抗硫化返原剂PK 900对丁腈橡胶性能的影响
丁腈橡胶丙烯腈含量对丁腈橡胶

橡 胶 工 业 CHINA RUBBER INDUSTRY
2024年1月 J a n . 2 0 2 4 29
原材料·配方
丁腈橡胶丙烯腈含量对丁腈橡胶/聚氯乙烯 发泡材料性能的影响
高贺勇,郭 超*,高贺昌,张建松,吴华明
(华美节能科技集团有限公司,河北 廊坊 065903)
母胶配方(用量/份)为:NBR(变牌号) 41, PVC 59,炭 黑 N330 12,碳 酸 钙 71,氯 化 石 蜡 63,发泡剂AC 29,其他 21,合计296。
NBR/PVC发泡材料的配方如表1所示。
表1 NBR/PVC发泡材料的配方
份
Tab. 1 Formulas of NBR/PVC foaming materials phr
(2)混炼胶制备。将母胶、硫黄、氧化锌、促进 剂ZDMC在开炼机上混炼,制得混炼胶,混炼胶冷 却后待用。
(3)挤出成型。将混炼胶以条状形式喂入挤 出 机,经 口 模 挤 出 定 型 后 进 入 发 泡 烘 箱 中 进 行 硫 化发泡。 1. 5 性能测试
(1)门尼粘度:按照GB/T 1232. 1—2016进行 测试,试样质量为25 g。
越好。胶料在发泡时需要较小的粘性和较大的弹 性 来 支 撑 泡 孔 生 长[17-18]。3308E-1和2875-1配 方
混炼胶硫化发泡过程中的tanδ曲线如图2所示。
从 图1和2可 以 看 出,与3308E-1配 方 混 炼 胶
相比,2875-1配方混炼胶的最大发泡力较大,这主
要是由于2875-1配方混炼胶始终具有相对较小的
0. 19 1. 00 0. 81 22. 08 79. 68 57. 60 936. 5 82. 68
橡胶硫化
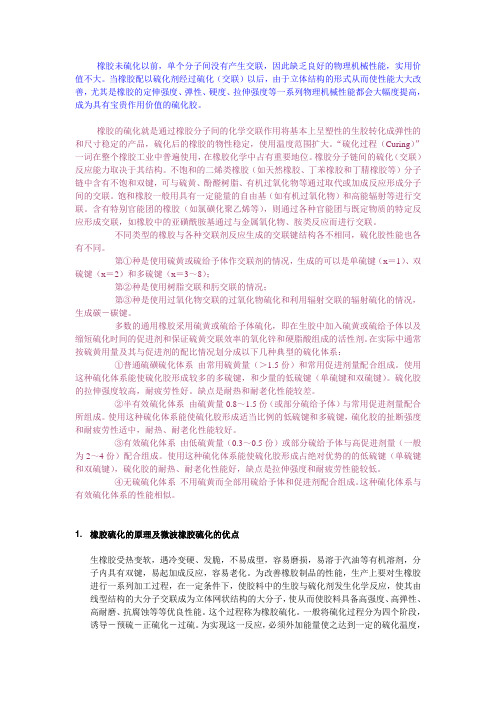
橡胶未硫化以前,单个分子间没有产生交联,因此缺乏良好的物理机械性能,实用价值不大。
当橡胶配以硫化剂经过硫化(交联)以后,由于立体结构的形式从而使性能大大改善,尤其是橡胶的定伸强度、弹性、硬度、拉伸强度等一系列物理机械性能都会大幅度提高,成为具有宝贵作用价值的硫化胶。
橡胶的硫化就是通过橡胶分子间的化学交联作用将基本上呈塑性的生胶转化成弹性的和尺寸稳定的产品,硫化后的橡胶的物性稳定,使用温度范围扩大。
“硫化过程(Curing)”一词在整个橡胶工业中普遍使用,在橡胶化学中占有重要地位。
橡胶分子链间的硫化(交联)反应能力取决于其结构。
不饱和的二烯类橡胶(如天然橡胶、丁苯橡胶和丁腈橡胶等)分子链中含有不饱和双键,可与硫黄、酚醛树脂、有机过氧化物等通过取代或加成反应形成分子间的交联。
饱和橡胶一般用具有一定能量的自由基(如有机过氧化物)和高能辐射等进行交联。
含有特别官能团的橡胶(如氯磺化聚乙烯等),则通过各种官能团与既定物质的特定反应形成交联,如橡胶中的亚磺酰胺基通过与金属氧化物、胺类反应而进行交联。
不同类型的橡胶与各种交联剂反应生成的交联键结构各不相同,硫化胶性能也各有不同。
第①种是使用硫黄或硫给予体作交联剂的情况,生成的可以是单硫键(x=1)、双硫键(x=2)和多硫键(x=3~8);第②种是使用树脂交联和肟交联的情况;第③种是使用过氧化物交联的过氧化物硫化和利用辐射交联的辐射硫化的情况,生成碳-碳键。
多数的通用橡胶采用硫黄或硫给予体硫化,即在生胶中加入硫黄或硫给予体以及缩短硫化时间的促进剂和保证硫黄交联效率的氧化锌和硬脂酸组成的活性剂。
在实际中通常按硫黄用量及其与促进剂的配比情况划分成以下几种典型的硫化体系:①普通硫磺硫化体系由常用硫黄量(>1.5份)和常用促进剂量配合组成。
使用这种硫化体系能使硫化胶形成较多的多硫键,和少量的低硫键(单硫键和双硫键)。
硫化胶的拉伸强度较高,耐疲劳性好。
缺点是耐热和耐老化性能较差。
助交联剂HVA-2对天然橡胶性能的影响_

第 3 期李秀明等.助交联剂HVA-2对天然橡胶性能的影响153助交联剂HVA-2对天然橡胶性能的影响李秀明1,邹 华1,2*,刘 军1,3(1.北京化工大学北京市新型高分子材料制备与加工重点实验室,北京 100029;2.北京化工大学弹性体材料节能与资源化教育部工程研究中心,北京 100029;3.北京化工大学北京市先进弹性体工程技术研究中心,北京 100029)摘要:研究助交联剂HVA-2在硫黄硫化体系下对天然橡胶(NR)性能的影响。
结果表明:加入助交联剂HVA-2后,NR胶料的t10延长,F max增大,硫化胶的拉伸强度、拉断伸长率和撕裂强度增大,剪切储能模量和损耗因子减小;随着老化时间的延长,硫化胶的交联密度增大;当助交联剂HVA-2用量为1份时,NR硫化胶的耐热氧老化和耐疲劳性能最好。
关键词:天然橡胶;助交联剂;耐热氧老化性能;耐疲劳性能中图分类号:TQ330.38+5;TQ332 文献标志码:A 文章编号:1000-890X(2017)03-0153-04硫黄硫化的天然橡胶(NR)具有很多优异的性能,如撕裂性能、动态疲劳性能等,因此广泛应用于轮胎、胶带等各类工业制品中。
随着工业的发展,对橡胶制品的耐热性要求越来越高,由于硫黄硫化NR的耐热氧老化性能不好,提高NR的耐热性一直是研究的热点。
助交联剂HVA-2是一种含有不饱和双键的化合物[1-2],其耐热性好,并能使硫化胶具备优良的耐屈挠疲劳性能和弹性,可以作为过氧化物硫化体系的助交联剂[3-5]。
但是,有关其在硫黄硫化体系中的应用研究报道还不多。
本工作研究助交联剂HVA-2用量对NR胶料性能的影响,旨在通过助交联剂HVA-2的使用,提高NR的耐热性,为生产耐热性优良的NR制品提供理论指导。
1 实验1.1 主要原材料NR,1#标准胶,云南天然橡胶产业股份有限公司产品;炭黑N220,青岛德固赛化学有限公司产品;助交联剂HVA-2,华星(宿迁)化学有限公司产品。
混炼工艺对丁腈橡胶性能的影响
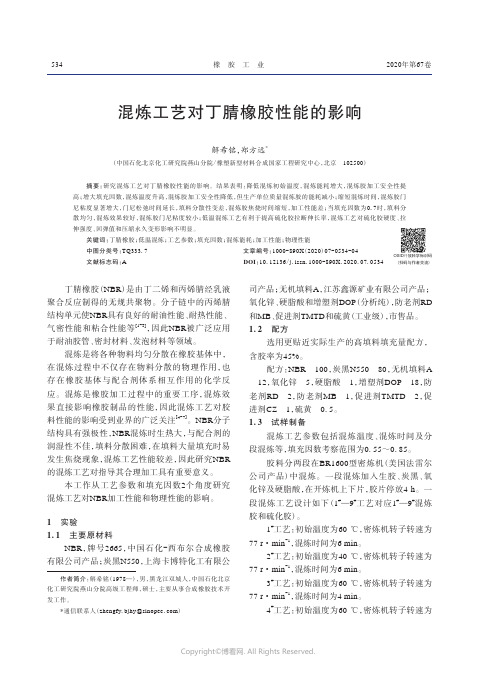
混炼工艺对丁腈橡胶性能的影响解希铭,郑方远*(中国石化北京化工研究院燕山分院/橡塑新型材料合成国家工程研究中心,北京102500)摘要:研究混炼工艺对丁腈橡胶性能的影响。
结果表明:降低混炼初始温度,混炼能耗增大,混炼胶加工安全性提高;增大填充因数,混炼温度升高,混炼胶加工安全性降低,但生产单位质量混炼胶的能耗减小;缩短混炼时间,混炼胶门尼粘度显著增大,门尼松弛时间延长,填料分散性变差,混炼胶焦烧时间缩短,加工性能差;当填充因数为0.7时,填料分散均匀,混炼效果较好,混炼胶门尼粘度较小;低温混炼工艺有利于提高硫化胶拉断伸长率,混炼工艺对硫化胶硬度、拉伸强度、回弹值和压缩永久变形影响不明显。
关键词:丁腈橡胶;低温混炼;工艺参数;填充因数;混炼能耗;加工性能;物理性能中图分类号:TQ333.7 文章编号:1000-890X(2020)07-0534-04文献标志码:A DOI:10.12136/j.issn.1000-890X.2020.07.0534丁腈橡胶(NBR)是由丁二烯和丙烯腈经乳液聚合反应制得的无规共聚物。
分子链中的丙烯腈结构单元使NBR具有良好的耐油性能、耐热性能、气密性能和粘合性能等[1-3],因此NBR被广泛应用于耐油胶管、密封材料、发泡材料等领域。
混炼是将各种物料均匀分散在橡胶基体中,在混炼过程中不仅存在物料分散的物理作用,也存在橡胶基体与配合剂体系相互作用的化学反应。
混炼是橡胶加工过程中的重要工序,混炼效果直接影响橡胶制品的性能,因此混炼工艺对胶料性能的影响受到业界的广泛关注[4-7]。
NBR分子结构具有强极性,NBR混炼时生热大,与配合剂的润湿性不佳,填料分散困难,在填料大量填充时易发生焦烧现象,混炼工艺性能较差,因此研究NBR 的混炼工艺对指导其合理加工具有重要意义。
本工作从工艺参数和填充因数2个角度研究混炼工艺对NBR加工性能和物理性能的影响。
1 实验1.1 主要原材料NBR,牌号2665,中国石化-西布尔合成橡胶有限公司产品;炭黑N550,上海卡博特化工有限公司产品;无机填料A,江苏鑫源矿业有限公司产品;氧化锌、硬脂酸和增塑剂DOP(分析纯),防老剂RD 和MB、促进剂TMTD和硫黄(工业级),市售品。
丙烯腈含量对氢化丁腈橡胶耐油和耐低温性能的影响

橡 胶 工 业CHINA RUBBER INDUSTRY 954第70卷第12期Vol.70 No.122023年12月D e c.2023丙烯腈含量对氢化丁腈橡胶耐油和耐低温性能的影响董勇修1,王志彬2,曹有华1,陈 琪2*(1.浙江丰茂科技股份有限公司,浙江宁波 315400;2.青岛科技大学橡塑材料与工程教育部重点实验室,山东青岛 266042)摘要:选取4种不同丙烯腈含量的氢化丁腈橡胶(HNBR),研究丙烯腈含量对HNBR耐油性能和耐低温性能的影响。
结果表明,随着丙烯腈含量的增大,HNBR硫化胶的拉伸强度和撕裂强度增大,4069液压油浸泡和热空气老化后的压缩永久变形增大,玻璃化温度和低温回缩10%的温度升高,-45 ℃压缩耐寒因数减小,耐低温性能变差。
关键词:氢化丁腈橡胶;丙烯腈含量;耐油性能;耐低温性能中图分类号:TQ333.7 文章编号:1000-890X(2023)12-0954-04文献标志码:A DOI:10.12136/j.issn.1000-890X.2023.12.0954氢化丁腈橡胶(HNBR)是通过丁腈橡胶(NBR)氢化制成的一种耐热和耐油弹性体。
HNBR由于分子结构含有较少或不含碳-碳双键,不仅具有NBR的耐油性能和耐磨性能,耐候性能和化学稳定性也得以改善,此外还具有大部分耐油橡胶所不具备的较高强度,尤为突出的是其耐高温性能较NBR大幅提高,可以在更为苛刻的环境中使用[1-5]。
HNBR因较高的性价比和优异的工艺性能,被广泛应用于各种油罐、密封件、燃料泵隔膜和阀门套衬垫,以及油田工业用井口密封、钻井管密封和保护层等[6-8]。
而我国一些用于特种领域的橡胶密封制品需要经受-45 ℃极端低温和150 ℃极端高温等多种恶劣环境[9],性能优异的HNBR满足这些高要求[10-11]。
因此,对耐高温性能优异的HNBR胶料进行配方改进以提高其综合物理性能、耐低温性能和耐特种液压油性能等成为研究热点[12]。
用作硫黄硫化体系抗硫化返原剂的多功能丙烯酸盐
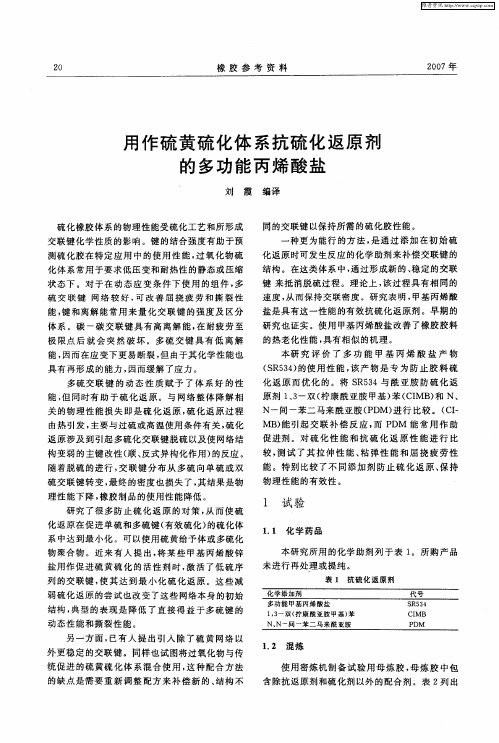
体 系 。碳 一碳 交联 键 具 有高 离解 能 , 在耐 疲 劳 至 极 限点 后 就 会 突然 破 坏 。多硫 交 键 具 有 低 离 解 能, 因而 在应 变下更 易断裂 , 由于其化学 性能也 但
具 有再形 成 的能力 , 因而缓 解 了应 力 。
盐是 具有这 一性能 的有效抗 硫化返 原剂 。早期 的
较 , 试 了其 拉伸 性 能 、 弹性 能 和屈 挠 疲 劳 性 测 粘
能 。特别 比较 了不 同添 加 剂 防止 硫 化 返 原 、 持 保
物理 性能 的有效性 。
1 试 验
1 1 化 学药品 . 本研究 所用 的化学 助剂列 于 表 1 。所 购产 品 未进 行再处理 或提纯 。
准 配 方 。使 用 开 炼 机 混 炼 胶 料 , 炼 前 , 先将 胶料 停放 一通 宵 。
表 2 配 方
制备 试样 所 用 的硫 化 温 度 通 常 为 1 ℃。按 照 最 6 高初 始记 录值 ( M ) 6 mi 的 记 录值 ( 0 和 0 n时 M6 ) 之 间的扭 矩差计 算 硫 化 返原 。 以 T 。 为试 样硫 。作 化 时间 。另外 , 化 至 6 mi 硫 0 n制备 返 原 试 样 。依
维普资讯
2 O
橡 胶 参 考 资 料
抗硫化返原剂WK-901在橡胶隔震支座胶料中的应用
性的影响如图1所示。
10
8
6
5
4
6
3
2
1 4
䒘ⴕ Ngm
2
0
2
4
6
8
10
ᬢ䬠h103s
WK-901用量/份:1—0. 3;2—0. 5;3—0. 7;4—1;5—2;6—3。 图1 抗硫化返原剂WK-901用量对胶料硫化平坦性的影响
从 图 1 可 以 看 出,抗 硫 化 返 原 剂 WK-901 用 量 越大,胶料的硫化平坦性越好,出现硫化平坦期越 早。当抗硫化返原剂WK-901用量为0. 3份时,胶 料的硫化曲线一直呈现下降趋势;当其用量为0. 5 份时,胶料的硫化曲线在1. 8 h左右开始趋于平坦; 当其用量为0. 7份时,胶料的硫化曲线在1. 2 h左右 开 始 趋 于 平 坦,并 略 有 上 升 趋 势;当 其 用 量 为 1 份 时,胶料的硫化曲线在1 h左右趋于平坦,并略有上 升趋势;当其用量为2和3份时,胶料的硫化曲线在 1 h以内趋于平坦,并有一定的上升趋势。 2. 1. 2 物理性能
534
橡 胶 工 业
2019年第66卷
抗硫化返原剂WK-901在橡胶隔震支座 胶料中的应用
王贤彬,赵晨旭,陆 浩,吴建伟,杨永兵,李志祥
(云南震安减震科技股份有限公司,云南 昆明 650000)
摘 要 :研 究 抗 硫 化 返 原 剂 W K - 9 0 1 用 量 对 橡 胶 隔 震 支 座 胶 料 及 成 品 性 能 的 影 响 。 结 果 表 明 :抗 硫 化 返 原 剂 W K - 9 0 1 对胶料的t10和t90基本无影响,但对硫化平坦性有显著影响;抗硫化返原剂WK-901对胶料老化前的物理性能有一定影响, 对老化后的物理性能有显著影响;随着抗硫化返原剂WK-901用量的增大,成品橡胶隔震支座内层胶的拉伸强度增大,拉 断伸长率降低,支座的屈服后刚度和等效水平刚度均增大。
橡胶技术网 - 国内外橡胶助剂工业的发展
提高硫黄硫化胶料在无氧条件下的老化性 能 ,即通常所说的抗硫化返原性能 ,一直是提高 轮胎等橡胶制品同步硫化质量和产品使用寿命 的关键问题 [ 11 ] 。特别是为了提高生产效率而采 取的高温硫化工艺已得到越来越广泛的应用 ,在 厚制品 (如轮胎 )高温硫化中提高胶料的抗硫化 返原性能就显得更为重要 。北京橡胶工业研究 设计院开发出了新型高效抗硫化返原剂 Z - 600 系列产品 。该系列产品除具有突出的抗硫化返 原性能外 ,还可提高 NR硫化胶的物理性能 ,降低 胶料的动态生热 [ 12 ] 。山西省化工研究所生产了 多功能抗硫化返原剂 DL - 268 J和后硫化稳定剂 HS - 258。DL - 268 的动态性能良好 ,具有抗硫 化返原性 ,可提高硫化胶的定伸应力 、耐热性能 及帘线 - 橡胶粘合强度 ,用于轮胎缓冲层和胎肩 胶 ,可有效防止“肩空 ”现象 ; HS - 258 是六亚甲 基 - 1, 6 - 二硫代硫酸钠二水合化合物 ,可改善 通用橡胶胶料的抗硫化返原性和动态性能 。
促进剂 D、M、DM、TMTD
防老 剂 甲 、RD、丁 、BLE、 FK - 40
防老剂 4010NA、4020
抗硫化返原剂WY9188在不同硫化体系配方中的应用
抗硫化返原剂WY9188在不同硫化体系配方中的应用李代强(贵州轮胎股份有限公司,贵州贵阳 550008)摘要:研究抗硫化返原剂WY9188在不同硫化体系配方中的应用。
结果表明:抗硫化返原剂WY9188在硫化过程中既能起到部分硫黄的作用,也能起到一定促进剂的作用;抗硫化返原剂WY9188用于不同的硫化体系配方,尤其是高硫低促配方体系中能够得到很好的抗硫化返原、焦烧安全和快速硫化的效果,但对部分物理性能有一定的负面影响,在对物理性能要求很高的产品中使用时需要适当调整配方以达到产品的使用要求。
关键词:抗硫化返原剂;硫化体系;高硫低促体系;高硫高促体系;硫化特性;物理性能中图分类号:TQ330.38+5;TQ336.1 文章编号:1006-8171(2021)01-0036-04文献标志码:A DOI:10.12135/j.issn.1006-8171.2021.01.0036硫化返原通常指当硫化温度过高、硫化时间过长或硫化胶经无氧老化时,正硫化后出现硫化曲线下降的现象[1]。
胶料过硫后,部分多硫键断裂生成双硫键和单硫键、甚至环硫键,使胶料的交联密度减小,而环硫键对胶料的物理性能无任何贡献[2-4]。
目前,提高天然橡胶(NR)抗硫化返原性能主要有以下措施:(1)改变促进剂的种类和用量;(2)加入硫载体化合物;(3)加入补偿型硫化体系以弥补交联键的损失;(4)添加有机锌皂类化合物[1]。
抗硫化返原剂WY9188化学名称为1,6-双(N,N-二苯并噻唑氨基甲酰二硫)-己烷,分子结构如图1所示。
从分子结构看,抗硫化返原剂WY9188两侧的苄基秋兰姆与促进剂TBzTD较为接近,中间参与交联的部分则与抗硫化返原剂HTS相似[5]。
抗硫化返原剂WY9188特殊的结构使其能在胶料硫化过程中参与交联,与硫黄共同作用形成碳-硫杂链交联键,不仅具有单硫键和双硫键的稳定性,而且具有多硫键的柔顺性,有助于胶料形成稳定的交联网络,在改善胶料抗硫化返原性能的同时,提高胶料老化后的各项性能保持率[5]。
不同炭黑品种对丁腈橡胶流变性能和热性能的影响
不同炭黑品种对丁腈橡胶流变性能和热性能的影响朱永康【摘要】研究了两个品种的炭黑即N330和N990(原生粒径分别为46 nm和>230 nm)对丁腈橡胶性能的影响.由两条高温流变动力学曲线(T1=180℃,T2=190℃)测定了活化能(Ea).炭黑含量不同的胶料于150℃下在液压平板硫化机中硫化.试样在100℃的空气循环烘箱内老化168 h,测定其老化前及之后的应力-应变.通过热重分析考察了填充炭黑丁腈橡胶在流动的氮气氛围中按10℃/min速率升温的热降解与热稳定性.【期刊名称】《世界橡胶工业》【年(卷),期】2014(041)001【总页数】6页(P12-17)【关键词】N330炭黑;N990炭黑;丁腈橡胶;交联密度;溶胀性能;热稳定性【作者】朱永康【作者单位】中橡集团炭黑工业研究设计院,四川自贡643000【正文语种】中文【中图分类】TQ330.38+10 前言丁腈橡胶常常用于制造汽车零部件,这是因为它在宽域的温度范围内具有耐燃油性、耐多种油品性和耐其它液体介质。
然而,丁腈橡胶本身并不能用于要求耐高热和耐臭氧的特定场合。
丁腈橡胶的耐臭氧和耐热老化性能相当差,这是由于其聚合物主链中含有不饱和键,这就使得丁腈橡胶在某些条件下发生断链现象。
文中将含N990炭黑的丁腈橡胶胶料,与含N330炭黑的丁腈橡胶进行胶料比较。
为此,用不同品种炭黑制备了丁腈橡胶胶料,并按照标准测试方法对硫化胶进行了试验。
围绕了性能测试结果进行了讨论,以确定可赋予橡胶胶料理想性能的适宜的炭黑品种。
1 实验部分1.1 材料研究采用的材料如下:1.1.1 橡胶丁腈橡胶(NBR Kraynac 34-50,加拿大Polysar公司产品),丙烯腈含量33.2%;100℃下的门尼黏度50;相对密度1.17g/cm3;灰分 0.5%。
1.1.2 填料1)高耐磨炉法炭黑N330(德固赛公司产品):黑色粒状粉末,粒径46nm,相对密度1.78~1.82g/cm3,CTAB比表面积83±6m2 /g。
- 1、下载文档前请自行甄别文档内容的完整性,平台不提供额外的编辑、内容补充、找答案等附加服务。
- 2、"仅部分预览"的文档,不可在线预览部分如存在完整性等问题,可反馈申请退款(可完整预览的文档不适用该条件!)。
- 3、如文档侵犯您的权益,请联系客服反馈,我们会尽快为您处理(人工客服工作时间:9:00-18:30)。
加工应用 合成橡胶工业,2008-11-15,31(6):472~474C H I NA SY NTHETI C RUB B ER I N DUST R Y抗硫化返原剂PK900对丁腈橡胶性能的影响贺春江1,陈传志2,李雪春2,张宪清2,赵红祥3(11中国铁道科学研究院金属及化学研究所,北京100081;21中国铁道科学研究院铁道部标准计量研究所,北京100081;31河南南阳天一密封制品有限公司,河南南阳474350) 摘要:以N,N′-间甲基苯基双(3-甲基马来酰亚胺)(简称PK900)作过氧化二异丙苯的交联助剂,研究了其对丁腈橡胶(NBR)硫化胶耐热性、耐溶剂性和物理机械性能的影响。
结果表明,加入PK900可以提高N BR硫化胶的交联密度,改善NBR硫化胶的耐热性和耐溶剂性;虽然物理机械性能稍有下降,但用量的增加对该性能的影响并不大。
关键词:N,N′-间甲基苯基双(3-甲基马来酰亚胺);过氧化二异丙苯;助交联剂;丁腈橡胶;交联密度;耐热性;耐溶剂性;物理机械性能 中图分类号:T Q314124 文献标识码:B 文章编号:1000-1255(2008)06-0472-03 以过氧化二异丙苯(DCP)硫化的丁腈橡胶(NBR)虽已具有很好的耐热性、耐溶剂性和弹性,但为了进一步提高这些性能,常用硫黄、三聚氰酸三烯丙酯及N,N-间苯撑双马来酰亚胺(HVA-2)等作为DCP的助交联剂[1-3]。
N,N′-间甲基苯基双(3-甲基马来酰亚胺)(简称PK900)是一种效果很好的抗硫化返原剂,当以其作为天然橡胶(NR)的助交联剂时,它能够参与交联反应,形成长的、柔顺的碳碳交联键,抑制硫化返原的发生,使NR硫化胶具有低生热、高模量保持率和优良的耐疲劳性能[4]。
PK900与H VA-2有类似的分子结构[4-6],由于PK900分子中的2个双键间距离更远,所以其参与交联所形成的碳链也更长更柔顺。
本工作以PK900作为DCP的助交联剂,研究了其对NBR硫化胶耐热性、耐溶剂性和物理机械性能的影响。
1 实验部分111 原材料DCP,上海高桥石油化工公司产品。
PK900,其分子式见图1,美国Flexsys公司提供。
NBR,牌号为N,中国石油兰州石化公司产品。
炭黑,牌号为N55,河北沙河炭黑厂产品。
其他原材料均为市售品。
Fig1 Structure for m ula of PK900112 实验方法NBR硫化胶的基本配方(质量份):NBR 100,硬脂酸110,炭黑50,DCP变量(110,114,116),PK900变量(110,210,310)。
在广东湛江橡塑机械制造厂生产的S(X) K-160A型冷辊开炼机上混炼,辊温为50℃左右,NBR先薄通5次,依次加入硬脂酸、炭黑,混炼均匀后加入DCP及PK900。
停放2d,适当返炼后在上海橡胶机械制造厂生产的25t平板硫化机上硫化,硫化温度为170℃,时间为12m in。
113 分析与测试硫化特性 用上海埃尔法仪器科技有限公司生产的MDR2000型无转子硫化仪测试混炼胶的硫化曲线,测试温度170℃。
①收稿日期;修订日期63。
作者简介贺春江(6—),男,硕士,助理研究员。
已发表论文余篇。
41:2007-07-27:2008-0-1:19710耐热性 用美国Perkin -El m er 公司生产的TG 2型分析仪测试,氮气保护,升温速率为20℃/m in,温度为50~600℃。
物理机械性能 用上海化工机械四厂生产的DX LL 10000型电子拉力试验机按照G B /T 528—1998测试拉伸强度和扯断伸长率,按照G B /T 529—1999测试撕裂强度。
耐溶胀性能 按照G B /T 1690—1992测试,介质为甲苯。
2 结果与讨论211 NBR 混炼胶的硫化特性从图2可以看出,随着PK 900用量的增加,NBR 混炼胶的最大转矩与最小转矩之差(ΔM )逐渐增大,其变化规律与未加PK 900的NBR 混炼胶相似。
这说明PK 900参与了NBR 的硫化反应,提高了体系的交联密度。
DCP and PK 900/ph r :sa mp le 1—110,0;sa mp le 2—114,0;s a mp le 3—116,0;s a mp le 4—110,110;s amp l e 5—110,210;s a mp le 6—110,310Fig 2 Effect of DCP and PK 900on vulcan i zati oncharact eristi c of NBR compound212 NBR 硫化胶的耐热性从图3可以看出,NBR 硫化胶加入PK900R ()—NB R ,D 1,K ;B —NB R ,D 1,K 1F 3 ff f K f NBR z 后,在500℃时的失重率为18107%,而未加PK 900时NBR 硫化胶的失重率为27152%,说明PK 900使NBR 硫化胶的耐热性得到改善。
这是由于PK 900参与形成长碳链桥键的耐热性比较好的缘故。
213 NBR 硫化胶的耐溶胀性从图4可以看出,未加PK 900时,随着DCP 用量的增加,NBR 硫化胶在溶胀后质量变化率(Δm )逐渐减小;加入PK 900后,NBR 硫化胶的Δm 大幅度减小,且随着PK 900用量的增加,Δm 逐渐减小。
这说明PK 900的加入提高了NBR 硫化胶的交联密度,改善了耐溶胀性能。
S amp le 1-6are t he s ame as in Fig 2Fi g 4 Effect of PK 900on s wel li ng resist ancei n t oluene ofNBR vulcan i zates214 NBR 硫化胶的物理机械性能从表1可以看出,未加PK 900时,随着DCP 用量的增加,NBR 硫化胶的拉伸强度、扯断伸长率和撕裂强度显著减小;加入PK 900后,N BR 硫化胶的拉伸强度和扯断伸长率稍有减小,撕裂强度减小幅度也不大;且随着PK 900用量的增加,物理机械性能下降趋势不明显。
这是因为PK 900参与了NBR 的硫化反应,形成的交联键比较长而柔顺,其硫化效果类似硫黄,交联网络可以更Tab le 1 Effect of PK 900on m echan i ca lp ropert ies of NBR vu l can i za tesSamp l e Tensile strength /M PaEl ongati on at break /%Tear strength /(kNm -1)1231635046192171521628103161218924184221332131185133315613331 S 6F 1374 第6期 贺春江等1抗硫化返原剂PK 900对丁腈橡胶性能的影响ec i p e phr :A 100C P 10P 9000100C P 10P 90010i g E e c t o P 900on hea t re sist a nce o vulca ni a t e s21910220728a mp le 1-a re t he same a s in ig 2均匀地承载外力的缘故。
因此,PK900用量的增加对NBR硫化胶物理机械性能影响并不大[7]。
3 结 论a)以PK900作DCP的助交联剂,可以提高NBR硫化胶的交联密度。
b)加入PK900可改善NBR硫化胶的耐热性和耐溶胀性。
c)加入PK900使NBR硫化胶的物理机械性能稍有下降,但影响并不大。
参考文献:[1] C o rnell J A1Mechan is m of rubber coagen t p er oxide cure s yste m[J]1R ubb Che m Technol,1970,43(3):613-6231[2] D ikland H G,R uardy T,van der Does L1New coagent s inperoxide vu l canizati on of EP M[J]1R ubb C he m Techno l,1993,66(5):693-7111[3] R ichard H C1Fundamentals of cu ring el ast om ers w it h p er oxi desand coagen ts[J]1R ubberWorl d,2006,233(5):28-351 [4] D at t a R N,I vanyM S,A kzo N1Che m i cal f o r reversi on res i st antcompounding[J]1R ubber World,1995,212(5):227-2301 [5] 陈朝辉1HAV-2在NB R硫化胶中的应用[J]1合成树脂与塑料,2001,18(2):20-221[6] 黄琛亚1P B M在过氧化物硫化胶中的作用机理[J]1合成橡胶工业,1998,21(5):286-2881[7] 何曼君1高分子物理[M]1上海:复旦大学出版社,1990:338-3411Effect of an ti2r ever si on P K900on pr oper t i es ofacr ylon itr ile2buta d i en e r ubberHe Chunjiang1,Chen Chuanz hi2,L i Xuechun2,Zhang Xianqing2,Zhao Hongxiang3(11M eta ls a nd Che m istry R e search I ns titu te,Ch ina Acade m y of Ra il w ay Sciences,Beijing100081,China; 21S tand ards a nd M etrology Research I n stitu te,Ch ina Ac a de m y of Ra il w ay Sciences,B eijing100081,C hin a;31N anya ng Tiany i Seal P roducts Co L td,N a nyang474350,Ch ina) Ab stra ct:The effec ts of PK900as the coagent of dicum yl per oxide on the heat r e sistance,solvent re2 sistance and m echanical pr operties of acr yl onitrile2 butadiene rubber(NBR)vulcanizates were studied1 The results showed that the cr osslinking density,the hea t resistance and solvent r e sistance of N BR vul2 caniz a tes were i mp r oved and the m echanical pr oper2ties decr eased slightly due to the addition of PK 9001The effect of amount of PK900on the m echan2 ical p r operties of NBR vulcanizates wa s not obvious1 Keywor ds:PK900;dicu m yl per oxide;c ocuring agent;acrylonitrile2butadiene r ubber;cr osslinking density;heat resistance;solvent resistance;m echan2 ical p r ope rty ●国内简讯● 中国合成橡胶工业协会2008年丁苯橡胶、丁腈橡胶及胶乳研讨会在南京召开 由中国合成橡胶工业主办、南京扬子石化金浦橡胶有限公司承办的中国合成橡胶工业2008年度丁苯橡胶、丁腈橡胶及胶乳生产技术交流研讨会于2008年10月15日至18日在南京召开。