薄板坯连铸连轧技术的发展和动态
近两年我国薄板坯连铸连轧装备技术的发展

近两年我国薄板坯连铸连轧装备技术的发展截止到2006年上半年,我国已有珠钢、邯钢、包钢、鞍钢、马钢、唐钢、涟钢、本钢、通钢、济钢、酒钢、唐山国丰等12家钢铁企业的13条薄板坯(包括中薄板坯)连铸连轧生产线(主要工艺参数见表1)相继投产,产能约为3500万t /a 。
这13条生产线的连轧机组均采用了目前最先进的机型。
CSP 线连轧机组全部采用CVC 轧机;FT SR 线连轧机组采用PC 轧机,在后两架采用在线磨辊系统ORG;ASP 线连轧机组的后4架则采用WRS 轧机。
先进的轧机配置和控制系统为热轧板带的板厚和板形高精度控制提供了有力的保证。
预计5年内,我国的薄板坯连铸连轧生产线可能将达到15条(将占世界的近30%),产能将突破4000万t/a,占我国热轧板卷产能的30%以上。
表1 我国13条薄板坯连铸连轧生产线的主要工艺参数和产能序号企业名称生产线形式连铸机流数铸坯厚度/mm铸坯宽度/mm 产能/万t ・a -11珠钢CSP 2流50~60950~13501802邯钢CSP 2流60~70900~16802603包钢CSP 2流50~70980~15602804鞍钢AS P(1700) 5鞍钢AS P(2150) 6马钢CSP 2流90~65900~16002607唐钢FTS R 2流90~70850~16803008涟钢CSP 2流70~55900~16002609本钢FTS R 2流90~70850~168026010通钢FTS R 1流90~70950~156013011济钢AS P(1700)2流135~150900~150028012酒钢CSP 2流70~52950~168026013唐山国丰ZSP(1450)2流130~170800~1300200 (1)薄板坯连铸连轧工艺实现生产高效化2005年唐钢薄板坯连铸连轧生产线取得了高效化生产,其FT SR 线年产量首次突破300万t 大关,达到301.123万t ,2005年12月份产量为27.23万t ,迎来了薄板坯连铸连轧生产线生产史上的一个新的里程碑。
我国薄板坯连铸连轧工艺发展现状及前景展望

我国薄板坯连铸连轧工艺发展现状及前景展望祝志新(辽宁科技大学材料成型及控制工程12级,鞍山114000)1引言薄板坯连铸连轧技术是20 世纪80 年代末世界钢铁工业发展的一项重大技术, 它的开发成功是近终形浇铸技术的重大突破。
1998年我国第一条薄板坯连铸连轧生产线在珠钢投产,从1998 年底到2006 年上半年, 我国已有珠钢、邯钢、包钢、鞍钢、唐钢、马钢、涟钢、本钢、通钢、济钢、酒钢、唐山国丰12 家钢铁企业的13 条薄板坯( 包括中薄板坯) 连铸连轧线相继投产, 年产能约3500 万t。
2001 年底, 全球已建成53 条薄板坯连铸连轧生产线, 共75 流, 包括CSP ( Compact StripProduct ion)、ISP (In—Line St rip Production) 、FTSR ( Free Thin Slab Roll)、QSP 、DSP 和CON ROLL 工艺形式。
在过去的25 年中,美国与中国的钢铁工业分别引领了前2 个10 年国际薄板坯连铸连轧技术的发展。
第 1 个10 年以美欧为主,美国则主要以电炉流程为主。
第 2 个10 年以中国为主,主要以转炉流程为特点,同时铸坯厚度向70 ~90mm发展。
现在,到了薄板坯连铸连轧技术发展的第3个10 年。
2011年以来中国钢铁行业面临严重危机。
导致危机的原因有以下几点:一是2011 年房地产、汽车、造船等下游行业增速明显减缓,导致对钢铁产品的需求下滑;二是由于宏观经济低迷,造成国际市场钢材需求量下降,2011 年我国钢材出口量增速明显下滑;三是四万亿经济刺激计划后导致国内钢铁行业扎堆上马,产能过剩,各企业为争夺有限的市场进行价格战,利润下滑。
没有更多经费投入到技术改良,产品研发上,高端产品不多,附加值低。
钢铁行业盛行丛林法则,企业兼并重组,削减产能是目前走出困境的良方。
2发展现状尽管如此,薄板坯连铸连轧技术仍是一项好的技术。
近期薄板坯连铸连轧技术的进步
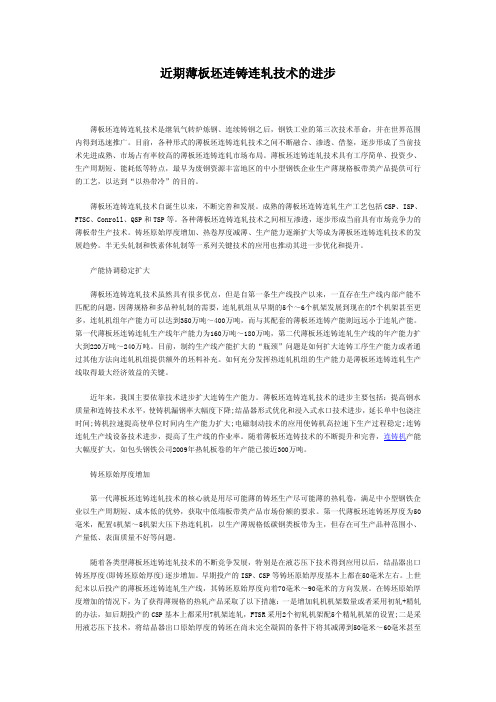
近期薄板坯连铸连轧技术的进步薄板坯连铸连轧技术是继氧气转炉炼钢、连续铸钢之后,钢铁工业的第三次技术革命,并在世界范围内得到迅速推广。
目前,各种形式的薄板坯连铸连轧技术之间不断融合、渗透、借鉴,逐步形成了当前技术先进成熟、市场占有率较高的薄板坯连铸连轧市场布局。
薄板坯连铸连轧技术具有工序简单、投资少、生产周期短、能耗低等特点,最早为废钢资源丰富地区的中小型钢铁企业生产薄规格板带类产品提供可行的工艺,以达到“以热带冷”的目的。
薄板坯连铸连轧技术自诞生以来,不断完善和发展。
成熟的薄板坯连铸连轧生产工艺包括CSP、ISP、FTSC、Conroll、QSP和TSP等。
各种薄板坯连铸连轧技术之间相互渗透,逐步形成当前具有市场竞争力的薄板带生产技术。
铸坯原始厚度增加、热卷厚度减薄、生产能力逐渐扩大等成为薄板坯连铸连轧技术的发展趋势。
半无头轧制和铁素体轧制等一系列关键技术的应用也推动其进一步优化和提升。
产能协调稳定扩大薄板坯连铸连轧技术虽然具有很多优点,但是自第一条生产线投产以来,一直存在生产线内部产能不匹配的问题,因薄规格和多品种轧制的需要,连轧机组从早期的5个~6个机架发展到现在的7个机架甚至更多,连轧机组年产能力可以达到350万吨~400万吨,而与其配套的薄板坯连铸产能则远远小于连轧产能。
第一代薄板坯连铸连轧生产线年产能力为160万吨~180万吨,第二代薄板坯连铸连轧生产线的年产能力扩大到220万吨~240万吨。
目前,制约生产线产能扩大的“瓶颈”问题是如何扩大连铸工序生产能力或者通过其他方法向连轧机组提供额外的坯料补充。
如何充分发挥热连轧机组的生产能力是薄板坯连铸连轧生产线取得最大经济效益的关键。
近年来,我国主要依靠技术进步扩大连铸生产能力。
薄板坯连铸连轧技术的进步主要包括:提高钢水质量和连铸技术水平,使铸机漏钢率大幅度下降;结晶器形式优化和浸入式水口技术进步,延长单中包浇注时间;铸机拉速提高使单位时间内生产能力扩大;电磁制动技术的应用使铸机高拉速下生产过程稳定;连铸连轧生产线设备技术进步,提高了生产线的作业率。
薄板坯连铸连轧技术的发展和动态
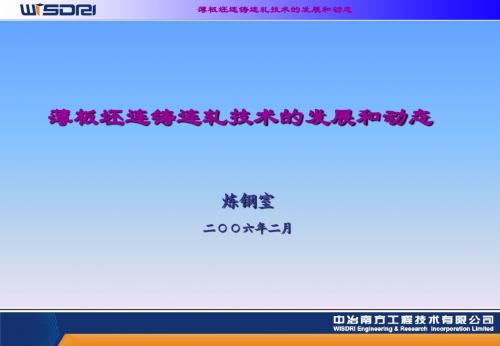
薄板坯连铸连轧技术的发展和动态
7、生产钢种 薄板坯连铸连轧生产线随着技术的不断成熟和完善,生产品 种不断扩大。低碳、超低碳钢、碳素结构钢、HSLA、耐候钢、 管线钢、热处理钢、弹簧钢、工具钢、耐磨钢、硅钢(取向 和无无取向)、不锈钢(铁素体和奥氏体)、多相和双相钢。 新发展的钢种主要就是硅钢(取向和无无取向)、不锈钢 (铁素体和奥氏体)、汽车用的新钢种多相和双相钢。
薄板坯连铸连轧技术的发展和动态
1、概述 薄板坯连铸连轧生产工艺是90年代世界钢铁工业发展的一项重 大新技术,经过十多年的发展,以投资省、成本低、节能、高 效的优势,得到快速发展。到2002年底世界上已有38个薄板坯 连铸连轧生产厂共56条生产线,总生产能力已超过5500万吨。 我国现已有6个钢铁企业建成12条薄板坯连铸连轧生产线,还 有3个钢铁企业正在建设。 随着工艺技术不断的发展和完善,采用半无头轧制技术、铁素 体轧制技术,生产的钢种不断扩大,已有几家厂家生产无取向 硅钢、取向硅钢及不锈钢,产品厚度变薄、宽度加宽、质量提 高,产品经酸洗平整后,以热代冷的市场进一步扩大,经济效 益显著。同时采用转炉配合薄板坯连铸连轧生产线生产,生产 线规模也在扩大,转炉可以提供优质钢水,更有助于薄板坯连 铸连轧工艺生产出更具有竞争力的产品,市场前景广阔。
薄板坯连铸连轧技术的发展和动态
2、薄板坯铸坯规格的划分 铸坯厚度100mm以下为薄板坯铸坯规格,CSP(西马克) 薄 板坯铸坯规格主要在90-45mm厚以下,DMG(DANIELI和日本三 菱组合) 薄板坯铸坯规格主要在100mm-70mm。 3、薄板坯连铸连轧工艺生产流程
薄板坯连铸机 机械剪 均热炉 事故剪 高压水除鳞箱 立辊轧机 7机架轧机(F1、F2 或R2 轧机出口二次精除鳞) 带钢冷却 卷取 下线
薄板坯连铸连轧无取向电工钢技术难点及发展趋势

薄板坯连铸连轧无取向电工钢技术难点及发展趋势薄板坯连铸连轧流程有许多优点,但在国内采用该工艺流程生产无取向电工钢的时间仅不到10年,仍有不少技术难关尚未攻克,存在可能影响无取向电工钢质量的潜在问题如下:铸坯浇注质量:该工艺铸坯易产生边裂,浇注过程辊缝收缩程度大,使铸坯受到夹持力,内部质量不佳。
带钢表面氧化铁皮较重:相对比传统工艺,薄板坯连铸连轧流程表面氧化铁皮更难去除,除鳞水压力高达40MPa。
对硅含量较高的无取向硅钢,氧化铁皮较其他钢种更难去除。
国内外一些钢厂在生产中均遇到过氧化铁皮严重、难以酸洗的问题。
瓦楞状缺陷:尽管薄板坯连铸连轧工艺能改善铸态组织,提高等轴晶比例,但总体晶粒细小。
尤其是在低碳(<50ppm)、硅较高(≥1.7%)的牌号(约50W470及以上牌号)的无取向硅钢薄板坯连铸过程无电磁搅拌,柱状晶比例高,热轧过程中无相变,细小柱状晶难以被破碎,产生纤维状组织,遗传至后道工序乃至成品表面产生几微米宽的瓦楞状缺陷。
这也成为薄板坯连铸连轧流程生产无取向电工钢产品过程中亟待解决的一个关键问题。
夹杂物尺寸:从目前薄板坯连铸连轧生产的实践经验来看,此流程由于夹杂物含量较高和热轧板中第二相析出物尺寸相比传统流程略小,与无取向电工钢工艺控制过程中希望热轧板中杂质元素尽可能以粗大第二相的形式存在的原则相悖,因此在生产更高级的无取向电工钢方面(如高牌号及薄规格)将有更大的难度。
发展趋势--高牌号薄规格高效电机和特殊用途钢:国内薄板坯连铸连轧工艺生产无取向硅钢的历史不足10年,有着广阔的发展空间,其发展趋势主要有以下方面:(1)高牌号产品:目前武钢CSP厂产品结构仍只覆盖中低牌号,50W350及以上高级别产品仍依赖成熟的传统厚板坯流程。
采用薄板坯连铸连轧流程生产高牌号无取向硅钢方面有着重大的研究价值,随着马钢常化线的新建,钢铁研究总院连铸中心与马钢合作开展了CS P流程生产高牌号无取向电工钢的系列研究,以期攻克薄板坯连铸连轧生产高牌号无取向硅钢(50W350及以上牌号)的技术难题。
薄板坯连铸连轧

薄板坯连铸连轧是生产热轧板卷的一项结构紧凑的短流程工艺,是继氧气转炉炼钢及连续铸钢之后,又一重大的钢铁产业的技术革命。
薄板坯连铸连轧是将传统的炼钢厂和热轧厂紧凑地压缩并流畅地结合在一起。
随着在大产业生产中的不断完善、不断发展,该工艺的节能和高效的特点突现出来,充分显示出该工艺的先进性、公道性和科学性,也给企业带来了巨大的经济效益。
薄板坯连铸连轧技术因众多的单位参与研究开发,已形成了各具特色的薄板坯连铸连轧生产工艺,如CSP、ISP、FTSR、CONROLL、TSP、QSP等。
其中推广应用最多的是CSP工艺。
各种薄板坯连铸连轧技术各具特色,同时又相互影响、相互渗透,并在不断地发展和完善。
一、三种薄板坯连铸连轧技术的各自现状:1.1 CSPCSP是由德国西马克公司开发的世界上最早投入工业化生产的薄板坯连铸连轧技术,自1989年在纽柯公司建成第一条生产线以来,随着技术的不断改进,该生产线不断发展完善,现已进入成熟阶段。
CSP技术的主要特点是:(1)采用立弯式铸机,漏斗型直结晶器,刚性引锭杆,浸入式水口,连铸用保护渣,电磁制动闸,液芯压下技术,结晶器液压振动,衔接段采用辊底式均热炉,高压水除鳞,第一架前加立辊轧机,轧辊轴向移动,轧辊热凸度控制,板形和平整度控制,平移二辊轧机等。
(2)可生产0.8mm或更薄的碳钢、超低碳钢。
(3)生产钢种包括:低碳钢、高碳钢、高强度钢、高合金钢及超低碳钢。
1.2 ISPISP是由德马克公司最早开发的,1992年1月在意大利阿尔维迪公司克雷莫纳厂建成投产,设计能力为50万吨/a。
它是目前最短的薄板坯连铸连轧生产线,主要技术特点是:(1)采用直弧型铸机,小漏斗型结晶器,薄片状浸入式水口,连铸用保护渣,液芯压下和固相铸轧技术,感应加热后接克雷莫纳炉(也可用辊底式炉),电磁制动闸,大压下量初轧机+带卷开卷+精轧机,轧辊轴向移动,轧辊热凸度控制,板形和平整度控制,平移式二辊轧机。
(2)生产线布置紧凑,不使用长的均热炉,总长度180m左右。
薄板坯连铸连轧技术发展现状及展望
结论
薄板坯连铸连轧轧制区组织模拟在优化工艺、提升产品质量和开发新型钢材 等方面具有重要意义。通过组织模拟,可以深入了解轧制过程中材料的组织变化 和性能特点,为生产工艺优化提供理论支持和实践指导。同时,针对不同应用场 景选择合适的钢种和轧制工艺参数也成为可能,有助于提高钢材产品的质量和附 加值。
未来研究方向
薄板坯连铸连轧轧制区背景及基 础概念
薄板坯连铸连轧是指将液态钢水倒入薄板坯连铸机中进行连续铸造,然后将 连铸坯送入轧机进行连续轧制。在这个过程中,钢水在连铸机中逐渐冷却凝固, 形成具有一定形状和尺寸的连铸坯。随后,连铸坯被送入轧机进行高温高压的连 续轧制,最终形成具有一定厚度、宽度和性能的钢材产品。
总的来说,中国薄板坯连铸连轧技术已经得到了广泛的应用和推广,并在不 断创新和发展。未来,随着市场的需求和行业的发展,薄板坯连铸连轧技术将在 钢铁产业中发挥更加重要的作用。
薄板坯连铸连轧是一种高效、节能的钢材生产工艺,具有较高的生产效率和 产品质量。在轧制过程中,钢材的组织形态和性能特点对产品的质量和使用性能 具有重要影响。因此,薄板坯连铸连轧轧制区组织模拟成为了一个备受的研究领 域。通过组织模拟,可以深入了解轧制过程中材料的组织变化和性能特点,为工 艺优化和产品性能提升提供理论支持和实践指导。
薄板坯连铸连轧技术面临的挑战包括技术更新换代、市场竞争和技术人才的 培养等方面。随着科技的不断发展,该技术将面临越来越多的新挑战和机遇。未 来,需要加强技术研发和创新能力,不断提高产品质量和降低成本,以适应市场 需求的变化。加强技术人才的培养和引进,为技术的发展和应用提供强有力的人 才支持。
总之,薄板坯连铸连轧技术在新形势下取得了显著进步和发展,具有广泛的 应用前景和重要的发展价值。未来,需要继续加强技术研发和创新能力,提高产 品质量和降低成本,加强技术人才的培养和引进,以推动该技术在现代制造业中 的进一步发展和应用。
薄板坯连铸连轧技术发展趋势
De eo m e t Tr n f Co t u u si g a d Ro l g v lp n e d o n i o s Ca tn n l n n i Te h o o y f r Th n S a c n l g o i lb
LiQnsa a ighn
f h n G n rlI n a d Se lD s n Is tt Wu a e ea r n t ei ntue o e g i )
Ab t a t T e p e e t st a in a d d v l p n f c n n o s c si g a d r l n e h o o y f r s r c h r s n i t n e e o me t o o  ̄ u u a t n o l g tc n l g o u o n i t i l b w r is re . Ma y n w c n i u u a t g a d r l n e h oo i s s c s s mi e d e s h n sa e e d s e t d n e o t o s c si n l g t c n lg e . u h a e - n ls n n o i
a s r c t ti a d l a ti po u t ol g T e e eo me t r n o o t u u c sig n d su a e o hn n u t - n rd c r ln . h d v lp n t d f c n i o s a t a n r h i e n n
注 ,并 先 后投 入 了大 量 的人 力 、物 力 进 行 研究 、
开 发 、推 广 ,从 18 9 9年 美 国 印第安 那 州 纽 柯 钢
薄板坯连铸连轧技术
薄板坯连铸连轧技术薄板坯连铸连轧是20世纪80年代末开发成功的新技术。
自1989年美国纽柯克拉兹维莱钢厂世界第一套薄板坯连铸连轧CSP生产线投产以来,该项技术发展很快,至今已建成和在建的薄板坯连铸连轧生产线(含中厚板坯连铸连轧)已近30条,生产能力达4000万吨以上,占热轧带钢总产量的11%。
薄板坯连铸连轧技术除SMS开发的CSP外还有DEMAG的QSP、DANIELI的FTSR和V AI的CONROL 等5种类型。
实践证明,它们具有三高(装备水平高、自动化水平高、劳动生产效率高)、三少(流程短工序少、布置紧凑占地少、环保好污染少)和三低(能耗低、投资低、成本低)等优点。
和传统工艺相比,薄板坯连铸连轧工艺还具有如下特点:⑴由于板坯厚度较薄,它在结晶器内冷却强度大,柱状晶短,铸态组织晶粒细化。
⑵直接轧制,取消了α—δ相变温度区的中间冷却,热轧变形在粗大奥氏体组织上直接进行,避免合金元素在板坯冷却过程中析出,而使成品组织得到弥散硬化和获得更精细、更均匀的金相组织。
⑶均热工艺、辊底炉式均热炉保证了板坯在轧制过程中头尾温度的均匀和稳定,而使带钢全长的力学性能和厚度公差均匀一致。
⑷强力高压水除鳞,保证带钢的表面质量。
⑸高精度动态液压压下厚度自动控制(HAGC)、板形和平直度自动控制(PCFC)、精确的宽度和温度自动控制使带钢的几何尺寸精度达到最高水平。
⑹较高的轧制温度、进精轧机的开轧温度一般控制在1100~1150℃,比常规轧机进精轧高100~150℃。
因此,即使精轧机架数少,也能更易轧制超薄热轧带钢。
⑺由于薄板坯连铸连轧机生产线的小时产量主要取决于连铸机的拉速和板坯宽度,因此轧制薄规格带钢不会像传统轧机那样受到很大影响。
薄板坯连铸连轧机的上述特点使其在产品质量和薄规格轧制上具有较大优势。
薄板坯连铸连轧技术综述
薄板坯连铸连轧技术综述薄板坯连铸连轧技术是一种先进的钢铁生产技术,它将连铸和连轧两个工序有机地结合在一起,实现了钢铁生产的高效、节能、环保和高质量。
本文将从薄板坯连铸连轧技术的原理、特点、应用和发展趋势等方面进行综述。
一、薄板坯连铸连轧技术的原理薄板坯连铸连轧技术是将连铸和连轧两个工序有机地结合在一起,实现了钢铁生产的高效、节能、环保和高质量。
其原理是:将熔融的钢水通过连铸机连续铸造成薄板坯,然后将薄板坯直接送入轧机进行连续轧制,最终得到所需的薄板产品。
这种技术不仅可以减少钢铁生产的能耗和环境污染,还可以提高钢铁产品的质量和生产效率。
二、薄板坯连铸连轧技术的特点1.高效节能:薄板坯连铸连轧技术将连铸和连轧两个工序有机地结合在一起,避免了传统钢铁生产中的多次加热和冷却过程,大大降低了能耗和生产成本。
2.环保节能:薄板坯连铸连轧技术可以减少钢铁生产中的二氧化碳、氮氧化物等有害气体的排放,降低了环境污染和对大气的负荷。
3.高质量:薄板坯连铸连轧技术可以实现钢铁产品的高质量生产,因为它可以避免传统钢铁生产中的多次加热和冷却过程,减少了钢铁产品的氧化和变形。
4.生产效率高:薄板坯连铸连轧技术可以实现钢铁产品的高效生产,因为它可以将连铸和连轧两个工序有机地结合在一起,减少了生产周期和生产成本。
三、薄板坯连铸连轧技术的应用薄板坯连铸连轧技术已经广泛应用于钢铁生产中,特别是在高端钢铁产品的生产中。
例如,汽车、航空航天、电子、建筑等领域的高端钢铁产品都可以采用薄板坯连铸连轧技术进行生产。
此外,薄板坯连铸连轧技术还可以用于生产高强度、高韧性、高耐磨性等特殊钢铁产品。
四、薄板坯连铸连轧技术的发展趋势随着钢铁生产技术的不断发展和进步,薄板坯连铸连轧技术也在不断地改进和完善。
未来,薄板坯连铸连轧技术将更加注重环保、节能和高效,同时还将更加注重钢铁产品的高质量和高附加值。
此外,薄板坯连铸连轧技术还将更加注重智能化和自动化,以提高生产效率和生产质量。
- 1、下载文档前请自行甄别文档内容的完整性,平台不提供额外的编辑、内容补充、找答案等附加服务。
- 2、"仅部分预览"的文档,不可在线预览部分如存在完整性等问题,可反馈申请退款(可完整预览的文档不适用该条件!)。
- 3、如文档侵犯您的权益,请联系客服反馈,我们会尽快为您处理(人工客服工作时间:9:00-18:30)。
薄板坯连铸连轧技术的发展和动态
2、薄板坯铸坯规格的划分 铸坯厚度100mm以下为薄板坯铸坯规格,CSP(西马克) 薄
板坯铸坯规格主要在90-45mm厚以下,DMG(DANIELI和日 本三菱组合) 薄板坯铸坯规格主要在100mm-70mm。
3、薄板坯连铸连轧工艺生产流程
薄板坯连铸机 机械剪 均热炉 事故剪 高压水 除鳞箱 立辊轧机 7机架轧机(F1、F2 或R2轧机出口二 次精除鳞) 带钢冷却 卷取 下线
薄板坯连铸连轧技术的发展和动态
轧制后的热带钢通过输出辊道运输,在输出辊道上设置有带 钢冷却装置。由轧制温度冷却到卷取温度后的带钢通过卷取机前 导板对中和卷取机前的夹送辊传递,进入地下卷取机卷成带卷。 卷取机具有液压型助卷辊,可实现自动踏步控制,以免产生带钢 压痕缺陷。
卷取完成后,由卸卷小车取下钢卷将钢卷放在钢卷鞍座上, 再由横移小车将钢卷运送和提升到地面1号步进梁钢卷鞍座上, 由步进梁向前运送钢卷,依次进行打捆、称重、标记,最后用钢 卷库的吊车将其从步进梁上卸料处吊运到钢卷库存放。
薄板坯连铸连轧技术的发展和动态
薄板坯连铸连轧技术的发展和动态
4、两种薄板坯连铸连轧工艺设备的主要区别 薄板坯连铸机机型不同:立弯型和直弧型机型, 均热炉型式不同:摆动式和横移式 7机架轧机有两种型式:0R+7F或2R+5F 见图
薄板坯连铸连轧技术的发展和动态
薄板坯连铸连轧技术的发展和动态
5、主要工艺技术特点 1)漏斗型结晶器:两家技术区别长漏斗和短漏斗,延长浸入式水 口寿命
当两流铸机同时生产,正对轧制线的一流称为A线,另一线称为 B线,B线炉内的板坯通过均热炉的摆动段(或横移段)运送到A线 的保温段内,然后输送到轧机进行轧制。
辊底式均热炉出口设有事故剪,当轧机出现故障时切断板坯。
薄板坯连铸连轧技术的发展和动态
当轧机发出要钢信号时,将板坯运送速度调整到与F1(采用0R +7F)或R1(采用2R+5F)入口速度相同。辊底式炉炉门打开,板 坯从辊底式炉出来后首先经过高压水除鳞箱(压力最大达 38MPa),以清除在连铸及加热过程中产生的氧化铁皮,进入立 辊轧机轧制边部,立辊轧机前,设置了一台板坯横断面形状检测仪, 为轧机的前馈控制提供依据,对最终产品质量尤其是超薄规格带钢 轧制极为有利。立辊轧机最大压下量为40mm。然后依次进入7机 架轧机(0R+7F或2R+5F)进行轧制,轧制成需要的产品尺寸。7机 轧机采用四辊CVC/CVCPLUS或PC,液压AGC控制、工作辊弯辊 及电动或液压活套等控制技术。在F1、F2(采用0R+7F) 或R2(采 用2R+5F)轧机出口侧均设有10Mpa的高压水除鳞装置进行二次 精除鳞,清除轧制过程中的二次氧化铁皮以获得更好的带钢表面质 连铸连轧生产工艺是90年代世界钢铁工业发展的一项重 大新技术,经过十多年的发展,以投资省、成本低、节能、高 效的优势,得到快速发展。到2002年底世界上已有38个薄板 坯连铸连轧生产厂共56条生产线,总生产能力已超过5500万 吨。我国现已有6个钢铁企业建成12条薄板坯连铸连轧生产线, 还有3个钢铁企业正在建设。 随着工艺技术不断的发展和完善,采用半无头轧制技术、铁素 体轧制技术,生产的钢种不断扩大,已有几家厂家生产无取向 硅钢、取向硅钢及不锈钢,产品厚度变薄、宽度加宽、质量提 高,产品经酸洗平整后,以热代冷的市场进一步扩大,经济效 益显著。同时采用转炉配合薄板坯连铸连轧生产线生产,生产 线规模也在扩大,转炉可以提供优质钢水,更有助于薄板坯连 铸连轧工艺生产出更具有竞争力的产品,市场前景广阔。
(3)当轧机正常生产换工作辊,或下游设备临时故障时起调节 和缓冲作用,即在薄板坯连铸连轧的“刚性”机组之间增加了炉子 的“柔性”环节,使连铸连轧工艺能顺利进行。最长缓冲时间15 分钟。
薄板坯连铸连轧技术的发展和动态
当以连铸机拉速进入到炉内的铸坯长度达到工艺给定的长度时, 由辊底式均热炉前的摆式剪进行分段,剪切成定尺坯。剪切后的板 坯立即进行升速,以使其与后续板坯脱开1.5~2m距离,然后以与 连铸机铸速相同的速度匀速通过加热段。当板坯的尾部离开加热段 时,板坯已经加热到所要求的温度。板坯被快速向前输送,经摆动 段到达保温段。
薄板坯连铸连轧技术的发展和动态
根据钢种的不同,由连铸机铸出的薄板坯以不同的拉坯速度进 入辊底式均热炉,辊底式均热炉的作用是:
(1)连续不断地接收铸机的高温连铸板坯,经加热和均热后及 时供给轧机合乎加热质量要求的薄板坯;
(2)解决连铸机拉速和F1/R1(采用0R+7F/2R+5F时)轧机 入口速度之间的速度不匹配问题;
在钢卷运输线上设有在线钢卷检查取样装置,以便随时对带 钢进行检查和取样。
薄板坯连铸连轧技术的发展和动态
最后由钢卷库吊车将其从运输机下料端卸下并以卧卷方式在 钢卷库内堆放冷却。热轧商品卷由车间吊车吊到冷却区堆放冷却, 一部分送冷轧,一部分送热轧酸洗,另一部分以直发卷直接发运。
薄板坯连铸连轧生产线见附图
薄板坯连铸连轧技术的发展和动态
3)结晶器液压振动技术 液芯压下或动态软压下技术:两家技术区别及凝固末端轻压下的 概念。
csp结晶器铜板长度1100mm(其中漏斗长850mm)。H2长 漏斗型直结晶器漏斗长约2110mm,由两段组成。其中结晶器长 1200mm,另有两对足辊和扇形段0上部的4对辊子,长度 910mm。 2)结晶器相关工艺技术
结晶器自动在线调宽技术,薄板坯和常规板坯均应用成熟; 结晶器钢液面自动检测; 结晶器漏钢预报系统,唐钢应用很好,大大降低漏钢率; 结晶器电磁制动技术, csp连铸机上的多,要求通钢量3.5t/min 以上用较好;
薄板坯连铸连轧技术的发展和动态
薄板坯连铸连轧技术的发展和动态
炼钢室
二○○六年二月
薄板坯连铸连轧技术的发展和动态
专题目录: 1、概述 2、薄板坯铸坯规格的划分 3、薄板坯连铸连轧工艺生产流程 4、两种薄板坯连铸连轧工艺设备的主要区别 5、薄板坯连铸连轧主要工艺技术特点 6、薄板坯生产线能生产的钢种 7、国内外薄板坯连铸连轧生产硅钢的情况