退火过程的技术参考
三级窒化工艺+氮化

三级窒化工艺+氮化 三级窒化工艺+氮化是一种常见的表面处理技术,广泛应用于材料科学、电子工程、化工等领域。
本文将从三级窒化工艺和氮化的概念、工艺流程、应用范围及优缺点等方面进行详细阐述,以帮助读者对该技术有更深入的了解。
一、三级窒化工艺 三级窒化工艺是一种表面处理方法,通过在材料表面生成氮化物层,提高材料的硬度、耐腐蚀性、抗磨损性等性能。
三级窒化工艺的核心是将氮原子扩散到材料表面,产生与基体材料结合紧密的氮化物层。
1. 氮化的概念 氮化是指将氮原子与其他原子结合形成化合物的过程。
氮化可以使材料表面形成硬度较高、耐磨损的氮化物层,从而提高材料的使用寿命和性能。
2. 三级窒化的原理 三级窒化工艺的原理是利用高温处理、氮气等气体的作用,将氮原子扩散到材料表面形成氮化物层。
三级窒化工艺的关键是掌握合适的温度、时间和气氛等参数,以确保氮原子的扩散与材料表面的反应达到最佳效果。
3. 三级窒化的工艺流程 三级窒化的工艺流程一般包括以下几个步骤:净化处理、预窒化处理、主窒化处理和后处理。
净化处理:将待处理材料进行清洗、酸洗等操作,去除表面的杂质和氧化物,保证材料表面的干净。
预窒化处理:将净化后的材料在气氛中进行加热处理,使材料表面形成一层薄薄的氮化物层,为后续的主窒化处理做好准备。
主窒化处理:在高温、氮气等气氛下,进行长时间的加热处理,使氮原子与材料表面反应生成厚的氮化物层。
该步骤是三级窒化工艺最重要的环节。
后处理:将主窒化处理后的材料进行淬火、退火等处理,消除工艺中产生的残余应力,提高材料的性能和稳定性。
4. 三级窒化的应用范围 三级窒化工艺广泛应用于各个领域,如金属材料、陶瓷材料、涂层等。
在金属材料方面,三级窒化可以使不锈钢、钢材、钛合金等表面形成硬度较高的氮化物层,提高材料的抗腐蚀性、硬度和耐磨损性。
在电子工程领域,三级窒化可以用于制作电子元件的表面保护层,保护器件不受外界环境的侵蚀。
在化工领域,三级窒化可以用于制作化学反应器的内衬等部件,提高其抗腐蚀性和耐高温性能。
浅析Q690D的焊接工艺
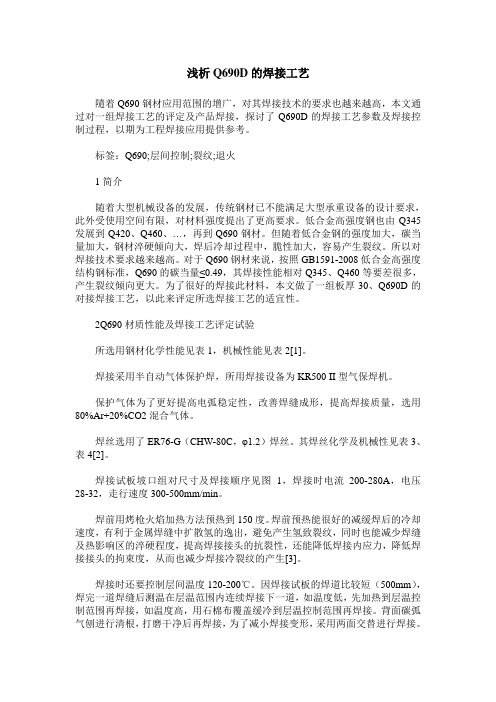
浅析Q690D的焊接工艺隨着Q690钢材应用范围的增广,对其焊接技术的要求也越来越高,本文通过对一组焊接工艺的评定及产品焊接,探讨了Q690D的焊接工艺参数及焊接控制过程,以期为工程焊接应用提供参考。
标签:Q690;层间控制;裂纹;退火1简介随着大型机械设备的发展,传统钢材已不能满足大型承重设备的设计要求,此外受使用空间有限,对材料强度提出了更高要求。
低合金高强度钢也由Q345发展到Q420、Q460、…,再到Q690钢材。
但随着低合金钢的强度加大,碳当量加大,钢材淬硬倾向大,焊后冷却过程中,脆性加大,容易产生裂纹。
所以对焊接技术要求越来越高。
对于Q690钢材来说,按照GB1591-2008低合金高强度结构钢标准,Q690的碳当量≤0.49,其焊接性能相对Q345、Q460等要差很多,产生裂纹倾向更大。
为了很好的焊接此材料,本文做了一组板厚30、Q690D的对接焊接工艺,以此来评定所选焊接工艺的适宜性。
2Q690材质性能及焊接工艺评定试验所选用钢材化学性能见表1,机械性能见表2[1]。
焊接采用半自动气体保护焊,所用焊接设备为KR500 II型气保焊机。
保护气体为了更好提高电弧稳定性,改善焊缝成形,提高焊接质量,选用80%Ar+20%CO2混合气体。
焊丝选用了ER76-G(CHW-80C,φ1.2)焊丝。
其焊丝化学及机械性见表3、表4[2]。
焊接试板坡口组对尺寸及焊接顺序见图1,焊接时电流200-280A,电压28-32,走行速度300-500mm/min。
焊前用烤枪火焰加热方法预热到150度。
焊前预热能很好的减缓焊后的冷却速度,有利于金属焊缝中扩散氢的逸出,避免产生氢致裂纹,同时也能减少焊缝及热影响区的淬硬程度,提高焊接接头的抗裂性,还能降低焊接内应力,降低焊接接头的拘束度,从而也减少焊接冷裂纹的产生[3]。
焊接时还要控制层间温度120-200℃。
因焊接试板的焊道比较短(500mm),焊完一道焊缝后测温在层温范围内连续焊接下一道,如温度低,先加热到层温控制范围再焊接,如温度高,用石棉布覆盖缓冷到层温控制范围再焊接。
7075铝合金残余应力释放的热处理工艺研究

7075铝合金残余应力释放的热处理工艺研究摘要:本文介绍了消除7075铝合金残余应力的常用热处理工艺措施,分析了各种热处理技术对消除残余应力所起到的作用,给出了针对7075铝合金的热处理工艺曲线,比较了各种热处理技术对消除7075铝合金残余应力的效果,为加工高强度的精密铝合金零件提供了技术参考。
关键词:7075铝合金残余应力热处理技术1 概述7075铝合金广泛应用于航空航天领域,属于a1-zn-mg-cu系可热处理强化的多元时效合金,具有高强度、低密度、热加工性能好等优点,固溶处理后经过人工时效处理后,抗拉强度可达600~700mpa,与45号钢的强度相当。
在150℃以下具有较高强度,其缺点是焊接性能较差,抗疲劳性能较差,有晶间腐蚀和严重的应力腐蚀倾向,并且为了获得高强度与高韧性,铝合金必须进行淬火处理。
当铝合金材料从大约470℃的高温快速淬入低温介质的淬火过程中,构件表面与心部存在很大的温度梯度,从而产生了很大的淬火残余应力。
故在使用过程中去除应力就相当必要。
本文所探讨的7075铝合金为应用于高精度的光学零件,对加工后的零件变形有较高要求。
在机械加工过程中,由于材料的去除,材料内部的残余应力将得到释放,此时往往产生很大的加工变形。
因此为了保证精密零件的尺寸稳定性应进行较好的残余应力释放。
2 实验方法实验材料选用7075-t6超硬铝合金板材,试样尺寸为15×150×220,分粗精加工两道工序进行加工,最终加工成10mm厚的平板试件,在粗精加工工序之间采用不同的热处理工艺进行残余应力的消除,精加工后利用三座标检验试样的平面度,比较宏观变形量的大小,利用钻孔法对试样内部残余应力的大小进行测定,比较微观应力值的大小。
本文所采用的消除残余应力的热处理工艺措施主要有以下几种:2.1 去应力退火去应力退火的目的是减小金属制件的内应力,降低材料的应力腐蚀倾向,保证零件尺寸的稳定性,同时其强度和硬度基本不下降。
半导体制造技术期末题库参考答案
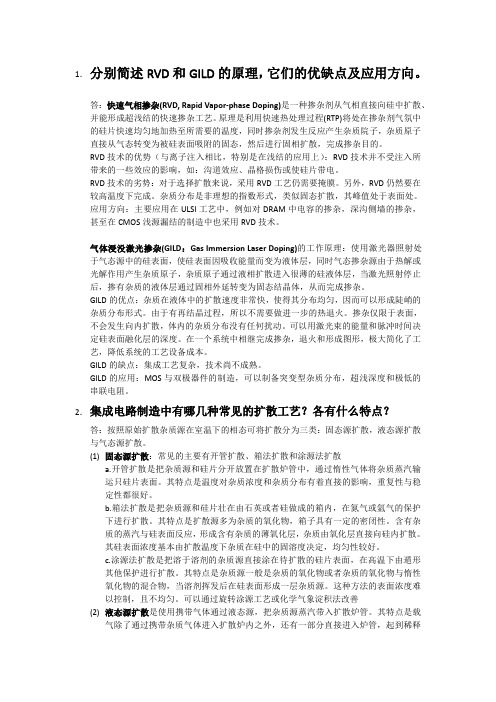
RVD 和 GILD 的原理, 它们的优缺点及应用方向。
答:快速气相掺杂(RVD, Rapid Vapor-phase Doping)是一种掺杂剂从气相直接向硅中扩散、 并能形成超浅结的快速掺杂工艺。 原理是利用快速热处理过程(RTP)将处在掺杂剂气氛中 的硅片快速均匀地加热至所需要的温度,同时掺杂剂发生反应产生杂质院子,杂质原子 直接从气态转变为被硅表面吸附的固态,然后进行固相扩散,完成掺杂目的。 RVD 技术的优势(与离子注入相比,特别是在浅结的应用上) :RVD 技术并不受注入所 带来的一些效应的影响,如:沟道效应、晶格损伤或使硅片带电。 RVD 技术的劣势:对于选择扩散来说,采用 RVD 工艺仍需要掩膜。另外,RVD 仍然要在 较高温度下完成。杂质分布是非理想的指数形式,类似固态扩散,其峰值处于表面处。 应用方向:主要应用在 ULSI 工艺中,例如对 DRAM 中电容的掺杂,深沟侧墙的掺杂, 甚至在 CMOS 浅源漏结的制造中也采用 RVD 技术。 气体浸没激光掺杂(GILD: Gas Immersion Laser Doping)的工作原理:使用激光器照射处 于气态源中的硅表面,使硅表面因吸收能量而变为液体层,同时气态掺杂源由于热解或 光解作用产生杂质原子,杂质原子通过液相扩散进入很薄的硅液体层,当激光照射停止 后,掺有杂质的液体层通过固相外延转变为固态结晶体,从而完成掺杂。 GILD 的优点:杂质在液体中的扩散速度非常快,使得其分布均匀,因而可以形成陡峭的 杂质分布形式。由于有再结晶过程,所以不需要做进一步的热退火。掺杂仅限于表面, 不会发生向内扩散,体内的杂质分布没有任何扰动。可以用激光束的能量和脉冲时间决 定硅表面融化层的深度。在一个系统中相继完成掺杂,退火和形成图形,极大简化了工 艺,降低系统的工艺设备成本。 GILD 的缺点:集成工艺复杂,技术尚不成熟。 GILD 的应用:MOS 与双极器件的制造,可以制备突变型杂质分布,超浅深度和极低的 串联电阻。 2. 集成电路制造中有哪几种常见的扩散工艺?各有什么特点? 答:按照原始扩散杂质源在室温下的相态可将扩散分为三类:固态源扩散,液态源扩散 与气态源扩散。 (1) 固态源扩散:常见的主要有开管扩散、箱法扩散和涂源法扩散 a.开管扩散是把杂质源和硅片分开放置在扩散炉管中,通过惰性气体将杂质蒸汽输 运只硅片表面。其特点是温度对杂质浓度和杂质分布有着直接的影响,重复性与稳 定性都很好。 b.箱法扩散是把杂质源和硅片壮在由石英或者硅做成的箱内,在氮气或氩气的保护 下进行扩散。其特点是扩散源多为杂质的氧化物,箱子具有一定的密闭性。含有杂 质的蒸汽与硅表面反应,形成含有杂质的薄氧化层,杂质由氧化层直接向硅内扩散。 其硅表面浓度基本由扩散温度下杂质在硅中的固溶度决定,均匀性较好。 c.涂源法扩散是把溶于溶剂的杂质源直接涂在待扩散的硅片表面,在高温下由遁形 其他保护进行扩散。其特点是杂质源一般是杂质的氧化物或者杂质的氧化物与惰性 氧化物的混合物,当溶剂挥发后在硅表面形成一层杂质源。这种方法的表面浓度难 以控制,且不均匀。可以通过旋转涂源工艺或化学气象淀积法改善 (2) 液态源扩散是使用携带气体通过液态源,把杂质源蒸汽带入扩散炉管。其特点是载 气除了通过携带杂质气体进入扩散炉内之外,还有一部分直接进入炉管,起到稀释
第三次作业参考答案

1、何谓退火和正火?两者的特点和用途有什么不同?退火是将钢件加热到Ac1或Ac3以上(30~50℃),保温一段时间,然后再缓慢的冷却(一般用炉冷)。
正火是将钢件加热到Ac3或Acm以上(30~50℃),保温一段时间,然后在空气中冷却,冷却速度比退火稍快。
退火与正火的主要区别是:正火是完全退火的一种变态或特例,二者仅是冷却速度不同,通常退火是随炉冷而正火是在空气中冷却,正火既适用于亚共析钢也适用于过共板钢,对于共析钢,正火一般用于消除网状碳化物;对于亚共析钢,正火的目的与退火基本相同,主要是细化晶粒,消除组织中的缺陷,但正火组织中珠光体片较退火者细,且亚共析钢中珠光数量多铁素体数量少,因此,经正火后钢的硬度、强度均较退火的高,由此可知,在生产实践中,钢中有网状渗碳体的材料需先经正火消除后方可使用其他工艺,而对热处理后有性能要求的材料,则据要求的不同及钢种不同选择退火工艺,如:要求热处理后有一定的强度、硬度,可选择正火工艺;要求有一定的塑性,尽量降低强度、硬度的则应选择退火工艺。
生产上常用的退火操作种类(1)完全退火(俗称退火)主要用于亚共桥钢和合金钢的铸件、锻件及热轧型材,有的也用做焊接结构件,其目的是细化晶粒,改善组织,消除残余应力,降低硬度、提高塑性,改善切削加工性能,完全退火是一种时间很长的退火工艺,为了缩短其退火时间,目前常采用等温火的工艺来取代完全退火工艺,同完全退火比较,等温火的目的与完全退火相同,但它大大缩短了退火时间。
(2)球化退火主要用于过共析钢及合金工具钢(如刀具、量具、模具以及轴承等所有钢种)。
其目的主要是降低硬度,改善切削加工性,并为以后淬火作好准备。
(3)去应力退火(又称低温退火)主要用来消除铸件、锻件及焊接件、热轧件等内应力。
(4)再结晶退火用来消除冷加工(冷拉、冷冲、冷轧等)产生的加工硬化。
目的是消除内应力,提高塑性,改善组织。
(5)扩散退火主要用于合金钢,特别是合金钢的铸件和钢锭。
半导体行业术语

半导体行业术语半导体行业术语是指用于描述和解释半导体及相关技术的术语和术语缩略语。
以下是一些常见的半导体行业术语及其参考解释。
1. 半导体(Semiconductor)- 指的是电导介于导体和绝缘体之间的固态材料,通常是以硅(Si)或镓(Ga)为主要成分,用于制造电子器件。
2. 集成电路(Integrated Circuit,IC)- 也被称为芯片,是将数十亿个晶体管、电阻器、电容器和其他电子元件集成到一块半导体晶片上的技术。
3. MOSFET(Metal-Oxide-Semiconductor Field-Effect Transistor)- MOSFET是一种常用的场效应晶体管,通过控制栅电压来调节源极电流。
4. CMOS(Complementary Metal-Oxide-Semiconductor)- CMOS是一种基于nMOS(n沟道金属-氧化物-半导体)和pMOS(p沟道金属-氧化物-半导体)技术的集成电路制造技术。
5. MEMS(Micro-Electro-Mechanical Systems)- MEMS是一种将微机械系统与电子技术相结合的技术,包括制造微型传感器、执行器和微型结构等。
6. 晶圆(Wafer)- 指的是在半导体制造过程中用于制作芯片的圆形硅片。
晶圆上会进行刻蚀、沉积、光刻等工艺。
7. 工艺(Process)- 指的是制造半导体器件所需的一系列步骤和工作流程,包括光刻、刻蚀、沉积、清洗等。
8. 掩膜(Mask)- 掩膜用于光刻工艺,上面有设计好的图案,通过光刻暴光制造电路芯片的图案。
9. Doping(掺杂)- 在半导体材料中引入杂质,以调整材料的导电性能。
常见的掺杂剂包括硼、磷、砷等。
10. 渗透磁场(Permeable Magnetic Field)- 渗透磁场是指在磁性材料的边界上产生的特殊磁场,常用于磁传感器和存储器中。
11. 氮化镓(Gallium Nitride,GaN)- 氮化镓是一种半导体材料,具有高电子流动性和较大的能隙,适用于高功率电子器件的制造。
退火窑温度的控制
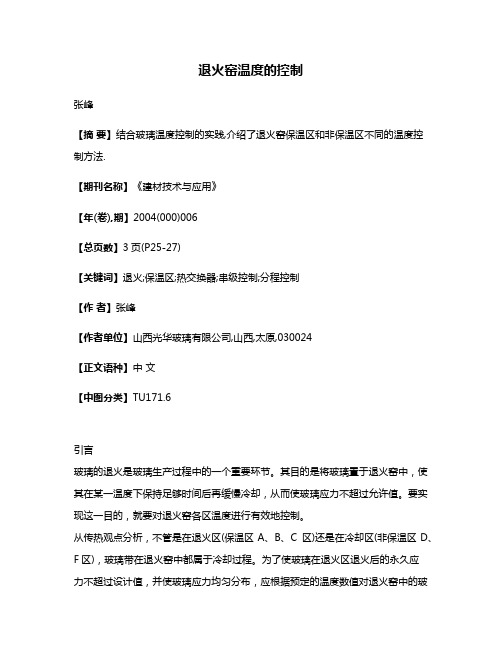
退火窑温度的控制张峰【摘要】结合玻璃温度控制的实践,介绍了退火窑保温区和非保温区不同的温度控制方法.【期刊名称】《建材技术与应用》【年(卷),期】2004(000)006【总页数】3页(P25-27)【关键词】退火;保温区;热交换器;串级控制;分程控制【作者】张峰【作者单位】山西光华玻璃有限公司,山西,太原,030024【正文语种】中文【中图分类】TU171.6引言玻璃的退火是玻璃生产过程中的一个重要环节。
其目的是将玻璃置于退火窑中,使其在某一温度下保持足够时间后再缓慢冷却,从而使玻璃应力不超过允许值。
要实现这一目的,就要对退火窑各区温度进行有效地控制。
从传热观点分析,不管是在退火区(保温区A、B、C 区)还是在冷却区(非保温区D、F区),玻璃带在退火窑中都属于冷却过程。
为了使玻璃在退火区退火后的永久应力不超过设计值,并使玻璃应力均匀分布,应根据预定的温度数值对退火窑中的玻璃板温度进行调节控制。
由于保温区和非保温区冷却方式不同,因此温度控制方式也不相同。
其中退火窑保温区采用热交换器对玻璃进行冷却;而退火窑非保温区则采用风嘴直接冷却。
1 退火窑保温区的温度控制退火窑保温区的(A、B、C)板上、板下都有热交换器。
热交换器内风量的大小和风温的高低决定着热交换器的冷却能力,而风量的大小和风温的高低都是通过一定的控制策略而实现的。
1.1 A区、B区的温度控制退火窑A区、B区的结构完全一样,采用的温度控制策略也完全相同,即两个边部采用分程控制法,中部采用串级控制法。
但是,A区、B区要求控制的温度却不相同,A区温度应控制在500~580 ℃左右,B区温度应控制在430~500 ℃左右。
1.1.1 A区、B区边部温度控制分程控制法的控制原理见图1。
由图1可以看出,分层控制法的控制原理为:先从现场控制点取得实时数据AI,PID模块对该数据处理后以百分比的形式输给分程模块SPLIT,分程模块SPLIT再将该百分值分为0~49 %和50 %~100 %两段,并将它们分别传给AO1和AO2两个输出模块。
连退机组退火炉炉压控制研究

连退机组退火炉炉压控制研究摘要:文章介绍了连续退火炉炉内氛围主要组成成分,阐述了氢气含量配比控制和炉内正常生产时的压力控制以及造成炉压炉波动的相关因素,分析了炉压波动的主要常见原因,并提供了具体问题的解决措施,在实际生产中,特别适用于特殊钢材的生产操作炉内氛围要求,使得退火炉炉内氛围得到有效控制,保证了带钢退火生产工艺稳定,满足各类带钢退火要求,提高产品质量。
关键词:连退机组;退火炉;炉压控制前言攀钢西昌钢钒冷轧厂连续退火炉是进口立式退火炉。
炉内氛围为氮气和氢气按照一定比例混合构成的氛围,炉内压力保持微正压保证带钢在炉内不被氧化,同时还可以去除带钢表面残留的氧化物,提高带钢的表面质量。
1保护气体注入控制攀钢连退线按照区段划分保护气体注入分8个主控制管路。
炉内氛围控制完全基于西门子公司的PCS 7软件,以Win CC作为人机界面,实现过程参数的在线检测、显示和调节,实现数据采集、报警和趋势记录,保证设备的控制精度和生产稳定运行。
为了防止空气进入炉内,加热炉在生产中常保持一定的正压,炉压是由大量保护气体注入形成的,保护气通过位于炉底的注入点流进炉内,在各注入支路的流量控制阀和炉顶的放散阀共同调节下,保证炉内一定的压力和炉内气氛再生,炉内压力的设定以保证加热炉安全性为主,防止带钢氧化来决定,因为退火炉内的气氛压力直接影响着带钢的质量和退火炉的安全,炉压低无法有效保证还原反应效果,炉压过高容易出现事故和浪费气体。
1.1保护气注入模式根据加热炉生产状态,保护气注入一共存在六种模式可供选择,各个模式间的切换遵循顺序,模式的启停完全由顺控完成,保证切换过程平稳性。
其中快冷段高氢模式HNx+RCH2和模式N2+RCH2间的切换需要经历HNx模式和N2模式,此过程也是由顺控自动完成的,不需要操作工进行干预。
1.2保护气注入流量修正1.2.1炉压控制及修正保护气体注入炉内后,按照工艺设定的炉压大小由炉压控制器采用PI控制,其比例系数取2,积分时间取200s。
- 1、下载文档前请自行甄别文档内容的完整性,平台不提供额外的编辑、内容补充、找答案等附加服务。
- 2、"仅部分预览"的文档,不可在线预览部分如存在完整性等问题,可反馈申请退款(可完整预览的文档不适用该条件!)。
- 3、如文档侵犯您的权益,请联系客服反馈,我们会尽快为您处理(人工客服工作时间:9:00-18:30)。
一、退火过程:
退火方式一般为电接触式,电极通过退火轮(接触轮)将大电流均匀导入铜线上,实现铜线的预热和加热.预热是将铜线加热到不至于氧化的最高温度,一般为250度左右;加热是将铜线加热到退火温度,一般为500~550度,使之再结晶.加热段有蒸汽保护,防止铜线氧化,再经过水冷却后,完成了退火(软化)过程。
二、技术要求:
1、退火电压和拉线速度及收线速度应保持同步性.
2、退火电流与退火线径的平方成正比,应根据线径大小设置退火电流.确保退火软铜线的性能符合GB3953的规定或理想的性能.
3、收线张力是通过储线器汽缸的压力进行调整.
4、铜线的直径偏差应符合GB3953的规定。
三、线径缩小的原因:
铜线在拉制过程中产生硬化现象,退火软化后,铜线的抗拉强度降低,塑性和延伸率增加.在收线张力的作用下,线径缩小是必然现象.但应当控制线径缩小的范围,一般不大于0.02mm(根据线径的大小而确定).如果收线张力减小,退火轮之间的铜线会抖动,接触不好,出现点火花现象,容易断线和加速退火轮的损坏.因此,应根据线径的大小选择收线张力。
四、措施:
将线径缩小的量,增加到定径模具的孔径上。