汽车仿真分析
汽车碰撞模拟仿真分析的关键参数分析与优化

汽车碰撞模拟仿真分析的关键参数分析与优化随着汽车安全意识的提升,汽车碰撞模拟仿真分析在汽车工程设计中扮演着越来越重要的角色。
通过模拟碰撞过程,可以准确地评估车辆在不同情况下的碰撞性能,优化车辆的设计,提高车辆的安全性能。
本文将探讨汽车碰撞模拟仿真分析中关键参数的分析与优化方法。
一、车身材料的选择与优化车身材料是影响碰撞模拟分析的重要参数之一。
传统的汽车多采用钢材作为主要材料,但随着新能源汽车的兴起,复合材料也得到广泛应用。
通过模拟分析,我们可以根据车辆的用途和碰撞要求,选择合适的材料。
例如,对于一般乘用车,可以选择具有较高强度和韧性的钢材,而对于电动汽车,可以考虑采用轻质的碳纤维复合材料。
同时,还可以通过优化设计来提高材料的使用效能,例如通过减少车身重量来提高车辆的燃油效率等。
二、碰撞角度的选择与优化碰撞角度是影响车辆碰撞模拟的另一个重要参数。
不同碰撞角度下,车辆的受力情况和变形程度都不同,因此需要根据实际情况进行选择和优化。
在汽车工程设计中,常用的碰撞角度包括正面碰撞、侧面碰撞、倾斜碰撞等。
通过模拟分析,可以评估不同碰撞角度下车辆的受力情况,为车辆的结构设计提供参考。
三、安全气囊的设计与优化安全气囊是汽车碰撞模拟中不可忽视的关键参数。
安全气囊能够在碰撞发生时迅速充气,并保护乘车人员免受伤害。
通过模拟分析,可以确定合适的安全气囊位置、数量和形式,以及充气速度和力度等参数。
同时,还可以通过优化设计来提高安全气囊的性能,例如调整充气时间和压力来减少碰撞时对乘车人员的冲击力。
四、制动系统的设计与优化制动系统是汽车碰撞模拟仿真中关键的安全参数之一。
制动系统的设计直接影响到车辆在发生碰撞时的制动性能和稳定性。
通过模拟分析,可以评估不同制动系统设计方案的有效性,并根据实际情况进行优化。
例如,可以通过调整制动力分配、优化制动盘和刹车片等参数来提高制动系统的性能,保证车辆在碰撞时能够及时停下。
五、车辆结构的刚度与强度优化车辆结构的刚度和强度是汽车碰撞模拟分析中的关键参数之一。
仿真分析对汽车碰撞安全性能的评估与改进

仿真分析对汽车碰撞安全性能的评估与改进随着汽车行业的发展和技术的不断进步,人们对汽车碰撞安全性能的要求也越来越高。
汽车碰撞安全性能的评估与改进是保障驾驶者和乘客生命安全的重要环节。
本文将从仿真分析的角度,探讨对汽车碰撞安全性能的评估与改进方法。
一、背景介绍汽车碰撞安全性能评估与改进是一项复杂而重要的工作。
在过去,针对汽车碰撞安全性能的评估多以实验室测试和道路试验为主。
然而,这些方法费时费力、成本高昂,并且难以覆盖各种碰撞场景。
因此,人们逐渐将仿真分析技术引入汽车碰撞安全性能的评估与改进工作中。
二、仿真分析的概念及优势1. 仿真分析的概念仿真分析是一种使用计算机模型和数值计算方法对汽车碰撞过程进行模拟和预测的技术。
通过建立适当的数学模型和物理模型,可以在计算机上模拟和预测汽车在不同碰撞场景下的性能表现。
2. 仿真分析的优势(1)节约时间和成本:相比实验室测试和道路试验,仿真分析可以大幅缩短评估时间,并大幅度降低评估成本。
(2)全面覆盖碰撞场景:通过建立不同碰撞场景的仿真模型,可以评估车辆在各种碰撞情况下的安全性能,包括正面碰撞、侧面碰撞、倾斜碰撞等。
(3)优化设计:仿真分析可以帮助工程师优化车辆结构和材料选择,提升车辆的抗碰撞能力。
(4)快速预测:在新车型开发阶段,仿真分析可以快速预测车辆的碰撞性能,帮助制定合理的改进方案。
三、汽车碰撞仿真分析的方法汽车碰撞仿真分析的方法主要包括以下几个方面:1. 碰撞模型建立首先,需要建立汽车的三维模型,并根据实际情况设置碰撞模型的初始条件和边界条件。
同时,还需将汽车模型转化为计算机可识别的格式,以便进行后续的数值计算。
2. 材料模型和力学模型在建立碰撞模型的基础上,还需要对汽车材料和力学模型进行定义和建模。
通过设置汽车材料的物理参数和材料性能,以及确定汽车的力学行为,可以更准确地预测碰撞过程中车辆的变形和受力情况。
3. 碰撞仿真计算通过数值计算方法,将碰撞模型的初始条件和边界条件输入到仿真软件中进行计算。
汽车碰撞模拟仿真分析2024

引言概述汽车碰撞模拟仿真分析是一种用于研究汽车碰撞行为和评估车辆安全性能的有效工具。
通过模拟仿真分析,可以预测车辆碰撞时的动力学响应、车辆结构变形、乘员保护性能等重要参数,从而为车辆设计和安全评价提供依据。
本文将从不同角度详细分析汽车碰撞模拟仿真分析的相关内容。
正文内容1. 碰撞模拟仿真的意义和优势1.1 碰撞模拟仿真的意义碰撞模拟仿真可以在物理实验之前对车辆性能和安全性进行全面有效的评估,为车辆设计提供指导和改进方向。
1.2 碰撞模拟仿真的优势碰撞模拟仿真可以大幅度节省成本和时间,减少人力资源和实验设备的消耗,同时可以对碰撞过程中的细节进行深入分析。
2. 碰撞模拟仿真的基本原理和方法2.1 碰撞模拟仿真的基本原理碰撞模拟仿真基于有限元法和多体动力学原理,通过对车辆和碰撞体建立的数学模型进行求解,得出车辆碰撞时的动力学响应和结构变形。
2.2 碰撞模拟仿真的基本方法碰撞模拟仿真的基本方法包括车辆建模、材料特性建模、约束条件设定、求解模拟过程和结果分析等。
3. 碰撞模拟仿真的关键技术与挑战3.1 车辆碰撞行为建模车辆碰撞行为建模是碰撞模拟仿真的关键技术之一,需要考虑车辆的刚体运动、车辆结构变形和碰撞力的传递等因素。
3.2 材料特性建模材料特性建模是碰撞模拟仿真中的关键技术之一,需要准确描述车辆结构材料的力学行为,即材料的本构关系和损伤模型。
3.3 碰撞力传递与刚体运动碰撞力传递与刚体运动是碰撞模拟仿真中的关键技术之一,需要准确计算车辆碰撞过程中的力学响应,包括碰撞时间、碰撞角度和碰撞动量等。
3.4 界面接触与摩擦界面接触与摩擦是碰撞模拟仿真中的关键技术之一,需要准确描述车辆和碰撞体之间的接触行为和摩擦特性,包括接触力和接触面积等。
3.5 解算算法与计算效率解算算法与计算效率是碰撞模拟仿真中的关键技术之一,需要选择合适的数值方法和算法,提高仿真计算的精度和效率。
4. 汽车碰撞模拟仿真的应用领域4.1 车辆设计与优化汽车碰撞模拟仿真可以帮助车辆制造商进行车辆设计和优化,提高车辆的安全性和性能。
汽车碰撞试验有限元仿真分析
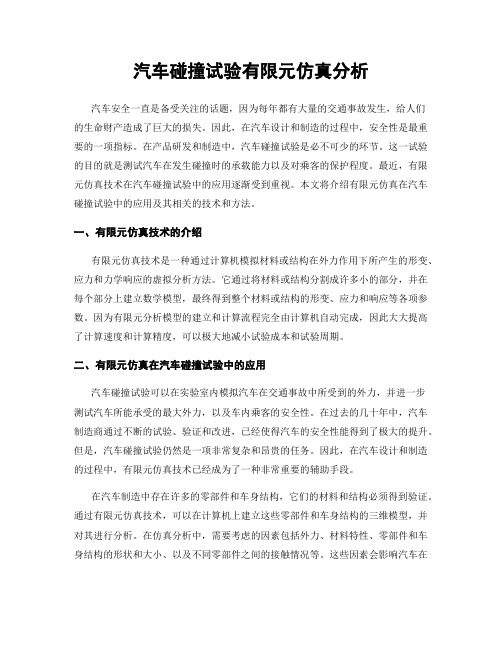
汽车碰撞试验有限元仿真分析汽车安全一直是备受关注的话题,因为每年都有大量的交通事故发生,给人们的生命财产造成了巨大的损失。
因此,在汽车设计和制造的过程中,安全性是最重要的一项指标。
在产品研发和制造中,汽车碰撞试验是必不可少的环节。
这一试验的目的就是测试汽车在发生碰撞时的承载能力以及对乘客的保护程度。
最近,有限元仿真技术在汽车碰撞试验中的应用逐渐受到重视。
本文将介绍有限元仿真在汽车碰撞试验中的应用及其相关的技术和方法。
一、有限元仿真技术的介绍有限元仿真技术是一种通过计算机模拟材料或结构在外力作用下所产生的形变、应力和力学响应的虚拟分析方法。
它通过将材料或结构分割成许多小的部分,并在每个部分上建立数学模型,最终得到整个材料或结构的形变、应力和响应等各项参数。
因为有限元分析模型的建立和计算流程完全由计算机自动完成,因此大大提高了计算速度和计算精度,可以极大地减小试验成本和试验周期。
二、有限元仿真在汽车碰撞试验中的应用汽车碰撞试验可以在实验室内模拟汽车在交通事故中所受到的外力,并进一步测试汽车所能承受的最大外力,以及车内乘客的安全性。
在过去的几十年中,汽车制造商通过不断的试验、验证和改进,已经使得汽车的安全性能得到了极大的提升。
但是,汽车碰撞试验仍然是一项非常复杂和昂贵的任务。
因此,在汽车设计和制造的过程中,有限元仿真技术已经成为了一种非常重要的辅助手段。
在汽车制造中存在许多的零部件和车身结构,它们的材料和结构必须得到验证。
通过有限元仿真技术,可以在计算机上建立这些零部件和车身结构的三维模型,并对其进行分析。
在仿真分析中,需要考虑的因素包括外力、材料特性、零部件和车身结构的形状和大小、以及不同零部件之间的接触情况等。
这些因素会影响汽车在发生碰撞时的变形、应力和响应能力,因此,在有限元仿真中,需要尽可能准确地考虑所有的因素。
三、有限元仿真在汽车碰撞试验中的技术和方法1.材料模型的建立有限元仿真中材料模型是一个非常关键的因素,因为材料的特性会直接影响汽车在发生碰撞时的响应能力。
汽车仿真行业行业分析报告

汽车仿真行业行业分析报告一、定义汽车仿真是指在计算机内部模拟真实交通情况并进行调试的技术。
它是二十一世纪智能交通领域的重要组成部分之一,使汽车行驶更加安全、高效和环保。
二、分类特点汽车仿真行业包括以下三类:1.交通仿真:以道路实景、车辆模型及各种路口交通组织形式等为基础,模拟真实的交通情况,并进行分析、评估和优化等。
2.汽车虚拟设计:将大量车辆性能参数输入电脑,通过计算机软件模拟出车辆在不同环境下的运行情况。
3.自动驾驶仿真:以车辆行驶路线、交通管制、无人驾驶风险评估为核心内容,使用计算机虚拟技术智能模拟真实道路交通情况,并测试不同驾驶情况下汽车的反应能力。
三、产业链汽车仿真行业的产业链主要包括汽车软件开发、汽车配件生产、模型创建、3D建模、数据采集与处理、虚拟现实技术、车联网技术等环节。
四、发展历程2006年:汽车仿真技术开始盛行,国内国际厂商相继建立汽车仿真中心。
2012年:自主研发的汽车仿真技术初步应用于智能交通系统。
2015年:国家发改委正式发布《汽车产业“十三五”规划》,提出“以智能驾驶、网络化车辆为主要目标”的技术路线图。
五、行业政策文件《国家智能汽车发展战略》(2017年)《工业和信息化部关于加快建设车联网产业体系的指导意见》(2017年)《交通运输部车辆自动驾驶道路测试管理规定》(2018年)六、经济环境中国在汽车生产和出口方面已经成为全球重要的汽车生产国家,并正在逐步从“中国制造”向“中国智造”转型。
随着政策的鼓励和资本的支持,汽车仿真行业发展前景十分广阔。
七、社会环境智能交通是促进社会发展的重要利器,在改善交通状况、减少交通事故、提高出行效率、节能减排等方面都有着积极的作用。
八、技术环境汽车仿真是虚拟现实、人工智能等前沿科技的应用,随着技术的不断提升,汽车仿真的应用范围和效能也随之不断提高。
九、发展驱动因素1.国家政策鼓励:“中国制造2025”计划和“智能中国”战略逐渐推进,政府大力推广智能驾驶技术。
汽车整车动力学仿真分析
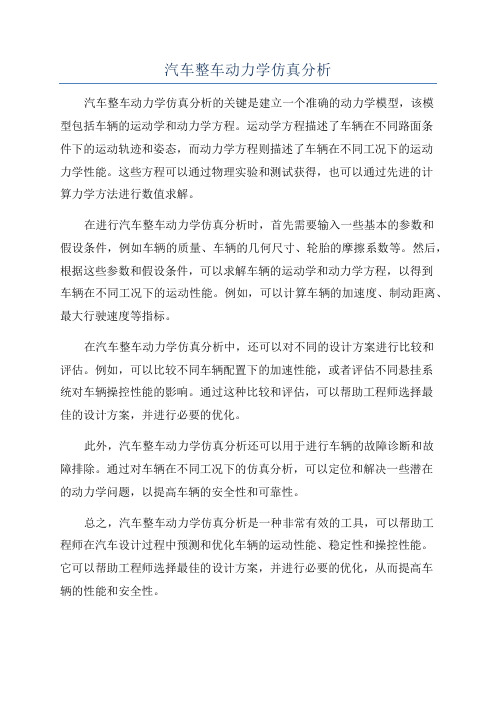
汽车整车动力学仿真分析
汽车整车动力学仿真分析的关键是建立一个准确的动力学模型,该模
型包括车辆的运动学和动力学方程。
运动学方程描述了车辆在不同路面条
件下的运动轨迹和姿态,而动力学方程则描述了车辆在不同工况下的运动
力学性能。
这些方程可以通过物理实验和测试获得,也可以通过先进的计
算力学方法进行数值求解。
在进行汽车整车动力学仿真分析时,首先需要输入一些基本的参数和
假设条件,例如车辆的质量、车辆的几何尺寸、轮胎的摩擦系数等。
然后,根据这些参数和假设条件,可以求解车辆的运动学和动力学方程,以得到
车辆在不同工况下的运动性能。
例如,可以计算车辆的加速度、制动距离、最大行驶速度等指标。
在汽车整车动力学仿真分析中,还可以对不同的设计方案进行比较和
评估。
例如,可以比较不同车辆配置下的加速性能,或者评估不同悬挂系
统对车辆操控性能的影响。
通过这种比较和评估,可以帮助工程师选择最
佳的设计方案,并进行必要的优化。
此外,汽车整车动力学仿真分析还可以用于进行车辆的故障诊断和故
障排除。
通过对车辆在不同工况下的仿真分析,可以定位和解决一些潜在
的动力学问题,以提高车辆的安全性和可靠性。
总之,汽车整车动力学仿真分析是一种非常有效的工具,可以帮助工
程师在汽车设计过程中预测和优化车辆的运动性能、稳定性和操控性能。
它可以帮助工程师选择最佳的设计方案,并进行必要的优化,从而提高车
辆的性能和安全性。
汽车碰撞模拟仿真分析对车辆整体结构刚度的优化策略

汽车碰撞模拟仿真分析对车辆整体结构刚度的优化策略一、引言车辆碰撞安全一直是汽车设计中至关重要的考虑因素之一。
在汽车行业中,进行碰撞模拟仿真分析成为了一种有效的手段,可以在设计阶段对车辆进行安全性能评估和优化。
本文将探讨使用碰撞模拟仿真分析技术对车辆整体结构刚度进行优化的策略。
二、汽车碰撞模拟仿真分析原理汽车碰撞模拟仿真分析是通过建立数学模型,并利用计算机软件对车辆在各种碰撞情况下的动态响应进行预测和分析。
其中,对车辆整体结构刚度的优化是模拟仿真分析的重要一环。
三、车辆整体结构刚度的意义车辆整体结构刚度是指车身结构在受到碰撞时的抗变形性能,也是保证车辆乘员安全的重要指标之一。
较高的整体结构刚度可以有效降低车身的变形程度,减少乘员的受伤风险。
四、优化策略一:材料选择与加强合理的材料选择和加强可以显著提高车身整体结构的刚度。
通过使用高强度钢材料或复合材料等新型材料,并在关键连接部位进行加固设计,可以提高车身的刚度和耐久性。
五、优化策略二:结构设计与优化车辆整体结构的设计和优化是提高刚度的重要手段。
通过在设计阶段采用适当的结构形式,如选择合适的梁柱形式、增加加强筋等,可以有效提高车辆整体结构的刚度。
六、优化策略三:优化悬挂系统悬挂系统是车辆整体结构的一部分,也对刚度的提高起到重要作用。
通过优化悬挂系统的设计,如增加悬挂支撑件、调整悬挂参数等,可以改善车辆的悬挂刚度,进而提升整体结构的刚度。
七、优化策略四:合理分配车身刚度在设计车辆整体结构的同时,合理分配车身的刚度也是提高整体刚度的关键。
通过在不同区域设置合适的刚度分布,可以减少碰撞能量对车辆的影响,降低乘员受伤的可能性。
八、模拟仿真分析在刚度优化中的应用利用碰撞模拟仿真分析技术,可以在设计阶段对车辆整体结构进行虚拟碰撞测试,验证刚度优化策略的有效性。
此外,通过分析仿真结果,可以得出最佳的刚度优化方案,为车辆的实际制造提供有力的指导。
九、结论汽车碰撞模拟仿真分析对车辆整体结构刚度的优化策略有重要意义。
汽车仿真模型分析报告
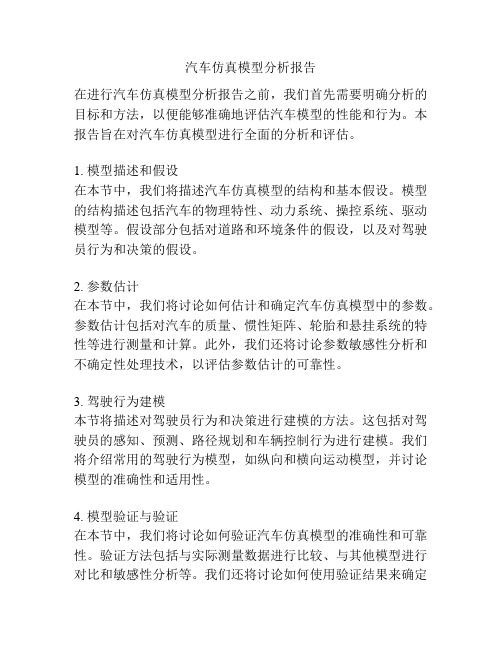
汽车仿真模型分析报告在进行汽车仿真模型分析报告之前,我们首先需要明确分析的目标和方法,以便能够准确地评估汽车模型的性能和行为。
本报告旨在对汽车仿真模型进行全面的分析和评估。
1. 模型描述和假设在本节中,我们将描述汽车仿真模型的结构和基本假设。
模型的结构描述包括汽车的物理特性、动力系统、操控系统、驱动模型等。
假设部分包括对道路和环境条件的假设,以及对驾驶员行为和决策的假设。
2. 参数估计在本节中,我们将讨论如何估计和确定汽车仿真模型中的参数。
参数估计包括对汽车的质量、惯性矩阵、轮胎和悬挂系统的特性等进行测量和计算。
此外,我们还将讨论参数敏感性分析和不确定性处理技术,以评估参数估计的可靠性。
3. 驾驶行为建模本节将描述对驾驶员行为和决策进行建模的方法。
这包括对驾驶员的感知、预测、路径规划和车辆控制行为进行建模。
我们将介绍常用的驾驶行为模型,如纵向和横向运动模型,并讨论模型的准确性和适用性。
4. 模型验证与验证在本节中,我们将讨论如何验证汽车仿真模型的准确性和可靠性。
验证方法包括与实际测量数据进行比较、与其他模型进行对比和敏感性分析等。
我们还将讨论如何使用验证结果来确定模型的适用范围和局限性。
5. 性能评估与改进本节将评估汽车仿真模型的性能和表现。
性能评估涉及模型的准确性、稳定性、即时性和可扩展性等方面。
我们将讨论如何根据评估结果对模型进行改进和优化,以提高模型的性能和可用性。
6. 结论和展望在本节中,我们将对整个汽车仿真模型分析报告进行总结,并提出未来的研究方向和改进建议。
我们还将讨论目前所遇到的挑战和限制,并展望汽车仿真模型研究的发展方向。
在以上的内容中,我们将对汽车仿真模型进行全面的分析和评估,并提出相应的建议和改进措施。
通过该报告,我们将能够更好地理解和应用汽车仿真模型,提高汽车系统设计和性能评估的效率和准确性。
- 1、下载文档前请自行甄别文档内容的完整性,平台不提供额外的编辑、内容补充、找答案等附加服务。
- 2、"仅部分预览"的文档,不可在线预览部分如存在完整性等问题,可反馈申请退款(可完整预览的文档不适用该条件!)。
- 3、如文档侵犯您的权益,请联系客服反馈,我们会尽快为您处理(人工客服工作时间:9:00-18:30)。
. ..z AVL-Cruise整车性能分析1 模型的构建要求1.1 整车动力性、经济性计算分析参数的获取收集和整理关于该车的整车配置组件参数数据。
主要包括发动机动力性、经济性参数;变速箱档位速比参数;后桥主减速比参数;轮胎参数;整车参数等。
具体参数项目见附录1。
1.2 各配置组件建模1.2.1 启动软件在桌面或程序中双击AVL-Cruise快捷图标,进入到AVL-Cruise用户界面,点击下图所示工具图标,进入模型创建窗口。
进入模型创建窗口1.2.2 建立整车参数模型进入模型创建窗口后,将鼠标选中Vehicle Model,鼠标左键点击整车图标,按住左键将图标拖曳到建模区,如下图所示:双击整车图标后打开整车参数输入界面,根据参数输入要求依次填写数据:Author:此处填写计算者,不能用中文,可以用汉语拼音和英文,该软件所有填写参数处均不能出现中文。
. ..zComment :此处填写分析的车型号。
Notice1、Notice2、Notice3:此处填写分析者认为需要注意的事项,比如特殊发动机型号等,没有可 以不填。
1.2.2.1 整车参数数据填写规则序号 驾驶室形式 迎风面积 风阻系数 备注1 奇兵车身(平顶) 5.0(1830*2760) 0.7 迎风面积=前轮距*整车高度2 奇兵车身(高顶) 6.422(1900*3380) 0.753 6系、9系平顶车身 6.1(2020*3020) 0.8 重卡风阻系数参考值:0.7-14 6系、9系高顶车身 7.0(2020*3460) 0.9 5高顶加导流罩7.3(2020*3637)0.92进入模型创建窗口后,将鼠标选中Engine Model ,鼠标左键点击发动机图标,按住左键将图标拖曳到建模区,如下图所示:作者名称、注解说明,可以不填注解说明,可以不填油箱容积 内外温差:0试验台架支点高度:100内外压差:0 牵引点到前轴距离轴距空载、半载、满载下整车重心到前轴中心距离、重心高度、鞍点高度、前轮充气压力、后轮充气压力整备质量 整车总重迎风面积风阻系数前轮举升系数后轮举升系数双击发动机图标后打开发动机参数输入界面,根据参数输入要求依次填写数据:1.2.3.1 发动机参数输入规则序号 发动机惯量 达到全功率的响应时间柴油热值 柴油密度 1 参考值:1.25参考值:0.1参考值:44000kj/kg0.82kg/L2 3按照图示箭头位置单击按钮,弹出外特性输入窗口:型号是否有增压器 发动机排量发动机工作温度缸数 冲程数 怠速转速 额定最高转速惯量 达到全功率响应时间0.1S燃油类型热值燃油密度作者名陈、注解说明 注解说明. ..z发动机转速与扭矩的关系从外特性数据表中可以直接得到;填写时注意对应关系即可。
1.2.3. 3 发动机万有特性曲线输入发动机万有特性数据的输入需要注意数据与单位一致;当万有特性数据只有相对油耗(g/kwh )数据时,发动机的万有特性数据输入需要使用Properties 选定指定油耗图来输入数据,如下图:此处根据厂家提供的发动机数据输入转速与扭矩关系此处根据厂家提供的发动机数据输入转速、扭矩、燃油消耗率的关系数据通过选定指定油耗图弹出:Specific Consumptoin Map窗口,在这个窗口里分别输入转速、BMEP、燃油消耗率的对应数据关系。
其中BMEP=2*3.14*n(转速)/V(排量)。
1.2.4变速箱模型建立将变速箱模块拖曳到建模窗口中。
双击图标后弹出变速箱对话框:添加注解或评论添加注解或评论单击此处输入速比. ..此处输入变速箱各档位速比1.2.5离合器模型建立将离合器模块拖曳到建模窗口中。
单击离合器模块弹出离合器对话框:z单击Pressure 弹出压盘力窗口如下图:1.2.6后桥主减器模型建立如下图单击鼠标左键弹出Gear Box 控制模块,鼠标左键选中Single Ratio 并拖曳到建模窗口:鼠标左键双击Single Ratio 弹出主减速器参数窗口:添加注解输入惯量输出惯量最大传递扭矩单击此处离合行程压盘力此处填写离合行程与压盘力的关系曲线输入惯量参考值:1.35; 输出惯量参考值:0.11. ..注解注解速比输入惯量:参考值0.02 输出惯量:参考值0.02效率:参考值0.94单击此处弹出对话框1.2.7轮间差速器模型建立鼠标左键将差速器图标拖曳至建模窗口,如下图:双击差速器图标弹出数据窗口,如下:z1.2.8制动器模型建立鼠标左键选中图标并拖曳至建模窗口,如下图:鼠标左键双击制动器图标,填出制动器数据窗口,如下图:1.2.9轮胎模型建立鼠标左键选中Wheel 图标并拖曳至建模窗口,如下图:注解 注解选择是否锁止输出惯量:参考值0.02输出惯量:参考值0.02输入惯量:参考值0.02扭矩分配因子:1注解 注解制动缸面积 摩擦系数制动力作用半径制动因子:盘式为1;鼓式大于1制动效率惯量:参考值1.0. ..z 鼠标左键双击Wheel图标弹出数据对话框,如下图:单击Rolling Radius弹出数据对话框,如下图:单击Rolling Resistance弹出数据对话框,如下图:注解注解惯量:参考值5.0轮荷修正系数参考值:0.02轮胎摩擦系数参考轮荷静态半径动态半径根据最高车速试验条件为设计满载质量下的测量的,因此,此处轮胎半径统一给静态负荷下半径滚动阻力参数输入数值表轮胎与地面的滚动阻力参考滚动阻力参数输入数值表输入数据。
需要注意的是:轮胎模型数据输入完成后,要通过单击Properties弹出的对话框中指定轮胎的位置前、后、左、右,如下图:1.2.10驾驶员模型建立鼠标左键选中驾驶室图标并拖曳到建模窗口,如右图所示:单击图标弹出数据对话框,如下图:. ..z鼠标左键单击Acceleration Pedal Characteristic 弹出数据对话框如下图:在此对话框中输入加速踏板与油门开启比例的对应关系;通常参考图中给出的数据填写;与此类似,依次点击Clutch Pedal Characteristic 和Brake Pedal Characteristic 按钮,可以依次弹出离合踏板与离合行程、制动踏板与制动压力的对应关系对话框,其数据填写与加速踏板一样。
注意:以上各组件数据的填写除了表明使用参考数据外,其余参数均应以实际数据填写。
2、整车模型的搭建2.1 平板车、自卸车8*4整车模型各组件模块均拖曳到建模窗口并填好数据后,如下图将各组件按照动力传递的顺序连接起来。
注解注解换档方式前进档数踏板制动力缓速器级数倒档数2.2 平板车、自卸车6*4整车模型3、计算任务的设定根据软件的设计和整车技算的需要,应设定如下计算任务:3.1、全负荷加速度计算任务其中包括三个子任务:. ..3.1.1、各档位最大加速度计算工况:此工况可以得到各档位下的最大加速度。
3.1.2、起步连续换档加速度计算工况:此工况可以得到起步连续换档到某一车速时的加速时间。
3.1.3、直接档加速度计算任务:此工况可以得到直接档在某一车速下加速到另一车速下的加速时间。
3.2、等速巡航计算工况3.2.1、各档位等速油耗计算工况:此工况可以计算出各个档位在设定车速下的等速百公里油耗。
3.2.2、最大车速计算工况:此工况可以计算出整车最大车速。
3.3、爬坡计算工况:此工况可以计算各档位最大爬坡度。
3.4、最大牵引力计算工况:此工况可以计算出各档位的最大牵引力,而且功率平衡图也是这一工况计算得出的。
3.5、制动滑行工况:此工况可以计算制定车速下整车的制动距离和制动时间。
3.6、计算任务加载方式前面涉及到的各种计算任务其加载方法是一样的,方法如下:3.6.1、如下图鼠标右键单击Project弹出子菜单,鼠标左键在子菜单上选中add—Task Folder添加到项目中。
3.6.2、建立完任务夹后,如下图,鼠标右键单击Task Folder弹出子菜单,鼠标左键在子菜单上选中所需的计算任务:比如,全负荷加速时间、等速油耗、爬坡性能、牵引力、制动滑行等。
z在各计算任务数据输入时注意选择与计算任务相适应的参数设置。
4、计算结果输出4.1、计算数据输出整车模型建立完成,经过检查无误后可以进行计算,计算输出的数据主要有:输出项目整车配置备注动力性最高车速(km/h)最大爬坡度(%)原地起步连续换档至最高车速80%时加速时间直接档最低稳定转速加速到最高车速80%时加速时间最大牵引力(N)初速度50km/h制动距离(mm)初速度50km/h制动时间(S)功率储备(最高档加速度m/s2)制动减速度a=v2/2s(m/s2)经济性L/100km 最高档等速30km/h等速40km/h等速50km/h等速60km/h等速70km/h等速80km/h综合计算值次高档等速30km/h等速40km/h等速50km/h等速60km/h等速70km/hz注:根据交通部发布的“营运货车燃料消耗限制和测量方法”的规定,营运货车的燃料消耗按照综合油耗计算,其计算公式:因此,在计算完各档位等苏油耗的基础上要根据以上的权重系数和计算公式进行综合油耗的计算。
4.2、计算图输出: 4.2.1、功率平衡图输出:如下图所示,在Result Manager 中左键单击traction force 文件夹,在弹出的下拉数据中左键单击 Suumation of Wheel Power 即可在右侧显示功率平衡图。
4.2.2、爬坡度曲线图:如下图所示,在Result Manager中左键单击traction force 文件夹,在弹出的下拉数据中左键单击Climbing Performance 图标即可在窗口右侧显示爬坡性能曲线图。
补充:考虑挂车情况下的牵引车建模考虑挂车情况下的牵引车建模模型如下图所示:带挂车的牵引车建模模型挂车参数输入:. ..z考虑挂车的整车风阻是通过公式:计算得出的。
因此,需要输入整车风阻系数、迎风面积和考虑挂车后被挂车挡住减少部分时的风阻系数、迎风面积等,具体参见下图:风阻系数输入列表:迎风面积输入列表:鞍点到挂车轴填0挂车整备质量整车总质量此数据中需要输入整车风阻系数、迎风面积和被挂车挡住后减少的迎风面积之间的关系;该数据需要试验获得此数据中需要输入整车风阻系数、迎风面积和被挂车挡住后减少的迎风系数之间的关系;该数据需要试验获得带挂车的牵引车模型虽然可以建立,但是挂车与整车之间的风阻系数、迎风面积、挂车减少后的风阻系数、迎风面积之间的关系却没有试验数据可以支撑,因此建立此详细模型需要一定的数据支持!如果没有详细的挂车模型参数,则仍然借用原有的将挂车等效到牵引头上的简化牵引车模型进行计算,其误差相差不大!说明以上是运用Cruise进行模型建立的基本数据输入、模型搭建、计算任务、结果输出等基础知识,部分内容尚未完善,今后会随着计算需求的改变和提高进行及时的修正。