MTBE催化剂使用寿命和失活的预防
MTBE生产工艺
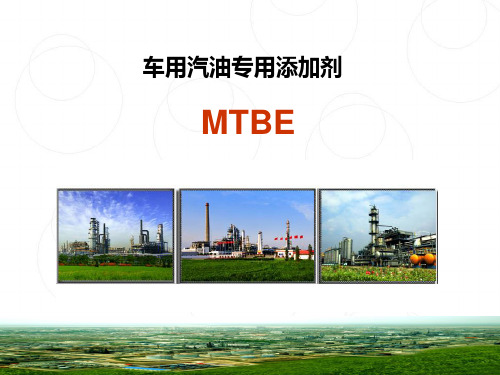
醇烯比过大:可使异丁烯转化率增加,但多余的甲 醇不仅增加了反应精馏塔的分离难度而且增加了 甲醇回收塔的负荷。
醇烯比过小:发生异丁烯聚合反应,放出大量热量, 造成反应器超温,烧坏催化剂。
MTBE反应的主要影响因素
(2)反应温度 反应温度的高低不仅影响异丁烯的转化率,
而且也影响MTBE的选择性、催化剂的使用寿命和 反应速度。
4.2.2 尾气排放量大 按照设计,装置不产生尾气,由于原料中C3
组分含量远高于设计值,装置不得不进行尾气排放。 目前尾气只能排入火炬。
五、吉化MTBE装置的技术改造情况
➢ 原设计:2.75万吨MTBE/年,设计运行时间:7200 小时
➢ 由吉化研究院开发,吉化设计院设计,吉化建设公司 安装的我国第一套万吨级工业化装置;
3.5 甲醇回收原理 利用C4和甲醇在水中溶解度的不同,用水做萃
取剂,将甲醇和C4分离,在用精馏的方法分离甲醇 与水。
流程
C4馏分 V402甲醇储罐 V401C4储罐 V409脱碱罐 R402AB净化器 R401反应器 T401反应精馏塔 T402萃取塔 T403甲醇回收塔
MTBE的工艺流程叙述
生产温度:一般50~70℃为宜,温度超过80 ℃, 副反应增加,催化剂寿命缩短,温度超过120℃, 催化剂失活。
二、工艺原理
3.3 催化蒸馏原理 反应与精馏在同一个塔内进行,反应放出的
热量用于精馏物料汽化,保证反应在恒温下进行。
3.4 产品分离原理 利用C4和甲醇形成最低共沸物的性质,采用共
沸精馏的方法,将MTBE与甲醇、C4进行分离。
3.2 醚化反应原理
混合C4中异丁烯与甲醇在强酸性苯乙烯系大 孔阳离子交换树脂催化剂作用下发生合成反应生 成MTBE。
MTBE合成装置醚后C4中甲醇和二甲醚含量高的原因分析及对策

MTBE合成装置醚后C4中甲醇和二甲醚含量高的原因分析及对策王华槟;刘春胜【摘要】分析北京燕山石油化工有限公司MTBE合成装置醚后C4中甲醇及二甲醚含量高的原因,通过采取更换甲醇萃取塔、用MTBE裂解装置甲醇回收塔替代MTBE合成装置的甲醇回收塔、提高催化剂活性、用近红外在线分析仪准确控制反应的进料醇烯比等措施,醚后C4中甲醇及二甲醚含量从1 0000 μg/g以上分别降低到甲醇含量不大于50 μg/g、二甲醚含量不大于500 μg,可满足下游装置烷基化生产的需要.【期刊名称】《石油炼制与化工》【年(卷),期】2010(041)004【总页数】6页(P6-11)【关键词】MTBE;甲醇;萃取;二甲醚;措施【作者】王华槟;刘春胜【作者单位】中国石化北京燕山石油化工有限公司,北京,102503;中国石化北京燕山石油化工有限公司,北京,102503【正文语种】中文北京燕山石油化工有限公司MTBE合成装置是以DMF抽提丁二烯和乙腈抽提丁二烯装置的提余液(混合C4)或炼油厂气体分馏装置的C4馏分和甲醇作为原料.C4中的异丁烯与甲醇发生醚化反应生成MTBE(甲基叔丁基醚).产品MTBE用于生产高纯度异丁烯,或作为高标号汽油生产中提高辛烷值的添加剂,醚化反应中过剩的甲醇被回收使用.醚化反应后的混合C4被称为醚后C4,其主要组分为异丁烷、正丁烷、正丁烯、顺-2-丁烯、反-2-丁烯及少量丁二烯.2005年以前该公司醚后C4作为民用液化气;2005年起,醚后C4作为炼油厂烷基化装置的生产原料,生产高辛烷值汽油组分--烷基化油.二甲醚和甲醇是烷基化过程中耗酸的主要杂质,并且会降低烷基化油的收率和辛烷值[1].本课题在对北京燕山石油化工有限公司MTBE合成装置醚后C4中甲醇及二甲醚含量高的问题进行分析的基础上,提出降低醚后C4中甲醇及二甲醚含量的有效措施,以满足下游装置烷基化生产的需要.在MTBE合成装置中,原料C4和甲醇进入反应器,在大孔强酸性阳离子树脂催化剂的作用下,C4中的异丁烯与甲醇发生醚化反应,生成MTBE.反应后的物料包括过剩甲醇、醚后C4、产品MTBE、副产物二甲醚、C8、MSBE(甲基仲丁基醚)、叔丁醇等,被送往共沸蒸馏塔分离.在共沸蒸馏塔底部流出纯度为98%以上的MTBE粗产品.粗MTBE送入MTBE精馏塔进一步分离,可得到高纯度的MTBE精产品.在共沸蒸馏塔内甲醇与醚后C4形成的共沸物从塔顶排出并送往甲醇萃取塔.在甲醇萃取塔中,以水为萃取剂,将醚后C4中的甲醇萃取,将形成的甲醇水溶液送进甲醇回收塔进行甲醇回收.甲醇回收塔底的水返回甲醇萃取塔,作为萃取水循环使用.而醚后C4则从甲醇萃取塔顶采出,并送往炼油厂,作为烷基化装置的生产原料.装置流程示意见图1.2005年MTBE合成装置醚后C4中甲醇和二甲醚的含量见表1.从表1可以看出,醚后C4中甲醇和二甲醚的含量都在1 000 μg/g以上,有时甚至超过10 000 μg/g.而生产要求醚后C4中甲醇含量不大于100 μg/g ,二甲醚含量不大于500 μg/g.因此应采取措施降低醚后C4中甲醇和二甲醚的含量.甲醇与水是完全互溶的.在进料负荷和进料中的甲醇含量一定时,甲醇萃取塔的萃取水量越大,萃余相醚后C4中的甲醇量越小[2],但萃取水量增加时,甲醇回收塔的处理负荷也随之增加.因此,如果萃取水量过大将造成甲醇回收塔的处理负荷超过其最大处理能力,导致甲醇回收塔返回甲醇萃取塔的萃取水中甲醇含量高,不利于萃取水对醚后C4中甲醇的充分萃取.相反,萃取水量越小,萃余相醚后C4中的甲醇含量就会偏大,达不到指标要求.因此需要通过改变萃取水量的实验确定提高甲醇萃取塔的萃取效果、使醚后C4中甲醇含量降低的萃取水量.MTBE合成装置甲醇回收塔是一个甲醇和水双组分高纯度分离的常压精馏塔.该塔为两段填料,灵敏板位于中部偏上.在塔内,由于甲醇挥发度比水大,提高甲醇回收塔灵敏板温度能降低从甲醇回收塔釜返回甲醇萃取塔的萃取水中甲醇的含量,进而可以使萃取水在萃取塔内充分萃取醚后C4中的甲醇,使醚后C4中甲醇含量降低.但在常压操作时,如果灵敏板温度高于90 ℃,容易使塔顶甲醇中的水含量超标.因此,将甲醇回收塔的灵敏板温度从75 ℃逐渐提高到90 ℃,考察甲醇回收塔的灵敏板温度对醚后C4中甲醇含量的影响.北京燕山石油化工有限公司MTBE合成装置的醚后C4是从2005年起才作为烷基化装置的生产原料的.2003年,MTBE合成装置生产能力由75 kt/a扩大到的150 kt/a时,并没有考虑对醚后C4中的甲醇含量进行控制.甲醇萃取塔的处理能力没有随装置的扩能而扩大,由此造成醚后C4中的甲醇含量的控制达不到烷基化装置的生产要求.因此,要从根本上解决醚后C4中甲醇含量高的问题,应更换或新增一个具有更大处理能力的甲醇萃取塔.2003年MTBE合成装置扩能改造时,同样没有对甲醇回收塔进行改造.甲醇回收塔原设计是处理生产75 kt/a MTBE所产生的甲醇水溶液.2003年以后合成装置的生产负荷已经提高到150 kt/a.该生产负荷所产生的甲醇水溶液已超过甲醇回收塔的设计处理能力.MTBE裂解装置也有一套甲醇回收系统,其中的甲醇回收塔与MTBE 合成装置的甲醇回收塔均为精馏塔.利用Aspen Plus模拟软件,采用NRTL模型对甲醇回收塔进行计算,结果见表2.从表2可以看出,在给定回流比为5.00时,处理MTBE合成、裂解两装置的所有甲醇水溶液(18 t/h,甲醇质量分数为34%)所需甲醇回收塔的理论级数为26.塔板效率按50%计算,实际所需级数为52.而MTBE裂解装置甲醇回收塔实际级数为57.因此,可以考虑用MTBE裂解装置甲醇回收塔替代MTBE合成装置的甲醇回收塔回收MTBE合成装置的甲醇水溶液.在MTBE合成装置中,没有对醚后C4中的二甲醚进行分离的工序.要降低醚后C4中二甲醚含量,只能从反应中抑制副产物二甲醚的生成量.在生成MTBE的醚化反应中,伴随着甲醇缩合生成二甲醚的副反应,对该副反应影响较大的因素有反应温度、空速和进料中甲醇的浓度,其中空速大小由装置负荷决定,而进料中甲醇的浓度取决于进料的醇烯比.在进料条件一定时,二甲醚的生成量随反应温度的升高而增加.混合C4中的异丁烯与甲醇反应生成MTBE的醚化反应温度一般控制在50~75 ℃.当反应器内的催化剂活性降低时,为了保持异丁烯的转化率,反应器的板层温度需随之提高.反应温度越高,二甲醚、异丁烯自聚物生成量越多.副产的二甲醚越多,醚后C4中的二甲醚含量越高.副产的异丁烯自聚物多,则易使催化剂的孔道堵塞,使催化剂的活性降低,又迫使反应温度继续提高,导致恶性循环.因此,提高催化剂的活性是解决提高异丁烯的转化率与减少二甲醚副产物之间矛盾的有效办法.醇烯比的控制是MTBE生产中十分关键的一个指标.实际生产中,醇烯比一般控制在1.0~1.2.醇烯比较大时,过量甲醇对催化剂有保护作用,即催化剂的活性端与甲醇结合,可减少催化剂被有害离子和化合物侵害.较高的醇烯比还可以使异丁烯的转化率增加,同时副产物异丁烯二聚体的含量可以大大降低.但是,过量的甲醇促进了甲醇缩合生成二甲醚的副反应.而且,过多的剩余甲醇增加了甲醇回收系统的处理负荷,使醚后C4与甲醇更难分离,导致醚后C4中甲醇含量偏高.醇烯比过小(不大于1)时,将迅速降低催化剂的活性,迫使反应温度提高,使二甲醚等副产物增加.准确控制醇烯比略大于1,既能保证甲醇在反应中有剩余但不会严重过量,又能对催化剂有一定的保护作用.因此,影响醚后C4中二甲醚含量的主要因素是催化剂的活性和反应器进料的醇烯比.将甲醇萃取塔的萃取水量由5 t/h提高到10 t/h.甲醇萃取塔的萃取水量提高后,甲醇回收塔的负荷随之增加.为了不影响甲醇回收塔顶甲醇的质量,应适当调整甲醇回收塔的热负荷、进出料量、回流量等相关工艺参数,以维持甲醇回收塔的灵敏板温度.改变萃取水量后,醚后C4中甲醇含量见表3.从表3可以看出,适当提高甲醇萃取塔的萃取水量对降低醚后C4中的甲醇含量有一定的作用,但是还达不到不大于100 μg/g的要求.但是萃取水量过大时,会导致萃取效果不稳定.这是因为,过大地提高甲醇萃取进水量的同时,也加大了甲醇回收塔的处理负荷,导致甲醇回收塔的处理效果不佳.从而导致甲醇回收塔底返回甲醇萃取塔的萃取水中甲醇含量较高.萃取水中甲醇含量高,则不能将醚后C4中的甲醇充分萃取.在不改变甲醇萃取塔操作条件的前提下,将甲醇回收塔的灵敏板温度从75 ℃逐渐提高到90 ℃,并调整相关的工艺参数,以保证甲醇回收系统的稳定运行.改变甲醇回收塔灵敏板温度后,醚后C4中甲醇的含量见表4.从表4可以看出,提高甲醇回收塔的灵敏板温度,可以降低甲醇回收塔底水中甲醇的含量,但是不能有效降低醚后C4中的甲醇含量.为了彻底解决甲醇萃取塔对甲醇萃取能力不足的问题,MTBE装置更换一个具有较大处理能力的甲醇萃取塔,两个甲醇萃取塔的规格对比见表5.2007年3月,新的甲醇萃取塔在MTBE装置中建成.在共沸蒸馏塔内,甲醇与醚后C4形成共沸物从塔顶排出并送往新的甲醇萃取塔.醚后C4则从新甲醇萃取塔顶采出,送往炼油厂作为烷基化装置的生产原料.采用新的甲醇萃取塔,在萃取水量约为7 t/h、甲醇回收塔灵敏板温度控制在86 ℃左右的条件下,醚后C4中甲醇含量见表6.从表6可以看出,采用新的甲醇萃取塔后,在不改变甲醇回收塔其它操作条件的情况下,MTBE合成装置醚后C4中的甲醇含量从1 000 μg/g以上降低到1 000 μg/g以下,但还没达到不大于100 μg/g的要求.由于MTBE裂解装置甲醇回收塔具有很强的甲醇回收能力.因此,可用MTBE裂解装置甲醇回收塔替代MTBE合成装置的甲醇回收塔处理甲醇萃取塔的甲醇水溶液.然后再把MTBE裂解装置甲醇回收塔底的部分水作为甲醇萃取塔的萃取水.用MTBE裂解装置甲醇回收塔替代MTBE合成装置的甲醇回收塔,在萃取水量为7 t/h、甲醇回收塔灵敏板温度控制在86 ℃左右的条件下,醚后C4中甲醇含量见表7.从表7可以看出,该项措施对降低醚后C4中的甲醇含量有明显的效果,醚后C4中的甲醇含量从大于100 μg/g降低到50 μg/g以下.为保证催化剂的活性,降低醚化反应温度,抑制副产物二甲醚的产生,应及时更换反应器中的催化剂.并且,在更换时采取以下措施,防止催化剂意外失活:①选择较好的催化剂.好的催化剂可以在高温苛刻反应条件下长期使用并保持一定的活性;较差的树脂催化剂,很快就有脱磺发生,反应活性容易降低.目前常用的催化剂为D-005型催化剂,但不同厂家生产的同型号催化剂在性能上有一定的差异,因此在使用中要注意比较.②催化剂装填时,不能将合格证、内袋、口绳等杂物装入反应器.③催化剂装入反应器后,尽快用甲醇浸泡,使甲醇与催化剂的活性基团结合,保护催化剂免受金属离子和含氮化合物的侵害.④催化剂在运输和储存时,必须注意防雨和防日晒,还须注意避开高温、干燥环境,防止催化剂脱水及被雨水中的化学物质污染.⑤因催化剂含水,所以应避免在严寒易冻的冬季更换催化剂,防止催化剂在0 ℃以下受冻而导致孔道破裂.更换催化剂前反应器出口温度为70~75 ℃,更换催化剂后,由于新催化剂的活性高,反应器出口温度降低到60 ℃左右.改造前,醇烯比的控制为人工取样分析和调整.通过人工从装置取样后,利用仪器分析进装置的混合C4原料中异丁烯的含量;操作人员再根据分析结果,通过计算后调整甲醇进料量.人工取样分析的结果有一段时间的滞后.为了更准确适时地控制装置进料醇烯比, 2005年MTBE装置引进近红外在线色谱分析仪.该仪器能对反应器的醇烯比做适时分析,并与DCS控制系统连接,将分析结果显示在DCS控制系统上.2007年开始,通过DCS控制系统将分析结果与甲醇进料控制阀串级并设置为"自动".这样,系统可以自动将反应器的醇烯比严格控制在1.03±0.1.控制过程见图2.准确控制醇烯比后MTBE装置醚后C4中二甲醚含量见表8.从表8可以看出,醇烯比的准确控制避免了甲醇严重过量、抑制了二甲醚的产生,醚后C4中二甲醚含量从原来的1 000 μg/g以上降低到500 μg/g以下.此外准确控制醇烯比后还对催化剂起到了一定的保护作用.2008年3月醚后C4中甲醇与二甲醚的含量见表9.从表9可以看出,实施以上措施后, MTBE合成装置醚后C4中的甲醇含量由原来的1 000 μg/g以上降低到50 μg/g以下,二甲醚的含量降低到500 μg/g以下,并趋于稳定,完全满足烷基化生产对醚后C4的要求.MTBE装置没有分离二甲醚的工序,因此,对醚后C4中二甲醚的控制,应着眼于醚化反应过程,减少副产物的产生;MTBE合成装置和MTBE裂解生产异丁烯装置均有甲醇回收系统,其工艺过程相同,两者存在可优化之处,在新装置设计时,可以考虑将两装置合建;醚后C4中的异丁烯与甲醇醚化成MTBE并提纯后,直接送入MTBE裂解反应器,再提纯为高纯度异丁烯;醚化反应剩余的甲醇及MTBE裂解产生的甲醇可在同一系统中回收.Key Words:MTBE; methanol; extraction; dimethyl ether; measure【相关文献】[1] 王迎春,高步良,陈国鹏,等.硫酸法烷基化原料的净化[J].石油炼制与化工,2003,34(1):15-18[2] 刘家祺.分离过程[M].北京:化学工业出版社,2002: 451-470AbstractThe causes of high methanol and DME contents in etherified C4fractions of MTBE synthesis unit at Yanshan Petrochemical Company were analyzed. Measures including the replacement of methanol extraction tower, using methanol recovery column of MTBE cracking unit as the methanol recovery column of MTBE synthesis unit, increase catalyst activity and properly control the ratio of methanol to olefin in feed, were adopted. Since then the methanol content and DME content in etherified C4fractions was dropped from more than 1 000 μg/g to less than50 μg/g and less than 500 μg/g, respectively, which could meet the requirements of downstream alkylation process.。
MTBE工艺手册

山西焦化股份有限公司山西焦化60万吨/年烯烃项目2万吨/年MTBE/丁烯-1装置工艺手册凯瑞化工股份有限公司二0一三年五月山西焦化股份有限公司山西焦化60万吨/年烯烃项目2万吨/年MTBE/丁烯-1装置MTBE单元工艺手册目录第一章工艺说明 (4)1.1 工艺原理、工艺特点 (4)1.2 操作变量分析 (5)第二章正常操作程序 (7)2.1 醚化单元 (7)2.2 催化蒸馏单元 (7)2.3 甲醇回收单元 (8)第三章开车准备 (10)3.1 R-4101A、R-4101B及SR-4101AB内部除锈和催化剂安装 (10)3.2 T-4101塔的安装方法 (10)3.3 T-4102、T-4103塔的安装 (11)3.4 投料前催化剂的脱水 (11)3.5 T-4103甲醇回收塔操作 (12)第四章装置的开工过程和开工方法 (13)4.1 醚化系统开车 (13)4.2 催化蒸馏系统开车 (13)4.3 甲醇回收系统开车 (14)第五章装置的停工过程和停工方法 (17)5.1 计划停工次序 (17)5.2 长期停工方法 (17)第六章事故处理原则 (19)6.1 反应器R-4101A/B的临时停工方法 (19)6.2 催化蒸馏塔T-4101的临时停工方法 (19)6.3 甲醇萃取塔T-4102、甲醇回收塔T-4103的临时停工方法 (20)第七章分析 (21)第八章工艺危险因素分析及控制措施 (22)8.1 职业危害因素及其影响 (22)8.2 职业危害因素的防治及治理 (23)第九章环境保护 (25)9.1 建议采用的标准规范 (25)9.2 污染物的排放及处理 (25)9.3 噪声控制 (26)9.4 环境监测机构及设施 (27)第十章设备检查与维护 (28)第一章 工艺说明1.1 工艺原理、工艺特点本工艺包采用预反应-催化蒸馏MTBE 合成技术路线。
1.1.1 MTBE 合成原理MTBE 合成原理以碳四原料中的异丁烯和甲醇为原料合成MTBE 的反应式为:(CH 3)2-C = CH 2+CH 3OH =(CH 3)3-C -O -CH 3在合成MTBE 的过程中,还同时发生少量的下列副反应:(1)异丁烯二聚生成二异丁烯(DIB )2(CH 3)2-C = CH 2 =(CH 3)3-C -CH 2-C (CH 3) = CH 2(2)异丁烯与原料中所含水份反应生成叔丁醇(TBA )(CH 3)2-C = CH 2 + H 2O =(CH 3)3-C -OH(3)甲醇缩合生成二甲醚(DME )2CH 3OH = CH 3-O -CH 3 + H 2O(4)1-丁烯与甲醇生成少量的甲基仲丁基醚(MSBE )CH 2=CH-CH 2-CH 3+CH 3OH = CH 3-CH 2-C (CH 3)-O -CH 3工业使用的催化剂一般为磺酸型二乙烯苯交联的聚苯乙烯结构的大孔强酸性阳离子交换树脂。
碳五含量增加对MTBE装置影响原因分析及对策

陕西延长(石油)集团有限责任公司延安石油化工厂(简称延安石油化工厂)120 kt/a 甲基叔丁基醚(MTBE)装置于2009年6月底建成投产,采用混相床-催化蒸馏技术,以大孔径强酸性阳离子交换树脂为催化剂生产MTBE。
装置所需C4原料由气分装置供给,原料甲醇外购。
装置运行过程中,因C4原料组分不合格,尤其是碳五含量的增加对装置运行产生巨大的影响,转化率和产品纯度下降,严重的影响了产品质量,甚至存在催化剂失活的风险。
为保证装置长、稳、安、满、优运行,分析了影响因素并采取相应措施,实现了装置长周期平稳运行。
1 MTBE装置对原料的要求MTBE原料碳四馏分由气体分馏装置提供,要求碳五含量不大于1%(m/m)[1],设计原料组成如表1所示。
2 原料组分中碳五含量的变化2012年9月7日至23日、2014年5月8日至21日,根据生产装置的需要,将气分装置脱戊烷塔(201-C-105)停运,脱丙烷塔(201-C-101)底出料(包含碳四和碳五组分)直接作为MTBE原料,从而导致了MTBE原料组分发生了变化。
在脱戊烷塔停运后,碳四原料中碳五含量较停运前明显增大,且超出了合格指标。
如果气分加工量按1920吨/天(80吨/小时)计算,每天将有27吨(收率按1.40%计算)碳五作为原料进入到MTBE装置,从而导致了产品质量、异丁烯转化率及操作参数发生了较大的变化。
3 碳五含量的增加对装置的影响3.1 对MTBE产品纯度的影响在原料中碳五含量增加后,会导致反应温度升高,副反应1-丁烯和甲醇反应生成甲基仲丁基醚(MSBE)的反应加剧,同时原料中所含水分与异丁烯反应,生成叔丁醇(TBA)。
由于其副反应的加剧,生成较多的副产物,导致了MTBE产品质量不合格.在碳五含量增加前MTBE产品纯度均在合格范围内,均在98%以上。
而在其增加后,由表2可知,平均产品纯度下降至96.70%,副反应生成的叔丁醇、甲基仲丁基醚、碳八增加,造成了产品质量不合格。
论影响MTBE产品质量的因素及解决措施

论影响MTBE产品质量的因素及解决措施MTBE是一种重要的燃料添加剂,被广泛应用于汽油中,可以提高汽油辛烷值,减少尾气排放。
MTBE产品质量的好坏直接影响到汽油品质及环境保护。
本文将讨论影响MTBE产品质量的因素以及相应的解决措施。
第一,原料质量。
MTBE的原料主要包括异戊二烯(IWC)和甲醇。
IWC的纯度和含杂质的浓度会影响到MTBE产品的纯度和杂质含量。
甲醇的纯度和含水量也会对MTBE的纯度产生影响。
为了保证MTBE产品的质量,需要对原料进行严格的选择和检测,以确保其符合规格要求。
还可以采用合理的配比策略来减少杂质的影响。
第二,催化剂的选择和活性。
MTBE的合成需要使用催化剂,一般选择固体酸催化剂。
催化剂的选择和活性对MTBE产品的产率和选择性有重要影响。
合理选择合适的催化剂,并进行优化和调整,可以提高MTBE产品的质量。
还需要保持催化剂的活性,定期进行再生或更换,以保持稳定的反应性能。
反应工艺参数的控制。
反应温度、压力、反应时间等工艺参数的选择和控制对MTBE产品的质量有重要影响。
温度过高会导致副反应和杂质生成,温度过低会影响反应速率和产率。
压力过高也会导致副反应和产物分解。
反应时间过长会降低产品的选择性。
需要根据具体情况选择合适的反应工艺参数,并通过实验和优化来控制和调整这些参数,以保证MTBE产品的质量。
第四,产品分离和纯化工艺。
MTBE产品中可能含有未反应的原料、副反应产物和杂质等。
为了获得高纯度的MTBE产品,需要进行分离和纯化处理。
常见的方法包括蒸馏、吸附和萃取等。
蒸馏是常用的分离工艺,可以根据组分之间的沸点差异进行分离。
吸附和萃取可以通过选择合适的吸附剂或溶剂来分离MTBE和其他组分。
还可以考虑使用适当的添加剂来改善分离和纯化工艺的效果。
影响MTBE产品质量的因素包括原料质量、催化剂选择和活性、反应工艺参数控制以及分离和纯化工艺等。
通过选择合适的原料、催化剂和工艺参数,以及进行有效的分离和纯化处理,可以提高MTBE产品的质量,并满足相关的标准和要求。
MTBE裂解制异丁烯催化剂的改进

中 图分 类 号 :E 2 . 1 T 64 9
异 丁烯是 重要 的精 细化工 原料 。高 纯度 异丁烯 (99 t ) 9.w% 可用 于 制 造 丁 基 橡 胶 、 异
2 1 催化 剂的 改进 .
艺 的完 善起到 了积 极 推动作 用 , 助 于异 丁 烯及 下 有 游 产品 的生产 。
2 2 工艺 流程 改进 .
.
催 化剂更 换 的 同时 , 艺流程 也做 了相应 改变 : 工 原工艺 为从 反 应 器 出来 的裂 解气 直 接 进 入 水 吸 收
第1 7期
杜春燕等 : T E裂解制异丁烯催化剂的改进 MB
l a
催化剂 的装 填尺 寸见 表 1 。反应 管 5× . , 25
10 g 。 6 k ) 该 反 应 为 吸 热反 应 , 高 反应 温 度 有 利 于裂 解 提 过 程 的进 行 。 同时 , 反应 又是 浓度增 大 的反应 , 该 增 加 反应 压 力不 利 于主反 应 的进行 , 另外 , 反应进 行 该
丁烯选 择 性 大 于 9 .% , 品异 丁烯 纯 度 大 于 90 产
9 . % 。新 型催化 剂 的缺点 : 化剂颗 粒小 , 击 易 99 催 撞
粉碎 。 2 1 2 催化 剂装填 ..
I
-
c H 3
。
嘶 0c a {c + H 长 5m, 10 根 , 一 一H 丽 =l 0 C 。 t I c 一 壬 z 总共 63 共装催化剂 30L(合成重量是 2
平 均 单 耗 下 降 0 0 tt 节 约 原 料 : 0 0 ×0 0 .6 , / 30 .6=
品纯 度 由 9 .7 升 高 到 9 . 3 , 耗 由 91% 95 % 单 1 7 / 降 低 到 1 6 tt 年 节 约 原 料 费 用 1 8 . 1tt . 5/ , 0
MTBE装置催化精馏塔段的优化设计
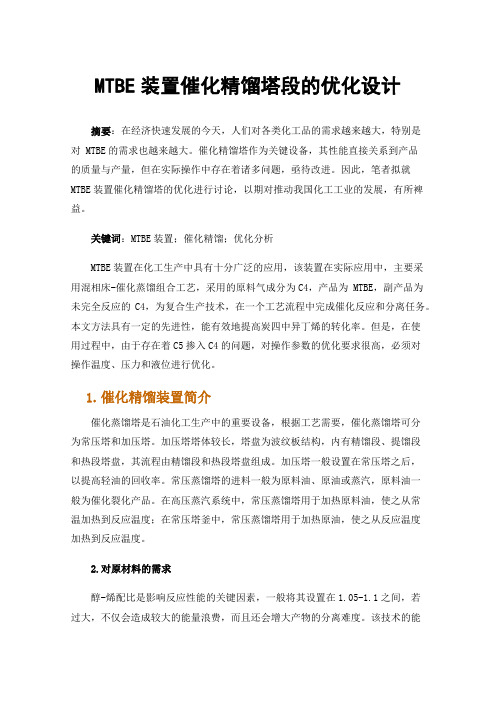
MTBE装置催化精馏塔段的优化设计摘要:在经济快速发展的今天,人们对各类化工品的需求越来越大,特别是对 MTBE的需求也越来越大。
催化精馏塔作为关键设备,其性能直接关系到产品的质量与产量,但在实际操作中存在着诸多问题,亟待改进。
因此,笔者拟就MTBE装置催化精馏塔的优化进行讨论,以期对推动我国化工工业的发展,有所裨益。
关键词:MTBE装置;催化精馏;优化分析MTBE装置在化工生产中具有十分广泛的应用,该装置在实际应用中,主要采用混相床-催化蒸馏组合工艺,采用的原料气成分为C4,产品为 MTBE,副产品为未完全反应的C4,为复合生产技术,在一个工艺流程中完成催化反应和分离任务。
本文方法具有一定的先进性,能有效地提高炭四中异丁烯的转化率。
但是,在使用过程中,由于存在着C5掺入C4的问题,对操作参数的优化要求很高,必须对操作温度、压力和液位进行优化。
1.催化精馏装置简介催化蒸馏塔是石油化工生产中的重要设备,根据工艺需要,催化蒸馏塔可分为常压塔和加压塔。
加压塔塔体较长,塔盘为波纹板结构,内有精馏段、提馏段和热段塔盘,其流程由精馏段和热段塔盘组成。
加压塔一般设置在常压塔之后,以提高轻油的回收率。
常压蒸馏塔的进料一般为原料油、原油或蒸汽,原料油一般为催化裂化产品。
在高压蒸汽系统中,常压蒸馏塔用于加热原料油,使之从常温加热到反应温度;在常压塔釜中,常压蒸馏塔用于加热原油,使之从反应温度加热到反应温度。
2.对原材料的需求醇-烯配比是影响反应性能的关键因素,一般将其设置在1.05-1.1之间,若过大,不仅会造成较大的能量浪费,而且还会增大产物的分离难度。
该技术的能耗主要体现在甲醇的循环利用上,而甲醇的质量分数不能高于共沸混合物的质量分数,是导致分离难度大的重要原因。
若蒸馏塔的操作压力为0.6兆帕,则甲醇在C4中的最大浓度为7.4一,若高于此浓度,则会直接引起甲醇落入到塔底,从而引起 MTBE质量不达标,若该比例过小,则甲醇的反应量不够,易引起异丁烯的转化率不足。
醚后碳四异构化技术增产MTBE

醚后碳四异构化技术增产MTBE作者:李子豪来源:《中国化工贸易·下旬刊》2018年第04期摘要:通过对直链烯烃骨架异构化反应的分析,结合碳四分子筛骨架异构化的特点,根据乌石化公司MTBE装置特点和醚后碳四性质,因地制宜采用无压缩机、无产物分馏塔的独特碳四异构化工艺,大幅增产MTBE。
关键词:醚后碳四;异构化;MTBE1 醚后碳四异构化项目背景MTBE装置是将含有异丁烯的碳四馏份与甲醇按照比例进行混合,在一定的温度和压力条件下,在强酸性阳离子交换树脂催化剂床层中使异丁烯与甲醇发生醚化反应生成MTBE。
MTBE是近年很好的汽油添加剂,其辛烷值高、可以与汽油以任意比例互溶而不发生。
汽油中添加MTBE可以使燃料消耗下降5-7%左右,并能减少汽车尾气对大气的污染。
乌石化公司现有一套5万吨/年MTBE生产装置,由于原料中异丁烯的含量较低,MTBE 装置一直低负荷运行,而装置副产的醚后碳四以前主要用作民用液化气燃烧,资源浪费严重。
公司综合考虑MTBE装置特点和醚后碳四性质,并依托现有碳五异构化单元再生系统于2015年新建一套12.6万吨/年醚后碳四异构化单元,使醚后碳四中的高浓度正构丁烯进行异构化反应转化为异丁烯,再进入MTBE装置醚化,解决因异丁烯量不足导致MTBE装置负荷低的问题,并提高经济效益。
2 技术路线2.1 直链烯烃骨架异构化催化反应及其机理一般认为,正丁烯骨架异构化主反应是单分子反应机理,经过正碳离子中间体。
而且正碳离子重排通过一个带质子的环丙烷,当该环被打开后,便形成伯丁基正碳离子,最后形成异丁烯。
正丁烯骨架异构同时伴随着各异构体之间的双键异构和顺反异构这两个可逆反应。
在理想状态,丁烯-l、顺丁烯-2、反丁烯-2、异丁烯四个组分达到平衡状态。
异构化的主要副反应是丁烯二聚生成C8烃,继而断裂成C3、C5烃[1]。
2.2 分子筛催化工艺及催化剂分子筛催化工艺中所采用的催化剂活性比氧化铝高,反应温度可以降低到350~400℃左右,收率提高40%左右。
- 1、下载文档前请自行甄别文档内容的完整性,平台不提供额外的编辑、内容补充、找答案等附加服务。
- 2、"仅部分预览"的文档,不可在线预览部分如存在完整性等问题,可反馈申请退款(可完整预览的文档不适用该条件!)。
- 3、如文档侵犯您的权益,请联系客服反馈,我们会尽快为您处理(人工客服工作时间:9:00-18:30)。
树脂催化剂的使用寿命及失活的预防措施
近30年来,大孔强酸型离子交换树脂由于其特有的孔结构和优异
的催化性能在国内外以合成MTBE为代表的醚化领域作为催化剂,得
到了广泛的工业应用,并同时还在不断开发和改进.
树脂催化剂在工业应用中随着时间的推移,会因各种原因失活或
中毒,从而导致异丁烯转化率下降及使用寿命缩短.生产管理人员,特
别是生产厂家要有足够认识,以便正确的选择催化剂和采取相应的有
效措施以延长催化剂使用寿命。
一、 大孔强酸型树脂催化剂的特点及发展
1、 树脂催化剂的特点
国内外合成MTBE工艺所用的催化剂,基本上是大孔强酸性阳离
子交换树脂。这种树脂催化剂是由苯乙烯和二乙烯苯在适量致孔剂作
用下形成具有大孔网状结构,再经磺化后使之带有磺酸基团的一种高
分子聚合物。其中骨架有聚苯乙烯,二乙烯苯是交联体,而苯环上的
磺酸基团则是起催化作用的活性中心。商家通常以氢型供货。
树脂催化剂的理化性质主要包括以下几方面:
(1) 水分含量——树脂通常含水约50%左右,可以提供水分小的风
干品以利使用方便。
(2) 体积交换容量——每毫升干树脂中氢离子的毫克当量数。树脂
催化剂的交换容量是决定其所具催化活性的重要因素,因此它
是催化剂出厂产品规格的关键指标之一。
(3) 孔结构特性——主要是孔容、比表面积和平均孔径,催化剂的
无数网状孔道是反应物料到达活性中心的通路,孔容高、比表
面大对醚化反应是有利的,同时孔径合适有利于反应、也有利
于防止二聚副产物的阻塞。
2、 树脂催化剂的改进和发展
80年代以来,大孔强酸型离子交换树脂催化剂在合成MTBE工
艺中得到广泛的工业应用。由Pwrolite公司生产的A-15树脂
催化剂(A-15的交换容量≥4.7mmol/g)就是一种。90年代中
后期该公司生产的A-35在欧美一些国家的MTBE装置中得到应
用,在同样条件下,A-35比A-15使异丁烯转化率可提高2%-5%
而液相空速提高10%以上。其主要原因是A-35比A-15具有更
高的交换容量(A-35的交换容量≥5.2mmol/g)即A-35比A-15
有更高的催化活性。国内90年代初的催化剂交换容量也达到了
像A-15的4.7mmol/g,90年代未也开始达到A-35的5.2mmol/g。
但相同的交换容量使用寿命却相差很大,比如进口的几套装置
国产化后最明显的就是使用寿命才是进口的一半。可见孔结构
对使用寿命的影响很大,因此目前催化剂的发展方向是向合适
的孔径、合适的孔容和更大的比表面积方向发展。
二、 树脂催化剂的失活
树脂催化剂在长期使用中会因各种原因造成失活或中毒,大体
可归为以下几种类型:
1、 阳离子交换中毒失活
醚化原料中存在的金属离子或碱性氮化物(氨和胺),会通过离
子交换,使树脂催化剂上的磺酸基团被中和。其结果表现为催
化剂的交换容量降低,活性中心减小.国内对此中毒的研究表明:
阳离子交换中毒表现为活塞推移式,即沿催化剂床层深入,最先
接触这些杂质的床层先中毒,中毒饱和后依次推移,床层呈现明
显饱和段、过渡段和空白段。
炼厂碳四原料中常因上游水不好带来的钠离子及钙离子,可
溶性锈蚀物的铁离子和铬离子,催化裂化分子筛催化剂的微量
铝离子和硅离子,以及炼厂碳四原料中通常含有的氨、甲胺等
碱性氮化物,都属于阳离子交换的毒物。
2、 可水解氮化物导致中毒失活
采用分子筛催化剂的催化裂化碳四和碳五原料中通常含有腈类
物质(如乙腈、丙腈),它们在醚化反应条件下与水反应直接水
解而生成氨,导致中和催化剂的磺酸基团。蒸汽裂解碳四原料
中会携带其上游丁二烯抽提的溶剂(DMF和NMP),它们与水反
应的产物,也会与催化剂的磺酸基团作用,导致催化剂失活。
应该注意:这些可水解氮化物造成的失活与上述阳离子交换失
活形成的活塞推移式中毒有所不同,是属于整个催化剂床层的
扩散性中毒。
3、 磺酸基团的脱落
树脂催化剂在较高温度下会发生聚合链的断裂和磺酸基团脱
落,从而导致活性永久损失。据研究表明,树脂脱磺与温度密
切有关。通常在大于80℃,树脂开始有脱磺,至120℃脱磺则
非常明显。
4、催化剂孔道阻塞
碳四原料中的二烯烃(丁二烯)随反应温度的增高,有强烈的聚
合倾向,所形成的聚合物积在树脂催化剂的孔道里,异丁烯的聚合物、
碳五中的双烯烃聚合物及原料中的胶质都会积在催化剂孔道里而堵
塞催化剂孔道,会阻塞反应物向活性中心的扩散,从而导致活性下降。
三、 催化剂失活的预防措施
1、 因地制宜合理选择原料净化方式
除操作因素外,防止催化剂中毒的最主要措施是对合成MTBE
的原料采用适当方式加以净化。应该注意到,来自炼厂FCC的
混合碳四与蒸汽裂解碳四含有的能使催化剂中毒的毒物多而复
杂。
2、 原料预处理的方式包括水洗和保护床二种,均在工业上得到采
用。
3、 水洗法通常是以无离子水或蒸汽凝结水与碳四原料在水洗塔中
逆向多次接触,来除去那些水溶性且在水中的分配系数远大于在烃中
分配系数的催化剂毒物。采用这种方法可以有效地脱除炼厂碳四原料
中夹带的碱性物质(NaOH、醇胺溶剂)、甲胺以及蒸汽裂解碳四中夹
带的丁二烯抽提溶剂(DMF和NMP)。但是,采用水洗法不能除去
二甲胺,仅能部分除去乙胺,对脱除乙腈的效果也十分有限。
保护床的原理是让一部分树脂对付阳离子来交换中毒以保护
催化剂,这种方法又称牺牲床(俗称离子过滤器),它对活塞推移式
中毒非常有效。但需注意用它来对付导致催化剂扩散性中毒的效果不
甚明显。
2、 保护床的设置
保护床的设置的以下几方面需要考虑:
(1) 保护床设在反应器外时,碳四原料中应配以适量甲醇,以防二
聚造成急剧温升;进保护床的温度应尽量低,以免醚化反应温升
过大;设置二台以便切换操作;所装树脂不宜太多,否则与反应器
无太大区别;单独用于净化甲醇原料的应设在催化蒸馏塔上游。
(2) 保护床设在反应器内,即净化和反应合一方式。这种方式避免
了器外设置不易控制温度的敝病,又能充分选择树脂催化剂反
应性能。但是缺乏在线更换净化剂的灵活性。
四、 保护和延长催化剂寿命的注意事项
1、 避免采用气体分馏脱碳三塔底物料直接作为MTBE的原料,这
种物料中可能携带有其上游脱硫或脱硫醇工艺所使用的碱性物
质,会导致催化剂寿命减少。
2、 原料碳四中的碳五含量的多少对MTBE的生产影响较大,一般
碳五含量小于1%时,产品质量比较正常,而大于2%时MTBE
的产品质量将达不到设计要求,同时异丁烯的转化率降低,副
反应产物增加。同时碳五中的双烯烃易在树脂催化剂上聚合形
成胶质,堵塞催化剂孔道,从而降低催化剂寿命,因此要注意
控制原料中碳五的含量。
3、 对于MTBE催化蒸馏工艺,在操作中应切实控制好灵敏点温度,
防止催化剂床超温使催化剂的磺酸集团高温脱落,同时温度越
高相应的孔道堵塞的速率越快,催化剂失活的越快。
4、 采用常规生产MTBE且下游无烷基化工艺时,可在操作后期适
当提高第二反应器的温度,以弥补因第一反应器催化剂部分失
活造成的转化率下降。
五、 催化剂的寿命
1、 催化剂的使用寿命基本可以描述为:催化剂寿命∝体积交换容
量;催化剂寿命∝比表面积。
2、 因此选择催化剂可以对其进行检验,达到科学正确的选择催化
剂。