羊毛纤维的炭化、洗毛与漂白工艺介绍
棉、毛、丝、麻纺纱工艺比较
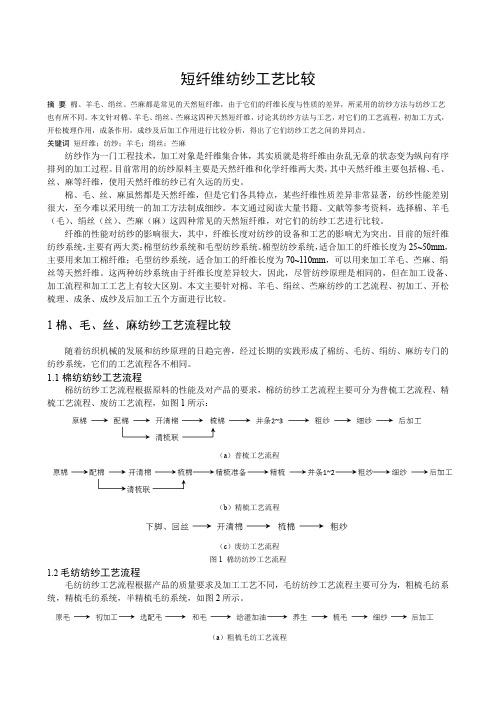
短纤维纺纱工艺比较摘要棉、羊毛、绢丝、苎麻都是常见的天然短纤维,由于它们的纤维长度与性质的差异,所采用的纺纱方法与纺纱工艺也有所不同。
本文针对棉、羊毛、绢丝、苎麻这四种天然短纤维,讨论其纺纱方法与工艺,对它们的工艺流程,初加工方式,开松梳理作用,成条作用,成纱及后加工作用进行比较分析,得出了它们纺纱工艺之间的异同点。
关键词短纤维;纺纱;羊毛;绢丝;苎麻纺纱作为一门工程技术,加工对象是纤维集合体,其实质就是将纤维由杂乱无章的状态变为纵向有序排列的加工过程。
目前常用的纺纱原料主要是天然纤维和化学纤维两大类,其中天然纤维主要包括棉、毛、丝、麻等纤维,使用天然纤维纺纱已有久远的历史。
棉、毛、丝、麻虽然都是天然纤维,但是它们各具特点,某些纤维性质差异非常显著,纺纱性能差别很大,至今难以采用统一的加工方法制成细纱。
本文通过阅读大量书籍、文献等参考资料,选择棉、羊毛(毛)、绢丝(丝)、苎麻(麻)这四种常见的天然短纤维,对它们的纺纱工艺进行比较。
纤维的性能对纺纱的影响很大,其中,纤维长度对纺纱的设备和工艺的影响尤为突出。
目前的短纤维纺纱系统,主要有两大类:棉型纺纱系统和毛型纺纱系统。
棉型纺纱系统,适合加工的纤维长度为25~50mm,主要用来加工棉纤维;毛型纺纱系统,适合加工的纤维长度为70~110mm,可以用来加工羊毛、苎麻、绢丝等天然纤维。
这两种纺纱系统由于纤维长度差异较大,因此,尽管纺纱原理是相同的,但在加工设备、加工流程和加工工艺上有较大区别。
本文主要针对棉、羊毛、绢丝、苎麻纺纱的工艺流程、初加工、开松梳理、成条、成纱及后加工五个方面进行比较。
1棉、毛、丝、麻纺纱工艺流程比较随着纺织机械的发展和纺纱原理的日趋完善,经过长期的实践形成了棉纺、毛纺、绢纺、麻纺专门的纺纱系统,它们的工艺流程各不相同。
1.1棉纺纺纱工艺流程棉纺纺纱工艺流程根据原料的性能及对产品的要求,棉纺纺纱工艺流程主要可分为普梳工艺流程、精梳工艺流程、废纺工艺流程,如图1所示:(a)普梳工艺流程(b)精梳工艺流程(c)废纺工艺流程图1 棉纺纺纱工艺流程1.2毛纺纺纱工艺流程毛纺纺纱工艺流程根据产品的质量要求及加工工艺不同,毛纺纺纱工艺流程主要可分为,粗梳毛纺系统,精梳毛纺系统,半精梳毛纺系统,如图2所示。
染整工艺学复习总略

第一章纺织纤维1.纤维素纤维:对碱的作用比较稳定对酸敏感不耐氧化剂2、蚕丝纤维:不耐碱对弱酸比碱稳定对还原剂的作用是较稳定3、羊毛: 对稀酸特别是弱酸比较稳定很不耐碱不耐氧化剂的作用。
4、粘胶纤维:对碱的稳定性较差对酸和氧化剂更敏感5、涤纶纤维:对弱酸,弱碱和普通氧化性漂白剂等较为稳定对强酸强碱不稳6、锦纶:对碱的稳定性比羊毛,蚕丝要高得多,易被氧化剂破坏,更不耐氯。
7、腈纶:耐较强的酸和弱碱,但不耐强碱,对氧化性漂白剂和还原剂都具有一定的稳定性。
第二章染整用水和染整助剂1、硬水:通常将含有钙、镁盐类的水称为硬水。
软水:钙镁盐类含量低的水称为软水。
软化方法:沉淀法络合法离子交换树脂法2、表面活性剂:以很低浓度就能显著降低溶剂的表面张力或液—液界面张力,改变体系的界面状态,这类物质叫表面活性剂。
表面活性原理:依据“相似者相亲”的规则。
亲水基团使分子有进入水的趋向,而憎水的碳氢长链则有逃出水相的倾向,这两种倾向平衡的结果是表面活性剂在表面富集,亲水基伸向水中,疏水基伸向空气表面活性剂在水表面吸附的结果是水表面似被一层非极性的碳氢链覆盖,从而导致水的表面张力下降。
分类:(一) 按亲水基分类离子型表面活性剂:表面活性剂溶于水,凡是能离解成离子的叫离子型表面活性剂。
非离子型表面活性剂:凡不能离解成离子的叫非离子型表面活性剂。
而离子型表面活性剂,按其在水中生成的表面活性剂离子种类,又可分为阴离子型表面活性剂、阳离子型表面活性剂和两性离子表面活性剂。
此外还有近来发展较快的、既有离子型亲水基又有非离子型亲水基的混合型表面活性剂(1阴离子型:极性基带负电(2、阳离子型:极性基带正电(3、两性型:分子中带有两个亲水基团,一个带正电,一个带负电(4、非离子型:极性基不带电(5混合型:此类表面活性剂分子中带有两种亲水基团,一个带电,一个不带电(二) 按疏水基分类(1 碳氢表面活性剂:疏水基为碳氢基团。
(2、氟表面活性剂:疏水基为全氟化或部分氟化的碳氟链( 3、硅表面活性剂:疏水基为由全甲基化的Si—O—Si、Si—C—Si或Si—Si主干,一般二甲硅烷的聚合物。
羊毛水洗变形的原理

羊毛水洗变形的原理
羊毛水洗变形的原理可以从以下几个方面进行阐述:
一、羊毛纤维的结构与性质
1. 羊毛纤维是一种天然蛋白纤维,主要组分是角质。
2. 羊毛纤维由皮层、角质层和髓部组成。
其中角质层含有大量的角蛋白,而皮层含有脂肪。
3. 羊毛纤维表面覆盖着薄片层,使其具有抗湿、排水及自清洁功能。
二、羊毛与水的相互作用
1. 羊毛纤维吸湿后,水分子会渗入纤维内部,使纤维肿胀。
2. 水分子会破坏羊毛纤维内部的氢键和离子键,使纤维强度下降。
3. 水分子也会溶解和浸透皮层中的油脂成分,破坏纤维表面结构。
4. 长时间浸泡会使羊毛纤维中的可溶性蛋白质溶出,破坏纤维完整性。
三、水洗羊毛的变形机理
1. 水分子在羊毛纤维内部扩散,破坏内部结构,导致纤维强度下降产生皱缩。
2. 水溶性成分的流失也会造成纤维收缩,产生起毛、绉缩等现象。
3. 纤维肿胀使纤维扭曲缠绕,在强烈的水流击打下发生变形。
4. 长时间浸泡会产生往返起毛、严重缠结等问题。
四、防止变形的对策
1. 正确选择水温、水流强度,避免产生磨损。
2. 使用特殊洗涤剂或添加剂,保护纤维表面。
3. 控制浸泡和挤压力度,缩短单批处理时间。
4. 洗后及时脱水,冷却整形,避免起毛固化。
五、总结
水分子与羊毛纤维内外部相互作用,破坏纤维结构,造成各向异性收缩变形。
针对羊毛的特性,优化水洗工艺,可以最大限度避免形变,实现优质洗涤。
3生物酶在羊毛前处理中的研究与应用

3生物酶在羊毛前处理中的研究与应用3.1生物洗毛与去杂(washing wool and removing weed with protease and cellulase)原毛中含有一定量的植物性杂质,如草籽、叶茎、麻屑、麻丝等。
这些杂质会影响纺织加工,产生条干不匀、断头增加、染色不匀等。
目前,毛纺行业生产中,含草杂率经常超标,致使成品毛条降等。
传统加工中去除羊毛中草杂的方法一般采用炭化法和机械法,这两种方法都会不同程度地损伤羊毛纤维。
有报道用纤维索酶、木质素酶等水解酶来代替炭化去除植物性杂质的。
Heine-E[3]等人用木质素过氧化生物酶处理,均发现处理后羊毛并没有受到化学或物理的损伤。
蒋少军等[4]介绍了纤维素酶在洗毛中的应用,结果表明:利用纤维素酶对纤维素的水解作用去除了羊毛中草杂,而且还能提高羊毛的白度,而羊毛的断裂强度、平均长度、短毛率等指标无大变化。
生物去杂是利用酶催化反应高度专一性的特点,加入的酶只促使植物性草杂发生降解,与毛纤维的粘着力下降,理化性质发生变化,最终形成短小的纤维素碎片,从原毛中分离,对羊毛蛋白不起作用,加之处理时温度较低,对羊毛不会造成损伤,再者,酶本身是蛋白质,易生物降解,所以可减轻环境污染。
以杰能科公司的中性纤维素酶IndiAge为例[5],对含草杂的羊毛进行生物浸渍处理的参考工艺:纤维素酶1g/L,PH=5.5-6.5,温度40-45℃,时间40min,浴比1:40。
原毛表面除了含有羊毛脂、羊汗、土杂、草屑污染物外,还存在另一种由细胞碎片和软角质蛋白原生质构成的蛋白质污染物(PCL),其与纤维间存在较强的氢键结合力,它的残存使洗净毛色泽黯沉,采用传统的洗毛方法很难完全去除。
生物洗毛可以去除羊毛表面里层的这些蛋白质污染物,在洗毛工艺中应用蛋白酶,采用二步法洗毛。
前二槽添加渗透剂和合成洗涤剂601洗去羊毛脂、羊汗、土杂,第三槽添加蛋白酶进行生物洗毛,去除洗去蛋白质污染物,提高洗净毛的质量。
退煮漂前处理

影响酶反应速度的因素有:
(1)酶退浆的浓度:淀粉被断裂的速度
几乎与浴中酶的剂量成正比。
(2)退浆的温度:淀粉酶有中温型(过去
多用中温型)和高温型两类,后者可耐95℃ 的高温,浴中短时间能耐更高温度,可以在1 10℃左右进行几十秒钟快速退浆。但必须避 免温度过高,导致活力的降低,适当地提高温 度目的是加速反应,缩短退浆时间,这时我们 允许酶的活力损失10~20%。
酶高温退浆速度极快.酶用量为0.3~3
克/升.在100~115℃处理15~30秒或85~
95℃处理几分钟,即可完成退浆任务。
3.3 氧化剂退浆
本法适用于所有浆料,特别是PVA。不了解 所上浆料的组成的情况下特别适用。它能使多种浆 料氧化分解成可溶性物质而去除。曾经用过的氧化 剂有:
(1)过氧化氢(H2O2): 在氧化退浆法中,被认为最理想的氧化剂是双 氧水和过硫酸盐。双氧水是30~35%或50% 浓度的液体,它对各种类型牌号的PVA都能
❖ 原布准备:检验、翻布(分批、分箱)、打 印和缝头等工作 。
❖ 1.1检验 发现问题,采取措施,保证成品的质量和避 免不必要的损失,同时也可提供纺织厂进一 步改进质量的有关资料。
检验的抽验率,视品种而定。一般品种的抽验率为10%左右;
检验的内容
❖ 包括物理指标和外观疵点。 ❖ 物理指标有长度、幅度、重量、密度和强力
❖ 助剂的其他作用
NaHSO3——防止煮练时纤维素被空气氧化 润湿剂——加快煮练液对织物的润湿和渗透
…
(5) 煮练设备及工艺
①煮布锅煮练
特点:
❖效果最好 ❖绳状、间歇、高温高压 ❖效率低 ❖劳动强度大
煮布锅示意图 工艺:
轧精炼液—进布—加盖—蒸汽排空气—关闭气阀—升温升 压—放出废液—淋洗—出锅
皮毛的工艺

皮毛的工艺
皮毛工艺是指将动物的皮毛进行加工和制作的过程。
主要包括以下几个步骤:
1. 剪羊毛:对于羊毛毛皮来说,首先要进行剃毛。
一般使用剃刀或者电动剪羊机进行剪羊毛的工作。
2. 清洗:清洗是皮毛加工中非常重要的一步,可以去除皮毛中的杂质和污渍。
使用温和的清洁剂和清水进行洗涤,然后进行漂白和染色等处理。
3. 除毛:对于一些不需要毛的部分,如动物的皮肤和内脏,需要进行除毛处理。
常用的方法有化学除毛和物理除毛。
4. 干燥:清洗后的皮毛需要进行干燥处理,以防止变质或者发霉。
可以使用自然晾晒或者机械烘干的方法。
5. 整理:将毛皮整齐地铺平,并进行修整和修剪,使其看起来更加美观。
6. 制作:根据皮毛的用途,将毛皮制作成不同的产品,如服装、毛绒玩具和家居用品等。
需要进行裁剪、缝纫和加工等操作。
7. 护理:对于制作好的皮毛产品,需要进行护理和保养。
可以使用特殊的皮毛护理产品,定期梳理和清洗,以延长其使用寿命。
总之,皮毛工艺需要经过多道工序和繁琐的步骤,其中每一步都需要技术和经验的支持。
同时,皮毛工艺也需要充分尊重和保护动物的生命和权益,遵循合法和道德的原则。
苎麻、毛丝、化学纤维的前处理
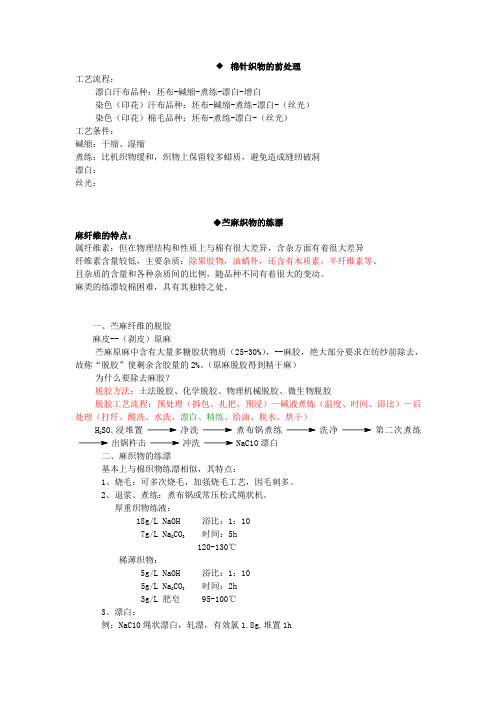
◆棉针织物的前处理工艺流程:漂白汗布品种:坯布-碱缩-煮练-漂白-增白染色(印花)汗布品种:坯布-碱缩-煮练-漂白-(丝光)染色(印花)棉毛品种:坯布-煮练-漂白-(丝光)工艺条件:碱缩:干缩、湿缩煮练:比机织物缓和,织物上保留较多蜡质,避免造成缝纫破洞漂白:丝光:◆苎麻织物的练漂麻纤维的特点:属纤维素:但在物理结构和性质上与棉有很大差异,含杂方面有着很大差异纤维素含量较低,主要杂质:除果胶物,油蜡外,还含有木质素,半纤维素等。
且杂质的含量和各种杂质间的比例,随品种不同有着很大的变动。
麻类的练漂较棉困难,具有其独特之处。
一、苎麻纤维的脱胶麻皮--(剥皮)原麻苎麻原麻中含有大量多糖胶状物质(25-30%),--麻胶,绝大部分要求在纺纱前除去,故称“脱胶”使剩余含胶量的2%。
(原麻脱胶得到精干麻)为什么要除去麻胶?脱胶方法:土法脱胶、化学脱胶、物理机械脱胶、微生物脱胶脱胶工艺流程:预处理(拆包、扎把、预浸)—碱液煮练(温度、时间、浴比)—后处理(打纤、酸洗、水洗、漂白、精练、给油、脱水、烘干)H2SO4浸堆置净洗煮布锅煮练洗净第二次煮练出锅杵击冲洗NaC1O漂白二、麻织物的练漂基本上与棉织物练漂相似,其特点:1、烧毛:可多次烧毛,加强烧毛工艺,因毛刺多。
2、退浆、煮练:煮布锅或常压松式绳状机。
厚重织物练液:18g/L NaOH 浴比:1:107g/L Na2CO3时间:5h120-130℃稀薄织物:5g/L NaOH 浴比:1:105g/L Na2CO3时间:2h3g/L 肥皂 95-100℃3、漂白:例:NaC10绳状漂白,轧漂,有效氯1.8g,堆置1h宜采用平幅加工,减少折痕和漂斑4、半丝光:提高对染料的吸附率为什么进行半丝光?◆羊毛的前处理原毛含有大量杂质:天然杂质:羊脂羊汗附加杂质:植物性杂质、尘土、色素原毛纺织前经洗毛、炭化、漂白等工序毛条、纱线或织物在染色前,洗呢一、洗毛(精练):洗毛的目的?1、杂质特点:羊脂:高级脂肪酸和胆固醇结合而成的酯及少量游离醇脂肪酸。
纺织工艺学 -----毛纺

纺织工艺学——毛纺简介纺织工艺学是研究纺织品的制造和加工过程的学科。
毛纺是纺织工艺学中的一个重要分支,主要研究以动物毛纤维为原料制造的纺织品的加工和制造工艺。
本文将介绍毛纺的基本概念、工艺流程、常见问题及解决方法。
毛纺是以动物毛纤维为原料,经过纺纱、织造、整理等工艺加工,制成各类毛织品。
动物毛纤维通常分为长纤维和短纤维两种。
•长纤维毛:如羊毛、兔毛等,纤维长度在5cm以上。
•短纤维毛:如马海毛、山羊绒等,纤维长度一般在2-5cm之间。
根据动物毛纺织品的用途和所需的性能,可以选择不同的纺纱方法和纺纱工艺。
毛纺的工艺流程一般包括纺纱、织造和整理三个环节。
1. 纺纱纺纱是将原料的动物毛纤维进行纺纱处理,制成纱线。
纺纱的主要工艺包括:1.清洗:将动物毛纤维进行清洗,去除其中的杂质。
清洗方法有机械清洗和化学洗涤两种。
2.进料:将清洗后的毛纤维送入纺纱机进行进料处理。
3.梳理:使用梳理机将毛纤维进行梳理,使其朝向一致,排列整齐。
4.牵伸:将梳理后的毛纤维进行牵伸,增加纤维的拉力和延伸性。
5.精梳:将牵伸后的毛纤维进行精梳处理,去除其中的短纤维和杂质。
6.粗纺:将精梳后的毛纤维进行粗纺,形成粗纱。
7.细纺:将粗纱进行细纺,形成细纱。
8.卷绕:将细纱卷绕成纺筒,方便储存和运输。
2. 织造织造是将纺纱后的纱线进行织造,制成毛纺织品。
织造的主要工艺包括:1.上机:将纱筒装入织机的纱框中,根据设计要求选择合适的织机和编织图案。
2.织造:通过织机的运转,将纱线织成织物。
织造过程中需要注意纱线的张力和密度,以确保织物的质量和纹理。
3.下机:将织造好的织物从织机上取下,并进行修整和整理。
3. 整理整理是对织物进行后续处理,使其具有所需的手感、光泽和外观效果。
整理的主要工艺包括:1.起毛:通过机械或化学方法使织物表面生成绒毛,增加手感和保暖性。
2.整经、整经:调整织物的纬纱和经纱的密度和张力,使其平整。
3.缩水:通过热水或蒸汽处理,使织物收缩,提升织物的弹性和柔软度。
- 1、下载文档前请自行甄别文档内容的完整性,平台不提供额外的编辑、内容补充、找答案等附加服务。
- 2、"仅部分预览"的文档,不可在线预览部分如存在完整性等问题,可反馈申请退款(可完整预览的文档不适用该条件!)。
- 3、如文档侵犯您的权益,请联系客服反馈,我们会尽快为您处理(人工客服工作时间:9:00-18:30)。
羊毛纤维的炭化、洗毛与漂白工艺介绍
Book Jims 新西兰羊毛局
原毛纺织前需先初步加工成为洗净毛。
加工时先通过选毛,使羊毛品质趋于均匀,再通过开毛打土,使羊毛蓬松,以提高洗涤效果。
然后进行洗毛,使羊毛脂形成稳定的乳化液,污浊杂质则浮在洗涤液中,经处理后可获得含水约40%的湿毛,再予以烘干。
生产中多利用联合机连续操作一次获得洗净毛,最后进入毛条制造工序。
1.羊毛炭化
羊毛炭化指的是针对羊毛上植物性草杂用硫酸腐蚀、烤焦、以致脱落分离的工艺。
炭化工艺中最重要的是减少羊毛损伤的前提下获得提高产率和白而松散的炭化毛。
1977年时,用3.5%(66°Be′硫酸),35%的轧酸液率,产率每小时80kg,碳化毛损伤达20%-30%,实现高产优质,采用浓酸快速工艺势所必然。
浓酸快速工艺的实施,关键在于表面活性剂的使用。
若能做到羊毛吸水时不优先吸酸,而高温焙烘时羊毛所结合的酸尽量的减少,则羊毛损伤就大为减少。
笔者认为,用带有弱阳荷性的非离子剂封闭住羊毛的基团,则浸酸后的羊毛吸酸量大为减少,最多可减少三分之二的吸酸。
使用表面活性剂有两个问题待解决,分别是:第一,传统非离子剂疏水的碳氢疏水链太短,其对羊毛亲和力不够大,必须用扩链剂扩大分子量,以增加其对羊毛的亲和力。
本文发现如用多乙烯多胺与C5-C6脂肪二羧酸先生成聚酰胺,然后用,如二甲基氨丙基胺等的扩链剂扩链,最后接上环氧基(环氧化试剂包括环氧氯丙烷,环氧溴丙烷,溴化环氧丁烷,氯化环氧已烷等)。
可以达到羊毛吸酸量减少80%的效果。
相比之下如下产品的效果都不能与之相比,如环氧化双六乙烯二胺,聚丙烯酸、双氰胺-双酰胺氨塑树脂(不环保),接上环氧氯丙烷的聚酰胺Hercosett125树脂(可能分子量太大)。
第二缺点是羊毛的炭化温度在在100℃-115℃的高温下条件,必须要选择在如此高的温度条件下稳定的表面活性剂。
有效的阴离子剂有二丁基萘磺酸钠,十二烷基苯磺酸钠,但是更为疏水一点的二异丁基萘磺酸钠,二异戊萘基磺酸钠更为有效。
虽然在水中溶解度低。
用三乙二醇丁醚增溶复配效果很好,适合作炭化羊毛保护剂。
在浸酸的前一槽助剂配比是:1%环氧扩链聚酰胺0.6%
二异丁基萘磺酸钠(含10%三缩乙二醇丁醚),应用8%(66°Be′硫酸)液,轧液率35%,产量为250-300kg/小时,羊毛烘干时含酸率不会高于1%,草籽炭化率符合质量标准,羊毛白度,松散度显著提高,用于纺纱牵伸效率提高,千锭时断头率减少40%,回丝减少了30%,毛纱强力提高了15%,毛纱乌斯脱不均匀减少了9%;此炭化毛染色时,染料对炭化毛上色率明显增加,而传统炭化毛吸酸不匀而造成尖染夹花现象消失。
此工艺目前处于国内外领先。
2.羊毛洗涤
传统的羊毛洗涤,洗毛的温度50℃-60℃碱性洗毛,用碳酸钠调PH 8.5-9.5,添加净洗剂的方法,对羊毛损伤大,手感差。
为了减少损伤后来采用中性洗毛法,温度没变只是PH 6.0-7.0,选用的阴离子洗剂主要有:对甲氧基脂肪胺苯磺酸钠,烷基苯磺酸钠等,为了提高洗净效果,往往加入硫酸钠,氯化钠,多磷酸钠等电介质,电介质加多了会使羊毛弹性降低,影响质量。
另一方面阴离子表面活性剂去油污效果差,需要复配非离子表面活性剂,这种阴、非离子复配型的表面活性剂所洗出的羊毛其白度、手感、松散度均属于中挡水平。
尤其是大多数国产的羊毛。
对付脂肪钙、镁皂即使添加了螯合剂EDTA(乙二胺四乙酸)及其钠盐再加上非离子剂洗液也不能洗掉。
原因是脂肪钙镁皂与螯合剂EDTA形成了凝胶粘沾在羊毛上。
只有使凝胶充分消散的情况下,才能彻底去除,一种方法是将EDTA钠盐改用胺盐:如EDTA-MEA(单乙醇胺盐)、EDTA-EN(乙烯二胺盐)、EDTA-NTA(氮川三醋酸盐)。
上述改良了的胺盐螯合剂虽然可有效消散脂肪钙、镁皂凝胶,但是对洗涤作用没有协和增溶的作用,更不能去有效洁净羊毛上粘土性污垢。
这就需要设计一种对粘土污垢和脂肪钙、镁皂(通常钙:镁比为4:1-3:1的复合皂)能协和增溶的表面活性剂复配处方。
带阳离子的聚胺与阴离子表面活性剂和超支链分散剂拼合下,可以不发生沉淀有效地增溶包埋粘土污垢和脂肪钙、镁皂而生成溶胶,并将溶胶从羊毛上剥离下来并稳定地悬浮在洗液中,不会再向羊毛上沉积,最终显著提高了洗净毛的白度和松散度。
这三类表面活性剂如下。
(1)聚胺类增溶分散剂是平均分子量为600的聚乙烯亚胺(PEI)接环氧乙烷,用甲基亚磺酸中和,再用硫酸二甲酯季铵化,最后用氯磺酸磺化的产品较为适合的亚胺是4.9二氧-1,12十二烷二胺(DODD)(EO)20和双(六亚甲基)三胺(EO)20季铵化后再硫酸化的产品。
(2)具有强力分散作用的表面活性剂也是解决污垢二次沉淀羊毛纤维的方法,这些分散性能好的表面活性剂诸如C12- C14烷基醇(EO)1.0-7.0硫酸盐,异构醇C13的聚氧乙烯醚,
高碳链的脂肪酸甲酯乙氧基化物FMEE及其衍生物等。
这类助剂耐氧化、硬水、电介质、
有好的润湿渗透和除油污效果,可与任何离子表面活性剂相容,其疏水部分能对粘土性污垢,及脂肪钙,镁皂有一定的锚固能力,并通过其亲水基因增溶分散于洗液中。
(3)超支链超级分散剂:超级分散剂种类很多,本文主要选择超支链化的超级分散剂。
虽然
超支链化的聚合物,并不是每一个重复单位内都有支链连接上,但这种结构上的不规正,无
碍于我们净洗去污的要求。
羊毛织物的清洗中,如若基质上含有茶渍或洒渍等相对较为亲水的污渍则在洗涤配方中
还得加上如下的组合剂:用C8-C16((EO)1.5-(EO)7.0)醋酸盐,其中尤以碳链短的去除
污渍更为明显,如C9-C11(EO)2.5醋酸盐与N甲基N十二烷基二缩乙二醇醋酸酯季胺盐
氯化物,此双组份以1.0:1.0的比例复配到整个净洗配方之中,占整个助剂重量的2.0-15.0% o.w.f.此工艺目前处于国内外领先。
3.有色羊毛的漂白
上世纪末,漂白是利用亚铁离子对羊毛色素和蛋白角质的亲合力差异,先将亚铁离子预
先媒染于羊毛的含色素部位,交替用热水将亚铁离子在羊毛不含色素的部位上冲洗下来。
这
样可以减少重金属对羊毛的催化损伤。
其方法和步骤一直延用至今。
(1)亚铁催化剂媒染的方法
硫酸亚铁(含六份结晶水)10g/L
亚磷酸(50%) 1-2g/L
甲酸调PH值至3.0-3.5
羟甲基咪唑啉衍生物(羊毛保护剂)3%,owf
于80℃处理60分钟。
→温水冲洗:40℃水冲洗5分钟,放去脚水
→还原冲洗:
BLANKIT IN(BASF) 0.15g/L
还原剂TD 0.3g/L
用氨水调PH 8.0
上述液于80℃冲10分钟,放去脚水→热水冲洗:80℃,冲洗10分钟,放去脚水。
→氧化漂白工艺:
过氧化氢(37%)10ml/L,焦磷酸钾10g/L,将PH调至8.0-8.5,于75℃漂45分钟-180分钟(视色素深浅)。
上述工艺时间长、能耗大、最大的问题在于脱色的羊毛,再经染色等处理纤维强力很差。
为了减少羊毛损伤和节能,本文新开发的尿黄毛脱色工艺如下:
→氧化漂白工艺:
过氧化氢(37%)10-20ml/L
层状硅酸钠0.5-1.0g/L
PH调至9.0-10.0
漂白活化剂(1) 0.5-3% o. w. f
羊毛保护剂(2) 2-5% o.w.f
螯合分散剂(3) 1g/L
氧漂于40℃,漂60分钟,然后加1g/L脱过氧化氢酶去除多余的自由基氧。
(5分钟)。