不同的行为批次和半连续反应器的两个化学反应的比较研究 毕业论文外文翻译
外文翻译--动力学研究与二氧化硫反应在低温和氢氧化钙在一固定床反应器
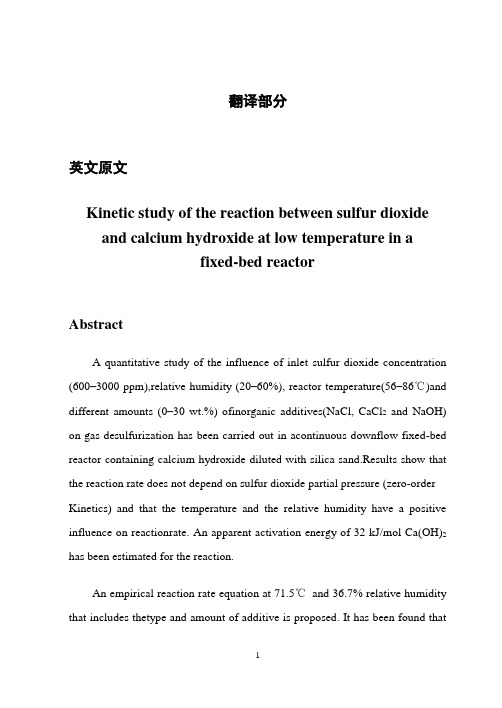
翻译部分英文原文Kinetic study of the reaction between sulfur dioxideand calcium hydroxide at low temperature in afixed-bed reactorAbstractA quantitative study of the influence of inlet sulfurdioxide concentration (600–3000 ppm),relative humidity (20–60%), reactortemperature(56–86℃)and different amounts (0–30 wt.%) ofinorganic additives(NaCl, CaCl2 andNaOH) on gas desulfurization has been carried out in acontinuous downflow fixed-bed reactor containing calcium hydroxide diluted with silica sand.Results show that the reaction rate does not depend on sulfur dioxide partial pressure (zero-order Kinetics) and that the temperature and the relative humidity have a positive influence on reactionrate. An apparent activation energy of 32 kJ/mol Ca(OH)2 has been estimated for the reaction.An empirical reaction rate equation at 71.5℃and 36.7% relative humidity that includes thetype and amount of additive is proposed. It has been found thatcalcium chloride is the bestadditive studied because it allows for a higher degree of sulfur dioxide removal. 2000 ElsevierScience B.V. All rights reserved.Keywords: Desulfurization; Sulfur dioxide; Calcium hydroxide; Kinetics; Inorganic additives1. IntroductionThe increasing concern during the last few years on the protection of the environmenthas had its influence on the design and operation of power plants, especially on thereduction of sulfur dioxide and nitrogen oxide emissions from them. They are the mainpollutants from coal and fuel-oil combustion in power plants. Both gases are responsiblefor acid rain.In USA and Europe, new power plants that use fuels with significant quantities ofsulfur have to meet severe standards to reduce these air pollutants. One of the majorproblems facing older power plants is that they were designed prior to the presentstandards for pollution control and therefore have no facilities on space to incorporatesuch controls.The technologies to control sulfur dioxide emissions can be distributed into threegroups by considering if the treatment is done before, during or after thecombustion. Itseems clear that the last group of technologies cited is the most advantageous, fromvarious points of view, for power stations which have been in operation for many years.These are called FGD technologies (Flue Gas Desulfurization),and among them, themost usedare: IDS (In-Duct Scrubbing, developed by General Electric); E-So x(developed by US EPA, Babcok and Wilcox, Ohio Coal Development Office and OhioEdison), EPRIHYPAS (Hybrid Pollution Abatement System, developed by ElectricPower Research Institute), DRAVO HALT (Hydrate Addition at Low Temperature,developed by Dravo), CONSOL COOLSIDE (developed by Consolidated CoalCom-pany)and ADVACATE(developed by Acurex and US EPA). These processes are basedon the injection of a solid sorbent plus water by spraying or injecting a slurry into theduct situated between the air preheater and the particulate collection system. Calciumhydroxide or limestone are usually used as sorbents to capture sulfur dioxide and acalcium sulfiter/sulfate mixture is obtained as the reaction product.Klingspor and Stromberg proposed a mechanism to explain the reactionbetween sulfur dioxide and calcium hydroxide or calcium carbonate in the presence ofwater vapor. According to them, when the relative humidity is low (below 20%), sulfurdioxide and water can be adsorbed on the solid surface, however, no reaction occursuntil there is at least a monolayer of water molecules adsorbed on the surface. As therelative humidity increases, less sulfur dioxide can be adsorbed on the surface becausewater adsorption on the solid occurs preferentially due to intermolecular forces. Thus,sulfur dioxide has to be absorbed on the adsorbed water, forming complexes where thesulfur atom isbound to the oxygen atom of water. This fact leads to the formation of apositive charged hydrogen atom that can combine with hydroxide or carbonate ions fromthe sorbent to form reaction intermediates and products. Experimental findings show thatthe reaction rates for lime and limestone are similar. Consequently, the complexformation SO2nH O is considered to be the rate-determining step, since all further reactions are different for the two types of sorbents. The initial rate of the process isindependent of sulfur dioxide concentration when the relative humidity is below 70%.Above this value, the reaction rate becomes gradually more and more dependent on thesulfur dioxide partial pressure. This fact can be attributed to the formation of stableconfigurations of water ligands around the sulfur dioxide molecules. Also, it has beenfound that the initial reaction rate is a very weak function of temperature but increasesexponentially with relative humidity, for both hydrated lime and limestone.Jorgensen also studied this reaction in a bench-scale sand bed reactor. Someof their conclusions point out that the calcium hydroxide conversion has a very strongdependence on relative humidity. The conversion rate is increased moderately withtemperature in agreement with activation energy of 25 kJ/mol. However, there is noclear indication of increasing conversion with increasing sulfur dioxide concentration.Ruiz-Alsop and Rochelle found that the relative humidity is the most importantvariable affecting the reaction of sulfur dioxide and calcium hydroxide. The chemicalreaction taking place at the surface of the unreacted calciumhydroxide presentszero-order kinetics in sulfur dioxide. At high relative humidity and/or high SO2concentration, the chemical reaction at the surface of the unreacted calcium hydroxidesolid controls the overall reaction rate. At low relative humidity and/or low sulfurdioxide levels, diffusion of sulfur dioxide through the solid product layer becomes therate-controlling step. The reaction rate has a weak temperature dependence. Theactivation energy of the reaction was estimated to be 12 kJ/mol.Experimental data by Krammer showed that the reaction ratedepends onthe sulfur dioxide concentration but only at low concentrations and not so obvious athigher concentrations. In contrast to other publications, they found that the influence ofSO2concentration on the reaction rate is rather linked to the conversion than to the 2relative humidity, which has a major impact on the conversion throughout the entirereaction as usually reported in literature. But they found out that the initial reaction rateseems to be independent of relative humidity and sulfur dioxide concentration, whichhad not been reported yet. They postulated that the reaction can be divided into thefollowing foursteps. During the initial stage, a chemisorption process of the sulfurdioxide on the particle surface seems to be important and the reaction rate decreasesexponentially with increasing conversion. Simultaneously, a nucleation processdominates the formation of the consecutive product layers where the reaction rateincreases with increasing relative humidity. The rate of reaction increases untilproduct layer diffusion takes over and reaction rate decreases again with conversion. Itshould be noted that only relative humidityhas an impact on product layer diffusion. Beyond a conversion of around 9%, reaction rate drops significantly, which can be dueto pore closure.Irabien consider the adsorption of sulfur dioxide on calcium hydroxideacting as a nonideal solid sorbent is the rate-limiting step. They use a parameterreferring to this nonideal behavior of the solid surface as independent of temperature butexponentially dependent on relative humidity. The authors obtained activationenergy of75 kJ/mol for the reaction.All published work thus far indicates that relative humidity has the greatest impact onthe reaction rate between sulfur dioxide and calcium hydroxide. The relative humidity isin turn correlated with the moisture content of the solids. Additives that will modify themoisture content of the calcium hydroxide solids in equilibrium with a gas phase of agiven relative humidity would then be expected to enhance the reactivity of calciumhydroxide towards sulfur dioxide in FGD processes.Organic and inorganic additives have been tested in spray dryer systems to improvethe desulfurization power of calcium hydroxide and calciumcarbonatew.It seems that inorganic hygroscopic salts such as barium, potassium, sodium and calciumchlorides and also cobalt, sodium and calcium nitrates would be the most effective ones.Some researchers also consider sodiumhydroxide as an effective additive due to itsalkaline and hygroscopic properties.Ruiz-Alsop and Rochelleindicated that deliquescence alone does notexplainthepositive effect of some salts. They contend that for an additive to be effective, it is alsonecessary that the hydroxide of the cation be very soluble, otherwise, the cation willprecipitate out as the hydroxide and the anion will form the calcium salt which could notbe hygroscopic. The effectiveness of a certain salt also depends on the relative humidity.This could be expected because when therelative humidity of the gaseous phase islower than the water activity in a saturated solution of the salt, it would not absorb waterand so, it would not enhance the calcium hydroxide reactivity. These researcherscontend that chlorides and sodium nitrate modify the properties of the product (half-hy-drated calcium sulfite) layer that is formed as the reaction takes place, therebyfacilitating the access of sulfur dioxide to unreacted calcium hydroxide, which remainsin the interior of the particle.The scope of the present work is to quantify the influence on the reaction rate ofsulfur dioxide concentration, relative humidity, temperature and type and amount ofadditive. An empirical equation, which relates the reaction rate with these variables, hasbeen obtained and an apparent activation energy value for the reaction has also beendetermined from kinetic constants at different temperatures by using the Arrhenius plot.2. Experimental sectionThis equipmentconsists of a continuous feeding and humidification system of a gaseous stream, afixed-bed reactor and an analytical system. The apparatus is operated with a personalcomputer using LabView software (NationalInstruments), which allows programmingand control of the experimental conditions, namely, nitrogen and sulfur dioxide flowrates, humidification temperature and electric resistance heating of the pipes to avoidcondensations and also provides the experimental data acquisition, in particular nitrogenand sulfur dioxide flow rates, reaction temperature, pressure, relative humidity andsulfur dioxide concentration, vs. reaction time.Simulated flue gas was obtained by mixing sulfur dioxide and nitrogen from separatecylinders in appropriate amounts using mass flow controllers Before mixing, pure nitrogenwas passed (by switching on valve 1 from thecomputer)through the humidificationsystemthat consisted of three cylindrical flasks with 200 ml of watereach submerged into a thermostatic bath. Each flask contains small glass spheres toimprove the contact between gas and water. After the humidification system, thetemperature and the relative humidity of the wet nitrogen were measured by using aVaisala HMP 235 transmitter .At the same location, the pressure was alsoMeasuredto calculate the flow rate of water vapour generated. Thewet nitrogen by-passed the reactor until the desired experimental conditionswerereached and then valve 2 was opened from the computer to allow thegaseous streamflow through the reactor. The bed was always humidified for 15 min while the sulfurdioxide analyser was set to zero. At this time, the desired flow of sulfur dioxide wasintroduced by a mass flow controller and the experiment began. Data generated duringthe experiment were stored in an EXCEL format computer file.The glass reactor, a jacketed Pyrex tube (450 mm height, 12 mm i.d.)with a porousplate to hold 1 g of dry calcium hydroxide (Probus, 99% purity and particle size smallerthan 0.05 mm in diameter)or calcium hydroxide–additive mixtures(all additives weresupplied by Fluka, 99% purity and particle size smaller than 0.05 mm in diameter) diluted with 8 g of silica sand (Merck;0.1–0.3 mm in diameter)to assure isothermaloperation and to prevent channelling due to excessive pressure drop, was thermostatedby pumping a thermal fluid (water–ethyleneglycol mixture) from an external thermostaticbath.The reacted flue gas is passed through a refrigeration systemin orderto remove water because it interferes with the SO2 analyser measurement.The output from the analyser was continu-ously collected by the computer for 1h (experiment time)and the concentration (ppm) of sulfur dioxide stored as a function of time (experimental curve). Each experiment wasconducted in the same manner except a reactive solid was substituted for the10 g ofinert silica(‘‘blank’’ experiment) to obtain a reference flow curve. The reaction rate wascalculated as SO2mol removed/h mol OH-from the area enclosed by the two curves (experimental and ‘‘blank’’). Some experiments were replicated to estimate the experimentalerror in reaction rate.3. ConclusionsIn this research, the quantitative influence of sulfur dioxide concentration, temperature,relative humidity and the type and amount of the three inorganic additives on thereaction rate between calcium hydroxide and sulfur dioxide have been determined.The SO2concentration (0–3000 ppm)was shown to have no significantinfluence on the reaction rate at a relative humidity of 38% and at 71.5℃. These results agree withthose of Ruiz-Alsop and Rochelle who indicated that sulfur dioxide concentrationdoes not influence the reaction rate at temperatures ranging from 30℃to 90℃; 17–90%relative humidity and sulfur dioxide concentration varying from 0 to 4000 ppm. Sinceour experiments are within the range of these experimental conditions, we assume thatsulfur dioxide concentration will not influence the reaction rate at our other experimentalconditions also.An empirical rate equation, which allows us to quantify the influence of temperatureand relative humidity on reaction rate has been developed and an apparent activationenergy of 32 kJ/mol Ca(OH)2 has been calculated. This value, relatively high, demonstrates the weak influence of temperature, but the reaction order of 1.2 withrespect to the relative humidity shows its strong influence on reaction rate.Three inorganic additives were tested to evaluate their quantitative influence onreaction rate. An empirical equation for each additive at 71.5℃and a relative humidityof 36.7% was developed.The kinetic rate constants for calcium chloride, sodium hydroxide and sodiumchloride were found to be respectively, 9, 5 and 0.81 times the rate constant for calciumhydroxide without any additive. The reaction orders for the weight ratio of the sameadditives were 0.6, 0.52 and y0.12, respectively. Calcium chloride is the best additivewhereas sodium chloride is an inhibitor.中文译文动力学研究与二氧化硫反应在低温和氢氧化钙在一固定床反应器摘要一个入口二氧化硫浓度(600-3000百万分之一),相对湿度(20-60%),反应器温度(影响的定量研究56-86℃)和不同的金额(0-30%重量)ofinorganic添加剂(氯化钠,氯化钙和氢氧化钠)对气体脱硫已进行acontinuous下行流了固定床反应器含有氢氧化钙与氧化硅sand.Results 稀释表明,反应速度不依赖于二氧化硫分压(零阶动力学),而温度和相对湿度对reactionrate积极的影响。
SCR反应器设计毕业设计
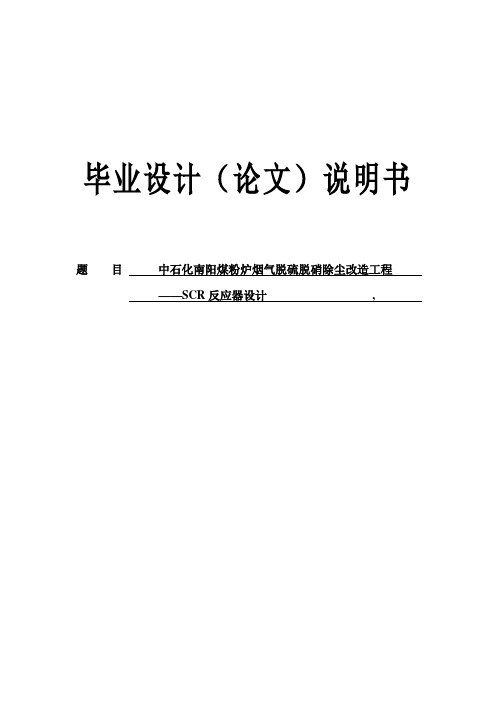
毕业设计(论文)说明书题目中石化南阳煤粉炉烟气脱硫脱硝除尘改造工程——SCR反应器设计,毕业设计(论文)原创性声明和使用授权说明原创性声明本人郑重承诺:所呈交的毕业设计(论文),是我个人在指导教师的指导下进行的研究工作及取得的成果。
尽我所知,除文中特别加以标注和致谢的地方外,不包含其他人或组织已经发表或公布过的研究成果,也不包含我为获得及其它教育机构的学位或学历而使用过的材料。
对本研究提供过帮助和做出过贡献的个人或集体,均已在文中作了明确的说明并表示了谢意。
作者签名:日期:指导教师签名:日期:使用授权说明本人完全了解大学关于收集、保存、使用毕业设计(论文)的规定,即:按照学校要求提交毕业设计(论文)的印刷本和电子版本;学校有权保存毕业设计(论文)的印刷本和电子版,并提供目录检索与阅览服务;学校可以采用影印、缩印、数字化或其它复制手段保存论文;在不以赢利为目的前提下,学校可以公布论文的部分或全部内容。
作者签名:日期:学位论文原创性声明本人郑重声明:所呈交的论文是本人在导师的指导下独立进行研究所取得的研究成果。
除了文中特别加以标注引用的内容外,本论文不包含任何其他个人或集体已经发表或撰写的成果作品。
对本文的研究做出重要贡献的个人和集体,均已在文中以明确方式标明。
本人完全意识到本声明的法律后果由本人承担。
作者签名:日期:年月日学位论文版权使用授权书本学位论文作者完全了解学校有关保留、使用学位论文的规定,同意学校保留并向国家有关部门或机构送交论文的复印件和电子版,允许论文被查阅和借阅。
本人授权大学可以将本学位论文的全部或部分内容编入有关数据库进行检索,可以采用影印、缩印或扫描等复制手段保存和汇编本学位论文。
涉密论文按学校规定处理。
作者签名:日期:年月日导师签名:日期:年月日注意事项1.设计(论文)的内容包括:1)封面(按教务处制定的标准封面格式制作)2)原创性声明3)中文摘要(300字左右)、关键词4)外文摘要、关键词5)目次页(附件不统一编入)6)论文主体部分:引言(或绪论)、正文、结论7)参考文献8)致谢9)附录(对论文支持必要时)2.论文字数要求:理工类设计(论文)正文字数不少于1万字(不包括图纸、程序清单等),文科类论文正文字数不少于1.2万字。
中英文文献以及翻译(化工类)

Foreign material:Chemical Industry1.Origins of the Chemical IndustryAlthough the use of chemicals dates back to the ancient civilizations, the evolution of what we know as the modern chemical industry started much more recently. It may be considered to have begun during the Industrial Revolution, about 1800, and developed to provide chemicals roe use by other industries. Examples are alkali for soapmaking, bleaching powder for cotton, and silica and sodium carbonate for glassmaking. It will be noted that these are all inorganic chemicals. The organic chemicals industry started in the 1860s with the exploitation of William Henry Perkin’s discovery if the first synthetic dyestuff—mauve. At the start of the twentieth century the emphasis on research on the applied aspects of chemistry in Germany had paid off handsomely, and by 1914 had resulted in the German chemical industry having 75% of the world market in chemicals. This was based on the discovery of new dyestuffs plus the development of both the contact process for sulphuric acid and the Haber process for ammonia. The later required a major technological breakthrough that of being able to carry out chemical reactions under conditions of very high pressure for the first time. The experience gained with this was to stand Germany in good stead, particularly with the rapidly increased demand for nitrogen-based compounds (ammonium salts for fertilizers and nitric acid for explosives manufacture) with the outbreak of world warⅠin 1914. This initiated profound changes which continued during the inter-war years (1918-1939).Since 1940 the chemical industry has grown at a remarkable rate, although this has slowed significantly in recent years. The lion’s share of this growth has been in the organic chemicals sector due to the development and growth of the petrochemicals area since 1950s. The explosives growth in petrochemicals in the 1960s and 1970s was largely due to the enormous increase in demand for synthetic polymers such as polyethylene, polypropylene, nylon, polyesters and epoxy resins.The chemical industry today is a very diverse sector of manufacturing industry, within which it plays a central role. It makes thousands of different chemicals whichthe general public only usually encounter as end or consumer products. These products are purchased because they have the required properties which make them suitable for some particular application, e.g. a non-stick coating for pans or a weedkiller. Thus chemicals are ultimately sold for the effects that they produce.2. Definition of the Chemical IndustryAt the turn of the century there would have been little difficulty in defining what constituted the chemical industry since only a very limited range of products was manufactured and these were clearly chemicals, e.g., alkali, sulphuric acid. At present, however, many intermediates to products produced, from raw materials like crude oil through (in some cases) many intermediates to products which may be used directly as consumer goods, or readily converted into them. The difficulty cones in deciding at which point in this sequence the particular operation ceases to be part of the chemical industry’s sphere of activities. To consider a specific example to illustrate this dilemma, emulsion paints may contain poly (vinyl chloride) / poly (vinyl acetate). Clearly, synthesis of vinyl chloride (or acetate) and its polymerization are chemical activities. However, if formulation and mixing of the paint, including the polymer, is carried out by a branch of the multinational chemical company which manufactured the ingredients, is this still part of the chemical industry of does it mow belong in the decorating industry?It is therefore apparent that, because of its diversity of operations and close links in many areas with other industries, there is no simple definition of the chemical industry. Instead each official body which collects and publishes statistics on manufacturing industry will have its definition as to which operations are classified as the chemical industry. It is important to bear this in mind when comparing statistical information which is derived from several sources.3. The Need for Chemical IndustryThe chemical industry is concerned with converting raw materials, such as crude oil, firstly into chemical intermediates and then into a tremendous variety of other chemicals. These are then used to produce consumer products, which make our livesmore comfortable or, in some cases such as pharmaceutical produces, help to maintain our well-being or even life itself. At each stage of these operations value is added to the produce and provided this added exceeds the raw material plus processing costs then a profit will be made on the operation. It is the aim of chemical industry to achieve this.It may seem strange in textbook this one to pose the question “do we need a chemical industry?” However trying to answer this question will provide(ⅰ) an indication of the range of the chemical industry’s activities, (ⅱ) its influence on our lives in everyday terms, and (ⅲ) how great is society’s need for a chemical industry. Our approach in answering the question will be to consider the industry’s co ntribution to meeting and satisfying our major needs. What are these? Clearly food (and drink) and health are paramount. Other which we shall consider in their turn are clothing and (briefly) shelter, leisure and transport.(1)Food. The chemical industry makes a major contribution to food production in at least three ways. Firstly, by making available large quantities of artificial fertilizers which are used to replace the elements (mainly nitrogen, phosphorus and potassium) which are removed as nutrients by the growing crops during modern intensive farming. Secondly, by manufacturing crop protection chemicals, i.e., pesticides, which markedly reduce the proportion of the crops consumed by pests. Thirdly, by producing veterinary products which protect livestock from disease or cure their infections.(2)Health. We are all aware of the major contribution which the pharmaceutical sector of the industry has made to help keep us all healthy, e.g. by curing bacterial infections with antibiotics, and even extending life itself, e.g. ß–blockers to lower blood pressure.(3)Clothing. The improvement in properties of modern synthetic fibers over the traditional clothing materials (e.g. cotton and wool) has been quite remarkable. Thus shirts, dresses and suits made from polyesters like Terylene and polyamides like Nylon are crease-resistant, machine-washable, and drip-dry or non-iron. They are also cheaper than natural materials.Parallel developments in the discovery of modern synthetic dyes and the technology to “bond” th em to the fiber has resulted in a tremendous increase in the variety of colors available to the fashion designer. Indeed they now span almost every color and hue of the visible spectrum. Indeed if a suitable shade is not available, structural modification of an existing dye to achieve this canreadily be carried out, provided there is a satisfactory market for the product.Other major advances in this sphere have been in color-fastness, i.e., resistance to the dye being washed out when the garment is cleaned.(4)Shelter, leisure and transport. In terms of shelter the contribution of modern synthetic polymers has been substantial. Plastics are tending to replace traditional building materials like wood because they are lighter, maintenance-free (i.e. they are resistant to weathering and do not need painting). Other polymers, e.g. urea-formaldehyde and polyurethanes, are important insulating materials f or reducing heat losses and hence reducing energy usage.Plastics and polymers have made a considerable impact on leisure activities with applications ranging from all-weather artificial surfaces for athletic tracks, football pitches and tennis courts to nylon strings for racquets and items like golf balls and footballs made entirely from synthetic materials.Like wise the chemical industry’s contribution to transport over the years has led to major improvements. Thus development of improved additives like anti-oxidants and viscosity index improves for engine oil has enabled routine servicing intervals to increase from 3000 to 6000 to 12000 miles. Research and development work has also resulted in improved lubricating oils and greases, and better brake fluids. Yet again the contribution of polymers and plastics has been very striking with the proportion of the total automobile derived from these materials—dashboard, steering wheel, seat padding and covering etc.—now exceeding 40%.So it is quite apparent even from a brief look at the chemical industry’s contribution to meeting our major needs that life in the world would be very different without the products of the industry. Indeed the level of a country’s development may be judged by the production level and sophistication of its chemical industry4. Research and Development (R&D) in Chemical IndustriesOne of the main reasons for the rapid growth of the chemical industry in the developed world has been its great commitment to, and investment in research and development (R&D). A typical figure is 5% of sales income, with this figure being almost doubled for the most research intensive sector, pharmaceuticals. It is important to emphasize that we are quoting percentages here not of profits but of sales income, i.e. the total money received, which has to pay for raw materials, overheads, staff salaries, etc. as well. In the past this tremendous investment has paid off well, leading to many useful and valuable products being introduced to the market. Examplesinclude synthetic polymers like nylons and polyesters, and drugs and pesticides. Although the number of new products introduced to the market has declined significantly in recent years, and in times of recession the research department is usually one of the first to suffer cutbacks, the commitment to R&D remains at a very high level.The chemical industry is a very high technology industry which takes full advantage of the latest advances in electronics and engineering. Computers are very widely used for all sorts of applications, from automatic control of chemical plants, to molecular modeling of structures of new compounds, to the control of analytical instruments in the laboratory.Individual manufacturing plants have capacities ranging from just a few tones per year in the fine chemicals area to the real giants in the fertilizer and petrochemical sectors which range up to 500,000 tonnes. The latter requires enormous capital investment, since a single plant of this size can now cost $520 million! This, coupled with the widespread use of automatic control equipment, helps to explain why the chemical industry is capital-rather than labor-intensive.The major chemical companies are truly multinational and operate their sales and marketing activities in most of the countries of the world, and they also have manufacturing units in a number of countries. This international outlook for operations, or globalization, is a growing trend within the chemical industry, with companies expanding their activities either by erecting manufacturing units in other countries or by taking over companies which are already operating there.化学工业1.化学工业的起源尽管化学品的使用可以追溯到古代文明时代,我们所谓的现代化学工业的发展却是非常近代(才开始的)。
外文翻译

PET的固相聚合反应:氮保护和高真空的影响摘要:我们研究过在固相聚合(SSP)薄(180mm)聚对苯二甲酸乙二醇酯(PET)切片反应条件的影响,在250℃下特性粘度(IV)增加和端基官能团耗尽,当固相聚合反应在真空条件下反应2小时,特性粘度从0.58增加到2.4l/g。
随着时间的推移,最初反应速率大大减慢,反应6小时特性粘度(IV)增加近2.75l/g,但我们仍能检测到羧基和末端羟基官能团的浓度分别为3和5,这表明结晶在限制末端官能团相互靠近,从而使官能团处于非活跃状态的作用,在这个阶段,升高温度至270℃使PET在真空下再次熔融,特性粘度在1.5小时内增至2.97l/g,可能由于结晶限制的释放,在熔体中允许一些不活跃端基相互接近。
我们发现这些暂时不活跃端基的计算对于一个特性粘度达1.3l/g的固相聚合的良好动力学描述是不可缺少的。
当使用氮气作为载气,比较在真空下的固相聚合,其反应速率和分子量会有所降低。
升华物是在固相聚合反应的真空条件下收集的,升华物由对苯二甲酸,单羟基对苯二甲酸酯,双羟乙基对苯二甲酸酯和环状低聚物组成。
这表明真空固相聚合的一个新的缩合机制的出现1介绍:固相聚合PET的后聚合常用来提高聚合物的数均分子量超过20000,期望应用于饮料瓶,轮胎和工业纤维。
当固相PET颗粒被加热到T=200~258℃时,通常认为有下列反应发生:酯交换/缩聚在这里,水和乙醇(EG)是可逆反应的副产物,无论通入惰性气体或保持减压,或者两种方法结合移除副产物都可促进正向反应的进行[6,7].整体反应速率受到内在反应速率结合的影响,活跃端基的扩散受[23-25]限制或促进酯交换反应[20],副产物从颗粒的内部扩散到颗粒表面[3,11,14,15,22,26]并且通过惰性气体移除。
高的客观反应速率下,尚未能根据酸(COOH)和末端羟基(OH),二乙二醇,醛等的浓度定义控制产品质量,研究已探讨反应参数(如温度[1,3,8-10,15,27-29]),颗粒大小[3,8,9,23,27,28],结晶水平[13,16,25,27,28],载气性质和速度[1,8,13,14,15,22],催化剂浓度[30,31]等的影响。
连串—平行及连串反应的等温优化毕业论文

毕业论文题目:连串—平行及连串反应的等温优化学院:物理与化学学院年级、专业:2009级、化学学生:黄芮学号:312009*********指导教师:彭昌荣完成日期:2013年 5月 20日目录摘要 (3)Abstract (4)前言 (5)1 等温优化计算实例 (5)1.1 等温优化结果 (7)2 非等温优化计算实例 (12)2.1 对该反应作等温搜索的计算结果 (15)3 结果与讨论 (16)总结与体会 (18)谢辞 (19)参考文献 (20)附MATLAB程序 (21)2摘要在精细化工生产中,以复杂反应系统为特征的、能生成不希望的最终产物的连串-平行反应或连串反应是俯拾皆是的,而这一类反应的目标又常常是希望获得高质量和高纯度的产品,根据反应的特点和约束条件,进行操作条件的优化是必要的。
本文首先对一个连串-平行反应实例的操作条件进行了等温优化并编写了相应的Matlab程序;其次对一个经典的连串反应的温度控制问题,采用各间隔反应时间内等温的方法进行了目标产物浓度最大问题的优化并编写了相应的Matlab 程序;第二个计算实例中提供的优化算法比庞特里亚金极大值原理要简单的多,尽管其优化的温度分布是次优的,但是,可以通过改变程序中间隔反应时间的数目来逼近最优。
关键词:连串-平行反应连串反应等温反应时间间隔庞特里亚金极大值原理3AbstractConsecutive-parallel or consecutive reaction is still widely used in fine chemical production which is characterized by quite complex reaction system which can produce undesirable end products. As the aim of the fine chemical industry is to produce high quality and purity products,It is essential to optimize operating conditions,taking into account constrains and reation’s characteristics. In this work, the first part of this paper dealed with the optimal isothermal operating conditions of a consecutive-parallel and the corresponding Matlab program for this type of reaction was programmed. Then the optimal temperature profile of a classical consecutive, taking into account the mximum concentration of objective product, and the corresponding Matlab program for this type of reaction were carried out by the several isothermal subintervals of reaction time on the basis of the characteristics of the studied reaction. The second computing example’s method proposed by myself compared with Pontryagin maximum principle was relatively simple. By Increasing the number of isothermal subintervals of reaction time, I’m sure the optimal results can approach to Pontryagin maximum principle’s computing results.Keywords: Consecutive-parallel reaction; Consecutive reaction; Isothermal subintervals of reaction time;Pontryagin maximum principle.45前 言连串(平行)反应是反应产物可以进一步反应生成其他产物的反应, 它是化学工业中常见的一类复杂反应[1,2]。
外文文献翻译

I. Simakovaa, A. Koskina, I. Deliya, A. SimakovbaBoreskov Institute of Catalysis, Siberian Branch of Academy of Sciences, pr. Ak. Lavrentieva, 5,630090, Novosibirsk, Russia, simakova@catalysis.ru,bCentro de Ciencias de la MateriaCondensada, Universidad NacionalAutónoma de México,Apdo.Postal 2681, Ensenada, B.C., México, andrey@ccmc.unam.mx摘要纳米钯催化剂的应用已获得超过过去几年中日益增长的重要性。
精细有机合成钯基催化方法允许更换传统的多步有机合成技术的劳动消耗,并从成本和环境影响的角度来看提供改善。
已培育的高比表面积活性炭的“Sibunit”的基板作为催化剂的基材使用,无论是在酸性或是碱性介质,同时在其表面超强酸性中心可以促进催化运行过程中产生不良反应情况下的化学惰性。
一种转换α-蒎烯商业的生物活性化合物衍生品和香水,以及与太阳紫外线过滤属性屏幕,作为一个重要的中间步骤,涉及催化加氢。
目前的工作目的是所要澄清的因素,有利于碳金属Pd的分散。
碳还原温度和预处理影响金属的大小在关于“Sibunit”选择性verbenol转换催化剂制备钯表面研究。
用电子显微镜法(TEM)来显示钯碳表面影响双氧水,硝酸氧化的金属分散度,硝酸。
在Pd / C催化剂样品verbenol加氢反应的催化活性是确定的。
最活跃的催化剂样品动力学特性在verbenol加氢反应获得。
关键词:TEM,钯,活性炭,萜类,香料,精细化学品1.引言超过钯金属催化剂的选择性加氢是用来生产有机化工原料最令人鼓舞的方式,包括染料等东西,药品,香料,维生素和有价值的商业中间体[1]。
化学反应工程

管式及釜式连续流动反应器:反应物连续不断地 加入反应器,同时产物连续不断地流出反应器, 如果是定态下操作,反应物进料时的组成和流量 及产物的组成和流量都不随计时器显示的时间而 变。 加料
均匀混合
加料
产物 产物 图2.3 釜式连续流动反应器
图2.2 管式连续流动反应器
半间歇反应器:将反应物 A 先放入反应器中,在 一定温度和压力下,反应物 B 连续加入反应器, 反应产物保留在反应器中,即为半间歇反应器。
均相反应动力学:是研究各种因素,如温度、催 化剂、反应物组成和压力等对反应速率、反应产 物分布的影响,并确定表达这些影响因素与反应 速率之间定量关系的速率方程
3.1 化学反应速率
化学反应速率:单位时间内,单位反应混合物体 积中反应物的反应量或产物的生成量。反应速率 是指某一瞬间的“瞬时反应速率”
生成目的产物所消耗的关键组分的物质的量 S 已转化的关键组分的物质的量
而
Y
生成目的产物所消耗的关键组分的物质的量 进入反应系统的关键组分的物质的量
由上两式可得:
Y Sx
第3章 均相反应动力学基础
均相反应:参与反应的各物质均处于同一个相内 进行化学反应则称为均相反应。 均相反应的前提:参与反应的所有物料达到分子 尺度上的均匀,成为均一的气相或液相
工业反应过程的原料中,各反应组分之间往往不 符合化学计量数的关系,此时通常选择不过量的 反应物计算转化率,这样的组分称为关键组分。 一般选择价格高的为关键组分。
2.2.4 多重反应的收率及选择性 对于单一反应,反应物的转化率即为产物的生成率 对于多重反应(如同时反应、平行反应、连串反应 等),除了反应物转化率的概念外还必须由目的产 物的收率的概念,收率以Y表示,其定义如下:
化工专业英语翻译(全21单元)
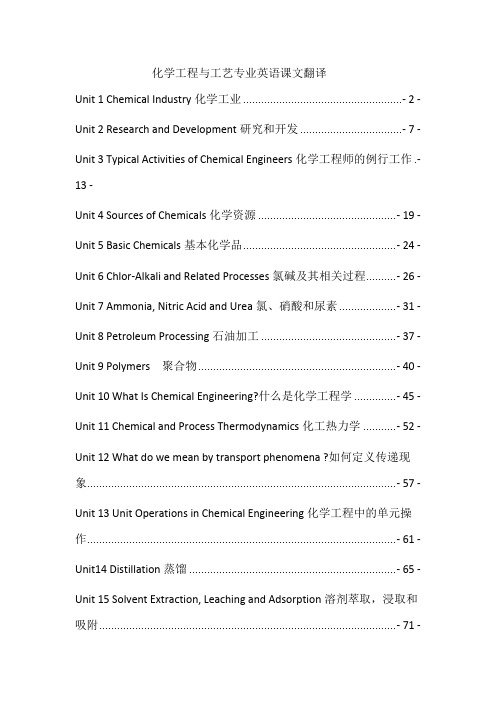
化学工程与工艺专业英语课文翻译Unit 1 Chemical Industry化学工业 ..................................................... - 2 - Unit 2 Research and Development研究和开发 .................................. - 7 - Unit 3 Typical Activities of Chemical Engineers化学工程师的例行工作 . -13 -Unit 4 Sources of Chemicals化学资源 .............................................. - 19 - Unit 5 Basic Chemicals基本化学品................................................... - 24 - Unit 6 Chlor-Alkali and Related Processes氯碱及其相关过程.......... - 26 - Unit 7 Ammonia, Nitric Acid and Urea氯、硝酸和尿素 ................... - 31 - Unit 8 Petroleum Processing石油加工 ............................................. - 37 - Unit 9 Polymers 聚合物.................................................................. - 40 - Unit 10 What Is Chemical Engineering?什么是化学工程学 .............. - 45 - Unit 11 Chemical and Process Thermodynamics化工热力学 ........... - 52 - Unit 12 What do we mean by transport phenomena ?如何定义传递现象....................................................................................................... - 57 - Unit 13 Unit Operations in Chemical Engineering化学工程中的单元操作....................................................................................................... - 61 - Unit14 Distillation蒸馏 ..................................................................... - 65 - Unit 15 Solvent Extraction, Leaching and Adsorption溶剂萃取,浸取和吸附................................................................................................... - 71 -Unit 16 Evaporation, Crystallization and Drying蒸发、结晶和干燥.- 76 - Unit 17 Chemical Reaction Engineering化学反应工程 ..................... - 82 - Unit18 Chemical Engineering Modeling化工建模 ............................ - 88 - Unit 19 Introduction to Process Design过程设计简介 ..................... - 92 - Unit 20 Material Science and Chemical Engineer材料科学和化学工程 .. -97 -Unit 21 Chemical Industry and Environment化学工业与环境 ....... - 103 -Unit 1 Chemical Industry化学工业1.化学工业的起源尽管化学品的使用可以追溯到古代文明时代,我们所谓的现代化学工业的发展却是非常近代(才开始的)。
- 1、下载文档前请自行甄别文档内容的完整性,平台不提供额外的编辑、内容补充、找答案等附加服务。
- 2、"仅部分预览"的文档,不可在线预览部分如存在完整性等问题,可反馈申请退款(可完整预览的文档不适用该条件!)。
- 3、如文档侵犯您的权益,请联系客服反馈,我们会尽快为您处理(人工客服工作时间:9:00-18:30)。
不同的行为批次和半连续反应器的两个化学反应的比较研究 M.D. Graua,1, J.M. Nougués b,2, L. Puigjaner b,*,2
a矿业及天然资源工程系,曼雷沙大学,加泰罗尼亚理工大学,AV.西班牙曼雷沙61-73基地,08240 . b巴塞罗那工业工程学院,加泰罗尼亚理工大学化学工程系,AV.西班牙巴塞罗那,对角线647,08028. 2001年10月收到,2002年2月19日发表 摘要:基于不同的行为的两个反应,批处理和半间歇反应器性能之间的比较研
究已经进行了在玻璃夹套设置与测量5升的反应器中,数据采集和控制系统。所选择的反应是酸 - 碱反应(乙酸乙酯皂化反应),和一个具有高的反应热(硫代硫酸钠,过氧化反应)的氧化 - 还原反应。甲第一差值的方法中,用于建立的动力学方程。对于使用的酸 - 碱反应的等温方法,根据该溶液的电导率,用于氧化反应的温度的测量的基础上使用的绝热方法。 此工作的重点在于得到的物种的浓度,在反应器中,通过实验测量与不同的传感器(pH,温度,等)所需要的值,以得到的浓度分布。对于酸 - 碱反应,它可以转换成浓度值的反应溶液的pH值测量。在氧化反应的情况下,通过测量唯一的反应器的温度为绝热的批处理模式下的操作,和在半间歇法的操作模式通过仿真得到的浓度分布。以前被验证实验获得的温度分布的数学模型。
关键词:批处理和半间歇反应器 ;模型 ;反应动力学
命名法 a:化学计量系数反应物A Ai:内传热面积(米2) A0:以外的传热面积(米2) B:反应物B的化学计量系数 cA :反应物的浓度(NaOH或H 2 O 2)(千摩尔米-3) cA0:初始反应物的浓度甲(千摩尔米-3) cA1:初始反应物的浓度在坦克(千摩尔米-3) cB:反应物B的浓度(千摩尔米-3) cB0:反应物B的初始浓度(千摩尔米-3) cB1:罐中反应物B的初始浓度(千摩尔米-3) cP:浓度的产品(千摩尔米-3) CJ:护套的流体的热容量(千焦耳千克-1 K -1) CP:的反应物的热容量(千焦耳千克-1 K -1) CM:的壁的热容量(千焦耳千克-1 K -1) Ea:活化能(千焦耳千摩尔-1) FW:护套的流体流(米3 s-1 ) F0: 添加流量(米3 s-1 ) [10] ,但反应物和产物的浓度的演变没有调查,这是非常重要的是要优化 运行性能,因为它已经指出,Hugo[11] 等人。 在这项工作中,为酸 - 碱反应,在反应器中存在的物种原位浓度通过测量溶液的pH值来确定。对于氧化还原反应,反应的电压分布实验得到,但其转换成浓度分布被认为是非常困难的。在这种情况下,浓度分布是通过模拟获得的。的动态的数学模型,预测的热行为的间歇式反应器,并在反应过程中反应物和产物的浓度的演变。对于该反应中,它有可能以获得实验的浓度分布,仅在绝热操作的箱子。在这种模式的操作中,它是通过只测量反应温度可能遵循的浓度演化。
为酸-碱反应的(低反应热),其中反应器的温度将保持控制,两种操作模式(分批或半间歇)是可能的。在硫代硫酸盐反应(非常的放热反应)的情况下,温度控制是唯一可行的半间歇反应器中。在这种情况下,当一组点被选择的反应物料的温度,也可以通过操纵一种反应物的进料速率,入口夹套温度保持在一个前缀的值来控制反应。因此,这种操作模式可以被使用,以控制反应,并且,它是特别有用的高度放热的过程,其中,安全是一个主要问题。从这个意义上说,的的作品Steensma和Westertep[12]和Stoessel[2]是非常相关的。Hugo和Steinbach[13]补料批式反应器和连续搅拌釜式反应器安全之间的比较研究。 纸张主要作用域从pH值和温度数据的浓度分布的模拟,然后预测实验的控制行为。因此,一个关键的贡献,目前的工作重点是在两个均相反应的行为的比较研究,批次和半连续反应器中进行。这些反应可再现的实验得到的,使用的传感器的pH,温度或潜在的,大量的数据,以便获得适当的信息,用来比较的批次和半间歇反应器中的操作模式的行为。一般,该比较是仅使用温度测量。这项工作给特殊的重要性,得到的浓度分布(通过pH值或温度的实验性的措施),显示出更好的两种操作模式之间的不同行为。在这种方式中,该研究导致一种推论批处理的方式来控制和半间歇反应器。 此外,使用简单的反应已被特别选择,因为,即使在发展的动能表达式,使用的方法是不同的,使得可以比较的等温反应器中和一个绝热反应器的行为。利益的工作还包括在比较两个非常不同的反应速度和热行为反应。 2、数学模型 在一般的方式,考虑这两个反应可以表示为: aA + bB→cC + dD 其中的一个a,b,c,和d是不同的对于每个反应: CH3COOCH2CH3 + NaOH→ CH3COONa + CH3CH2OH Na2S2O3 + 2H2O2 →Na2S3O6 + Na2SO4 + 2H2O 将反应率被假定为成比例的反应物A和B的浓度的第一顺序,和溶液的密度是恒定的:
r = kcAcB…………………………………………………………………………(1)
其中 ,k 是一个函数,所述的温度的Arrhenius表达式: k = k0 e−EaR(T+273) ………………………………………………………… (2) 两种方法可以通过以下方式获得的动力学参数 k 0 和 E a。 2.1.等温法
得到的溶液在不同温度下的电导率的档案。因此,一组在不同温度下的k值 可以以下方式获得的,然后通过绘制lnk对1 T 式中的对数表达 Eq(2) ,k 0
和Ea值可以很容易地获
得:
……………………………………………………(3)2.2.(直
接法) 考虑到能量平衡方程完全是被称为反应物料,获得以下表达式:
………………………………………………………………(4) (4)给出了在每一时刻的速率常数: ………………………………………………………………… (5) 导数d T d t 可以计算从所记录的温度-时间曲线。然后时,ln k被计算,使用从Ea得到的值(5) 。 下面的过程是类似的等温方法。 批处理和半间歇反应器的动态行为可以被描述由一组微分方程套壁和夹克内的循环流体的能量平衡的反应混合物中,产生的质量和能量平衡。
批式反应器的整体质量平衡: …………………………………………………………………………(6) ……………………………………………………………………………
(7) 半间歇反应器的整体质量平衡:…………………………………………………………………… (8) ……………………………………………………………………… …(9)间歇式反应器的组件的质量平衡: …………………………………………………………… (10) …………………………………………………
…………(11) 半间歇反应器中的组件的质量平衡:
…………………………………………………… (12) …………………………………………………………… (13) 对于pH值的酸 - 碱反应,转化浓度分布不同操作模式的研究需要不同的表达式。如果A代表NaOH和乙乙酸乙酯,唯一的贡献对pH值的NaOH的存在是由于,因为乙酸钠的贡献可以忽略不计。在这些条件下: POH = −log cA ………………………………………………………………
(14)不然
cA = 10(pH−14) …………………………………………………………………(15)否则为间歇式反应器中,浓度可以表示为:
cA = cA0(1 − x)………………………………………………………………… (16)从式(15)和 (16) : ……………………………………………………………(17)半间歇反应器中时,被认为是,试剂A的添加效果,必须考虑该混合物的初始浓度在加入时间: ……………………………………………………………………(18)和
……………………………………………………………(19)当馈送的NaOH停止反应器中在批处理模式下操作,并建模方程是前面所指出的那些。
用于氧化反应和绝热的间歇式反应器中,从(4)和(10)得到: …………………………………………………………………(20)通过集成这个方程,得到下面的表达式:
………………………………………………………………(21)
的差异之间的初始温度和最终温度,当转换是 x = 1时,,被定义为Δ T ad: ……………………………………………………………… (22)公式(21)可以改写为: ……………………………………………………………………(23)使用表达式(23),可以得到具有不同的反应物和产物的浓度。 批式反应器的能量平衡: ………………………………………………… (24) 半间歇反应器的能量平衡:
CpVQCpcHrkcVTTadFdtdMBAT)(
0……………………………………… (25)
批次和半间歇反应器外壁的能量平衡: …………………………………………………………………(26) 通过 QM = [14]所示。3、工厂介绍
在中试规模的反应器中(图1)中,pH值,电导率,电压和温度的已获得的实验措施。它由一个5升玻璃夹套反应器中,设置有一个数据采集系统基于GPIB总线和PC软件。
图1 试验工厂。 在夹套中循环的流体的流率可以前缀或通过差开闭阀控制,提供一种替代
的加热-冷却流体(热水或冷水),表1中表示的不同模式的状态的阀门操作。 表1中 阀门
阀门 行动 Ia II b IIIc V1 反应A入口 X X(*) V2 反应B入口 X V3 护套流体入口 X X