浅谈转炉滑板挡渣出钢技术
转炉无渣出钢工艺技术(推广版)

20
七、挡渣技术指标
下渣量
挡渣方法 机构自动挡渣
渣层厚度 (mm)
26.8
推导下渣量 ( kg/t钢)
4.7
实测下渣量 ( kg/t钢)
2.0
挡渣塞挡渣 挡渣球挡渣
32.3 46.6
5.7 7.9
6.3 7.2
21
挡渣成功率
挡渣成功率比较 120.00 100.00
挡渣成功率/%
100.00 89.10 70.10
8
二、挡渣系统工作原理及技术难点
1、挡渣系统的工作原理
在转炉出钢口 末端安装闸阀系 统。通过自动下 渣检测系统来控 制液压闸阀快速 开启或关闭出钢 口,达到挡渣的 目的。
挡渣系统示意图
9
2、技术难点
挡渣机构工作环境温度高(900-1500℃),温差大, 机构易变形,液压油缸和液压管路易被烧坏. 液压系统管路布置安装困难(与转炉同步旋转、不受冶炼 喷溅影响、原转炉托圈、耳轴无管路安装位置). 温度高、挡渣机构重、安装精度高,因此挡渣机构更换难 度大,时间长,但必须满足转炉快节奏的生产要求. 转炉出钢过程环境恶劣,粉尘多,且受安装位置的限制, 自动下渣检测信号采集困难. 挡渣机构快速开启对液压系统的要求高(系统环境温度高、 压力高、管路易振动、易泄漏). 钢水、炉渣氧化性强,对耐材的侵蚀严重。
4
2、国内外研究状况
常用挡渣方法
前挡渣 常用 挡渣方法 挡渣帽
挡渣球 挡渣塞
后挡渣 气动挡渣法 气动吹渣法 电磁挡渣法
5
常用挡渣方法比较
挡渣方法
挡渣球法
示意图
挡渣原理
利用挡渣球密度介于钢、 渣之间,在出钢结束时 堵住出钢口以阻断渣流 入钢包内。 其比重与挡渣球相近,伴 随着出钢过程逐渐堵住 出钢口,实现抑制涡流 和挡渣的作用。
梅钢250t转炉滑板挡渣技术应用实践

梅钢250t转炉滑板挡渣技术应用实践
刘自康;郑毅
【期刊名称】《宝钢技术》
【年(卷),期】2024()2
【摘要】介绍了上海梅山钢铁股份有限公司250 t转炉出钢挡渣工艺、滑板挡渣控制模式及滑板挡渣系统维护方法。
通过采用滑板挡渣+红外下渣检测的挡渣技术,实现了出钢挡渣的全自动控制,挡渣成功率达到100%,钢包回磷质量分数降低
0.0013个百分点,平均出钢口寿命提高34炉,钢铁料消耗下降3 kg/t,取得了较好的经济效益。
【总页数】4页(P75-78)
【作者】刘自康;郑毅
【作者单位】上海梅山钢铁股份有限公司规划科技部;上海梅山钢铁股份有限公司梅钢技术中心
【正文语种】中文
【中图分类】TF062
【相关文献】
1.滑板挡渣技术在河钢宣钢150t转炉的应用
2.涟钢210吨转炉滑板挡渣技术应用实践
3.180 t转炉滑板挡渣出钢技术应用实践
4.转炉出钢滑板挡渣+挡渣标技术的实践与应用
5.宝钢250t转炉滑板挡渣机构耐材使用实践
因版权原因,仅展示原文概要,查看原文内容请购买。
宝钢炼钢厂转炉挡渣工艺技术的发展

开发与应用宝钢炼钢厂转炉挡渣工艺技术的发展孙兴洪,蒋小弟(宝山钢铁股份有限公司炼钢厂,上海 200941) 摘要:采用转炉出钢挡渣工艺技术控制转炉出钢下渣量,必须关注和解决转炉出钢全过程的下渣控制。
评价转炉出钢挡渣效果的关键指标是挡渣成功率和钢包中的渣厚。
宝钢炼钢厂转炉出钢挡渣工艺技术的发展,目标是实现转炉出钢全过程的自动判渣和挡渣,提高挡渣成功率,减少出钢下渣量。
关键词:转炉;出钢;钢包;渣厚;挡渣中图分类号:TF724.5 文献标志码:B 文章编号:1008-0716(2010)02-0058-05D evelopm en t of the S lag 2stopp i n g Technology dur i n g C onver ter Tapp i n g i n Ba osteel S teelm a k i n g P lan tSUN X in gh on g and J I AN G X iaod i(Steel m a k i ng P lan t,Baosha n I r on &Steel C o.,L td.,Shan gha i 200941,C h i na ) Abstrac t:W hen using a slag 2stopp ing technology t o r educe the a mount of slag int o the ladle,operators m ust pay attenti on t o the r oughing slag contr ol in the whole pr ocess of converter tapping .The r e a r e t w o key indicators:the achieve m ent r a tio of slag st opping and the slag thickness in the ladle .They can be used to evalua te the effect of slag 2stopping .The developm ent of the slag 2st opping technol ogy f or converter tapping in B aosteel Steel m aking Plant ai m s at the realizati on of the aut om atic slag adjust m ent and slag 2st opp ing in the whole p r ocess of converter tapping t o i mpr ove the achieve m ent r atio of slag 2stopp ing and t o reduce the a mount of slag in the ladle .Key wor ds:converter ;tapp ing;ladle;slag thickness;slag 2stopping孙兴洪 首席工程师 6年生 6年毕业于重庆大学现从事炼钢工艺研究 电话 66352 x @0 前言钢包渣的主要来源是转炉出钢时的下渣、合金化过程中产生的渣,以及工艺需要进行的钢包渣改质、精炼二次造渣等。
120t转炉滑板挡渣系统应用技术

120t转炉滑板挡渣系统应用技术
吴代平;徐兆春;杨正武;章香林;张文全;王玉龙;王军
【期刊名称】《安徽冶金科技职业学院学报》
【年(卷),期】2013(023)004
【摘要】通过对某厂120t转炉相关设备技术开发,成功应用了滑板挡渣系统,既节约大量投资费用,又完全实现滑板挡渣功能.
【总页数】3页(P5-7)
【作者】吴代平;徐兆春;杨正武;章香林;张文全;王玉龙;王军
【作者单位】马钢股份公司第一钢轧总厂安徽马鞍山243011;马钢股份公司第一钢轧总厂安徽马鞍山243011;马钢股份公司第一钢轧总厂安徽马鞍山243011;马钢股份公司第一钢轧总厂安徽马鞍山243011;马钢股份公司第一钢轧总厂安徽马鞍山243011;马钢股份公司第一钢轧总厂安徽马鞍山243011;马钢股份公司第一钢轧总厂安徽马鞍山243011
【正文语种】中文
【中图分类】TG232.7
【相关文献】
1.120t转炉应用滑板挡渣技术实践研究 [J], 戚翠芬;晁霞;王杨;刘燕霞;付菁媛;高静;张华英;杨颖
2.转炉滑板挡渣液压系统功能改进 [J], 高振军
3.提高120t转炉挡渣系统耐材使用效果的生产实践 [J], 李伟;李成江;李彦明;童则明
4.转炉出钢滑板挡渣+挡渣标技术的实践与应用 [J], 张艳龙;丛铁地;彭飞;魏建华;姜学锋
5.包钢120t转炉滑板挡渣技术的改进 [J], 邵亮;宋超;刘佳旭;付岳;石龙
因版权原因,仅展示原文概要,查看原文内容请购买。
转炉出钢口工艺技术操作规程
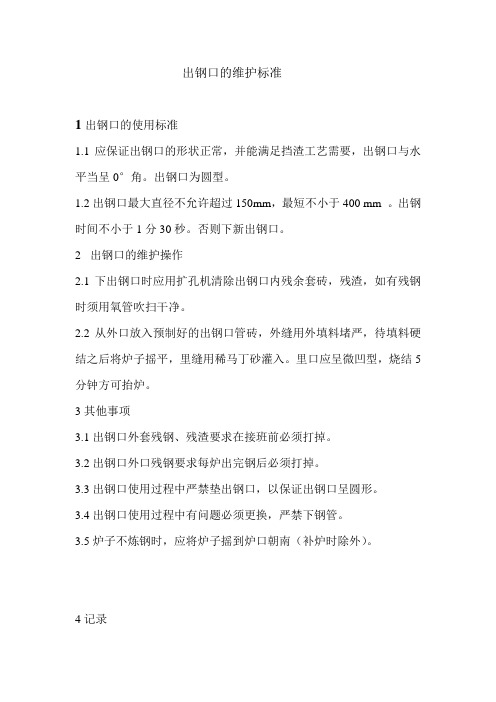
出钢口的维护标准
1出钢口的使用标准
1.1应保证出钢口的形状正常,并能满足挡渣工艺需要,出钢口与水平当呈0°角。
出钢口为圆型。
1.2出钢口最大直径不允许超过150mm,最短不小于400 mm 。
出钢时间不小于1分30秒。
否则下新出钢口。
2出钢口的维护操作
2.1下出钢口时应用扩孔机清除出钢口内残余套砖,残渣,如有残钢时须用氧管吹扫干净。
2.2从外口放入预制好的出钢口管砖,外缝用外填料堵严,待填料硬结之后将炉子摇平,里缝用稀马丁砂灌入。
里口应呈微凹型,烧结5分钟方可抬炉。
3其他事项
3.1出钢口外套残钢、残渣要求在接班前必须打掉。
3.2出钢口外口残钢要求每炉出完钢后必须打掉。
3.3出钢口使用过程中严禁垫出钢口,以保证出钢口呈圆形。
3.4出钢口使用过程中有问题必须更换,严禁下钢管。
3.5炉子不炼钢时,应将炉子摇到炉口朝南(补炉时除外)。
4记录。
济钢210T转炉滑板挡渣

文档收集于互联网,已重新整理排版.word版本可编辑.欢迎下载支持.东北大学继续教育学院毕业设计(论文)开题报告设计(论文)题目:济钢210T转炉滑板挡渣改造项目姓名:许维康学号:072N专业:冶金工程学习中心:济南博文教育学习中心住址:济南市历城区鲍山街道电话:Email:开题日期:2017 年7 月 6 日指导教师:李阳第一章研究的主要内容近年来,随着我国钢材消费结构的变化,对高品质、高附加值钢的需求量越来越大,同时在当前严峻的钢铁行业形势下,建设高效率、低成本的洁净钢平台越来越成为钢厂的工作重点。
减少转炉出钢下渣量是提高钢水洁净度、提高转炉钢产品的质量和命中率、降低炼钢生产成本最有效的途径。
在转炉出钢时进行有效的挡渣操作,不仅能够改善钢水质量,提高合金收得率,还可为精炼操作提供良好的条件。
目前国内转炉出钢挡渣主要还是采用挡渣球、挡渣塞等挡渣方法,这些方法在提高挡渣效果方面均有一定的效果,但仍不能满足部分品种钢稳定生产的需要。
转炉冶炼过程中的脱碳、升温以及脱磷、脱硫等反应都与炉渣密切相关,转炉炉渣具有高氧化性的特点,并含有大量的硫、磷等有害元素。
如果转炉出钢过程大量下渣,不仅会增加钢水的脱氧及合金化难度,增加脱氧剂及合金消耗,还会引起钢包回磷及增加氧化夹杂物含量,增加钢包等的耐材消耗和后道精炼工序成本,严重时造成钢水成分出格,增加了炼钢生产成本。
因此,转炉出钢下渣量必须控制得越低越好。
济钢炼钢厂210区域现有210t顶底复吹转炉两座,平均单炉产钢量217t,年产量约260万吨,产品定位为高端产品、高端客户和重点工程,产品以高强、海工、船板、容器、油罐、桥梁、管线等高级别产品为主,高专比在80%以上。
目前采用传统的挡渣棒挡渣方式,挡渣效果不稳定,吨钢下渣量约5.0kg/t钢,挡渣成功率96.5%,转炉下渣问题严重影响了钢水质量和产品提升。
为提升产品质量控制水平,增强高级别产品的生产保障能力,为了解决转炉出钢下渣量大的难题,济钢对210 t 转炉挡渣系统进行了技术改造,引进了先进的滑板挡渣和红外下渣检测技术,不仅提高了挡渣成功率,而且有效地减少了出钢下渣量,提高了钢水质量和高等级品种钢的生产能力,同时还提高了合金收得率,进一步降低了生产成本,取得了良好的经济效益。
转炉出钢挡渣改进生产实践

阳春新钢铁有限责任公司,广东阳春 529600摘要:转炉挡渣工艺是高洁净钢生产工艺中重要的一环, 挡渣效果不好会直接造成钢水杂质含量高、回磷量大成分出格、后续精炼处理难度增加、钢铁料消耗高等问题,影响钢水质量。
本文结合目前实际挡渣情况进一步探索研究影响转炉挡渣合格率的因素,制订相应对策,提高挡渣合格率,减少转炉出钢下渣量,从而达到改善钢水质量、减少废品的目的。
关键词:转炉、挡渣、高挡渣率1 前言随着我国国民经济的发展,钢材的消费结构正在不断地发生变化,对钢水的洁净度提出了越来越高的要求。
在实际生产中,要求转炉在出钢过程中最大限度地减少下渣量、降低钢水的氧化性及提高炉外精炼的冶金效果,相对于成本较高的精炼过程,转炉挡渣出钢是生产低成本洁净钢的最简单有效途径[1]。
国内某炼钢厂(120吨转炉)2021年5-12月平均挡渣合格率95.6%(下渣≤50mm炉数占比),平均每月因下渣导致磷超国标判废2炉,每炉重量180吨,每月360吨,吨钢加工费用500元,平均每月因成分出格损失18万元。
2 挡渣塞挡渣原理现在国内钢厂转炉挡渣法有挡渣球法,挡渣塞法,气动挡渣,滑板挡渣法,各有利弊[2]。
某炼钢厂采用挡渣塞法挡渣,具有操作简便,使用成本低等优点。
挡渣塞呈陀螺形,粗端有4个凹槽、8个棱角,能够破坏钢水涡流,减少涡流卷渣。
其比重在3.4~ 4.0 g/cm3之间,能浮于钢渣界面,出钢时用专用机械将挡渣塞吊置出钢口上方,缓缓加到钢水面上,随钢水流尽,挡渣塞能堵住出钢口而阻挡炉渣流出,实现抑制涡流和挡渣的作用。
挡渣塞简图及挡渣原理见图1。
图1挡渣塞简图及挡渣原理3 分析影响挡渣成功的因素根据挡渣塞挡渣原理、相关文献及现场生产实践,分析影响挡渣合格率的因素有:1、挡渣塞的工艺参数,如比重、形状、流钢槽的数量、宽度、形状等;2、挡渣塞耐材质量的稳定性,是否受潮,在出钢时是否炸裂;3、挡渣塞的制作质量:挡渣塞整套装置是由挡渣塞,导向杆组成,在使用时将导向杆套在挡渣塞上,出钢至1/2∽2/3时通过挡渣塞投放装置,对准出钢口,插入钢水中,当导向杆卡子松动、衔接不紧密在加挡渣塞时导向杆易掉落、熔化与出钢口定位不准;4、出钢口的形状,当出钢口内口有钢渣堆积时会呈现不规则形状,与挡渣塞配合存在间隙,有漏渣的风险;5、加挡渣塞的时机,挡渣时出钢口的角度与夹持机构上挡渣棒的位置配合不好,加挡渣塞过早或过晚都会影响挡渣效果;6、转炉炉型的控制,出钢口周边及炉帽的日常维护做好有利于挡渣率的提高。
转炉炼钢工艺(溅渣护炉)

溅渣护炉的负面影响
吹炼终点[%C] ·[%O]积随炉龄变化情 吹炼终点 积随炉龄变化情 况
关于经济炉龄的问题
生产率、 生产率、成本与炉龄关系
溅渣护炉的优点
大幅度降低耐材消耗; 大大提高转炉作业率,达到高效增产目的; 投资回报率高; 溅渣护炉综合效益每吨钢约为2~10元。
溅渣护炉的负面影响
底吹透气砖覆盖渣层厚度与吹炼终点[%C] ·[%O]积的关 底吹透气砖覆盖渣层厚度与吹炼终点 积的关 系
溅渣护炉的负面影响
底吹透气砖覆盖渣层厚度与吹炼终点[%C] ·[%O]积的关 底吹透气砖覆盖渣层厚度与吹炼终点 积的关 系
炉渣粘度的控制
过低的炉渣粘度有利溅渣的操作,即易溅起、挂 渣且均匀,但由于渣层过薄,会在摇炉时挂渣流 落; 而粘度过大,溅渣效果差,耳轴!渣线处不易溅到, 且炉底易上涨,炉膛变形,所以粘度需要根据实 际情况合理调整; 炉渣过热度增高,粘度下降。
溅渣操作参数控制
为了在尽可能短的时间内将炉渣均匀喷 敷在整个炉衬表面而形成有足够厚度的 致密溅渣层。必须控制好溅渣操作手段, 即根据炉形尺寸,来控制喷吹N2气压力 和流量、枪位和喷枪结构尺寸等喷溅参 数。
其它参数
喷溅时间:通常为2.5~4min; 喷枪夹角:许多厂家的经验表明采用12 度夹角比较理想。
需要采取的其它措施
炉衬材质不能因实行溅渣护炉技术而降 低,对使用镁碳砖而言,其碳含量应控 制为下限; 控制和降低终渣FeO含量; FeO 合理调整终渣MgO含量; 提高溅渣层熔化性温度,降低炉渣过热 度; 降低出钢温度。
- 1、下载文档前请自行甄别文档内容的完整性,平台不提供额外的编辑、内容补充、找答案等附加服务。
- 2、"仅部分预览"的文档,不可在线预览部分如存在完整性等问题,可反馈申请退款(可完整预览的文档不适用该条件!)。
- 3、如文档侵犯您的权益,请联系客服反馈,我们会尽快为您处理(人工客服工作时间:9:00-18:30)。
浅谈转炉滑板挡渣出钢技术
随着我国国民经济的发展,对钢材的消费结构正在发生变化,加之众多企业日益关注转炉生产特殊钢,这些都对低成本生产高洁净度钢水提出了越来越高的要求。
就转炉炼钢生产企业而言,为生产IF钢(超低碳钢)、石油管线钢、硅钢、轴承钢、弹簧钢等高附加值产品,减少转炉出钢时的下渣量是提高钢水洁净度,从而提高转炉钢产品的质量和档次,降低其生产成本最有效的途径。
转炉挡渣出钢技术方法
一、转炉挡渣出钢“提质降耗”
在转炉炼钢生产中,炉内冶炼时产生大量熔融状态的炉渣。
这些炉渣会随着转炉的出钢流入钢包中,进而影响钢包耐火材料的寿命;造成钢水回硫、回磷,影响钢水质量;增加炉后铁合金的消耗,增加后续工序合成渣的用量,延长精炼工序处理时间。
因此,在转炉出钢时,应采用挡渣出钢技术以严格控制转炉的下渣量。
自1970年日本新日铁发明了挡渣球以来,为了提高转炉出钢过程的挡渣效果,减少下渣量,国内外有关工作者在挡渣技术方面进行了大量的探索,相继发明了挡渣球法、挡渣塞法、挡渣料法、滑板法、气动挡渣法、出钢口吹气干扰涡流法等几十种挡渣方法,并结合炼钢生产实际情况不断加以改进,挡渣效果逐渐优化。
实践证明,转炉出钢口滑动水口挡渣技术以机械或液压方式开启或关闭出钢口,以达到挡渣目的,可以有效控制前期和后期下渣,挡渣成功率可以达到100%,相对其他挡渣技术,挡渣效果最优。
二、转炉出钢口滑动水口应合理选材
转炉出钢口内水口:铝锆碳质性能较优。
考虑到转炉的特殊冶炼环境,目前市场上转炉出钢口内水口材质主要以不烧镁碳质为主,其成分大体类似于转炉出钢口砖,其使用寿命在30炉~80炉。
已有科研工作者开始尝试研究镶嵌氧化锆复合内水口,其使用寿命有望达到120炉以上,甚至与转炉出钢口耐火砖同步。
有研究曾将不烧铝锆碳材质的内水口与不烧镁碳材质的内水口在某钢企120吨转炉进行使用对比,结果发现相同使用寿命的情况下,铝锆碳质内水口使用效果明显好于镁碳质的内水口,主要表现在扩孔小且均匀,用后子母口端面放射状裂纹相对少而小。
三、转炉出钢口滑板:重烧铝锆碳质适应性较好。
为了满足部分钢企提出的18炉~20炉甚至25炉以上长寿命的要求,滑板材质从常规重烧铝锆碳质向本体采用重烧铝锆碳滑板,镶嵌层采用锆质材料的复合结构转型。
目前,市场上主要产品有镶嵌锆环的上滑板搭配镶嵌锆板的下滑板、镶嵌锆板的上滑板搭配镶嵌锆板的下滑板、镶嵌锆环的上滑板搭配滑道止滑区镶嵌锆饼的下滑板等几种类型。
这几种不同类型的镶嵌滑板在国内120吨~300吨不同型号的转炉上,在前期挡
渣和后期挡渣都采用的情况下使用寿命大都可稳定在15炉~18炉。
如果前期挡渣采用其他挡渣手段,仅采用后期挡渣寿命可稳定在20炉次左右甚至可达到25炉次以上。
通过对国内钢企客户炼钢环境调研,并结合在某钢企120吨转炉出钢口滑动水口工业化应用实践来看,重烧铝锆碳质滑板在今后的几年内还有其存在的市场空间和价值。
鉴于此类型滑板经过高温烧成,高温性能稳定,具有高温强度高、抗冲刷和抗侵蚀性能优良等一系列优点,在120吨~300吨不同型号转炉上有较好适应性。
在前后期都采用挡渣操作的情况下,其寿命可稳定在10炉~13炉,如果仅采用后期挡渣操作使用寿命至15炉以上。
虽然镶嵌锆质滑板使用寿命比常规重烧铝锆碳滑板有一定幅度延长,但其生产工艺复杂程度大大增加,生产成本大幅度提高,且随使用寿命延长带来的不安全隐患加大,同时对实际滑动水口及机构操作和评判人员水平也提出更苛刻的要求。
因此,应针对不同钢企客户的实际炼钢环境和滑板寿命需求进行成本测算,综合权衡性价比和利润空间,选用合适的材质。
此外,市场上亦出现过少量重烧镁碳质、低温烧成铝碳质、中温烧结尖晶石碳质等出钢口滑板。
然而这几种材质均非市场主流,且对转炉炼钢环境均存在较大不适应性。
转炉出钢口外水口:不烧铝锆碳质效果较好。
目前,市场上转炉出钢口外水口的材质主要有不烧铝锆碳质、不烧铝碳质和不烧镁碳质三种,由于具有成本优势镁碳质暂据市场主流。
此三类水口大都经过浸渍沥青处理以达到封闭气孔、增强致密度及抗侵蚀性能的目的。
其使用寿命与出钢口滑板同步,可达到10次~15次。
根据有关批量工业化应用实践来看,不烧铝锆碳质使用效果明显优于不烧铝碳质,而不烧铝碳质的使用效果略优于不烧镁碳质。
不烧铝碳质外水口的主要缺点是多次使用后扩孔较大,抗钢水、钢渣冲刷和侵蚀性能较差。
不烧镁碳质的外水口主要缺点在于,转炉出钢挡渣工作结束后,外水口钢壳底部及外水口下部易挂渣或结冷钢,钢厂俗称“结胡子”,当采用机械工具清理“胡子”时,不可避免对外水口造成机械损伤,形成使用隐患。
同时与铝锆碳质相比,其高温强度偏低、热震性能较差,容易在使用8炉~10炉后于铸孔内部产生竖裂纹,存在较大安全隐患。
四、开发高档材质优化技术应用是方向
鉴于转炉出钢口滑动水口挡渣技术能够满足高附加值优质钢材料冶炼时高质量和低成本的双重优势,笔者预测,随着冶金技术、滑板技术的进步和市场的发展,会有越来越多的钢企在转炉上应用此技术。
针对目前存在的问题,结合市场的新发展,该技术今后的发展方向应侧重以下几方面:
开发滑动水口新材质。
目前转炉出钢口滑动水口常规材质仍已重烧铝锆碳为主,耐材工作者下一步应继续加大研发力度,在含锆材料引入类型和复配比例上、新型抗氧化剂合金添加剂、碳源引入类型等各方面深入探索,进一步提高滑板的综合性能,开发出更适应转炉炼钢环境的新型高档材质。
对于镶嵌锆质滑板,研
究工作者应进一步提高锆板、锆环制备的精细化水平,开发出更适应转炉炼钢环境的锆质新材料,才能够从根本上突破目前转炉滑板20炉的寿命“瓶颈”。
探索新型滑动机构。
转炉出钢口滑动水口机构较钢包滑动水口机构体积更大、更笨重,工人操作起来需要借助专用的机构吊具和专用拆装工具,劳动强度较大、效率低。
如何开发出一种劳动强度低且操作自动化程度高的新型转炉出钢口滑动水口机构,还有许多工作值得深入研究。
此外,转炉滑板在频繁出钢过程中,滑动水口机构亦要经历较钢包滑动水口机构更高温度的烘烤,对机构弹簧等部件能否持续安全使用是极大的考验,而这直接关系到机构中上下滑板之间的面压稳定性问题。
如何降低转炉滑动水口机构使用过程的表面温度,保证高效长时间安全运行,是目前面临的主要挑战。