柴油加氢装置的原理
柴油加氢装置的原理

柴油加氢装置的原理
柴油加氢装置是一种利用催化剂催化反应的装置,用于将柴油中的硫、氮和其他杂质还原为较为纯净的烷烃化合物。
该装置主要由催化剂床、加氢循环系统、加氢炉和分离装置等组成。
柴油加氢装置的主要原理是通过将柴油引入加氢炉中,在高温和高压的条件下与氢气一起进入催化剂床。
催化剂床中的催化剂会催化柴油分子中的硫化物、氮化物和其他杂质与氢气发生反应,将其转化为气体。
而催化剂床中的气体会与床外的循环氢气混合后再次进入催化剂床,形成加氢循环。
在催化剂床中,硫化物会被催化剂吸附并转化为硫化氢
(H2S),氮化物会被还原为氨(NH3),氧化物则会被还原为水蒸气(H2O)。
同时,催化剂会催化柴油中的不饱和化合物和芳香化合物转化为饱和烷烃化合物,提高柴油的燃烧性能和稳定性。
经过催化反应后的气体会进入分离装置,通过冷凝、吸附和脱水等工艺,将其中的硫化氢、氨和水蒸气等杂质分离出来,以获得处理后的柴油。
分离后的杂质则经过进一步的处理或回收利用,从而实现对柴油中杂质的有效去除。
柴油加氢装置的主要目的是降低柴油中硫、氮等杂质的含量,以满足环保要求和提高柴油燃烧效率。
它不仅可以提高柴油的质量,还可以减少柴油的污染排放,对保护环境和人体健康具有重要意义。
柴油加氢可行性研究报告

柴油加氢可行性研究报告一、前言柴油是一种广泛应用于交通运输和工业生产的燃料,然而,由于其高含硫量和产生的污染物排放,柴油燃料已经成为环境保护的焦点。
在此背景下,柴油加氢技术被认为是一种有效的环保和能源节约方式。
因此,本报告将探讨柴油加氢技术的可行性,包括技术原理、应用前景以及经济和社会影响等方面。
二、技术原理柴油加氢技术是一种利用氢气将柴油分子结构进行变换,去除其中的硫和氮等杂质,从而提高柴油的质量和燃烧效率的技术。
该技术的主要原理是利用氢气与柴油中的硫、氮等杂质发生化学反应,将其转化为相对较为稳定的物质,从而降低污染物排放。
柴油加氢技术的关键是加氢反应器,其主要由催化剂、反应器筒体、加热器、冷却器、压缩器等部件组成。
当柴油燃料与氢气一起进入反应器内,经过催化剂的作用,原始的含硫和氮的柴油会经过一系列的化学反应,最终得到低硫和低氮的高质量柴油。
三、应用前景1.环保效益:柴油加氢技术可以明显降低柴油燃料中的硫和氮含量,从而有效减少柴油燃烧所产生的二氧化硫、氮氧化物等大气污染物排放。
2.节能效益:由于加氢后的柴油具有更高的燃烧效率,因此可以减少燃油消耗,从而节约能源。
3.车辆维护成本降低:低硫和低氮的柴油燃料可以减少车辆排放系统的腐蚀和损坏,从而降低车辆维护成本。
4.社会影响:柴油加氢技术的应用还可以提高柴油的利用效率,缓解能源供需紧张局面,减少化石能源对环境的影响。
四、经济影响尽管柴油加氢技术具有明显的环保和能源节约效益,但其推广应用仍面临一定的经济压力。
柴油加氢技术需要投入大量的资金来建设加氢装置,并且每吨柴油加氢处理的成本也相对较高。
此外,柴油加氢技术涉及到复杂的反应过程和催化剂的研发,需要进行大量的科研投入。
因此,从经济角度考虑,柴油加氢技术的推广应用需要政府和企业的支持和鼓励。
从长远来看,柴油加氢技术的投资可以带来可观的回报。
随着环保意识的不断增强,柴油加氢技术的应用前景广阔。
在未来,随着柴油加氢技术的成熟,其成本也将逐步降低,从而增加其在柴油燃料生产领域的竞争力。
柴油加氢技术总结_锅炉技术总结范文

柴油加氢技术总结_锅炉技术总结范文柴油加氢技术是一种新型的能源利用技术,能够有效地降低柴油对环境的污染程度,提高燃料利用效率,具有广泛的应用前景。
经过多年技术研究和实践,目前柴油加氢技术已成熟,以下是柴油加氢技术的总结:一、柴油加氢技术概述柴油加氢技术是一种利用氢气将柴油分子中的碳氢键断裂,再与氢原子结合生成新的高氢化合物的过程。
该技术能够改善柴油的性能和组成,提高柴油的热值和燃烧效率,降低柴油的凝固点和燃烧产物中的污染物含量。
柴油加氢技术是一种改变柴油分子结构的过程,其原理是通过加氢反应将长链烃分子裂解成更短的链烃分子,降低分子量,增加分子中的氢原子含量,使其更易于燃烧。
1.改善燃油性能2.提高燃料利用效率通过柴油加氢技术,可以降低柴油的凝固点,增加柴油的可流动性,使柴油更易于燃烧,从而提高燃料利用效率。
3.降低柴油对环境的污染柴油加氢技术能够降低柴油对环境的污染程度,使其燃烧产生的污染物含量更少,具有更好的环保性能。
目前,柴油加氢技术已经得到了广泛应用。
在燃油加氢方面,一般采用常压或低压加氢工艺,通常使用的反应器有固定床反应器和流化床反应器等。
五、柴油加氢技术的优势和不足1.柴油加氢技术的优势主要体现在其能够有效地降低燃料的污染程度,提高燃料利用效率,同时也可以降低柴油的凝固点。
2.柴油加氢技术的不足主要在于其投资成本较高,而且加氢反应条件要求严格,操作难度较大。
未来柴油加氢技术的发展趋势主要包括以下几个方面:1.技术研究不断深入随着柴油加氢技术的应用越来越广泛,未来将有更多的研究机构和企业投入到该领域的技术研究中,是技术不断深入发展。
2.技术应用更加广泛未来柴油加氢技术将会在更多的领域得到应用,并且在不断发展的新能源领域中,具有较大的发展前景。
3.推广普及加氢技术未来柴油加氢技术将会得到更多的推广和普及,更多的汽车需求将使用加氢技术的柴油燃料,从而提高柴油燃油的效率和环保性能。
综上所述,柴油加氢技术是一种具有较大发展前景的新兴能源技术,尤其对于环保和低碳经济有着十分重要的作用,未来该技术将会得到更广泛的应用和推广。
柴油加氢工艺及催化剂
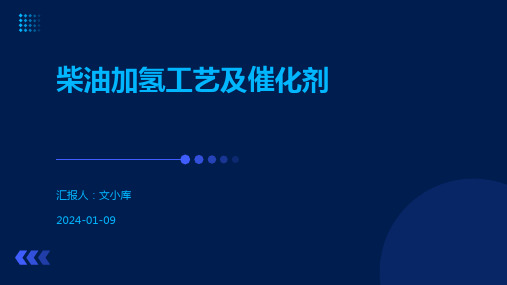
再生
催化剂在加氢反应过程中会发生失活,研究有效的再生 方法,如化学再生、热再生等,以恢复催化剂的活性, 延长其使用寿命。
回收利用
催化剂经再生后仍可继续使用,应研究催化剂的回收利 用技术,实现资源的循环利用,降低生产成本并减少环 境污染。
THANKS
谢谢您的观看
它通过在高温高压条件下,利用氢气与柴油中的硫、氮等杂质以及烃类化合物的 反应,将其转化为硫化氢、氨气和水蒸气等气体,从而脱除杂质并改善柴油的燃 烧性能。
柴油加氢工艺的原理
柴油加氢的基本原理是加氢反应,即将氢气与柴油中的硫、 氮等杂质以及烃类化合物进行反应,生成硫化氢、氨气和水 蒸气等气体,同时将烃类化合物中的不饱和烃转化为饱和烃 ,提高油品的稳定性。
探索新型制备方法
要点一
传统制备方法
采用沉淀法、溶胶-凝胶法、微乳液法等传统方法制备柴油 加氢催化剂,这些方法虽然成熟,但存在成本高、周期长 等缺点。
要点二
新型制备方法
研究新型的制备方法,如模板法、自组装法、离子液体法 等,以简化制备过程、降低成本、提高催化剂性能和缩短 研发周期。
加强催化剂的再生与回收利用
VS
浸渍法是一种常用的催化剂制备方法 ,通过将载体浸入含有活性组分的溶 液中,再经洗涤、干燥和煅烧等后处 理,得到催化剂。该方法操作简便, 适用于制备高分散度的催化剂。浸渍 法的优点是活性组分在载体上分布均 匀,有利于提高催化剂的活性。
溶胶-凝胶法
一种新型的催化剂制备方法
溶胶-凝胶法是一种新型的催化剂制备方法,通过将金 属盐溶液与沉淀剂反应,生成凝胶态的溶胶,再经干 燥和煅烧等后处理,得到催化剂。该方法具有操作简 便、成本低廉等优点,适用于制备高纯度、高分散度 的催化剂。溶胶-凝胶法的优点是活性组分在载体上分 布均匀,有利于提高催化剂的活性。
探究柴油加氢处理工艺的研究进展

探究柴油加氢处理工艺的研究进展柴油加氢处理是目前柴油加工工艺中的一个重要环节,通过加氢处理可以提高柴油的性能和质量,使得柴油燃烧更加充分和稳定,减少对环境的污染。
近些年来,柴油加氢处理工艺的研究取得了一些重要进展,为柴油加工工艺的优化和提高提供了新的思路和方法。
本文将通过对柴油加氢处理工艺的研究进展进行探究,分析其对柴油燃烧性能和环保性能的影响,以及未来的发展方向和挑战。
一、柴油加氢处理工艺的基本原理柴油加氢处理工艺是指通过加氢反应,将柴油中的多环芳烃、烯烃和硫化物等不饱和和有害物质转化为饱和和无害物质的工艺。
该工艺的基本原理是通过高压加氢反应器中加入氢气,并在催化剂的作用下,使柴油中的不饱和烃和有害物质发生加氢反应,生成饱和烃和无害物质,从而提高柴油的性能和质量。
1. 催化剂的研究催化剂是柴油加氢处理中的关键技术之一,其性能和稳定性直接影响了加氢反应的效果。
近年来,研究人员对催化剂的微观结构和成分进行了深入研究,通过控制催化剂的孔道结构、活性中心和晶面结构等,提高了催化剂的活性和选择性,使得加氢反应更加高效和稳定。
2. 工艺条件的优化柴油加氢处理工艺涉及到高温高压等复杂的工艺条件,其优化对提高加氢效率和降低能耗具有重要意义。
近年来,研究人员通过对工艺条件进行系统优化和控制,降低了加氢反应的活化能,提高了反应速率和选择性,使得柴油加氢处理的成本和能耗得到了有效的降低。
3. 反应机理的研究加氢反应的反应机理对于提高加氢效率和降低副反应具有重要意义。
近年来,研究人员通过理论模拟和实验研究,对加氢反应的反应机理进行了深入探究,揭示了加氢反应的动力学过程和影响因素,为进一步优化加氢工艺提供了基础理论支撑。
4. 柴油质量的改善通过柴油加氢处理工艺,可以降低柴油中的硫含量、多环芳烃含量和烯烃含量,提高柴油的蜡含量和密度,从而改善柴油的燃烧性能和环保性能。
近年来,研究人员通过优化加氢工艺,使得柴油的硫含量、芳烃含量和烯烃含量得到了有效降低,柴油的燃烧性能和环保性能得到了显著改善。
柴油加氢装置
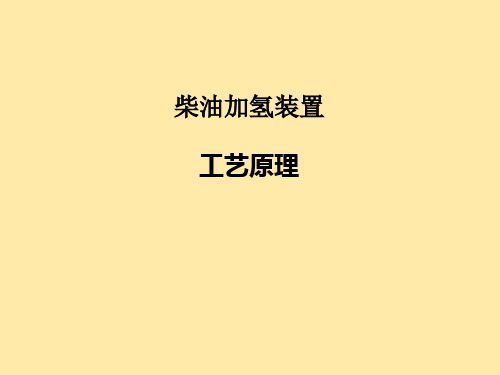
精制反应器内发生的反应
含硫有机物
催化剂
H2
烃类
含氮有机物
H2
催化剂
烃类
含氧有机物
H2
催化剂
烃类
金属有机物
H2
催化剂
烃类
烯烃
催化剂
H2
烷烃
H2S NH3 H2O 金属单质
与重整精制反应不同有:烃类碳数不同,杂质含量不同。 与重整精制反应相同有:均为放热反应,体积缩小反应。
低 分 罐
精制油去分馏塔 污水
在改质反应器内发生的主要反应第1、2步反应,
十六烷值为零
十六烷值约20以上
非柴油组分
想避免第3步反应的发生,就要控制好反应深度,即反应 温度、反应压力、反应空速、氢油比等。
新氢 原料泵
柴油加氢精制装置反应系统工艺流程
循环氢压缩机 冷却器
排放氢
加热炉
1
2
高
低分气
分
罐
低
高 分 罐
污水
冷氢
低分气
低 分 罐
精制油去分馏塔 污水
高分罐分离的是油、水、氢气三相的。
新氢 原料泵
柴油加氢精制装置反应系统工艺流程
循环氢压缩机 冷却器
排放氢
加热炉
1
2
高
低分气
分
罐
低
污水
分 罐
精制反应器
改质反应器
冷氢
精制油去分馏塔 污水
排除的污水中,含有H2S、NH3,这是物 理方法第一次脱除S、N、O元素。
催化剂
烯烃
催化剂
H2
烃类 烃类 烃类 烃类 烷烃
汽柴油加氢技术总结汇报
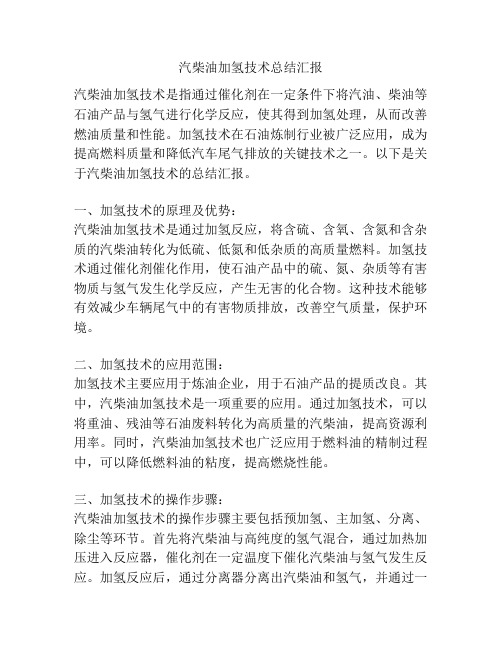
汽柴油加氢技术总结汇报汽柴油加氢技术是指通过催化剂在一定条件下将汽油、柴油等石油产品与氢气进行化学反应,使其得到加氢处理,从而改善燃油质量和性能。
加氢技术在石油炼制行业被广泛应用,成为提高燃料质量和降低汽车尾气排放的关键技术之一。
以下是关于汽柴油加氢技术的总结汇报。
一、加氢技术的原理及优势:汽柴油加氢技术是通过加氢反应,将含硫、含氧、含氮和含杂质的汽柴油转化为低硫、低氮和低杂质的高质量燃料。
加氢技术通过催化剂催化作用,使石油产品中的硫、氮、杂质等有害物质与氢气发生化学反应,产生无害的化合物。
这种技术能够有效减少车辆尾气中的有害物质排放,改善空气质量,保护环境。
二、加氢技术的应用范围:加氢技术主要应用于炼油企业,用于石油产品的提质改良。
其中,汽柴油加氢技术是一项重要的应用。
通过加氢技术,可以将重油、残油等石油废料转化为高质量的汽柴油,提高资源利用率。
同时,汽柴油加氢技术也广泛应用于燃料油的精制过程中,可以降低燃料油的粘度,提高燃烧性能。
三、加氢技术的操作步骤:汽柴油加氢技术的操作步骤主要包括预加氢、主加氢、分离、除尘等环节。
首先将汽柴油与高纯度的氢气混合,通过加热加压进入反应器,催化剂在一定温度下催化汽柴油与氢气发生反应。
加氢反应后,通过分离器分离出汽柴油和氢气,并通过一系列的脱硫、脱氮、脱杂等工艺处理,最终得到高质量的汽柴油产品。
四、加氢技术的优势与不足:加氢技术具有以下优势:1. 改善燃料质量:通过加氢处理,汽柴油的硫含量、氮含量和杂质含量得到有效降低,提高了燃料的质量。
2. 降低尾气排放:加氢技术能够减少燃料中的有害物质含量,从而降低了汽车尾气中的污染物排放,改善环境质量。
3. 提高能源利用率:通过将废料油转化为汽柴油,提高了资源利用效率,减少了能源浪费。
不足之处:1. 技术要求高:加氢技术对催化剂稳定性、反应条件、操作参数等要求较高,需要专业技术人员掌握和操作。
2. 设备投资大:加氢技术需要投入大量设备和催化剂,投资成本较高。
柴油加氢装置(汽柴油生产技术课件)
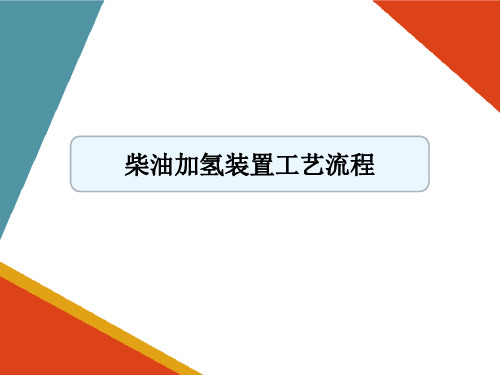
高分罐
LIC 排污
循环氢
LI 低分罐
图5—9 高分罐液位控制示意图
高分罐液位是油相液面高度。偏
高油相和气相分离效果将下降,偏低易形 成高压串低压导致分馏塔操作紊乱。
高分罐界位是水相与油相的界面
高度。偏高油带水,偏低水带油。
高分罐液位的影响因素:
1、高分罐与低分罐压差变化; 2、原料泵出口流量变化; 3、高分罐温度变化。
精制柴油十六烷值偏低,说明反应没有达到部分达到了第2步反应, 也即反应深度不够工艺要求。
1、反应温度偏低; 2、反应压力偏低;
3、催化剂活性偏低; 4、空速偏大。
1、塔顶压力偏 低; 2、塔顶温度偏 高;
精制油从低分罐来 原料泵
回流罐 粗汽油
分 馏 塔
粗汽油干点偏高?
柴油出装置
塔底的轻组分没有气化 上升到塔顶:
低分气
高
分
罐
低
分
分
馏
罐
塔
图5—10 低分罐压力控制示意图
低分罐的作用,一是分担些分馏塔
顶负荷,再是环节高压直接到低压而导致 分离塔的操作紊乱。
低分罐压力的影响因素:
1、高分罐压力变化; 2、分馏塔压力变化; 3、低分罐顶气体出口流量变化; 4、低分罐出口换热器的压降变化。
低分气
从高分罐来 低分罐
石脑油去催化重整装置
分
馏
塔
精制柴油溴价不合格的原
因?
柴油出装置
精制油从低分罐来 原料泵
回流罐
石脑油去催化重整装置
分馏Βιβλιοθήκη 塔精制柴油硫含量超标?
柴油出装置
循环氢压缩机
2、高分罐排污力度 不够工艺要求
新氢
- 1、下载文档前请自行甄别文档内容的完整性,平台不提供额外的编辑、内容补充、找答案等附加服务。
- 2、"仅部分预览"的文档,不可在线预览部分如存在完整性等问题,可反馈申请退款(可完整预览的文档不适用该条件!)。
- 3、如文档侵犯您的权益,请联系客服反馈,我们会尽快为您处理(人工客服工作时间:9:00-18:30)。
由焦化柴油,催化柴油经过液控阀进入柴油反冲洗过滤器除去原料油中大于25μm的颗粒,过滤后的原料油经原料油/精制柴油换热器,与精制柴油换热后进入原料油缓冲罐稳压,然后经原料油泵升压,在流量的控制下,与混合氢混合作为混合进料混合进料经反应流出物/混合进料热热器与反应流出物换热后分四路进入加热炉进行加热,加热后汇成一路进入反应器(R101),反应后经反应流出物/混合进料换热器与混合进料换热后进热高压分离器。
热高分气体经热高分气/混合氢换热器换热后,再经热高分器空冷器冷至49℃进入冷高压分离器。
为了防止反应流出物中的铵盐在低温部分析出,通过注水泵将脱盐水注至上游处的管道中。
冷却后的热高分气在中进行油、气、水三相分离。
自塔顶部出来的循环氢(冷高分气)经循环氢脱硫塔入口分液罐分液后,进入循环氢脱硫塔底部,设有层浮阀塔盘,自贫溶剂缓冲罐来的贫溶剂,经循环氢脱硫塔贫溶剂泵升压后进入第一层塔盘。
脱硫后的循环氢自塔顶出来,经循环氢压缩机入口分液罐分液后进入循环氢压缩机升压,然后分成两路,一路作为急冷氢去反应器(R101)控制反应器床层温升,另一路与来自新氢压缩机出口的新氢混合成为混合氢。
自底部出来的富液在液位控制下与来自底部来的富液合并后至装置外。
V102底部出来的热高分油在液位控制下经过液力透平(HT101)回收能量后进入热低压分离器(V104)。
热低分气经热低分气/冷低分油换热器(E103)与冷低分油换热,再经热低分气冷却器(E104)冷却到49℃后与冷高分油混合进入冷低压分离器(V105)。
自V104底部出来的热低分油与经热低分气/冷低分油换热器(E103)与热低分气换热后的自V105底部出来的冷低分油混合后进入产品分馏塔第26层塔盘。
V105气相与产品分馏塔顶气及汽油脱硫化氢汽提塔塔顶气合并后去干气脱硫塔(T104)脱硫后送装置外管网。
V103与V105底部排出的酸性水及分馏部分V106、V107排出的酸性水合并至公用工程部分含硫污水除油器(V117)进行脱气除油后,污水经泵送至装置外处理。
装置外来的新氢经新氢压缩机入口分液罐(V108)分液后进入新氢压缩机(C102A,B),经三级升压后与C101出口的循环氢混合成为混合氢。
二、分馏部分
从反应部分来的低分油直接进入产品分馏塔(T101),T101设与36层浮阀塔盘,塔底通入汽提蒸气。
塔顶油气经产品分馏塔顶空冷器(A102)。
产品分馏塔顶冷却器(E109)冷凝冷却至40℃,进入产品分馏塔顶回流罐(V106)进行气、油、水三相分离。
闪蒸出的气体送至T104脱硫;含硫污水送至含硫污水除油器(V117);油相经产品分馏塔回流泵(P103A,B)升压后,一部分作为分馏塔顶回流,另一部分作为汽油脱硫化氢汽提塔(T102)的进料。
为了抑制硫化氢对塔顶管道和冷换设备的腐蚀,在塔顶管道注入缓蚀剂。
产品分馏塔底油经柴油泵P105A,B升压后,一部分经汽油脱硫化氢汽提塔底重沸器(E111)、精制柴油/汽油脱硫化氢汽提塔进料换热器(E112)换热,然后与另一部分混合,再经原料油/精制柴油换热器(E105A,B,C)换热后进入精制柴油空冷器(A103)冷却至50,最后经电离脱水设施脱水后出装置。
产品分馏塔顶油作为汽油脱硫化氢汽提塔的进料先经精制柴油/汽油汽提塔进料换热器(E112)换热至200℃后进入T102顶部。
T102内装两层散装填料,塔顶油气经汽油脱硫化氢汽提塔顶冷却器(E110)冷却至40℃,进入汽油脱硫化氢汽提塔顶回流罐(V107)进行气、油、水三相分离。
闪蒸出的气体与低分气、分馏塔顶气合并送至T104脱硫后至装置外管网;含硫污水与高分污水、V106底含硫污水一起送至含硫污水除油器(V117);油相经汽油脱硫化氢汽提塔顶回
流泵(P104A,B)升压后,全部作为汽油脱硫化氢汽提塔回流。
汽油脱硫化氢汽提塔底油,一部分作为塔底循环经汽油脱硫化氢汽提塔底重沸器换热至210℃后进入T102底部,另一部分经精制汽油冷却器(E113)冷却至40℃后至装置外。
三、气体脱硫部分
低分气与产品分馏塔顶气、汽油脱硫化氢汽提塔顶气混合后至干气脱硫塔入口分液罐(V115)分液,分液后的酸性气进入干气脱硫塔(T104)底部。
T104内装三层散堆填料,贫液自贫溶剂缓冲罐(V113)来,经干气脱硫塔贫溶剂泵(P107A,B)升压后进入T104顶部。
由塔底上升的气体与由塔顶下流的贫液在塔中逆流接触,气体中的硫化氢被胺液吸收。
塔顶经脱硫后的气体经脱硫干气分液罐(V114)分液后在压力控制下送装置外管网。
富液自塔底排出,经干气脱硫塔富溶剂泵(P114A,B)升压后在液位控制下与来自T103底部来的富液合并后至装置外。
四、公用工程部分
1、
催化剂预硫化流程
为了使催化剂具有活性,新鲜的或再生后的催化剂在使用前均必须进行活化-预硫化。
本设计采用液相硫化方法,硫化剂为二甲基二硫化物(DMDS)。
硫化时,系统内氢气经C101按正常操作路线进行循环。
DMDS自硫化剂罐来,混入原料油泵(P101A、B)入口,经高压换热器E101A、B进入反应进料加热炉(F101),按催化剂预硫化升温曲线的要求升温,通过反应器R101中催化剂床层进行预硫化。
自R101来的流出物经E101A、B冷却后进入热高压分离器V102进行分离,热高分经A101冷凝后进入冷高压分离器V103进行分离,冷高分气体循环至循环氢压缩机C101,催化剂预硫化过程中产生的水从V103底部间断排出。
2、催化剂再生流程
为了恢复使用过的催化剂活性,催化剂需要再生,该装置催化剂再生按器外再生方式考虑。
五、开工、停工流程
开工时,开工油从罐区来,经原料油过滤器(FI101)、原料油/精制柴油换热器(E105A、B、C)、原料油缓冲罐(V101)、原料油泵(P101A、B)进入系统,待高分、低分建立液位后,引至A103,反应部分建立循环。
反应部分催化剂预硫化的同时,开工油向分馏部分进油,待产品分馏塔建立液位后,分馏部分可以建立油循环,以缩短开工时间。
停工时,原料油缓冲罐(V101)中油经不合格油线出装置。
反应部分油从冷低压分离器(V105)经不合格油线出装置。
分馏部分油品经产品线或不合格油线出装置。
原料经过滤脱水进原料缓冲罐,经泵与氢气混合进入反应器,(在空冷前要注水)经空冷水冷进入高分,油气水三相分离后油进入低分,然后进入分馏塔分馏后的精柴产品。
气路主流程主要是:新氢经缓冲罐进新氢压缩机,提压后进入循环氢缓冲罐和循环氢混合。
在系统中循环氢在反应加热炉前进入,高分分离,经循环压缩机在系统中循环。
柴油加氢装置重沸炉出口温度一般控制在340--350℃之间,最高不大于多少度
400℃。