多头蜗杆的车削方法
浅谈多线蜗杆的车削方法
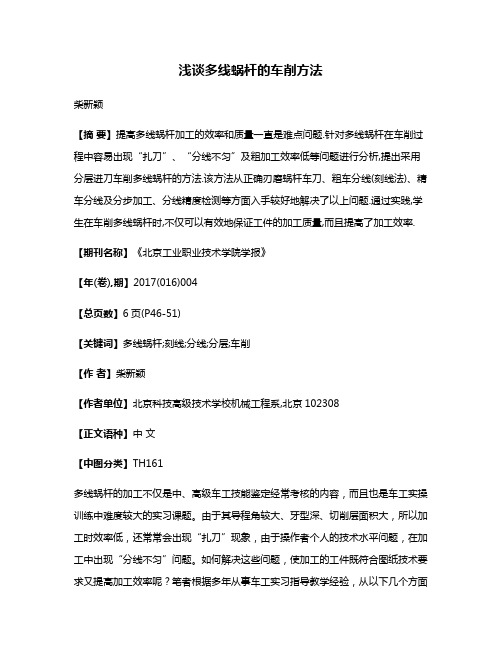
浅谈多线蜗杆的车削方法柴新颖【摘要】提高多线蜗杆加工的效率和质量一直是难点问题.针对多线蜗杆在车削过程中容易出现“扎刀”、“分线不匀”及粗加工效率低等问题进行分析,提出采用分层进刀车削多线蜗杆的方法.该方法从正确刃磨蜗杆车刀、粗车分线(刻线法)、精车分线及分步加工、分线精度检测等方面入手较好地解决了以上问题.通过实践,学生在车削多线蜗杆时,不仅可以有效地保证工件的加工质量,而且提高了加工效率.【期刊名称】《北京工业职业技术学院学报》【年(卷),期】2017(016)004【总页数】6页(P46-51)【关键词】多线蜗杆;刻线;分线;分层;车削【作者】柴新颖【作者单位】北京科技高级技术学校机械工程系,北京102308【正文语种】中文【中图分类】TH161多线蜗杆的加工不仅是中、高级车工技能鉴定经常考核的内容,而且也是车工实操训练中难度较大的实习课题。
由于其导程角较大、牙型深、切削层面积大,所以加工时效率低,还常常会出现“扎刀”现象,由于操作者个人的技术水平问题,在加工中出现“分线不匀”问题。
如何解决这些问题,使加工的工件既符合图纸技术要求又提高加工效率呢?笔者根据多年从事车工实习指导教学经验,从以下几个方面入手:正确刃磨车刀、采用分层法粗车、精车分线及步骤和正确的检测,较好地解决了车削中“扎刀”的问题,也提高了加工效率和分线精度。
车削蜗杆的方法主要有左右切削、切槽、分层切削3种方法[1]。
1.1 左右切削法在车削中为防止3个切削刃同时参加切削而引起扎刀,利用左右进给的进刀方式逐渐车至槽底的方法,称为左右车削法。
采用左右车削法车削时,背吃刀量不能太大,尤其是向右侧赶刀时,存在切削阻力大,排屑不顺畅,易产生“扎刀”现象,并且效率低。
1.2 切槽法切槽法是先用矩形螺纹车刀将螺旋直槽车至蜗杆齿根处,然后再粗车刀粗车成形的方法,称为直槽法。
利用直槽法车削比左右切削法效率提高了,但是学生需要刃磨切槽刀、蜗杆粗、精车刀,由于切槽刀的角度及刃磨是一大难点,不易掌握,当模数较大时,刀头太长,刀具强度低,易产生刀头折断现象。
矿产
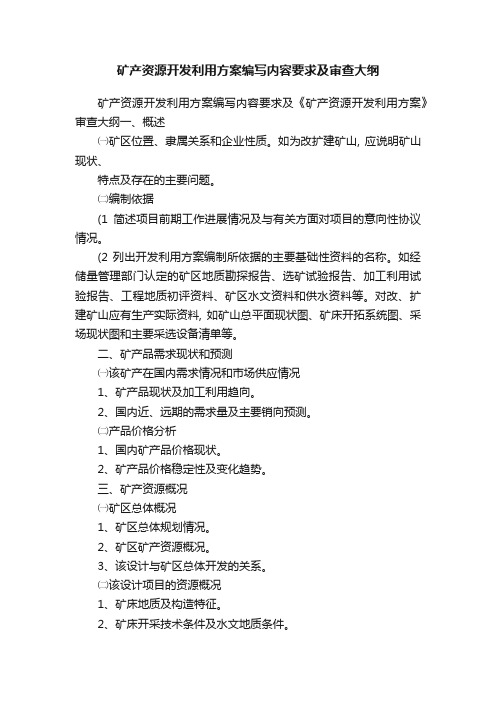
矿产资源开发利用方案编写内容要求及审查大纲
矿产资源开发利用方案编写内容要求及《矿产资源开发利用方案》审查大纲一、概述
㈠矿区位置、隶属关系和企业性质。
如为改扩建矿山, 应说明矿山现状、
特点及存在的主要问题。
㈡编制依据
(1简述项目前期工作进展情况及与有关方面对项目的意向性协议情况。
(2 列出开发利用方案编制所依据的主要基础性资料的名称。
如经储量管理部门认定的矿区地质勘探报告、选矿试验报告、加工利用试验报告、工程地质初评资料、矿区水文资料和供水资料等。
对改、扩建矿山应有生产实际资料, 如矿山总平面现状图、矿床开拓系统图、采场现状图和主要采选设备清单等。
二、矿产品需求现状和预测
㈠该矿产在国内需求情况和市场供应情况
1、矿产品现状及加工利用趋向。
2、国内近、远期的需求量及主要销向预测。
㈡产品价格分析
1、国内矿产品价格现状。
2、矿产品价格稳定性及变化趋势。
三、矿产资源概况
㈠矿区总体概况
1、矿区总体规划情况。
2、矿区矿产资源概况。
3、该设计与矿区总体开发的关系。
㈡该设计项目的资源概况
1、矿床地质及构造特征。
2、矿床开采技术条件及水文地质条件。
高精度多头蜗杆的车削方法
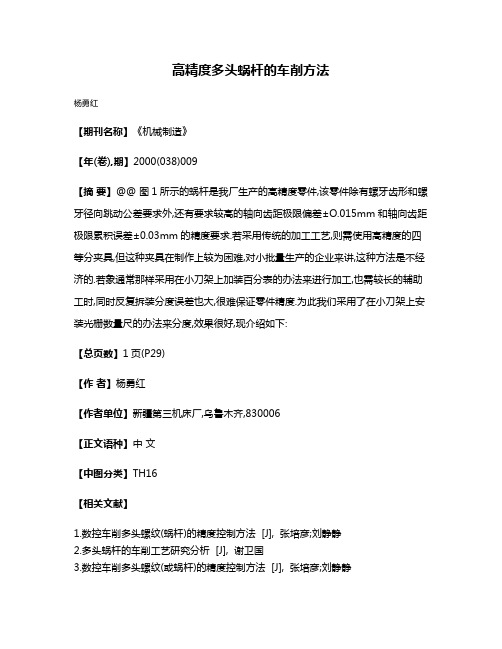
高精度多头蜗杆的车削方法
杨勇红
【期刊名称】《机械制造》
【年(卷),期】2000(038)009
【摘要】@@ 图1所示的蜗杆是我厂生产的高精度零件,该零件除有螺牙齿形和螺牙径向跳动公差要求外,还有要求较高的轴向齿距极限偏差±O.015mm和轴向齿距极限累积误差±0.03mm的精度要求.若采用传统的加工工艺,则需使用高精度的四等分夹具,但这种夹具在制作上较为困难,对小批量生产的企业来讲,这种方法是不经济的.若象通常那样采用在小刀架上加装百分表的办法来进行加工,也需较长的辅助工时,同时反复拆装分度误差也大,很难保证零件精度.为此我们采用了在小刀架上安装光栅数量尺的办法来分度,效果很好,现介绍如下:
【总页数】1页(P29)
【作者】杨勇红
【作者单位】新疆第三机床厂,乌鲁木齐,830006
【正文语种】中文
【中图分类】TH16
【相关文献】
1.数控车削多头螺纹(蜗杆)的精度控制方法 [J], 张培彦;刘静静
2.多头蜗杆的车削工艺研究分析 [J], 谢卫国
3.数控车削多头螺纹(或蜗杆)的精度控制方法 [J], 张培彦;刘静静
4.多头蜗杆的车削 [J], 张燕平
5.在多线螺纹和多头蜗杆车削教学中应注意的两个问题 [J], 李小强;王宏斌
因版权原因,仅展示原文概要,查看原文内容请购买。
单件生产中多头蜗杆的车削论文:单件生产中多头蜗杆的车削
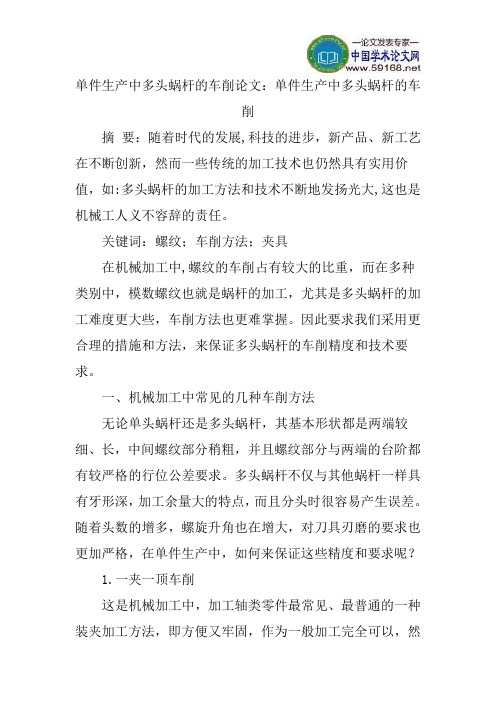
单件生产中多头蜗杆的车削论文:单件生产中多头蜗杆的车削摘要:随着时代的发展,科技的进步,新产品、新工艺在不断创新,然而一些传统的加工技术也仍然具有实用价值,如:多头蜗杆的加工方法和技术不断地发扬光大,这也是机械工人义不容辞的责任。
关键词:螺纹;车削方法;夹具在机械加工中,螺纹的车削占有较大的比重,而在多种类别中,模数螺纹也就是蜗杆的加工,尤其是多头蜗杆的加工难度更大些,车削方法也更难掌握。
因此要求我们采用更合理的措施和方法,来保证多头蜗杆的车削精度和技术要求。
一、机械加工中常见的几种车削方法无论单头蜗杆还是多头蜗杆,其基本形状都是两端较细、长,中间螺纹部分稍粗,并且螺纹部分与两端的台阶都有较严格的行位公差要求。
多头蜗杆不仅与其他蜗杆一样具有牙形深,加工余量大的特点,而且分头时很容易产生误差。
随着头数的增多,螺旋升角也在增大,对刀具刃磨的要求也更加严格,在单件生产中,如何来保证这些精度和要求呢?1.一夹一顶车削这是机械加工中,加工轴类零件最常见、最普通的一种装夹加工方法,即方便又牢固,作为一般加工完全可以,然而加工精度较高的工件时,要采用这种方法,必须用四爪盘找正,(以保证工件的精度)。
装卡要牢固,有的操作者怕夹伤工件,就用垫铜皮的方法加以预防,由于加工螺纹时,螺旋升角,对车削的阻力也大,所以装卡一定要牢固,牢固了就会卡伤工件(尽管垫铜皮了)夹的不牢固工件会产生旋转,也会产生位移,怎样才能既保证精度又不使工件夹伤呢?2.两顶尖车削这种加工方法是一种较方便的能保证工件有良好同轴度的加工方法,它是采用两顶尖支承工件,因此不会夹伤工件的现象发生。
可是它的强度呢?在一次技能竞赛中,加工的就是一个蜗杆,有位师傅就是采用两顶尖的方法进行车削,其结果是撅了一次,又一次,最终把工件撅废了,也没能完成以上两种车削方法虽然都可行。
但一个容易夹伤工件,一个容易撅废工件,人什么方法使其即装夹牢固又不夹伤工件,即保证精度而又不撅活呢?二、夹具的合理使用我这里所说的夹具,并不是制造特别复杂的那种,它只是一个带有开口的夹套。
三头蜗杆车削技术
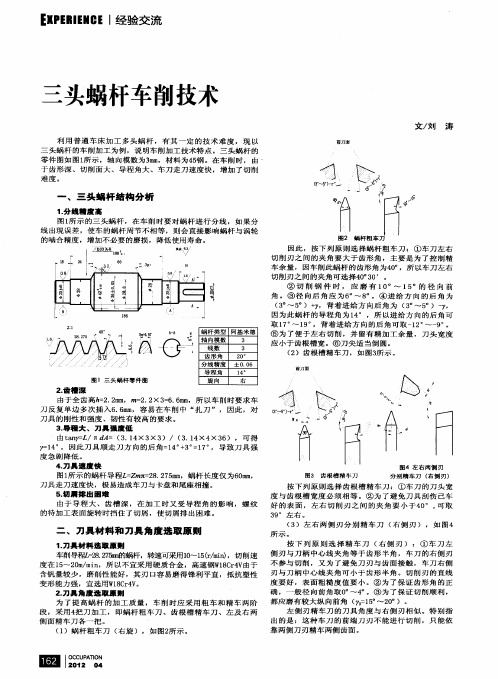
涛
前刀面
/1 r\ \
oo 吲
L ̄ 、
却
、
三 头 蜗 杆 结 构 分 析
G
。
1分线 精 度 高 . 图 l 示 的三 头 蜗 杆 ,在 车 削 时 要对 蜗 杆 进 行 分 线 ,如 果分 所 线 出现 误 差 ,使 车 的蜗杆 周 节 不相 等 ,则 会直 接 影 响蜗 杆 与 涡轮 的 啮合 精度 ,增 加不 必要 的磨损 ,降 低使 用 寿命 。
2. 槽 深 齿 由于全 齿 高 h 2 2l,m= . = . II Il I 2 2×3 6 6 ,所 以车 削 时要 求 车 =.咖 刀反复单边多次插入66皿 . m ,容 易在 车 削 中 “扎 刀 ” , 因此 ,对 刀 具 的 刚性 和 强 度 、韧 性 有较 高 的要 求 。 3. 程大 、刀 具 强度 低 导 由t n = a T L/Ⅱd A= ( . 4×3 31 X3)/ ( . 4×4×3 31 6) ,可 得 y 4 =1 。。 因此 刀 具 顺 走 刀 方 向的 后角 =1 + 。 1 ,导 致 刀 具 强 4。 3 = 7。 度 急 剧 降低 。 4 刀具 速 度 快 . 图1 所示 的蜗 杆 导程 Z = 8 2 5 m = mu 2 . 7 m ,蜗杆 长 度 仅 为6 r , 0 m a 刀 具走 刀 速度 快 ,极 易造 成车 刀 与卡 盘和 尾 座 相撞 。 5 切■ 排 出 困难 . 由于 导 程 大 、 齿 槽 深 ,在 加 工 时 又 受 导 程 角 的 影 响 , 螺 纹 的待加 工 表 面 旋转 时 挡 住 了切 屑 ,使 切 屑 排 出 困难 。
E P RE O 经验交流 X E IN EI
果 表 的指 针 都 处 于 同 一 位 置 ,说 明 刀 的 角度 已 装 好 。用 此 种 方法 对 刀 ,要 求 在磨 刀 时 采用 的样 板 如 图6 所示 。 在 车 蜗 杆 的 过 程 中采 用 的 切 削 液 是 用 纯 碱 与 皂 粉 的 比 此样 板 要 求B 与C 平 行 ,A 与B 、c 面 面 面 面 面垂 直 。 为 3: 约 1 5 g 1( . k )加 水 3 k 混合 稀 释 而 成 ,该 切 削 液 主要 0g ③ 分 线 方 法 。笔 者 采 用 的 是轴 向 分 线 法 , 先 调 整 好 小 特 点是 可 以 使 切 屑 顺 利 排 出 ,拖 板 与机 床 导 轨 平 行 度 后 ,利 用 小滑 板 刻度 确 定 直 线 移 动 洁 ,切 削 时没 有 油 烟 影 响等 优 点 。 分 线 , 在 车 好 一 条 螺 旋 槽 后 , 利用 小 滑 板 刻 度 配 合 百 分 表 使 车 刀 移 动 一 个 螺 距 ,再 车 相 邻 的 另 一 条 螺 旋 槽 ,从 而 达 四 、三 头 蜗 杆 实 际 - 过 程 r 到分 线 的 目的 。 ④ 车 削 方 法 。采 用 开 倒 、 顺 车 方 法 切 削 。并 使 蜗 杆 的 三 头蜗 杆 的轴 向模 数 为m 3 n = n ,齿 形角 为2 o  ̄ o ,螺旋 线 方 向 为右 旋 , 导程 角 为 1 4。,工 件 材料 为 4 钢 ,毛 坯 为热 轧 圆 粗 车 刀 在 刚 车 好 的槽 的 范 围 内 进 行 左 右 切 削 。车 好 第 一 螺 5 旋 槽 以后 ,再 车 第 二 条 、第 三 条 、 螺 旋 槽 , 由于 刚 才 切 槽 钢 ,尺寸为  ̄5 X 10 m 0 9 m o在机 械加 工前 ,安排调 质处理 T 3 。 2 5 刀 宽 度 已经 控 制 蜗 杆 槽 粗 车 的 宽 度 , 所 以能 控 制 好 每 单 边 工 序 安排 应 将 粗 车 、精 车 分 开 , 工件 装 夹 要 牢 固 。 都 留0 2Ⅱ的精 车 余 量 ,如 图 7 示 。 .Ⅱ n 所 1粗 车各 外 圜 . ( ) 用 三 爪 自定 心 卡 盘 装 夹 毛 坯 外 圆 , 伸 长 约 1 1 O m,车 平 端 面 ,粗 车 蜗 杆 外 圆 (4 lm / 4× 1 6 m 2 m 的 外 ' 0m 。 8m 圆至 3 ×4 . m 。 2 的外 圆至 2 × 1 . m 。 O 1 5 m 5 7 7 5 m ( 2)掉 头 夹 工 件  ̄4 4的外 圆 , 校 正 后 夹 紧悬 伸 长 度 约 图7倒 、顺车削方法 7 m ,车 端 面 ,保 证 总 长 1 7u。 0m 8 nn ( 3)粗 车 (2 的外 圆至 2 /0 ' 2×2 . m , 粗 车 2 的外 圆 95m 5 5 精 车蜗 杆 . 至 2 7×2 . m 。 车 2 的 外 圆 至 3 1 5m 8 0×2 m 3 m。 ( )用 两 顶 尖 装 夹 。先 精 车 蜗 杆 外 圆 至  ̄4 m ,表 面 1 2m 2 热 处理 。调 质T 3 略 ) . 2 5( 粗 糙度 3 2Jl 去 除蜗 杆 表面 和 两 端 毛刺 。 . I ll , 3. 精 车外 圜 半 ( )采 用 图4 示 左 、右 两侧 刃精 车 刀 。用 百分 表 校 正 2 所 ( )用 三 爪 自定 心 卡 盘 装 夹 4 外 圆 并校 正 。车 两 端 左 侧 ( 1 4 背走 刀 方 向 )精 车 刀 并 对 刀 ,低 速 精 车 第 一 条 螺 旋 面 钻 中 心孔 ( 3 6 。 中 心孔 表 面 粗 糙 度 值 要 小 且 圆整 。 A/) 槽 右 侧 面至 车 刀 主 刀 刃 与 齿 根 圆相 触 及 ,表 面 粗糙 度 达 规 保 证 总 长达 尺寸 要 求 。 定 要 求 ,记 录 中滑 板 进 刀 刻 度 值 为O 若 表 面粗 糙 度 不 够 理 ( )采 用 一 夹 一 顶 的装 夹 方 式 , 半精 车 外 圆 。① 车左 想 则 可 使 用 小 拖 板 赶 刀 、修 光 ,但 须 保 证 齿 厚 单 边 余 量 不 2 端 台阶 。外 圆各 留精车 余 量 l ,长 度至 尺 寸要 求 。② 工 件调 得 小 于 0 1 m m .m。 头 ,车右 端 台阶 。外 圆各 留精车余 量 l ,长 度至尺 寸要 求 。 m 然 后 以百 分 表 和 小 拖 板 刻 度 配 合 作 轴 向分 线 ,使 小 4 半精 车 蜗杆 外圆 。粗 车蜗 杆 . 拖 板 移 动 一 个 齿 距 ,用 直 进 法 精 车第 二 条 螺 旋 槽 同方 向侧 ( )调 整车 床 。准 备 刀具 。 1 面 , 直 至 到 记 录 中拖 板 进 刀 刻 度 处 , 表 面 粗 糙 度 达 要 求 。 ( )按模数 ×头数 ( x3 2 3 )。调整 车床挂轮和各手柄位 置。 用 同样 方 法 车好 第 三 条螺 旋 槽 。 ( ) 采 用 一 夹 一 顶 装 夹 方 式 。夹 右 端 2 m 外 圆使 台 3 Om 精 车牙 面 的加工 顺序 : 1 牙侧 a 一2 槽 面 槽牙 侧c 面一 3 槽牙 阶 紧 贴 卡 爪 。百 分 表 校 正 蜗 杆 外 圆 调 动 量 控 制 在 0 0 m . 2 m以 侧e 一3 面 槽牙侧 f 面一2 牙侧d 一 1 槽 面 槽牙侧 b ,如 图8 示 。 面 所 内并夹 紧 。顶尖 顶 一 端 。 半精 车 蜗 杆 外 圆至 4 . m 及 两 端 2 5m 倒 角2 。 。 O ( )粗 车 蜗杆 。蜗 杆 有关 参 数 值 见表 1 4 。
ZA型多线蜗杆的车削加工方法

总第215期2021年第3期机械管理幵发MECHANICAL MANAGEMENT AND DEVELOPMENTTotal 215No.3,2021机械分析与设计D01:10.16525/l4-1134/th.2021.03.029Z A型多线蜗杆的车削加工方法殷勇(中钢集团西安重机有限公司,陕西西安710201 )摘要:以某公司生产过的Z A 型三线蜗杆为例,详细分析其在普通车床上的车削加工技术。
结合生产实践,分 析零件参数、加工设备和刀具、加工步骤,得出“在普通车床上加工Z A 型三线蜗杆的方法,不仅可使制造和刃 磨方便、成本低,适用于单件小批量制造,而且能够完成粗精加工,省去繁锁的精磨工序,效率较高,满足一般 加工精度和使用要求”的结论。
关键词:Z A 型多线蜗杆车削加工中图分类号:TG 511文献标识码:A文章编号:1003-773X (2021 )03-0068-03引言蜗杆传动具有突出的特点,传动比大、结构尺寸紧凑、工作可靠性高、寿命长、冲击小、无噪声,轴向 力大、易发热、效率低。
所以蜗杆传动通常用来传递 两个交错轴之间的运动和动力。
本文就以常见的ZA 型多线蜗杆为例,对其车 削加工技术进行研究。
1蜗杆传动概况蜗杆传动由蜗杆和蜗轮组成(见图1),用于传 递交错轴之间的运动和动力,一般两轴交错角为 90° ,且以蜗杆为主动件,具有如下特点[1_3]:1) 传动比大,传动准确。
设蜗杆头数为2|,蜗轮 齿数为则蜗杆传动的传动比i =泌1Q 2) 传动平稳、无噪声。
蜗轮副的啮合是连续的, 且啮合齿对多。
3) 如果蜗杆的螺旋升角小于啮合面的当量摩擦 角时,能够实现自锁。
4) 传动效率低。
通常传动效率为〇.5~0.92,自锁 蜗轮副的传动效率为0.4 ~ 0.45。
5) 蜗轮副易发热磨损。
蜗轮副是滑动摩擦传动, 运行中会产生较大的热量,故蜗轮的制造材料常为 青铜等有色金属。
图1蜗杆传动收稿日期:2021-01-23作者简介:殷勇(1962—),男,上海人,毕业于陕西广播电视大 学机械设计与制造专业,专科,工程师,长期从事技术和质量 管理、知识产权管理及冶金机械装备加工工艺研究工作。
「双头ZA蜗杆的车削及检测分析」
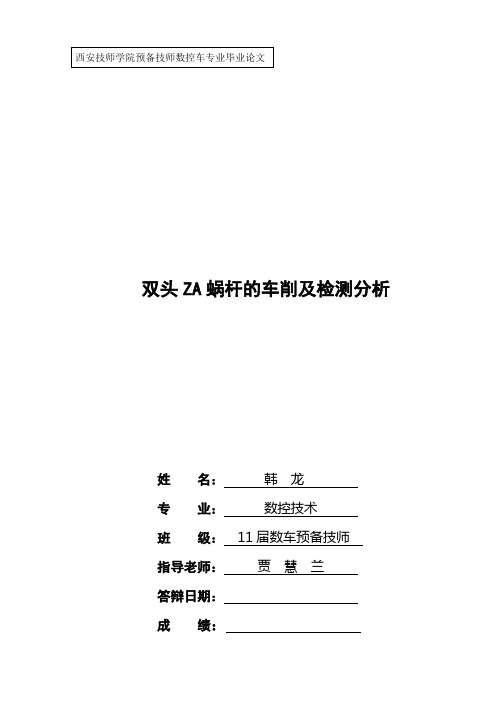
双头ZA蜗杆的车削及检测分析姓名:韩龙专业:数控技术班级:11届数车预备技师指导老师:贾慧兰答辩日期:成绩:目录引言 (2)一、双头阿基米德(ZA)蜗杆的图纸分析 (3)(一)蜗杆的基本要素及尺寸计算 (4)(二)ZA蜗杆的车削难点分析 (5)二、双头阿基米德(ZA)蜗杆的车削加工 (5)(一)装夹方式的选择 (6)(二)刀具几何参数、结构及装刀方法选用 (7)(三)图1-1双头ZA蜗杆车削方法的应用与具体的车削步骤 (8)(四)切削用量的选择 (8)(五)车削加工中应注意的问题 (8)三、双头ZA蜗杆的检测及质量分析 (8)(一)蜗杆质量表面、尺寸、形状精度的检测 (9)(二)蜗杆的质量分析 (10)四、结束语 (11)五、致谢词 (12)参考文献 (13)摘要本文通过对双头阿基米德(ZA)蜗杆的加工难点的分析、制定出其车削工艺、精度的检测方法、质量分析等相关内容的介绍,使我们对在普通卧式车床车削蜗杆的工艺有了较为深刻的认识和理解。
有助于日后加工中加工经验的积累和参考应用。
关键词:双头蜗杆加工质量分析检测引言蜗杆、蜗轮组成的蜗杆副,常用于减速传动机构中,以传递两轴在空间成90°交错的运动,蜗杆的齿形角(α)是在通过蜗杆轴线的平面内,轴线垂直面与齿侧之间的夹角。
蜗杆一般可分为米制蜗杆(α=20°)和英制蜗杆(α=14.5°)两种。
我国常用的米制蜗杆。
按齿形分又可分为轴向直廓蜗和法向直廓蜗杆。
通常轴向直廓蜗杆应用较多,即阿基米德蜗杆。
蜗杆的力学性能要求及选材:1.足够的强度;2.良好的减摩、耐磨性;3.良好的抗胶合性;40、45,调质HBS220~300——低速,不太重要、40、45、40Cr,表面淬火,HRC45~55——一般传动;15Cr、20Cr、12CrNiA、18CrMnT1O20CrK渗碳淬火、HRC58~63——高速重载;本文主要介绍双头阿基米德(ZA)蜗杆的车削与检测技术,蜗杆结构部分待加工,如图1-1所示。
多线螺纹和多头蜗杆的车削及检测
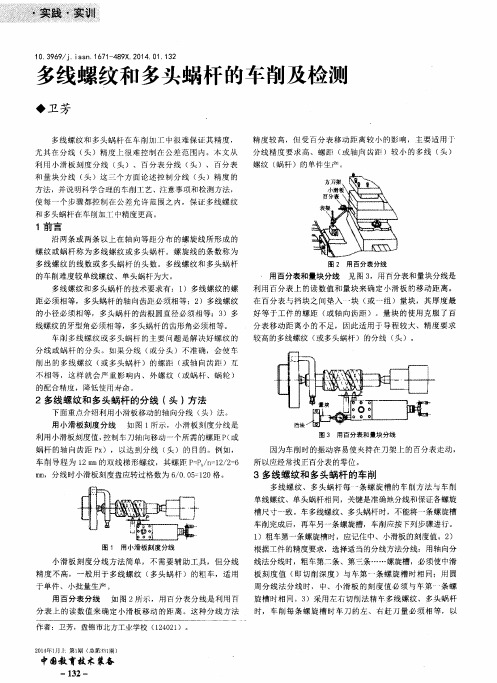
图 2 用 百 分 表分 线
用百分表和量块分线
见图 3 ,用百分表和量块分线是
利用 百分表上 的读数值 和量 块来确 定小滑板 的移动 距离 。
在 百分表与挡 块之 间垫入 ‘ 块 ( 或… ‘ 组 )量 块,其厚 度最 好等 于工件 的螺距 ( 或 轴 向齿距 )。量 块的使用 克服 了百 分表移 动距离 小 的不足,因此 适用于 导程较 大、精度 要求 较高的多线螺纹 ( 或多头蜗杆 )的分线 ( 头 )。
线螺纹的牙型角必须相等,多头蜗杆 的齿形角必须相等 。
车 削多线螺 纹或 多头蜗杆 的主要 问题是解 决好螺 纹的 分线 或蜗杆 的分 头。如果 分线 ( 或分 头 )不准 确,会使 车 削 出的 多线 螺纹 ( 或 多头蜗 杆 )的螺 距 ( 或轴 向齿距 )互 不相 等 ,这样 就会 严重影 响 内、外 螺纹 ( 或 蜗杆 、蜗轮 ) 的配合精度 ,降低使用寿命 。
中径相等 。
办 c 口 d
使两 条螺旋槽 的
图 5. 多线梯形螺纹螺距和多头蜗杆齿距的检测
杆一 头螺旋槽 分度 圆位置 处 )的表 b佰 ,同时确定 刀架位 置处表 a值及小滑板位置处表 C值。 2 )移动 中滑板将 表 b从螺旋槽 中退 出,小滑板轴 向移
1 )粗车第ห้องสมุดไป่ตู้条螺旋槽 时,应记住中、小滑板的刻度值 。2 )
图 1 用小滑板刻度分线
根据工件 的精度要求 ,选择适 当的分线方法分线 :用轴向分 线 法分线时 ,粗 车第■条、第 i条 ……螺旋槽 ,必须使中滑 板刻度 值 ( 即切 削深度 )与车第 一条 螺旋槽 时相 同;用 圆
周分线 法分线 时, 中、 小滑 板 的刻 度值 必须 与车第一’ 条螺 旋槽时相 同。3 )采用左右切 削法精午多线螺纹 、多头蜗杆 时,车 削每条 螺旋槽 时车 刀的左、 有赶 刀量 必须相 等 ,以
- 1、下载文档前请自行甄别文档内容的完整性,平台不提供额外的编辑、内容补充、找答案等附加服务。
- 2、"仅部分预览"的文档,不可在线预览部分如存在完整性等问题,可反馈申请退款(可完整预览的文档不适用该条件!)。
- 3、如文档侵犯您的权益,请联系客服反馈,我们会尽快为您处理(人工客服工作时间:9:00-18:30)。
0.8。
② 三爪卡盘夹持90.05mm处,活顶尖 后支持,车削M14 1.25至00.5 15 mm。
③ 调头夹持M14 1.25处,活顶尖后支持, 车各外圆,均留余量0.50.1mm。
④ 切退刀槽2mm 0.5mm4处, 2mm 1mm2处至图样要求。
38.5mm。0 0.06
mm,保证长度
c.车57 mm至57.30.1mm,保证
长度65mm。
d.倒角1.5 45°(两处)和蜗杆螺纹, 一端以20°角。
e.工件调头,车3000.014
mm至
300.1mm,保证长度50mm。
f.车350.007mm至3500..15
证长度35mm。
mm,保
g.车40mm至400.02
mm。
h.倒角1.5 45°三处和蜗杆螺纹一端
的20°角。
③ 调整车床。
a.调整车床各部间隙,减少主轴的轴向 窜动和径向跳动,减少母丝杠的轴向窜 动。
b.按模数6(导程18.85mm)调整车床 挂轮和各手柄位置。
(3)热处理。
图4.11 双头蜗杆
① 调质。T235。 ② 校直。跳动量不大于1mm。 (4)半精车各外圆及粗车蜗杆螺纹。 ① 修研两端中心孔。 ② 两顶尖安装半精车各外圆。
a.车350.007mm至3500..150
证长度33mm。
mm,保
b.车40mm至4000.2
c.用百分表校正小溜板,使导轨与工件 轴线平行。
④ 刀具的准备和安装。
a.按图4.5所示蜗杆螺纹粗车刀刃磨。
b.车刀安装,应对准工件轴线,两侧刀 刃中线垂直于工件轴线。
⑤ 粗车蜗杆螺纹。
a.粗车第一条螺旋槽。 b.移动小溜板9.425mm,粗车第二条
螺旋槽。
(5)精车。
5.多头蜗杆在车削中的测量
(1)齿厚测量法。
测量时,先将齿高卡尺读数调整到
等于蜗杆的齿顶高(即等于轴向模数
ms),然后法向卡入齿廓,其齿厚卡尺 测得的读数就是蜗杆螺纹中径(d2)处
的法向齿厚。
图4.9 用齿厚卡尺测量法向齿厚
1—齿高度尺 2—齿厚度尺
(2)三针测量和单针测量法。
在车削过程中无法用三针测量,一般都 采用单针测量。
课题四 多头蜗杆车削
学习目标 了解多头蜗杆的结构特点,掌握多头蜗
杆的分头方法。 了解多头蜗杆精车刀的几何角度和技术
要求,掌握正确的安装方法。 掌握多头蜗杆的车削工艺。 掌握多头蜗杆的检测方法。
一、基础知识
1.蜗杆的结构特点
图4.1 蜗杆蜗轮传动
一般蜗杆的齿形分为轴向直廓(阿
② 调头车端面,保证总长337mm,钻 中心孔。
图4.12 多头蜗杆
③ 三爪卡盘夹持已粗车的外圆,活顶尖
顶另一端,车削各外圆,留余量2~ 2.5mm;车削各阶台端面,留余量 0.5mm。
(3)热处理。 ① 正火。170~211 HB。 ② 校直。各部跳动量不大于1mm。 (4)半精车各外圆及粗车蜗杆螺纹。
mm处,活顶尖支持,用百分表校正
⑤ 工件调头,四爪卡盘垫铜垫夹持2200..0024
mm处,活顶尖后支持,用百分表校正
25 0.065mm处,跳动量不大于
0.02mm,车蜗杆螺纹退刀槽至图样要求。
⑥ 用百分表分头法粗车蜗杆螺纹,齿轮 游标卡尺测量齿厚3.3 9880.05mm。
(5)精车。
① 工件调头,四爪卡盘垫铜垫夹持1500..001021
① 精车外圆5700.06
② 精车蜗杆螺纹。
mm至尺寸。
【练习4.2】 车削一如图4.12所示的多头 蜗杆。单件生产。
1.工艺分析 2.车削加工工艺及步骤
(1)下料。38 339mm。
(2)粗车。
① 三爪卡盘装夹,伸出长度40mm,车 端面,钻中心孔,车外圆见光长30mm。
二、多头蜗杆车削实例练习
【练习4.1】 车削图4.11所示的双头蜗杆, 单件生产。
1.工艺分析 2.车削加工工艺及步骤
(1)下料。65mm 274mm。
(2)粗车。 ① 三爪卡盘装夹,车端面,钻中心孔。
② 调头车端面钻中心孔,保证总长 270mm。
③ 两顶尖安装粗车各部外圆,留全量 2~3mm,车各阶台面,留全量0.5mm。
基米德螺线)蜗杆和法向直廓(延长渐
开线)蜗杆两种。
2.多头蜗杆的分头方法
(1)轴向分头法
当车好一条螺旋槽后,工件不动,
车刀轴向移动一个螺距,再车第二条螺
旋槽。
① 小溜板刻度分头法。
② 用百分表和量块分头法。
③ 利用开合螺母结合小溜板移动分头法。
图4.2 蜗杆齿形种类
图4.3 用百分表和量块控制小溜板的移动距离
(1)粗车
① 粗车第一条螺旋槽,记住中溜板和小 溜板左、右“赶刀”的刻大值。
② 进行分度。
(2)半精车
① 采用轴向分头法 ② 采用圆周分头法
(3)精车
精车时,其切削速度和切削深度比
半精车时要小,这时只精车牙槽左、右
两侧面,不车底径。
图4.8 双头蜗杆的精车
① 采用轴向分头法。 ② 采用圆周分头法。 ③ 多头蜗杆分头不均匀性的修正。
图4.6 蜗杆螺纹精车刀
(3)蜗杆螺纹车刀的安装
精车轴向直廓蜗杆螺纹时,车刀两
侧刀刃所组成的平面应在蜗杆轴向截面
内。
精车法向直廓蜗杆螺纹时,车刀两
侧刀刃所组成的平面应在蜗杆法向截面
内。
图4.7 可调节螺旋升角的弹簧刀杆
1—紧固螺钉 2—开口弹簧钢套 3—刀杆体 4—垫圈 5—紧固刀杆螺母
4.多头蜗杆的车削方法
1—挡块 2—量块 3—百分表 4—小刀架 5—工件
(2)圆周分头法
① 挂轮齿数杆螺纹粗车刀 (2)蜗杆螺纹精车刀
图4.4 多孔插盘
1—定位插销 2—定位销孔 3—螺母 4—转盘 5—三爪卡盘 6—螺钉 7—拨块
图4.5 蜗杆螺纹粗车刀