氰化尾渣还原焙烧酸浸提铁及氰化浸金新工艺_郑雅杰
陕西某黄金冶炼厂焙烧氰化浸渣提金方法研究报告

陕西某黄金冶炼厂焙烧氰化浸渣提金方法研究报告本文研究了陕西某黄金冶炼厂焙烧氰化浸渣提金方法,分析了该方法的优缺点,并从工艺流程、操作技术、设备应用等方面对该方法进行了详细阐述。
一、工艺流程本研究采用的焙烧氰化浸渣提金方法主要由以下几个步骤组成:1. 氰化浸渣焙烧:将氰化浸渣送入焙炉中进行高温处理,使其得到充分焙烧,达到剥离金属的效果。
2. 氰化浸渣破碎:将焙烧后的氰化浸渣进行破碎,得到较小的颗粒状物料。
3. 搅拌:将破碎后的氰化浸渣与水一起搅拌,使其形成悬浮液。
4. 沉淀:将悬浮液静置一段时间,使其沉淀,得到含金泥浆。
5. 过滤:将含金泥浆进行过滤,去除杂质。
6. 洗涤:将过滤后的含金泥浆用水进行洗涤,使其去除残留杂质。
7. 烘干:将洗涤后的含金泥浆放入焙炉中进行烘干,得到金粉末。
二、操作技术1. 焙烧操作温度的选择:在本研究中,焙烧时采用了950℃的高温,能够使氰化浸渣得到充分焙烧,并且可以保证金属与其他杂质迅速分解。
2. 破碎操作:在氰化浸渣破碎时,应采用适当的粉碎机,能够将氰化浸渣破碎成较小的颗粒状物料。
3. 悬浮液搅拌操作:搅拌时间和强度应根据浸出效果进行调整。
4. 沉淀时间的选择:沉淀时间应根据泥浆中悬浮颗粒的大小、颗粒浓度等因素进行调整。
5. 过滤操作:过滤应选用细孔滤纸,过滤时应逐渐加压。
三、设备应用本研究采用了较新的设备,包括高温焙炉、永磁搅拌器、温度控制系统等。
这些设备的应用,不仅能够提高提金效率,而且能够保证产品质量。
四、优缺点分析本研究采用的焙烧氰化浸渣提金方法具有以下优点:1. 提金效率高:在保证产品质量的前提下,可以达到较高的提金效率。
2. 工艺流程简单:焙烧氰化浸渣提金方法的工艺流程相对简单,易于操作。
3. 环保性好:焙烧氰化浸渣提金方法的环保性好,能够减少对环境的影响。
但该方法也存在一些缺点,主要包括:1. 能源消耗大:焙烧氰化浸渣需要较高的温度,因此消耗的能源较大。
福建某氰化尾渣综合利用试验研究

福建某氰化尾渣综合利用试验研究
肖坤明;谢文清;郑新烟;黎志泉
【期刊名称】《矿产综合利用》
【年(卷),期】2013(000)005
【摘要】针对福建某氰化尾渣,采用浮选、焙烧、浸出、磁选进行金、铁以及硫的回收利用.试验先进行黄铁矿的浮选,得到的硫精矿品位为8.63%,回收率为86.97%,其中含金5.26g/t,金回收率为74.59%.然后对硫精矿进行焙烧制硫酸,硫总回收率为85.80%.对烧渣进行还原焙烧后进行浸金,金浸出率为95.49%.对浸出后的浸渣进行弱磁磁选,得到品位为61.56%的铁精矿,铁总回收率为73.15%.有效的回收利用了氰化尾渣中的有价元素.
【总页数】4页(P72-75)
【作者】肖坤明;谢文清;郑新烟;黎志泉
【作者单位】福建省双旗山矿业有限责任公司,福建德化362500;福建省双旗山矿业有限责任公司,福建德化362500;福建省双旗山矿业有限责任公司,福建德化362500;福建省双旗山矿业有限责任公司,福建德化362500
【正文语种】中文
【中图分类】TD982
【相关文献】
1.某焙烧氰化尾渣综合利用试验研究 [J], 谢建宏;张崇辉;李慧;刘思伟;王素
2.浅析氰化尾渣资源化综合利用及污染防治措施 [J], 刘栎灵
3.某氰化尾渣资源综合利用示范工程的总图布置研究 [J], 易世友
4.氰化尾渣的综合利用 [J], 张永东
5.焙烧氰化尾渣综合利用与新工艺探讨 [J], 党晓娥;刘安全
因版权原因,仅展示原文概要,查看原文内容请购买。
某氰化尾渣直接还原焙烧——磁选选铁试验

某氰化尾渣直接还原焙烧——磁选选铁试验刘娜;孙体昌;刘真真;蒋曼【摘要】对铁品位高达48.05%的某氰化尾渣进行了直接还原焙烧磁选试验研究.结果表明,在烟煤2用量为20%,还原温度为1 150℃,还原时间为40 min,还原产物磨矿细度为-0.074 mm占78%,1次弱磁选磁场强度为87.56 kA/m情况下获得了铁品位为94.11%、回收率为90.14%的还原铁粉.该工艺不仅高效地富集了铁,而且使硫等含量较高的有害成分富集到了尾矿中.%Experimental research on eyanided tailings containing 48. 05% grade of iron by the process of direct reduction roast-magnetic separation tests was carried out. The results indicated that under the condition of roasting at 1 150 ℃ for 40 min with 20% bituminous coal 2,and grinding fineness of -0. 074 mm 78% and magnetic intensity,the DRI with Fe grade of 94. 11% and recovery of 90. 14% was obtained by the process of one roughing low intensity magnetic separation with intensity of 87. 56 kA/m. In the process,iron was concentrated efficiently,meanwhile high content of harmful ingredients , sulfur are enriched into tailings.【期刊名称】《金属矿山》【年(卷),期】2012(000)011【总页数】3页(P145-147)【关键词】氰化尾渣;直接还原焙烧;磁选;还原铁粉【作者】刘娜;孙体昌;刘真真;蒋曼【作者单位】北京科技大学土木与环境工程学院;北京科技大学土木与环境工程学院;北京科技大学土木与环境工程学院;北京科技大学土木与环境工程学院【正文语种】中文氰化尾渣是目前黄金冶炼行业的主要固体废弃物,其化学成分大多比较复杂,通常富含 Au、Ag、Cu、Fe、Pb、Zn、Sb 等金属元素,是宝贵的二次资源。
氰化尾渣还原焙烧酸浸提铁及氰化浸金新工艺_郑雅杰
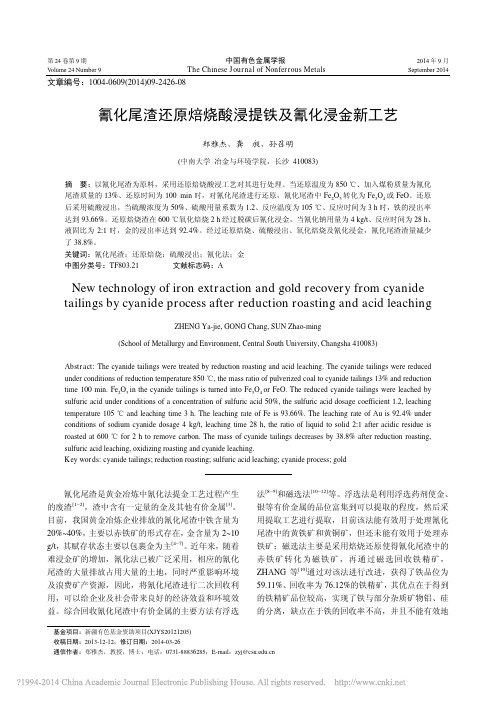
38.4 28.73 18.61 5.08 1.71 1.35 1.34 1.24 0.886 0.209 2.445
由表 1 可知,氰化尾渣中含量较多的元素为 O、 Fe、Si 和 Al,还含有一定量的 As 和 Cu。 对氰化尾渣中铁的物相进行分析,结果表明矿样 中铁主要以两种形式产出: 一是赋存在磁性铁矿物(包 括磁铁矿和假象赤铁矿)中,其分布率为 13.87%;二 是呈高价氧化铁存在于赤 ( 褐 ) 铁矿中,所占比例为 83.18%。对氰化尾渣进行扫描电镜分析,其结果如图 1 所示。 由图 1 可知,部分微细粒赤铁矿(H)呈单体产出, 其余部分则以各种形式与脉石镶嵌构成不同比例的连 生体,相互之间的接触界线多呈不平直的锯齿状或港 湾状,少数可呈浸染状包裹在脉石中而构成较为复杂 的交生关系,图 1(a)显示部分赤铁矿(H)呈单体产出, 部分沿脉石(G)边缘嵌布;图 1(b)显示不规则状脉石 (G)沿赤铁矿(H)边缘毗连镶嵌;图 1(c)显示不规则状 赤铁矿(H)与脉石(G)镶嵌, 构成极为复杂的交生关系。 煤粉为无烟煤,使用前先经干燥、磨细后通过孔 径为 0.55 mm 的筛子,其成分分析结果如表 2 所列。 由表 2 可知,该无烟煤灰分含量为 8.3%,挥发分
2427
分离铁相中包裹的金,使得这部分金很难被回收。 本文作者通过还原焙烧酸浸工艺对氰化尾渣进行 处理,有效地浸出了氰化尾渣中的有价金属铁,铁的 浸出率达到 93.66%, 得到的硫酸铁酸浸液可用于制取 氧化铁红、聚合硫酸铁、绿矾和铁黄等[13−18]。采用该 工艺能使氰化尾渣中的金得到充分解离,采用常规氰 化法处理酸浸后渣,金的浸出率达到 92.4%。经过上 述处理后,氰化尾渣的质量减少了 38.8%,为氰化尾 渣中有价金属的综合回收利用及减少氰化尾渣的排放 提供了一条可行途径。
氰化渣综合回收铁、金的工艺研究

氰化渣综合回收铁、金的工艺研究随着我国黄金产业的不断发展,每年相继伴随着大量氰化渣的产生。
这些氰化渣综合回收利用率低,不仅占用大量耕地,而且严重污染环境。
由于这些氰化渣中含有大量可综合回收利用的有价金属,但至今,并未有合理有效的方法将其综合回收利用,因此,寻找一种合理有效的方法综合回收冶金工业废渣中的有价金属显得十分迫切,具有相当可观的经济效益和社会环境效益。
本文以山东招远某氰化渣为研究对象,在系统研究其工艺矿物学特性的基础上,提出了“复合添加剂还原焙烧-水浸-磁选”的新工艺来回收氰化渣中的铁,并利用硫脲法来回收尾渣中的金。
本研究主要包括两大部分:(1)复合添加剂还原焙烧-水浸-磁选法回收氰化渣中铁的工艺研究。
实验过程中研究了还原焙烧温度、焙烧时间、活性炭用量、复合添加剂用量、水浸温度、水浸时间、水浸液固比、激磁电流强度等条件对氰化渣中铁回收的影响,获得了最佳的实验条件:在原矿细磨至粒度小于74μm占85%,焙烧温度750℃,焙烧保温时间60min,氰化渣:活性炭粉:硫酸钠:碳酸钠(重量百分比)=l00:10:10:3,转速20r/min,水浸温度60℃,水浸时间5min,水浸液固比为15:1以及激磁电流为2A的条件下,可获得铁品位59.11%,回收率75.12%的铁精矿,产品基本满足工业生产的要求。
(2)硫脲法回收尾渣中金的工艺研究。
实验过程中研究了硫脲浓度、pH值、浸金液固比、浸出时间对尾渣中金回收的影响,获得了最佳的实验条件:当浸出液固比3:1,浸出温度60℃,浸出时间6h,pH值1-1.5,硫脲浓度2kg/t时,可获得最佳金的浸出率为82.30%。
本文还利用X射线衍射(XRD)、扫描电镜(SEM)、能谱面扫描(EDS)、X射线荧光(xRF)等现代分析测试手段对氰化渣铁回收工艺过程中的物相变化进行分析,表征了还原焙烧-水浸-磁选过程中各主要物相的变化规律:在水浸过程中,经复合添加剂还原焙烧所产生的可溶性物质经水浸后被洗除,而不溶性的非磁性物质经磁选后随之进入非磁性物质,部分的杂质铝、硅矿物等经水浸后被去除,还有部分进入非磁性物质,复合添加剂焙烧只能改变矿物的物相特征,但是通过水浸过程才能有效的实现铁与杂质矿物之间的有效分离,使铁的品位和回收率有所提高。
焙烧氰化尾渣中有价金属梯级分离回收工艺

焙烧氰化尾渣中有价金属梯级分离回收工艺
王建军;郭建东;欧海涛;薛希刚
【期刊名称】《有色金属工程》
【年(卷),期】2024(14)3
【摘要】梯级分离回收焙烧氰化尾渣中的有价金属,对提高资源综合利用率、消解氰化尾渣危废对冶金行业持续发展具有重要意义。
以焙烧氰化尾渣为原料,采用一级酸浸浸取金铜锌、二级还原焙烧—磁选回收含金铁精矿、三级浮选回收金的梯级分离回收工艺方法,焙烧氰化尾渣中的金、铜、锌、铁的综合回收率分别达到63.07%、80.5%、70.31%、80.64%。
该技术方法能够有效解决焙烧氰化尾渣中金、铜、锌、铁的综合回收技术难题,实现了焙烧氰化尾渣的高值化、资源化利用,同时将焙烧氰化危废转化为二次高价值资源,解决了焙烧氰化危废无害化处置的冶金行业共性技术难题。
【总页数】8页(P90-97)
【作者】王建军;郭建东;欧海涛;薛希刚
【作者单位】山东国大黄金股份有限公司
【正文语种】中文
【中图分类】TF831;TD953
【相关文献】
1.焙烧氰化尾渣有价金属回收试验研究
2.氰化尾渣氯化焙烧回收有价金属的试验研究
3.焙烧氰化尾渣回收有价金属试验
4.氰化尾渣中有价元素回收现状与展望
5.氰化尾渣中有价元素回收及未来发展
因版权原因,仅展示原文概要,查看原文内容请购买。
- 1、下载文档前请自行甄别文档内容的完整性,平台不提供额外的编辑、内容补充、找答案等附加服务。
- 2、"仅部分预览"的文档,不可在线预览部分如存在完整性等问题,可反馈申请退款(可完整预览的文档不适用该条件!)。
- 3、如文档侵犯您的权益,请联系客服反馈,我们会尽快为您处理(人工客服工作时间:9:00-18:30)。
2 结果与讨论
2.1 还原温度对铁浸出率的影响 有研究表明,Fe3O4 与硫酸反应的活性高于 Fe2O3 与硫酸反应的活性
[19−20]
图3
分层装料示意图
,为了提高铁的浸出率,采用
Fig. 3 Schematic diagram of layer filling
煤粉还原氰化尾渣后硫酸浸出,煤粉还原铁氧化物为 间接还原反应, 采用分层方式有利于 Fe2O3 的还原[21]。 取 200 g 氰化尾渣与占其质量 20%的煤粉(40 g) 以分层装料方式装入刚玉坩埚中焙烧 70 min,冷却后 进 行 硫酸 浸出 , 硫酸 浸出 条 件如 下: 反 应温 度为 105 ℃,反应时间为 3 h,硫酸用量系数为 1.2,硫酸 浓度为 50%。分层装料方式示意图如图 3 所示,温度 对 Fe2+及总铁浸出率的影响如图 4 所示,还原产物 由图 4 可知,Fe2+浸出率及总铁浸出率均随着温 度的升高而增大,说明温度升高有利于还原反应的进 行,当温度从 650 ℃升高到 700 ℃时,总铁浸出率由 65.9% 增加到 81.03% ,Fe 2+ 浸出率由 17.6% 增加到 26.1% 。继续升高温度至 850 ℃时,总铁浸出率为 82.1%,增长幅度较小,Fe 浸出率为 67.3%。通过计
Fig. 1 SEM images of cyanide tailings (H—Hematite; G— Gangue): (a) Evenly dispersed solids; (b) Single block solid; (c) Single cellular solids 表2 无烟煤工业分析结果 Analysis results of industrial anthracite (mass Vdaf 11.1 C 80.6
1.3
分析方法 采用电感耦合等离子光谱仪(Intrepid Ⅱ XSP)分
算可知,硫酸浸出 Fe3O4 后浸出液中 Fe2+与总铁的物 质的量的比为 1:3, 当还原温度为 850 ℃时, 酸浸液中 Fe2+与总铁物质的量的比超过 1:3,说明 Fe2O3 还原为 Fe3O4 后,又进一步还原为 FeO。因此,适宜的还原温 度为 700 ℃, 此时, Fe2+和总铁的浸出率分别为 26.66% 和 81.03%。同样条件下,不经过还原反应,硫酸直接 酸浸氰化尾渣, 总铁浸出率仅为 46%, 这是由于 Fe2O3
38.4 28.73 18.61 5.08 1.71 1.35 1.34 1.24 0.886 0.209 2.445
由表 1 可知,氰化尾渣中含量较多的元素为 O、 Fe、Si 和 Al,还含有一定量的 As 和 Cu。 对氰化尾渣中铁的物相进行分析,结果表明矿样 中铁主要以两种形式产出: 一是赋存在磁性铁矿物(包 括磁铁矿和假象赤铁矿)中,其分布率为 13.87%;二 是呈高价氧化铁存在于赤 ( 褐 ) 铁矿中,所占比例为 83.18%。对氰化尾渣进行扫描电镜分析,其结果如图 1 所示。 由图 1 可知,部分微细粒赤铁矿(H)呈单体产出, 其余部分则以各种形式与脉石镶嵌构成不同比例的连 生体,相互之间的接触界线多呈不平直的锯齿状或港 湾状,少数可呈浸染状包裹在脉石中而构成较为复杂 的交生关系,图 1(a)显示部分赤铁矿(H)呈单体产出, 部分沿脉石(G)边缘嵌布;图 1(b)显示不规则状脉石 (G)沿赤铁矿(H)边缘毗连镶嵌;图 1(c)显示不规则状 赤铁矿(H)与脉石(G)镶嵌, 构成极为复杂的交生关系。 煤粉为无烟煤,使用前先经干燥、磨细后通过孔 径为 0.55 mm 的筛子,其成分分析结果如表 2 所列。 由表 2 可知,该无烟煤灰分含量为 8.3%,挥发分
New technology of iron extraction and gold recovery from cyanide tailings by cyanide process after reduction roasting and acid leaching
ZHENG Ya-jie, GONG Chang, SUN Zhao-ming (School of Metallurgy and Environment, Central South University, Changsha 410083) Abstract: The cyanide tailings were treated by reduction roasting and acid leaching. The cyanide tailings were reduced under conditions of reduction temperature 850 ℃, the mass ratio of pulverized coal to cyanide tailings 13% and reduction time 100 min. Fe2O3 in the cyanide tailings is turned into Fe3O4 or FeO. The reduced cyanide tailings were leached by sulfuric acid under conditions of a concentration of sulfuric acid 50%, the sulfuric acid dosage coefficient 1.2, leaching temperature 105 ℃ and leaching time 3 h. The leaching rate of Fe is 93.66%. The leaching rate of Au is 92.4% under conditions of sodium cyanide dosage 4 kg/t, leaching time 28 h, the ratio of liquid to solid 2:1 after acidic residue is roasted at 600 ℃ for 2 h to remove carbon. The mass of cyanide tailings decreases by 38.8% after reduction roasting, sulfuric acid leaching, oxidizing roasting and cyanide leaching. Key words: cyanide tailings; reduction roasting; sulfuric acid leaching; cyanide process; gold
氰化尾渣是黄金冶炼中氰化法提金工艺过程产生 的废渣
[1−2]
法[8−9]和磁选法[10−12]等。浮选法是利用浮选药剂使金、 银等有价金属的品位富集到可以提取的程度,然后采 用提取工艺进行提取,目前该法能有效用于处理氰化 尾渣中的黄铁矿和黄铜矿,但还未能有效用于处理赤 铁矿;磁选法主要是采用焙烧还原使得氰化尾渣中的 赤 铁 矿转 化为 磁 铁矿 ,再 通 过磁 选回 收 铁精 矿, ZHANG 等[10]通过对该法进行改进,获得了铁品位为 59.11%、回收率为 76.12%的铁精矿,其优点在于得到 的铁精矿品位较高,实现了铁与部分杂质矿物铝、硅 的分离,缺点在于铁的回收率不高,并且不能有效地
2428
中国有色金属学报
2014 年 9 月
图2
氰化尾渣还原酸浸−氰化法回收金工艺流程
Fig. 2 Flow chart of gold recovery from cyanide tailings by cyanide process after reduction roasting and acid leaching
第 24 卷第 9 期 Volume 24 Number 9
中国有色金属学报 The Chinese Journal of Nonferrous Metals
2014 年 9 月 September 2014
文章编号:1004-0609(2014)09-2426-08
氰化尾渣还原焙烧酸浸提铁及氰化浸金新工艺
1 实验
1.1 实验原料 氰化尾渣取自新疆某黄金冶炼厂,呈粒度极细小 的红褐色粉末状,化学分析得其铁含量为 9.55%,金 含量为 5.6 g/t。X 荧光光谱半定量分析其主要元素含 量如表 1 所列。
表1 氰化尾渣中主要元素含量
Table 1 Main chemical components of cyanide tailings (mass fraction, %) O Fe Si Al Ca Na S K As Cu Others 图1 氰化尾渣的 SEM 像
,渣中含有一定量的金及其他有价金属 。
[3]
目前,我国黄金冶炼企业排放的氰化尾渣中铁含量为 20%~40%, 主要以赤铁矿的形式存在, 金含量为 2~10 g/t,其赋存状态主要以包裹金为主
[4−7]
。近年来,随着
难浸金矿的增加,氰化法已被广泛采用,相应的氰化 尾渣的大量排放占用大量的土地,同时严重影响环境 及浪费矿产资源,因此,将氰化尾渣进行二次回收利 用,可以给企业及社会带来良好的经济效益和环境效 益。综合回收氰化尾渣中有价金属的主要方法有浮选
析浸金液中金;采用日本 Rint−2000 型 X 射线衍射仪 分析部分固体物质的物相;采用扫描电镜(SEM)对部 分固体产物的形貌进行表征。 1.4 计算 硫酸浸出时,氰化尾渣中铁以 Fe2O3 计,渣中 Fe2O3 完全浸出时所需要的硫酸用量为理论硫酸用量 时,硫酸用量系数记为 1。亚铁浸出率为浸出液中亚 铁物质的量与实验所取氰化尾渣中总铁物质的量的 比。总铁浸出率为浸出液中总铁物质的量与实验所取 氰化尾渣中总铁物质的量的比。
2427
分离铁相中包裹的金,使得这部分金很难被回收。 本文作者通过还原焙烧酸浸工艺对氰化尾渣进行 处理,有效地浸出了氰化尾渣中的有价金属铁,铁的 浸出率达到 93.66%, 得到的硫酸铁酸浸液可用于制取 氧化铁红、聚合硫酸铁、绿矾和铁黄等[13−18]。采用该 工艺能使氰化尾渣中的金得到充分解离,采用常规氰 化法处理酸浸后渣,金的浸出率达到 92.4%。经过上 述处理后,氰化尾渣的质量减少了 38.8%,为氰化尾 渣中有价金属的综合回收利用及减少氰化尾渣的排放 提供了一条可行途径。