减压渣油
重油及渣油的物理组成
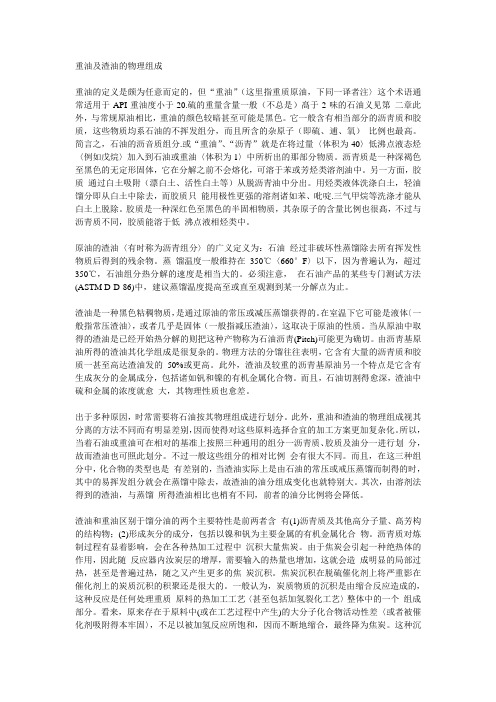
重油及渣油的物理组成重油的定义是颇为任意而定的,但“重油”(这里指重质原油,下同一译者注〉这个术语通常适用于API重油度小于20.硫的重量含量一般(不总是)髙于2味的石油义见第二章此外,与常规原油相比,重油的颜色较暗甚至可能是黑色。
它一般含有相当部分的沥靑质和胶质,这些物质均系石油的不挥发组分,而且所含的杂原子(即硫、逋、氧)比例也最高。
简言之,石油的沥音质组分.或“重油”、“沥青”就是在将过量〈体积为40〉低沸点液态烃〈例如戊烷〉加入到石油或重油〈体积为1〉中所析出的那部分物质。
沥青质是一种深褐色至黑色的无定形固体,它在分解之前不会熔化,可溶于苯或芳烃类溶剂油中。
另一方面,胶质通过白土吸附(漂白土、活性白土等)从脱沥青油中分出。
用烃类液体洗涤白土,轻油馏分即从白土中除去,而胶质只能用极性更强的溶剂诸如苯、吡啶.三气甲烷等洗涤才能从白土上脱除。
胶质是一种深红色至黑色的半固相物质,其杂原子的含量比例也很髙,不过与沥青质不同,胶质能溶于低沸点液相烃类中。
原油的渣油〈有时称为沥青组分〉的广义定义为:石油经过非破坏性蒸馏除去所有挥发性物质后得到的残余物。
蒸馏温度一般维持在350℃〈660°F〉以下,因为普遍认为,超过350℃,石油组分热分解的速度是相当大的。
必须注意,在石油产品的某些专门测试方法(ASTM D-D-86)中,建议蒸馏温度提高至或直至观测到某一分解点为止。
渣油是一种黑色粘稠物质,是通过原油的常压或减压蒸馏获得的。
在室温下它可能是液体〔一般指常压渣油〉,或者几乎是固体(一般指减压渣油〉,这取决于原油的性质。
当从原油中取得的渣油是已经开始热分解的则把这种产物称为石油沥靑(Pitch)可能更为确切。
由沥靑基原油所得的渣油其化学组成是很复杂的。
物理方法的分馏往往表明,它含有大量的沥青质和胶质一甚至高达渣油发的50%或更高。
此外,渣油及较重的沥青基原油另一个特点是它含有生成灰分的金属成分,包括诸如钒和镍的有机金属化合物。
催化裂化的原料和产品及催化剂

催化裂化的原料和产品及催化剂一、催化裂化的原料催化裂化的原料范围广泛,可分为馏分油和渣油两大类.馏分油主要是直流减压馏分油(VGO),馏程350~500℃,也包括少量的二次加工馏分油如焦化蜡油等;渣油主要是减压渣油、脱沥青的减压渣油、加氢处理重油等。
渣油都是以一定的比例掺入到减压馏分油中进行加工,其掺入的比例主要是受制于原料的金属含量和残炭值.对于一些金属含量很低的石蜡基原油也可以直接用常压重油作为原料。
通常评价催化裂化原料的指标有馏分组成、特性因数K值、相对密度、苯胺点、残炭、含硫量、含氮量、金属含量等。
(一)馏分组成对于饱和烃类为主要成分的直流馏分油来说,馏分越重越容易分裂所需条件越缓和,且残炭产率也越高,对于芳烃含量较高的渣油并不服从此规律。
对于重质原料,密度只要小于0。
92g/cm3 ,对馏程无限制.(二)烃类族组成含环烷烃多的原料容易裂解,液化气和汽油产率高,汽油辛烷值也高是理想的催化裂化原料。
含烷烃多的原料也容易裂化,但气体产率高,汽油产率和辛烷值较低含芳烃多的原料,难裂化,汽油产率更低,液化气产率也低,且生焦多,生焦量与进料的化学组成有关。
烃的生焦能力:芳烃>烯烃>环烷烃>烷烃。
(三)残炭残炭值反映了原料中生焦物质的多少。
残炭值越大,焦产率就越高。
馏分油原料的残炭值一般不大于0.4﹪,而渣油的残炭值较高,一般都在0。
4﹪以上,致使焦炭产率高达10﹪(质)左右,热量过剩,因此解决取热问题是实现渣油催化裂化的关键之一。
目前我国已有装置能处理残炭量高达7%~8%的劣质原料。
(四)含硫、含氮化合物含硫量会影响裂化的转化率、产品选择性和产品质量.硫含量增加,转化率下降,汽油产率下降,气体产率产率增加。
原料中的含氮化合物,特别是碱性含氮化合物能强烈的吸附在催化剂表面,中和酸性中心,是催化剂活性下降;中性氮化物进入裂化产物会使油品安定性下降。
(五)金属金属包括碱性金属钠和铁、镍、钒、铜等重金属。
渣油加氢工艺的研究与应用
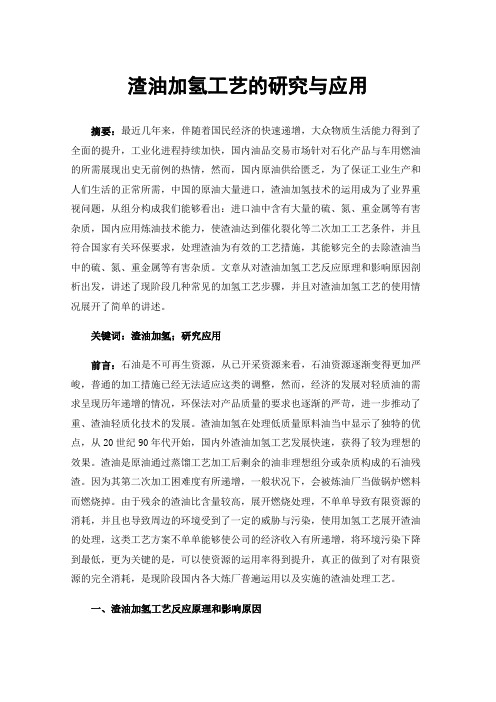
渣油加氢工艺的研究与应用摘要:最近几年来,伴随着国民经济的快速递增,大众物质生活能力得到了全面的提升,工业化进程持续加快,国内油品交易市场针对石化产品与车用燃油的所需展现出史无前例的热情,然而,国内原油供给匮乏,为了保证工业生产和人们生活的正常所需,中国的原油大量进口,渣油加氢技术的运用成为了业界重视问题,从组分构成我们能够看出:进口油中含有大量的硫、氮、重金属等有害杂质,国内应用炼油技术能力,使渣油达到催化裂化等二次加工工艺条件,并且符合国家有关环保要求,处理渣油为有效的工艺措施,其能够完全的去除渣油当中的硫、氮、重金属等有害杂质。
文章从对渣油加氢工艺反应原理和影响原因剖析出发,讲述了现阶段几种常见的加氢工艺步骤,并且对渣油加氢工艺的使用情况展开了简单的讲述。
关键词:渣油加氢;研究应用前言:石油是不可再生资源,从已开采资源来看,石油资源逐渐变得更加严峻,普通的加工措施已经无法适应这类的调整,然而,经济的发展对轻质油的需求呈现历年递增的情况,环保法对产品质量的要求也逐渐的严苛,进一步推动了重、渣油轻质化技术的发展。
渣油加氢在处理低质量原料油当中显示了独特的优点,从20世纪90年代开始,国内外渣油加氢工艺发展快速,获得了较为理想的效果。
渣油是原油通过蒸馏工艺加工后剩余的油非理想组分或杂质构成的石油残渣。
因为其第二次加工困难度有所递增,一般状况下,会被炼油厂当做锅炉燃料而燃烧掉。
由于残余的渣油比含量较高,展开燃烧处理,不单单导致有限资源的消耗,并且也导致周边的环境受到了一定的威胁与污染,使用加氢工艺展开渣油的处理,这类工艺方案不单单能够使公司的经济收入有所递增,将环境污染下降到最低,更为关键的是,可以使资源的运用率得到提升,真正的做到了对有限资源的完全消耗,是现阶段国内各大炼厂普遍运用以及实施的渣油处理工艺。
一、渣油加氢工艺反应原理和影响原因在渣油加氢的过程当中,时常会同时出现精制和裂化两种反应,其主要的反应方式有以下几个方面:1.脱硫反应渣油加氢处理工艺当中最为关键的化学反应则是脱硫反应,因为渣油硫化物的类别以及结构繁琐多样,因此,在实际的反应过程当中,所囊括的脱硫反应也较为繁琐。
过氧乙酸氧化-萃取脱除渣油中硫化合物

1 实验部分
1.1 试剂与仪器
试 剂 :甲 苯 ,分 析 纯 ,国 药 集 团 化 学 试 剂 有 限 公
司 ;碳 酸 钠 ,分 析 纯 ,吴 江 市 汇 通 化 工 有 限 公 司 ;冰
乙 酸 ,分 析 纯 ,天 津 市 鼎 盛 鑫 化 工 有 限 公 司 ;N ,N ⁃二
甲 基 甲 酰 胺 (DMF),分 析 纯 ,辽 宁 新 兴 化 学 试 剂 厂 ;
doi:10.3969/j.issn.1672⁃6952.2021.03.002
Removal of Sulfur Compounds in Residue by Peracetic Acid Oxidation⁃ Extraction
Sun Lijuan1,Cao Zubin1,Han Dongyun1,Wang Rong1,Gao Yi 2
本文采用乙酸⁃过氧乙酸体系对玛瑞减压渣油 (MRVR)进 行 氧 化 脱 硫 ,通 过 傅 立 叶 红 外 光 谱 仪 (FT⁃TR)分析渣油氧化前后官能团变化,结合 XPS 检 测 有 机 硫 类 型 及 分 布 ,选 用 N,N ⁃二 甲 基 甲 酰 胺 (D M F )作 为 渣 油 的 萃 取 剂 ,研 究 其 脱 硫 效 果 。
(2)
式中 ,Y 为回收率 ,% ;Q 为脱硫率 ,% ;W1 为萃余油
中硫质量分数,%;W2 为原料中硫质量分数,%。
2 渣油氧化前后的表征
2.1 红外光谱图 图 1 为 OXVR 和 MRVR 的红外光谱图。从图 1
可 以 看 出 ,3 442 cm-1 处 均 出 现 了 饱 和 脂 肪 酸 -OH 的特征峰;2 925、2 854 cm-1 处较强的特征峰为亚甲 基(-CH2)中 C-H 伸 缩 振 动 吸 收 峰 ;1 460 cm-1 处 特征峰为饱和烃 C-H 弯曲的震动吸收峰。OXVR 曲线中,1 600~1 617 cm-1 处的芳烃吸收峰减弱[6],是 部分 C=C 被过氧乙酸氧化的结果;1 300、1 145 cm-1 处为脂链砜物质中 O=S=O 伸缩震动引起特征峰。 由此可见,玛瑞减压渣油经乙酸⁃过氧乙酸体系氧化, 部分噻吩硫及其衍生物被氧化为砜类物质。
减粘裂化

4
二、减粘裂化工艺流程
反应温度: 400~450℃ 反应压力: 4~5atm
5
炉式减粘裂化工艺原理流程
返回 本节
6
与炉式减粘裂化相比, 塔式减粘反应温度低、 停留时间长
反应塔式减粘裂化工艺流程图
7
三、操作因素分析
1.原料 组成和性 质 2.裂化温 度
影响因素
3.裂 化压 力
4.反 应时 间
8
组分;
重石脑油组分经过加氢处理脱除硫及烯烃后,
可作催化重整原料;
也可将全部减粘石脑油送至催化裂化装置,经 过再加工后可以改善稳定性,然后再脱硫醇。
3
减粘柴油含有烯烃和双烯烃,故安定性差,需加 氢处理才能用作柴油调和组分。 减粘重瓦斯油性质主要与原料油性质有关,介于 直馏VGO和焦化重瓦斯油的性质之间,其芳烃含 量一般比直馏VGO高。 减粘渣油可直接作为重燃料油组分,也可通过减 压闪蒸拔出重瓦斯油作为催化裂化原料。
10
减粘裂化
• 减粘裂化是以常压重油或减压渣油为原料
进行浅度热裂化反应的一种热加工过程。 主要目的是为了减小高黏度燃料油的黏度 和倾点,改善其输送和燃烧性能。 • 一、原料和产品 • 二、减粘裂化工艺流程 • 三、操作因素分析
1
返回 本章
一、原料和产品
1.原料油
常用的减粘裂化原料油有常压重油、减压 渣油和脱沥青油。 原料油的组成和性质对减粘裂化过程的操 作和产品分布与质量都有影响
返回 本节
原料组成和性质的影响
原料沥青质含量、残炭值、 黏度、硫含量、氮含量及 金属含量越高,越难裂化。
蜡含量越高,原料越重,减粘 效果越明显。
9
裂化温度:裂化温度随原料 油性质和要求的转化深度而 定。
渣油加氢技术浅析

渣油加氢技术浅析摘要:作为原油中最重的馏分,渣油是加氢裂化工艺的重要原料之一。
由于不同油田生产的原油其性质和组成相差甚远,因此,通过对渣油的性质和组成的分析,一方面,为选择适宜的加工途径,生产合适的石油产品提供必要的依据;另一方面,为加氢裂化、加氢精制等生产过程中所使用催化剂的开发及其工艺的优化提供技术支持。
关键词:渣油;加氢;工艺中图分类号:u416文献标识码: a 文章编号:近年来,随着能源危机的日益加剧,原油变劣、变重,轻质油品的需求日益增加以及环保要求越来越严格等多种因素的影响,渣油的利用越来越被人们所重视,渣油深度转化也成为炼油厂长期追求的目标。
如何深度加工产量日益增长的重质原油和其中的大量高硫减压渣油,以满足经济发展对清洁燃料和低硫锅炉燃料油的需要和环保法规的要求,已经成为21世纪世界炼油工业开发的重点。
1渣油原料的主要特点渣油是原油中最重的馏分,包括常压渣油和减压渣油。
常压渣油是原油在常压蒸馏装置中蒸馏后的塔底剩余物,而减压渣油是常压渣油在减压蒸馏装置中进一步蒸馏后的塔底剩余物。
原油中大部分的硫、氮、残炭和金属等杂质均富集浓缩于渣油中,渣油原料具有自身独特的特点。
从化学组成看,渣油含有较大量的金属、硫和氮等杂质元素以及胶质、沥青质等非理想组分。
从化学性质看,渣油平均分子量大、氢碳比低,在反应中易结焦物质多。
从物理性质看,渣油粘度大、密度高。
不同原油的渣油有其各自的特点,如有的渣油镍高、钒低,有的渣油硫高、氮低,而有的则相反。
2渣油加氢的发展背景2.1世界原油资源有限世界原油资源十分有限,以目前开采速度计算,世界原油储量可采40年左右,因此,原油资源十分紧张,应合理、充分利用宝贵的石油资源。
2.2原油变重、变劣世界原油质量总变化趋势为:含硫和高硫原油比例逐年增加,含酸和高酸原油的产量也逐年增加。
含硫原油和高硫原油的产量约占75%o同时,世界高酸原油 (酸值大于1.0mgkoh/g)产量和稠油产量也在不断增加,到20世纪末,世界稠油产量占到了原油总产量的30%,因此,重质原油的加工日益受到石油工业的重视。
催化技术问答第二章
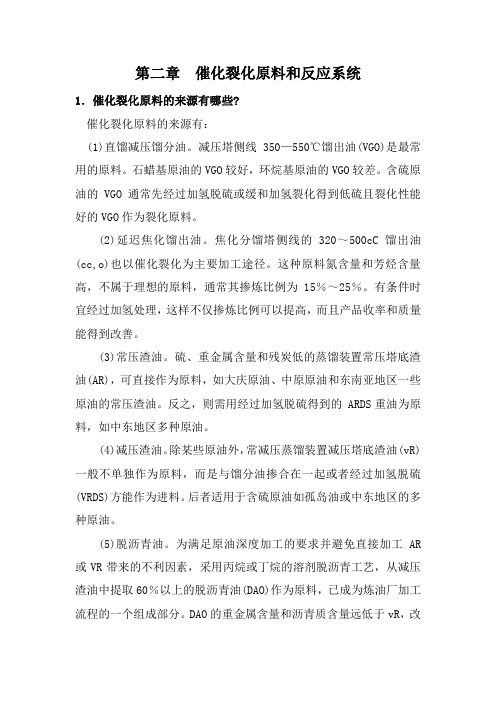
第二章催化裂化原料和反应系统1.催化裂化原料的来源有哪些?催化裂化原料的来源有:(1)直馏减压馏分油。
减压塔侧线350—550℃馏出油(VGO)是最常用的原料。
石蜡基原油的VGO较好,环烷基原油的VGO较差。
含硫原油的VGO通常先经过加氢脱硫或缓和加氢裂化得到低硫且裂化性能好的VGO作为裂化原料。
(2)延迟焦化馏出油。
焦化分馏塔侧线的320~500cC馏出油(cc,o)也以催化裂化为主要加工途径。
这种原料氮含量和芳烃含量高,不属于理想的原料,通常其掺炼比例为15%~25%。
有条件时宜经过加氢处理,这样不仅掺炼比例可以提高,而且产品收率和质量能得到改善。
(3)常压渣油。
硫、重金属含量和残炭低的蒸馏装置常压塔底渣油(AR),可直接作为原料,如大庆原油、中原原油和东南亚地区一些原油的常压渣油。
反之,则需用经过加氢脱硫得到的 ARDS重油为原料,如中东地区多种原油。
(4)减压渣油。
除某些原油外,常减压蒸馏装置减压塔底渣油(vR)一般不单独作为原料,而是与馏分油掺合在一起或者经过加氢脱硫(VRDS)方能作为进料。
后者适用于含硫原油如孤岛油或中东地区的多种原油。
(5)脱沥青油。
为满足原油深度加工的要求并避免直接加工 AR 或VR带来的不利因素,采用丙烷或丁烷的溶剂脱沥青工艺,从减压渣油中提取60%以上的脱沥青油(DAO)作为原料,已成为炼油厂加工流程的一个组成部分。
DAO的重金属含量和沥青质含量远低于vR,改善了原料质量。
含硫原油的DAO最好经过加氢脱硫(可与VGO合并处理)。
我国还成功开发了溶剂脱沥青一催化裂化组合工艺,将催化裂化油浆也作为脱沥青原料,可回收其中的饱和烃,获得较高的产品收率。
(6)其他。
我国开发成功的芳烃抽提一催化裂化组合工艺,把催化裂化装置产生的重循环油经过双溶剂抽提除去重芳烃后返回做回炼油,可明显提高轻质油产率和装置处理。
2.渣油有什么特点?渣油中,各污染物含量的范围如表2—1所示。
表2—1渣油中各污染物含量的范围渣油的特点是:(1)金属。
常减压讲解

原油与~2(常顶循)、E-8(常一)、~2(常三2)、~2(常四2)、~2(减五2)、~2(减渣一路6)、~2(减二)换热到140℃。
两路原油换热混合后分四路进行换热:
一路:
原油经E-14(减三2)、~2(减渣二路5)、E-16(常二中2)、E-17/1~2(减二中3)、E-18(减三1);
二路:
减三线油从减压塔第4层集油箱馏出,进减三线汽提塔(C-5II),汽提出的轻组分和水蒸汽返回减压塔。汽提后的减三线油287℃经减三线泵(~2)抽出,与原油(E-
18、E-14)换热,经ER-2发汽后,再经减三线冷却器(~2)冷却到90℃~98℃出装置作HVI
150、HVI200润滑油基础油原料。
减四线油从减压塔第6层集油箱馏出,进入减四线汽提塔(C-5III),汽提出的轻组分和水蒸汽返回减压塔,汽提过的减四线油328℃经减四线泵(~2)抽出,依次与~
原油经E-19(常三1)、~2(减渣一路5)、~2(常四1)、~2(常二1)、~2(减二中2);
三路:
原油经E-24(减一中2)、E-25(常一中1)、~2(减渣二路4)、~2(减六1)、~2(减渣二路3);
四路:
原油经~2(减四3)、E-30(减一中2)、E-31(常一中1)、~2(减渣一路4)、~2(减四2)、~2(减渣一路3)。
41、42、43后进入装置。自
2004年4月下旬开始,在大庆原油中掺混5%~10%的俄罗斯原油。###
4主要产品及付产品
主要产品:
初顶汽油、常顶汽油、常一线、常二线、常三线、常四线、减顶油、减一线、减二线、减三线、减四线、减五线、减六线、热渣油、冷渣油。
付产品:
初顶瓦斯、常顶瓦斯、减顶瓦斯。5工艺原理
- 1、下载文档前请自行甄别文档内容的完整性,平台不提供额外的编辑、内容补充、找答案等附加服务。
- 2、"仅部分预览"的文档,不可在线预览部分如存在完整性等问题,可反馈申请退款(可完整预览的文档不适用该条件!)。
- 3、如文档侵犯您的权益,请联系客服反馈,我们会尽快为您处理(人工客服工作时间:9:00-18:30)。
减压渣油摘要:中国石化济南分公司焦化装置曾以不同比例掺炼RFCC油浆,针对实际生产数据,经多方面分析对比,认为RFCC油浆不适宜作为焦化装置原料,尤其是较大比例掺炼油浆时综合效益将大大降低。
关键词:RFCC油浆减压渣油焦化设备磨损效益1、前言焦化装置以减压渣油为主要原料,主要产品为焦化汽油、柴油、蜡油及石油焦,是实现重油轻质化的主要手段,它以加工原料和加工工艺的灵活性日益受到炼油企业的重视。
重油催化裂化(RFCC)外甩油浆是改善催化裂化工况的常用手段,而该油浆的出路一直是各炼厂需解决的头痛问题。
济南分公司50万吨/年延迟焦化装置原设计原料为减压渣油:RFCC油浆为9:1的混合原料,后来该装置又成功开发了浮渣回炼、甩油回炼、全厂污油回炼等新工艺,为实现对炼厂原油的吃干榨尽起到了重要作用。
济南分公司焦化装置曾以不同比例掺炼过RFCC油浆,但RFCC油浆作为焦化装置的原料究竟有何利弊,掺炼比例多少合适,有何经济效益?本文针对济南分公司焦化装置掺炼RFCC催化油浆的实际情况,从其对产品分布影响、产品质量影响、设备磨损情况、经济效益四个方面进行分析,以期找到问题的最佳答案,实现炼厂效益最佳化。
2、RFCC油浆与减压渣油性质比较济南分公司焦化装置原料减压渣油来自常减压装置,以胜利油田临盘原油为主;RFCC油浆来自80万吨/年催化裂化及140万吨/年催化裂化装置,内含有一定的催化剂固体粉末,一般为2g/l,最高达到过9.2g/l(2003年10月24日分析数据)。
两种原料性质见表1。
由表1可见,与减压渣油相比,RFCC油浆的密度较大,芳烃含量高,残炭、粘度小于减压渣油,S、N含量与减压渣油基本相近。
表1 RFCC油浆及减压渣油的主要性质分析项目减压渣油RFCC油浆密度g/m3 982.4 1071.8粘度(100℃)mm2/s614.7 41.50残炭%(m)16.34 15.74硫含量%(m)12510 10168凝固点℃37 22盐含量%/ 0.18总氮ppm 6371 6358族组成饱和烃%21.65 20.41芳烃%37.96 60.54胶质%38.27 16.53沥青质% 2.12 2.523、焦化装置掺炼RFCC油浆生产概况济南分公司50万吨/年延迟焦化装置于2002年11月28日一次开车成功,开工初期全部以减压渣油作为原料。
2003年3月份以后,基本按照RFCC油浆掺炼比例为10%的设计值作为原料,直至7月份第一周期按计划停工。
焦化装置第二周期生产于2003年8月3日开车成功,其中8月份全部以减压渣油作为原料以110%负荷生产9月份曾掺炼部分常压渣油作为原料。
进入2003年10月份以后,随着全厂生产方案的调整,焦化装置的负荷及RFCC油浆掺炼比例出现大幅度调整,本文所取数据多来自这一时期。
2003年10月1日~8日,焦化装置仍然全部以减压渣油为原料,10月8日以后开始大比例掺炼油浆,由于罐区来料中RFCC油浆掺炼比例有时无法确定,且11月中旬炼厂原油中掺入黄岛油和沙轻原油,该文仅采取了较准确的掺炼比为25%、33%、41%的数据进行分析,该期间原料性质亦无大变化。
10月18日~25日,油浆掺炼比例为25%,处理量36~40T/H;11月1日~5日,RFCC油浆掺炼比为41.6%,处理量35T/H,该期间由于处理量较低,为提高加热炉管内介质线速度,采取了部分蜡油回炼进原料罐的措施;11月24日~30日,油浆量维持在20T/H左右,掺炼比为33%,装置以62.5T/H的处理量满负荷生产。
4、掺炼RFCC油浆后对产品收率的影响掺炼RFCC油浆前后主要产品收率变化见表2。
表2 掺炼RFCC油浆前后主要产品收率变化注:A、掺炼比为41%时部分蜡油回炼作原料;B、掺炼比为33%时改为生产-10#柴油方案。
从表2可以看出,焦炭产率随着掺炼量的增加而明显增加,焦化汽柴油收率及装置总液收明显下降。
如掺炼比为33%时,较不掺炼RFCC油浆时对比,焦炭收率增加4.58%,装置总液收降低7.78%。
另外,本次RFCC油浆掺炼比达到41%时,由于加工负荷较低(仅56%),采取了部分蜡油回炼进原料罐的方式,(目的是为了增加加热炉管内线速度避免炉管结焦,增加原料线速度减少油浆中催化剂固体颗粒沉积,)因此该段时期汽柴油收率较高,但焦炭收率高达38.67%,装置总液收仅52.38%,同样说明了以上观点。
分析认为,掺炼RFCC油浆后,由于油浆中芳烃含量高,油浆中约有50%左右的蜡油馏分,该组分难以裂解,相对减压渣油而言易于结焦,因此掺炼油浆后蜡油收率会有所上升,汽柴油收率则下降明显,焦炭收率明显升高。
5、掺炼RFCC油浆后对产品质量的影响由于我装置仅化验分析焦化汽柴蜡油的密度及馏程,不分析族组成,因此由于分析数据主要受控制手段的影响,生产上焦化汽柴蜡油的密度及馏程变化不大,在此未予列出;焦化蜡油残炭在生产负荷不变的情况下随着油浆的掺炼比不同应有所变化,但由于济南分公司焦化装置在掺炼油浆期间生产负荷大幅度波动,蜡油残炭受加热炉注汽量的影响较大,也不具有分析比较价值;焦炭中硫含量又主要受济南分公司原油硫含量的影响,因此我们仅分析比较受掺炼油浆影响较大的焦炭灰份予以分析比较,见表3。
表3 掺炼油浆前后焦炭灰份变化油浆掺炼比% 0 9.2 25 33 41焦炭灰份% 0.15 0.21 0.48 0.58 0.36由表3可见,随着油浆掺炼比的增大,焦炭灰份呈明显上升趋势。
油浆掺炼比为41时焦炭灰份反倒为0.36%,分析认为由于蜡油大比例回炼,生焦率较高,稀释了焦炭灰份所致。
6、掺炼RFCC油浆后存在的生产问题6.1 对产品质量的影响在焦化原料中掺炼RFCC油浆首先必须考虑对焦炭质量的影响,主要指对焦炭灰份的影响,因为RFCC油浆中的固体颗粒的带入首先反映在焦炭灰份升高上。
2B焦炭灰份指标为0.5%,在未掺炼RFCC油浆的情况下,焦炭灰份一般低于0.2%,一旦掺炼量过大或RFCC油浆中固体含量过高,都极易引起焦炭灰份超标。
11月中旬,原料为沙轻原油期间,焦炭灰份最高达1.73%(11月12日数据),已属不合格品(3B级焦炭为1.2%)。
后切断罐区来的RFCC油浆后(仅保留80万吨/年催化裂化来的油浆),焦炭灰份迅速降至0.39(11月22日数据),焦炭灰份受RFCC 油浆影响极为明显。
这说明为保证焦炭质量,控制RFCC油浆掺炼比及RFCC油浆中的固体含量非常必要.在焦化原料中掺炼RFCC油浆还对焦化蜡油有较大影响。
由于RFCC油浆中芳烃含量较高,该组分难以裂解,因此掺炼油浆后很大一部分又随着焦化蜡油组分作为产品出装置,最终又回到催化裂化装置。
如此循环,既增大了催化、焦化装置的能耗,又使得焦化蜡油质量变差。
前已述及济南分公司焦化蜡油未做出掺炼油浆前后的质量分析对比,但据安庆分公司焦化装置的实际生产数据知,该装置掺炼8%的RFCC油浆后,蜡油族组成中饱和烃由59.17%下降至51.1%,下降了8%,芳烃含量由36.06%增加到41.41%,增加了5.35%,蜡油残炭由0.1%升高至0.35%,可见蜡油质量明显变劣。
6.2 RFCC油浆带水的影响RFCC油浆密度一般都比水大,脱水比较困难,特别是当RFCC油浆若在罐区内与冷渣油混合时,更容易带水。
若原料带水严重,将引起操作大幅波动,其至会出现原料泵、辐射进料泵抽空等严重后果。
因此,在掺炼RFCC油浆时,我装置每次都是先将RFCC油浆来料线油头外甩半小时后再进装置。
尽管如此,仍多次出现罐区来RFCC油浆量不稳,原料罐液面因RFCC油浆带水而异常升高现象。
因此,RFCC油浆掺炼前必须严格脱水。
6.3 原料换热器垢RFCC油浆中含有较多的固体颗粒及稠环芳烃,在换热器内易结垢。
焦化装置原料进装置流程为RFCC油浆与减压渣油经混合器混合后,混合原料依次与柴油、中段循环油、蜡油换热后进入分馏塔,走的均为壳程。
由于RFCC油浆中固体颗粒在换热器壳程中更易沉积,将导致换热器压降增大,检修时抽芯非常困难,换热器管束严重损坏。
该现象已在长岭分公司焦化装置发生过,当时该厂曾试验掺炼RFCC油浆到30%,后来该厂将RFCC油浆进装置换热器改为油浆走管程,且掺炼率严格控制在不大于7%。
6.4 分馏塔底循环过滤器内焦粉沉积结焦RFCC油浆中催化剂固体粉末除在原料换热器内沉积外,另一重要沉积点为焦化分馏塔底。
由于底循环的作用,该固体粉末最终沉积在底循环过滤器内。
另外,在分馏塔底360℃温度下,RFCC油浆较易结焦。
济南分公司焦化装置自从10月份掺炼RFCC油浆以来,焦化分馏塔底循环过滤器经常堵塞,导致底循环泵提不起量,常常用蒸汽反吹扫,仍难以奏效,只好拆开清理,仅11月份就拆开清理3次,拆开后发现过滤器内含较多小焦块及焦粉与催化剂粉末混合后的粉状物,堵塞严重。
而在第一开工周期期间(最大掺炼比为10%),该过滤器未曾拆开清理过,这进一步验证了大比例掺炼RFCC油浆是导致底循环过滤器堵塞的主要原因。
6.5 掺炼RFCC油浆对管线、泵等设备的磨损由于RFCC油浆中催化剂固体颗粒硬度极大,线速度低时会在所过之处沉积,但线速度较大时更会对设备造成严重磨损,尤其是泵体叶轮及底循、炉管等管线,因为介质在该处线速度极高,国内已有多家焦化装置在这上面吃过大亏。
石家庄分公司焦化装置曾因掺炼RFCC油浆使底循环泵叶轮磨损得簿如刀刃,后来更换为专门的RFCC油浆泵。
为此该厂焦化装置现严格控制RFCC油浆掺炼比为5%,最大7%,在此之前焦化装置平均半年被迫停工一次,而今该装置已平稳运行500多天,正争创长周期运行装置;乌鲁木齐炼油厂焦化装置曾因掺炼RFCC油浆使原料泵、底循泵、辐射进料泵叶轮磨损严重全部报费;沧州分公司焦化装置曾因掺炼RFCC油浆使底循环管线磨损的最簿处仅2mm,险些酿成大火,现该厂RFCC 油浆全部做燃料油外卖;福建分公司焦化装置曾因掺炼RFCC油浆将辐射泵出口调节阀阀芯磨损得严重泄漏。
我焦化装置为新建装置,设备磨损带来的危害尚未显现出来。
为减轻磨损带来的损失,济南分公司焦化装置回炼RFCC油浆后曾将辐射泵由倒至1#旧泵,但由于旧泵先天不足,在满负荷下超电流,现仍然运转2#进口泵。
另外,为避免RFCC油浆掺炼比大使加热炉炉管结焦,车间控制较高的注汽量以提高炉管内线速度,加上原料在加热过程中的分解、气化,加热炉管内线速将高达40~50m/s,炉管磨损问题相当严峻。
为此车间已在下次检修计划中将上述易损部位列入重点检测部位。
(催化油浆系统的设计线速度一般<2m/s,因此,焦化装置的设备磨损情况要比催化装置的油浆系统严重得多。
)6.6 掺炼RFCC油浆后因结焦率大而影响处理量生产实践已证明,随着油浆掺炼比的提高装置焦炭产率将大幅度提高,因此当装置满负荷生产时,由于焦炭塔内生焦高度过高带来的危害则显现出来。