镁合金半固态成型
半固态镁合金成形技术概述

重庆科技学院课程结业考试(论文)题目半固态镁合金成形技术概论院(系)冶金与材料工程学院专业班级材料工程技术08-02学生姓名刘明强学号2008630578任课教师孙建春职称讲师评定成绩___ _ __ 评语:年月日半固态镁合金成形技术概述姓名:刘明强学号:2008630578摘要:半固态镁合金制备是在20世纪末新起的最新制备镁合金的技术,半固态技术被认为是21世纪最具发展前途的近终成形技术之一[1]。
本文旨在为大家阐述半固态镁合金成形技术的基本概论,包括镁合金的相关阐述(性能、应用、加工技术等);半固态成形技术的概念,半固态金属浆料的制备,以及半固态加工材料的制备技术等;重点是镁合金与半固态成形技术的结合,包括半固态镁合金浆料的制备,半固态镁合金材料的制备,半固态镁合金材料的热处理,半固态镁合金成形技术的国内国外现状和未来展望,同时阐述半固态镁合金制备的优缺点。
关键词:半固态、镁合金、浆料、半固态成形、流变成形前言:镁及镁合金作为一种新型的应用材料,近年来已广泛应用于军用、民用领域,如在航空航天、航海、通信、医疗、广播电视、音响影像器材、微电子技术、光学仪器等领域内,在汽车、摩托车、工具、家电电器、手机、计算机及电子设备等制品中都可看到镁合金的终极,在炼钢脱硫、铝合金生产、防腐工程中都离不开镁原料。
在汽车行业,上海汽车集团公司、一汽集团、东风汽车集团、江铃汽车公司等国内大的汽车公司均开始使用镁制零部件。
根据相关研究,汽车单车自重没减轻100Kg,每百公里耗油可减少0.7L左右,每节省1L燃料可减少二氧化碳排放量 2.5g。
而通过镁合金零部件的使用可有效的实现汽车轻量化目标。
镁合金应用于交通工具,除减中和降低油耗,还可以提高整车加速、制动性能,还能降低行驶振动和噪声,提高舒适度,可以加快散热,使发动机的综合性能提高一个档次,具有良好的经济效益。
镁合金的半固态成形目前是各国研究的热点:Ya-no Ei ji等利用余热的冷却斜槽近液相线铸造或得了半固态AZ91D镁合金组织;J M Kim等利用两步加热法得到了半固态AZ91镁合金浆料;Czerwinski F开发了半固态加工与挤压、喷射成形结合在一起的心的镁合金加工技术,一Mg-9% Al-1%Zn为例分析力组织性能变化规律;Chen J Y和Fan Z研究了半固态浆料的流变模型;Koren Z等研究了AZ91和AM503镁合金半固态热压铸和冷压铸成形。
半固态镁合金成型用镁合金原材料

半固态镁合金成型用镁合金原材料半固态镁合金成型用镁合金原材料,这个听起来复杂的名词其实跟我们的生活息息相关。
想象一下,手里拿着一个轻巧的手机壳,还是一台炫酷的笔记本电脑,哎呀,那可都是镁合金的功劳!镁合金这种材料,虽然名字不算响亮,但在现代科技中可谓是“隐形英雄”。
它的特点就是轻、强、耐用,简直就是为现代制造业量身定制的。
你要知道,镁合金的密度可比铝还低,强度却高得多,简直让人想大喊一声“太牛了”。
先说说这个半固态成型的技术。
嘿,听起来像个高大上的名词,其实就是把镁合金加热到一种介于固态和液态之间的状态。
就像咱们在厨房里做饭,锅里的水刚开始冒泡,那种状态。
这时候,镁合金的流动性好,能很轻松地被模具塑形,想变成什么形状就变成什么形状,真是“随心所欲”啊!这个过程可大大提高了产品的成型精度,省去了不少后期加工的麻烦。
嘿,谁不想轻松一点呢?说到原材料,那可就有讲究了。
优质的镁合金原材料就像选菜一样,得挑得精挑细选。
纯度得高,杂质越少,成型出来的产品就越坚固。
想象一下,你吃的每一口食物,都是精挑细选的结果,好的原材料直接决定了你的餐桌上能端出什么。
就像镁合金一样,只有选对了原材料,才能让最终的产品在市场上脱颖而出,赢得消费者的青睐。
你知道吗?在生产过程中,温度的控制也是至关重要。
就像你煮饭时要掌握火候,太小了饭不熟,太大了锅就容易烧焦。
半固态成型同样讲究,温度稍微不对,可能就会出现气泡、裂纹,简直是大煞风景。
工人们就像厨房里的大厨,要时刻关注着温度,确保每一个环节都做到最好。
可别小看这些细节,往往正是这些微小的变化,决定了最终产品的质量。
除了这些,镁合金的应用场景也是五花八门。
无论是汽车、飞机,还是电子产品,镁合金都能找到它的位置。
在汽车制造中,镁合金不仅能减轻车身重量,还能提高燃油效率。
说白了,镁合金就像汽车的减肥药,吃了之后,车子轻快得像风一样,驾驶起来更顺畅。
谁不想在路上飞驰的时候,感受那种畅快淋漓的感觉呢?除了性能出色,镁合金在环保方面也是不容小觑。
镁合金半固态成型用模具

镁合金半固态成型用模具一、镁合金半固态成型用模具的设计1. 成型零件的特点镁合金半固态成型工艺的特点是成型零件具有较高的强度和硬度,同时还具有优异的成型精度和表面质量。
因此,模具的设计需要考虑成型零件的特点,在保证成型零件精度和表面质量的基础上,尽可能地降低设备成本和生产成本。
2. 模具结构设计模具结构设计是模具设计的关键环节,其设计需要考虑到材料的选择和成型零件的结构特点。
对于镁合金半固态成型,通常采用的模具结构包括上模、下模和模具芯。
上模用于固定模具,下模用于支撑工件,而模具芯则用于成型工件的内部空腔。
3. 模具材料选择模具材料的选择对模具的寿命、使用性能和成本都有着直接的影响。
对于镁合金半固态成型,需要选择耐磨性好、热膨胀系数低、导热性能好的材料。
常用的模具材料包括优质合金钢、硬质合金和陶瓷材料等。
4. 模具温控系统设计模具在半固态成型过程中需要保持一定的温度,以保证工件成型时的温度控制和成型质量。
因此,对于镁合金半固态成型用模具,需要设计相应的温控系统,以实现对模具的恒温控制和稳定工作温度。
二、镁合金半固态成型用模具的制造1. 模具加工工艺模具加工工艺通常包括数控加工、线切割、磨削和装配等环节。
数控加工通常用于模具的大型结构部件加工,如上模和下模等;线切割用于模具的小孔和内部复杂结构的加工;磨削则用于模具的表面精加工,以提高模具的表面质量和精度;最后进行模具的装配和调试,以保证模具的成型精度和稳定性。
2. 表面处理工艺模具的表面处理通常包括热处理、表面涂层等。
热处理可以提高模具的耐磨性和使用寿命,同时还可以改善模具的机械性能;表面涂层可以提高模具的表面硬度和耐磨性,从而提高模具的表面质量和成型精度。
3. 模具检测与质量控制模具的质量控制通常包括模具的检测和试模等。
模具的检测主要包括外观检测、尺寸检测和材料检测等,以保证模具的质量和使用性能;试模则用于验证模具的成型工艺和成型零件的质量,以保证模具能够正常运行和生产出合格的工件。
镁合金半固态压铸汽车产品实例

镁合金半固态压铸汽车产品实例1.引言1.1 概述镁合金半固态压铸技术是一种新兴的铸造工艺,能够制造出高强度、轻量化的汽车零部件。
随着汽车工业的发展和对轻量化材料需求的增加,镁合金半固态压铸技术得到了广泛关注和应用。
本文将通过介绍镁合金半固态压铸技术的原理和特点,以及汽车产品中的应用实例,来探讨这一技术在汽车制造领域中的潜力和前景。
镁合金半固态压铸技术是将镁合金加热到半固态状态,通过压铸成型得到所需的零部件。
相比传统的压铸工艺,镁合金半固态压铸技术具有以下几个显著的优势。
首先,半固态状态下的镁合金具有较低的黏度和较高的塑性,使得其在压铸过程中更容易充填模腔,提高了产品的成形质量和尺寸精度。
其次,半固态压铸过程中的镁合金具有较低的热应力,可有效降低零部件的变形和缩松现象。
此外,由于镁合金具有良好的可再生性和循环利用性,采用半固态压铸技术制造汽车零部件有助于环境保护和可持续发展。
在汽车产品中,镁合金半固态压铸技术已得到广泛应用。
一方面,由于镁合金具有优异的强度和刚度,采用半固态压铸技术可以制造出更轻量化、更节能的汽车零部件。
例如,采用半固态压铸技术制造的发动机缸体和传动壳体重量可以减轻20以上,同时提高了产品的耐久性和可靠性。
另一方面,由于镁合金具有良好的导热性能,采用半固态压铸技术可以制造出具有良好散热效果的汽车零部件。
例如,采用半固态压铸技术制造的发动机散热器可以有效降低发动机的温度,提升整车的燃油经济性和动力性能。
综上所述,镁合金半固态压铸技术是一种有潜力的汽车零部件制造技术,具有轻量化、节能和环保等优势。
随着该技术的不断发展和完善,相信在未来的汽车制造领域中将得到更广泛的应用。
1.2 文章结构文章结构部分的内容可以描述文章的组织方式和结构设计,以便读者能够更好地理解和阅读文章。
具体内容如下:文章结构:本文主要分为三个部分,分别是引言、正文和结论。
1. 引言部分:引言部分首先对镁合金半固态压铸技术进行概述,介绍其在汽车制造领域中的重要性和应用背景。
镁合金 挤压 织构

镁合金挤压织构镁合金挤压织构是指通过挤压工艺将镁合金加热至半固态状态,然后通过专用的模具进行挤压成型,从而使得镁合金材料在微观结构上具有某种特定的排列方式。
镁合金挤压织构的形成对提高镁合金材料的力学性能和耐蚀性能具有重要意义。
镁合金是一种理想的轻质结构材料,在航空、汽车等领域具有广泛的应用前景。
然而,由于镁合金本身的晶格结构和力学性质的特殊性,这使得其在加工过程中容易发生晶体变形和织构演化,从而影响材料的力学性能。
为了克服这个问题,研究人员针对镁合金的挤压工艺进行了改进和优化,通过调节挤压温度、挤压速度和模具几何参数等工艺参数,使得挤压织构得以控制和调整。
镁合金挤压织构可以通过以下几个方面进行表征和分析。
首先,可以通过控制挤压温度和变形速率,实现镁合金晶体的畸变和旋转,从而改善材料的力学性能和耐蚀性能。
其次,挤压过程中材料的流动模式和流动速度也会对织构的形成产生影响。
通过合理调节挤压速度和挤压比例,可以使得材料流动的轨迹和方式变得均匀,从而使得织构的形成得以控制。
另外,挤压织构的形成还与材料中的变形激发和晶粒取向有关。
挤压过程中,晶粒的变形演化和织构的形成是相互联系的,二者的关系需要通过显微观察和实验分析进行探究。
实际应用中,镁合金挤压织构可以通过改变挤压参数和热处理工艺来实现。
例如,通过调整挤压温度和挤压速度,可以实现晶体内部的组织变形和晶粒取向的调整。
同时,在挤压完成后,对材料进行热处理,可以进一步稳定挤压织构,并提高材料的力学性能和耐蚀性能。
总之,镁合金挤压织构是一种通过控制挤压工艺参数和热处理工艺,使得镁合金材料具有特定的排列方式,从而提高材料的力学性能和耐蚀性能的方法。
这种材料加工方法在航空、汽车等领域具有潜在的应用前景,同时也为镁合金的进一步研究和开发提供了新的思路和方法。
镁合金半固态压铸件通用技术要求

镁合金半固态压铸件通用技术要求
嘿,朋友们!今天咱来聊聊镁合金半固态压铸件通用技术要求。
想象一下,这就好比是给镁合金打造了一个超级厉害的“标准套装”!
先来说说镁合金这玩意儿吧。
它呀,那可是相当轻便又坚固,就像一个小巧灵活的大力士!比如说汽车零件,用了镁合金半固态压铸件,车不就更轻更省油了嘛!这难道不是超棒的吗?
那这通用技术要求都有啥呢?尺寸精度就是很重要的一项呢!总不能做出来的东西大小都不合适吧,那怎么用啊?就好比你买双鞋,尺码不对还怎么走路呀!还有表面质量,得光滑平整吧,不能坑坑洼洼的,那多难看呀!这不跟人的脸一样嘛,谁不想有张干净光滑的脸呀!
对强度的要求也很高哦!这就像是人的骨头,得足够硬才能撑得住呀!你想想,如果强度不够,那用着用着坏了怎么办?多闹心啊!而且呀,工艺过程也要严格控制呢,温度啦、压力啦,都得把握得恰到好处,这就跟做菜一样,火候掌握不好,菜就不好吃啦!
咱再想想,要是没有这些通用技术要求,那得乱套成啥样呀?到处都是不合格的产品,那可不行!所以说呀,这些要求真的是超级重要的!我就觉得,我们必须得严格按照这些要求来做,这样才能做出高质量的镁合金半固态压铸件呀!这样我们的各种产品才能更好用、更耐用呀!你们说是不是这个理呀!。
半固态成型镁合金组织与耐腐蚀性能影响
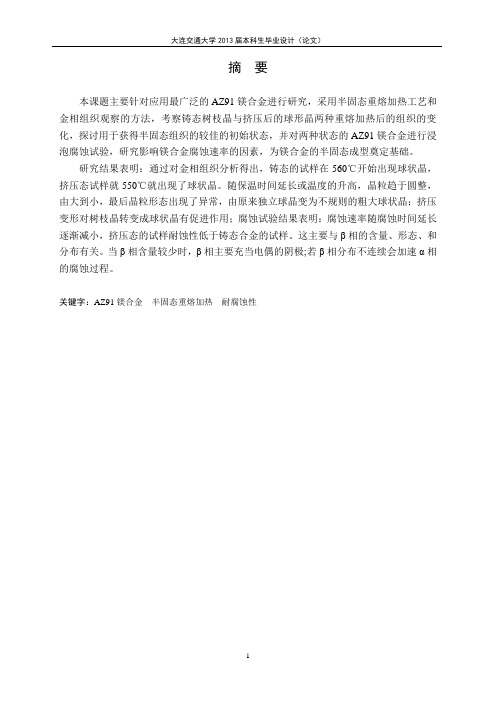
摘要本课题主要针对应用最广泛的AZ91镁合金进行研究,采用半固态重熔加热工艺和金相组织观察的方法,考察铸态树枝晶与挤压后的球形晶两种重熔加热后的组织的变化,探讨用于获得半固态组织的较佳的初始状态,并对两种状态的AZ91镁合金进行浸泡腐蚀试验,研究影响镁合金腐蚀速率的因素,为镁合金的半固态成型奠定基础。
研究结果表明:通过对金相组织分析得出,铸态的试样在560℃开始出现球状晶,挤压态试样就550℃就出现了球状晶。
随保温时间延长或温度的升高,晶粒趋于圆整,由大到小,最后晶粒形态出现了异常,由原来独立球晶变为不规则的粗大球状晶;挤压变形对树枝晶转变成球状晶有促进作用;腐蚀试验结果表明:腐蚀速率随腐蚀时间延长逐渐减小,挤压态的试样耐蚀性低于铸态合金的试样。
这主要与β相的含量、形态、和分布有关。
当β相含量较少时,β相主要充当电偶的阴极;若β相分布不连续会加速α相的腐蚀过程。
关键字:AZ91镁合金半固态重熔加热耐腐蚀性ABSTRACTThe main subject of the study for the most widely used AZ91 magnesium alloy,with Semi-solid remelting heating process and microstructure observation,inspected changes in the organizations investigated cast dendrites and squeeze both spherical crystal remelting heated and explored better initial state for semi-solid structure.AZ91 magnesium alloy of two states for immersion corrosion was tested,studying factors affecting the corrosion rate of magnesium alloys,which laid the foundation for the semi-solid forming of magnesium alloy.The results showed that, spherical crystal was found in the cast of the specimen at 560 ℃while extruded samples at 550 ℃ by analysis of the microstructure.With the holding time or temperature increases, the grain tended rounded, descending,and the last grain morphology appeared abnormal, irregular coarse spherical crystal from the original independent Spherulite ;The organization from dendrite into spherical crystal was promoted by compressional deformation.The corrosion test results showed that: the corrosion rate gradually decreased with the etching time extending, while the specimen corrosion resistance of squeezed state was lower than the cast alloy specimens.This mainly depended on the content of the β phase, morphology and distribution.When β phase content was small, the β phase mainly acte d as a galvanic cathode;The β phase discontinuous distribution would accelerate the corrosion process of the α-phase.Key words: AZ91Magnesium alloy semi-solid remelting heating corrosion resistance目录第一章绪论 (1)1.1课题来源及意义 (1)1.2镁及其合金发展与应用 (1)1.3半固态加工的概念与发展 (3)1.3.1半固态加工的概念 (3)1.3.2半固态加工的发展 (3)1.4半固态金属浆料或坯料的制备 (5)1.4.1机械搅拌法 (5)1.4.2电磁搅拌法 (5)1.4.3应变诱发熔化激活法 (6)1.4.4半固态等温热处理法 (6)1.4.5注射成形 (6)1.5镁合金表面防腐处理 (6)1.6课题的主要内容 (10)第二章试验材料、设备及试验过程 (11)2.1试验材料 (11)2.2试验设备 (11)2.3试验过程 (14)2.3.1等温热处理试验 (14)2.3.2 金相试样制备 (14)2.3.3 金相显微组织观察 (16)2.3.4 镁合金的耐腐蚀性能实验 (16)第三章试验结果讨论与分析 (18)3.1铸态半固态等温处理显微组织 (18)3.2挤压态半固态等温处理显微组织 (21)3.3耐腐蚀性能分析 (25)第四章结论 (27)谢辞 (28)参考文献 (29)第一章绪论1.1课题来源及意义镁合金作为最轻的工程金属材料,被誉为“21世纪的绿色工程材料”。
镁合金半固态压铸成形及其控制技术

镁合金半固态压铸成形及其控制技术摘要:在众多的合金材料中,镁合金因其重量轻、延展性高、硬度性能良好等优势,被广泛应用在压铸材料中,本文主要分析镁合金半固态压铸成形的方式以及控制技术,希望能够为压铸行业发展提供意见参考。
关键词:镁合金;半固态压铸;成形;控制技术在压铸成形材料中,铝合金与镁合金的应用较为广泛,同铝合金相比较,镁合金的强度以及延展性要更高,在压铸成形的材料中,结构相对牢固可靠。
新的发展形势下,对于镁合金的需求越来越大,镁合金的应用范围不断扩大,甚至在航空航天以及通讯设备上得到了良好的应用。
为了更好地研究镁合金成形材料,本文便针对镁合金半固态压铸成形技术进行简单分析。
1镁合金半固态压铸成形所采用的方法通常情况下,有三种途径可以实现镁合金半固态压铸成形,即触变压铸、流变压铸以及处变注射三种方法,接下来将依次进行详细分析:1.1镁合金半固态的触变压铸方法该方法是通过对半固态镁合金锭进行二次加热,变为固液后,借助密闭的送料机将其传送给压铸机,再输送到压射料筒中。
整个的压铸工作是靠冲头动作来完成的。
在二次加热前,半固态镁合金锭固相率基本在 48%-58% 之间,粘稠度较高,然二次加热后,固液镁合金锭在处于压射状态下,会受到切变作用,降低粘稠度,这样一来便提高了流动性,有助于压射成形。
1.2镁合金的流变压铸方法有关研究表明,同液态镁合金相比较,半固态镁合金的成形技术更有助于镁合金零件的压铸成型,压铸件的质量也更高。
因此,镁合金的流变压铸方法便是将液态镁合金通过降温或者搅拌的方式,来将其转变为半固态浆料后,输送到压铸机进行压铸工艺。
由此可知,在镁合金的流变压铸工艺中,关键在于液态合金到半固态合金的转化,在实际的工作中,发现这一过程最难控制的,便是成形温度,所以该方法对于温度和设备有着较高的要求。
1.3镁合金触变注射法在压铸工艺不断发展进步的大环境下,美国一家企业,根据塑料注射成型原理,对镁合金压铸工艺深入研究,开发了新型镁合金触变成形机,该专利设备主要适用于小型压铸件或者已经成型的设备加工,随后在日本投入生产,同时在生产专利设备的基础上,有对其进行创新,研发出具有热流道成形技术的模具,适用于性能要求不高的镁合金构件生产,譬如手机、电脑外壳生产。
- 1、下载文档前请自行甄别文档内容的完整性,平台不提供额外的编辑、内容补充、找答案等附加服务。
- 2、"仅部分预览"的文档,不可在线预览部分如存在完整性等问题,可反馈申请退款(可完整预览的文档不适用该条件!)。
- 3、如文档侵犯您的权益,请联系客服反馈,我们会尽快为您处理(人工客服工作时间:9:00-18:30)。
半固態觸變鑄造加熱方式
就半固態成形製程而言,感應加熱因具有乾淨、快速、適合 自動化和低工作環境溫度等優點,成為目前歐美日觸變鑄造業的 不二選擇。但是,感應加熱因表層效應(Skin Effect)關係,精確 控制熔漿內外溫度均勻性極不容易。然為了得到高品質與高良率 製程,需要有精確控溫的周波加熱技術來產生穩定溫度熔漿;這一 關鍵參數在金屬半固態成形時尤其重要。
鎂合金成型方法
鎂合金的廣泛應用,使得它的成型技術受到越來越多的觀注. 镁合金成形分为变形和铸造两种方法.
壓鑄是应用最广的镁合金成形方法。 壓鑄法是以活塞將融熔金屬壓入模穴中,凝固成型。
<a. 冷室壓鑄法 Cold chamber die casting>: 採料管給料,氣體灌入多,導入式自動給湯機,熔鑄壓力較 高,模具大型,可鑄面積大,技術成熟度高,適用於肉厚及大鑄 件。射出時間較長,產出率較低。
半固態成形比較DIE CASTING的主要優點
半固態成形比較DIE CASTING的主要優點
1.操作溫度較壓鑄低約100℃,因此模具壽命較長,模具之潤 滑需求亦減少,不必機外先融熔鎂合金,減少能源耗損及工作場 所之髒亂。 2.半固態成形中,由於鎂熔料有部分是處於固相狀態,而液 相部份亦是處於較低的溫度。因此在凝固冷卻的過程中,成品的 形狀收縮較小,所以成品公差變化小,尺寸再現性高。
Density
98%
88%
半固態射出成型技術簡介
半固態成型技術觸變成型則將金屬顆粒經射出機的射出單元 加熱至部分熔融狀態,並剪切並冷卻至半固態後,再以螺杆推送 注射成型,是由塑膠射出成型衍生應用在金屬的成型製程。
半固態射出成型法-構造及進料圖
將鎂合金顆粒由加料筒(Feed Stock)送到射出成型機的料管內, 加熱至半固態後,同時以螺桿(Screw)施加外力。攪拌成球狀組織之 半固態鎂合金材料,然後再以螺桿送料射到模穴成型.
半固態成形比較DIE CASTING的主要優點
3.強度較佳 a.可得到球粒組織結構。 b.流動模式為層流(laminar flow),氣孔率較壓鑄成形之氣 孔率少. 層流(laminar flow) 紊流(turbulent flow)
TYPICAL MECHANICAL PROPERTIES Thixomolding vs. Die Cast Mg. AZ91D
半固態成型方法介紹
流變鑄造是將液態之金屬一面攪拌(目的為得到球狀晶)一面 冷卻至固液兩相共存區,而後將此半固態黏漿直接傳送至冷室壓 鑄機鑄造成工件,此製程稱為流變鑄造,亦稱為攪動鑄造 (StirCasting)。 觸變鑄造是將已具球狀晶之棒材或鑄錠重新加熱至固液兩相 共存之半固態區,而後再以壓鑄機鑄造或鍛造機鍛造。本法不必 使用金屬之熔解爐,僅是將錠材由全固態加熱至固相分率較高 (50~80%) 之半固態,因其仍維持固體之形狀 , 故可使用自動機器 (Robot)手臂夾持進行後續之壓鑄或鍛造步驟。而此法有點類似於 傳統之鍛造製程,因此又稱為觸變鍛造(Thixoforging)。
半固態射出成型機台
半固態射出成型技術是由塑膠射出成型衍生出來的,但兩種射 出機台是不能換用的.因為不僅在套筒上,螺桿上所用的材料不同, 射出裝置,螺桿的旋線裝置等也都是為觸變成型機而專門設計的
半固態觸變鑄造成型介紹
觸變鑄造(Thixocasting) 是 先製造半固態非樹枝狀組織熔 漿再鑄造成棒材,在本文統一 稱為「半固態原材料」,然後 依據所需要重量鋸切成固定尺 寸原材料備用。利用精確溫控 加熱設備將半固態原材料從室 溫加熱至特定固相體積分率之 半固態熔漿後,將其送入壓鑄 機料筒或鍛造機模穴內壓鍛成 型零件。
觸變鑄造的製造流程圖
半固態鑄造成型製程
半固態成型零件之優點只有在精準製程調適下才能有效彰顯 出來,例如原材料如何被適當加熱至特定半固態溫度(特定固相 比例)及其保溫時間以獲得較佳均勻溫度和球化組織。 此製程基本上可分為兩個階段。首先是將一般鎂合金鑄錠變 為鎂合金「半固態原材料」.鎂合金「半固態原材料」由於熔解需 有保護氣氛防止氧化與燃燒問題,鎂合金經冷加工,將其鑄造之 樹枝狀晶塑性加工變形成微細晶粒後亦可作為半固態原材料使用 。
半固態成型方法介紹
觸變成型是將金屬顆拉或碎片(Chip)加熱至固液兩相共存區 (較低之固相分率.非固體之形態),以螺桿剪切(目的為得到球狀品 )並推送此半固態黏漿射出成型,此法類似塑膠射出製程。此法亦 不需金屬熔解爐,原料係於枓管內加熱。 流變成型將一般之金屬錠溶解至液態精練後,在經冷卻至兩 相區,而後以螺桿剪切推送此半固態黏漿射出成型。
周波感應加熱設備
周波感應加熱設備目前兩種自動運作方式. 一種是利用數個獨立的「固定式」加熱線圈每隔一時間差同 時加熱數個金屬錠,此間隔時間差約略為零件成形週期。每個獨 立加熱線圈可以輸出在不同時間區段不同大小的加熱功率,金屬 錠在同一個線圈由室溫加熱至半固態。
周波感應加熱設備
另外一種周波感應加熱的作法是利用旋轉盤使金屬錠在不同 線圈內依序加熱至半固態。可說是最早加熱半固態鋁錠的專利。 利用轉盤機構與數個周波感應線圈,將數個金屬錠同時加熱,加 熱後上升感應加熱線圈,轉盤往前旋轉後,所有金屬錠向前移動 至下一個感應線圈位置,感應線圈再下降加熱。這樣,讓每一個 金屬錠,依序經過不同加熱線圈加熱,直到最後一個加熱線圈,金 屬錠達到半熔融態.
Property Ultimate Tensile Strength Yield Strength Elongation % Thixomolded 295 Mpa [43.0 KSI] 184 MPa [26.0 KSI] 10% Die Cast 230 MPa [33.0 KSI] 150 MPa [22.0 KSI] 3%
鎂合金比較塑膠件的優勢
尺寸穩定及抗潛變性佳-不會有成形變形撓曲及材質老化問題 優良導熱性-改善電子產品散熱問題 極佳吸震性-使用在汽車座框架及坦克車吸震 優良的機械強度抗撓曲性 抗衝擊性〃抗疲勞性-不須為剛性問題增加補強設計,框體自 70cm高落下亦不破損 耐磨耗性良好 非磁性金屬-電磁遮蔽性佳(EMI) 輕薄設計的可行性-比重1.8但形成薄壁<1.2mm,局部更可薄至 0.6mm 金屬材質,質感佳,並可完全回收,符合環保法規ISO-14000 收縮率小-厚度可達20MM.無收縮下陷問題.RIB厚度或BOSS直徑 可達平均厚度之3-4倍.不致於產生收縮下陷問題
電磁攪拌連續鑄造半固態原材料示意圖
應變引發先熔簡介
應變引發先熔是先將一般鑄錠,施以相當的加工量,使其內 部 殘留足夠的應變量;再加熱至半固態溫度,使其因應變引發而 形成球狀晶半固 態熔湯。应变诱发熔化激活法(SIMA)是将常 规铸锭经过预变形,如进行挤压,滚压等热加工制成半成品棒料 ,这时的显微组织具有强烈地拉长形变结构,然后加热到固液两 相区等温一定时间,被拉长的晶粒变成了细小的颗粒,随后快速 冷却获得非枝晶组织铸锭。
較具成本效益的半固態熔漿(SemisolidSlurry)製造方法有兩 種: 凝固攪動法(Agitation During Solidification) 應變引發熔漿活化法(Strain-induced Melt Activation,簡稱 SIMA)
凝固攪動法之攪動動能可後是零件成型,利用周波感應加熱方式將原材料從室溫加 熱至固、液相共存狀態,再利用壓機加以鍛壓(或利用壓鑄機壓 鑄)對半固態熔漿施加一剪切力(Shear Force), 使熔漿因剪切 變(Shear Thinning),降低表觀黏度而有優越流動性之原理來成 型零件。
半固態原材料製造
壓鑄法
<b. 熱室壓鑄法 Hot chamber die casting>: 以鵝頸管式自動給湯,氣體灌入少,熔鑄壓力較低,使用模具 較小,可鑄面積小,技術成熟度高,適用於肉薄及小鑄件。國內 業者採用此法較多,理由是成型周期短,廢料少。射出時間較短 ,產出率較高,機器結構較複雜,成本較高
半固態成型簡介
鎂合金半固態成型 專題報告
MID SOPHIN_WANG
2003/12/17
概述
在電子產品追求人性化的聲浪下,傳統的塑膠外殼已不能滿 足產品設計的需求,因應潮流而起的解決之道正是鎂合金成型品. 鎂合金成型品在電子業的應用具有工程塑膠無法取代的諸多優勢. 在品質及環保的的要求下,以鎂合金製作電子產品的外殼及 內部零件已成為主流趨勢.鎂合金的成型也受到越來越多的關注.
金屬半固態成型有別於全液態鑄造及全固態鍛造製程,其可 排除鑄造件孔洞過多及鍛造品高殘留應力之缺點,係結合兩製程 的優點所發展出來之全新製程。此技術於1970年代初期萌芽,發 展迄今已近30年。 所謂半固態(Semi-Solid)顧名思義為一半固態及一半液態之狀 態,廣而言之為同時含有部份固態及部份液態之形態。以金屬材料 而言,最重要的是此時的固相之品體組織是“球狀”的而非一般 的“樹枝狀”結構.此是應用金屬半固態成型技術的關鍵點。 目前半固態金屬成形技術沿革按制差異大約可區分流變鑄造 、觸變鑄造、觸變成型及流變成型。
半固態合金感應加熱技術及限制
(1)合金種類之影響建立感應加熱參數前,需參考個別合金 之凝固特性,就觸變鑄造製程之工程觀點而言,半固態熔漿需在 相同成型週期內以微小液相比例誤差被重複製造出來,才能達到 量產要求。
半固態合金感應加熱技術及限制
(2)半固態鎂合金感應加熱 建立良好感應加熱參數,係根值於熟悉硬體設備功能、感應 加熱原理與個別合金之凝固特性。如果感應加熱設備係利用熔漿 溫度回饋訊號,來控制加熱線圈功率輸出,則量測溫度之熱電偶 位置最好約略在渦電流透入深度ä ,以避免熱電偶位在偏低溫熔 漿中央位置,造成熔漿外圍全部液化,形成無謂熔損,而熔漿之 中央位置尚屬低溫半固態狀態,使熔漿內、外溫差過大。要達成 以上目標,預備鑄造成型的半固態合金黏漿的溫度準確性以及溫 度均勻性就要藉助具有可程式控制感應加熱功能之設備,才能達 成精確控制鎂錠溫度之要求。