光学表面疵病标准。
光学元件表面光洁度标准
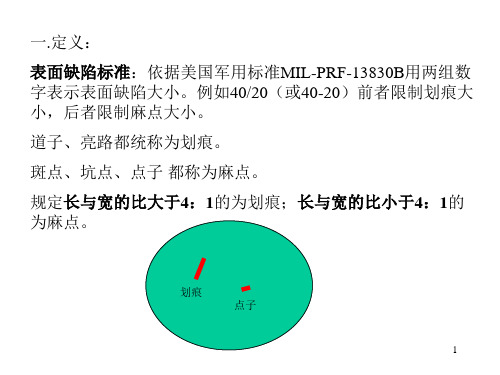
在如图(1)所示的区或有2条长1mm
[50×(2+21)./106]0+[#40划×(痕3+2长+2)度/10]为+[2(0×2(2++22))/10];+[140×0#10划/10痕]=6长6 度为(4+4+4+4)
2.60#划痕乘以划痕长度与元件直径之比为60×(2+2)/20;
40#划痕乘以划痕长度与元件直径之比为40×(4+4+4+4)/20
10#划痕长度2mm对于表面质量要求20-10该产品最大划痕长度1mm<1/5。
图中有20#划痕长1度/4mDm。为1/4×20=5mm
1.60#划痕长度为(2+2);
60#划痕长2mm
40#划痕长度为(最4+大4+4划+4)痕的长度和为:
最大划痕的长度和为:
对(于图长 片与是宽放比大的≥5不:2是1m的实m产际品+尺2不寸m能)m用=简4单m公m式计算等效直径
3.所有级数的划痕乘以划痕长度与元件直径之比所得乘积之和为:
[60×(2+2)/20]+[40×(4+4+4+4)/20=36
元件最大划痕级数为60;60的一半为60/2=30)36>30;因此,元件不合格。
6
如左图所示的产品
则20#划痕长度mm。10#划痕长度
规定长与宽的比大于4:1的为划痕;
2mm对于表面质量要求20-10该产
左图是大家看的编号2的样品(图 片是放大的不是实际尺寸)
图中的划痕为20#,且长度>1/4D。 对于表面质量要求20-10该产品不 合格。但本次样品未提出表面质量 要求,而是要大家自已决定光洁度 等级。因此该产品划痕可判为40#。
光学零件表面庇病标准解析(MIL-PRF-13830B)

划2划痕:以美国军用标准《MIL-PRF-13830B》的表面质量划痕样板作为各级数划痕的比对标准。
(注意:美国军用标准未指明划痕的标号,也即未确定划痕的宽度和深度,只能以实际观察到的划痕的大小为准。
) 划痕级数就是划痕的标号,标准样版有10#、20#、40#、60#、80# 5个级数。
划痕的宽度不易计量,一般划痕以标准样板作为各级数划痕的比对标准。
如果用显微镜放大后,是可以度量出大小的。
参照国标GB/T1185-2006,与美国军用标准比对,元件上划痕的庇病的实际宽度,单位为:1/1000mm。
如:判断为40#划痕,那么划痕的宽度为: 40*(1/1000mm)=0.04mm。
便于划痕大小的计算,特将一些术语以代号表示:最大划痕级数“J”,较小划痕级数“J1、J2、J n+1”;最大划痕长度“L”,较小划痕长度“L1、L2、L n+1 ”;等效直径“D0”。
2.1当元件上的划痕级数超过表面质量要求的划痕级数时,元件不合格。
例如:元件的表面质量要求为60—40,则代表元件的划痕必须≤60#,如果元件有>60#的划痕,则元件不合格。
左图中(图片是放大的不是实际尺寸),元件上的划痕为20#,且长度>1/4D 。
对于表面质量要求20-10该元件不合格。
但本次未提出表面质量要求,如果要判定光洁度等级,该元件上的划痕可判为40#。
2.2当元件上的划痕级数未超过表面质量要求的划痕级数,但元件上存在最大划痕时,所有最大划痕的长度之和应不超过元件直径的1/4。
公式表达:∑L ≤1/4 D 0例如:有一长30mm 宽10mm 的元件,元件的表面质量要求为60—40,有2条 60#,长为3 mm 划痕,它的等效直径为20mm ,1/4D 为1/4×20=5mm ,最大划痕的长度和为:3mm+3mm=6mm ,元 件上最大划痕的长度之和超过元件直径的1/4,所以元件不合格。
60#划痕长3mm60#划痕长3mm左图中(图片是放大的不是实际尺寸),直径5mm ,图中有20#划痕长度2.2mm ,10#划痕长度7mm ,对于表面质量要求20-10该产品不合格。
GB光洁度标准
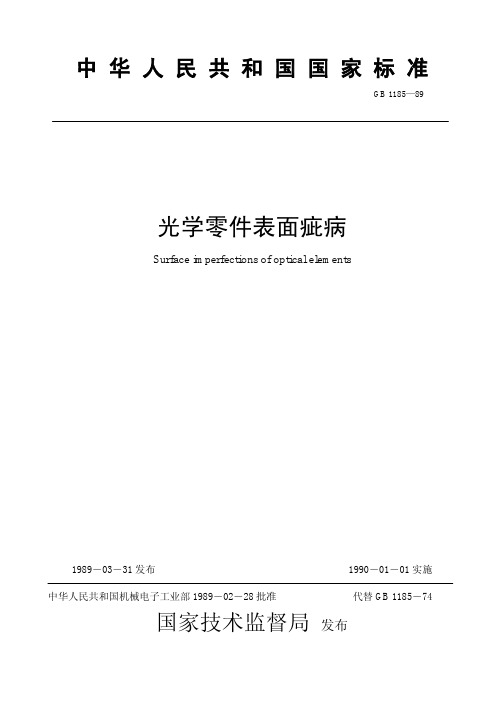
中华人民共和国国家标准GB 1185—89光学零件表面疵病Surface imperfections of optical elements1989-03-31发布1990-01-01实施中华人民共和国机械电子工业部1989-02-28批准代替GB 1185-74国家技术监督局发布1 主题内容与适用范围本标准规定了光学零件表面疵病术语、代号、换算、标志、密集和试验方法。
本标准适用于光学零件抛光表面的检验。
2 术语、代号2.1 表面疵病B表面疵病系指麻点、擦痕、开口气泡、破点及破边。
2.2 级数J级数J表征表面疵病大小,Sqrt(M)的值即为J。
其中,M为表面疵病的面积,mm2。
正方形表面疵病的级数J是以mm为单位的边长数值。
2.3 个数GG为允许的表面疵病数目。
3 换算换算系指较大级数的表面疵病允许用若干个具有较小级数的表面疵病来代替,其面积之和不超过原级数的表面疵病面积,但不允许将表面疵病换算为多于40个较小级数的表面疵病。
根据需要,表面疵病也可以不允许换算(见4.1.2条)。
表面疵病级数与疵病个数换算系数按表1。
表 1疵病个数 1 2.5 6.3 16 400.004 ----0.0063 0.004 ---0.01 0.0063 0.004 --0.016 0.01 0.0063 0.004 -0.025 0.016 0.01 0.0063 0.0040.04 0.025 0.016 0.01 0.00630.063 0.04 0.025 0.016 0.010.10 0.063 0.04 0.025 0.0160.16 0.10 0.063 0.04 0.025级数J0.25 0.16 0.10 0.063 0.040.40 0.25 0.16 0.10 0.0630.63 0.40 0.25 0.16 0.101.0 0.63 0.40 0.25 0.161.6 1.0 0.63 0.40 0.252.5 1.6 1.0 0.63 0.404.0 2.5 1.6 1.0 0.636.3 4.0 2.5 1.6 1.010 6.3 4.0 2.5 1.6注:①表面疵病原级数个数乘疵病个数换算系数等于换算后的级数个数(结果应化为整数)。
美军标关于表面疵病的说明

一.定义:表面缺陷标准:依据美国军用标准MIL-PRF-13830B用两组数字表示表面缺陷大小。
例如40/20(或40-20)前者限制划痕大小,后者限制麻点大小。
道子、亮路都统称为划痕。
斑点、坑点、点子都称为麻点。
规定长与宽的比大于4:1的为划痕;长与宽的比小于4:1的为麻点。
当元件的不同区域表面光洁度要求不一样时,等效直径的计算以区域进行:表面质量要求高的内区域其等效直径以内区域为准(如有效孔径的区域),表面质量要求低的外区域计算的是整体元件的等效直径。
§美军标规定对于非圆形元件其直径取相等面积圆的直径。
划痕:以美国军用标准《MIL-O-13830》的表面质量划痕样板作为各级数划痕的比对标准。
(注意:美军标未指明划痕的计量单位也即未确定划痕的宽度和深度,只能以实际观察样版为标准。
)这里的划痕级数就是通常的划痕号数,标准样版有10#、20#、40#、60#、80# 5个级。
§SC-QA027表面质量标准共有7条划痕判定标准,前5条是美军标的规定,后两条是公司内控标准。
以下逐条讲解:1.当元件的划痕级数超过表面质量要求的划痕级数时,元件不合格。
例如:元件的表面质量要求为60—40,则代表元件的划痕必须≤60#,如果元件有>60#的划痕,则元件不合格。
2.当元件的划痕级数未超过表面质量要求的级数,但元件存在最大划痕时,所有最大划痕的长度之和应不超过元件直径的1/4。
例如:有一长30mm宽10mm的元件,元件的表面质量要求为60—40,有2条60#长为3 mm划痕。
它的等效直径为20mm1/4D为1/4×20=5mm最大划痕的长度和为:3mm+3mm=6mm6mm>5mm元件最大划痕的长度和超过元件直径的1/4。
所以元件不合格。
3.当元件存在最大划痕,而最大划痕的长度之和未超过1/4D,要求所有级数的划痕乘以划痕长度与元件直径之比所得乘积之和,不得超过最大划痕级数的一半。
光学表面疵病标准

表5 0.02mm-3.0mm光学零件表面的疵病级数参考值
二、麻点
(3)美军标规定表面疵病的第二个数字(如80-50)表示麻点 的级数(计量单位为 1%mm),是该光学表面允许麻点的最 大直径。任何一个光学表面上,每 20mm 直径上,最多只允 许有一个最大尺寸的麻点,该 20mm 直径上所有麻点的直径 总和,不得超过最大尺寸麻点直径的一倍。而直径小于 0.0025mm 的麻点可不作统计。同时还规定,若图样上未规定 表面疵病的极限尺寸时,应按表 6 求算。
下面对各种情况的擦痕进行举例说明:
三、擦痕
当零件的擦痕级数超过表面疵病要求的擦痕级数时,零件不合格。 例1,零件的表面质量要求为60-40,则代表零件的擦痕宽度必须 ≤60μm,如果零件表面有宽度>60μm的擦痕,则该零件不合格。
当零件的擦痕级数未超过表面质量要求的级数,且只存在最大擦痕 时,所有最大擦痕的长度之和应不超过零件直径的1/4,即
表4 0.004mm-0.025mm光学零件表面的疵病级数参考值
二、麻点
俄国标准规定,对位于光学系统像平面及其像平 面附近的光学零件表面采用 0-10、0-20 或 0-40级 别的表面疵病还分别给出了不同通光孔径的表面 中心区和边缘区,某一级别表面疵病麻点的最大 直径和最大麻点的个数。使用这个标准,设计师 在图样上很好标注,检验人员也很容易计算。不 在光学系统像平面附近的光学零件表面采用Ⅰ、 Ⅱ、Ⅲ、Ⅳ、Ⅴ、Ⅵ、Ⅶ、Ⅷ、Ⅷ a、Ⅸ、Ⅸa等 11个级别的表面疵病(麻点直径从0.02mm至 3.0mm)见表 5。
表7 擦痕间的相关数据
三、擦痕
(2)俄国标准也在表 4 和表 5 中分别规定了不同 通光孔径的光学表面中,某一表面疵病级别允许 擦痕的最大直径和最大尺寸擦痕的长度。
光学 元件表面光洁度标准1(可编辑)

光学元件表面光洁度标准1(可编辑)* 一.定义: 表面缺陷标准:依据美国军用标准MIL-PRF-13830B用两组数字表示表面缺陷大小。
例如40/20(或40-20)前者限制划痕大小,后者限制麻点大小。
道子、亮路都统称为划痕。
斑点、坑点、点子都称为麻点。
规定长与宽的比大于4:1的为划痕;长与宽的比小于4:1的为麻点。
点子划痕当元件的不同区域表面光洁度要求不一样时,等效直径的计算以区域进行:表面质量要求高的内区域其等效直径以内区域为准(如有效孔径的区域),表面质量要求低的外区域计算的是整体元件的等效直径。
划痕点子 A区20-10 B区80-50 如左图元件表面质量要求不同,则在判定A区是否符合要求时,应取内圆直径进行计算。
而B区则取整个元件的圆直径三角的面积为(低×高)/2 a ×b /2 三角等效直径D 长方形面积长×宽 a ×b 长方形的等效直径D D 面积π D/2 2 a b 美军标规定对于非圆形元件其直径取相等面积圆的直径。
a h A区:20-10 B区:80-50 3mm 1mm 4mm 2mm 对于长方形元件(当长与宽的比 5:1时)可以用简单公式:等效直径 (长+宽)/2来计算。
如左图元件 A区等效直径为(1+3)/2 2mm B区等效直径为(2+4)/2 3mm 对于长与宽比?5:1的产品不能用简单公式计算等效直径划痕: 以美国军用标准《MIL-O-13830》的表面质量划痕样板作为各级数划痕的比对标准。
(注意:美军标未指明划痕的计量单位也即未确定划痕的宽度和深度,只能以实际观察样版为标准。
) 这里的划痕级数就是通常的划痕号数,标准样版有10#、20#、40#、60#、80# 5个级。
SC-QA027表面质量标准共有7条划痕判定标准,前5条是美军标的规定,后两条是公司内控标准。
以下逐条讲解: 1.当元件的划痕级数超过表面质量要求的划痕级数时,元件不合格。
光学外观标准
3 GB 1185-89
注:外观表面质量等级级数和标准ISO 10110中相同; 拆分方式与标准ISO 10110相同。
13/12
其他标准
4 各标准之间的转换
1.2 1.1 ,即80-50外观,口径20mm转化为ISO10110-7标准后为1*1.1。
注:以上面积计算中,麻点的几何形状为圆形,擦痕为长方形!
光学零件外观标准总结
1 ISO 10110外观标准解读
1.1 ISO 10110标准中外观要求示例:
2/12
1 ISO 10110外观标准解读
1.2 外观对比限度板
使用方法:1)室内光; 2)检验背景为黑色挡板;3)检验光源为24、27W日光灯;4)放置 在灯下反射观察;5)若检验镜片时有使用放大镜则观察限度板时也须使用放大镜; 6)限度板上的线条为该限度要求可允许的最大缺陷,超过此限度为不良.
如Ⅳ级外观,D。=20mm,总面积=0.06284*20=1.2568mm²,转换为ISO10110 为: 1*1.1。
若D。=20mm,回想美国军标中80-50转化为1*1.1,所以GBⅣ级外观对应美国军 标为80-50。
结束 谢谢!
此课件下载可自行编辑修改,此课件供参考! 部分内容来源于网络,如有侵权请与我联系删除!
8/12
3 MIL美国军标中外观解读
美国军标中对光学零件表面质量说明及可接受缺陷规定用"擦痕"、"麻点"说明。擦 痕和麻点用两个代表其限制尺寸的号数来标记,第一个代号是擦痕号,第二个代号是 麻点号。
擦痕指相对长的缺陷,一般长宽比在20:1左右,如:擦痕、划伤、划丝。 麻点指点状缺陷,一般为远的,如麻点、麻坑包含物。
光学零件表面疵病标准(德国DIN3140)
Din3140光洁度标准★1/1×0.041/表示对气泡的要求例:1/1×0.04 允许一个直径为0.04的气泡实际上气泡的面积为:1×0.042=0.0016mm2可以拆分成许多小气泡,但其总面积不变。
如:1/1×0.04等价于1/3×0.025或1/6×0.016,1/16×0.001 etc如果表示中带有括号,则不能分拆为多个小气泡。
★2/012/表示对条纹的要求2/01表示允许01级条纹条纹共分01~04级★3/3(1)0.53/表示对光圈的要求3/3(1)0.5表示光圈数为3,括号中数字表示在两个垂直方向中光圈数的差值,即一个方向光圈为3,垂直方向光圈为2局部误差(平滑的干涉条纹上的微小偏差)允许0.5个圈★4/3.2’4/表示对偏心的要求4/3.2’表示面倾角为3.2’,如换算成在球心处偏心量C:C=面倾角×球面半径/3438例:R=53.43 面倾角3.2’则C=3.2×53.43/3438=0.0497mm★5/1×0.063;K2×0.004;R0.15/表示对表面疵病的要求5/1×0.063;K2×0.004;R0.11×0.063表示允许一个尺寸为0.063mm的麻点,同气泡一样,也可以用麻点面积折算成许多的小麻点,如:1×0.063麻点面积为:1×0.0632=0.004mm2可以折算成如下:3×0.05;6×0.025;16×0.016;40×0.010也可折算成:1×0.04+4×0.025 只要保持麻点总面积不变同样,带有括号的,不能分拆成多个小麻点。
K2×0.004表示允许2条任意长度,宽度为0.004mm的划痕划痕也可用同等划痕面积来拆成许多小划痕,但总面积不变。
(美军标)光学零件表面疵病标准-MIL13830A(摘要)
光学零件表面疵病标准-擦痕、麻点说明(美国军用标准:MIL-O-13830A/11.Sep63)1.目的:光学零件表面质量说明及可接受缺陷(defects)规定,陆军用擦痕、麻点说明MIL-O-13830A 为了在实际检验中领会,执行此标准,特做以下文字规定。
1.1擦痕(scratch)和麻点(dig)用两个代表其限制尺寸的号数来标记。
第二个号为麻点号。
擦痕指相对较长的缺陷,一般长比宽在20:1左右,如:擦痕、划丝、划伤等。
麻点指点状缺陷,一般为圆的如麻点、麻坑包含物等。
1.2擦痕的判断可参考有关擦痕标准。
2.擦痕2.1擦痕号(第一个号)表示擦痕最大宽度。
2.1.1球面光学零件:擦痕的宽度等于最大宽度时其长度不能大于零件直径或有效孔径的25%。
每个零件不能多于两条擦痕。
2.1.2柱面光学零件在直径20mm的范围内。
擦痕宽度等于最大宽度时,擦痕长度不大于5mm可以允许。
允许擦痕的最多数目为该有效柱面上直径为20mm的区域的多少。
例如:πDH=柱面面积(有效面积)其中:D=柱面镜的过光长度(直径)H=柱面镜的过光长度(高度)π=3.1416有效柱面面积/0.25π20mm2=允许擦痕最大数2.1.3当存在最宽擦痕,如果较小宽度的擦痕符合下面公式,可以接受。
∑(N×(L/D)≤(Nmax)/2其中:D=直径,N=测量的擦痕数,L=擦痕长度,Nmax=规定的擦痕号光学零件中擦痕数乘以擦痕长度和零件直径之比的和不大于擦痕号(规定)的一般可以接受。
2.1.4 一个擦痕其宽度大于擦痕规定数的(0.0001英寸)0.00025mm,则不能接受。
2.1.5 当无最宽擦痕时,擦痕不能超过以下公式:光学零件中擦痕数乘以擦痕长度和零件直径之比的和不大于擦痕号,则可以接受。
2.1.6 小于10(0.01mm宽)可以忽略。
3. 麻点3.1 麻点号表示最大直径的麻点。
麻点号是以最大麻点的直径给出,单位为1/100mm(0.01mm一丝)。
光学零件表面庇病
划2划痕:以美国军用标准《MIL-PRF-13830B》的表面质量划痕样板作为各级数划痕的比对标准。
(注意:美国军用标准未指明划痕的标号,也即未确定划痕的宽度和深度,只能以实际观察到的划痕的大小为准。
) 划痕级数就是划痕的标号,标准样版有10#、20#、40#、60#、80# 5个级数。
划痕的宽度不易计量,一般划痕以标准样板作为各级数划痕的比对标准。
如果用显微镜放大后,是可以度量出大小的。
参照国标GB/T1185-2006,与美国军用标准比对,元件上划痕的庇病的实际宽度,单位为:1/1000mm。
如:判断为40#划痕,那么划痕的宽度为: 40*(1/1000mm)=0.04mm。
便于划痕大小的计算,特将一些术语以代号表示:最大划痕级数“J”,较小划痕级数“J1、J2、J n+1”;最大划痕长度“L”,较小划痕长度“L1、L2、L n+1 ”;等效直径“D0”。
2.1当元件上的划痕级数超过表面质量要求的划痕级数时,元件不合格。
例如:元件的表面质量要求为60—40,则代表元件的划痕必须≤60#,如果元件有>60#的划痕,则元件不合格。
左图中(图片是放大的不是实际尺寸),直径5mm ,图中有20#划痕长度2.2mm ,10#划痕长度7mm ,对于表面质量要求20-10该产品不合格。
对于表面质量要求40-20,则该产品所有的划痕级数分别乘以对应划痕长度之和与元件等效直径之比所得的乘积之和为:20×2.2/5+10×7/5=25+14=3939<40,元件符合40-20。
例:元件为 10mm,表面质量要求60—40,有2条长2mm 的50#划痕,1条长3mm 的40#划 痕,另2条长2mm 的40#划痕,2条长2mm 的20#划痕,10#划痕长度合计10mm。
所有的划 痕级数分别乘以对应划痕长度之和与元件等效直径之比所得的乘积之和为:[50×(2+2)/10]+[40×(3+2+2)/10]+[20×(2+2)/10]+[10×10/10]=66元件最大划痕为60#,66>60,因此,元件不合格。
- 1、下载文档前请自行甄别文档内容的完整性,平台不提供额外的编辑、内容补充、找答案等附加服务。
- 2、"仅部分预览"的文档,不可在线预览部分如存在完整性等问题,可反馈申请退款(可完整预览的文档不适用该条件!)。
- 3、如文档侵犯您的权益,请联系客服反馈,我们会尽快为您处理(人工客服工作时间:9:00-18:30)。
主要内容
麻点
斑点
表面疵 病擦痕源自破边名词解释麻点:光学零件表面呈现的微小的点状凹穴,包括开口 气泡、破点,以及细磨或精磨后残留的砂痕等。
斑点:光学零件表面经侵蚀或镀膜后形成的在 反射光中呈干涉色突变的局部腐蚀或覆盖。
定义
擦痕:光学零件表面呈现的微细的长 方形凹痕。
破边:光学零件有效孔径之 外边缘破损。不包括 可发展的裂纹。
含义:镀膜前的疵病公差是:基本级数为0.063mm,其许有个 数为3个 ;
镀膜层公差为C:基本级数为1.6mm,其许有个数为2个; 长擦痕公差为L:基本级数0.1mm(长擦痕的最大宽度),其许有个数为2
个; 破边公差为E:为1mm。
表1 GB/T1185-2006符号
一、表面疵病标注方法
(2)俄国国家标准 OCTlll41一65是在苏联光学工业部标准 HO1675一57的基础上进行修订后,于1965年升为国家标准的。 俄国标准规定表面疵病的代号为р, 其值由阿拉伯数字或罗马 数字(0-10、0-20、0-40、Ⅰ、Ⅱ、Ⅲ、Ⅳ、Ⅴ、Ⅵ等)表示 。如:一般分划板的刻字面可选 0-20 级,一般物镜可选Ⅴ级 。
表面疵病级数与疵病个数换算系数见表 2。
表 2 表面疵病级数与疵病个数换算系数
表3 个数换算值系列
二、麻点
基本级数0.25mm换算成较小的级数
图1 换算示意图
二、麻点
(2)俄国标准规定,位于光学系统像平面及其像平 面附近的光学零件表面采用 0-10、0-20或 0-40 级 别的表面疵病(麻点直径从 0.004mm至 0.025mm )(见表 4),小于 0.002mm 的麻点不作考核。
表面疵病对光学产品的危害
1、离开成象面较远的光学零件表面疵病,会挡去一部分有用的 成象光线,并产生杂散光而降低象面衬度,其影响程度用疵病 面积与光束孔径之比,即挡光比来描述,也可用产生的杂散光 量来描述。
2、位于成象面及其附近的零件,由于此处光束孔径极小,稍有 疵病就会产生较大的挡光比,以致在视场内直接看到疵病轮廓 或阴影。其影响程度一般用疵病的大小及数量来描述。
表4 0.004mm-0.025mm光学零件表面的疵病级数参考值
二、麻点
俄国标准规定,对位于光学系统像平面及其像平 面附近的光学零件表面采用 0-10、0-20 或 0-40级 别的表面疵病还分别给出了不同通光孔径的表面 中心区和边缘区,某一级别表面疵病麻点的最大 直径和最大麻点的个数。使用这个标准,设计师 在图样上很好标注,检验人员也很容易计算。不 在光学系统像平面附近的光学零件表面采用Ⅰ、 Ⅱ、Ⅲ、Ⅳ、Ⅴ、Ⅵ、Ⅶ、Ⅷ、Ⅷ a、Ⅸ、Ⅸa等 11个级别的表面疵病(麻点直径从0.02mm至 3.0mm)见表 5。
表 6 中的光束直径是指进入观察者眼睛的轴向光束在所研究的 光学表面上的直径。如是出瞳直径大于3.5mm ,则进入人眼 的光束直径取3.5mm,若出瞳直径小于 3.5mm,则进入人眼 的光束直径应与出瞳直径相同,可见美军标规定表面疵病的 标注方法也很方便,只要设计师选好(也可以参考表 6)该表 面疵病的级数(最大尺寸的麻点直径)标注在图样上就可以 了。设计人员比较容易标注,检验人员也很容易计算。
表5 0.02mm-3.0mm光学零件表面的疵病级数参考值
二、麻点
(3)美军标规定表面疵病的第二个数字(如80-50)表示麻点 的级数(计量单位为 1%mm),是该光学表面允许麻点的最 大直径。任何一个光学表面上,每 20mm 直径上,最多只允 许有一个最大尺寸的麻点,该 20mm 直径上所有麻点的直径 总和,不得超过最大尺寸麻点直径的一倍。而直径小于 0.0025mm 的麻点可不作统计。同时还规定,若图样上未规定 表面疵病的极限尺寸时,应按表 6 求算。
3、仪器的外露光学表面及一眼就能看到的零件,需要从仪器本 身“美观”的角度加以考虑,通常控制其疵病的大小。
各国标准的比较
一、表面疵病标注方法
(1)ISO 10110-7系列标准中公差项目的代号采用数字码,表面疵病的 代号为“5”; 我国标准规定表面疵病的代号为B,其值由 G x J表示(G 为个数,J为 级数表示表面疵病的大小且以㎜为单位的数值分级,级数值为疵病面 积的平方根),如:一般物镜可选项 3 x 0.4。 示例:面积法疵病公差组(包括一般疵病公差、特定要求时的镀膜 层疵病公差、长擦痕疵病公差、破边疵病公差): B/ 3X0.063;C2X1.6;L2X0.1;E1
(3)美国军用标准MIL一0一13830A中规定,表面疵病的标注形 式为: A一B或A/B 美军标规定表面疵病的极限尺寸应用两个数字表示(如80-50 ),第一个数字表示擦痕的等级(单位为μm),第二个数字 表示麻点的等级(单位为 1/100mm)。如:一般物镜可选 60-40。
一、表面疵病标注方法
标准规定较小的疵病S可有较F多的数量,只要其疵病面积总
和相等或不超过规定疵病的面积,但不允许疵病向尺寸增 大的方向换算。 2、5/〔A x S〕 当在标注中有方括号时,表示为不允许按面积换算,其符 号A及S的意义与前同。
二、麻点
(1)我国标准规定表面疵病大小以毫米为单位,级数值是 该级表面疵病大小的最大值,一般疵病的级数为疵病面积 的平方根。一般疵病级数对应出圆麻点的直径,长圆形麻 点以最大轴线长度和最小轴线长度的算术平均值折算成麻 点的直径,不规则麻点以最大长度和最大宽度的算术平均 值近似为面积的平方根。开口气泡和破点均当作麻点处理 。级数小于 0.004 的表面疵病(麻点)不作考核。表面疵 病级数公比数为 1.6,疵病个数换算系数公比数为 2.5。表 面疵病原级数个数乘换算系数等于换算后的级数个数(结 果应化为整数),但不允许将表面疵病换算成多于40个较 小级数的表面疵病。换算表中给出了从 0.004mm 到 10mm 18 个表面疵病级,零件图上需给的表面疵病由设计师按此 表中的数选取。
(4)英国BS4301:1968规定表面疵病的标注 形式为:5/A x B x C
5—表面疵病的允许程度记号; A—允许疵病数量; B—检验条件等级; C—检验疵病用放大镜的倍数; A、B、C之间用“x”号隔开。
一、表面疵病标注方法
(5)西德DIN3140一7规定表面疵病的标注形式有以下几种: 1、 5/A x S 5—表面疵病允许程度记号; A—允许疵病数量; S—疵病的尺寸等级(最大尺寸)。 当疵病的面积为F时,S值规定由下式计算: