冶金专业毕业论文
冶金英语毕业论文范文

冶金英语毕业论文范文Title: Technological Advances in Metallurgy: Enhancing Efficiency and Sustainability in the Industry Abstract:The field of metallurgy has witnessed significant progress in recent years, driven by ongoing advancements in technology. These advancements have led to improved efficiency, enhanced sustainability, and reduced environmental impact in the metallurgical industry. This paper aims to explore some of the key technological developments that have shaped the field of metallurgy and their impact on the industry. The study highlights how these advancements have resulted in increased productivity, energy conservation, and the adoption of more sustainable practices. Additionally, it discusses the challenges and opportunities that lie ahead in the pursuit of further advancements in metallurgy.Introduction:Metallurgy plays a crucial role in various industries, including manufacturing, construction, and transportation. The production of metals involvescomplex processes that require careful consideration of cost, time, energy, and environmental factors. Over the years, technological advancements have revolutionized the field of metallurgy, providing innovative solutions to longstanding challenges and opening new doors for the industry.Body:1. Advanced Extraction Techniques:One area where technological advancements have significantly impacted metallurgy is in the extraction of metals from ores. Traditional extraction methods often involved extensive energy consumption and the emission of harmful pollutants. However, the introduction of innovative techniques such as hydrometallurgy and bioleaching has transformed the extraction process. These methods utilize chemical reactions and microorganisms to extract metals, resulting in reduced energy consumption and environmental impact.2. Innovations in Smelting and Refining:Smelting and refining are crucial steps in the metallurgical process, where the impurities are removed to obtain pure metals. Technological advancements have introduced processes such aselectrorefining, which utilize electricity to purify metals. This innovative approach results in higher purity levels, reduced waste generation, and enhanced cost-effectiveness.3. Automation and Robotics:Automation and robotics have significantly transformed the metallurgical industry, leading to increased efficiency and productivity. Automated systems can perform complex tasks with precision and consistency, reducing the potential for human error. They also allow for continuous monitoring and data collection, enabling real-time optimization of processes. The integration of robotics in industries such as the steel sector has resulted in safer working conditions, improved quality control, and faster production rates.4. Sustainable Practices:The metallurgical industry has faced increasing pressure to adopt more sustainable practices that minimize environmental impact. Technological advancements have played a pivotal role in facilitating this transition. For instance, the introduction of energy-efficient furnaces and advanced waste treatment systems has significantlyreduced energy consumption and emissions. Additionally, the use of recycled materials and waste valorization techniques has decreased the industry's reliance on virgin resources, promoting a circular economy approach.Conclusion:Technological advancements have revolutionized the field of metallurgy, enabling the industry to enhance efficiency, productivity, and sustainability. From advanced extraction techniques to automation and robotics, these innovations have transformed traditional processes and paved the way for new possibilities. The integration of sustainable practices has further reduced the environmental impact of the industry. However, challenges lie ahead, such as ensuring the responsible use of technology and addressing the potential drawbacks associated with automation. By harnessing the potential of emerging technologies and focusing on sustainable practices, the metallurgical industry can continue its growth trajectory while minimizing its ecological footprint.。
冶金-连铸-炼钢-炼铁-毕业论文

毕业设计(论文)学校:科技学院专业:冶金工程概论班级: 2015级能化一班学生:龚禄星学号: 2015444487指导教师:高绪东摘要溅渣护炉技术作为一项工艺简单、综合经济效益高的新技术,正别外国许多厂家推广、使用,分析了该技术的优势及存在的问题和解决办法,以及该技术的应用现状和应用前景。
转炉溅渣护炉是在出钢后,将转炉留渣的粘度和氧化镁含量调整到合适的围,在车间原有的氧枪或另设专用喷枪,向氧化镁含量、高粘度的炉渣喷一定压力和流量的氮气,将粘渣吹溅到炉衬上全面涂挂、冷却、凝固成一层炉渣质的保护层,避免了在冶炼时炉衬和炉渣的直接接触,从而起到减缓耐火材料的蚀损,延长转炉炉龄的作用。
溅渣护炉作为一项实用技术,经过国外许多钢厂实践后,对提高转炉炉龄和降低耐火材料消耗的效果非常显著。
关键词:溅渣护炉;转炉;应用目录1存在问题及解决办法 (1)2溅渣护炉工艺的冶金因素及其优势 (2)3国外溅渣炉技术的发展 (3)4国转炉炉龄现状及溅渣护炉技术的发展 (5)5应用现状及应用前景 (6)致信 (7)参考文献 (8)1存在问题及解决办法任何一项技术的应用不可能没有缺陷,在一些早期设备上,氧枪结瘤就是一个问题。
溅渣技术使用后,往往使枪结瘤出现次数增加。
实践证明,在溅渣过程中,若炉残留少量钢水,氧枪结瘤将更加严重。
解决这个问题,有几种方法证明是有效的。
第一,有充足冷却水的炉子不出现结瘤问题;第二,将用于吹炼的热氧枪移走,换上冷枪完成溅渣,氧枪结瘤几乎完全消除。
这表明氧枪结瘤与温度和热量的传递有关。
渣子和冷枪的表面结合并不紧密,如果在溅渣时冷凝钢不出现在氧枪上,那就不会再氧枪上形成粗糙的外壳以使炉渣粘附其上。
溅渣后将氧枪停放在支架上,形成的渣壳将冷却,并与氧枪分离,脱落。
使用底吹搅拌技术的BOF转炉对溅渣技术的应用提出了新的要求。
在溅渣时炼钢工必须小心,不能使炉底的渣太多;氮气的流速必须足够高,以便将炉渣吹离炉底;另外要调整经过透气砖喷吹气体的压力、流量。
冶金技术论文

冶⾦技术论⽂当代,论⽂常⽤来指进⾏各个学术领域的研究和描述学术研究成果的⽂章,简称之为论⽂。
它既是探讨问题进⾏学术研究的⼀种⼿段,⼜是描述学术研究成果进⾏学术交流的⼀种⼯具。
它包括学年论⽂、毕业论⽂、学位论⽂、科技论⽂、成果论⽂等,论⽂⼀般由题名、作者、摘要、关键词、正⽂、参考⽂献和附录等部分组成,其中部分组成可有可⽆。
冶⾦技术论⽂1 摘要:钢铁是⼈类使⽤最多的⾦属材料,钢铁⼯业被称为现代⼯业的脊梁。
我国作为⼀个发展⼤国,每年对于钢铁的需求都是极为庞⼤的。
据不完全统计,我国每年⽣产的粗钢产量超过五亿吨。
然⽽在钢铁⽣产的过程中,不可避免的会产⽣⼆次资源。
结合我国为数巨⼤的钢铁产量,在其中发展循环经济的效益也就显得⼗分可观。
关键词:钢铁循环经济;粉末冶⾦技术;应⽤ 近年来,可持续发展意识已在各⾏各业的⽣产活动中得到⼴泛体现,在钢铁冶炼⾏业中亦是如此。
随着冶炼技术的不断发展成熟,我国对钢铁冶炼产⽣的⼆次资源也形成了有效的利⽤,即使⽤粉末冶炼技术[1-3]。
通过对粉末冶炼技术的应⽤,可以有效的提⾼⾦属资源的利⽤能⼒,从⽽提⾼钢铁⾏业的⽣产效率。
因此,本⽂将对粉末冶⾦技术在钢铁循环经济中的应⽤展开⼀系列的介绍和讨论[4]。
1粉末冶⾦技术应⽤于钢铁循环经济的意义 1.1提升资源利⽤率 粉末冶⾦技术的应⽤能够对钢铁冶炼产业造成诸多积极影响,⽽其中最为直接的便是提⾼资源的利⽤效率。
顾名思义,粉末冶⾦多的原材料是粉末,⽽冶⾦主要对象则是⾦属,所以,在其冶炼过程中需要使⽤到⼤量的⾦属粉末[5]。
⼀般⽽⾔,如⽆特殊需求,钢铁企业不会刻意的制取⾦属粉末进⾏冶炼。
但在实际的⽣产活动中,经过⼀定的⼯艺流程之后,往往会产⽣相当⼀部分的含⾦属粉末,这些粉末,⽆疑可以通过粉末冶⾦技术进⾏⼆次加⼯,⽽不⾄于被当作⼯业垃圾处理导致资源浪费。
1.2提升经济效益 钢铁循环经济备受政府和企业推崇的原因还在于其经济效益,我国钢铁产业规模巨⼤,因此⽽产⽣的⾦属粉末总量也极为庞⼤,通过粉末冶⾦技术的⼆次加⼯,可以在⼀定程度上减少其在原材料⽅⾯的投⼊,并且由此⽽⽣产出的钢铁数量也不在少数,另外,从某种⽅⾯来说,这也可以减少企业在粉末处理⽅⾯投⼊的费⽤,由此,在增收减⽀共同影响下所产⽣的经济效益也就不⾔⽽喻了。
冶金毕业论文:高炉煤气干法除尘_毕业论文范文_

冶金毕业论文:高炉煤气干法除尘古典文学中常见论文这个词,当代,论文常用来指进行各个学术领域的研究和描述学术研究成果的文章,简称为论文。
以下就是由编为您提供的冶金。
1 前言高炉煤气干法除尘工艺相比于传统的湿法除尘工艺,以其煤气净化质量高、节水、节电、运行费用低、环境污染小、出口煤气温度高,使 trt 发电量大幅提高等优点,在钢铁行业广泛应用。
在实际生产过程中,难免会遇到高炉炉况不正常现象,高炉顶温控制不当,严重偏高或偏低的情况下,对高炉煤气干法除尘的影响非常大。
中天钢铁8 号高炉经常出现低顶温现象,导致高炉煤气干法除尘器滤袋表面湿灰黏结,造成滤袋透气性降低,箱体压差升高,存在很大的安全隐患。
同时煤气中的水蒸气冷凝成水,造成除尘灰在箱体锥部结块,无法正常对除尘器各箱体进行放灰作业,严重影响高炉的稳定和正常生产。
为了解决这个问题,我们进行了彻底的调查和研究,找到了解决问题的措施。
2 控制措施2.1 增加焦炭烘烤工艺在高炉炉顶煤气流动和传热是固体之间以对流传热为主;顶部气体温度取决于热储备区温度、热流率 , 温度 , 即:高炉 , 因为 t 空几乎是恒定的 , 因此 , 最高温度的关键因素是热流率和炉料的温度。
在不变的热流率的条件下 , 温度越低 ,t,t 空材料差异 , 更大的气体通过通过炉料的热量越多 , 更少的热量以及天然气,烟气温度较低;另一方面,材料温度较高,t,t空材料差异较小, 气体通过通过炉料的热量越少 , 气体 , 更多的热量随烟气温度较高。
故将我们对入炉焦炭采用烟气烘烤工艺进行加热。
从8 号高炉热风炉烟道引一根dn800 的管道至槽下,将热风炉煤气燃烧产生的烟气通过风机抽到料仓,利用烟气的余热对焦炭进行烘烤加热,不但有效去除了焦炭中的水分,减少该部分水分气化吸热而的热量消耗 , 并提高焦炭的温度 , 从而提高高炉煤气除尘干燥进口的煤气温度。
2.2 缩短脉冲周期一旦高炉出现长时间低顶温的状态,干法除尘器的运行就会面临巨大的考验,当干法除尘器进口煤气温度长时间低于80℃时,即出现潮灰大量黏附在滤袋表面,导致滤袋透气性降低,荒、净煤气压差增大,损坏滤袋,严重时可以导致花板变形、损坏,存在很大的安全风险。
钢铁冶金小论文

论中国钢铁冶金技术发展史姓名:杨帅班级:姓名:杨帅班级:1010级建筑工程技术一班级建筑工程技术一班 系部:材料与工程系系部:材料与工程系我虽然不是钢铁冶金专业的学生,但是通过选修本课程,不仅使我自己加深了对钢铁冶金技术的了解,在一定程度上弥补了我对钢铁冶金认识的空白,同时,使我对中国钢铁冶金技术发展史有了更具体的了解与认识。
冶金是研究如何经济地从矿石或其他原料中提取金属或金属化合物,并采用各种加工方法制成具有一定性能的金属材料的科学。
冶金工业的发展是伴随人类活动而一步步发展起来的,可归结为:石器→青铜器→铁器→工业化石器→青铜器→铁器→工业化((钢铁) →信息社会信息社会((多种新材料多种新材料) )中国作为世界文明古国,钢铁的发展要远早于其他国家。
中国古代炼钢方法可分为两类。
一是以块炼铁为原料,采用渗碳技术使其成钢。
二是以生铁为原料,采取脱碳技术使其成钢。
钢。
二是以生铁为原料,采取脱碳技术使其成钢。
早期出现的大量钢制品主要是用第一种方法炼成,就是把块炼铁直接放在炽热的木炭上加热,渗碳木炭上加热,渗碳((在高温下活性碳原子渗入铁的表面在高温下活性碳原子渗入铁的表面 , , ,使含碳量增加使含碳量增加使含碳量增加 ) ) ),再经,再经反复锻打而成。
反复加热煅打的次数越多,钢件越硬,由十次,三十次,五十次增至近百次从而得到所谓的“百炼钢”。
这就是百炼成钢工艺的起源。
多次反复锻打可排除钢中夹杂物(铁矿石中的脉石成分)多次反复锻打可排除钢中夹杂物(铁矿石中的脉石成分),减少残留夹杂物的尺寸的尺寸 ,从而使其成分趋于均匀,组织趋于致密,细化晶粒,改善钢的性能。
古代人们虽然不知道为什么打的次数越多,古代人们虽然不知道为什么打的次数越多,钢件越硬,钢件越硬,但是这种锤炼技术却一直延续下来了。
延续下来了。
在掌握冶炼块炼铁后不久,又学会了生铁冶铸,是把炼炉加高,强化地鼓风,使竖炉里的氧化还原反应更充分,使竖炉里的氧化还原反应更充分,炼炉的温度也有相应的提高。
冶金工程硕士毕业论文
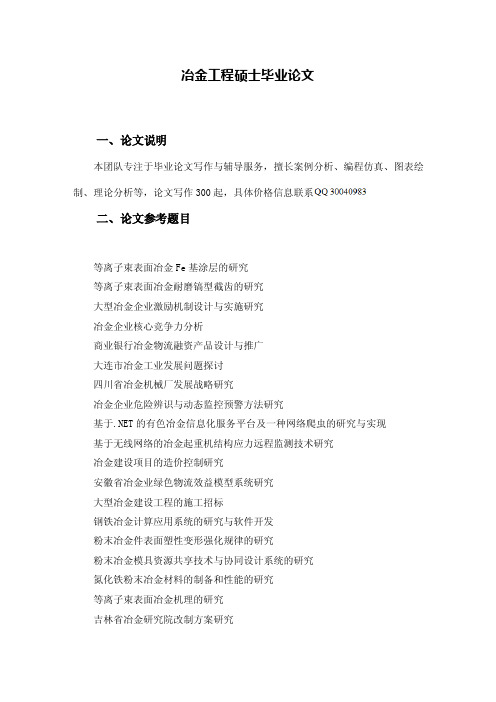
冶金工程硕士毕业论文一、论文说明本团队专注于毕业论文写作与辅导服务,擅长案例分析、编程仿真、图表绘制、理论分析等,论文写作300起,具体价格信息联系二、论文参考题目等离子束表面冶金Fe基涂层的研究等离子束表面冶金耐磨镐型截齿的研究大型冶金企业激励机制设计与实施研究冶金企业核心竞争力分析商业银行冶金物流融资产品设计与推广大连市冶金工业发展问题探讨四川省冶金机械厂发展战略研究冶金企业危险辨识与动态监控预警方法研究基于.NET的有色冶金信息化服务平台及一种网络爬虫的研究与实现基于无线网络的冶金起重机结构应力远程监测技术研究冶金建设项目的造价控制研究安徽省冶金业绿色物流效益模型系统研究大型冶金建设工程的施工招标钢铁冶金计算应用系统的研究与软件开发粉末冶金件表面塑性变形强化规律的研究粉末冶金模具资源共享技术与协同设计系统的研究氮化铁粉末冶金材料的制备和性能的研究等离子束表面冶金机理的研究吉林省冶金研究院改制方案研究UMG-Si制备过程中湿法冶金除B分子动力学模拟及实验研究冶金企业技术创新系统协同评价研究云南冶金集团供应链管理系统规划研究冶金复合双金属管界面力学性能研究冶金级硅直接制备太阳能级硅预处理实验研究等离子冶金梯度碳化物高强韧截齿刀头组织性能研究激光淬火铁基粉末冶金材料摩擦磨损性能研究某冶金企业钢管生产线自动化改造实现基于安全检查表的冶金企业安全文化评价研究冶金级硅造渣精炼除硼动力学研究粉末冶金粉尘对呼吸系统健康影响大型冶金企业工程建设进度控制研究多功能数控等离子束表面冶金实验设备的研制基于BP神经网络的冶金工艺专家系统的研究与实现基于循环经济的天津冶金企业节能减排对策研究湿法冶金置换过程的建模与优化湿法冶金置换过程建模与优化控制首钢冶金废渣工程项目风险管理研究冶金地质单位安全管理信息化系统研究与设计磷吸杂改善产业化冶金多晶硅太阳电池性能氯化物熔盐去除冶金级硅中杂质硼的研究ABB公司中国区冶金服务业务的营销策略研究加入WTO后国有冶金企业防止人才流失对策研究生物冶金技术在R公司应用的可行性研究基于数据的湿法冶金全流程优化控制补偿方法的研究国内有色冶金项目EPC总承包商的质量保修管理分析鸿泰公司粉末冶金制品市场拓展策略研究基于平衡计分卡的S冶金矿业集团公司绩效评价体系的构建冶金级硅造渣氧化精炼除硼研究鞍山市冶金行业发展对策研究低硅烧结矿分形结构及冶金性能的研究冶金废渣对低阶煤低温催化干馏影响的研究大型冶金企业风险管控研究铜对磷硼铁基粉末冶金材料摩擦磨损性能的影响冶金项目风险管理的技术手段研究粉末冶金汽车同步器齿毂精密成形模具研究粉末冶金模具PDM系统的研究开发冶金炉渣梯级利用技术研究大型冶金工程项目施工阶段风险控制与管理研究铜冶金城市铜产业链发展模式研究基于神经网络的双辉等离子表面冶金仿真预测系统的开发中国冶金进出口总公司预算管理研究湿法冶金浓密洗涤过程控制策略研究基于胜任力的有色冶金设计院技术人员人力资源管理研究铁氮粉末冶金材料的应用探索与铁氮相变的理论研究基于UG的粉末冶金模具CAD系统精整工艺模块的研究与开发基于内部控制的有色冶金企业风险评估体系研究包头冶金工业发展对策研究基于人工神经网络冶金产品价格的决策与分析粉末冶金钼板轧制工艺有限元模拟与试验研究基于UG的粉末冶金模具成形模CAD系统的开发研究冶金熔化过程中利用电极烧结废料增硅增碳的实验研究基于安全人机工程理论的钢铁冶金天车作业安全研究磷、硼对铁基粉末冶金材料摩擦磨损特性的影响西门子变频器在华营销策略研究基于QHSE的冶金建设项目管理研究大型冶金建设工程项目进度控制研究上市公司环境信息含量问题研究基于环境信息披露的我国冶金行业上市公司绿色竞争力评价研究湿法冶金全流程建模与优化湿法冶金浸出过程建模与优化高性能粉末冶金渐开线直齿轮的研究与开发基于UG的粉末冶金工艺性判别系统开发与研究铁基粉末冶金零件的性能改善冶金过程数据处理方法和遗传算法研究碱性液腐蚀冶金多晶硅太阳电池表面织构的研究熔融态冶金级硅中杂质的挥发去除行为研究基于SolidWorks的粉末冶金拉下式成形模CAD系统的开发原位合成莫来石晶须韧化微波冶金用刚玉—莫来石耐火材料的研究湿法冶金浓密洗涤过程建模及关键变量预测湿法冶金铜萃过程铜组分含量预测方法的研究湿法冶金铜萃取过程的建模与优化基于UG的参数化粉末冶金模具图形库的研究与开发高强度、高复杂度粉末冶金齿轮的设计及制备粉末冶金模具CAD系统开发及其关键技术的研究冶金行业烟气特性及其除尘器的选型研究冶金重型车车架结构优化方法的研究热锻条件下大型钢锭内部主要冶金缺陷的演变大型冶金工程建设项目的招标研究制备微冶金结合涂层的电弧喷涂方法工艺研究Al-P系中间合金粉末冶金合成工艺研究19世纪下半期俄国煤炭业和黑色冶金业发展述略某航空发动机粉末冶金涡轮盘低循环疲劳寿命研究重钢铁矿石冶金性能及合理经济配矿的研究冶金硅太阳电池的欧姆接触制作及质量分析基于JSP技术的冶金设备寿命周期管理系统的研究基于装配模型的粉末冶金成形模CAD系统的开发粉末冶金316L不锈钢的制备及性能研究冶金工程EPC项目进度管理研究莱芜市Y粉末冶金厂1万吨粉末冶金制品项目可行性分析冶金建设工程质量评判与信息管理方法研究粉末冶金闸瓦的研究与设计120T冶金重载运输车有限元分析及关键部件优化冶金企业内部铁路运输区域安全监控关键技术研究提高汉钢烧结矿冶金性能试验研究冶金设备检修维护企业人力资源管理基于数据驱动的生物氧化冶金过程控制及优化研究云南冶金科研中心绿色建筑技术应用策略研究粉末冶金热锻连杆的有限元分析单面焊陶瓷衬垫熔渣与熔池金属冶金行为研究熔体发泡法与粉末冶金法制备多孔泡沫钢工艺研究粉末冶金多元增强钛基复合材料的制备、微观结构及力学性能利用低品位、高含碳冶金尘泥制备金属化球团研究镍包铜复合粉末的制备工艺及其粉末冶金行为的研究JQ型无铅汽油发动机粉末冶金摇臂镶块的研制冶金管理系统的设计与实现冶金企业铁路智能运输调度系统的设计与实现冶金焦化有毒物质职业健康风险评估研究电子束熔炼冶金硅中杂质蒸发行为研究泡沫铝芯三明治的粉末冶金制备及其性能研究冶金企业危险源辨识与评价双层辉光离子渗含钛表面冶金高速钢及其摩擦磨损特性的研究含氮铁基粉末冶金材料制备的热力学分析及性能研究基于钻石模型的江油冶金机械产业集群发展对策研究冶金级硅精炼除硼研究粉末冶金铝基固体自润滑材料的研究我国冶金企业R&D组织设计研究真空冶金法提纯高铝掺杂单晶硅尾料湿法冶金铜萃取组分含量软测量方法研究冶金项目施工进度控制优化及管控系统研究民国时期冶金学术组织探析湿法冶金浸出过程建模与优化温压粉末冶金模具工作状况的数值模拟钙脱氧的氧化物冶金钢中夹杂物及大线能量焊接性能研究粉末冶金法制备Fe-锰锌铁氧体基软磁材料的研究中国二十二冶集团A类冶金工程项目管理模式优化研究冶金硅太阳电池的P-N结制造工艺分析与优化冶金材料微波介电性能变温测试技术研究冶金工业出版社人力资源规划研究中间包冶金过程模拟与结构优化闭孔泡沫铝与铝及铝合金覆板的冶金结合等离子束表面冶金Fe基涂层的研究等离子束表面冶金耐磨镐型截齿的研究大型冶金企业激励机制设计与实施研究冶金企业核心竞争力分析商业银行冶金物流融资产品设计与推广大连市冶金工业发展问题探讨四川省冶金机械厂发展战略研究冶金企业危险辨识与动态监控预警方法研究基于.NET的有色冶金信息化服务平台及一种网络爬虫的研究与实现基于无线网络的冶金起重机结构应力远程监测技术研究冶金建设项目的造价控制研究安徽省冶金业绿色物流效益模型系统研究大型冶金建设工程的施工招标钢铁冶金计算应用系统的研究与软件开发粉末冶金件表面塑性变形强化规律的研究基于供应链的有色冶金企业原料供应管理系统设计中国冶金建设集团公司发展战略研究航空冶金特种工艺质量控制研究等离子原位冶金碳化钨结晶过程研究改善昆钢焦炭冶金性能研究有色冶金职业技能鉴定管理信息系统设计与实现钨钼冶金过程中氨氮废水的治理研究四川省有色冶金研究院中长期战略研究天津天铁冶金集团有限公司建设工程项目管理研究创新型冶金企业持续创新重大风险动态分析和管理机制研究钢铁冶金企业大宗材料采购管理系统的设计与实现冶金多晶硅的电学性能研究粉末冶金精密成型压机新型模架设计与优化邯钢高炉原燃料冶金性能对喷煤量影响的研究双层铁基粉末冶金材料组织与性能研究离子液体在黄铜矿湿法冶金中的应用研究准格尔矸石电厂CFB灰中提取冶金级氧化铝工艺研究高碱度CASMTN六元熔融还原炉渣冶金性能研究Al_2O_3/SiO_2比对烧结矿成矿特性与冶金性能影响研究200T全自动粉末冶金压机的研制基于物理冶金学和BP网络的热轧带钢组织—性能的模拟和预测冶金余热回收节能方案的研究冶金法提纯工业硅的研究冶金法多晶硅铜沉淀行为研究铁基粉末冶金材料感应烧结过程研究在升级冶金级硅衬底上用ECR-PECVD沉积多晶硅薄膜冶金法多晶硅中的缺陷及磷吸杂实验研究粉末冶金钼管热挤压工艺基础研究冶金企业煤气爆炸危险区域划分及泄漏扩散模拟冶金熔体表面性质分析的数字成像检测系统研究冶金炼钢工业厂房施工工期进度管理工业硅的冶金法提纯研究南钢高炉炉料冶金性能及炉渣粘度研究信息技术环境下中职冶金专业课研究性学习的实践探索大型冶金建设项目的进度控制和预测模型中国冶金设备总公司项目管理模型冶金高炉工程进度控制研究基于人力资本定价的企业中层经理薪酬激励研究粉末冶金钢—铜合金双金属翻边轴瓦材料的研制耐液锌腐蚀粉末冶金材料的研究粉末冶金摩擦材料特征摩擦组元与铜基体的界面及其对摩擦磨损机理影响研究用低品位矿和钼渣湿法冶金制备钼酸盐的研究粉末冶金材料结合面特征参数识别与研究粉末冶金法制备Al_2O_3/Cu复合材料及其变形组织与性能的研究冶金过程中统计模式识别—神经网络优化程序的研制粉末冶金法制备SiCw/AZ91复合材料研究利用冶金渣余热催化气化城市生活垃圾的试验研究双膜工艺深度处理冶金综合废水中试研究粉末冶金Fe-2Ni-1Cu-0.6C合金烧结助剂的研究氧化物冶金工艺对热轧EH40钢板大线能量焊接性能的影响粉末冶金钛合金及多孔钛研究砷污染治理及砷资源回收利用的清洁生产新技术研究冶金法制备高纯硅工艺研究铁矿石冶金性能测控网络系统的研究数字视频技术在冶金过程监控中的应用合金元素对粉末冶金Mg合金组织和性能的影响铝合金激光焊接冶金研究火法冶金工艺处理电子线路板并富集贵稀金属的试验研究NdB_6合成及多元(TiB+TiC+Nd_2O_3)/Ti的粉末冶金工艺制备技术高能球磨粉末冶金制备工艺对Al基复合材料组织与性能的影响机械合金化-粉末冶金SiCp/6061Al复合材料的制备工艺及性能研究国有企业改革过程中的政府职能定位问题研究湿法冶金浸出过程监测与故障追溯聚晶立方氮化硼刀具硬切削粉末冶金气门座圈的研究冶金矿山矿井安全现状模糊综合评价研究PTA原位合成含TiB_2金属陶瓷涂层的冶金过程及组织控制粉末冶金制备钛基复合材料的组织与机械性能的研究准高速列车用铜基粉末冶金闸片材料的研制鄂尔多斯电力冶金股份有限公司内部控制自我评价问题研究放电等离子烧结WC颗粒增强铁基粉末冶金材料及其性能研究冶金工业企业建筑环境色彩改造研究冶金石灰竖窑燃烧过程的仿真模拟研究冶金工业废渣类添加剂对燃煤助燃脱硝的影响及机理研究固定合同总价模式下冶金工程项目成本管理研究粉末冶金A1CuMgSi材料的制备工艺及性能研究真空感应熔炼和定向凝固提纯冶金级硅研究冶金行业机电工程项目成本控制分析与研究冶金法去除工业硅中杂质的研究基于模糊粗糙理论及智能优化算法的冶金备件采购优化研究鲁中冶金矿业集团公司发展战略研究烧结矿冶金性能测控系统的设计铁矿石冶金性能测控系统设计及其智能炉温控制算法研究银氧化锡电接触材料组织性能研究湿法冶金浓密洗涤过程监测与故障诊断粉末冶金烧结钢用渗铜剂的成分与性能研究稀土添加对粉末冶金钛合金组织与性能影响研究钨湿法冶金离子交换新工艺的研究粉末冶金结合微弧氧化制备医用钛基复合材料及其性能表征江苏Metallurgy机械公司目标集聚战略研究泡沫铝粉末冶金复合加热法制备技术的试验研究高砷冶金废料的回收与综合利用冶金工业厂区绿色建筑技术应用策略研究MoS_2在铁基粉末冶金摩擦材料中的作用机理云南冶金集团管控模式优化研究粉末冶金法制备泡沫铝材料的工艺研究基于VTK的冶金流动过程仿真研究粉末冶金法制备新型Si-Al电子封装材料的研究粉末冶金法制备Cu/C复合材料的性能研究物理冶金多晶硅太阳电池三层氮化硅薄膜的设计及研制等离子束表面冶金涂层的耐腐蚀性研究PCBN刀具切削粉末冶金气门座圈切削性能研究单向压制时粉末冶金台阶零件的密度分布规律研究利用含钛冶金渣制取光催化材料的实验研究AZ31B镁合金焊接冶金性能研究冶金桥式起重机静动态特性和疲劳寿命分析粉末冶金法制备β-SiCp/Al电子封装材料工艺与性能研究等离子刻蚀周边工艺与冶金硅太阳电池的漏电粉末冶金气门座的合金设计及组织性能模糊神经网络控制技术在粉末冶金电炉控制系统中的应用研究双辉等离子表面冶金技术制备Fe-Al-Cr合金层及其性能研究褐煤制备冶金还原气的研究美国对华反补贴调查的损害认定机制研究利用硅片切割废料研制冶金辅料的实验研究等离子束表面冶金高硅涂层研究粉末冶金法制备Cu/TiB_2复合材料及其性能的研究中国有色(沈阳)冶金机械有限公司国际创业战略研究压力容器用钢氧化物冶金技术研究Mg_2B_2O_(5w)/ZK60镁基复合材料粉末冶金法制备及性能研究冶金尘泥含碳球团还原动力学研究物理法提纯冶金级硅及其机理研究超纯铁粉制备粉末冶金铁基结构材料及其渗碳处理性能研究冶金法制备多晶硅的晶体生长及其杂质缺陷研究氧化镁真空炭热还原物料制备研究粉末冶金法制备生物医用多孔钛及性能研究等离子束表面冶金层的耐空蚀性能研究冶金企业内部铁路运输地面安全控制关键技术研究宁夏英力特河滨冶金有限公司营销策略研究国有大型冶金企业技术创新体制建设研究Nox在三相流化床中催化氧化难选冶金精矿循环条件的研究夹杂物对粉末冶金涡轮盘应力强度因子及裂纹扩展寿命的影响研究粉末冶金Fe-C-Cu-Cr-Mn材料组织与性能研究粉末冶金Ti-47Al-2Nb-2Cr合金高温变形行为及组织演变规律研究粉末冶金FGH4169高温合金的制备、组织、力学性能及热加工性能研究合金元素对粉末冶金镁锌复合材料组织和性能的影响北票市粉末冶金产业集群升级对策研究湿法冶金置换过程监测与故障追溯冶金企业铁路运输编组取送调车作业计划编制优化冶金企业生产与物流作业管理决策支持系统湿法冶金过程中若干金属富集分离技术的应用研究高强高耐磨粉末冶金热作模具(GFR)材料组织设计与制备泡沫铝的粉末冶金制备方法及其相关性能研究回转窑焙烧优质活性冶金石灰的质量研究烧结工艺对铜基粉末冶金摩擦材料性能的影响基于核心竞争力的国有冶金企业集团战略管理模式研究球磨/粉末冶金法制备AZ91镁合金组织及显微硬度的研究粉末冶金原位合成Al-Cu合金的组织与性能研究第三冶金公司数据监控系统的设计与实现电弧熔炼—粉末冶金制备Fe掺杂高锰硅化物热电材料造球技术在冶金再生资源中的应用研究大型冶金建设项目管理的研究——宝钢2~#彩涂工程全过程管理中国冶金科工股份有限公司投资价值分析深孔钻机粉末冶金刹车块研究微细铬铁粉对铁基粉末冶金材料性能的影响重钢五流方坯连铸中间包控流装置及冶金效果的研究大型冶金工程施工组织设计的应用研究汽车同步器粉末冶金同步环用湿式铜基摩擦材料粉末冶金法制备Ni包覆TiC颗粒增强H13钢复合材料性能的研究短碳纤维表面处理及粉末冶金法制备Cf/Al复合材料的研究纳米金属合金粉体制备及其粉末冶金特性研究(Fe-Ni与W-Ni-Fe纳米合金制备研究)高等职业学校高技能人才培养研究高校科技创新团队建设研究铬对铜基粉末冶金材料摩擦磨损性能的影响基于抽样模拟技术的有色冶金配料过程优化方法研究大系统理论在钢铁冶金加热过程中的应用研究冶金动力企业的备件管理研究K417G热裂纹粉末冶金修复技术研究重金属湿法冶金过程钙镁结晶的基础相化学研究宁夏英力特河滨冶金有限公司高纯硅铁市场竞争力提升的对策研究基于分段形态表示的冶金能源缺失数据填补铁在铜基粉末冶金摩擦材料中的作用冶金铁矿企业提升质量管理竞争力的研究与实践冶金行业喷印标记执行机构及其控制系统的研制核电槽楔铜合金电真空冶金及成型工艺的研究粉末冶金反应合成碳化钒颗粒增强铁基复合材料制备工艺基础研究粉末冶金渗铜钢力学性能与摩擦磨损性能研究中国第三冶金建设公司干部管理研究合金元素对粉末冶金低合金钢性能和组织的影响研究基于SOA的冶金行业检化验信息系统的设计与实现重钢LF炉品种钢精炼渣料配方优化及冶金性能研究Fe-Mn-C粉末冶金低合金钢粉的预混合制备研究粉末冶金电加热烧结炉的温度控制系统电渣冶金炉渣成分与物相的变化研究粉末冶金TiAl合金的包套轧制工艺及其热处理研究粉末冶金铜基摩擦材料制备及摩擦学性能研究粉末冶金温压高性能铁基材料的研制粉末冶金纳米羟基磷灰石—钛复合材料的制备及生物活性制备工艺对铁基粉末冶金航空刹车材料组织与性能的影响铜基粉末冶金摩擦材料基体及其摩擦锰锌铁氧体软磁复合材料的粉末冶金工艺研究粉末冶金法制备Nb_3Al超导体及其超导性能研究粉末冶金法制备纳米金刚石/铜基复合材料及其性能研究八钢高炉入炉原料的冶金性能及配料优化研究高温冶金炉煤气爆炸特性研究粉末冶金法制备硼酸镁晶须增强镁基复合材料的研究钨钼分离理论及新工艺研究非均相含钛冶金熔渣流变特性及导电性研究热处理对粉末冶金Ti-47Al-2Cr-2Nb-0.2W合金显微组织及力学性能的影响SDM冶金设计公司的发展战略研究转底炉处理冶金含锌尘泥的理论分析及实验研究冶金烧结除尘灰气力输送试验与应用新民冶金配料厂成本管理信息系统设计与开发熔体处理对提高高性能铝材冶金质量和力学性能的作用研究冶金行业上市公司股利政策的实证研究——以重钢股份公司为例矿产资源企业发展战略研究鞍山铁塔集团冶金渣公司组织再造分析深孔钻机用铜基粉末冶金刹车片材料的研究电子束熔炼提纯冶金级硅工艺研究高速铁路用Cu-Fe粉末冶金刹车材料的研究包套轧制—粉末冶金法制备泡沫铝夹心板材料的研究粉末冶金法制备Ni-Co-Al系高温合金的摩擦学性能研究NbC颗粒增强45CrMoV粉末冶金复合材料的制备与性能研究气基直接还原竖炉用氧化球团的制备及其冶金特性研究川威LF炉精炼渣的组成及冶金性能的研究昆钢LF炉精炼渣的组成及冶金性能的研究辽宁冶金技师学院办公自动化系统的设计与实现粉末冶金制备Cu/Invar电子封装复合材料的研究有色冶金污泥的稳定化/固化处理研究粉末轧制及相关粉末冶金方法制取变形镁合金板带材的研究我国经济过剩运行下冶金行业发展的对策研究电磁净化技术理论及工艺研究吉林电子信息职业技术学院冶金实训中心的成本控制研究耐高浓度铁离子的菌种驯化及其浸矿实验研究粉末冶金钼合金热锻的性能和显微组织研究基于改进GTD法的冶金煤气流量缺失数据填补小模数弧齿锥齿轮粉末冶金成形齿面的设计与模具制作冶金企业铁路运输取送车优化调度方法研究能源预测及能源优化技术在冶金企业中的应用研究国内冶金行业继续教育现状的调查与统计分析冶金设备用宽温铁基固体自润滑复合材料的研究与制备。
冶金工程毕业论文文献综述
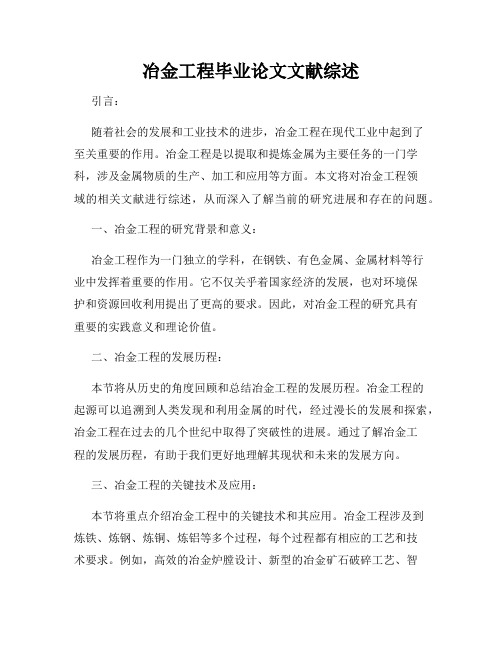
冶金工程毕业论文文献综述引言:随着社会的发展和工业技术的进步,冶金工程在现代工业中起到了至关重要的作用。
冶金工程是以提取和提炼金属为主要任务的一门学科,涉及金属物质的生产、加工和应用等方面。
本文将对冶金工程领域的相关文献进行综述,从而深入了解当前的研究进展和存在的问题。
一、冶金工程的研究背景和意义:冶金工程作为一门独立的学科,在钢铁、有色金属、金属材料等行业中发挥着重要的作用。
它不仅关乎着国家经济的发展,也对环境保护和资源回收利用提出了更高的要求。
因此,对冶金工程的研究具有重要的实践意义和理论价值。
二、冶金工程的发展历程:本节将从历史的角度回顾和总结冶金工程的发展历程。
冶金工程的起源可以追溯到人类发现和利用金属的时代,经过漫长的发展和探索,冶金工程在过去的几个世纪中取得了突破性的进展。
通过了解冶金工程的发展历程,有助于我们更好地理解其现状和未来的发展方向。
三、冶金工程的关键技术及应用:本节将重点介绍冶金工程中的关键技术和其应用。
冶金工程涉及到炼铁、炼钢、炼铜、炼铝等多个过程,每个过程都有相应的工艺和技术要求。
例如,高效的冶金炉膛设计、新型的冶金矿石破碎工艺、智能化的冶金制造过程控制等等。
同时,这些技术的应用也涵盖了冶金材料的应用领域,如航空航天、汽车制造、电子工业等,对促进工业的发展和提高产品质量起到了重要的作用。
四、冶金工程研究的热点领域:本节将介绍当前冶金工程研究的热点领域。
随着科技的发展,冶金工程也在不断演进和创新。
例如,基于大数据和人工智能的冶金工程优化、绿色冶金技术的研究、冶金废料的资源化利用等等。
这些新领域的涌现为冶金工程的未来发展提供了新的思路和机遇。
五、冶金工程研究中存在的问题和挑战:本节将对当前冶金工程研究中存在的问题和挑战进行讨论。
虽然冶金工程在过去几十年取得了巨大的进步,但仍然面临着一些困难和挑战,如高能耗、重金属污染、资源短缺等。
了解这些问题有助于我们认识到冶金工程研究中的瓶颈,并寻找解决方案。
【工程】冶金工程毕业设计

【关键字】工程冶金工程毕业设计篇一:冶金专业毕业设计优秀范文摘要本文是以白钨精矿为原料年产1000吨APT(仲钨酸铵)生产车间的设计说明书。
按照一般有色冶金生产车间设计的步骤,文章首先介绍了APT生产的的现状;结合原料特征,通过对APT整个工艺过程生产方法的比较,选择了NaOH高压浸出分解白钨精矿—离子交换法除杂和转型—选择沉淀法分离钨钼—蒸发结晶生产APT;通过对各生产工序金属平衡、物料平衡计算和设备选型,确定了各工序所需原料的量和设备的型号、规格和数目;并进行了合理的车间配置;通过分析生产过程中工业三废的产生和危害,提出了三废处理的方案;根据生产过程需要,对车间进行了劳动定员;进而对整个工艺过程进行了技术经济分析,计算结果表明本设计所采用工艺流程技术上可行,经济上合理。
「关键词」白钨精矿NaOH高压浸出离子交换APT 设计AbstractThe specification is a workshop of 1000t/y Ammonium paratungstate(APT) produced with scheelite concentrates. Following the general design steps of nonferrous metallurgy workshop, the present situation of the APT production was first presented. According to the characteristics of the raw material , technological process of sodium hydroxide(NaOH) leaching at high pressure—ion exchange—selectively precipitation to separate Mo—evaporation and crystallization process was selected as the process of APT production. The quantity of various materials in every process were fixed up and the corresponding equipments were designed or selected(include the type, size and number) originated from the result of calculating of the balance of metal and matter. The workshop is reasonably designed. The strategy of dealing with the industrial waste was proposed following the analysis of the source and the harm of the waste. The work force was arranged according to the requirement of producing process. At last, the economic target was analyzed. All these results shows that the process of this design is reasonable and economical.Keywords: Scheelite concentrates; sodium hydroxide leaching at high pressure; ion exchange; ammonium paratungstate; design.第一章文献综述1.1 钨冶金概况自1781年由瑞典化学家舍勒发现以来,钨以其具有熔点高、硬度大、耐磨和耐腐蚀等优良性能而得到广泛应用,在冶金机械、石油化工、航空航天和国防工程等诸多领域中有着极其重要的地位。
- 1、下载文档前请自行甄别文档内容的完整性,平台不提供额外的编辑、内容补充、找答案等附加服务。
- 2、"仅部分预览"的文档,不可在线预览部分如存在完整性等问题,可反馈申请退款(可完整预览的文档不适用该条件!)。
- 3、如文档侵犯您的权益,请联系客服反馈,我们会尽快为您处理(人工客服工作时间:9:00-18:30)。
. . . . . . 资.料 . .. 毕 业 课 题
课题名称: 浅 议 连 铸 坯 质 量 控 制
学 号 姓 名 专业班级 指导教师
2014年 3 月 9 日. . . .
. . 资.料 . .. 目 录 目 录.............................................1 摘 要.............................................2 ⒈ 连铸坯纯净度与产品质量..........................3 1.1纯净度与质量的关系............................3 1.2提高纯净度的措施..............................3 ⒉连铸坯的表面质量.................................4 2.1表面裂纹......................................4 2.2表面夹渣......................................5 2.3皮下气泡与气孔................................6 ⒊连铸坯内部质量...................................6 3.1中心偏析......................................6 3.2中心疏松......................................7 3.3内部裂纹......................................7 ⒋连铸坯的外观形状.................................8 4.1鼓肚变形.....................................8 4.2菱形变形.....................................8 4.3圆铸坯变形...................................9 . . . .
. . 资.料 . .. 摘 要 连铸坯质量决定着最终产品的质量。从广义来说所谓连铸坯质量是得到合格产品所允许的连铸坯缺陷的严重程度,连铸坯存在的缺陷在允许范围以内,叫合格产品。连铸坯质量是从以下几个方面进行评价的: (1)连铸坯的纯净度:指钢中夹杂物的含量,形态和分布。 (2)连铸坯的表面质量:主要是指连铸坯表面是否存在裂纹、夹渣及皮下气泡等缺陷。连铸坯这些表面缺陷主要是钢液在结晶器内坯壳形成生长过程中产生的,与浇注温度、拉坯速度、保护渣性能、浸入式水口的设计,结晶式的内腔形状、水缝均匀情况,结晶器振动以及结晶器液面的稳定因素有关。 (3)连铸坯的内部质量:是指连铸坯是否具有正确的凝固结构,以及裂纹、偏析、疏松等缺陷程度。二冷区冷却水的合理分配、支撑系统的严格对中是保证铸坯质量的关键。 (4)连铸坯的外观形状:是指连铸坯的几何尺寸是否符合规定的要求。与结晶器内腔尺寸和表面状态及冷却的均匀程度有关。 本文从以上四个方面对实际生产中连铸坯的质量控制采取的措施进行说明。 . . . .
. . 资.料 . .. ⒈连铸坯纯净度度与产品质量 1.1纯净度与质量的关系 纯净度是指钢中非金属夹杂物的数量、形态和分布。与模铸相比,连铸的工序环节多,浇注时间长,因而夹杂物的来源范围广,组成也较为复杂;夹杂物从结晶器液相穴内上浮比较困难,尤其是高拉速的小方坯夹杂物更难于排除。夹杂物的存在破坏了钢基体的连续性和致密性。大于50μm的大型夹杂物往往伴有裂纹出现,造成连铸坯低倍结构不合格,板材分层,并损坏冷轧钢板的表面等,对钢危害很大。夹杂物的大小、形态和分布对钢质量的影响也不同,如果夹杂物细小,呈球形,弥散分布,对钢质量的影响比集中存在要小些;当夹杂物大,呈偶然性分布,数量虽少对钢质量的危害也较大。 例如:从深冲钢板冲裂废品的检验中发现,裂纹处存在着100~300μm不规则的CaO-Al2O3和Al2O3的大型夹杂物。 再如,由于连铸坯皮下有Al2O3
夹杂物的存在,轧成的汽车薄板表面出现黑线缺陷,
导致薄板表面涂层不良。 还有用于包装的镀锡板,除要求高的冷成型性能外,对夹杂物的尺寸和数量也有相应要求。国外生产厂家指出,对于厚度为0.3mm的薄钢板,在1m2面积内,粒径小于50μm的夹杂物应少于5个,才能达到废品率在0.05%以下,即深冲2000个DI罐,平不到1个废品。可见减少连铸坯夹杂物数量对提高深冲薄板钢质量的重要性。 对于极细的钢丝(如直径为0.01~0.25mm的轮胎钢丝)和极薄钢板(如厚度为0.025mm的镀锡板)中,其所含夹杂物尺寸的要求就可想而知了。此外,夹杂物的尺寸和数量对钢质量的影响还与铸坯的比表面积有关。一般板坯和方坯单位长度的表面积(S)与体积(V)之比在0.2~0.8。随着薄板与薄带技术的发展,S/V可达10~50,若在钢中的夹杂物含量相同情况下,对薄板薄带钢而言,就意味着夹杂物更接近铸坯表面,对生产薄板材质量的危害也越大。所以降低钢中夹杂物就更为重要了。
1.2提高纯净度的措施 提高钢的纯净度就应在钢液进入结晶器之前,从各工序着手尽量减少对钢液的污染,并最大限度促使夹杂物从钢液中排除。为此应采取以下措施: ⑴无渣出钢。转炉应挡渣出钢;电炉采用偏心炉底出钢,阻止钢渣进入盛钢桶。 ⑵根据钢种的需要选择合适的精炼处理方式,以纯净钢液,改善夹杂物的形态。 ⑶采用无氧化浇注技术。经过精炼处理后的钢液氧含量已降到20×10-6以下;在盛钢桶→中间罐→结晶器均采用保护浇注;中间罐使用双层渣覆盖剂,钢液与空气隔绝,避免钢液的二次氧化。 ⑷充分发挥中间罐冶金净化器的作用。采用吹Ar搅拌,改善钢液流动状况,消除中间罐死区;加大中间罐容量和加深熔池深度,延长钢液在中间罐停留时间,促进夹杂物上浮,进一步净化钢液。 ⑸)连铸系统选用耐火度高,融损小,高质量的耐火材料,以减少钢中外来夹杂物。 ⑹充分发挥结晶器的钢液净化器和铸坯表面质量控制器的作用。选用的浸入式水口应有合理的开口形状和角度,控制注流的运动,促进夹杂物的上浮分离;并辅以性能良好的保护渣,吸收溶解上浮夹杂净化钢液。 另外,还可以向结晶器内喂入包芯合金线,实现结晶器内微合金化,这不仅提高了合金的吸收率,而且能精确控制钢液成分,调整凝固结构,改善夹杂物形态,有利于钢. . . . . . 资.料 . .. 的质量。 ⑺采用电磁搅拌技术,控制注流的运动。计算指出,在静止状态下,大于1mm的渣粒上浮速度约100~200cm/s;而注流向下流动速度为60~10cm/s;可见结晶器液相穴内注流流股冲击区域夹杂物上浮是有困难的;有部分夹杂物很可能被凝固的树枝晶所捕集。实际上在铸坯表面以下10~20cm处往往夹杂物含量较高。安装电磁制动器可以抑制注流的运动,促进夹杂物上浮,提高钢液的纯净度。
⒉连铸坯的表面质量 连铸坯表面质量的好坏决定了铸坯在热加工之前是否需要精整,也是影响金属收得率和成本的重要因素,还是铸坯热送和直接轧制的前提条件。连铸坯表面缺陷形成的原因较为复杂,但总体来讲,主要是受结晶器内钢液凝固所控制。
2.1表面裂纹
表面裂纹就其出现的方向和部位,可以分为面部纵裂纹与横裂纹;角部纵裂纹与横裂纹;星状裂纹等。 2.1.1纵向裂纹
纵向裂纹在板坯多出现在宽面的中央部位,方坯多发生在棱角处。表面纵裂纹直接影响钢材质量。若铸坯表面存在深度为2.5mm,长度为300mm的裂纹,轧成板材后就会形成1125mm的分层缺陷。严重的裂纹深度达10mm以上,将造成漏钢事故或废品。 其实早在结晶器内坯壳表面就存在细小裂纹,铸坯进入二冷区后,微小裂纹继续扩展形成明显裂纹。由于结晶器弯月面区初生坯壳厚度不均匀,其承受的应力超过了坯壳高温强度,在薄弱处产生应力集中致使纵向裂纹。坯壳厚度不均匀还会使小方坯发生菱变,圆坯表面产生凹陷,这些均是形成纵裂纹的决定因素。 影响坯壳生长不均匀的原因很多,但关键仍然是弯月面初生坯壳生长的均 匀性,为此应采用以下措施: ⑴结晶器采用合理的倒锥度。坯壳表面与器壁接触良好,冷却均匀,可以避免产生裂纹和发生拉漏。 ⑵选用性能良好的保护渣。在保护渣的特性中粘度对铸坯表面裂纹影响最大,高粘度保护渣使纵裂纹增加。 ⑶浸入式水口的出口倾角和插入深度要合适,安装要对中,以减轻注流对铸坯坯壳的冲刷,使其生长均匀,可防止纵裂纹的产生。 ⑷根据所浇钢种确定合理的浇注温度及拉坯速度。 ⑸保持结晶器液面稳定。 ⑹钢的化学成分应控制在合适的范围。
2.1.2角部裂纹 角部纵裂纹常常发生在铸坯角部10~15mm处,有的发生在棱角上,板坯的宽面与窄面交界棱角附近部位,由于角部是二维传热,因而结晶器角部钢水凝固速度较其他部位要快,初生坯壳收缩较早,形成了角部不均匀气隙,热阻增加,影响坯壳生长,其薄. . . . . . 资.料 . .. 弱处承受不住应力作用而形成角部纵裂纹。 角部纵裂纹产生关键在结晶器。通过试验指出,倘若将结晶器窄面铜板内壁纵向加工成凹面,呈弧线状,这样在结晶器1/2高度上,角部坯壳被强制与结晶器壁接触,由此热流增加了70%,坯壳生长均匀,因而避免了铸坯凹陷和角部纵裂纹。 另外,还发现当板坯宽面出现鼓肚变形时,若铸坯窄面能随之呈微凹时,则无角部纵裂纹发生;这可能是由于窄面的凹下缓解了宽面凸起时对角部的拉应力。 小方坯的菱变会引起角部纵裂纹。为此结晶器水缝内冷却水流分布要均匀,保持结晶器内腔的正规形状、正确尺寸、合理倒锥度和圆角半径及规范的操作工艺,可以避免角部裂纹的发生。
2.1.3横向裂纹 横向裂纹多出现铸坯的内弧侧振痕波谷处,通常是隐避看不见的。经金相检查指出,裂纹深7mm,宽0.2mm,处于铁素体网状区,也正好是初生奥氏体晶界。晶界处还有AlN或Nb(CN)的质点沉淀,因而降低了晶界的结合力,诱发了横裂纹的产生。当奥氏体晶界沉淀质点粗大,呈稀疏分布,板坯横裂纹产生的废品减少。铸坯矫直时,内弧侧受拉应力作用,由于振痕缺陷效应而产生应力集中,如果正值 脆化温度区,促成了振痕波谷处横裂纹的生成。当铸坯表面有星状龟裂纹时,由于受矫直应力的作用,以这些细小的裂纹为缺口扩展成横裂纹;若细小龟裂纹处于角部,则会形成角部横裂纹。还有,浇注高碳钢和高磷硫钢时,若结晶器润滑不好,摩擦力稍有增加也会导致坯壳产生横裂纹。减少横裂纹可从以下几方面着手: ⑴结晶器采用高频率,小振幅振动;振动频率在200~400次 ,振幅2~4mm,是减少振痕深度的有效办法。振痕与横裂纹往往是共生的,减小振痕深度可降低横裂纹的发生。 ⑵二冷区采用平稳的弱冷却,矫直时铸坯的表面温度要高于质点沉淀温度或高于γ→α转变温度,避开低延性区。 ⑶降低钢中S、O、N的含量,或加入Ti、Zr、Ca等元素,抑制C-N化物和硫化物在晶界的析出,或使C-N化物的质点变相,以改善奥氏体晶粒热延性。 ⑷选用性能良好的保护渣;保持结晶器液面的稳定。 ⑸横裂纹往往沿着铸坯表皮下粗大奥氏体晶界分布,因此可通过二次冷却使铸坯表面层奥氏体晶粒细化,降低对裂纹的敏感性,从而减少横裂纹的形成。