20CrMnTi齿轮端面磨削裂纹原因分析
磨削裂纹产生的原因及措施
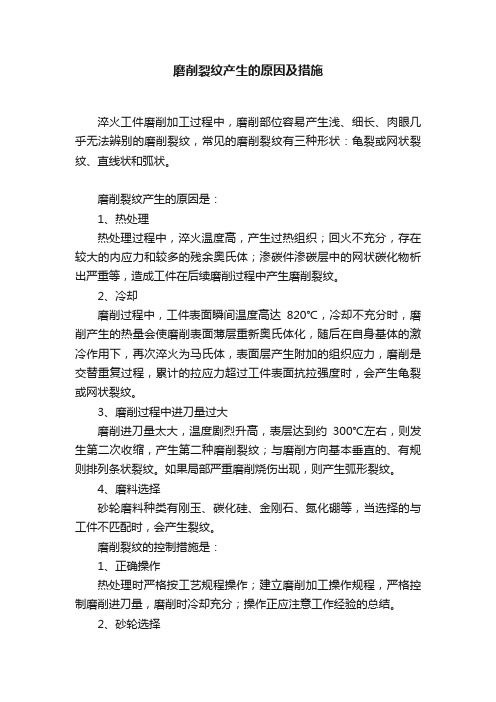
磨削裂纹产生的原因及措施淬火工件磨削加工过程中,磨削部位容易产生浅、细长、肉眼几乎无法辨别的磨削裂纹,常见的磨削裂纹有三种形状:龟裂或网状裂纹、直线状和弧状。
磨削裂纹产生的原因是:1、热处理热处理过程中,淬火温度高,产生过热组织;回火不充分,存在较大的内应力和较多的残余奥氏体;渗碳件渗碳层中的网状碳化物析出严重等,造成工件在后续磨削过程中产生磨削裂纹。
2、冷却磨削过程中,工件表面瞬间温度高达820℃,冷却不充分时,磨削产生的热量会使磨削表面薄层重新奥氏体化,随后在自身基体的激冷作用下,再次淬火为马氏体,表面层产生附加的组织应力,磨削是交替重复过程,累计的拉应力超过工件表面抗拉强度时,会产生龟裂或网状裂纹。
3、磨削过程中进刀量过大磨削进刀量太大,温度剧烈升高,表层达到约300℃左右,则发生第二次收缩,产生第二种磨削裂纹;与磨削方向基本垂直的、有规则排列条状裂纹。
如果局部严重磨削烧伤出现,则产生弧形裂纹。
4、磨料选择砂轮磨料种类有刚玉、碳化硅、金刚石、氮化硼等,当选择的与工件不匹配时,会产生裂纹。
磨削裂纹的控制措施是:1、正确操作热处理时严格按工艺规程操作;建立磨削加工操作规程,严格控制磨削进刀量,磨削时冷却充分;操作正应注意工作经验的总结。
2、砂轮选择1)尽可能选用锋利的砂轮,切削速度快,磨削效率高,磨削表面不易过热。
2)正确选择砂轮结构和硬度级别,以获得自由磨削效应。
3)陶瓷和金属作粘结剂的砂轮,适用于磨削热较高的场合;树脂粘结砂轮,适用磨削热较小的场合。
脆性较大的粘结剂,磨粒容易脱落,有利于使砂轮保持锐利状态。
4)SiC磨料磨削钢和铁基耐热合金时,产生强烈的化学磨损,刚玉类磨料磨削钢时无此反应。
相反,刚玉类磨料磨削玻璃、硅酸盐类陶瓷涂层时,会产生强烈的化学反应,SiC磨料无此反应。
3、如果已产生磨削裂纹,如果未超过加工余量,可进行多次低温回火,去除磨削应力,再按正确的磨削加工方法加工,磨去裂纹深度进行挽救。
汽车齿轮用20CrMnTiH钢顶锻裂纹产生原因及改进措施
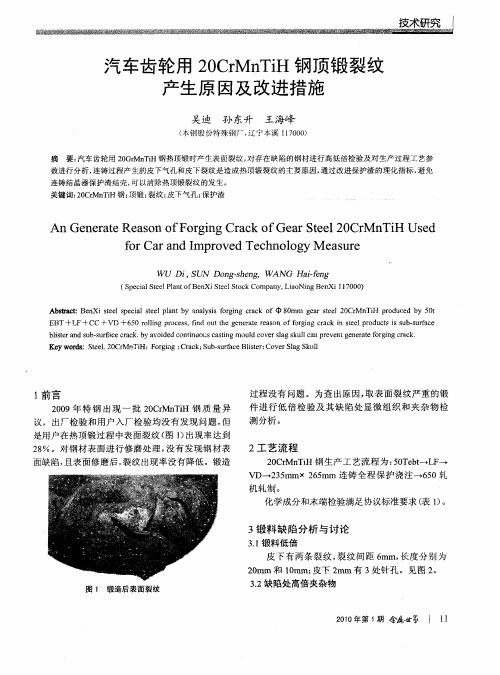
汽 车齿轮用 2 C Mn i 顶锻 裂纹 0 r TH钢 产 生 原 因及 改进 措 施
吴迪 孙 东升 王 海峰
( 本钢股 份特 殊钢 厂, 宁本溪 1 70 ) 辽 0 0 1 摘 要: 汽车齿轮用 2 G Mn i 0 r TH钢热顶锻时产生表面裂纹 , 对存在缺 陷的钢材进行 高低 倍检验及对 生产过程工 艺参
≤
0 2 .5 0 0 .6
0 0 ~ .4
O.1 0 0. O7
铁 素体 +珠 光 体 , 孔 周 围无脱 碳 。 针
圉
34组织 缺 陷对 热顶 锻 裂纹 的影 响 .
由于钢 材 存 在 裂纹 、表 面 气 孔 和 皮 下气 孔 , 加 热 炉 内表 面缺 陷外 露被 氧 化 而 形成 脱 碳 层 , 陷 处 缺 强 度 降低 , 热 顶 锻 下 , 下 部 位 存 在 很 大 的压 应 在 上
表 1 2 C Mn i 0 r TH钢的化学成 分和 末端检测 结果
项目
C S i ^ f n
化 学 成 分/ %
P S C r Ni C u
T i
末端/ பைடு நூலகம் 职
丁 g
3 ~ 6
4 2 4 0
J1 5
2 ~ 8
3 5 3 2
标准 检 验 值
1 前言
20 0 9年 特 钢 出 现 一 批 2 C Mn i 钢 质 量 异 O r TH
过 程 没有 问题 。为查 出原 因 , 取表 面 裂 纹 严 重 的锻
件进行低倍检验及其缺 陷处显微组 织和 夹杂物检
测分 析 。
议 ,出厂 检验 和 用 户入 厂 检验 均没 有 发 现 问题 , 但 是用户 在热 项 锻过 程 中表面 裂 纹 ( 1出现 率达 到 图 ) 2 %。对钢 材 表面 进 行修 磨 处 理 , 有 发现 钢 材 表 8 没 面缺 陷, 且表 面修 磨后 , 裂纹 出现 率没有 降 低 。锻 造
20CrMnTi渗碳齿轮磨削裂纹的分析与解决
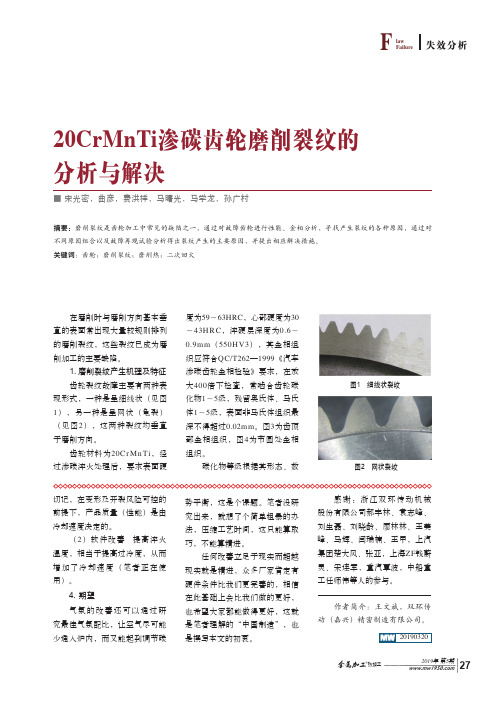
图1 细线状裂纹
图2 网状裂纹
感谢:浙江双环传动机械股份有限公司郝丰林、袁志峰、刘生磊、刘晓龄、廖林林、王美峰、马辉、闫瑞楠、王甲,上汽集团楚大风、张亚,上海ZF钱蔚灵、宋连军,重汽覃波,中船重
图3 齿顶部金相组织
图4 节圆处金相组织
量、大小、分布情况确定,具体
说明如表1所示。
残留奥氏体等级按其含量多
少确定,马氏体等级按其针体大
小确定,具体说明如表2所示。
通过对故障齿轮进行金相、
性能分析,齿轮金相组织及热处
图5 裂纹齿轮金相
图6 导致磨削裂纹的鱼骨图分析。
20CrMnTi锻造开裂原因分析_崇鹏

图 5 氮化钛夹杂物
图 8 ห้องสมุดไป่ตู้常区域组织 F + P
5 分析与讨论 从化学成分上看,钢的成分符合国家标准。 从金相检验结果来看,钢中裂纹走向交错分布, 裂纹形态各异,说明钢基体承受了较大的作用力或基 体本身存在缺陷而无法承受这种作用力下的变形,导 致形成了较复杂的裂纹特征。 有的裂纹附近出现大量的高温氧化圆点,因高温 氧化圆点必须在 900℃ 以上,而且还要有一定的时间 才能形成,这么多的高温氧化圆点应该在加热炉内才 能形成,也就是说钢材在锻造加热前已经有暴露于外 表的缺陷。而且裂纹内填充了大量的夹杂物,这些夹 杂物有内生的氧化夹杂物、大量的氮化钛夹杂物以及
12
的部位有明显的富碳现象( 图 7) ,而正常区域组织为 F + P( 图 8) 。
图 2 整个试面上的夹杂物
櫯櫯櫯櫯櫯櫯櫯櫯櫯櫯櫯櫯櫯櫯櫯櫯櫯櫯櫯櫯櫯櫯櫯櫯櫯櫯櫯櫯櫯櫯櫯櫯櫯櫯櫯櫯櫯櫯櫯櫯櫯 ● 鄂钢科技
图 3 裂纹周围的氧化物
图 6 混合组织区
图 4 裂纹头部的外来夹杂物
图 7 增碳部位组织 P + F网
櫯櫯櫯櫯櫯櫯櫯櫯櫯櫯櫯櫯櫯櫯櫯櫯櫯櫯櫯櫯櫯櫯櫯櫯櫯櫯櫯櫯櫯櫯櫯櫯櫯櫯櫯櫯櫯櫯櫯 ●2010 年第 4 期
20CrMnTi 锻造开裂原因分析
崇 鹏 ( 扬子重机)
摘 要 通过成分分析、金相检验等方法对 20CrMnTi 制成的半成品锻造开裂原因进行分 析。结果表明: 由于钢中存在大量的夹杂物,导致锻造开裂。
≤0. 035
Cu
Cr
0. 04
1. 03
― 1. 00 ~ 1. 30
( %) Ti 0. 075 0. 04 ~ 0. 10
4 金相检验 取缺陷处试样横向制样观察,整个试面布满了大 量的夹杂物( 图 2 ) ,有的夹杂物沿轧制方向延伸较 长,甚至超过几个视场。试面上有多条裂纹,有的从 边缘向里延伸,有的在心部自绘而成,交错分布; 有的 裂纹周围氧化现象较严重,有高温氧化圆点( 图 3) ; 有的裂纹附近填满大块的外来夹杂物( 图 4) 、金黄色 的氮化钛( 图 5) 和一些少量的内生氧化物。用 2% 硝酸酒精浸蚀后,肉眼观察整个试面的组织颜色不一 致,有明显的组织差异; 在显微镜下观察,整个试面组 织极不均匀,缺陷部位的组织为混合组织( 图 6) ,有
20CrMnTi齿轮开裂失效分析

20CrMnTi齿轮开裂失效分析
刘洪波;李宁;李红印;邹鹏;陈炳欣
【期刊名称】《热处理技术与装备》
【年(卷),期】2024(45)2
【摘要】20CrMnTi齿轮经过真空渗碳及高压气淬低温回火热处理后,在磨齿工序发现齿轮开裂。
通过化学成分分析、硬度测试、金相组织观察和断口形貌分析等方法对20CrMnTi齿轮开裂原因进行分析,结果表明齿坯存在过烧缺陷是导致齿轮开裂的根本原因。
【总页数】3页(P44-46)
【作者】刘洪波;李宁;李红印;邹鹏;陈炳欣
【作者单位】弗迪动力有限公司齿轮工厂;石家庄钢铁有限责任公司技术中心【正文语种】中文
【中图分类】TG156.5
【相关文献】
1.20CrMnTi钢冷挤压开裂的失效分析
2.20CrMnTi齿轮钢锻打开裂原因分析及措施
3.20CrMnTi万向十字轴开裂失效分析
4.20CrMnTi钢花键轴开裂失效分析
5.20CrMnTi齿轮开裂失效分析
因版权原因,仅展示原文概要,查看原文内容请购买。
20CrMnTi圆钢加工开裂原因分析及改进措施

20CrMnTi圆钢加工开裂原因分析及改进措施王雷国;王建忠;姚建辉;杜敬洲【期刊名称】《金属世界》【年(卷),期】2018(000)002【总页数】4页(P60-63)【作者】王雷国;王建忠;姚建辉;杜敬洲【作者单位】河钢邯钢品质管理部,河北邯郸 056015;河钢邯钢品质管理部,河北邯郸 056015;河钢邯钢品质管理部,河北邯郸 056015;河钢邯钢品质管理部,河北邯郸 056015【正文语种】中文渗碳钢20CrMnTi淬透性较高,经渗碳淬火后具有硬而耐磨的表面与坚韧的心部,具有较高的低温冲击韧性,正火后可切削性良好,抗疲劳性能相当好,被广泛用于制造承受高速、中等或重载荷、冲击及摩擦的重要零件,如齿轮、齿圈、齿轮轴十字头等。
邯钢一炼钢厂有一台200 mm×200 mm断面方坯连铸机,具有中间包连续测温、结晶器电磁搅拌、末端电磁搅拌等功能。
大型轧钢厂棒材生产线全线轧机能够实现全线无扭控制轧制,轧线上设有测径仪,可保证产品尺寸精度。
邯钢大型轧钢厂棒材生产线于2011年3月投产,年设计生产能力为80万t,产品规格为φ12~90 mm圆钢,其中20CrMnTi占全部产量的5%。
但是该品种自生产以来,断续在使用过程中发生了几起较为典型的加工开裂问题,经过系列分析,找出了导致加工开裂的原因,并制定了改进措施,使加工开裂问题得到控制。
原因分析根据加工开裂质量异议处理情况,认为导致20CrMnTi加工开裂原因主要分为炼钢原因、轧钢原因和用户加工原因。
其中,20CrMnTi的化学成分要求见表1。
炼钢原因某用户反馈的棒材20CrMnTi在锻造、辗环过程发生纵向裂纹(见图1),用户加工工艺为:圆钢—中频加热—下料—锻打—辗环—机加工—热处理。
从缺陷试样上切取金相试样进行裂纹缺陷分析(见图2),裂纹深度为2.61 mm,裂纹头部宽度0.57 mm,裂纹周围可见大量氧化物质点,裂纹周围组织存在严重脱碳,判定该裂纹缺陷为铸坯裂纹。
浅析20CrMnTi热轧棒材表面裂纹特点及产生原因
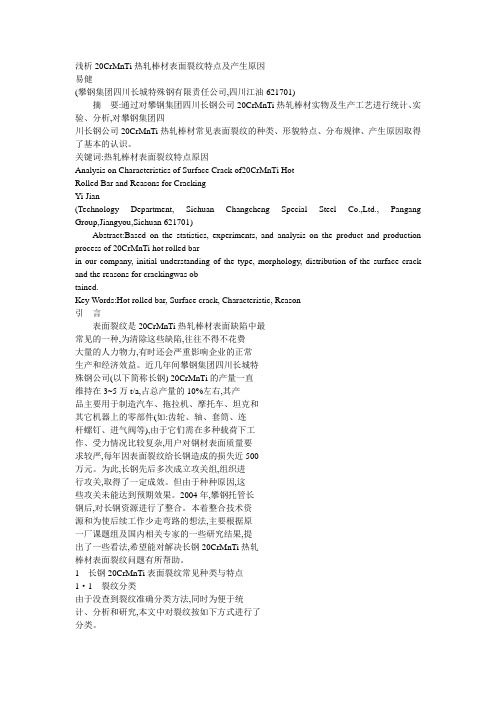
双侧裂纹;(3)三面裂纹;(4)周身裂纹。并按各次
试验进行分析通过对四次试验结果的统计分析可知:
分别抽取了20支钢材对应检查,结果见表3。
表3第二次试验20CrMnTi表面裂纹情况
Table3Examination results on surface cracks of the
rolled bar produced by continuous casting blank
坯型
表面情况每支裂纹条数裂纹严重者裂纹较轻者
万元。为此,长钢先后多次成立攻来自组,组织进行攻关,取得了一定成效。但由于种种原因,这
些攻关未能达到预期效果。2004年,攀钢托管长
钢后,对长钢资源进行了整合。本着整合技术资
源和为使后续工作少走弯路的想法,主要根据原
一厂课题组及国内相关专家的一些研究结果,提
出了一些看法,希望能对解决长钢20CrMnTi热轧
关键词:热轧棒材表面裂纹特点原因
Analysis on Characteristics of Surface Crack of20CrMnTi Hot
Rolled Bar and Reasons for Cracking
Yi Jian
(Technology Department, Sichuan Changcheng Special Steel Co.,Ltd., Pangang Group,Jiangyou,Sichuan 621701)
锭型裂纹率/%
大锭尾60.00
小锭尾75
大锭头50
小锭头100
从表2中的数据可以看出:本次实验的10炉大
锭轧材表面裂纹产生机率比小锭轧材产生机率低。
20crmnti棒材剪切端部开裂分析及预防措施

w(Cr) 1. 00-1. 30
1. 12 1. 15
!(Ti) 0. 04-0. 10
0.06 0.08
2.2硬度测定
利用便携式硬度计在2支试样的开裂端面上进 行硬度测定,每支试样分别打6个点,结果如表2所 示,可以看出材料的芯部区域硬度远高于 20CrMnTi钢热轧态正常组织的硬度220 HB。
37
验,剪切面纵向组织有明显的朝一侧的流变现象,开 裂处中心纵向截面为裂纹缺陷,裂纹深度约为6. 85 mm,裂纹底部较为尖锐,裂纹内未发现有氧化物, 裂纹两侧未发现有脱碳现象,裂纹旁边存在马氏体 条带组织,且马氏体条带与裂纹开口处相交,如图 2-3所示。把试样横截面磨制检验,发现心部区域 存在马氏体组织,正常处组织为铁素体+珠光体,如 图45所示%
表1 20CrMnTi钢试样化学成分/%
标准值 试样1 试样2
!(C) 0. 18-0. 23
0. 20 0.20
!(Si) 0. 17-0. 37
0. 26 0. 23
! (Mn) 0. 80-1. 10
0. 99 0. 97
!(P) "0. 035
0. 011 0. 015
!(S) "0. 035
3端裂影响因素分析
3.1 钢的组织
20CrMnTl属于亚共析钢,正常组织为珠光体 +铁素体,而上述检测的组织中存在异常组织(马氏 体),马氏体组织的特征是硬而脆,故马氏体组织的 变形性能极差,其在受到较大剪切应力时会不易产 生变形而开裂%
图2开裂处中心纵向微观形貌(25G )
3.2剪切温度
剪切温度的高低直接与剪切应力相关%温度高 需要的剪切力降低,反之则增大%根据对现场 20CrMnTl钢剪切断面观察,剪切温度高低对应的 剪切断面颜色也有所不同,产生剪切裂纹的钢材端 部呈现出银白色(剪切温度V350 H),剪切断面为 蓝色(剪切温度$350 H)的未发现有剪切裂纹,具 体形貌如图6所示%
- 1、下载文档前请自行甄别文档内容的完整性,平台不提供额外的编辑、内容补充、找答案等附加服务。
- 2、"仅部分预览"的文档,不可在线预览部分如存在完整性等问题,可反馈申请退款(可完整预览的文档不适用该条件!)。
- 3、如文档侵犯您的权益,请联系客服反馈,我们会尽快为您处理(人工客服工作时间:9:00-18:30)。
徐州科源液压股份有限公司生产的合金钢齿轮,表层经渗碳淬火硬化后,在磨齿轮端面时发现裂纹、剥落及烧伤痕迹。
根据齿轮渗碳层金相组织的显微分析,可以看出组织为马氏体、残余奥氏体和碳化物。
其中,残余奥氏体含量(体积分数)约在30%,碳化物级别为3级。
按照《JB/T6141.3-1992重载齿轮渗碳金相检验》标准评判,此金相组织为4级,残余奥氏体含量较高,致使磨削时组织转变量较多,表面应力较大,存在磨削裂纹潜在危险。
1显微组织观察与显微硬度测试1.1显微组织分析根据齿轮心部的显微分析,看到组织为板条状马氏体。
根据表面组织的显微分析,可以看出磨削平面表层为一较薄的亮层,次表层为颜色较暗的回火层。
再往里才过渡到低温回火处理的正常组织。
组织分布说明,零件磨削过程中,表层已被加热到奥氏体温度,因未经回火,质地坚硬,难以腐蚀,故在金相试样上呈白亮层。
白亮层为二次淬火形成的马氏体组织。
该组织的形成是由于磨削区磨削进给量非常大或冷却不足时,磨削区的温度非常高,达到了奥氏体化临界温度以上,随后冷却时形成了淬火马氏体组织。
此时,组织变化造成体积比随之变化,产生了压应力。
次表层温度虽也较高,但在相变温度下却高于低温回火温度,故在磨削过程中继续回火转变,成为回火索氏体和回火屈氏体。
该组织容易接受腐蚀,在金相试样上呈暗黑色,受磨削热的影响,温度可达到200~500℃,致使残留奥氏体转变生成马氏体。
这一转变使体积比增大,在工件内部产生相变应力,再加上砂轮磨削工件时所造成的撕裂应力,造成磨削裂纹。
1.2硬度及渗碳层深度检测切割制样,对截面试样进行硬度检测,即在垂直于磨削平面的深度上测其显微硬度。
根据测量结果,表面白亮层硬度很高;次层的低硬度与回火温度相对应;往内部的低温回火过渡时,硬度却又升高,并在一定深度范围内保持一定值;直到超过渗碳层后,硬度值逐渐下降。
金相法测得渗碳层深1.2~1.4mm ,符合技术要求。
1.3裂纹微观形貌磨削裂纹断面清洁而无氧化色,呈脆性形态的断口形貌。
显微观察磨削裂纹深度较浅(0.2~0.4mm )并沿晶发展,尾部较细尖,裂纹在次表层分叉。
2综合分析由上述显微组织观察结果与显微硬度测试结果的一致性可判断,此批齿轮磨削时产生了磨削裂纹和浅层剥离,属于典型的磨削开裂。
磨削裂纹是磨削拉应力超过材料断裂强度所致。
砂轮的切削是利用砂轮中许多多角形的砂粒形成很多小刀,和工件接触时进行摩擦切削。
切削过程中,刀刃(砂粒)前面的金属受到挤压和撕裂,刀刃后面的金属与砂轮的剧烈摩擦使晶粒受拉和滑移,因而引起金属的弹性与塑性变形。
当切削作用停止后,金属表层在弹性变形力的作用下力求恢复原位,因此出现平行磨削轨迹的拉伸应力,但磨削裂纹的形成不仅与磨削条件和工艺有关,还与材质、热处理不良等因素有密切关系。
2.1磨削工艺的影响磨削加工工艺参数对磨削烧伤和裂纹的产生具有决定性作用。
磨削时,由于金属的塑性变形以及砂轮与工件的剧烈摩擦,使磨削所消耗的80%的功变成热量。
大部分的热量导入工件表面,可以使表面瞬时温度达到800~1000℃,严重时甚至可使表面呈金属融化状态。
这种高温势必引起工件表面层组织和性能的改变。
磨削变热的特点是瞬间(约0.01s )快速升温,形成很陡的温度梯度,随即又以800~1000℃/s 的速度冷却。
受热后表层金属体积膨胀,但受到内层冷金属的制约,引起塑性变形方式缓解,因此产生残余拉应力。
温度越高,金属导热性越差;温度梯度越陡,则热应力越大。
所以,选择合理的磨削工艺参数尤为重要。
(1)磨削深度的影响。
增加磨削深度,单颗粒的切削厚度增大,同时参与切削的磨粒数也增多。
因此,在磨削过程中磨削力增大、产生热量增多,导致磨削表面及表层内的温度增加,且受到回火作用的程度与深度也增加。
因此,磨削深度的增加加大了工件被烧伤的程度和裂纹的形成。
所以,必须严格控制磨削深度,尤其是硬度较高的工件。
(2)砂轮切削速度的影响。
提高砂轮切削速度或增大20CrMnTi 齿轮端面磨削裂纹原因分析郁静(徐州科源液压股份有限公司,徐州221116)摘要:合金钢表层经渗碳、氮化等硬化的零件,在磨加工时较易发生表面磨削损伤。
磨削损伤主要指磨削烧伤和磨削裂纹。
磨削烧伤和磨削裂纹的存在,严重降低了零件的使用寿命,是不允许存在的缺陷。
本文将重点讨论在实际生产过程中对该类缺陷的原因分析和排查,并提出相应的解决措施。
关键词:20CrMnTi 合金钢齿轮磨削裂纹工艺与装备1352017第7期总第248期现代制造技术与装备砂轮直径,使砂粒的切削厚度随着砂轮圆周速度增加而减少。
曾有人研究磨削切削深度与砂粒速度之间的关系,得出提高砂轮速度必须减少切削深度的对应关系,找出了非磨损烧伤的安全区。
根据实际情况,若要实现无烧伤磨削,砂轮圆周速度为600m/min时,切入深度应控制在0.09mm以下。
若砂轮速度提高到1000m/min,切入深度应减少到0.05mm左右。
若砂粒的切削圆半径与切削之间比例失调,砂粒的切削刃后面的材料受挤压而产生塑性变形引起摩擦,使摩擦热增加和磨削区温度急剧升高导致烧伤。
再者,如果选用的砂轮过硬,粒度过细,砂轮表面也易被磨堵塞,从而使砂轮和工件间形成挤压摩擦,使切削区产生大量的热,也易导致烧伤。
(3)工件转速的影响。
若工件转动速度增加时,虽单颗粒的切削厚度增大,磨削热也增加,但工件转速增大,意味着热源在工件表面的移动速度加快。
因此,磨削区的热作用时间缩短,单位时间内单位切削面积上传入工件的热量减少,结果是随工件转速的增大,工件最表面的峰值温度有所增加,次表面的峰值温度有所降低。
工件移动速度越快,表面层内的温度下降梯度也越大。
因而,回火层深度反而减少。
由此可见,适当增大工件转速有利于减轻烧伤。
2.2材质的影响材料加工性能与其化学成分和组织密切相关。
钢中碳的含量从0.1%增加到0.8%时,磨削的单位效率可提高4倍,且零件的表面质量指标可获得最佳数值。
如果钢中加入Cr、Mo、Ni、W和V等合金元素,可生成Cr23C6、Fe3Mo3C、Fe3W3C和MoC、VC、WC、TiC等碳化物。
由于WC、TiC和VC等碳化物稳定性好,在奥氏体中溶解度低,同时具有高硬度和融化温度,所以这些残留碳化物会使砂轮磨粒迅速磨损,从而使磨削区的摩擦热增加,温度急剧上升。
这不仅降低了加工效率,还会引起工件表层内较深组织的变化和裂纹的形成。
工件内部组织分布不均匀,呈网络状或条状时,易在磨削后延脆性组织分布方向出现磨削裂纹。
这时由于不同显微组织热导率不同,当钢中存在较多的碳化物和残余奥氏体时,将严重影响钢的导热能力,增加磨裂的敏感性。
2.3渗碳工艺的影响渗碳层碳浓度过高或碳化物形成网状分布或块状分布于晶界,不但削弱了晶界的结合,而且明显地影响热传导,加剧磨削裂纹的生成。
淬火后,组织应力、热应力增大。
磨削时,也易产生应力集中而开裂。
2.4淬火工艺的影响对于渗碳件来说,出现磨削裂纹倾向也随渗碳后淬火温度的提高而增加。
20CrMnTi钢经930℃渗碳后,分别预冷到860℃和830℃淬火,再经200℃回火处理后,淬火温度高,磨裂倾向大。
这是由于高温引起晶粒长大而形成的粗针状马氏体中含碳量的增加使热导率减小,摩擦热增加,因而也增加了热应力。
此外,高碳马氏体存在许多微裂纹,被认为是高碳马氏体断裂强度降低的主要原因。
实践证明,粗大马氏体和大量残余奥氏体的存在,即使谨慎的轻微磨削也极易产生磨削裂纹。
2.5回火工艺的影响淬火后的回火温度、保温时间和回火次数,对磨裂倾向影响很大。
回火温度低,保温时间短,回火不充分,则硬度较高,马氏体中微裂纹多而脆性大,极易产生磨削裂纹。
20CrMnTi渗碳淬火后磨削全部出现磨裂,经180℃回火后磨裂比例降至60%~70%;当在200℃保温3小时回火后,磨裂倾向已趋于0。
对于未回火的马氏体组织磨削,磨削热足以使马氏体发生转变,析出碳化物,造成零件表面与内部的比容差,从而引起较高的内应力,形成裂纹。
2.6磨削液的影响磨削液在对工件表面冷却的同时具有对冲洗切屑、防止砂轮孔隙堵塞等的清洁作用,以及减少磨粒与工件间的摩擦、防止零件温度上升、保持零件尺寸精度避免磨削损伤等作用。
如果在磨削时冷却不充分或磨削液选用不当,磨削产生的热量也足以使磨削表面薄层重新奥氏体化,随后再次淬火形成淬火马氏体,使表面层产生附加的组织应力。
再加上磨削所形成的热量使零件表面的温度升高极快,这种组织应力和热应力的迭加可能导致磨削表面出现磨削裂纹。
后续的循环应力将使裂纹扩展开来形成宏观裂纹。
特别注意轴和齿轮类零件的转角台阶处,由于磨削过程中冷却液不易进入而引起“热积聚”现象。
磨削温度较高,散热条件较差,易引起磨削烧伤和磨削裂纹,此时磨削工艺参数的选择尤为重要。
2.7机床精度的影响由于机床主轴跳动造成砂轮与工件互相撞击也会引起烧伤。
3建议措施对现场的工艺及工艺的执行情况进行排查、整改,整改措施如下。
第一,降低渗碳件的淬火温度。
在930℃中渗碳,渗碳后直接淬火,淬火温度由860℃降至830℃。
第二,调整回火温度与回火保温时间。
春、秋、夏三季的回火时间由2小时延长至3小时;冬季延长至4小时,且回火温度的下限从180℃提高到200℃,80排量以上的齿轮进行二次回火2H,或在160~180℃的热油中进行时效12小时。
第三,控制表面碳浓度,碳浓度控制在0.65%~0.8%。
碳浓度分布梯度要平缓,以保障良好的表面强度和应力分布。
重载齿轮的碳含量应控制在下限,以有利于控制碳化物的大小和形状。
碳含量控制在上限时,会增强形成残余奥氏体的趋向,并有增加碳化物、表层氧化与降低齿根强度的趋向。
据有关资料表明,美国对重载齿轮表面碳浓度已控制在0.65%左右。
第四,控制残余奥氏的数量,防止齿轮在磨削时产生组织转变而产生较大的组织应力。
严格控制残余奥氏体136处妨碍焊接的杂质清理干净,露出金属光泽并打磨成圆滑过渡。
(2)施焊。
施焊过程相对于一般的焊接过程更为复杂。
由于其材质的特殊性(轨道材质为U71Mn),往往焊缝容易出现裂纹、气孔等一系列问题。
因此,要考虑到与原材料的融合,尽量减少热影响等因素。
所以,对于焊材的选择及焊接方法的选择应该尤为慎重,特别地,对于焊工的技能要求也非常高,以达到尽可能少地出现焊接缺陷。
轨道凹坑处补焊前火焰预热至300℃,预热范围凹坑中心到两侧各100mm。
焊接过程中,必须始终保持该预热温度。
层间温度控制在300~350℃,最高不超过350℃。
采用轨道专用手工盖面焊条OK83.28Ф4mm小电流,一次施焊将凹坑填满,中间不得停顿,且注意将焊渣清理干净。
(3)焊后处理。
为了使补焊后的材料性能达到要求,同时消除焊接过程中的如残余应力等缺陷,常常对补焊后的零件做热处理,使其达到最佳的使用性能。