科德角工厂案例分析报告
科德角工厂案例分析

每小时湿果数量:900-75=12辆
每小时烘干的能力:600-75=8辆
湿贮藏室3200-75=42.66辆,也就是42辆后湿贮藏室贮藏满,卡车需要等待 因为42十12=3.5,也就是说10点半之后卡车就需要等待
卡车等待费用(将每小时卡车等待车辆*10):
6*10+10*10+14*10+18*10+22*10+26*10+30*10+34*10+38*10+30*10+22*10+14*
②干果比例为45%,湿果比例为55%。(干果675个,湿果825个),此时的
瓶颈仍然是烘干
成本
每小时湿果数量:825-75=11辆
每小时烘干的能力:600-75=8辆
湿贮藏室3200-75=42.66辆,也就是42辆后湿贮藏室贮藏满,卡车需要等待
因为42十11=3.82,也就是说10:49分之后卡车就需要等待
科德角工厂生产瓶颈分析报告
Q1
么?
主要问题:
1、车辆卸货排队时间过长
2、高峰期加班费支出过大
主要原因:
1、流程瓶颈限制了整个加工厂的 产能,导致运来的红酸果无法及时处理;2、
工人的工作时间安排不合理, 零时工的管理不佳,缺勤率高,影响生产过程
补充问题一:加工红酸果的制作流程是线性流程一一对象专业化布置。
25-27湿果贮存
250桶/箱
250桶/箱
400桶/箱
最大贮存湿果3200桶
3台*1500桶/台*h
非高峰:1人 下午5点-下午11点/人 高峰:1人
上午11点-下午11点/人
干
非高峰:8人
下午5点-下午11点/人
工厂管理 之 案例分析
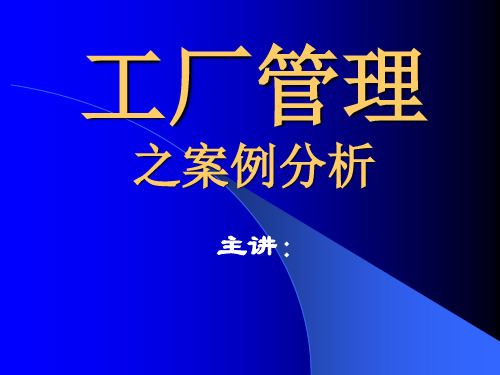
合理化改善
3、合理化四步骤
1.消化:了解目的,熟悉方法 2. 融化:调适于企业体制及文化 3. 活化:PDCA循环不已 4. 同化:形成经营理念,达成全员共识
合理化改善
4、PDCA循环不已
P 计划
1优.正势常计计划划、异常计划、A 改正
D 执
再执行
行
2.人人有责,各自负责
3.异常比率控制在不影 响正常工作的范围内
工厂布置,整齐美观?
管路规划
厂房规划,
色调、亮度、通风…一劳永逸
走道与搬运
往后发展计划
高薪重赏,必有勇夫?
不为与不能
毛虫与蝴蝶
年资与经验
年龄+工龄=60 则退休
台塑60项目探讨
高薪重赏,必有勇夫?
103专案
做了10年后,若3年内职 务再无变化则退休
日本某企业加薪制度如下规定: 每加薪1元,须给公司创造10元价值
检查找到不良 的源头;包括 如设计不良、 材料不良、模 具不良等;可 以消除5%的不 良。
配套措施一:首件检查(大量生产时的) 由质检员、主管检查
配套措施二:制程检查 由作业者的主管检查
新手太多,品质难为? ISO推行过程中的“四不”
不作假 不合理的改善 不增加负担 不应付检查
ISO推行应是现行作 业中的举手之劳
货
出库,凭单销票,每日清账、有 错误补偿法 异常及时处理
账 相
每日逢零、逢低、动态循环盘点 ABC分类法
符 的
类 别
数量 种类 所占比重
价值比重
加强管理,发 检查频率或方法 展免检厂商
方
A类 5% 少 70%~80%
2次/天
d报告案例详解
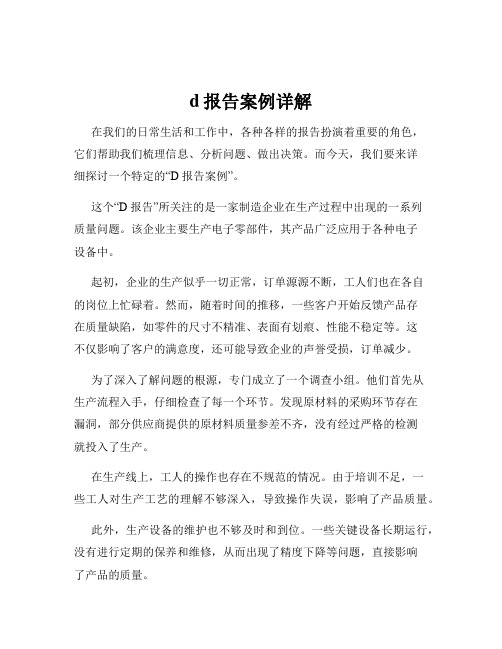
d报告案例详解在我们的日常生活和工作中,各种各样的报告扮演着重要的角色,它们帮助我们梳理信息、分析问题、做出决策。
而今天,我们要来详细探讨一个特定的“D 报告案例”。
这个“D 报告”所关注的是一家制造企业在生产过程中出现的一系列质量问题。
该企业主要生产电子零部件,其产品广泛应用于各种电子设备中。
起初,企业的生产似乎一切正常,订单源源不断,工人们也在各自的岗位上忙碌着。
然而,随着时间的推移,一些客户开始反馈产品存在质量缺陷,如零件的尺寸不精准、表面有划痕、性能不稳定等。
这不仅影响了客户的满意度,还可能导致企业的声誉受损,订单减少。
为了深入了解问题的根源,专门成立了一个调查小组。
他们首先从生产流程入手,仔细检查了每一个环节。
发现原材料的采购环节存在漏洞,部分供应商提供的原材料质量参差不齐,没有经过严格的检测就投入了生产。
在生产线上,工人的操作也存在不规范的情况。
由于培训不足,一些工人对生产工艺的理解不够深入,导致操作失误,影响了产品质量。
此外,生产设备的维护也不够及时和到位。
一些关键设备长期运行,没有进行定期的保养和维修,从而出现了精度下降等问题,直接影响了产品的质量。
针对这些问题,企业采取了一系列的改进措施。
在原材料采购方面,建立了严格的供应商评估和筛选机制,确保原材料的质量稳定可靠。
对于工人的培训,制定了全面的培训计划,包括理论知识和实际操作的培训,并定期进行考核,确保工人能够熟练掌握生产工艺。
在设备维护方面,设立了专门的设备维护团队,制定了详细的设备维护计划,定期对设备进行保养和维修,确保设备的正常运行。
经过一段时间的努力,企业的产品质量得到了显著的提升,客户的满意度也逐渐恢复。
这个“D 报告案例”给我们带来了很多启示。
首先,质量管理是一个系统工程,需要从原材料采购、生产过程控制、人员培训、设备维护等多个方面入手,任何一个环节的疏忽都可能导致质量问题。
其次,及时发现问题并采取有效的解决措施至关重要。
《企业管理案例》分析报告及问题详解

《企业管理案例》分析报告及问题详解《企业管理案例》分析及答案案例1: 一位富于理想的企业家一位富有理想的工匠正打算开办一家自己的企业。
他喜欢木工并想生产工艺桌、柜架和其他家具。
在这之前,他和三个合作者曾为他所在城市的一些大型企业生产了花梨木和核桃木会议桌。
这位有志于成为企业家的人表达了他的思想,这看起来更富于理想化而非商业化。
他相信,享受职业乐趣的氛围而获得成功。
他甚至愿意在付给员工固定的薪水之后,分享企业利润。
试分析:1.对这些人来说会出现哪些企业家的预期回报?它们可能会怎样影响企业的成功?答:其预期回报有:获得成功的满足感;更高的利润;独立自主、按照自己的意愿行动;灵活的工作时间。
这个预期的企业家完全是个工匠,他可能缺乏商业判断力或商业背景。
他的基本特点是熟悉产品工艺技术,他喜欢职业所带来的满足感。
这些动机可以保证产品的质量,如果他再掌握一些经营管理方面的知识,就有可能成功。
2.你愿意对他的新企业投资吗?答:他表达了希望建立富于理想化而非专业化企业的理想,他的最大优势是其专业工作经验。
而对未来的发展和变化很少有计划,缺乏长远的打算,所以这种企业很难有所发展和吸引到投资。
案例2:购买一家现存企业创立企业四年之后,老王打算卖掉自己的企业——奔马公司。
奔马公司是老王亲手创立的,因为他喜欢制作奔马。
经过几年的经营,已经相当成功,收入以年平均50%的增长率增长。
奔马在全国范围的玩具店都有出售。
老张是在同一位企业经纪人接触后了解到这一机会的,他想从大公司退休,并认为这个企业是一个好机会。
试分析:1.你认为老张应该使用哪种评估方法来评价这个企业,为什么?答:如果能够得到和他相似的公司的过去的销售信息,采用市场评估法比较合适。
收益法和现金流量法也会提供一个实际的价值。
这家公司即没有出现财务困难,也没有利润减少的明显迹象。
2.老张还需要考虑什么会计信息?需要做出哪些调整?答:会计人员应该检查账目以确定他们是否采用了合适的会计方法。
《青山制作所》案例分析报告
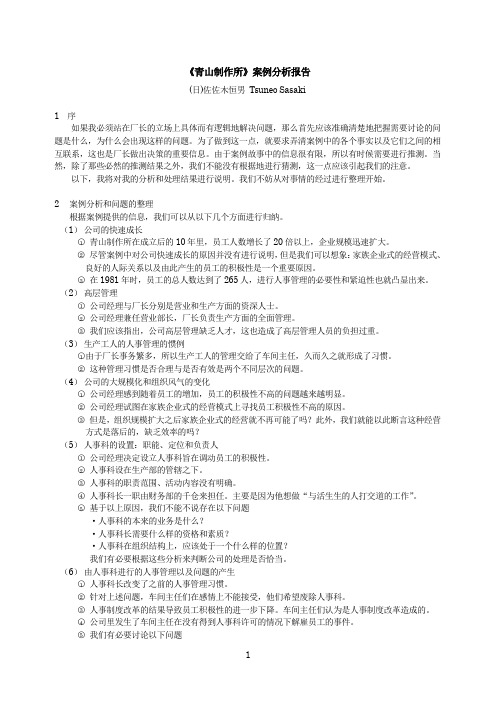
《青山制作所》案例分析报告(日)佐佐木恒男Tsuneo Sasaki1 序如果我必须站在厂长的立场上具体而有逻辑地解决问题,那么首先应该准确清楚地把握需要讨论的问题是什么,为什么会出现这样的问题。
为了做到这一点,就要求弄清案例中的各个事实以及它们之间的相互联系,这也是厂长做出决策的重要信息。
由于案例故事中的信息很有限,所以有时候需要进行推测。
当然,除了那些必然的推测结果之外,我们不能没有根据地进行猜测,这一点应该引起我们的注意。
以下,我将对我的分析和处理结果进行说明。
我们不妨从对事情的经过进行整理开始。
2案例分析和问题的整理根据案例提供的信息,我们可以从以下几个方面进行归纳。
(1)公司的快速成长○1青山制作所在成立后的10年里,员工人数增长了20倍以上,企业规模迅速扩大。
○2尽管案例中对公司快速成长的原因并没有进行说明,但是我们可以想象:家族企业式的经营模式、良好的人际关系以及由此产生的员工的积极性是一个重要原因。
○3在1981年时,员工的总人数达到了265人,进行人事管理的必要性和紧迫性也就凸显出来。
(2)高层管理○1公司经理与厂长分别是营业和生产方面的资深人士。
○2公司经理兼任营业部长,厂长负责生产方面的全面管理。
○3我们应该指出,公司高层管理缺乏人才,这也造成了高层管理人员的负担过重。
(3)生产工人的人事管理的惯例○1由于厂长事务繁多,所以生产工人的管理交给了车间主任,久而久之就形成了习惯。
○2这种管理习惯是否合理与是否有效是两个不同层次的问题。
(4)公司的大规模化和组织风气的变化○1公司经理感到随着员工的增加,员工的积极性不高的问题越来越明显。
○2公司经理试图在家族企业式的经营模式上寻找员工积极性不高的原因。
○3但是,组织规模扩大之后家族企业式的经营就不再可能了吗?此外,我们就能以此断言这种经营方式是落后的,缺乏效率的吗?(5)人事科的设置:职能、定位和负责人○1公司经理决定设立人事科旨在调动员工的积极性。
金星啤酒厂案例分析

金星啤酒厂案例分析第一篇:金星啤酒厂案例分析金星啤酒厂案例分析2012年2月29日我们学校组织了对金星啤酒厂的参观,在这期间,我们通过实地参观和工作人员讲解我们主要了解了金星啤酒的生产线情况、厂子的营销方法和企业文化。
下面我们将从以上三个方面来阐述我们小组本次参于的收获。
经过进一个小时的行程我们观来到终金星啤酒厂,然后经过以一段时间的休息和调整。
由讲解员带领我们参观了,金星啤酒厂的生产线,首先进入的映入眼帘的是几个高大的啤酒发酵罐。
然后进入第一个灌装车间,从酒瓶的清洗、啤酒装瓶、酒瓶压盖、贴商标、高温杀菌到啤酒的装箱打包全部是自动化得。
从讲解员的解说可以得知,一瓶小小的啤酒的生产是多么复杂从粮食的选择、发酵到最后的灌装销售是一个漫长的过程,金星啤酒厂为了保证啤酒的质量,特别设置了一个化验室,实时采样检测啤酒的质量标准。
产品生产线结构紧凑,效率高,全程无菌作业,保证酒的卫生要求,通过这次参观我也知道了生啤酒和熟啤酒的区别,原来啤酒灌装完毕后是生啤酒。
在经过一次高温杀菌就成了熟啤酒了。
生产线是一个企业的心脏,它关系到企业产品的规模和质量。
只有拥有好的生产线,才是保证企业竞争力的最好办法。
金星啤酒之所以在河南、甚至全国如此有名。
这与它们的营销理念和营销方法是分不开的。
企业十分注重他营销队伍的质量,经过多年的历练,企业现在已经建立了一支高素质强能力的营销队伍,在这个知识炸弹的时代,企业看到只有不断学习才能保持自己的优越性。
企业非常重视营销人员的学习能力,建立了中国人力资源开发研究会MBA班、特邀孙巍老师授课节选。
用新知识和新思想自己和团队。
企业同样看重营销队伍的执行力情况,多年来打造了营销团队的狼性执行力。
让企业执行力落到实处。
企业高层的领导艺术更是这支营销团队堆越战越勇的主要原因。
公赏罚分明,注重实践:课堂学习,战场练习。
一个企业的营销关系着企业百分之七十的利润。
一个钢铁营销队伍是企业制胜的法宝。
人们把企业文化比喻为一个企业的灵魂,只一点也不夸张。
科德角工厂案例分析
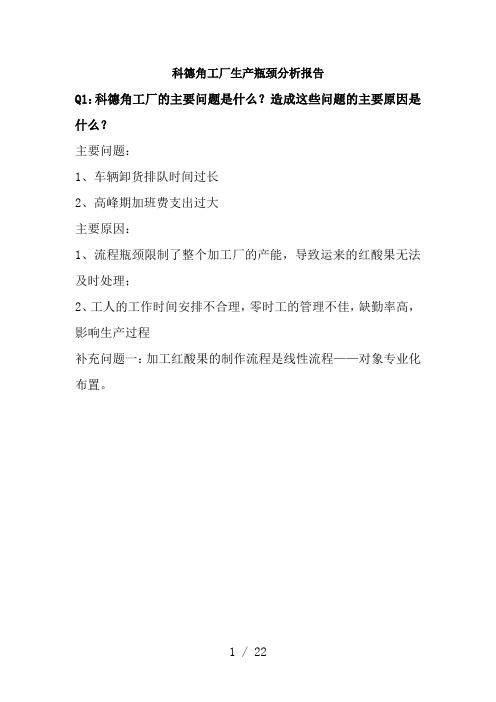
科德角工厂生产瓶颈分析报告Q1:科德角工厂的主要问题是什么?造成这些问题的主要原因是什么?主要问题:1、车辆卸货排队时间过长2、高峰期加班费支出过大主要原因:1、流程瓶颈限制了整个加工厂的产能,导致运来的红酸果无法及时处理;2、工人的工作时间安排不合理,零时工的管理不佳,缺勤率高,影响生产过程补充问题一:加工红酸果的制作流程是线性流程——对象专业化布置。
流程图Q2:分析该生产系统存在的瓶颈。
如果湿果的比例有变化,瓶颈是否有变化呢?瓶颈:由流程图可看出,此时烘干是瓶颈,为600桶/小时烘干完成时间:12600/600=21小时>12小时分选完成时间:18000/1200=15小时>12小时但<21小时比例:烘干湿果的瓶颈能力为600桶/小时,而每小时运送红酸果数量为1500桶/小时,600/1500=40%结论:当湿果所占比例小于40%时,分选是瓶颈;当湿果所占比例大于40%时,烘干是瓶颈。
补充问题二干果比例为40% 45% 50% 55% 60% 时的瓶颈和生产成本以及再算增加一台烘干机的情况下卡车等待时间和加班成本①干果比例为40%,湿果比例为60%.(干果600个,湿果900个)此时的瓶颈仍然是烘干。
成本:每小时湿果数量:900÷75=12辆每小时烘干的能力:600÷75=8辆湿贮藏室3200÷75=42.66辆,也就是42辆后湿贮藏室贮藏满,卡车需要等待因为42÷12=3.5,也就是说10点半之后卡车就需要等待卡车等待费用(将每小时卡车等待车辆*10):6*10+10*10+14*10+18*10+22*10+26*10+30*10+34*10+38*10+30 *10+22*10+14*10+6*10=2720每名工人加班费用:(23.75-11-8)*18.75=89.06总的加班费用=89.06*38=3384.28增加一台烘干机成本:卡车等待成本:1020.8每名工人加班费用:(20.56-11-8)*18.75=29.25总加班成本:29.25*38=1111.5总共节约的成本:3971.98②干果比例为45%,湿果比例为55%。
科德角工厂案例分析

科德角工厂生产瓶颈分析报告Q1:科德角工厂的主要问题是什么?造成这些问题的主要原因是什么?主要问题:1、车辆卸货排队时间过长2、高峰期加班费支出过大主要原因:1、流程瓶颈限制了整个加工厂的产能,导致运来的红酸果无法及时处理;2、工人的工作时间安排不合理,零时工的管理不佳,缺勤率高,影响生产过程补充问题一:加工红酸果的制作流程是线性流程——对象专业化布置。
流程图Q2:分析该生产系统存在的瓶颈。
如果湿果的比例有变化,瓶颈是否有变化呢?瓶颈:由流程图可看出,此时烘干是瓶颈,为600桶/小时烘干完成时间:12600/600=21小时>12小时分选完成时间:18000/1200=15小时>12小时但<21小时比例:烘干湿果的瓶颈能力为600桶/小时,而每小时运送红酸果数量为1500桶/小时,600/1500=40%结论:当湿果所占比例小于40%时,分选是瓶颈;当湿果所占比例大于40%时,烘干是瓶颈。
补充问题二干果比例为40% 45% 50% 55% 60% 时的瓶颈和生产成本以及再算增加一台烘干机的情况下卡车等待时间和加班成本①干果比例为40%,湿果比例为60%.(干果600个,湿果900个)此时的瓶颈仍然是烘干。
成本:每小时湿果数量:900÷75=12辆每小时烘干的能力:600÷75=8辆湿贮藏室3200÷75=42.66辆,也就是42辆后湿贮藏室贮藏满,卡车需要等待因为42÷12=3.5,也就是说10点半之后卡车就需要等待卡车等待费用(将每小时卡车等待车辆*10):6*10+10*10+14*10+18*10+22*10+26*10+30*10+34*10+38*10+30*10+22*10+14* 10+6*10=2720每名工人加班费用:(23.75-11-8)*18.75=89.06总的加班费用=89.06*38=3384.28增加一台烘干机成本:卡车等待成本:1020.8每名工人加班费用:(20.56-11-8)*18.75=29.25总加班成本:29.25*38=1111.5总共节约的成本:3971.98②干果比例为45%,湿果比例为55%。
- 1、下载文档前请自行甄别文档内容的完整性,平台不提供额外的编辑、内容补充、找答案等附加服务。
- 2、"仅部分预览"的文档,不可在线预览部分如存在完整性等问题,可反馈申请退款(可完整预览的文档不适用该条件!)。
- 3、如文档侵犯您的权益,请联系客服反馈,我们会尽快为您处理(人工客服工作时间:9:00-18:30)。
科德角工厂生产瓶颈分析报告Q1:科德角工厂的主要问题是什么?造成这些问题的主要原因是什么?主要问题:1、车辆卸货排队时间过长2、高峰期加班费支出过大主要原因:1、流程瓶颈限制了整个加工厂的产能,导致运来的红酸果无法及时处理;2、工人的工作时间安排不合理,零时工的管理不佳,缺勤率高,影响生产过程补充问题一:加工红酸果的制作流程是线性流程——对象专业化布置。
流程图Q2:分析该生产系统存在的瓶颈。
如果湿果的比例有变化,瓶颈是否有变化呢?瓶颈:由流程图可看出,此时烘干是瓶颈,为600桶/小时烘干完成时间:12600/600=21小时>12小时分选完成时间:18000/1200=15小时>12小时但<21小时比例:烘干湿果的瓶颈能力为600桶/小时,而每小时运送红酸果数量为1500桶/小时,600/1500=40%结论:当湿果所占比例小于40%时,分选是瓶颈;当湿果所占比例大于40%时,烘干是瓶颈。
补充问题二干果比例为40% 45% 50% 55% 60% 时的瓶颈和生产成本以及再算增加一台烘干机的情况下卡车等待时间和加班成本①干果比例为40%,湿果比例为60%.(干果600个,湿果900个)此时的瓶颈仍然是烘干。
成本:每小时湿果数量:900÷75=12辆每小时烘干的能力:600÷75=8辆湿贮藏室3200÷75=42.66辆,也就是42辆后湿贮藏室贮藏满,卡车需要等待因为42÷12=3.5,也就是说10点半之后卡车就需要等待卡车等待费用(将每小时卡车等待车辆*10):6*10+10*10+14*10+18*10+22*10+26*10+30*10+34*10+38*10+30*10+22*10 +14*10+6*10=2720每名工人加班费用:(23.75-11-8)*18.75=89.06总的加班费用=89.06*38=3384.28增加一台烘干机成本:卡车等待成本:1020.8每名工人加班费用:(20.56-11-8)*18.75=29.25总加班成本:29.25*38=1111.5总共节约的成本:3971.98②干果比例为45%,湿果比例为55%。
(干果675个,湿果825个),此时的瓶颈仍然是烘干成本每小时湿果数量:825÷75=11辆每小时烘干的能力:600÷75=8辆湿贮藏室3200÷75=42.66辆,也就是42辆后湿贮藏室贮藏满,卡车需要等待因为42÷11=3.82,也就是说10:49分之后卡车就需要等待成本:卡车等待成本:1*10+4*10+7*10+10*10+13*10+16*10+19*10+22*10+25*10+17*10+9*10+1* 10=1440每名工人加班费用:(22.125-11-8)*18.75=58.59总加班成本:58.59*38=2226.42增加一台烘干机成本:卡车等待成本:208.8(方法同上)每名工人加班费用:(20.34-11-8)*18.75=25.125总加班成本:25.125*38=954.75共节约成本:2502.87③干果比例为50%,湿果比例为50%(干果750个,湿果750个)每小时烘干的数量(卡车数量来计) 600÷75=8辆每小时湿果的卡车数量:750÷75=10辆湿贮藏室3200÷75=42.66辆,也就是42辆后湿贮藏室贮藏满,卡车需要等待。
因为42÷10=4.2,也就是在从开始工作后的4个小时(也就是11点),贮藏室才会堆满。
成本:卡车等待成本:800每名工人加班费用:(21-11-8)*18.75=37.5总加班成本:37.5*38 =1425增加一台烘干机每小时烘干的数量(卡车数量来计) 800÷75=10.66辆因为在11:00工人开始上班,而且此时并没有卡车等待。
而每小时的烘干能力是10.66>10(每小时湿果卡车数量),所以不会有卡车等待费用。
也没有加班费用的产生④干果比例为55%,湿果比例为45%(干果825个,湿果675个)每小时烘干的数量(卡车数量来计) 600÷75=8辆每小时湿果的卡车数量:675÷75=9辆湿贮藏室3200÷75=42.66辆,也就是42辆后湿贮藏室贮藏满,卡车需要等待。
因为42÷9=4。
66,也就是在从开始工作后的4.66个小时(也就是11多点),贮藏室才会堆满。
根据同样的方法可以算出等待的卡车数量为8辆,卡车等待成本为360,加班费用成本:1*18.75*38=712.5增加一台烘干机之后每小时烘干的数量(卡车数量来计) 800÷75=10.66辆因为在11:00工人开始上班,而且此时并没有卡车等待。
而每小时的烘干能力是10.66>9(每小时湿果卡车数量),所以不会有卡车等待费用。
也没有加班费用的产生Q3:解释卡车为什么要等那么长时间。
按题设70%的湿果来算,烘干是造成红酸果无法及时处理的瓶颈,以及工人上班的时间安排不合理,造成了卡车等待的问题:首先将第一批卸货的湿红酸果装进贮存箱里,其他在卡车上要等待贮存箱里的红酸果进入下一工序后才能卸货;湿果运来的速度为12600(18000*70%)/12=1050桶/小时,换算为1050÷75=14辆,每小时烘干的能力为600桶(600÷75=8辆)。
可以看出,每小时的烘干能力远远小于湿果运来的速度。
同时由于工人安排在11:00工作,而储藏室在10:00就已经储藏满了,所以工人的工作时间最少要提前一个小时。
补充问题三每小时湿果数量:1050÷75=14辆每小时烘干的能力:600÷75=8辆湿贮藏室3200÷75=42.66辆,也就是42辆后湿贮藏室贮藏满,卡车需要等待因为42÷14=3,也就是说10点之后卡车就需要等待如果将工人的工作时间提前安排一小时可以看到卡车等待成本:54*10=540每名工人加班费用:(25.75-10-8)*18.75=145.3125总的加班费用=145.3125*38=5521,875可以看出来:提前一小时安排工人工作减少了80的卡车等待成本。
Q4、按计划,处理酸果的工人每天工作12个小时(即要加班4小时),但实际工作时间为什么会大大超过12个小时原因:1、根据上面的计算可以看出是受到瓶颈制约,因为烘干的能力只有600桶,远远小于每个小时运来的红酸果的数量。
这使得加班时间大大超过12小时;2、工人上班时间较晚,不合理的工作计划可能影响了流程进行Q5、在工厂劳动力安排方面,高峰期和非高峰期工作计划是否合理?1、高峰期不合理:根据补充问题二的计算可以看出工人在11点工作的安排是不合理的,因为在10:00时贮藏室就已经贮藏满了,11:00就已经有卡车在等待了,所以应该提前工人的工作时间,至少提前一个小时。
2、低峰期较合理:在低峰期,平均每天运行的红酸果总量,较高峰期少了许多,因此将红酸果的处理工序开始时间延后,有利于充分利用设备生产能力,避免机器空转造成浪费。
Q6、奥布里恩打算安装两台新的烘干机($75000/台),把十六个干果贮存箱改造成干湿兼用贮存箱($15000/个)。
这样可行吗?奥布里恩方案从整体上来说并不能解决问题(1) 如果增加两台烘干机,则烘干的处理能力为(3+2)×200=1000桶/小时,根据下面的图可以看出来,增加两台烘干机之后卡车等待的时间减少,卡车等待的成本减少到194,工人的加班时间也大量缩短了,加班费用减少。
总共可以节约6568.86元。
所以购买两台烘干机的建议是可行的。
成本:卡车等待成本:1561.5每名工人加班费用:(20.45-11-8)*18.75=27.1875总加班费用27.1875*38=1033.125共节约了:8328.75⑵解决瓶颈问题后,储藏问题并不突出,耗资240,000元改造干果贮存箱,是不划算的。
Q7、、你的改进建议是什么,尽量拓展思路1 购买一台烘干机的同时将工人的工作时间提前4个小时(提前到7点) 分析方案一、操作工人提前至7点上班方案一工人加班成本和司机等待成本司机等待成本:如图所示,超过湿果最大库存量3200部分所示的面积,代表了每桶所需要的等待时间的总和,单位为桶小时第一阶段等待S1=(19:00-14:07)*2200/2=5379桶小时 第二阶段等待S2=(22:40-19:00)*2200/2=4037桶小时桶操作工人加工时间9小时时间方案一湿果加工图总等待S=S1+S2+S3=9416桶小时=125.55车小时司机等待成本:125.55*10=1255.5美元工人加班成本:接收工人加班成本:2.67(加班时间)*15(加班人数)*(12.5*1.5)(每人加班费用)=1032.2美元操作工人加班成本:9(加班时间)*38(加班人数)*18.75(每人加班费用)=6412.5美元总工人加班成本:1032.2+6412.5=7444.7美元总成本:1255.5+7444.7=8700.2美元高峰期(20天)总成本:8700.2*20=174003美元方案一比原计划节省的成本:279434-174003=105429美元方案二:操作工人提前至7点上班,同时增加一台烘干机方案二工人加班成本和司机等待成本此方案中,湿果每小时能加工800个,而分选机每小时只能加工1200个,所以干果出现库存,每小时增加450-(1200-800)=50个 司机等待成本:湿果库存3000不超过湿果最大库存量3200,干果库存600不超过干果最大库存4000,所以无司机等待 司机等待成本:0美元 工人加班成本:接收工人加班成本:0美元操作工人加班成本:3.75(加班时间)*38(加班人数)*18.75(每人加班费桶时间用)=2671.9美元总工人加班成本:2671.9+0=2671.9美元总成本:0+2671.9=2671.9美元高峰期(20天)总成本:2671.9*20=53437.5美元方案二比方案一节省的成本:174003-53437.5=120565.5美元方案三:操作工人提起至7点上班,同时增加2台烘干机.方案三工人加班成本和司机等待成本此方案中,湿果每小时能加工1000个,而分选机每小时只能加工1200个,所以干果出现库存,每小时增加450-(1200-1000)=250个桶时间司机等待成本:湿果库存600不超过湿果最大库存量3200,干果库存3000不超过干果最大库存4000,所以无司机等待司机等待成本:0美元工人加班成本:接收工人加班成本:0美元当全部果子接收完后,只需0.6小时就加工完全部湿果,在这0.6小时内干果已加工0.6*200=120个,干果剩余库存3000-120=2880个,此时所有的分选机产能1200个都可以分配给加工干果,所以只需要2880/120=2.4小时就能加工完所有果实,总加班时间为0.6+2.4=3小时。