自卸汽车F式举升机构的设计正式
中顶自卸车举升机构的设计

中顶自卸车举升机构的设计李焕【摘要】Mainly for roof design of dump truck lifting mechanism made a detailed analysis and Exposition. Including the design of the auxiliary frame and the design of lifting mechanism. Illustrates the factors that should be considered in design and the final design results.%主要针对中顶式自卸车举升机构的设计做了详细的分析和阐述,主要包括副车架的设计和举升机构的设计,说明了设计时要考虑的因素以及最终的设计结果。
【期刊名称】《汽车实用技术》【年(卷),期】2016(000)008【总页数】3页(P69-71)【关键词】上装;副车架;举升机构【作者】李焕【作者单位】安徽江淮汽车股份有限公司,安徽合肥 230601【正文语种】中文【中图分类】U462.110.16638/ki.1671-7988.2016.08.021CLC NO.: U462.1 Document Code: A Article ID: 1671-7988 (2016)08-69-03自卸汽车是利用本车发动机动力驱动液压举升机构,将其车厢倾斜一定角度卸货,并依靠车厢自重使其复位的专用汽车。
自卸车由两大部分组成,底盘和上装。
自卸车底盘是由主机厂生产的,专门用于改装自卸汽车的专用类底盘,与公路类底盘的区别在于变速箱上多了一个用于提供上装动力的取力器。
自卸车上装是由改装厂完成的,自卸车上装的作用就是完成货箱举升倾斜的过程,让货箱内的货物顺利卸下,并能够自动复位并锁止。
自卸车上装按照卸货方式分类,分为后倾式和侧倾式两种,其中后倾式又分为中顶式后倾和前顶式后倾两种,本文主要针对中顶式后倾结构的自卸车的举升机构的设计开展研究。
重型自卸汽车举升液压系统设计
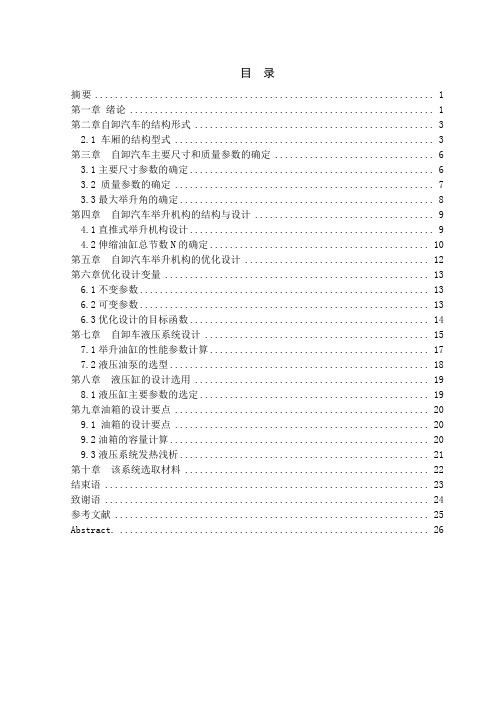
3.2质量参数的确定[1]
额定装载质量是自卸汽车的基本使用性能参数之一。目前,中、长距离公路运输趋向使用重型自卸汽车,以便提高运输效率、降低运输成本,额定装载质量一般为9~19t;而承担市区或市郊短途运输的自卸汽车额定装载质量为4.5~9t。同时,还应考虑到厂家的额定装载质量合理分级,以利于产品系列化、部件通用化和零件标准化。此外,额定装载质量还必须与选用的二类货车底盘允许的最大总质量相适应。
改装部分质量主要包括:车厢质量、副车架质量、液压系统质量、举升机构质量以及其他改装部件的质量。改装部分质量既可通过计算、称重求得,也可根据同类产品提供的数据进行估算。
自卸汽车整车整备质量是指装备齐全、加够燃料、液压油和冷却液的空车质量。它一般是二类底盘整备质量与改装部分质量的总和。是自卸汽车总体设计的重要设计参数之一。
通常由二类货车底盘改装的自卸汽车(Me<15t)质量利用系数略低于原货车的质量利用系数。国产自卸汽车的ηGO=1.0~1.5,国外自卸车的ηGO=1.3~2.0.如表3—2所示
图3—2自卸汽车质量利用系数
由此ηGO= =0.652(1—4)
自卸汽车的质心位置是指满载时整车质量中心位置,自卸汽车的质心位置对使用性能(例如汽车的制动性、操纵稳定性等)影响很大。因此,自卸汽车总体设计时应尽量使质心位置接近原货车的质心位置。
较低
系统倾卸稳定性
较差
较好
系统耐冲性
较好
较差
直推式举升机构结构简单,较易于设计。但这样易导致油缸泄漏或双缸不同步,进而造成车厢举升受力不均。目前,该类举升机构主要用于重型自卸汽车。
综上所述,结合选择车型情况,对于长安SC3043JD32自卸车,本文选用油缸直推式举升机构。并能承受较大的偏置载荷;举升支架在车厢后部,车厢受力状况较好。
自卸汽车举升机设计

机电与车辆工程学院毕业设计题目:自卸汽车举升机设计班级:车辆工程姓名:占伟学号: 1608100125指导教师:苑风霞日期: 2014年5月自卸汽车举升机设计摘要:自卸汽车是利用发动机传给变速箱,在通过取力器来带动液压泵来驱动液压举升机构,将货箱倾斜一定角度从而达到自动卸货的目的,并依靠货箱自重使其复位。
因此,液压举升机构是自卸汽车的重要工作系统之一,其结构形式、性能好坏直接影响自卸汽车的使用性能和安全性能。
本论文首先对自卸式汽车进行了说明,同时根据设计需要对液压系统进行了简要的阐述,设计液压系统。
液压缸也要通过计算和选择合适设计所需要的负荷,本次毕业设计的主要内容集中于自卸汽车液压缸机械连接结构和液压系统的设计,介绍了自卸汽车的整个工作原理以及举升机构的工作原理,,并对液压缸及其附属部件也进行了合适的选择。
最终得到一整套符合要求的汽车自卸系统。
关键词:自卸汽车,液压缸机械设计,液压系统设计1绪论 (1)1.1 自卸汽车的作用和分类 (1)1.2 自卸汽车的举升机构 (2)1.3自卸汽车的结构特点 (2)1.4 直推式自卸汽车运动方式 (3)2 液压系统设计 (4)2.1 液压概述 (4)2.1.1 液压技术的发展 (4)2.1.2 液压传动 (4)2.2 自卸汽车液压系统设计 (5)3液压缸计算与选择 (8)3.2液压缸内径D和外径D1的确定 (9)3.3活塞的行程确定 (11)3.4各参数的校核 (12)3.5缸筒的要求 (13)3.6液压缸的确定 (14)4导轨的设计与液压缸连接方式设计 (15)4.1上导轨的形状设计 (15)4.2上导轨强度校准 (16)4.3下导轨图形设计 (17)4.4下导轨的强度和刚度校核 (18)4.5自卸车连接铰链设计 (19)4.5.1铰接处销轴的直径计算 (19)4.5.2车厢尾部销轴的直径计算 (21)5 液压元件选择 (22)5.1 液压泵的确定 (22)5.2 阀类元件的确定 (25)选择阀类元件应注意的问题 (25)5.3 油箱的选择 (26)5.4 滤油器的选择 (26)5.5 管路的选择 (27)致谢辞 (29)1绪论1.1 自卸汽车的作用和分类自卸汽车又称翻斗车,它是依靠发动机动力驱动液压举升机构,将货箱倾斜一定角度从而达到自动卸货的目的,并依靠货箱自重使其复位的一种重要专用汽车。
毕业设计(论文)-重型自卸车货箱与举升装置设计(含全套cad图纸)[管理资料]
![毕业设计(论文)-重型自卸车货箱与举升装置设计(含全套cad图纸)[管理资料]](https://img.taocdn.com/s3/m/e1824fe2a2161479161128a9.png)
重型自卸车货箱与举升装置设计摘要自卸汽车是利用发动机动力驱动液压举升机构,将货箱倾斜一定角度从而达到自动卸货的目的,并依靠货箱自重使其复位的。
自卸机构负责货物的举升倾卸,卸货时驾驶员操纵液压阀的控制手柄,动力由发动机输出经变速器再到取力器,取力器驱动液压泵给液压缸提供动力,液压缸推动货箱实现货物的倾卸。
液压举升机构是自卸汽车的重要工作系统之一,其结构形式、性能好坏直接影响自卸汽车的使用性能和安全性能。
本次毕业设计的主要内容集中于自卸汽车液压缸及液压系统的设计,介绍了液压设计的前期准备工作:设计的依据、设计的一般原则和设计步骤。
通过对自卸汽车举升机构几种方案的比较,确定该车的举升机构的方案, 并对该方案进行了力学分析计算和液压系统设计。
设计采用直推式举升机构, 具有结构简单,行程长,兼具经济性的特点。
然后对液压缸的刚度、强度、系统压力、升降时间进行了验算和校核,最终确定了该方案的合理性和安全性。
另外,本说明书对取力器和货箱也进行了设计和计算。
关键词:自卸汽车,液压系统,举升机构,取力器HEA VY DUMP TRUCK PACKING CASE AND THE DE SIGN OF LIFT ING DEVICEABSTRACTThe dump truck uses the engine power actuation hydr aulic pr ess ure lif ting organization,packing container incline certain angle,thus serves the pur pos ewhich unloads cargo automatically,and depends upon the packing container dead weight to cause its replacement.The auto-dumping mechanism is mainly responsible for the lif ting and dumping of the the goods ar e neededto be unloaded,the oper ator will control the handle of the hydraulic valve,andthen the goods are dumped by the series of engines fr om the engine to thegear box,and then to the power-out device driving the liquid pump to give thepower to liquid tank,which pushes the compartment to tilt the goods.Thehydraulic pressure lifting or ganization is one of dump truck's impor tant wor k systems,its str uctur al style,perf or mance quality immediate influence dumptr uck's oper ational perf or mance and safety perf or mance.The content of this graduation design has focused on the design of the dumptr uck hydr aulic cylinder and hydr aulic systems,intr oducing the design ofhydraulic des ign pr eparation wor k,and the design basis,general principles and par ed with the several plans of lifting mechanis m,we have chosen oneplan finally,f or we have designed the calculation of the mechanical analysis andthe hydr aulic design put to use to keep the push type liftingmechanism,which has simple str uctur e,long route of tr avel,and economic.What’s more,we alse have checked its stiff ness,strength,systematicpressure,lif ting up and down time,f inally we decided the reasonableness and addition,we alse made the design and calculation of thePower-Take-Off and the goods’compartment.Keyword s:dump truck,hydraulic pr ess ure urn design,hydraulic pr essuresystem,Lif ting mechanis m,Pow er-Take-Of f目 录第一章 前言 .................................................................................................................................................. 1 第二章 总体方案分析及确定3 § 自卸汽车的分类...............................................................3 ............................................................. §§ 总设计内容分析 车厢设计.......................................................................... ...................................................... 4 5§§车厢结构设计 车厢选择材料 ...................................................... 5 6 § 举升机构分析 .............................................................................................. 6 §§ 液压系统的组成部分及作用 自卸汽车举升机构现存方案及其优缺点 ...... 6 7第三章 液压举升系统的设计 ......................................................................................... 10 § 举升机构设计中应考虑的问题 (10)§ 爬行现象 10§车厢在最大举升位置时,车厢后地板离地面的高度。
自卸汽车几种举升方式的对比分析
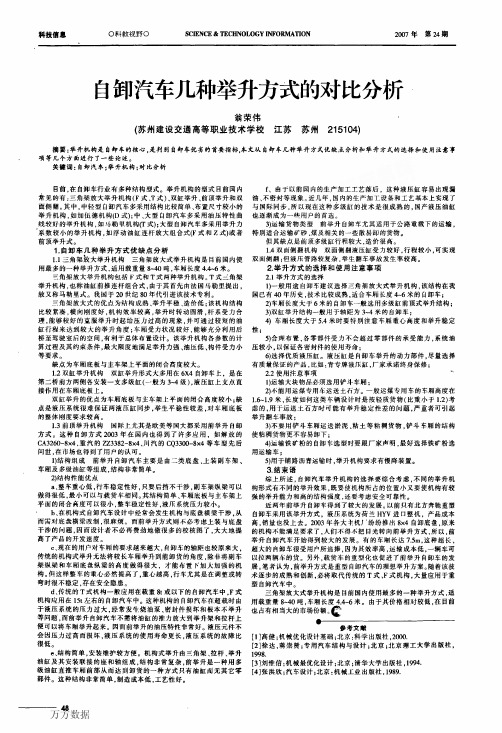
f、由于以前国内的生产加工工艺落后,这种液压缸容易出现漏 油、不密封等现象。近几年,国内的生产加t设备和工艺基本上实现了 与国际同步.所以现在这种多级缸的技术是很成熟的,国产液压油缸 也逐渐成为一螋用户的首选。
31运输货物类型前举升自卸车尤其适用于公路重载下的运输, 特别适合运输矿砂.煤及相关的一些散易卸的货物。
2.学位论文 马锐 自卸汽车举升机构的设计 2007
自卸汽车是利用发动机动力驱动液压举升机构,将货箱倾斜一定角度从而达到自动卸货的目的,并依靠货箱自重使其复位。因此,举升机构是自卸
汽车的重要工作系统之一,其设计质量直接影响自卸汽车的使用性能。
本论文首先综述了自卸汽车的研究现状,对自卸汽车举升机构以及其液压
系统进行了说明,对影响举升机构性能的主要参数进行分析。同时根据研究需要对机械系统动力学仿真分析软件ADAMS进行了简要的阐述,并对举升机构
设计、参数化设计和二次开发以及其在ADAMS软件中的应用进行了详细的介绍。
本论文以SGA3723自卸汽车为研究对象,对该车举升机构以及其液
压系统的计算进行了详细的说明。采用ADAMS软件,建立了对举升机构的关键参数进行参
1)结构组成前举升自卸汽车主要是由二类底盘、上装副车架、 车厢及多级油缸等组成,结构非常简单。
2)结构性能优点 a、整车重心低.行车稳定性好,只要后挡不干涉.副车架纵梁可以 做得很低,最小可以与载货车相同。其结构简单、车厢底板与主车架上 平面的闭合高度可以很小,整车稳定性好,液压系统压力较小。 b、在机构式自卸汽车设计中经常会发生机构与底盘横粱干涉.从 而需对底盘横梁改制。很麻烦。而前举升方式则不必考虑上装与底盘 干涉的『玎j题,因而设计者不必再费劲地做很多的校核图了。大大地提 高了产品的开发速度。 c、现在的用户对车厢的要求越来越大,自卸车的轴距也较原来大, 传统的机构式举升无法将较长车厢举升到能卸货的角度.除非将副车 架纵梁和车厢底盘纵梁的高度做得很大,才能布置卜.加人加强的机 构。但这样整车的重心必然提高了,重心越高,行车尤其是在调整或转 弯时很不稳定,存在安全隐患。 d、传统的T式机构一般应用在载重8t或以下的自卸汽车中.F式 机构应用在15t左右的自卸汽车中。这种机构的自卸汽车在超载时由 于液压系统的压力过大.经常发生烧油泵、密封件损坏和根本不举升 等问题,而前举升自卸汽车不需将油缸的推力放大到举升架和拉杆上 便可以将车厢举升起来。因而前举升的油压特性非常好。液压元件不 会因压力过高而损坏.液压系统的使用寿命更长。液压系统的故障比 很低。 e、结构简单,安装维护较方便。机构式举升由三角架、拉杆、举升 油缸及其安装联接的座和轴组成.结构非常复杂。前举升是一种用多 级油缸直推车厢前部从而达到卸货的一种方式只有油缸而无其它零 部件。这种结构非常简单,制造成本低,工艺性好。
基于Solidworks的运输车的举升机构设计.

本设计是独立自主完成并顺利通过答辩,只可用于学习交流,不可用于商业活动。
另外:有需要电子档的同学可以加我3103064563,我存有该设计的全部电子档,旨在互相帮助,共同进步,共同探讨新的研究方案,维护社会主义文明,建设社会主义和谐社会。
基于Solidworks的运输车的举升机构设计作者:00000000 指导老师:000000000000000 机械设计制造及其自动化摘要:随着国民经济的快速发展,我国专用汽车市场进入了快速成长期。
作为专用汽车中一个分支的自卸汽车,陆续出现了多种多样的型式,其中最常见的是后倾式自卸运输车。
本文首先对自卸运输车进行了简单的介绍,接着按照自卸运输车举升机构的设计过程,完成了对举升机构的选型、机构的受力分析和计算,最后,通过Solidworks 软件对自卸运输车及其举升机构进行了三维动画的展示。
关键词:专用汽车,自卸汽车,举升机构,三维动画1 绪论1.1 课题的提出自卸运输车又成翻斗车,它是利用自身动力驱动液压举升机构,使运输车车厢具有自动倾卸货物的能力和回复到原位功能的一种专用功能的自卸运输车。
自卸运输车运输的货物有:沙、石、土、垃圾、建材、粮食、肥料和农产品等散装货物。
它的分类方式如下:1.按用途方式:用于公路运输的普通自卸运输车;非公路运输的重型自卸运输车,主要常见于矿区装卸作业与大中型土建工程。
2.按载重总质量级别分类:轻型自卸运输车(1.8-6t);中型自卸运输车(6-14t);重型自卸运输车(≥14t)。
3.按传动类型分类:机械传动、液压机械传动和电力传动。
4.按卸载货物方式分类:后倾式、侧倾卸式、三面卸式、货厢升高后倾式等多种形式。
5.按倾卸机构方式分类:前置直推式、后置直推式、液压缸前推连杆式、液压缸后推连杆式。
6.按车厢结构分类:一面开启式、三面开启式和无后栏板式。
自卸运输车在工程建筑中,常与挖掘机、装载机、带式输送机等联合作业,构成装运、倾卸生产线,进行土方、沙石、松散物料等的装载运输。
自卸车举升机构设计
目录摘要............................................................. Abstract (Ⅱ)第1章绪论 (3)1.1 课题的提出 (3)1.2 专用汽车设计特点 (5)1.3课题的实际意义 (6)1.4 国内外自卸汽车的发展概况 (7)第2章轻型自卸车主要性能参数的选择 (13)2.1整车尺寸参数的确定 (13)2.2质量参数的确定 (14)2.3其它性能参数 (16)2.4本章小结 (16)第3章自卸车车厢的结构及设计 (17)3.1 自卸汽车车厢的结构形式 (17)3.1.1车厢的结构形式 (17)3.1.2车厢选材 (18)3.2车厢的设计规范及尺寸确定 (19)3.2.1车厢尺寸设计 (19)3.2.2车厢内框尺寸及车厢质量 (20)3.3车厢板的锁启机构 (17)3.4 本章小结 (17)第4章自卸举升机构的设计 (18)4.1自卸举升机构的选择 (18)4.1.1举升机构的类型 (18)4.1.2自卸汽车倾卸机构性能比较 (21)4.2举升机构运动及受力分析及参数选择 (23)4.2.1机构运动分析 (30)4.2.2举升机构受力分析及参数选择 (32)4.3本章小结 (26)第5章液压系统设计 (27)5.1液压系统工作原理及结构特点 (27)5.1.1工作原理 (27)5.1.2液压系统结构布置 (28)5.1.3 液压分配阀 (28)5.2油缸选型及计算 (29)5.3油箱容积及油管内径计算 (30)5.4取力器的设计 (31)5.5本章小结 (42)第6章副车架的设计 (43)6.1副车架的截面形状及尺寸 (43)6.2副车架前段形状及位置 (44)6.2.1 副车架的前端形状及安装位置 (44)6.2.2 纵梁及横梁的连接设计 (46)6.2.3 副车架及主车架的连接设计 (36)6.3副车架主要尺寸参数设计计算 (37)6.3.1副车架主要尺寸设计 (37)6.3.2副车架的强度刚度弯曲适应性校核 (37)6.4本章小结 (44)结论 (45)参考文献 (46)致谢 (47)第1章绪论1.1 课题的提出专用自卸车是装有液压举升机构,能将车厢卸下或使车厢倾斜一定角度,货物依靠自重能自行卸下或者水平推挤卸料的专用汽车。
基于SOLIDWORKS的自卸汽车举升机构的仿真设计
第3秒,举升到约7。时)。
对最大VOll Mises应力最可能出现的画面时的三角板执行详细的静态分析,应力分布如图9所示。三角 板的最大应力值为219.4 MPa,接近于许用应力225MPa,主要发生在与车厢连接的铰接孔A处及与拉杆连 接的铰接孔B处,三角板的中间部分,应力最低,且应力分布很不均匀。
Key words:Dump truck;Lifting mechanism;Simulation:FEA
万方数据
南通航运职业技术学院学报 JOURNAL OF NANTONG VOCATIONAL&TECHNICAL SHIPPING COU正GE
V01.8 No.2 Jun.2009
基于SOLIDWORKS的自卸汽车举升机构的仿真设计
孙旭 (南通航运职业技术学院 交通工程系。江苏
南通226010)
摘 要:运用机械仿真设计软件SolidWorks(集成COSMOSMotion与COSMOSWorks)建立了组合连杆式自卸汽车
98南通航运职业技术学院学报200910改进后的三角板及应力分布图11改进后的三角板静态位移分布图结束语通过联合虚拟样机技术运动仿真与有限元技术对自卸车举升机构进行设计完成了从举升机构布置关键零部件的改进设计等一系列工作并在理论与实际相结合的基础上对设计的结果做出正确的评估
第8卷第2期 2009年6月
系,AABC为三角板,BD为拉杆,CE为油缸。在A点三角板与车厢铰接,在B点三角板与拉杆铰接,在C点 三角板与油缸铰接,在D点拉杆与副车架铰接,在E点与油缸与副车架铰接。ABCDE、A’B’C’DE分别为举 升机
图1举升机构样机等效模型简图
圈2自卸车的虚拟样机模型(举升后)
(2)创建三维实体模型。本模型有6个零件,分别是车厢(载荷)、三角板(左、右)、支撑杆、液压缸体、液
举升机构的设计说明书
2.6 举升机构的设计自卸汽车举升机构又称倾卸机构,包括车箱、车厢板锁紧机构、液压举升系统和举升连杆等组成。
其作用是将车厢倾斜一定的角度,使车厢中的货物自动倾卸下来,然后再使车厢降落到车架上。
2.6.1 自卸汽车举升机构的结构形式根据举升液压缸与车厢的连接形式的不同,分为直推式举升机构和连杆式举升机构两大类。
自卸汽车对举升机构的设计要求如下:(1)利用举升机构实现车厢的翻转,其安装空间不能超过车厢底部与主车架间的空间;(2)结构要紧凑,可靠,具有很好的动力传递性能;(3)完成倾卸后,要能够复位;(4)在最大举升角时,车厢后板下垂最低点与地面保持一定斜货高度。
1.油缸直推式直推式举升机构的举升液压缸直接作用在车厢底架上,示意图如图2.10所示。
图2.11 单杠直推式倾斜机构这种机构结构简单紧凑、举升效率高、工艺简单、成本较低。
采用单缸时,容易实现三面倾斜。
另外,若油缸垂直下置时,油缸的推力可以作为,车厢的举升力,因而所需的油缸功率较小。
但是采用单缸时机构横向强度差,而且油缸的推程较大;采用多节伸缩时密封性也稍差。
连杆式倾卸机构的举升液压缸通过连杆作用在车厢底架上。
常用的连杆式倾卸结构有:油缸前推连杆式(马勒力举升臂式)、油缸后推连杆式(加伍德举升臂式)、油缸前推连杆式、油缸后推连杆式、油缸浮动连杆式、油缸俯冲连杆式。
表2-11自卸汽车举升机构特性比较结构型式车型举例性能特征结构示意图连杆组合式油缸前推连杆组合式五十铃TD50ALCQD、QD362横向刚度好、举升转动圆滑平顺举升力系数小,省力,油压特性好,但缸摆角大活塞行程稍大。
油缸后推连杆组合式五十铃TD50A-D、QD352、HF352转轴反力小,举升力系数大,举升臂较大,活塞行程短。
油缸后推连杆组合式日产PTL81SD举升力适中,杆系受力比较小,举升过程中油缸的摆动角度很小,油缸的行程也比较短,但因为机构集中在车后部,车厢底板受力大。
油缸浮动连杆式YZ-300油缸进出油管活动范围大,油管长,举升力系数较小。
自卸汽车举升机构设计概述(doc 31页)
自卸汽车举升机构设计概述(doc 31页)分类号编号烟台大学毕业论文(设计)T式自卸汽车举升机构设计The design of T- type column hydraulic car lift申请学位:工学学士学位院系:机电汽车工程学院专业:机械设计制造及其自动化姓名:学号:指导老师:2014年6月1日烟台大学.T式自卸汽车举升机构设计姓名:指导教师:2014年6月1日烟台大学烟台大学毕业论文(设计)AbstractWith the national economic growth, China's auto market has entered a special rapidgro wth. 2005 Special Purpose Vehicle manufacturers have been 628, Special Purpose Vehicle has reached more than 4900 varieties,2005 special vehicle production reached700,000, Accounting f or 40% of total truck. As a Special Purpose Vehicle in a branch ofthe dump truck, has been found in a wide variety of types , of which the most common isBack ward curved dump truck.In this paper, firstly, I made a general about the auto unload vehicle design anditsdevelopment domestic and abroad. Then, according to the process of the design of lifting mechanism of dump truck, completed the analysis of mechanism selection, mechanism of stress analysis are also calculated, h ydraulic system design and motion simulation.Key words: Special Purpose Vehicle, Dump Truck, Lifting mechanism, motion simulation烟台大学毕业论文(设计)目录第一章绪论 (1)1.1引言 (1)1.2 国内外专用车辆的发展概况 (1)1.2.1 国外专用车辆发展概况 (1)1.2.2 我国专用汽车的发展状况 (2)1.3自卸车概述 (2)第二章自卸车举升机构选型 (4)2.1自卸车载重与车厢举升角的确定 (4)2.1.1自卸车载重 (4)2.1.2车厢举升角的确定 (4)2.2举升机构结构选型 (4)第三章自卸汽车举升机构的结构与设计 (7)3.1T 式举升机构运动与受力的解析计算 (7)第四章液压系统设计 (12)4.1确定系统方案 (12)4.1.1液压回路系统的设计 (12)4.2液压系统主要元件的性能参数计算与选型 (13)4.2.1举升油缸的性能参数计算与选型 (13)4.2.2液压油泵性能参数计算与选型 (14)4.2.3管路选择 (15)4.2.4油箱容积设计 (15)第五章T式自卸汽车举升机构的动力学仿真 (16)5.1 T式自卸汽车举升机构系统实体模型的建立 (16)5.2举升机构的动力学仿真 (18)5.2.1 模型导入 (18)5.2.2编辑模型构件 (19)5.2.3运动副建立 (19)5.3对三维模型进行运动仿真分析 (20)5.3.1设置运动仿真解算方案 (20)5.3.2仿真曲线输出。
- 1、下载文档前请自行甄别文档内容的完整性,平台不提供额外的编辑、内容补充、找答案等附加服务。
- 2、"仅部分预览"的文档,不可在线预览部分如存在完整性等问题,可反馈申请退款(可完整预览的文档不适用该条件!)。
- 3、如文档侵犯您的权益,请联系客服反馈,我们会尽快为您处理(人工客服工作时间:9:00-18:30)。
矿产资源开发利用方案编写内容要求及审查大纲
矿产资源开发利用方案编写内容要求及《矿产资源开发利用方案》审查大纲一、概述
㈠矿区位置、隶属关系和企业性质。
如为改扩建矿山, 应说明矿山现状、
特点及存在的主要问题。
㈡编制依据
(1简述项目前期工作进展情况及与有关方面对项目的意向性协议情况。
(2 列出开发利用方案编制所依据的主要基础性资料的名称。
如经储量管理部门认定的矿区地质勘探报告、选矿试验报告、加工利用试验报告、工程地质初评资料、矿区水文资料和供水资料等。
对改、扩建矿山应有生产实际资料, 如矿山总平面现状图、矿床开拓系统图、采场现状图和主要采选设备清单等。
二、矿产品需求现状和预测
㈠该矿产在国内需求情况和市场供应情况
1、矿产品现状及加工利用趋向。
2、国内近、远期的需求量及主要销向预测。
㈡产品价格分析
1、国内矿产品价格现状。
2、矿产品价格稳定性及变化趋势。
三、矿产资源概况
㈠矿区总体概况
1、矿区总体规划情况。
2、矿区矿产资源概况。
3、该设计与矿区总体开发的关系。
㈡该设计项目的资源概况
1、矿床地质及构造特征。
2、矿床开采技术条件及水文地质条件。