的应用在机械设计中,FMEA的应用可以帮助设计团队避免或减少设计缺陷,降低产品的故障率和维修成本。
通过FMEA分析,设计团队可以识别潜在的故障模式和问题,及早进行改进,确保产品在生产和使用过程中的可靠性和安全性。
例如,在设计一个机械零部件时,可以通过FMEA分析识别可能的故障模式,如材料疲劳、装配不当等,从而改进设计和工艺,提高产品的可靠性。
结论FMEA作为一种重要的分析方法,在机械设计中扮演着关键的角色。
通过FMEA分析,设计团队可以及早发现并解决潜在的故障问题,提高产品的可靠性和安全性。
因此,在机械设计过程中,设计团队应该充分利用FMEA这一工具,从而设计出高质量、可靠性强的机械产品。
机械系统的可靠性分析与设计
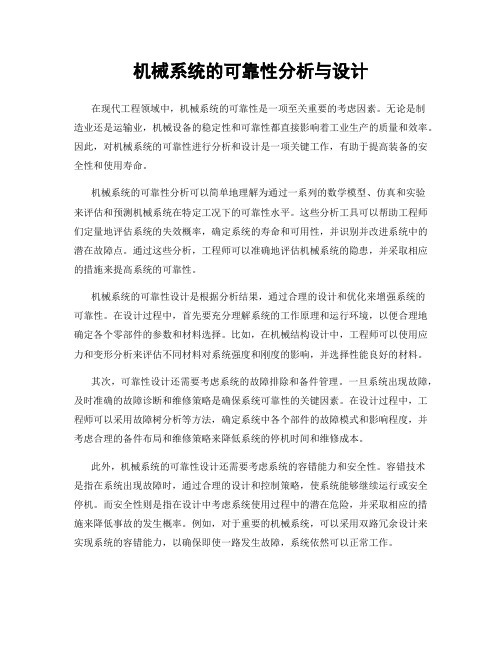
机械系统的可靠性分析与设计在现代工程领域中,机械系统的可靠性是一项至关重要的考虑因素。
无论是制造业还是运输业,机械设备的稳定性和可靠性都直接影响着工业生产的质量和效率。
因此,对机械系统的可靠性进行分析和设计是一项关键工作,有助于提高装备的安全性和使用寿命。
机械系统的可靠性分析可以简单地理解为通过一系列的数学模型、仿真和实验来评估和预测机械系统在特定工况下的可靠性水平。
这些分析工具可以帮助工程师们定量地评估系统的失效概率,确定系统的寿命和可用性,并识别并改进系统中的潜在故障点。
通过这些分析,工程师可以准确地评估机械系统的隐患,并采取相应的措施来提高系统的可靠性。
机械系统的可靠性设计是根据分析结果,通过合理的设计和优化来增强系统的可靠性。
在设计过程中,首先要充分理解系统的工作原理和运行环境,以便合理地确定各个零部件的参数和材料选择。
比如,在机械结构设计中,工程师可以使用应力和变形分析来评估不同材料对系统强度和刚度的影响,并选择性能良好的材料。
其次,可靠性设计还需要考虑系统的故障排除和备件管理。
一旦系统出现故障,及时准确的故障诊断和维修策略是确保系统可靠性的关键因素。
在设计过程中,工程师可以采用故障树分析等方法,确定系统中各个部件的故障模式和影响程度,并考虑合理的备件布局和维修策略来降低系统的停机时间和维修成本。
此外,机械系统的可靠性设计还需要考虑系统的容错能力和安全性。
容错技术是指在系统出现故障时,通过合理的设计和控制策略,使系统能够继续运行或安全停机。
而安全性则是指在设计中考虑系统使用过程中的潜在危险,并采取相应的措施来降低事故的发生概率。
例如,对于重要的机械系统,可以采用双路冗余设计来实现系统的容错能力,以确保即使一路发生故障,系统依然可以正常工作。
总之,机械系统的可靠性分析与设计是确保机械设备安全可靠运行的重要手段。
通过对系统进行综合的可靠性分析,工程师们可以识别系统中的潜在故障点,并采取相应的设计和控制措施来提高系统的可靠性。
机械设计中的材料可靠性分析

机械设计中的材料可靠性分析在机械设计领域中,材料的可靠性是一个至关重要的因素。
材料的可靠性直接影响着机械产品的寿命、性能以及安全性。
因此,进行材料可靠性分析是确保机械产品质量和可持续性发展的关键步骤。
一、材料可靠性的定义和重要性材料可靠性是指材料在使用环境和工作条件下维持其设计寿命和预期性能的能力。
在机械设计中,材料可靠性的分析旨在评估材料在特定条件下的可靠性,并确定任何可能导致材料失效的潜在问题。
其中,材料的失效可能包括疲劳、断裂、变形以及化学腐蚀等。
材料可靠性的重要性不言而喻。
首先,材料的寿命直接关系到机械产品的使用寿命。
在设计阶段,合理评估材料的可靠性可以帮助工程师选择合适的材料,从而提高机械产品的寿命。
其次,材料的性能也对机械产品的性能表现起着至关重要的作用。
通过合理的材料可靠性分析,可以确保材料在工作条件下的稳定性和可靠性,从而提高机械产品的性能。
二、材料可靠性分析的方法1. 材料参数评估在材料可靠性分析中,首先需要评估材料的参数。
这包括强度、硬度、断裂韧性、疲劳寿命等。
通过实验测试或者参考相关文献,获取材料参数的数据,并进行分析和比较,从而确定材料的可靠性。
2. 多因素分析材料的可靠性分析需要考虑多种因素,如工作条件、应力分布、材料的物理化学性质等。
通过建立合适的数学模型,综合考虑这些因素,可以最大程度地准确评估材料的可靠性。
3. 可靠性预测通过在不同工作条件下对材料进行可靠性测试和评估,可以预测材料在实际使用中的可靠性表现。
利用可靠性预测模型,可以预测材料的失效情况,并及时采取相应措施,确保机械产品的安全运行。
三、材料可靠性分析的应用材料可靠性分析在机械设计中有着广泛的应用。
以下是其中的几个典型应用场景:1. 材料选择在机械设计初期,通过对不同材料的可靠性分析,可以帮助工程师选择最合适的材料。
根据工作条件、预期性能和寿命需求等因素,评估不同材料的可靠性,以指导材料的选择和设计方案的确定。
- 1、下载文档前请自行甄别文档内容的完整性,平台不提供额外的编辑、内容补充、找答案等附加服务。
- 2、"仅部分预览"的文档,不可在线预览部分如存在完整性等问题,可反馈申请退款(可完整预览的文档不适用该条件!)。
- 3、如文档侵犯您的权益,请联系客服反馈,我们会尽快为您处理(人工客服工作时间:9:00-18:30)。
2008-6-6
5
中国可靠性网
载荷
载荷类型
轴向载荷——力在作用在零件的轴线上,大小相等,方 向相反,包括轴向拉伸和轴向压缩(表1(a))载荷 在轴向载荷作用下,应力沿横截面的分布式均匀的。 零件上主应力与最大切应力的关系为
针对不同的失效模式确定相应的失效判据,如 最大正应力、最大剪应力、最大变形能、最大 应变、最大磨损量等;
针对不同失效判据,应用相关专业(如材料力 学、弹塑性理论、有限元分析、断裂力学和实 验应力分析等)知识进行应力分析计算;
2008-6-6
26
中国可靠性网
基本随机变量
载荷
机械产品所承受的载荷大都是一种不规则的、不能 重复的随机性载荷 ,例如 自行车因人的体重和道路的情况差别等原因,其 载荷就是随机变量。 飞机的载荷不仅与载重量有关,而且飞机重量、 飞行速度、飞行状态、气象及驾驶员操作有关。
零件的失效通常是由于其所承受的载荷超过了零件 在当时状态下的极限承载能力的结果。
机器在使用过程中超载使用,润滑不良,清洁不 好,腐蚀生锈,表面碰伤,在共振频率下使用,违 反操作规程,出现偶然事故,没有定期维修或维修 不当等,都会造成零件的早期破坏。
2008-6-6
19
中国可靠性网
应力-强度干涉理论
应力-强度干涉模型
在机械产品中,零件(部件)是正常还是失效决定 于强度和应力的关系。 当零件(部件)的强度大于应力时,其能够正常 工作; 当零件(部件)的强度小于应力时,其发生失 效。 因此,要求零件(部件)在规定的条件下和规定 的时间内能够承载,必须满足以下条件
根据以上干涉模型计算在干涉区内强度大于应
力的概率——可靠度。如图4所示,当应力为 时,强度大于应力的概率为
∞
P(S > s0 ) = ∫ f (S )dS
s0
f S (S ) —— 强度分布密度函数
应力s0 处于 ds 区间内的概率为
P⎜⎛ ⎝
s
0
− ds 2
≤s≤
s0
+
ds ⎟⎞ = 2⎠
冶金质量 机械制造工艺缺陷
2008-6-6
18
中国可靠性网
使用维护情况
主要指使用中的环境影响和操作人员和使用维 护的影响
如工作环境中的温度、湿度、沙尘、腐蚀液(气) 等的影响,操作人员的熟练程度和维护保养的好坏 等。
机器的使用和维修状况也是失效分析必须考虑 的一个方面。
贴紧的情况下可以不考虑。
在剪切载荷作用下,力大小沿平行于最小切应力 的横截面上均匀的。
2008-6-6
7
中国可靠性网
载荷
载荷类型
接触载荷——两个零件表面间的接触有点接触、线 接触和面接触。零件受载后在接触部位的正交压缩 载荷称为接触载荷(表1(e)) 例如,滚动轴承工作时,滚子与滚道之间,齿轮 传动中轮齿与轮齿之间的压力都是接触载荷。 在接触载荷作用下,主应力与最大切应力之比是 不定。
环境介质与零件失效 环境温度与零件失效
材料性能与生产情况 使用维护情况
2008-6-6
3
中国可靠性网
基本随机变量
应力、强度定义:
在机械产品中,广义的应力是引起失效的负荷,强 度是抵抗失效的能力。由于影响应力和强度的因素 具有随机性,所以应力和强度具有分散特性。
可靠度的一般表达式
假 事件设,(S因> s此0 ) 两与独⎜⎝⎛ s0立− d2事s ≤ 件s ≤ s同0 +时d2s ⎟⎠⎞发为生两的个概独率立为的随机
∞
dR = f (s0 )ds ⋅ ∫ f (S )dS
因为上式
s0
s0
为应力区间内的任意值,现考虑整
个应力区间内的情况,有强度大于应力的概率
2008-6-6
12
中国可靠性网
图1 交变应力的类型
σ min
σa
σ max σ a σ m
2008-6-6
13
中国可靠性网
设计与几何形状及尺寸
由于制造(加工、装配)误差是随机变量,所 以零、构件的尺寸也是随机变量
设计者仅根据材料的常规性能指标做出决定,而这 些指标根本不能反映材料对所发生的那种类型的失 效的抗力
2008-6-6
14
中国可靠性网
工作环境
环境介质与零件失效
环境介质包括气体、液体、液体金属、射线辐照、 固体磨料和润滑剂等。他们可能引起的零件失效情 况列于表2中。
S > s或S − s > 0
S——零件(部件)的强度; s——零件(部件)的应力。
2008-6-6
20
中国可靠性网
应力-强度干涉模型
实际工程中的应力和强度都是呈分布状态的随机变 量,把应力和强度的分布在同一座标系中表示(如 图3所示)
R(t) = P(S > s) = P(S − s > 0)
2008-6-6
21
中国可靠性网 http://www.kekaБайду номын сангаас
图3 应力-强度干涉模型
f (s)
f (S)
f (s)
f (S)
2008-6-6
22
中国可靠性网
可靠度的一般表达式
载荷
载荷类型
扭转载荷——作用在垂直于零件轴线平面内的力 偶,它使零件发生扭转变形。
在扭转载荷作用下,横截面上切应力的分布规律 是:从表面最大到横截面中心处为零(这里讲的 “中心点”,是指扭转中心轴线与横截面的交点)
剪切载荷——使零件内相邻两截面发生相对错动的 作用力。
表1(d)表示螺栓在连接接合面处受剪切,并与 被连接孔壁互压。螺杆还受弯曲,但在各接合面
机械可靠性设计分析
Mechanical Reliability Design & Analysis
北京航空航天大学工程系统工程系
2008-6-6
1
中国可靠性网
内容提要
基本随机变量 应力-强度干涉理论
应力-强度干涉模型 可靠度的一般表达式
(可靠度)为
∞
⎡∞
⎤
R
=
∫
dR
=
∫
−∞
f
(s)⋅
⎢⎢⎣s∫
f
(S )dS⎥ds
⎥⎦
当已知应力和强度的概率密度函数时,根据以
上表达式即可求得可靠度。
2008-6-6
25
中国可靠性网
应力分布的确定
用FMEA确定需要进行可靠度计算的重要失效 模式,如:静强度断裂、屈服、失稳、变形过 大、疲劳、磨损、腐蚀等 ;
要确定应力和强度的随机特性,首先应了解影响应 力和强度随机性的因素。
影响应力的因素
影响应力的主要因素有所承受的外载荷、结构的几 何形状和尺寸,材料的物理特性等
影响强度的因素
影响强度的主要因素有材料的机械性能、工艺方法 和使用环境等
2008-6-6
4
中国可靠性网
f (s)ds
f s (s) —— 应力分布密度函数;
2008-6-6
23
中国可靠性网
图4 概率密度函数联合积分求可靠度
f (s)
f (S)
f (s)
f (S)
s0
ds
2008-6-6
24
中国可靠性网
最主大应切力应(力σ()τ)= 2
弯曲载荷——垂直于零件轴线的载荷(有时还有力 偶),它使零件产生弯曲变形。 在弯曲载荷作用下,零件横截面上的主应力分布的规 律是:从表面应力最大改变到中性轴线处应力为零。 并且,中性轴线一侧为拉伸应力,另一侧为压缩应 力。
2008-6-6
6
中国可靠性网
当强度的均值大于应力的均值时,在图中阴影部分 表示的应力和强度 “干涉区”内就可能发生强度小于 应力——即失效的情况
这种根据应力和强度干涉情况,计算干涉区内强度 小于应力的概率(失效概率)的模型,称为应力— —强度干涉模型。
在应力——强度干涉模型理论中,根据可靠度的定 义,强度大于应力的概率可表示为
设计方案的合理性和设计考虑因素不周到是零 件失效的重要原因之一。例如:
轴的台阶处直角形过度,过小的内圆角半径,尖锐 的棱边等造成应力集中,这些应力集中处,有可能 成为零件破坏的起源地
对零件的工作条件估计错误,如对工作中可能的过 载估计不足,造成设计的零件的承载能力不够
选材不当是导致失效的另一重要原因
氧化、腐蚀、氢脆、腐蚀疲劳、气 液流冲蚀
液体:Cl—、OH—、NaOH、NO2—、 腐蚀、应力腐蚀、腐蚀疲劳、气蚀
H2S、水-固(砂石)
和泥沙磨损
液体金属:Hg-Cu合金;Cd、Sn、Zn -铜、Pb-铜,Nb、K-不锈钢
液体汞脆、液体金属脆化、合金中 的Ni、Cr元素在液体Pb中发生 选择性溶解,液体金属腐蚀
中子辐照,紫外线照射
磨料:矿石、煤、岩石(润滑 剂)、泥浆、水溶液
造成材料脆化,造成高分子材料老 化
磨粒磨损,腐蚀磨损综合作用
2008-6-6
16
中国可靠性网
图2 与温度有关的零件失效的分析
2008-6-6
17
中国可靠性网
应力分布的确定
确定采用的修正系数对计算的名义应力进行适 当的修正,得到相应应力分量的最大值。常用 的应力修正系数有:应力集中系数、载荷系 数、温度系数、表面处理等;
应力分布的确定 强度分布的确定 用矩法确定应力和强度的分布
一维随机变量 多维随机变量