齿轮的数控加工原理及误差分析
加工渐开线圆柱齿轮公法线误差的分析

使用过程中齿面出现磨损或拆修后安装有偏心,以及轮 齿在齿圈上分布不均匀,都会引起它上面的工作 台回
转不均 匀 ,从而直接 影响被加工齿 轮的公法线 长度 变动
( 防止 由于齿 轮副的误差及齿轮传动 时产生 1)
的热 变形 而使 轮齿 卡住 。 ( 给 齿 面 间 的 润 滑 油 留 有 空 间 ) T常在 滚齿 机 上完成 ,即 滚刀和 齿 J n
匹配间隙,以满足机床 的精度要求。但如果轴瓦间隙 过大 ,就必须 由专业厂或机床厂进行修理 ,使该部件
重 新达 到 出厂精 度 。
轮利用啮合原理来实现展成运动即分齿运动。而齿坯
的旋转完全 由机床工作台带动 ,也就是说滚刀与齿坯 之间严格按一定速比作均匀 的回转运动 ,来确保齿轮
关键词 :齿 轮 运动精度 公法线
中图分 类号 :T 8 G6
文献标 识码 :B
■
一 汽光 洋转 向装 置有 限公 司 吴一 芳 杨 久奎
1 齿轮公法线 的定义
、
、
公法 线是 与基 圆相 切 、与 异侧齿 面相 交 的直线 。 公法 线 的作用 :公 法线 的误 差直 接影 响其 齿 轮传
差 ( w △F =
一 l) m 。它是评定齿轮运动精度 的 .
4I 汽车T艺-材料 A& 5 TM
21年 期 02 第5
.
AT 1 &/' 4
界
差 ,即△ = 均一
它是评定齿轮齿侧间隙的一
因素。
个检验项 目,为了测量准确 ,在沿齿圈大致成 1 0 2。
根据齿轮的具体使用情况和要求,所选的衡量和
检测指标各不相同。实际应用时 ,要根据具体情况进
行 选择 。
齿轮传动轴的传动误差与回转间隙分析

齿轮传动轴的传动误差与回转间隙分析引言齿轮传动是常见的一种机械传动形式,广泛应用于工业机械领域。
在齿轮传动中,传动误差和回转间隙是重要的性能指标,对传动系统的精度和运行稳定性有着重要影响。
本文将针对齿轮传动轴的传动误差与回转间隙进行详细分析,探讨它们的原因以及对传动系统性能的影响。
一、传动误差的定义与分类传动误差是指齿轮传动轴在工作过程中由于齿轮的制造、装配等因素,导致输出轴承载方向的误差。
在齿轮传动中,常见的传动误差主要包括齿形误差、齿隙误差和轴向移位误差。
1. 齿形误差:齿形误差是指齿轮齿廓形状与理想齿廓的差异。
齿形误差可以通过齿轮的制造工艺、加工精度以及齿形检测仪器的性能等因素引起。
齿形误差会导致传动系统的噪声和振动增加,降低传动系统的工作效率。
2. 齿隙误差:齿隙误差是指齿轮齿槽之间的间隙大小不一致。
齿隙误差可以由齿轮的制造工艺、装配过程中的间隙控制等因素引起。
齿隙误差会导致传动系统的动态特性变差,降低传动系统的响应速度和稳定性。
3. 轴向移位误差:轴向移位误差是指齿轮轴在工作过程中由于装配不精确或轴向载荷造成的轴向偏移。
轴向移位误差会导致传动系统的运行不平稳,产生冲击和振动,严重时会导致传动轴的断裂。
二、传动误差的影响因素传动误差的产生与多个因素相关,主要包括齿轮的加工工艺、装配精度、使用环境、负载情况等。
1. 加工工艺:齿轮的加工工艺是影响传动误差的重要因素之一。
制造齿轮时,加工精度越高产生的传动误差就越小。
高精度的加工设备和工艺可以减少齿形误差和齿隙误差的产生。
2. 装配精度:齿轮装配过程中的精度控制也会对传动误差产生重要影响。
装配精度越高,齿轮的传动误差就越小。
装配精度主要包括齿轮齿轮间隙的控制、轴向偏移的控制等。
3. 使用环境:齿轮传动系统的使用环境对传动误差有着重要影响。
高温、高湿、高腐蚀等环境会导致齿轮表面的磨损加剧,进而影响传动误差。
4. 负载情况:齿轮传动系统的负载情况也会对传动误差产生影响。
影响齿轮工作平稳性的加工误差分析 - 普通齿轮传动
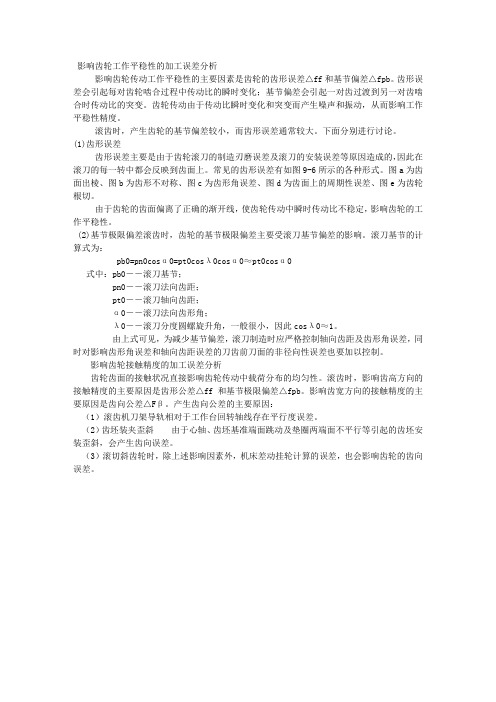
影响齿轮工作平稳性的加工误差分析影响齿轮传动工作平稳性的主要因素是齿轮的齿形误差△ff和基节偏差△fpb。
齿形误差会引起每对齿轮啮合过程中传动比的瞬时变化;基节偏差会引起一对齿过渡到另一对齿啮合时传动比的突变。
齿轮传动由于传动比瞬时变化和突变而产生噪声和振动,从而影响工作平稳性精度。
滚齿时,产生齿轮的基节偏差较小,而齿形误差通常较大。
下面分别进行讨论。
(1)齿形误差齿形误差主要是由于齿轮滚刀的制造刃磨误差及滚刀的安装误差等原因造成的,因此在滚刀的每一转中都会反映到齿面上。
常见的齿形误差有如图9-6所示的各种形式。
图a为齿面出棱、图b为齿形不对称、图c为齿形角误差、图d为齿面上的周期性误差、图e为齿轮根切。
由于齿轮的齿面偏离了正确的渐开线,使齿轮传动中瞬时传动比不稳定,影响齿轮的工作平稳性。
(2)基节极限偏差滚齿时,齿轮的基节极限偏差主要受滚刀基节偏差的影响。
滚刀基节的计算式为:pb0=pn0cosα0=pt0cosλ0cosα0≈pt0cosα0式中:pb0――滚刀基节;pn0――滚刀法向齿距;pt0――滚刀轴向齿距;α0――滚刀法向齿形角;λ0――滚刀分度圆螺旋升角,一般很小,因此cosλ0≈1。
由上式可见,为减少基节偏差,滚刀制造时应严格控制轴向齿距及齿形角误差,同时对影响齿形角误差和轴向齿距误差的刀齿前刀面的非径向性误差也要加以控制。
影响齿轮接触精度的加工误差分析齿轮齿面的接触状况直接影响齿轮传动中载荷分布的均匀性。
滚齿时,影响齿高方向的接触精度的主要原因是齿形公差△ff和基节极限偏差△fpb。
影响齿宽方向的接触精度的主要原因是齿向公差△Fβ。
产生齿向公差的主要原因:(1)滚齿机刀架导轨相对于工作台回转轴线存在平行度误差。
(2)齿坯装夹歪斜由于心轴、齿坯基准端面跳动及垫圈两端面不平行等引起的齿坯安装歪斜,会产生齿向误差。
(3)滚切斜齿轮时,除上述影响因素外,机床差动挂轮计算的误差,也会影响齿轮的齿向误差。
齿轮的误差及其分析

齿轮误差及其分析第一节:渐开线圆柱齿轮精度和检测对于齿轮精度,主要建立了下列几个方面的评定指标:一.运动精度:评定齿轮的运动精度,可采用下列指标:1.切向综合总偏差F i′:定义:被测齿轮与理想精确的测量齿轮单面啮合时在被测齿轮一转,(实际转角与公称转角之差的总幅度值)被测齿轮的实际转角与理论转角的最大差值。
切向综合总偏差F i′。
(它反映了齿轮的几何偏心、运动偏心和基节偏差、齿形误差等综合结果。
)ΔF i2.齿距累积总偏差F p,齿距累积偏差F pk。
定义:齿轮同侧齿面任意弧段(k=1或k=z)的最大齿距累积偏差。
它表现为齿距累积偏差曲线的总幅值。
——齿距累积总偏差。
在分度圆上,k个齿距的实际弧长与公称弧长之差的最大绝对值,称k个齿距累积误差ΔF pk。
k为2到小于Z/2的正数。
这两个误差定义虽然都是在分度圆上,但实际测量可在齿高中部进行。
这项指标主要反映齿轮的几何偏心、运动偏心。
用ΔF p 评定不如ΔF i′全面。
因为ΔF i是在连续切向综合误差曲线上取得的,而ΔF p不是连续的,它是折线。
ΔF i′= ΔF p+ Δf f测量方法:一般用相对法,在齿轮测量机上测量。
3.齿圈径向跳动ΔF r与公法线长度变动ΔF w:ΔF r定义:在齿轮一转围,测头在齿槽,于齿高中部双面接触,测头相对于齿轮轴线的最大变动量。
它只反映齿轮的几何偏心,不能反映其运动偏心。
(用径跳仪测量检测。
)由于齿圈径跳ΔF r 只反映齿轮的几何偏心,不能反映其运动偏心。
因此要增加另一项指标。
公法线长度变动ΔF w。
ΔF w定义:在齿轮一周围,实际公法线长度最大值与最小值之差。
ΔF w=W max-W min测量公法线长度实际是测量基圆弧长,它反映齿轮的运动偏心。
测量方法:用公法线千分尺测量。
4.径向综合误差ΔF i″和公法线长度变动ΔF w:齿轮的几何偏心还可以用径向综合误差这一指标来评定。
ΔF i″定义:被测齿轮与理想精确的测量齿轮双面啮合时,在被测齿轮一转,双啮中心距的最大变动量。
阐述渐开线齿轮齿形误差的分析方法

阐述渐开线齿轮齿形误差的分析方法1.前言渐开线齿轮是机器中常用的一种零件,它的用途是传递动力或运动。
齿轮之间的传动,是依靠主动轮的牙齿依次推动被动轮的牙齿来实现的。
牙齿两侧面的形状(齿面形状,即齿形)对于齿轮的传动和工作平稳性都有重要影响。
因此,必须了解渐开线齿轮齿形误差产生的原因及分析方法。
2.渐开线齿轮齿形特点所谓渐开线,是一根切线在基圆(作为描绘渐开线基础的一个圆)上纯滚动(即没有滑动的转滚运动)时,画出该切线滚动边缘上任意一点的运动轨迹。
如图1所示:图中的aa1和bb1就是切线纯滚动时a1和b1两点所画出来的渐开线。
显然,因为是同一个基圆,所以这两条渐开线是完全一样的,仅仅是它们的起点不同。
渐开线齿轮传动时,具有在任何瞬时的转速比都不改变,并且在相互啮合的齿轮的齿轮副中心距发生变化时传动比仍保持不变的特点。
在加工时,可以用模数、压力角相同的齿轮刀具加工模数、压力角相同而齿数不同的齿轮,因此,在机械制造行业中渐开线齿形齿轮应用得最为普遍。
3.渐开线齿轮齿形误差的分类及产生原因齿形误差是指在齿轮工作部分容纳实际齿形的两理论齿形间的法向距离,其△f只允许偏向齿体内。
在渐开线齿轮加工过程中,容易产生以下几种齿形误差:a.齿形角误差:即不是标准压力角的齿形,而是压力角大于或小于标准值的齿形,产生这种情况是由于磨齿时砂轮磨削角调整偏大或偏小,以至使所磨齿轮的基圆半径发生了变化。
b.齿形不对称:即齿歪现象,一面齿形的压力角大于标准值,而另一面齿形的压力角小于标准值。
齿形不对称的原因往往是由于采用锥面砂轮时,砂轮两边锥面磨削角修整得大小不同所致。
c.齿形曲率改变:即实际齿形曲率大于或小于理论齿形曲率,曲率的改变是由齿轮加工时的安装误差引起的。
d.齿形根切:即齿根部的渐开线齿形被切去,它的形成多数是由于所磨齿轮齿数较少,而磨削角又太小以及砂轮外圆无圆角引起的。
e.齿根圆角和齿顶特粗误差:即齿根过渡曲线部分的圆角太大,或接近齿顶的一部分齿形特别粗大。
关于数控加工的误差分析及应对措施

关于数控加工的误差分析及应对措施xx年xx月xx日•数控加工误差概述•数控加工误差分析•数控加工误差应对措施目录•数控加工误差控制案例分析•总结与展望01数控加工误差概述数控加工误差是指工件在数控加工过程中产生的尺寸、形状、表面质量等参数与理想状态下的工件参数之间的偏差。
数控加工误差包括机床、刀具、夹具、工件、切削液等多个因素的影响,这些因素相互作用,导致加工误差的产生。
由于工件或刀具的位置不准确,导致加工出的工件与理想状态下的工件参数之间的偏差。
定位误差由于机床、刀具、夹具等设备的制造、安装、调整不当,导致加工出的工件与理想状态下的工件参数之间的偏差。
几何误差由于切削过程中切削力的大小、方向、作用点等因素发生变化,导致加工出的工件与理想状态下的工件参数之间的偏差。
切削力误差由于机床、工件、刀具等在切削过程中产生的热量变化,导致加工出的工件与理想状态下的工件参数之间的偏差。
热误差1 2 3数控加工误差会导致工件的尺寸、形状、表面质量等参数与理想状态下的工件参数存在偏差,从而影响加工精度。
加工精度下降由于数控加工误差的存在,可能导致工件在装配、使用过程中出现故障,影响产品的整体性能和寿命。
产品质量下降为了控制数控加工误差,需要进行反复的调试和修正,增加了生产周期和成本。
生产效率降低02数控加工误差分析编程误差数控编程过程中,由于计算方法或近似处理等原因,导致加工路径与实际路径存在偏差,从而产生误差。
工件误差工件本身存在形状、尺寸等方面的误差,也会对加工精度产生影响。
机床误差机床本身精度不高或长期使用导致磨损,也会对加工精度产生影响。
刀具误差刀具在加工过程中会受到磨损、变形等因素影响,导致加工精度降低。
误差产生的原因分析03尺寸误差加工过程中,由于刀具磨损、温度变化等因素影响,导致加工出的工件尺寸与设计要求存在偏差。
误差对加工精度的影响01位置误差加工过程中,刀具与工件之间的相对位置不准确,导致加工出的工件形状、尺寸与设计要求存在偏差。
滚齿机加工原理及误差分析
滚齿机:主要用滚刀按展成法加工圆柱齿轮,蜗轮,链轮等齿面的齿轮加工机床。
滚齿机校正机构常见种类:行星式,复式偏心式,凸轮摆杆式,附加回转工作台式等。
决于齿轮机床的精度、刚度、刀具和齿轮毛坯的质量及其安装精度。
所以针对滚齿机工作台误差的滚齿机主要用滚刀按展成法加工圆柱齿轮、蜗轮、链轮等齿面的齿轮加工技术,在机械加工中占有重要地位。
因为在齿轮加工中出现了分度蜗轮的周节累计误差和周期误差,而齿轮加工精度取来源这一问题,本文使用滚齿机行星摆杆机构对其进行校正,用以减少分度蜗轮的周节累计误差和周期误差,使加工出来的齿轮达到满足加工精度的要求。
国内采用的滚齿机校正构,在机床制造行业中, 一开始制造精密机床, 由于各厂的设备条件差, 在滚齿机上不能加工精度较高的蜗轮, 分度精度满足不了产品的要求。
因而, 各厂先后在各型滚齿机上采用了各种类型的校正机构, 大都取得了不同程度的效果, 制出了精密分度蜗轮。
当时, 着重引进国外现成为结构, 近几年来, 无论在结构型式上, 或在简化结构, 或校正效果等方面均有较快的发展。
我国共采用了行星式、复式偏心式、凸轮摆杆式、和附加回转工作台式等多种类型的校正机构。
RS2 型滚齿机校正机构,只能能校正分度蜗轮副的周期误差。
但结构不够紧凑,校正机构在机床的外边,需要另置地基,并将机床的罩壳也换掉。
5355M型滚齿机校正机构也属于行星式,但没有周期误差校正凸轮, 机构是封闭的。
其结构复杂, 构件将近85 种, 使用不方便, 需将机床的双蜗杆传动改成单蜗杆传动, 此时, 必需拆除一根蜗杆。
由于校正机构安装位置不够妥当,使得一部分齿轮外露。
这种结构不太适用于大型滚齿机。
FO-10滚齿机行星式校正机构,该机构有一定的简化, 它省去了四根摆杆和一根长套筒, 结构就比较紧凑一些。
它装在机床分度挂轮箱处, 不需另置地基, 但其构件的种数仍然较多, 达45种, 放大比为0.182毫米每秒。
这种机构的轮廓尺寸较大。
机械加工误差产生的原因及措施
机械加工误差产生的原因及措施汇报人:2024-01-01•机械加工误差产生的原因•减小机械加工误差的措施•机械加工误差的补偿措施目录•提高机械加工精度的途径01机械加工误差产生的原因原理误差总结词原理误差是由于加工原理的不完善而导致的误差。
详细描述原理误差主要表现在机床或刀具的转动和移动过程中,由于设计原理或机构原理的限制,导致加工出的零件与理论值存在偏差。
例如,齿轮加工中,由于齿轮的齿廓理论是完美的,但在实际加工中,由于机床和刀具的精度限制,无法完全复制理想的齿廓形状,从而产生原理误差。
工具、夹具与机床的制造误差总结词工具、夹具与机床的制造误差是由于这些设备的制造精度不足而导致的误差。
详细描述工具、夹具和机床是机械加工中的重要组成部分,它们的制造精度直接影响着零件的加工精度。
例如,刀具的制造误差会导致加工表面的粗糙度不均匀,夹具的定位精度不高会导致零件的位置精度偏差,机床的主轴回转误差则会影响零件的圆度等。
调整误差是由于加工过程中的调整不准确而导致的误差。
详细描述在机械加工过程中,需要对工具、夹具和机床进行多次调整,如刀具的更换、夹具的定位、机床的校准等。
由于调整过程中的人为操作和设备本身的特性,往往会产生一定的调整误差。
例如,刀具的安装角度偏差会影响切削深度和表面粗糙度,夹具的调整不当会导致零件的定位不准确。
总结词VS总结词测量误差是由于测量设备的精度限制和测量方法的不完善而导致的误差。
要点一要点二详细描述测量是机械加工中不可或缺的一环,但由于测量设备的精度限制和测量方法的不完善,往往会产生测量误差。
例如,使用卡尺测量时,由于卡尺的刻度精度有限,会导致测量结果存在误差;同时,测量方法的不正确也会导致误差的产生。
如测量时没有保证工件与卡尺之间的平行度或垂直度,就会产生测量误差。
02减小机械加工误差的措施直接减小或消除误差法直接减小或消除误差法是通过直接减少或消除原始误差来降低加工误差的方法。
例如,通过提高机床的几何精度、减小刀具和夹具的制造误差、提高工件的定位精度等措施,可以有效地减小加工误差。
齿轮误差测量技术
齿轮误差测量技术齿轮误差测量技术是一种用于评估齿轮传动精度的重要手段,它能够帮助我们了解齿轮系统的性能特征和运行稳定性。
本文将介绍齿轮误差测量技术的原理、方法和应用。
一、齿轮误差的定义齿轮误差是指齿轮齿面形状与标准理论齿面形状之间的偏差。
齿轮误差包括齿距误差、齿厚误差、齿形误差和齿向误差等。
这些误差会直接影响齿轮的传动性能和运行精度。
二、齿轮误差测量的原理齿轮误差测量的原理基于齿轮传动中齿轮的相对运动。
通过比较实际齿轮的齿面形状与理论标准齿面形状之间的差异,可以得到齿轮的误差信息。
三、齿轮误差测量的方法1. 压痕法:利用齿轮传动中的轻微滑动,通过测量齿面的压痕形状和尺寸来推测齿轮的误差。
2. 测量仪法:使用齿轮测量仪器,如齿轮测量机、齿轮检测仪等,通过测量齿轮齿距、齿厚、齿形等参数来评估齿轮的误差。
3. 光学法:利用光学原理,通过测量齿轮齿面的反射光线,可以得到齿轮的误差信息。
4. 数学建模法:采用计算机模拟和数学建模的方法,通过建立齿轮传动的数学模型,可以计算出齿轮的误差。
四、齿轮误差测量的应用1. 齿轮制造和质量控制:齿轮误差测量技术可以用于齿轮的制造过程中,帮助制造商控制齿轮的质量,提高齿轮的精度和可靠性。
2. 齿轮故障诊断:通过测量齿轮的误差,可以判断齿轮是否存在故障或磨损,及时进行维修和更换,避免齿轮故障对机械设备的影响。
3. 齿轮优化设计:通过分析齿轮的误差信息,可以优化齿轮的设计和制造工艺,提高齿轮的传动效率和性能。
4. 齿轮研究和发展:齿轮误差测量技术可以用于齿轮的研究和发展,帮助研究人员了解齿轮的性能特点,推动齿轮技术的进步和创新。
总结起来,齿轮误差测量技术可以帮助我们评估齿轮的传动精度和运行稳定性。
通过测量齿轮的误差,可以指导齿轮的制造、质量控制和故障诊断,同时也促进了齿轮技术的研究和发展。
在实际应用中,我们可以根据具体情况选择合适的测量方法和仪器,以获得准确可靠的齿轮误差信息。
齿轮加工误差分析及加工质量提高方法
随着齿轮工业的不 断 发 展,齿 轮 制 造 和 测 量 技 术 不 断 提高。影响其精度的 因 素 很 多,通 过 对 影 响 齿 轮 加 工 精 度 因素的分析,来 寻 求 提 高 滚 齿 精 度 的 途 径 ,使 齿 轮 加 工 精 度得到不断提高,是我 们 在 今 后 的 生 产 实 际 中 需 要 不 断 解 决的问题。
(7)提高接触精 度。 研 磨 是 在 其 他 金 属 切 削 加 工 方 法 未能满足工件精度和 表 面 粗 糙 度 要 求 时,所 采 用 的 一 种 精 密加工工艺。自身具 有 润 滑 作 用,研 磨 时 的 磨 料 对 工 件 进 行微量切削的压力可 达 工 件 的 工 作 负 荷,被 研 工 件 表 面 不 划伤、不嵌砂、不胶 合,且 可 在 很 高 温 度 下 使 用。 当 齿 轮 加 工精 度 低、齿 面 粗 糙,在 啮 合 中 仅 有 少 数 几 点 接 触 时 ,会 产 生噪声和振 动,研 磨 可 以 降 低 噪 声 ,成 为 提 高 产 品 质 量 的 关键问题。研磨剂可 以 用 于 各 种 材 料 的 齿 轮 及 蜗 轮 、蜗 杆 研磨,可以使其精度 提 高 2 个 等 级 以 上。 只 要 适 当 选 择 研 磨剂的粒度,可 以 满 足 所 要 求 的 任 何 粗 糙 度 值 ,从 而 可 以 提高传动效率。需要 进 行 磨 削 的 齿 轮,在 精 滚 和 硬 化 处 理 后可不经磨 齿,装 配 后 直 接 在 工 作 状 态 下 进 行 研 磨 ,其 效 率比磨齿高 十 几 倍 至 几 十 倍 ,且 质 量 超 过 磨 齿,又 比 磨 齿 经 济 。 因 此 ,它 是 一 种 提 高 齿 轮 精 度 的 有 效 方 法 。 5 结 束 语
- 1、下载文档前请自行甄别文档内容的完整性,平台不提供额外的编辑、内容补充、找答案等附加服务。
- 2、"仅部分预览"的文档,不可在线预览部分如存在完整性等问题,可反馈申请退款(可完整预览的文档不适用该条件!)。
- 3、如文档侵犯您的权益,请联系客服反馈,我们会尽快为您处理(人工客服工作时间:9:00-18:30)。
齿轮的数控加工原理及误差分析
1 引言
随着生产的发展, 数控机床特别是加工中心已得到广泛的应用。
在数控机床上, 加工齿轮是复合加工要解决的问题, 目前大多数数控机床已具备了齿轮加工的潜在能力。
为了在数控机床上加工齿轮并保证齿轮的加工精度, 应了解齿轮加工过程中可能产生的各种误差, 以便针对各种误差找出原因, 寻求相应的解决办法。
本文提出数控机床加工齿轮的方法, 并分析、比较在数控机床上由不同的加工方式加工齿轮所产生的误差。
2 滚齿加工原理
用齿轮滚刀加工齿轮, 其传动原理与一对螺旋齿轮的啮合原理相同, 而滚刀可以看成是一个齿数无穷多(头数可以为1) 的螺旋齿轮。
切削运动是滚刀的转动; 分齿运动是随着滚刀的转动, 齿坯也要相应的转动, 要求滚刀转速n刀与齿坯转速n工之间严格保持着相当于齿条与这个被加工齿轮啮合的关系。
也就是滚刀转动中刀齿在轴向移动一个齿距, 齿坯也相应地转过相应的齿距, 这个运动是滚齿加工最重要的运动。
垂直进给运动即滚刀沿齿坯齿宽方向的垂直进给(走刀) S。
加工过程如图1所示。
图1 滚齿加工示意图
3 对数控机床的要求
为了实现齿轮的加工, 需控制2 个伺服进给轴和2个伺服旋转轴。
以卧式加工中心为例,齿轮加工需要的运动有: 切削运动, 由机床主轴驱动滚刀回转; 展成运动, 即回转工作台按啮合关系回转; 齿宽方向的进给运动, 即滚刀的走刀运动, 由Y轴提供; 齿径方向的进给运动, 由X轴提供; 除有上述4 个基本运动外, 主轴相对“工作台”还应有可调的α角度(图2) 。
主轴的旋转运动实现滚刀在加工中的主体运动,滚刀的旋转运动和工件的旋转运动形成范成运动。
如图2所示为滚齿加工的示意图。
图2 齿轮加工运动示意图
4 误差分析
数控系统精度。
由图2可看出, 保证各轴的位置精度和运动精度是保证齿轮加工精度的重要条件。
对于配有设计完善的位置伺服系统的加工中心, 其定位精度和加工精度主要取决于位置检测元器件的精度和2个旋转轴静态和动态的同步精度。
一般来说,高精度的数控系统完全可以满足上述精度要求。
如果是一般的数控系统, 则要计算刀具旋转轴的分度误差, 按展成关系折算到旋转工作台上是否能满足所加工齿轮的精度要求。
例如, 滚齿时所要求达到7级精度, 加工一个齿数为100, 模数为3 的齿轮, 折算到刀具主轴的分度精度应大于01035°。
加工误差。
主要是由于工作台和刀具转速不均匀, 使刀具相对工
作台的瞬时传动比发生变化, 从而使被加工齿轮引起误差, 该误差是由回转工作台分度蜗轮本身的制造误差(采用电子齿轮分度可不考虑此项误差) 和滚刀轴的跳动所造成的。
在数控机床上加工齿轮, 由于刀具主轴是悬臂梁, 刀具所受到的力矩对刀具主轴有影响。
一般滚齿机的刀具主轴是简支梁, 在同样的受力情况下, 悬臂梁产生翘曲变形, 对加工误差影响很大。
铣齿与滚齿有所不同。
在普通机床上是采用具有渐开线齿形的“模数铣刀”逐齿铣出齿轮的齿廓,这种方法的加工精度受齿数的影响。
基于数控加工的特点, 可以采用柱状或片状铣刀用展成法加工齿轮。
柱状铣刀加工原理如图3所示: 垂直进给运动S走出齿深; 铣刀沿齿坯齿宽方向进给(走刀) 一次, 展成回转一个φ角度, 如图4所示, 再次沿齿宽方向进给一次, 直至展成整个齿面; 分齿后加工下一个齿面。
由图3可以看出, 柱状铣刀用展成法对齿轮进行断续展成切削加工, 其理论上的渐开线是由单一参数的基圆渐开螺旋线的有限切平面族来近似的, 而理论渐开螺旋面是这个单一参数的无限个平面的包络面,由它引起的齿形误差在齿形和齿面上都可以反映出来, 误差形成原理如图4所示。
图3 铣齿加工示意图图4齿形棱度形成示意图
式中: φ—工件齿形上相邻切削点在工件上的相邻角度; ρx —齿面某点的曲率半径; ρ—切削刃处的曲率半径。
又因为
假设: ρH —展成长度; N ′—展成的次数; rj—基圆半径; α—分度圆上的齿形压力角。
上式表明展成时的回转角度φ越大, 展成的次数就越少; 基圆直径越小, 引起的齿形误差就越大。
展成的最小回转角度取决于刀具主轴上的分度精度。
在展成过程中, 刀具的径向跳动量ΔEr 和刀具轴向窜动量ΔEx , 对被切齿轮齿形的影响有如下关系:
滚齿时的误差公式为
Δf =ΔEr sinα+ΔEx cosα( 6)
铣齿时的误差公式为
Δf =ΔEr cosα+ΔEx sinα( 7)
刀具径向跳动量的大小将直接反映在齿形上。
因此, 采取有效措施保证刀具主轴的精度是稳定齿轮加工精度的主要措施之一。
5 结论
(1) 在数控机床上加工齿轮, 需要机床具有至少两个联动旋转轴, 否则不能实现齿轮加工需要的基本运动, 通常采用机床主轴并附加一个数控旋转工作
台。
(2) 在数控机床上采用滚齿方式加工齿轮时,主轴的径向跳动和运动平稳性是保证齿轮精度的关键因素。
主轴的误差直接影响齿轮的齿形误差, 同时对
齿面波形高度影响也很大。
(3) 使用数控机床加工齿轮, 对刀具展成时回转角度的分辨率有严格的要求, 即对编码器能达到的最大分辨率有要求。
(4) 使用滚齿方式加工齿轮, 较铣齿展成方式更为方便和具有较高的效率, 齿面的波形高度也较低。