连铸连轧技术
短流程连铸连轧成套装备的检测技术与质量控制

短流程连铸连轧成套装备的检测技术与质量控制随着钢铁行业的发展和技术进步,短流程连铸连轧技术在钢铁生产中得到广泛应用。
短流程连铸连轧成套装备由连铸机、连轧机和配套设备组成,能够直接将铁水连续铸造成坯料,并通过连续轧制工艺进行成形,最终生产出各类钢产品。
而为确保短流程连铸连轧装备生产的钢材质量,需要依靠有效的检测技术和质量控制手段。
一、检测技术1. 成分检测技术:短流程连铸连轧生产出的钢材种类繁多,要求的成分及其精度也不同。
因此,通过使用光谱分析仪等现代化的成分检测仪器,可以快速、准确地分析出钢材的成分,确保其符合质量标准。
2. 形貌检测技术:短流程连铸连轧生产的钢材形貌要求较高,需要保持均匀的厚度、平整的表面和较少的缺陷。
利用激光坡度仪、高精度测厚仪等设备,可以对钢材进行形貌检测,确保其达到质量要求。
3. 缺陷检测技术:连铸连轧过程中,钢材容易出现缺陷,如气泡、夹杂物、麻点等。
采用超声波、射线和磁粉等无损检测技术,可以对钢材进行缺陷检测,确保产品质量。
4. 物理性能检测技术:钢材的物理性能对其使用寿命和安全性具有重要影响,需要通过拉伸试验、冲击试验、硬度测试等手段进行检测,确保产品的物理性能符合标准。
二、质量控制1. 生产过程控制:通过在短流程连铸连轧生产过程中监测、调整参数,如冷却水流量、坯料温度、轧辊间隙等,保持生产过程的稳定性和可控性,确保产品质量。
2. 质量管理体系:建立完善的质量管理体系,包括编写质量管理手册、制定工艺流程文件、制定操作规程等。
通过监督、检查与评审等手段,对质量管理体系进行持续改进,并执行ISO9000质量管理体系标准,提高产品质量。
3. 检验与检测:在生产过程中,对关键工序进行全程抽检与检测,并依据检测结果进行调整和改进。
同时,建立合理的产品抽样方案,并委托第三方实验室进行产品质量检测,确保产品符合质量标准。
4. 过程监控与问题处理:通过实时监控生产过程中的关键节点和指标,如成型温度、材料流速等,及时发现问题并进行处理。
钢的连铸连轧技术
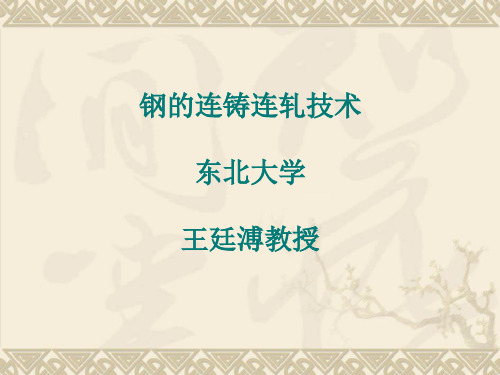
(3) 热加工履历不同,N,C,S等析出物的固溶析出历
程,机制不同,其形态分布通过控轧控冷更易控制,更有 利于合金元素作用的发挥和组织性能的提高。冷装既析出 再固溶较难;连铸连轧时无(少)析出,始终固溶再经变 形诱导析出,更细更均布,未析出部分再经相变沉淀硬化, 进一步提高性能质量; (4) 连铸连轧工艺控制得当更有利于钢的高温塑性,防 止裂纹等缺陷的产生,提高 成形质量,CC-DR,DHCR防 止“红送裂纹”产生。
2.2 铸坯质量的保证技术
(1)保证连铸坯质量是连铸及连铸连轧工艺得以成立 和发展的前提(物美价廉) 由于炼钢技术(炉外精练)提高了钢的纯净度, (S,P,N,H,O等)杂质含量由过去500×10-6降至100×10- 6,及连铸技术的提高(保护浇注,潜入式水口,保护渣润 滑,电磁搅拌,气水雾化冷却,软压下,压缩浇铸等)已使 连铸坯质量基本得到保证。一般无缺陷率可在96%以上,满 足生产要求,故检测难而无需检测。在诸多内外表面缺陷中, 最障碍连铸连轧工艺实现的是表面裂纹缺陷,因其不能进行 表面清理; (2)表面裂纹的形成机理:开裂必须:受力;弱点,应 力集中超过断裂强度。一般碳钢三个高温脆性区为图2所示。
2.1 连铸连轧的金属学特点 (与传统工艺相比)
(1) 铸坯热履历不同使原始晶粒组织不同 1)近终形连铸快冷,枝晶短,晶粒细均,偏析少, 有利; 2)但历程无相变细化晶粒作用,无γ-α-γ,易使原 始γ体晶粒粗大, (α+γ)HCR甚至易产生混晶 (原γ长大,α被吞蚀或变成细的新γ晶), 不利。这只 有通过粗轧高温大压下再结晶作用来补救,但低温热装却与 冷装无异; (2) 热加工履历不同,液芯软压下改善中心组织,晶粒 细化作用大,疏松偏析少;;
2 流 3 × 9 0( 公 称 ) 涟源钢 7 铁厂 钢)转炉 机 / 1 05 t 实 际 出 ( CSP 铸 ( 800~1600) 机 立弯型 ( 70~55) × 230 SMS 轧 0 . 8 ~1 2. 7 炉 291m× 2 7 机架 辊底式均热 2 8. 0 2004-3
连铸连轧新技术培训

连铸连轧新技术培训1. 概述连铸连轧是一种现代金属加工技术,通过连续铸造和连续轧制工艺,可高效地生产各种形状和尺寸的金属材料。
这项技术在钢铁、铜、铝等金属行业得到广泛应用,它具有节能、高效、减少环境污染等优点。
为了提高工人的专业技能和生产效率,连铸连轧新技术培训成为企业重要的任务之一。
2. 连铸连轧工艺概述连铸连轧是一种集连续铸造和连续轧制于一体的金属加工流程。
其基本原理是通过连铸机将熔融金属倾注到连铸结晶器中,通过结晶器内的冷却工艺将金属液固化成坯料;然后将坯料传送至连轧机进行连续轧制,最终得到所需尺寸的金属材料。
连铸连轧工艺具有以下优点:•节省能源:连续工艺能够减少能量损失和热能浪费。
•提高生产效率:连铸连轧工艺可以实现高速连续生产,减少工艺中的停机时间,提高材料的产量。
•保证产品质量:连续工艺可以有效控制金属材料的组织和性能,提高产品的一致性。
•减少环境污染:连铸连轧工艺可以减少废水、废气和废渣的排放,是一种环保的金属加工技术。
3. 连铸连轧新技术培训的意义连铸连轧技术的应用给企业带来了巨大的改变,但也带来了对工人技能要求的提升。
新技术的引入需要对操作人员进行培训,以确保其熟练掌握新工艺和设备操作,提高工作效率和产品质量。
连铸连轧新技术培训的意义主要包括以下几个方面:3.1 提高工人技能水平通过新技术培训,工人能够掌握先进的操作技能和工艺知识,提高他们在连铸连轧生产线上的技能水平。
准确、熟练的操作有助于提高工作效率和产品质量。
3.2 降低操作失误率连铸连轧工艺操作复杂,一些操作失误可能导致设备故障和产品缺陷。
通过培训,可以帮助工人了解工艺流程和设备操作规范,提高操作的准确性和规范性,降低操作失误率。
3.3 提高生产效率熟练的连铸连轧技术操作员能够高效地完成生产任务,减少停机时间,提高生产线的运行效率。
培训可以帮助工人学习提高操作速度和配合其他操作员的技巧,从而提高生产效率。
3.4 推动企业发展连铸连轧新技术的应用可以提高产品的质量和竞争力,推动企业在市场上的发展。
连铸连轧工艺
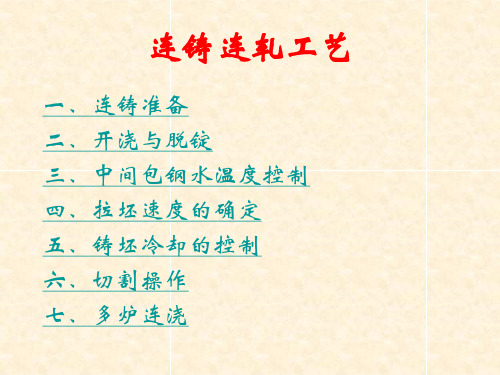
3.3 钢水在钢包中的温度控制
根据冶炼钢种严格控制出钢温度, 根据冶炼钢种严格控制出钢温度,使其在较窄的范围 内变化;其次,要最大限度地减少从出钢、钢包中、 内变化;其次,要最大限度地减少从出钢、钢包中、钢包 运送途中及进入中间包的整个过程中的温降。 运送途中及进入中间包的整个过程中的温降。 实际生产中需采取在钢包内调整钢水温度的措施: 实际生产中需采取在钢包内调整钢水温度的措施: ①钢包吹氩调温。 钢包吹氩调温。 ②加废钢调温。 加废钢调温。 ③在钢包中加热钢水技术。 在钢包中加热钢水技术。 ④钢水包的保温。 钢水包的保温。
• △T4:钢包精炼结束钢水在静置和运往连铸
平台的温降
分析: 分析: 热量损失形式:钢水上表面通过渣层的热损失、 热量损失形式:钢水上表面通过渣层的热损失、 钢包包衬吸热。 钢包包衬吸热。 热量损失大小:钢包内衬吸热降低, 热量损失大小:钢包内衬吸热降低,加了保温 温降减小低。 剂,温降减小低。
• △T5:钢水从钢包注入中间包过程中产生的温降 分析: 分析: 热量损失形式:辐射热损失、对流热损失、钢包吸热。 热量损失形式:辐射热损失、对流热损失、钢包吸热。 影响因素:钢流保护状况;中间包的容量、材质、 影响因素:钢流保护状况;中间包的容量、材质、 烘烤温度及保温措施 降低热量损失的措施: 降低热量损失的措施: 钢流需保护,采用长水口; ①钢流需保护,采用长水口; 减少浇铸时间; ②减少浇铸时间; 充分预热中间包内衬; ③充分预热中间包内衬; 中间包钢液面添加保温剂; ④中间包钢液面添加保温剂; 速的确定和控制
4.1、拉速定义: 4.1、拉速定义:拉坯速度是以每分钟从结晶器拉出的铸坯 长度来表示。拉坯速度应和钢液的浇注速度相一致。 长度来表示。拉坯速度应和钢液的浇注速度相一致。 4.2、拉速控制的意义:拉速控制合理, 4.2、拉速控制的意义:拉速控制合理,不但可以保证连铸 生产的顺利进行,而且可以提高连铸生产能力, 生产的顺利进行,而且可以提高连铸生产能力,改善铸坯的 质量。现代连铸追求高拉速。 质量。现代连铸追求高拉速。 4.3、拉速确定: 4.3、拉速确定: 确定原则: 1)确定原则: 确保铸坯出结晶器时的厚度能承受钢水的静 压力而不破裂,对于参数一定的结晶器,拉速高时, 压力而不破裂,对于参数一定的结晶器,拉速高时,坯壳 反之拉速低时则形成的坯壳厚。 薄;反之拉速低时则形成的坯壳厚。 一般认为,拉速应确保出结晶器的坯壳厚度为12 14mm。 12一般认为,拉速应确保出结晶器的坯壳厚度为12-14mm。
连铸连轧工艺
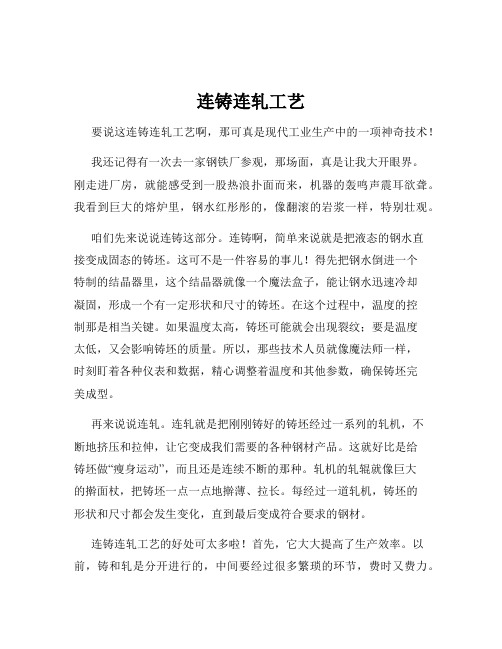
连铸连轧工艺要说这连铸连轧工艺啊,那可真是现代工业生产中的一项神奇技术!我还记得有一次去一家钢铁厂参观,那场面,真是让我大开眼界。
刚走进厂房,就能感受到一股热浪扑面而来,机器的轰鸣声震耳欲聋。
我看到巨大的熔炉里,钢水红彤彤的,像翻滚的岩浆一样,特别壮观。
咱们先来说说连铸这部分。
连铸啊,简单来说就是把液态的钢水直接变成固态的铸坯。
这可不是一件容易的事儿!得先把钢水倒进一个特制的结晶器里,这个结晶器就像一个魔法盒子,能让钢水迅速冷却凝固,形成一个有一定形状和尺寸的铸坯。
在这个过程中,温度的控制那是相当关键。
如果温度太高,铸坯可能就会出现裂纹;要是温度太低,又会影响铸坯的质量。
所以,那些技术人员就像魔法师一样,时刻盯着各种仪表和数据,精心调整着温度和其他参数,确保铸坯完美成型。
再来说说连轧。
连轧就是把刚刚铸好的铸坯经过一系列的轧机,不断地挤压和拉伸,让它变成我们需要的各种钢材产品。
这就好比是给铸坯做“瘦身运动”,而且还是连续不断的那种。
轧机的轧辊就像巨大的擀面杖,把铸坯一点一点地擀薄、拉长。
每经过一道轧机,铸坯的形状和尺寸都会发生变化,直到最后变成符合要求的钢材。
连铸连轧工艺的好处可太多啦!首先,它大大提高了生产效率。
以前,铸和轧是分开进行的,中间要经过很多繁琐的环节,费时又费力。
现在呢,一气呵成,从钢水到钢材,速度快得惊人。
其次,它还能节省能源和原材料。
因为整个过程是连续的,减少了中间的停顿和运输,也就降低了能源的消耗和材料的损失。
而且啊,这种工艺生产出来的钢材质量也更稳定,性能更优越。
在实际应用中,连铸连轧工艺已经广泛用于生产各种类型的钢材,比如建筑用的螺纹钢、汽车制造用的板材等等。
可以说,我们生活中的很多东西都离不开它。
不过,这连铸连轧工艺也不是没有挑战的。
比如说,设备的维护就是个大问题。
那些轧机和结晶器整天高强度工作,很容易出现故障。
一旦出了问题,就得赶紧抢修,否则会影响整个生产进度。
还有就是对操作人员的技术要求很高,他们得时刻保持警惕,应对各种突发情况。
短流程连铸连轧成套装备的工作原理和技术优势
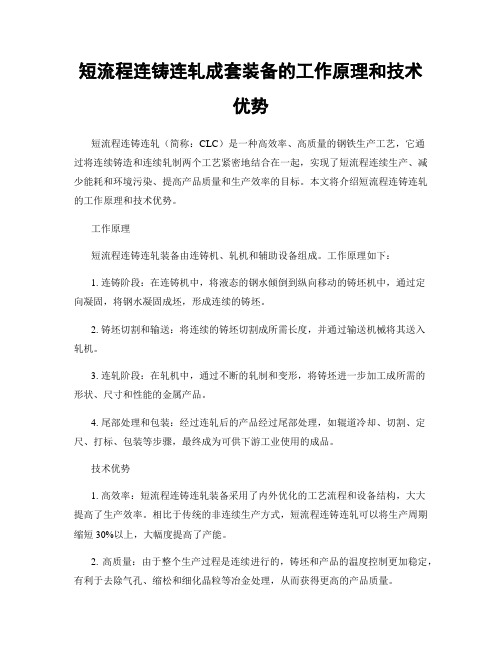
短流程连铸连轧成套装备的工作原理和技术优势短流程连铸连轧(简称:CLC)是一种高效率、高质量的钢铁生产工艺,它通过将连续铸造和连续轧制两个工艺紧密地结合在一起,实现了短流程连续生产、减少能耗和环境污染、提高产品质量和生产效率的目标。
本文将介绍短流程连铸连轧的工作原理和技术优势。
工作原理短流程连铸连轧装备由连铸机、轧机和辅助设备组成。
工作原理如下:1. 连铸阶段:在连铸机中,将液态的钢水倾倒到纵向移动的铸坯机中,通过定向凝固,将钢水凝固成坯,形成连续的铸坯。
2. 铸坯切割和输送:将连续的铸坯切割成所需长度,并通过输送机械将其送入轧机。
3. 连轧阶段:在轧机中,通过不断的轧制和变形,将铸坯进一步加工成所需的形状、尺寸和性能的金属产品。
4. 尾部处理和包装:经过连轧后的产品经过尾部处理,如辊道冷却、切割、定尺、打标、包装等步骤,最终成为可供下游工业使用的成品。
技术优势1. 高效率:短流程连铸连轧装备采用了内外优化的工艺流程和设备结构,大大提高了生产效率。
相比于传统的非连续生产方式,短流程连铸连轧可以将生产周期缩短30%以上,大幅度提高了产能。
2. 高质量:由于整个生产过程是连续进行的,铸坯和产品的温度控制更加稳定,有利于去除气孔、缩松和细化晶粒等冶金处理,从而获得更高的产品质量。
3. 节约能源和环保:短流程连铸连轧装备采用了先进的能量回收和净化设备,有效利用余热和废气等资源,降低了能耗和环境污染。
相较于传统工艺,其能源消耗可以减少20%以上,有利于可持续发展。
4. 灵活性:短流程连铸连轧工艺适应性强,可生产多种材料和规格的产品,包括普通碳素钢、合金钢、不锈钢等。
同时,它也可以灵活应对市场需求的变化,快速调整生产线的生产规模和品种组合。
5. 降低投资和运营成本:短流程连铸连轧装备比传统装备的投资成本更低,且占地面积较小,使得钢铁企业能够降低建设成本和运营成本。
总结短流程连铸连轧成套装备的工作原理和技术优势使其成为现代钢铁生产的重要工艺。
连铸连轧
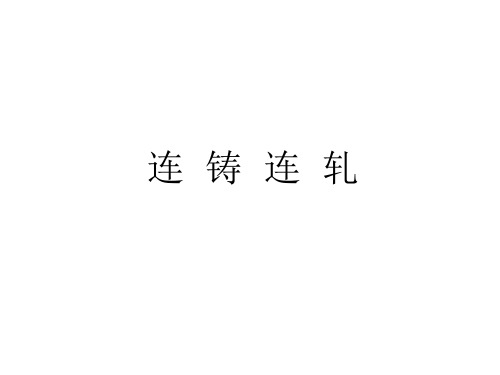
连铸机的形式
连铸工艺流程:1)炼钢炉炼出的合格钢水经炉外精炼处理;2)钢包运
送到浇铸位置注入中间包,通过中间包注入强制水冷铜模—结晶器内;3)
当结晶器内钢水升到要求的高度后,开动拉坯机,以一定速度把引锭杆(牵 着铸坯)从结晶器中拉出 4)铸坯被拉出结晶器后,为使其更快地散热,需
才能投入使用。毛管轧制就是对穿孔后的毛管进行壁厚加工,实现减 壁延伸,是壁厚接近或等于成品壁厚。
连轧管机组轧制过程示意图
1-轧辊 2-浮动芯棒 3-毛管
(4) 管材的定、减径
毛管在轧管机上进行了以减壁为主的加工后,已成为壁厚接近于
成品的荒管。为了扩大产品使用范围,就需要对其外径进行加工,同 时对壁厚继续进行少量加工,这就是钢管生产中的第三个阶段—定径、
要进行喷水冷却,称之为二次冷却,通过二次冷却支导装置的铸坯逐渐凝固。
1-钢包 2-中间包 3-结晶器及震荡装置 4-电子搅拌器 5-二冷区支导装置 6-拉矫机 7-切割装置 8-辊道 9-轧件
管 材 轧 制
三辊行星轧机生产线
电解铜
熔化
铸造
轧制
二联拉
盘拉
成品
退火
水平缠绕
内螺纹成型
退火
铸轧法生产铜管工艺流程图
连 铸 连 轧
连铸连轧(CCDR):由连铸机生产出来的高温无缺陷坯,无需清理
和再加热(但需短时间均热和保温处理)而直接轧制成材,即把“铸” 和“轧”直接连成一条生产线的工艺流程。
CCDR生产线
1-钢包 2-双臂回转架 3-中间包 4-弧形连铸机 5-剪断机 6-粗轧机组 7-中轧机组
薄板坯连铸连轧技术综述
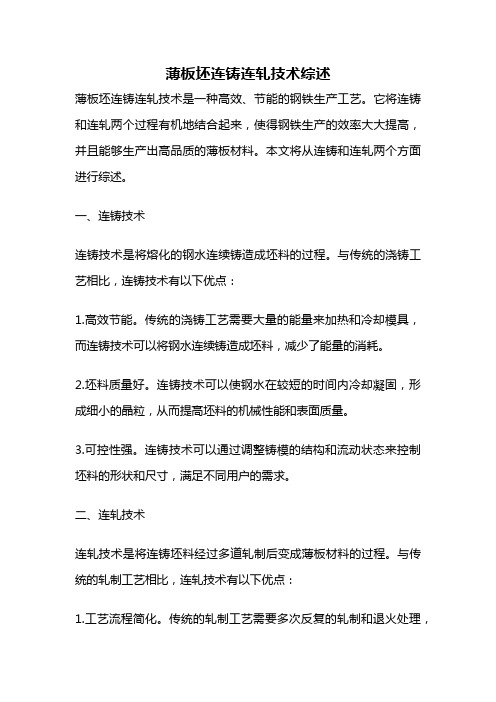
薄板坯连铸连轧技术综述薄板坯连铸连轧技术是一种高效、节能的钢铁生产工艺。
它将连铸和连轧两个过程有机地结合起来,使得钢铁生产的效率大大提高,并且能够生产出高品质的薄板材料。
本文将从连铸和连轧两个方面进行综述。
一、连铸技术连铸技术是将熔化的钢水连续铸造成坯料的过程。
与传统的浇铸工艺相比,连铸技术有以下优点:1.高效节能。
传统的浇铸工艺需要大量的能量来加热和冷却模具,而连铸技术可以将钢水连续铸造成坯料,减少了能量的消耗。
2.坯料质量好。
连铸技术可以使钢水在较短的时间内冷却凝固,形成细小的晶粒,从而提高坯料的机械性能和表面质量。
3.可控性强。
连铸技术可以通过调整铸模的结构和流动状态来控制坯料的形状和尺寸,满足不同用户的需求。
二、连轧技术连轧技术是将连铸坯料经过多道轧制后变成薄板材料的过程。
与传统的轧制工艺相比,连轧技术有以下优点:1.工艺流程简化。
传统的轧制工艺需要多次反复的轧制和退火处理,而连轧技术可以将这些过程有机地结合起来,减少了生产环节和能源消耗。
2.产品质量稳定。
连轧技术可以通过调整轧制工艺参数来控制薄板材料的厚度和表面质量,保证了产品质量的稳定性。
3.生产效率高。
连轧技术可以实现高速轧制,大大提高了生产效率和产量。
三、薄板坯连铸连轧技术的应用薄板坯连铸连轧技术已经广泛应用于钢铁生产领域。
它不仅可以生产高品质的薄板材料,而且还可以有效地节约能源和减少环境污染。
目前,国内外很多大型钢铁企业都采用了薄板坯连铸连轧技术,如宝钢、鞍钢、武钢等。
同时,随着技术的不断进步和创新,薄板坯连铸连轧技术将会有更广阔的应用前景。
薄板坯连铸连轧技术是一种高效、节能、高质量的钢铁生产工艺。
它在钢铁生产中发挥着越来越重要的作用,是推动钢铁产业可持续发展的重要手段之一。
- 1、下载文档前请自行甄别文档内容的完整性,平台不提供额外的编辑、内容补充、找答案等附加服务。
- 2、"仅部分预览"的文档,不可在线预览部分如存在完整性等问题,可反馈申请退款(可完整预览的文档不适用该条件!)。
- 3、如文档侵犯您的权益,请联系客服反馈,我们会尽快为您处理(人工客服工作时间:9:00-18:30)。
ISP工艺也称在线热带钢生产工艺。ISP生产线的工
艺流程一般为:电炉或转炉炼钢→钢包精炼→连铸机→
大压下量初轧机→剪切机→感应加热炉→克日莫那炉→
热卷箱→高压水除鳞机→精轧机→输出辊道和层流冷却 →卷取机。
薄板坯连铸连轧
1-中间包; 2-结晶器; 3-液芯压下; 4-除鳞机; 5-预轧机; 6-剪切机; 7-感应加热炉; 8-热卷箱; 9-事故剪; 10-除鳞机; 11-精轧机; 12-层流冷却; 13-卷取机
输送辊
机→立辊轧机→粗轧机→保温辊道→三次除鳞装置→精 轧机→输出辊道和带钢冷却段→卷取机。
薄板坯连铸连轧
1-连铸机; 2-旋转式一次除鳞; 4-二次除鳞; 5-立辊轧机; 7-保温辊道; 8-三次除鳞; 10-输出辊道和层流冷却;
3-隧道式加热炉; 6-粗轧机; 9-精轧机; 11-卷取机
薄板坯连铸连轧
连续铸钢
连续铸钢 连续铸钢的优越性
• 简化了工序,缩短了流程
省去了脱模、整模、钢锭均热、初轧开坯等工序。由 此可节省基建投资费用约40%,减少占地面积约30%,劳动 力节省约70%。
• 提高了金属收得率
采用模铸工艺,从钢水到钢坯,金属收得率为84%88%,而连铸工艺则为95-96%,金属收得率提高10-14%。
薄板坯连铸连轧
3、FTSR工艺技术(Flexible Thin Slab Rolling) FTSR工艺(Flexible Thin Slab Rolling)被称之为生产
高质量产品的灵活性薄板坯轧制工艺。FTSR工艺流程一
般为:电炉或转炉炼钢→钢包精炼→薄板坯连铸机→旋
转式除鳞机→剪切机→辊底式隧道式加热炉→二次除鳞
3-AOD;
4-传送车;
6-加热炉; 7-立辊轧机; 8-粗轧机;
9-精轧机;
10-卷取机
薄板坯连铸连轧
5、QSP工艺技术
QSP技术是日本住友金属开发出的生产中厚板坯的
技术,开发的目的在于提高铸机生产能力的同时生产高 质量的冷轧薄板。QSP工艺生产流程一般为:电炉或转 炉炼钢→钢包精炼炉→薄板坯连铸机→剪切机→辊底式 隧道加热炉→立辊轧边机→粗轧机→高压水除鳞机→精 轧机→卷取机。
近终型浇铸
薄带连铸
与连铸连轧过程相比,每吨钢可节省能源达800kJ, CO2排放量降低85%,NOx降低90%,SO2降低70%。薄 带铸轧技术尤其适合我国钢铁工业的发展情况,由于能 够有效抑制Cu、S、P等夹杂元素在钢材基体中的偏析, 从而可实现劣质矿资源(如高磷、高硫、高铜矿或废钢
等)有效综合利用,节省宝贵资源,是钢铁工业实现可
薄板坯连铸连轧
1-电弧炉;
2-钢包精炼炉; 3-连铸机;
4-均热炉;
7-单机架斯特克尔轧机;
5-卷取机;
8-层流冷却;
6-立辊轧边机;
9-成品带卷
薄板坯连铸连轧
7、CPR工艺技术(Casting Pressing Rolling) CPR工艺即铸压轧工艺,用于生产厚度小于25mm 的合金钢和普碳钢热轧带材。它利用浇铸后的大压下 (60%的极限压下量),仅使用一组轧机,最终可生产厚 度为6.0mm的薄带卷,也可生产低碳钢、管线钢、铁素 体和奥氏体不锈钢及高硅电工钢等。该生产线包括一台 连铸机、一台感应炉、除鳞机、一台四辊轧机。工艺流 程示意为:电炉或转炉炼钢→钢包精炼炉→薄板坯铸压
双辊薄带连铸的基本原理图
近终型浇铸
宝钢薄带连铸发展历史回顾
2003年,建成一条带宽1200mm双辊薄带连铸中试线并 投入使用。 2004年,完成不锈钢成卷试验。 2005年,完成碳钢成卷试验。 2006年,完成硅钢成卷试验。 2007年,展开第二阶段攻关。 2008年,完成在线四辊热轧机的增设并成功投入试验。 2009年2月,中国第一条薄带连铸连轧生产线——宝钢股 份薄带连铸产业化攻关项目全线投入试生产。
持续发展的重要内容。
近终型浇铸
薄带连铸工艺与其他工艺比较
投资成本 生产成本
近终型浇铸
薄带连技术与新材料开发 采用薄带连铸技术在新材料开发,特别是在 生产很难热加工产品时,更是具有工艺上的优势, 由于铸带是在冷却速度达到100~1000 C/s的条 件下形成的,二次枝晶间距仅为2-5μm,显微组 织均质细晶,且具有遗传性,沿带厚成份偏析很 小。这对高合金材料的生产十分有益,特别是在 难以轧制的高合金薄带钢生产方面有着巨大发展 潜力。例如,目前国外在开发的TWIP钢、INVAR合 金、铁素体不锈、镁合金带、高硅钢等。
连续铸钢 亨利· 贝塞麦
连续浇铸最早由亨利· 贝塞麦提出,并于1846 年开始试验,但是直到1937年才实现了铜合金的 连铸,1950年制出钢液的连铸机。 连铸技术在钢铁生产中的应用 是钢铁冶金工业的一次技术革命, 它不仅大大提高了生产率,减少了 材料消耗,提高了能源效率,并且 提高了材料的质量。此后还出现了 连铸连轧O.C.C技术。
铸平台上,钢水经中间包和布流水口注入到双 辊连铸机,铸成厚度为2~5mm的薄带坯, 经单 机架四辊轧机轧制后,冷却、卷取。
近终型浇铸
宝钢薄带连铸中试机组主要参数
设备名称 冶炼 连铸机 电弧炉/LF/VOD 铸机型式/台数/流数 结晶辊直径 浇注速度MAX 铸带厚度/ 生产钢种 16t,各1 座 双辊等径薄带连铸机/1/1 800 mm 110 m.min-1 2~5 mm 碳钢、不锈钢、硅钢 技术参数
连续铸钢
• 降低了能源消耗
采用连铸工艺比传统工艺可节能1/4-1/2。
• 生产过程机械化、自动化程度高
设备和操作水平的提高,采用全过程的计算机管理,不 仅从根本上改善了劳动环境,还大大提高了劳动生产率。
• 提高质量,扩大品种
几乎所有的钢种均可以采用连铸工艺生产,如超纯净度 钢、硅钢、合金钢、工具钢等约500多个钢种都可以用连铸 工艺生产,而且质量很好。
薄板坯连铸连轧
1-回转台; 2-钢包; 3-中间罐; 4-连铸机; 5-剪切机; 6-加热炉; 7-除鳞机; 8-粗轧机; 9-加热炉; 10-事故剪; 11-除鳞机; 12-精轧机; 13-层流冷却; 14-卷取机; 15-预留卷取机
薄板坯连铸连轧
2、ISP工艺技术(Inline Strip Production)
近终型浇铸
ThyssenKrupp Steel缩短热轧板生产工艺
传 统 技 术
连铸、热连轧
250 mm 工艺阶段: 中间储备: 1.5-25 mm 连 铸 ,
约
250mm
薄板坯连铸连轧
62 mm 工艺阶段: 中间储备 0.8-9 mm
薄 板 坯 连 铸 ,
62 mm 约
新 技 术
薄带连铸
1.5-3 mm 工艺阶段: 中间储备
连续铸钢
2、 21世纪钢铁工业发展趋势
(1) 产品更加纯洁化 (2) 生产工艺更加高效低耗 (3) 生产过程对环境更加友好
薄板坯连铸连轧
薄板坯连铸连轧
典型的薄板坯连铸连轧工艺流程由炼钢(电炉或转炉)— 炉外精炼—薄板坯连铸—连铸坯加热—热连轧等五个单元 工序组成。该工艺将过去的炼钢厂和热轧厂有机地压缩、 组合到一起,缩短了生产周期,降低了能量消耗,从而大 幅度提高经济效益。 薄板坯连铸连轧技术因众多的单位参与研究开发,形 成了各具特色的薄板坯连铸连轧生产工艺,如:CSP、ISP 、FTSR、CONROLL、QSP、TSP、CPR等,其中推广应 用最多的是CSP工艺,由西马克· 德马格公司开发。
薄板坯连铸连轧
1-单流连铸机; 4-隧道式加热炉; 7-除鳞机;
2-软压下装置; 5-立辊轧边机; 8-精轧机;
3-剪切机; 6-初轧机、除鳞机; 9-卷取机
薄板坯连铸连轧
6、TSP工艺技术(Tippins-Samsung Process)
倾翻带钢新技术,简称TSP。TSP工艺流程一般为:
电弧炉(AC或DC)或转炉炼钢→钢包精炼→薄板坯连铸 机→步进式加热炉→高压水除鳞机→立辊轧边机→单机 架斯特克尔轧机→层流冷却→卷取机。
4、CONROLL工艺技术 CONROLL工艺是奥钢联工程技术公司开发的用于生 产不同钢种的连铸连轧生产工艺。CONROLL工艺流程 为:常规连铸机→板坯热装(或直接)进步进梁式加热炉 →带立辊可逆粗轧机→精轧机架→输出辊道和层流冷→ 卷取机
薄板坯连铸连轧
1-钢包加热炉; 2-电炉; 5-连铸机;
连 铸 ,薄 板 坯 8 -20 mm
. 3 mm
薄带连铸
(水平带钢连铸技术)
8-20 mm 精整
薄 带 连 铸
近终型浇铸
由于缩短工艺流程,从而减少了吨钢100kg的CO2排放量
• 对于薄板坯连铸厂来说,节 省了板坯加热的能耗 • 还降低了轧制力 • 如果热轧卷的厚度足够薄, 还能够省掉冷轧工序
250 热轧 连铸 薄板坯
连续铸钢 连铸的发展史
1、现代炼钢技术的发展(连铸技术的作用) (1) 1947年-1974年:
技术特点:转炉、高炉的大型化;以模铸-初轧为核心, 生产外延扩大。
(2) 1974年-1989年:
技术特点:全连铸工艺,以连铸机为核心。
(3) 1989年-现在:
技术特点:连铸-连轧工艺,以薄板坯,连铸-连轧为代 表,钢厂向紧凑化发展。
近终型浇铸
宝钢薄带连铸技术方向选择
钢水由SEN注入两个逆向 旋转的水冷辊与两耐火材料侧 封板组成的三角熔池,钢液接 触水冷辊,经传导传热过程, 首先形成半凝固层、凝固层, 然后在双辊的逆向转动下进入 吻合点,经过铸轧最终成为厚 度在2-6mm左右的薄带坯。再 经1或2机架四辊热轧机在线轧 制成为厚度1-3mm薄带后成卷。
轧→感应加热炉→旋转式高压水除鳞机→精轧机→层流
冷却→卷取机。
薄板坯连铸连轧
1-结晶器; 5-除鳞区;