套筒窑
气烧套筒窑内燃烧条件的优化研究

气烧套筒窑内燃烧条件的优化研究摘要:本研究旨在优化气烧套筒窑内的燃烧条件,以提高窑炉的热效率和生产效率。
通过实验和数值模拟,我们探讨了不同的燃烧参数对窑炉内温度分布、烟气成分、燃烧效率等因素的影响,并对窑炉内部的气流和温度场进行了分析。
研究结果表明,在一定的氧化剂过剩系数下,适当提高燃料供给量和燃料与空气的混合速度,可以显著提高窑炉的热效率和生产效率。
本研究对于气烧套筒窑内的燃烧优化提供了有益的参考和指导。
关键词:气烧套筒窑、燃烧条件、热效率、生产效率、数值模拟一.绪论气烧套筒窑作为一种常见的烧结设备,在陶瓷、水泥、建材等行业得到广泛应用。
气烧套筒窑内的燃烧条件直接关系到窑炉的热效率和生产效率,因此研究气烧套筒窑内的燃烧优化显得尤为重要。
本文旨在对气烧套筒窑内的燃烧条件进行优化研究,探讨不同燃烧参数对窑炉内部温度分布、烟气成分、燃烧效率等因素的影响,并对窑炉内部的气流和温度场进行分析,为提高气烧套筒窑的燃烧效率和生产效率提供参考和指导。
二.气烧套筒窑内燃烧的基本原理2.1 气烧套筒窑的结构和燃烧方式气烧套筒窑由进料段、烧结段和冷却段组成。
窑炉内部设置有燃烧器,将燃料和空气混合后燃烧,产生高温气体,将进料段的原材料进行热解和烧结,最终得到产品。
在窑炉的烧结段,高温气体与原材料进行热交换,完成烧结和半烧的过程。
在冷却段,对烧结完成的产品进行冷却,降低产品温度。
2.2 燃料与空气的混合过程燃料与空气的混合是气烧套筒窑内燃烧的关键过程。
在窑炉内部,燃料和空气在燃烧器内混合,形成可燃气体混合物。
燃烧器的结构和参数会影响混合的质量和效果。
混合质量的好坏,直接关系到气体的燃烧效率和热效率。
2.3 燃烧过程燃料和空气混合后,在燃烧器内部发生燃烧反应,产生高温燃烧气体,同时释放出热能。
这些燃烧气体通过喷嘴进入气烧套筒窑的进料段,与原材料进行热交换,完成热解和烧结的过程。
在烧结段,高温气体继续与原材料进行热交换,完成半烧和烧结的过程。
高温低氧燃烧(HTAC)技术在套筒窑上的应用

◎董卫东高温低氧燃烧(HTAC )技术在套筒窑上的应用前言:高温低氧燃烧(HTAC )技术是20世纪90年代以蓄热式燃烧技术为基础开发并在国外开始推广使用的一项全新环保节能燃烧技术。
该技术通过两项技术手段来实现:一是采用蓄热式烟气余热回收装置,将助燃空气预热到800以上,最大限度地回收高温烟气显热,实现余热的极限回收;二是控制燃烧区氧的浓度在15%~2%以内,达到燃烧过程NOx 的最低排放。
其燃烧基本原理是将燃料喷射到一种高温低氧的助燃剂中进行混合和燃烧。
高温低氧燃烧这概念中,高温是指参与燃烧反应的助燃剂温度高(一般>800℃),低氧是指助燃剂中氧气的浓度低(一般<15%)。
套筒式竖窑又名环形套筒窑,是上世纪60年代初德国贝肯巴赫-威尔曼斯特勒公司(BECKENBACH WARMESTELLE GMBH )发明的,与瑞士麦尔兹双膛竖窑同属世界上先进的石灰窑型,其主要特点是在窑内设置上、下两个内套筒,利用上、下内套筒与窑壳形成一个环形空间,并在窑壳外设置有蓄热式燃烧室,利用内筒与窑壳之间由异型耐火砖组合成的上、下拱桥将热量传递至环形空间内,通过拱桥的间错布置实现热量的均匀分布,石灰石原料自上而下在环形空间内经过预热、煅烧、冷却形成冶金石灰。
本文从高温低氧燃烧(HTAC )技术特性以及套筒窑的工艺特点入手,对比分析了高温低氧燃烧技术所需条件与现有套筒窑工艺的结合的可行性。
一、高温低氧燃烧(HTAC )技术理论分析按照燃烧学中理论燃烧温度的定义,实际理论燃烧温度的计算公式可表示为:T th 为理论燃烧温度;Qf 为燃料燃烧的化学热,kJ;L n 为实际空气消耗量,m 3;C a 为空气的平均比热容,kJ (/m 3·K );t a 为空气的预热温度,K;C f 为煤气的平均比热容,kJ (/m 3·K );t f为煤气的预热温度,K;C cp 为燃烧产物在tcp 温度下的平均比热容,kJ (/m 3·K );V n 为燃烧产物量,m 3。
白灰厂套筒窑存在问题

白灰厂5#6#7#套筒窑目前存在的问题
5#套筒窑8月11号检修,在清理废气管道积灰时,发现管道内有很多料石,最近几天在上料过程中明显听到有料石掉入废气管道,经检查发现5#导流槽有砸漏情况,导流槽破损会导致料石进入废气管道,会使管道内径变窄,影响了废气风机的排放量,要想达到预定值需增加废气风机频率,导致废气风机的用电量相比6#和7#高很多,造成用电成本上升。
如果长时间导流槽不进行焊补,导流槽砸落部位将会扩大,料石将直接掉落大墙耐火砖上,对窑顶大墙及上内套筒耐材都会有很大影响,根据套筒窑检修周期表,5#--7#套筒窑已经生产15个月,现已经达到每年将对套筒窑窑内耐材进行检查,对窑内积灰进行清理。
如果把5-7#套筒窑检修定于LNG投产以后检修的话。
恐怕有可能与1-4#窑拆迁相对应,为了保证期间对钢厂石灰的正常供应,请领导给予批示,将导流槽和预热带大墙掉砖情况及时处理,用时估计20天左右。
特此说明。
附件:白灰分厂套筒窑检修周期表:。
某焦化套筒窑施工技术总结(DOCX 41页)

目录一、工程概况 (1)1.套筒窑简介 (3)2.发展形势 (3)3.主要工程量 (4)二、对工程的认识及感悟: (5)三、技术总结施工主体思想 (7)1. 11.8m窑下附属结构安装 (7)1.1 底板环形圈安装 (7)1.2 筒体安装 (8)1.3 内部构件安装 (10)2. 窑体中段及内筒IC2安装 (15)2.1 内筒IC1上半部分 (15)2.2 第一吊装单元 (16)2.3 第二吊装单元 (16)2.4 内筒IC2支柱安装 (17)2.5 第三吊装单元 (17)2.6 T型梁安装 (18)2.7 第四吊装单元(内筒IC2) (18)2.8 第五、六吊装单元 (19)3. 窑顶系统安装 (21)3.1 V2系统外壳 (22)3.2 V2系统内壳 (24)3.3 上内筒IC3 (26)3.4 窑顶锥体 (28)3.5 V3及旋转布料器 (30)3.6 V4、V5、V6 防雨罩 (31)4.附属结构安装 (32)4.1 热交换器 (32)4.2 上料导轨 (33)4.3 上下部主楼梯 (34)4.4 上部平台及过桥 (34)四、技术方案的更新与优化 (35)九江焦化2*600T套筒窑工程技术工作总结一、工程概况1.套筒窑简介:套筒窑是原德国贝肯巴赫炉窑公司于1960年发明的,现已属于意大利贝肯巴赫公司。
贝肯巴赫窑由砌有耐火材料的窑壳和分成上下两端的内套筒组成,窑壳和内套筒同心布置,石灰石位于窑体和内套筒之间的环形空间内以利于气流穿透,故又名为环形套筒竖窑。
下内套筒位于竖窑的下部,结构为双层钢壳形成环隙,环隙内通空气冷却,其内外侧砌耐火砖衬;上内套筒悬挂在窑顶部。
上下内套筒各有其不同的功能,上内套筒主要是将高温废气抽出用于预热喷射空气;下内套筒主要用于产生循环气流形成并流煅烧,同时起到保证气流均匀分布的作用。
贝肯巴赫窑的结构特点是因设置了内套筒而在一个窑身内就形成了并流煅烧。
贝肯巴赫窑套筒窑从上到下分为:预热带、上部煅烧带(逆流)、中部煅烧带(逆流)、下部煅烧带(并流)、冷却带,其核心为下部并流煅烧带,石灰最终在下部煅烧带内烧成,保证了能够煅烧出优质活性石灰。
(完整版)套筒窑窑本体主要设备设施参数

每座套筒窑窑本体主要设备设施参数如下:1)上料卷扬小车系统,1套卷扬提升能力:4t;上料周期:约3min卷扬料斗容积:3m3For personal use only in study and research; not for commercial use电机功率:45kW,配变频器带一组限位开关2)窑顶布料系统,1套For personal use only in study and research; not for commercial usea.旋转布料器:驱动形式:两点液压马达驱动控制形式:接近开关控制For personal use only in study and research; not for commercial useb.料钟,1台动作形式:液压缸提升料钟行程:700mmFor personal use only in study and research; not for commercial use3)燃烧系统由6台上燃烧器和6台下燃烧器组成。
上燃烧器周圈均布在套筒窑外窑壳▽24.3m高度上,下燃烧器周圈均布在套筒窑外窑壳▽20.4m高度上。
4)换热器,1台结构形式为管状形式换热器,结构组成包括:烟气进口箱、管束箱、烟气出口箱和内衬结构等。
烟气进口温度:750℃烟气出口温度:400℃空气进口温度:常温℃空气出口温度:450℃5)出灰机,6台由固定框架和活动框架及液压缸等组成,圆周均布在外窑壳▽8.9m高度上。
驱动形式:液压缸驱动出灰能力:50kg/次液压缸行程:200mm6)带阀门的电振给料机,1台出灰能力:100t/h7)内套筒由上内套筒、中内套筒和下内套筒组成;上内套筒悬挂于套筒窑内上部;中内套筒和下内套筒组成安装于套筒窑内下部土建基础上。
8)驱动风机:2台(1台全风,1台变频)能力:75.4Nm3/min(每台风机)静压:6800mmH2O工作温度:常温装机功率:132kw有一台风机电机为变频控制。
套筒窑的应用、特点及发展前景分析

李延涛
摘 要 :本 文介 绍 了套 筒窑 在炼 钢 、 电石 : 中的应 用 ,套筒窑 的结 构特 点及 工作 原理 , 【业 石灰 活 性度 对炼 钢 、 电石工 业 的影 响 ,以及套 筒 窑发展 过程 和前 景展望 。 件 。而 高活性 度 的石 灰作 为炼 钢 溶剂 , 灰 石 活 性度 一般 大于 3 0 0ml以上 才 能实现 以上
好 ,因此要求 的石 灰活 性度 一 定要高 ,电石
种 少之 又 少 , 例如 目前 国 内高 铁 正在高 速 发 展 阶段 , 高速 钢 轨 刚刚 可 以实现 国产化 ,而
高速 车 轮 目前 全部 依靠 进 口。 以, 制 出 所 研
工业中, 生产 电石所 需石 灰活 性 度一般 大 于 3 0 ,才 能实现 以上效 果 。 3 ml 目前 国 内冶 金及 电石 行 业 中大 多 企业 在 采 用套 筒窑来煅 烧合 格石 灰 。 套筒窑 是德 国 贝肯 巴赫 窑炉 公 司发 明的 。 贝肯 巴赫 公 司 创 建 于 12 99年 ,主 要设 计煅 烧 活性石 灰 的 竖窑 ,15 以前 ,一 直用 焦 炭作 为燃料 , 9 5年 烧 出 的石 灰 活性 度 很低 。环 形 套筒 窑 是在 6 年 代初 产 生的 ,诞生 后得 到广泛推 广 , 0 至今 在全 世界 已有 4 0多座 , 国化 工系 统 0 我 于上 世纪 8 0年代 末在 张家 口 , 头,兰州 , 包 太原 化工 部 门建 了 5座 10/ 5t d的套筒 窑 , 接 着马钢、 钢、 梅 首钢 引进 50/ 0t d套筒 窑,99 19 年, 本钢 引进 一座 30/ 0t d套筒 窑 。原来 引进
好 的钢 种 , 当今 经 济高 速发 展 的中 国迫 在 在 眉 睫 。而轧 制 出好 的 品种钢 ,必须 要有 好 的 原材 料 钢种 。 中,炼钢 用石 灰就 是全 材料 其 之 一 ,而石 灰活 性度 的高低 ,将直 接影 响转 炉 等 的冶炼 效 果 。
套筒窑资料汇总
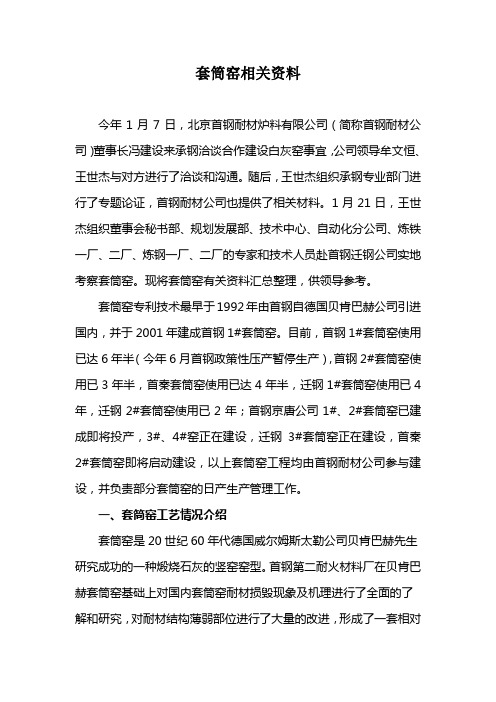
套筒窑相关资料今年1月7日,北京首钢耐材炉料有限公司(简称首钢耐材公司)董事长冯建设来承钢洽谈合作建设白灰窑事宜,公司领导牟文恒、王世杰与对方进行了洽谈和沟通。
随后,王世杰组织承钢专业部门进行了专题论证,首钢耐材公司也提供了相关材料。
1月21日,王世杰组织董事会秘书部、规划发展部、技术中心、自动化分公司、炼铁一厂、二厂、炼钢一厂、二厂的专家和技术人员赴首钢迁钢公司实地考察套筒窑。
现将套筒窑有关资料汇总整理,供领导参考。
套筒窑专利技术最早于1992年由首钢自德国贝肯巴赫公司引进国内,并于2001年建成首钢1#套筒窑。
目前,首钢1#套筒窑使用已达6年半(今年6月首钢政策性压产暂停生产),首钢2#套筒窑使用已3年半,首秦套筒窑使用已达4年半,迁钢1#套筒窑使用已4年,迁钢2#套筒窑使用已2年;首钢京唐公司1#、2#套筒窑已建成即将投产,3#、4#窑正在建设,迁钢3#套筒窑正在建设,首秦2#套筒窑即将启动建设,以上套筒窑工程均由首钢耐材公司参与建设,并负责部分套筒窑的日产生产管理工作。
一、套筒窑工艺情况介绍套筒窑是20世纪60年代德国威尔姆斯太勒公司贝肯巴赫先生研究成功的一种煅烧石灰的竖窑窑型。
首钢第二耐火材料厂在贝肯巴赫套筒窑基础上对国内套筒窑耐材损毁现象及机理进行了全面的了解和研究,对耐材结构薄弱部位进行了大量的改进,形成了一套相对比较先进、拥有自主知识产权的内衬设计,实践证明效果良好。
1、套筒窑内部结构特点套筒窑的结构如图2所示。
其主要有外套筒和同中心的上、下内套筒(5和18)构成,物料从环状的截面通过(预热、煅烧);该窑外设上下两排燃烧室(12和15),燃烧室的数量有燃料种类和窑的设计产量而定,燃烧室上、下错开分布,同排均匀分布;每个燃烧室均用“火桥”(16)把窑壳和内套筒连接起来,这样把煅烧带分为三部分——上煅烧带(28)、中煅烧带(29)和下煅烧带(30);上燃烧室(12)、下燃烧室(15)以及位于并流煅烧带(30)和冷却带(31)之间的内套筒上的循环气体入口(17)是相互不重合布置的,从而保证了在窑的整个截面上气体分布均匀;上、下内套筒的双壁钢壳衬有耐火材料,并用冷却空气(23)冷却,热气通过设在“火桥”内的管道离开内套筒,进入下环管(8),然后在作为二次空气送到燃烧室(12和15);驱动风机(32)把空气输送到预热器中用热废气预热,经预热后的空气被送到上环管(27)中,再从环形主管分配到喷射器(11),由喷射器带动循环气体循环。
贝肯巴赫环形套筒窑的技术特性

贝肯巴赫环形套筒窑的技术特性1、石灰石由料斗运至窑顶,经由一密封装置自动进入窑内,可避免大气进入窑内。
石灰石经窑顶的装料漏斗进入环形窑体。
环形套筒是由窑体外壳的耐火内衬和与窑外壳同心布置的下内筒和上内筒组成的。
上、下内筒位双壁夹层钢结构,衬有耐火材料,由空气冷却。
2、石灰石穿过预热带进入煅烧带,煅烧带布置上、下两层烧嘴,每一层由5个圆柱形燃烧室组成,每层的每个燃烧室都对称的固定在环形套筒内。
两层烧嘴将煅烧带分位两个部分:逆流运行的上部煅烧带和并流运行的下部煅烧带。
3、每个燃烧室上部有一个由耐火材料制成的拱桥,连接窑外壳和下内筒。
热气体从燃烧室出来,通过拱桥下边形成的一个自然净角空间,穿过石灰石料层料床,均匀分布到套筒截面各个石灰石料层中。
4、上、下燃烧室和连接下内筒和并流带与冷却带之间循环气体入口是错位布置的,有利于气体在窑横截面均匀分布。
5、冷却带在并流带下部,生石灰的热量转移到同逆流运行的石灰冷却气体。
石灰冷却气体由废气风机抽吸,成品灰经冷却带下部的液压推杆系统自动卸出,通过出料台进入石灰窑下部的石灰料仓。
6、用于预热驱动空气的废气,通过悬挂的上内筒抽吸到热交换器。
下内筒带有用于疏导热回流气体的开口和导管。
7、中压的环境空气被两台罗茨风机送入换热器,并在热交换器中被预热。
预热后的驱动空气从热交换器中出来进入环管,并经环管分布导5个喷射器中。
8、并流气体和被预热的石灰冷却空气一起被喷射器抽吸,通过循环气体入口进入内筒。
经由安置在上层拱桥内部的管道导出,被喷射器的驱动空气驱使进入5个下部燃烧室。
在下部燃烧室中,由于过剩空气的提供,燃料进入环形空间的石灰石料层前,就已经充分燃烧。
9、预热空气从下内筒出来,通过安置在5个上层拱桥的冷却管道被环管收集,作为预热燃烧气被送入到烧嘴。
10、热气体离开下部燃烧室后,分成两股不同的气流:一股气流被喷射器驱动下,穿过并流带;另一股气流被废气风机抽吸向上,穿过介于两层烧嘴间的中部煅烧带。