连铸工艺技术讲义
连铸工艺技术培训课程

连铸工艺技术培训课程连铸工艺技术是一项重要的金属加工工艺,用于制造高质量的连续铸造产品。
掌握这一技术对于提高生产效率、确保产品质量至关重要。
为了帮助学习者更好地掌握连铸工艺技术,我们特别推出连铸工艺技术培训课程。
这个培训课程旨在向学习者介绍连铸工艺技术的基本原理、设备和操作要点。
课程包括以下几个主要内容:1. 连铸工艺技术概述:学习连铸工艺技术的基本概念和发展历程,了解连铸在金属加工中的重要性和应用范围。
同时,学习者还将了解到连铸工艺的优点和挑战。
2. 连铸设备及操作:学习连铸设备的种类和结构,了解连铸的整体工作流程。
同时,学习者还将学习设备的操作要点,包括设备的启动、停机、维护和故障处理等技巧。
3. 连铸操作的关键因素:学习连铸操作中的关键因素,如浇注速度、结晶器温度、浇注气氛等,以及如何调整这些因素以实现最佳的连铸效果。
学习者还将了解到如何通过控制连铸工艺参数来改善产品质量。
4. 连铸工艺缺陷与改进:学习连铸工艺中常见的缺陷问题,如浇注不均匀、表面气泡、内部夹杂物等,并了解各种改进方法。
通过学习这些内容,学习者将能够识别和解决连铸工艺中的常见问题。
5. 连铸工艺的质量控制:学习连铸工艺的质量控制方法,包括在线监测和离线检验。
学习者将了解到如何通过监测和检验来确保产品达到质量标准,并学习如何记录和报告关键的质量数据。
此外,我们还将提供实践环节,让学习者有机会亲自进行连铸工艺的操作和实验。
通过实践,学习者可以更深入地理解和掌握连铸工艺技术。
本培训课程适用于想要了解连铸工艺技术的初学者和从事连铸工作的技术人员。
无论你是学习连铸工艺的新手还是有经验的从业者,本课程都将帮助你提升你的技能和知识水平。
加入我们的连铸工艺技术培训课程,让我们一起学习、交流和进步!6. 连铸参数优化:学习如何通过优化连铸参数来提高产品质量和生产效率。
学习者将了解到如何选择合适的浇注速度、结晶器温度、浇注过程中的振动参数等关键参数,并学习如何通过实验和数据分析来确定最佳的参数组合。
炼钢连铸工艺介绍PPT课件

.
26
提高连铸坯表面质量的措施
3). 初生坯壳的均匀性。结晶器弯月面初生坯壳不均 匀会造成纵裂和凹陷,导致拉漏。坯壳生成的均匀性决 定于钢成分、结晶器冷却、钢液面稳定性和保护渣润滑 性能。
沿窄面向上流股动量太强或流股中含有沿窄面向上流股动量太强或流股中含有气泡降低了密度流股向上提升引起了弯月气泡降低了密度流股向上提升引起了弯月面区液面波动太大液渣渗入到坯壳与铜板的面区液面波动太大液渣渗入到坯壳与铜板的气隙困难导致弯月面的不均匀热流从而产气隙困难导致弯月面的不均匀热流从而产生纵裂纹
阳春新钢铁连铸工艺介绍
2.中间包:它的作用是减压、稳流、去渣、 贮钢、分流和中间包冶金等重要作用。
3.中包小车:它的作用是用来支撑、运输、 更换中间包的设备。
.
3
4.结晶器:它的作用是一个水冷的钢锭模,是 连铸机非常重要的部件,是连铸设备的心 脏。
5.结晶器振动装置:它的作用是固定结晶器、 铸坯脱模。
6.二次冷却系统装置:它的作用是冷却、支 撑、导向。
⑴钢中总氧法
钢中的氧以两种形式存在:溶解于钢中的 溶解氧和存在于氧化物的氧,钢中的总氧 含量是两者之和。钢中的总氧含量越低, 说明钢中氧化物夹杂越少,钢就越干净。
⑵钢中酸溶铝损失法
.
15
定义:二次氧化是指钢水中的合金元素与空气中的 氧、炉渣、耐火材料中的氧化物发生化学反应,生 成新的氧化物相而污染钢水。 2.1:钢水与空气的二次氧化: 2.1.1:注流与空气接触吸氧 2.1.2:注流卷入空气吸氧 2.1.3:钢水裸露吸氧 2.2:钢水与耐火材料的二次氧化: 2.2.1:中间包衬 包衬材料中含有SiO2被钢水中的Al还原生成Al2O3, 使钢洁净度降低。因此,中间衬向碱性材质方向发 展。
连铸工艺部分讲义 ppt课件

第一部分:
二、中间包
连铸耐材
14
第一部分:
二、中间包
连铸耐材
15
第一部分: 连铸耐材
二、中间包
4、中间包的准备 :
4.1 快换机件、上水口、座砖安装 4.1.1 喷涂:用石墨粉喷涂上水口座圈外圆和快换机构的加紧环内壁。 4.1.2 吻合:下装上水口并使其下表面露出加紧环1~2mm,调整上水口吹氩 进气口,必须使其与快换机构的吹氩喷嘴吻合。 4.1.3 检测压力:检查快换机构里的空气弹簧,其压力在1200~1600N。 4.1.4 清理:清理干净盖板下表面、上水口下表面和中包座圈上表面。 4.1.5 确认垂直:在中间包上方目测上水口是否垂直于水平面,否则重装。 4.1.6 捣打紧密:座砖、上水口座圈、定位板之间的缝隙必须使用已拌匀的 捣打料捣打紧密。 4.1.7 涂抹结合面:上水口与座砖结合面泥浆饱满,泥浆用玻璃水混成。 4.1.8 座砖就位:座砖底面与定位板上表面在安装前必须干净,就位后用木 锤打结实。 4.1.9 测试:安装完毕后用浸入式水口测试快换机构2次,观察快换机构是 否灵活,观察上水口与浸入式水口之间有无缝隙。
25
第一部分: 连铸耐材
二、中间包
8、关于长寿命中间包:
26
第一部分: 连铸耐材
二、浸入式水口
1、作用: 隔绝空气,防止
钢水二次氧化。
2、材质:
大多为镁碳或铝碳 加锆质材料组成, 也有石英材料制成 的。
结晶器卷渣示意图
保护渣层
结晶器卷渣示意图
A,B,C为卷渣处
27
第一部分: 连铸耐材
二、浸入式水口
一、连铸耐材
连铸耐材
8
第一部分:
二、中间包
连铸耐材
连铸工艺培训课件讲解
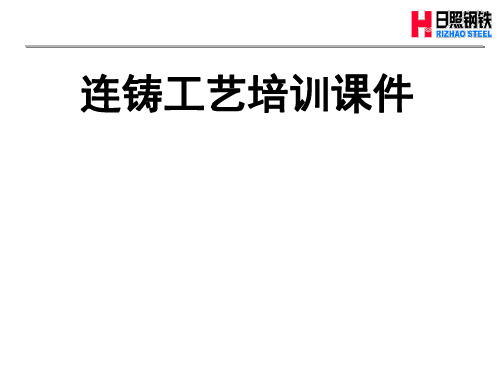
2.2、连铸的优越性
a、简化生产工序,缩 短工艺流程 b、提高综合成材率 c、降低能耗 e、易于实现机械自动化 f、扩大钢种,提高产品质量
弧形连铸机的几个重要参数
台数:凡是共用一个钢包同时浇注一流或 多流铸坯的一套连铸设备,称为一台连铸 机。 机数:具有独立的传动系统和工作系统, 当其他组出事故时仍照常工作的一组设备 称为一个机组。一台连铸机可由一机或多 多机组成。 流数:每台连铸机所能同时浇注铸坯的总 根数称为连铸机流数。
2007年4月1日原炼钢厂分设成立第一炼钢厂。目前,第一炼钢厂要生产优质碳素钢、冷 镦钢、焊接用钢、预应力钢棒、建筑用钢、船板用低合金高强度钢等,牌号标准有国标以外 的日标、欧标、英标、美标和韩标等。已经具备年产550万吨钢以上的生产能力。
1.2 炼钢工艺概述
1.2 炼钢工艺概述
炼钢厂的任务
铁水罐 混铁炉
Vmax=(Km/δmin)2 Lm 式中 Vmax—最大拉坯速度,m/min;
Lm —结晶器有效长度,mm; Km —结晶器内钢液凝固系数,mm/min1/2;结 晶器凝固系数可用经验公式Km=37.5/D0.11估算。 δmin—最大坯壳厚度,mm。
圆弧半径 用经验公式确定基本圆弧半径,也是连
t
最大拉坯速度
限制拉坯速度的因素主要是铸坯出结晶
器下口坯壳的安全厚度(最小坯壳厚度)。
对于小断面铸坯壳安全厚度为8~10mm;大
断面铸坯坯壳安全厚度不小于15mm。
根据凝固定律:δ=K凝
或
δ=K凝
t
L vC
式中 K凝—凝固系数,mm/min1/2;铸坯综合凝固系 数K凝为24~30 mm/min1/2。为保险起见,板坯 K凝取值较小,碳素钢K凝取28 mm/min1/2 ,弱钢冷 却钢种K凝取24~25mm/min1/2。 最大拉坯速度:
连铸工艺讲义

1.1.4铸坯凝固组织的控制
1.2.2过热度的ΔT确定
中间包内钢水的过热度ΔT取决于钢种、铸坯断面及浇注条 件等因素。如钢中含碳低,铸坯断面小、过热度应大些;钢中 碳、硅、锰含量高,铸坯断面大,过热度可取低值。浇注条件 主要指钢包及中间包的热工状况,即钢水在钢包及中间包内热 量损失引起的温降。 ΔT=t出钢-Δt过程-tl 式中Δt过程是从出钢到开始浇注的过程温降,其表达式如下: Δt过程=Δt1+Δt2+Δt3+Δt4+Δt5 式中:Δt1--出钢过程中钢水的温降; Δt2--出钢后到钢包处理前钢水的温降; Δt3—钢包处理过程中钢水的温降; Δt4—处理后至钢包开浇前钢水的温降; Δt5—钢水从钢包注入中间包的温降。 钢水过程温降如下图所示:
干净,以确保最终产品的性能。
在连铸钢水准备阶段,为了尽量减少钢中非金属夹杂 物的含量,应在脱氧、挡渣出钢及炉外精炼等方面做好工 作。
四、连铸工艺控制
1.拉速的确定和控制
拉坯速度是指连铸机每一流单位时间拉出铸坯的长度 (m/min),或每一流单位时间拉出铸坯的重量(t/min),后者 也有称为浇注速度的。显然,在铸坯断面一定的情况下,提 高拉坯速度(或浇注速度)可以提高连铸机的生产能力。 拉坯速度是连铸机的重要工艺参数之一,其大小直接影 响到钢水的凝固速度及铸坯的内部质量,为了提高连铸机的 生产能力,通常要提高拉坯速度。但是,拉速过高会造成结 晶器出口处坯壳厚度不足,坯壳过薄的铸坯,不足以承受拉 坯力和钢水的静压力,以致坯壳被拉裂而产生漏钢事故。即 使未漏钢,也会造成铸坯鼓肚和裂纹等缺陷。因此,提高拉 速应以获得良好的铸坯结构和保证正常操作为前提,通常在 一定工艺条件下,拉坯速度有一最佳值。
连铸连轧生产技术的讲义共40页

13、遵守纪律的风气的培养,只有领 导者本 身在这 方面以 身作则 才能收 到成效 。—— 马卡连 柯 14、劳动者的组织性、纪律性、坚毅 精神以 及同全 世界劳 动者的 团结一 致,是 取得最 后胜利 的保证 。—— 列宁 摘自名言网
15、机会是不守纪律的。——雨 特 67、今天应做的事没有做,明天再早也 是耽误 了。——裴斯 泰洛齐 68、决定一个人的一生,以及整个命运 的,只 是一瞬 之间。 ——歌 德 69、懒人无法享受休息之乐。——拉布 克 70、浪费时间是一桩大罪过。——卢梭
连铸连轧生产技术的讲义
11、战争满足了,或曾经满足过人的 好斗的 本能, 但它同 时还满 足了人 对掠夺 ,破坏 以及残 酷的纪 律和专 制力的 欲望。 ——查·埃利奥 特 12、不应把纪律仅仅看成教育的手段 。纪律 是教育 过程的 结果, 首先是 学生集 体表现 在一切 生活领 域—— 生产、 日常生 活、学 校、文 化等领 域中努 力的结 果。— —马卡 连柯(名 言网)
钢的连铸讲义
世界上第一台工业连铸机; 50年代,工业应用时期; 到50年代末,有连铸机30台,产量110t,连铸比0.34% 60年代,稳步发展时期; 到60年代末,有连铸机200余台,产量4000万t. 70年代,迅猛发展时期; 1981年连铸比33.8%. 80年代,完全成熟时期; 1990年连铸比64.1%;
炼钢生产的大炉容量、高浇铸温度和钢本身 比热低,这些在有色金属生产中未曾遇到过。 一项最重要的开拓性工作是如何提高一台连铸 机的浇铸能力,最关键的是浇铸速度。 1913年,瑞典人皮尔逊提出结晶器以可变的频 率和振幅做往复振动的想法。 1933年德国人容汉斯(S.Junghans)真正将 这一想法付诸实施。
宽板坯铸机于1959年建在原苏联的新列别茨克 厂。日本住友和罗西为新日铁光厂提供的世界上 第一台不锈钢宽板坯连铸机在1960年12月投产, 宽度为1050mm。
在整个50年代,连续铸钢技术尽管开始步入工 业生产,但产量很少,1960年的产量仅为115万 吨,连铸比仅为0.34﹪。
1.3.4 60年代弧形铸机引发的一场革命
❖ 连铸产品的均一性好,质量好; ❖ 易于实现机械化和自动化。
表:炼钢-轧钢不同生产流程的轧钢能耗比较
工艺过程
炼铸均初
连钢
加
轧 轧钢燃
钢锭热轧
铸坯
热
制 料消耗
开
清
×109J/t
坯
理
1 模铸钢锭冷装 O O O O 轧制IC-CCR
O
O
O 2.01
2 模铸钢锭开坯 O O O O 后 直 接 轧 制 IC -DR
(四)连铸工艺与操作课件.ppt
三、连铸生产工艺
上引锭杆 开浇 启车拉矫 脱引锭杆 切割 钢包更换 中间包更换
精品
停车
1.上引锭杆
油缸驱动→引 锭杆放到中间轨道→ 送入拉矫机引锭杆经 二冷段→入结晶器上 100-150mm→ 反 向 至结晶器下口 150mm 处 → 拉 矫 机 引锭杆夹紧定位→完 成安装操作.
精品
2.开 浇
连铸连轧新技术
第二讲 连铸工艺与操作
精品
主要内容
一、概 述 二、生产模拟 三、生产工艺 四、连铸设备 五、工艺参数
精品
一、概 述 1.连铸的发展概况 2.连铸机的特点 3.连铸机的机型
精品
1.连铸的发展概况
连续铸钢(连铸)是将钢水通过连铸机直接铸成钢坯 ,从而取代模铸和初轧开坯的一种钢铁生产先进 工艺。世界各国都以连铸比(连铸坯产量占钢总产 量比例)的高低来衡量钢铁工业生产结构优化的程 度和技术水平的高低。连铸的好处在于节能和提 高金属收得率。
精品
弧型连铸机:
设备高度明显下降,能够 适应提高拉速和加大断面的要 求
又分为:
直弧型连铸机:
采用直结晶器从结晶器下 保留2m直线段,然后为弧型段, 铸坯由直变弯,最后通过拉矫机 将弧形坯矫直; 优点:夹杂物易上浮,且比立弯式 高度低;
全弧型连铸机:
铸坯的运动轨迹是一条弧 线.结晶器,二冷段全为弧型,拉 矫机、切割机和出坯系统布置 在水平线上.
连轧为代 表,钢厂向紧凑化发展。
精品
2、 21世纪钢铁工业发展趋势
(1) 产品更加纯洁化 (2) 生产工艺更加高效低耗 (3) 生产过程对环境更加友好
精品
•
连铸液体金属是19世纪提出的。最初只能用
于浇铸低熔点的有色金属。1933年现代连铸之父
连铸工艺控制培训讲义
目录第一章连铸钢水的质量控制1.1 连铸钢水的温度控制------------------------- 11.2 连铸钢水的成分控制------------------------- 51.3 钢水含氧量的控制 ------------------------- 16 第二章中间包冶金2.1 中间包冶金功能 ----------------------------172.2 中间包钢水夹杂物的去除-------------------- 202.3 中间包操作过程的流动现象------------------ 242.4 中间包精炼技术---------------------------- 29 第三章连铸保护渣3.1 连铸用中间包覆盖剂------------------------ 293.2 结晶器保护渣------------------------------ 34 第四章连铸操作4.1 生产准备状态 ------------------------------414.2 备机操作 ----------------------------------444.3 浇铸操作 ----------------------------------484.4 连铸钢水拒浇的条件 ------------------------52 第五章连铸常见工艺事故及处理措施5.1 钢包事故 ----------------------------------555.2 中间包事故---------------------------------575.3 结晶器事故---------------------------------605.4 其它事故 ----------------------------------63第六章连铸的先进工艺6.1 结晶器液位自动控制 ------------------------656.2 动态软压下 -------------------------------686.3 方坯连铸电磁搅拌技术 ----------------------706.4 高碳连铸的组合电磁搅拌技术 ----------------78第一章连铸钢水的质量控制与传统的模铸相比,连铸对钢水质量有着严格的要求,它既要保证稳定适宜的钢水温度和脱氧程度,以满足可浇性;又要最大限度地降低钢中S、P杂质及气体含量,以确保连铸的顺行和铸坯质量的提高,保证合格钢水的及时供应,是提高连铸生产的基础和前提。
连铸连轧生产技术讲义(概论-1)
提高拉速措施:
•结晶器优化技术; •结晶器液面波动检测控制技术; •结晶器振动技术; •结晶器保护渣技术; •铸坯出结晶器后的支撑技术; •二冷强化冷却技术; •铸坯矫直技术; •过程自动化控制技术。
如果说提高拉速是小方坯连铸机高效化的核心,那么板坯连 铸机高效化的核心就是提高连铸机作业率。
目前提高连铸机作业率的技术主要有: (1)多炉连浇技术:异钢种多炉连浇;快速更换长水口;在线调宽;中 间包热循环使用技术;防止浸入式水口堵塞技术。 (2)连铸机设备长寿命技术:长寿命结晶器,每次镀层的浇钢量为20~ 30万t;长寿命的扇形段,上部扇形段每次维修的浇钢量100万t,下部扇 形段每次维修的浇钢量300~400万t。 (3)防漏钢的稳定化操作技术:结晶器防漏钢预报系统;结晶器漏钢报 警系统;结晶器热状态运行检测系统。 (4)缩短非浇注时间维护操作技术:上装引锭杆;扇形段自动调宽和调 厚技术;铸机设备的快速更换技术;采用各种自动检测装置;连铸机设 备自动控制水平。提高板坯连铸机设备坚固性、可靠性和自动化水平, 达到长时间的无故障在线作业,是提高板坯连铸机作业率水平的关键。
连铸的方法
根据铸坯与结晶器器壁间是否有相对运动可以分为:
有相对滑动-固定振动式结晶器 无相对滑动-移动式结晶器
连铸技术发展的四个阶段
第一阶段 (1840~1930年) 金属连续浇铸思想的启蒙阶段
1840年美国人塞勒斯(Sellers)获得连续铸铅的专利; 1856年英国人贝塞麦(Henry Bessemer)提出了采用双辊 连铸机浇铸出了金属锡箔、铅板和玻璃板,并获专利; 1887年德国人戴伦(R.M.Daelen)提出了与现代连铸机 相似的连铸设备的建议,在其开发的设备中已包括了上下敞 开的结晶器、液态金属注入、二次冷却段、引锭杆和铸坯切 割装置等。
- 1、下载文档前请自行甄别文档内容的完整性,平台不提供额外的编辑、内容补充、找答案等附加服务。
- 2、"仅部分预览"的文档,不可在线预览部分如存在完整性等问题,可反馈申请退款(可完整预览的文档不适用该条件!)。
- 3、如文档侵犯您的权益,请联系客服反馈,我们会尽快为您处理(人工客服工作时间:9:00-18:30)。
中间包预热装置
长水口机械手 水口快换装置
大包回转台
主要功能-称重、旋转、事故旋转、升降、倾 动、锁紧和包盖操作。
中间包与中间包车
中间包的结构能使中间罐内钢水流动模式最 优化,促进夹杂物上浮。中间罐钢水的深度满足 在正常换钢包时不会出现涡流。
3、50年代-连续铸钢进入实用化
30余台方坯铸机建成; 加拿大Atlas Steel厂54年建成610mm宽板坯 铸 机; 1959、1960年苏联建成宽板坯铸机; 采用连铸的多是电炉钢厂,钢种多为特殊钢; 技术水平较低:产量低、作业率低,不能实现 连浇。
4、60年代-连铸发展起步阶段
连铸工艺技术
首钢京唐:王胜东
连续铸钢的回顾与发展
首钢京唐连铸机工艺特点
首钢京唐连铸机设备组成
连铸工艺控制技术 连铸坯表面质量
一、连铸技术发展回顾
1、早期的连铸技术开发(1886~1937)
浇铸有色金属; 金属液面波动大; 拉漏频繁,采取的对策主要靠提高结晶器冷却 强度以及“ 拉-停-拉”方法以增加坯壳厚 度,减少拉漏。
技术特点
大包下渣 检测 结晶器液位控制 结晶器电磁流场控制 液压振动控制 漏钢预报 结晶器冷却控制 中间包液位 控制 凝固模型与 动态二冷控制 质量判定 (QUART)
动态轻压下 控制
优化切割控制 板坯跟踪
液压控制
1650连铸机技术特点
• 大包回转台:蝶形大包回转台,带大包倾斜 功能,可减少大包余钢 • 大包盖升降装置:安装在大包回转台上部 • 保护浇铸:从中间包流入结晶器的钢水采用 浸入式水口进行保护 • 钢水连续测温系统:将在中间包内安装钢水 连续测温装置,以便在浇铸过程中检测钢水 温度 • 浸入式水口快换装置:采用浸入式水口快换 装置,以便在浇铸位更换浸入式水口
Scovill Mfg公司的Junghans铸机示意图
Bristol Brass公司的Rossi铸机示意图
连铸由有色金属转向浇铸钢水
40年代末欧、美、苏等钢厂开始进行钢水连 铸试验; 1954年Halliday开发的“ 负滑脱”振动技 术” 取得突破; 结晶器润滑剂、浸入式水口等技术; 连铸浇铸钢水取得成功。
1650连铸机技术特点
• 结晶器振动台:INMO结晶器系统提供了精确 的结晶器振动导向。液压振动装置可最大限度 的灵活选择振动参数。可单独对振动行程、振 动频率以及振动曲线进行调整,以改善润滑效 果,减少振痕深度。 • 结晶器及扇形0段的快速更换:由于所有的介 质连接自动完成,因此可实现结晶器及弯曲段 的快速更换。 • 结晶器框架:对于维修铜板,可用最少的时间 从结晶器框架上将铜板和背板快速地移出,同 时方便所有维修操作
产量,百万吨
日本
西欧
美国
其它各国
年代
60~75年间世界连铸坯产量的增长
6、80年代-连铸技术成熟阶段
生产高质量钢铸坯技术和体制已经确立; 板坯连铸开始采用HCR、HDR工艺; 高速连铸、中间包加热、液压振动、电磁制动 、 拉漏预报、二冷动态控制、轻压下等大批新 工 艺技术采用; 年产300万吨以上的大型连铸板坯铸机建立; 发达国家连铸比超过或接近90%; 以高拉速、高作业率、高质量、高度自动化、 高稳定性生产为标志,常规连铸达到了其成熟 阶段。
板坯喷号机
• 基本上喷号机包括一个喷嘴,其可在板坯上写 出较大的、清晰的、易分辨的字符。 • 喷号过程的原理是以热金属涂层为基础的。通 过喷枪喂送两根金属丝并且使用产生电弧的电 流使其同时熔化。这样热金属被喷入到板坯的 表面。 • 字符的形式由喷号装臵的自动化系统确定
四、连铸工艺控制技术
1、钢水准备
早期连铸方法示意图
早期连铸方法示意图
早期连铸方法示意图
2、早期连铸技术的突破
1937年,S.Junghans开发成功振动结晶 器 连铸方法并在Scovill Mfg公司投产; 1938年I.Rossi购买了德国Junghans连铸技 术的专利和设备制造权;
振动结晶器连铸技术随后在有色金属工 业应用。
重要的连铸工艺技术:
高拉速技术:
均匀强冷结晶器、保护渣、液压振动、 电磁制动、拉漏预报、辊道冷却等; 大包下渣监测、大容量中间包、保护浇铸、 中间包多重堰、过滤器、浸入式水口防堵 塞、结晶器液面控制、防卷渣、FC结晶器、 电磁搅拌、中间包加热、亚包晶钢铸坯表 面裂纹防止、多点矫直、二冷动态控制、 喷嘴堵塞自动监测、二冷喷水宽度控制、 压缩铸造、轻压下等;
弧形铸机开发成功; 实现多炉连浇、船板等钢种连铸的成功表明了 连铸在产量、质量方面的优越性; 日本钢铁业开始引入连铸; 1966年英国Shelton钢铁公司在其卡尔多转炉 钢厂实现全连铸; 主要是欧洲电炉钢厂和美国的平炉钢厂采用连 铸,1970年世界连铸比为4.4%。
1963年瑞士Von Moos厂建成的85×85mm弧形试验铸机
1965年前苏联建成的弧形小板坯铸机
1964年德国曼内斯曼胡金根厂建成的低压头弧形宽板坯铸机
5、70年代-连铸快速发展时期
日本钢铁厂大规模采用连铸技术; 1972年新日铁大分厂300t转炉-3台板坯铸机 结合实现全连铸; 大包回转台、滑动水口、集装辊扇形段、保护 浇铸、液面控制、上装引锭杆、电磁搅拌、多 点矫直、小辊密排、二冷自动配水、小方坯多 级结晶器、刚性引锭杆等开发成功; 低碳铝合金钢、沸腾钢替代钢种等连铸成功, 低碳铝合金钢实现了铸坯无清理; 70年代末世界连铸比提高到28.4%。
零段及扇形段
零段示意图
扇形段示意图
板坯火焰切割装置
• 位臵:在火焰切割机入口辊道之后 • 功能:将坯尾废钢与热铸坯分离并把最后的 板坯按预定的长度进行分割;测量将被切割 的板坯长度 • 部件:一台火焰切割机(支撑框架和切割小 车);支撑框架;测量辊
去毛刺机
通过锻造合金钢制成的一系列对称(双边) 的锤子在线去除毛刺。这些锤子沿去毛刺辊以 60度的角度悬挂在6个轴上,当辊子转动时, 离心力使锤子延伸至其去毛刺直径。由于辊子 的速度和锤子的重量,在毛刺从产品上去除之 前,毛刺被高速的锤子敲击若干次,然后毛刺 通过流槽被导入到废钢容器内。
结晶器液压振动 台
零段及扇形段
零段布置在结晶器与扇形段之间,具有导向、支 撑结晶器下口出来的热铸坯,提供足够的垂直高度起 到浮渣的作用,并将铸坯从结晶器导向扇形段,同时 对铸坯进行充分的冷却。在零号扇形段内,铸坯经过 连续弯曲到铸机的基本半径。
扇形段包括1~19#扇形段。铸坯在扇形段中通 过气水冷却直到完全凝固。在浇铸过程中,扇形段对 铸坯提供支撑、运输和导向,也可运输引锭杆。扇形 段可全程实现远程辊缝调节,4~19#扇形段可对铸坯 凝固末端实施轻压下。
要有合适的钢水温度 浇注过程所需要的过热度,T=T出钢- T过程-Tl
Tl=1536 - (90 * C + 6.2 * Si + 1.7 * Mn + 28 * P + 40 * S + 2.6 * Cu + 2.9 * Ni + 1.8 * Cr + 5.1 * Al)
T过程= T1+ T2+ T3+ T4+ T5
7、90年代-传统连铸的进一步完善和近 终形连铸技术的兴起
传统连铸向进一步降低生产成本、强化高级产 品生产、注重环境的方向发展; 近终形连铸取得成功: - CSP、ISP等薄板坯连铸技术被愈来愈多的 工厂采用,品种也逐步扩大; - QSP、CONROLL等中厚度板坯连铸连轧技术 开发成功。
1650连铸机技术特点
• 铸流对中:所有连铸机更换部件,均将在维修 区域相应的台架上完成预对中后再进行安装, 在将部件装入连铸机时没有必要进行对中。 • 下渣检测系统:配备下渣检测系统,用于检测 在浇铸结束时大包钢渣。该系统可使连铸机收 得率最优,并且能减少板坯夹杂。
三、首钢京唐连铸机设备组成
铸机平台设备简介
优质洁净钢铸坯生产技术:
高生产率连铸技术:
高拉速连铸技术、连铸坯热装轧制技术、结 晶器在线高速调宽技术、正常速度终止浇铸 技术、拉漏预报技术、浸入水口防堵塞技术、 结晶器辊道长寿技术、热中间包循环使用技 术等。
二、首钢京唐设计工艺要求
• 可浇铸钢种范围广泛 • 能生产高质量板坯(考虑质量因素:板坯形状、 板坯表面质量、板坯内部质量) • 可操作的拉速范围宽、高产能 • 稳定、可靠的操作 • 最大的设备稳定性 • 快速更换主要设备元件、以达到缩短将设备维 护时间的目的
措施:
■ 钢包内吹氩搅拌; ■ 加废钢降温; ■ 炉外精炼加热; ■ 中间包加热; ■ 加强调度管理。
钢水成分的控制
1、碳含量
碳是对组织影响最大的元素,多炉连浇时,钢水含碳量差 别小于0.02%,注意包晶钢存在区。 (中碳亚包晶钢碳含量控 制、超低碳钢防增碳等);
1650连铸机技术特点
• 中间包快换:可进行中间包快换操作 • 结晶器液位控制:在正常浇铸过程中,将采用 中间包塞棒对钢水流速进行自动调节,采用涡 流传感器检测结晶器液位 • 结晶器调宽:可离线进行,也可在浇铸过程中, 在同时考虑调节速度和锥度的情况下,采用最 优算法,进行安全、平稳的调节 • 结晶器铜板设计实现了均匀冷却,并且可制支 撑凝固铸坯。窄面锥度可根据板坯宽度、浇铸 速度、以及不同钢种进行动态控制
1650连铸机技术特点
• 良好的铸坯支撑装置:所有扇形段按分节辊设 计。这样设计保证极小的偏差,确保了板坯质 量(外部形状、内部裂纹、偏析等) • 辊缝调节:扇形段1-19段均具备辊缝调节装置, 通过HMI系统对辊缝进行调节 • 轻压下:扇形段4-19能进行动态轻压下 • 扇形段快速更换:所有扇形段均能实现快速更 换,具备介质自动连接功能,这样可减少检修 时间。