齿轮误差分析
齿轮传动轴的传动误差与回转间隙分析

齿轮传动轴的传动误差与回转间隙分析引言齿轮传动是常见的一种机械传动形式,广泛应用于工业机械领域。
在齿轮传动中,传动误差和回转间隙是重要的性能指标,对传动系统的精度和运行稳定性有着重要影响。
本文将针对齿轮传动轴的传动误差与回转间隙进行详细分析,探讨它们的原因以及对传动系统性能的影响。
一、传动误差的定义与分类传动误差是指齿轮传动轴在工作过程中由于齿轮的制造、装配等因素,导致输出轴承载方向的误差。
在齿轮传动中,常见的传动误差主要包括齿形误差、齿隙误差和轴向移位误差。
1. 齿形误差:齿形误差是指齿轮齿廓形状与理想齿廓的差异。
齿形误差可以通过齿轮的制造工艺、加工精度以及齿形检测仪器的性能等因素引起。
齿形误差会导致传动系统的噪声和振动增加,降低传动系统的工作效率。
2. 齿隙误差:齿隙误差是指齿轮齿槽之间的间隙大小不一致。
齿隙误差可以由齿轮的制造工艺、装配过程中的间隙控制等因素引起。
齿隙误差会导致传动系统的动态特性变差,降低传动系统的响应速度和稳定性。
3. 轴向移位误差:轴向移位误差是指齿轮轴在工作过程中由于装配不精确或轴向载荷造成的轴向偏移。
轴向移位误差会导致传动系统的运行不平稳,产生冲击和振动,严重时会导致传动轴的断裂。
二、传动误差的影响因素传动误差的产生与多个因素相关,主要包括齿轮的加工工艺、装配精度、使用环境、负载情况等。
1. 加工工艺:齿轮的加工工艺是影响传动误差的重要因素之一。
制造齿轮时,加工精度越高产生的传动误差就越小。
高精度的加工设备和工艺可以减少齿形误差和齿隙误差的产生。
2. 装配精度:齿轮装配过程中的精度控制也会对传动误差产生重要影响。
装配精度越高,齿轮的传动误差就越小。
装配精度主要包括齿轮齿轮间隙的控制、轴向偏移的控制等。
3. 使用环境:齿轮传动系统的使用环境对传动误差有着重要影响。
高温、高湿、高腐蚀等环境会导致齿轮表面的磨损加剧,进而影响传动误差。
4. 负载情况:齿轮传动系统的负载情况也会对传动误差产生影响。
齿轮传递误差

齿轮传递误差一、引言齿轮传递误差是指在齿轮传动过程中,由于制造工艺、材料性能、运动精度等因素的影响,使得实际传动比与理论传动比之间存在差异的现象。
齿轮传递误差会对机械设备的运行精度和寿命产生重要影响,因此研究齿轮传递误差具有重要意义。
二、齿轮传递误差的分类1. 几何误差几何误差是指由于加工和装配等原因导致齿轮副中心距、啮合角度、模数等几何参数与理论值之间存在偏差。
几何误差是影响齿轮副传动精度最主要的因素之一。
2. 运动误差运动误差是指由于机构本身刚度不足或外力干扰等原因导致齿轮副转动过程中出现的偏移。
运动误差会导致实际啮合点位置与设计啮合点位置不同,从而影响传动精度。
3. 材料和加工质量问题材料和加工质量问题也会对齿轮传递误差产生影响。
例如,材料的硬度、强度等性能不符合要求,或者加工过程中出现的表面粗糙度、几何形状等问题都会导致齿轮副传动精度下降。
三、齿轮传递误差的计算方法1. 理论传动比计算法理论传动比是指在理想情况下齿轮副的传动比。
根据齿轮几何参数和啮合理论,可以通过以下公式计算出理论传动比:i = (z2/z1) * (cosα1/cosα2)其中,i为传动比;z1和z2为两个齿轮的齿数;α1和α2为两个齿轮啮合时法线与切线夹角。
2. 实际传动比测量法实际传动比是指在实际运行中齿轮副的传动比。
可以通过测量输出轴转速和输入轴转速,然后计算出实际传动比。
实际测量中需要注意测量仪器的精度和稳定性。
3. 频谱分析法频谱分析法是一种基于信号处理技术的方法,可以通过对输入输出信号进行频谱分析,从而得到齿轮副的传动误差。
该方法需要使用专门的测试设备和软件。
四、减小齿轮传递误差的方法1. 提高齿轮几何精度提高齿轮几何精度是减小齿轮传递误差最有效的方法之一。
可以通过提高加工精度、改进加工工艺等方式来提高齿轮几何精度。
2. 优化设计在设计阶段就考虑到齿轮副的传动误差问题,采取合适的设计方案和材料选择,可以有效地减小传动误差。
齿轮加工中剃齿的误差分析及处理

剃齿 加 工 过 程 中 ,刀 具 与 工 件 间 没 有 传 动 链 , 而 是一种 自由运 动 。剃 齿 对 校 正 被 剃 齿 轮 的各 项 误 差 能力是 不 同的 ,有 些 剃 齿 误 差 能够 校 正 ,有 些 剃 齿误 差基 本 不 能 校 正 ,或 校 正 后 又 转 换 为 以别 的 误 差形 式 出现 。剃齿 是 “自由啮合 ”,无强 制 的分 齿 运 动 ,故分 齿均 匀性 无 法 控 制 。 由 于 剃 前 齿 轮 有 径 向 误差 ,在 开始 剃 齿 时 ,剃 齿 刀 只 能 与 工 件 上 距 旋 转 中心 较远 的齿 廓 作 无 侧 隙 啮合 的剃 削 ,而 与 其 他 齿 则变 成有 齿 侧 间 隙 ,但 此 时无 剃 削作 用 。连 续 径 向 进给,其他齿逐渐与刀齿作无侧 隙啮合。结果齿圈 原有 的径 向跳 动 △F 减 少 了 ,但 齿 廓 的位 置 沿 切 向 发生 了新 的变 化 ,公 法 线 长 度 变 动 量 △F 增 加 。其 转 移 量 的大小 可按 下式计 算 :
合评价齿轮的运动精度时,其合成值  ̄/AFZr+AFZw要 小 于 实测 的 运 动 精 度 。所 以 ,剃 齿 后 出现 齿 轮 公 法 线 长度 变 动 量 超 差 ,并 不一 定 意 味 着 该 齿 轮运 动 精
度 不合 格 。只要 齿 轮 的齿 圈 径 向 跳 动 和 公 法 线 长 度 变 动量 这两个 误 差项 目的实 际误 差 值 之 和 不超 过 两 单 项允 许误 差 之 和 ,即 可认 为该 T 件合 格 。这 就 避 免 了 因单 项误 差超 差就 判断齿 轮报 废而 造成 的损失 。
免这 种 中凹齿 形 的 产生 。 中 凹齿
形是 剃齿 加工 过程 中存在 的主 要 图1 齿形中凹
齿轮精度出现偏差的5大原因
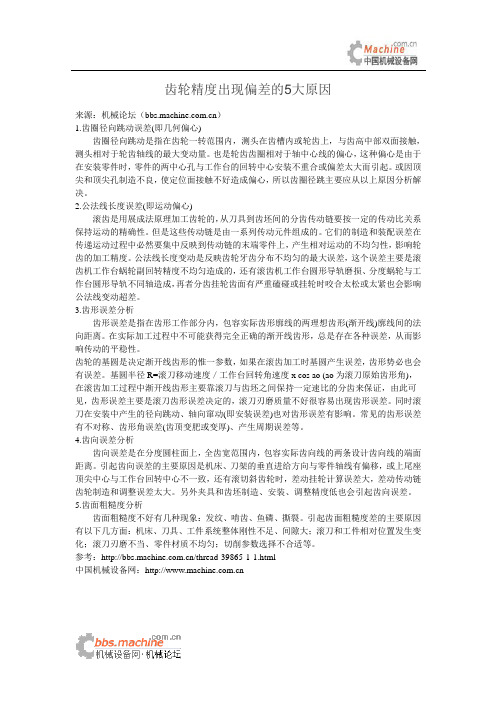
齿轮精度出现偏差的5大原因来源:机械论坛()1.齿圈径向跳动误差(即几何偏心)齿圈径向跳动是指在齿轮一转范围内,测头在齿槽内或轮齿上,与齿高中部双面接触,测头相对于轮齿轴线的最大变动量。
也是轮齿齿圈相对于轴中心线的偏心,这种偏心是由于在安装零件时,零件的两中心孔与工作台的回转中心安装不重合或偏差太大而引起。
或因顶尖和顶尖孔制造不良,使定位面接触不好造成偏心,所以齿圈径跳主要应从以上原因分析解决。
2.公法线长度误差(即运动偏心)滚齿是用展成法原理加工齿轮的,从刀具到齿坯间的分齿传动链要按一定的传动比关系保持运动的精确性。
但是这些传动链是由一系列传动元件组成的。
它们的制造和装配误差在传递运动过程中必然要集中反映到传动链的末端零件上,产生相对运动的不均匀性,影响轮齿的加工精度。
公法线长度变动是反映齿轮牙齿分布不均匀的最大误差,这个误差主要是滚齿机工作台蜗轮副回转精度不均匀造成的,还有滚齿机工作台圆形导轨磨损、分度蜗轮与工作台圆形导轨不同轴造成,再者分齿挂轮齿面有严重磕碰或挂轮时咬合太松或太紧也会影响公法线变动超差。
3.齿形误差分析齿形误差是指在齿形工作部分内,包容实际齿形廓线的两理想齿形(渐开线)廓线间的法向距离。
在实际加工过程中不可能获得完全正确的渐开线齿形,总是存在各种误差,从而影响传动的平稳性。
齿轮的基圆是决定渐开线齿形的惟一参数,如果在滚齿加工时基圆产生误差,齿形势必也会有误差。
基圆半径R=滚刀移动速度/工作台回转角速度x cos ao (ao为滚刀原始齿形角),在滚齿加工过程中渐开线齿形主要靠滚刀与齿坯之间保持一定速比的分齿来保证,由此可见,齿形误差主要是滚刀齿形误差决定的,滚刀刃磨质量不好很容易出现齿形误差。
同时滚刀在安装中产生的径向跳动、轴向窜动(即安装误差)也对齿形误差有影响。
常见的齿形误差有不对称、齿形角误差(齿顶变肥或变厚)、产生周期误差等。
4.齿向误差分析齿向误差是在分度圆柱面上,全齿宽范围内,包容实际齿向线的两条设计齿向线的端面距离。
齿形齿向误差分析
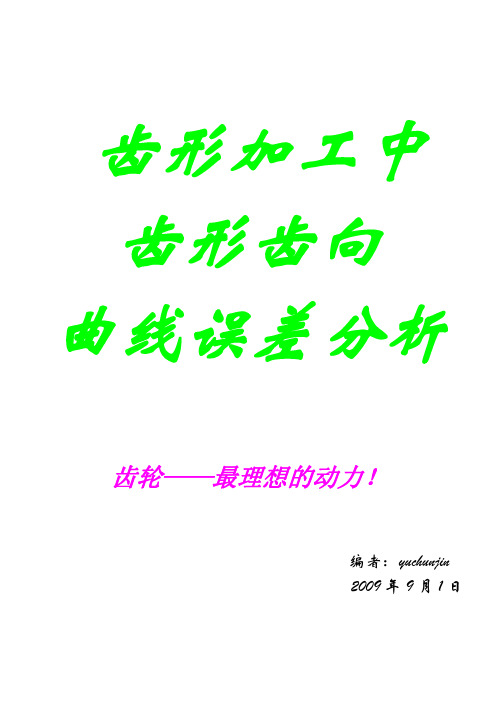
3、两侧四根曲线都倾斜,且倾斜的方向相反,见《图四》, 第六页
这种情况是由于滚齿机刀架导轨相对于工作台回转轴线在径 向的平行度误差的影响。
《图四》
4、齿向曲线基本走向不倾斜,但弯弯曲曲,我们称之为 螺旋线形状误差,这里分两种情况:a、形状不规则,数值不 大,如《图五》所示。主要是齿坯的硬度偏低或刀具不快,在 制齿过程中造成齿面拉毛或者是进刀量过大,走刀速度过快引 起机床振动造成的;b、形状规则,具有不变的波长和基本不变 的宽度如 b 图所示,主要原因是进给丝杆的轴向和径向跳动, 分度传动链的短周期误差引起的。
《图九》
第四页
齿向误差曲线分析
在渐开线圆柱齿轮精度误差项目中,螺旋线(齿向)精度 是重要项目之一,是影响齿轮接触精度的主要指标之一。如果 齿向误差较大,会影响齿轮的接触精度,降低齿轮的使用寿命, 破坏传动平稳性、振动和噪喑。
一、测量部位评定长度的选取 为了正确地全面地反映的形状,一般在齿轮的圆周上均分 四个齿面上测量,然后在另一侧齿面上进行同样的测量,测量 部位应在齿轮的分度圆附近。如果齿轮的模数越大,则要考虑 在同一齿面上测量两人个截面。 测量长度应是整个齿宽,评定长度应考虑端面倒棱的影响。 二、螺旋线误差曲线形状 1、无螺旋线误差的曲线为理论螺旋线,为一条直线。见《图 一》a 所示。当设计螺旋线为鼓形时,无螺旋线误差的曲线为 中凸,见《图一》b 所示。 2、有螺旋线误差的曲线,曲线倾斜,对于右哀旋齿轮, 曲线向右倾斜,则螺旋角增大,反之则螺旋角减小;对于左旋 齿轮,曲线向右倾斜,则螺旋角减小,反之则增大,见《图一》 c、b。
a
b
c
d
《图六》 2、同一侧四根曲线向同一方向倾斜,而另一侧四根曲线也向
同一方向倾斜,两侧都是顶正或顶负,如《图七》a、b 所示。
齿轮的误差及其分析

齿轮误差及其分析第一节:渐开线圆柱齿轮精度和检测对于齿轮精度,主要建立了下列几个方面的评定指标:一.运动精度:评定齿轮的运动精度,可采用下列指标:1.切向综合总偏差F i′:定义:被测齿轮与理想精确的测量齿轮单面啮合时在被测齿轮一转,(实际转角与公称转角之差的总幅度值)被测齿轮的实际转角与理论转角的最大差值。
切向综合总偏差F i′。
(它反映了齿轮的几何偏心、运动偏心和基节偏差、齿形误差等综合结果。
)ΔF i2.齿距累积总偏差F p,齿距累积偏差F pk。
定义:齿轮同侧齿面任意弧段(k=1或k=z)的最大齿距累积偏差。
它表现为齿距累积偏差曲线的总幅值。
——齿距累积总偏差。
在分度圆上,k个齿距的实际弧长与公称弧长之差的最大绝对值,称k个齿距累积误差ΔF pk。
k为2到小于Z/2的正数。
这两个误差定义虽然都是在分度圆上,但实际测量可在齿高中部进行。
这项指标主要反映齿轮的几何偏心、运动偏心。
用ΔF p 评定不如ΔF i′全面。
因为ΔF i是在连续切向综合误差曲线上取得的,而ΔF p不是连续的,它是折线。
ΔF i′= ΔF p+ Δf f测量方法:一般用相对法,在齿轮测量机上测量。
3.齿圈径向跳动ΔF r与公法线长度变动ΔF w:ΔF r定义:在齿轮一转围,测头在齿槽,于齿高中部双面接触,测头相对于齿轮轴线的最大变动量。
它只反映齿轮的几何偏心,不能反映其运动偏心。
(用径跳仪测量检测。
)由于齿圈径跳ΔF r 只反映齿轮的几何偏心,不能反映其运动偏心。
因此要增加另一项指标。
公法线长度变动ΔF w。
ΔF w定义:在齿轮一周围,实际公法线长度最大值与最小值之差。
ΔF w=W max-W min测量公法线长度实际是测量基圆弧长,它反映齿轮的运动偏心。
测量方法:用公法线千分尺测量。
4.径向综合误差ΔF i″和公法线长度变动ΔF w:齿轮的几何偏心还可以用径向综合误差这一指标来评定。
ΔF i″定义:被测齿轮与理想精确的测量齿轮双面啮合时,在被测齿轮一转,双啮中心距的最大变动量。
阐述渐开线齿轮齿形误差的分析方法

阐述渐开线齿轮齿形误差的分析方法1.前言渐开线齿轮是机器中常用的一种零件,它的用途是传递动力或运动。
齿轮之间的传动,是依靠主动轮的牙齿依次推动被动轮的牙齿来实现的。
牙齿两侧面的形状(齿面形状,即齿形)对于齿轮的传动和工作平稳性都有重要影响。
因此,必须了解渐开线齿轮齿形误差产生的原因及分析方法。
2.渐开线齿轮齿形特点所谓渐开线,是一根切线在基圆(作为描绘渐开线基础的一个圆)上纯滚动(即没有滑动的转滚运动)时,画出该切线滚动边缘上任意一点的运动轨迹。
如图1所示:图中的aa1和bb1就是切线纯滚动时a1和b1两点所画出来的渐开线。
显然,因为是同一个基圆,所以这两条渐开线是完全一样的,仅仅是它们的起点不同。
渐开线齿轮传动时,具有在任何瞬时的转速比都不改变,并且在相互啮合的齿轮的齿轮副中心距发生变化时传动比仍保持不变的特点。
在加工时,可以用模数、压力角相同的齿轮刀具加工模数、压力角相同而齿数不同的齿轮,因此,在机械制造行业中渐开线齿形齿轮应用得最为普遍。
3.渐开线齿轮齿形误差的分类及产生原因齿形误差是指在齿轮工作部分容纳实际齿形的两理论齿形间的法向距离,其△f只允许偏向齿体内。
在渐开线齿轮加工过程中,容易产生以下几种齿形误差:a.齿形角误差:即不是标准压力角的齿形,而是压力角大于或小于标准值的齿形,产生这种情况是由于磨齿时砂轮磨削角调整偏大或偏小,以至使所磨齿轮的基圆半径发生了变化。
b.齿形不对称:即齿歪现象,一面齿形的压力角大于标准值,而另一面齿形的压力角小于标准值。
齿形不对称的原因往往是由于采用锥面砂轮时,砂轮两边锥面磨削角修整得大小不同所致。
c.齿形曲率改变:即实际齿形曲率大于或小于理论齿形曲率,曲率的改变是由齿轮加工时的安装误差引起的。
d.齿形根切:即齿根部的渐开线齿形被切去,它的形成多数是由于所磨齿轮齿数较少,而磨削角又太小以及砂轮外圆无圆角引起的。
e.齿根圆角和齿顶特粗误差:即齿根过渡曲线部分的圆角太大,或接近齿顶的一部分齿形特别粗大。
齿轮误差名词解释

齿轮误差名词解释齿轮误差是指齿轮传动中由于制造和装配等因素导致的偏差,常常表现为齿轮间的轴向偏移、径向偏移、倾斜、测量误差等。
齿轮误差对于齿轮传动的正常运行具有重要影响,这也是工程师在设计和制造齿轮时需要考虑的一项重要指标。
首先,齿轮误差通常被描述为齿轮齿形偏差。
齿轮的齿形偏差主要是由于制造和切削等工艺过程中产生的偏差所致。
齿形偏差包括齿距偏差、齿顶偏差、齿根偏差等。
齿距偏差是指齿轮齿距与其理论值之间的偏差,这会直接影响到齿轮传动的传动比和传动效率。
齿顶和齿根偏差则会影响到齿轮的啮合性能和噪声水平。
其次,齿轮误差还包括轴向偏移误差。
轴向偏移误差是指齿轮轴线与理想位置之间的偏差。
这种误差会导致齿轮轴向力的不均匀分布,从而引发齿轮的振动和噪声。
除了轴向偏移误差,径向偏移误差也是一种常见的齿轮误差。
径向偏移误差是指齿轮中心距离理想中心线的偏差。
这种误差会导致齿轮轴承载荷不均匀,从而影响齿轮传动的工作寿命和可靠性。
齿轮的倾斜是另一种常见的齿轮误差。
倾斜是指齿轮齿面与它所在平面之间的夹角偏差。
这种误差会导致齿轮在传动过程中发生侧向力和额外的扭矩,从而引起齿轮传动的低效率和噪声。
除了倾斜误差外,测量误差也是一种重要的齿轮误差。
由于齿轮通常需要通过测量来确定其精度和质量,测量误差会对齿轮传动的评估和使用产生重要影响。
为了解决齿轮误差对齿轮传动性能的不利影响,工程师们通常采取一系列措施进行误差补偿和校正。
例如,制造过程中可以采用高精度的数控切削技术来减小齿形偏差;装配过程中可以通过精度检测和调整来减小轴向偏移和径向偏移误差。
此外,齿轮的设计和传动结构的优化也是降低齿轮误差的重要手段。
总结起来,齿轮误差是指齿轮传动中由于制造和装配等因素造成的偏差。
齿轮误差主要包括齿形偏差、轴向偏移误差、径向偏移误差、倾斜误差和测量误差等。
这些误差会对齿轮传动的性能和可靠性产生重要影响,因此在齿轮设计和制造过程中需要重视对齿轮误差的控制和优化。
- 1、下载文档前请自行甄别文档内容的完整性,平台不提供额外的编辑、内容补充、找答案等附加服务。
- 2、"仅部分预览"的文档,不可在线预览部分如存在完整性等问题,可反馈申请退款(可完整预览的文档不适用该条件!)。
- 3、如文档侵犯您的权益,请联系客服反馈,我们会尽快为您处理(人工客服工作时间:9:00-18:30)。
1.1 齿圈径向跳动误差(即几何偏心)
齿圈径向跳动是指在齿轮一转范围内,测头在齿槽内或轮齿上,与齿高中部双面接触,测头相对于轮齿轴线的最大变动量。
也是轮齿齿圈相对于轴中心线的偏心,这种偏心是由于在安装零件时,零件的两中心孔与工作台的回转中心安装不重合或偏差太大而引起。
或因顶尖和顶尖孔制造不良,使定位面接触不好造成偏心,所以齿圈径跳主要应从以上原因分析解决。
1.2公法线长度误差(即运动偏心)
滚齿是用展成法原理加工齿轮的,从刀具到齿坯间的分齿传动链要按一定的传动比关系保持运动的精确性。
但是这些传动链是由一系列传动元件组成的。
{HotTag}它们的制造和装配误差在传递运动过程中必然要集中反映到传动链的末端零件上,产生相对运动的不均匀性,影响轮齿的加工精度。
公法线长度变动是反映齿轮牙齿分布不均匀的最大误差,这个误差主要是滚齿机工作台蜗轮副回转精度不均匀造成的,还有滚齿机工作台圆形导轨磨损、分度蜗轮与工作台圆形导轨不同轴造成,再者分齿挂轮齿面有严重磕碰或挂轮时咬合太松或太紧也会影响公法线变动超差。
1.3齿形误差分析
齿形误差是指在齿形工作部分内,包容实际齿形廓线的两理想齿形(渐开线)廓线间的法向距离。
在实际加工过程中不可能获得完全正确的渐开线齿形,总是存在各种误差,从而影响传动的平稳性。
齿轮的基圆是决定渐开线齿形的惟一参数,如果在滚齿加工时基圆产生误差,齿形势必也会有误差。
基圆半径R= 滚刀移动速度/工作台回转角速度x cos ao (ao为滚刀原始齿形角),在滚齿加工过程中渐开线齿形主要靠滚刀与齿坯之间保持一定速比的分齿来保证,由此可见,齿形误差主要是滚刀齿形误差决定的,滚刀刃磨质量不好很容易出现齿形误差。
同时滚刀在安装中产生的径向跳动、轴向窜动(即安装误差)也对齿形误差有影响。
常见的齿形误差有不对称、齿形角误差(齿顶变肥或变厚)、产生周期误差等。
1.4齿向误差分析
齿向误差是在分度圆柱面上,全齿宽范围内,包容实际齿向线的两条设计齿向线的端面距离。
引起齿向误差的主要原因是机床、刀架的垂直进给方向与零件轴线有偏移,或上尾座顶尖中心与工作台回转中心不一致,还有滚切斜齿轮时,差动挂轮计算误差大,差动传动链齿轮制造和调整误差太大。
另外夹具和齿坯制造、安装、调整精度低也会引起齿向误差。
1.5齿面粗糙度分析
齿面粗糙度不好一般有几种现象:发纹、啃齿、鱼磷、撕裂。
引起齿面粗糙度差的主要原因有以下几方面:机床、刀具、工件系统整体刚性不足、间隙大;滚刀和工件相对位置发生变化;滚刀刃磨不当、零件材质不均匀;切削参数选择不合适等。