1780精轧机工作辊设计
1780工艺流程简述

1 工艺流程简述检查合格的热态连铸板坯,经由连铸车间出坯跨的热送辊道送往炉前。
在入炉辊道上由托钢机托至步进加热炉受料台架上,再由步进梁托入炉内加热。
板坯在加热炉内被加热到~1250℃,用出钢机将加热后的板坯从加热炉中托出放到出炉辊道上,由粗轧除鳞机清除板坯表面氧化铁皮,进入粗轧机组将板坯轧到厚度为32~60mm的中间带坯。
在粗轧机组后设测宽仪、予留测厚仪。
为保证精轧质量,进入精轧机的中间坯温度应在920~1150℃之间,不合格的中间坯在粗轧入口辊道上由废钢推出机推至收集台架上。
合格的中间坯经过中间辊道、保温罩,经飞剪切头切尾,再经过精轧除鳞机除去二次氧化铁皮,然后送入精轧机组轧制到成品带钢厚度。
精轧机组机架间设有液压活套装置,使带钢进行恒定微张力轧制,保证带钢的轧制精度。
在精轧机后设有测厚仪、测宽仪、板型仪,测量并显示带钢的厚度、宽度,与精轧机组的F1~F7液压HGC控制系统、正弯辊系统配合,以提高带钢纵向尺寸精度和减少带钢横向厚度公差。
带钢终轧温度控制在850℃~950℃之间。
轧制后的带钢通过输出辊道经夹送辊送入卷取机卷取。
在精轧机组和卷取机之间的辊道上设有层流冷却装置,分别对带钢上、下表面进行喷水冷却,根据带钢的钢种、厚度、速度和终轧温度的要求来调节喷水集管的组数和水量,将带钢卷取温度控制到400℃~750℃之间。
带钢经卷取机卷取成卷后,卸卷、打捆后由运卷小车运至运输线。
再由运输系统分别送往检查线和成品库。
2 装机水平1. 采用四点高压水除鳞以提高带钢表面质量(粗轧除鳞机、R1/R2粗轧机除鳞、精轧除鳞机)。
2. 粗轧机组选用一台二辊可逆万能轧机和一台四辊可逆万能轧机;R1轧机设电动APC、液压HGC、轧辊冷却、高压水除鳞、水压除尘,工作辊采用油膜轴承;R2轧机设电动APC、液压HGC、轧辊冷却、高压水除鳞、水压除尘,工作辊均采用四列园锥密封滚子轴承,支承辊采用油膜轴承。
E1/E2立辊轧机均设有长行程AWC· SSC系统对粗轧板坯进行宽度控制及头尾形状控制以提高板坯边部质量和收得率。
辊道升降机构的结构设计及计算
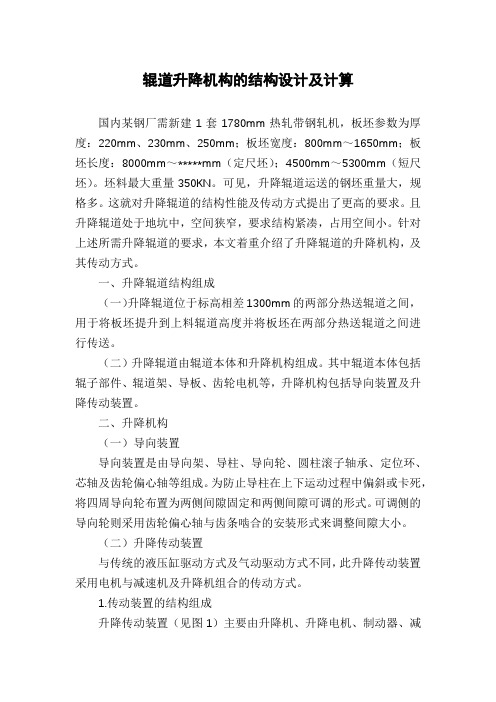
辊道升降机构的结构设计及计算国内某钢厂需新建1套1780mm热轧带钢轧机,板坯参数为厚度:220mm、230mm、250mm;板坯宽度:800mm~1650mm;板坯长度:8000mm~*****mm(定尺坯);4500mm~5300mm(短尺坯)。
坯料最大重量350KN。
可见,升降辊道运送的钢坯重量大,规格多。
这就对升降辊道的结构性能及传动方式提出了更高的要求。
且升降辊道处于地坑中,空间狭窄,要求结构紧凑,占用空间小。
针对上述所需升降辊道的要求,本文着重介绍了升降辊道的升降机构,及其传动方式。
一、升降辊道结构组成(一)升降辊道位于标高相差1300mm的两部分热送辊道之间,用于将板坯提升到上料辊道高度并将板坯在两部分热送辊道之间进行传送。
(二)升降辊道由辊道本体和升降机构组成。
其中辊道本体包括辊子部件、辊道架、导板、齿轮电机等,升降机构包括导向装置及升降传动装置。
二、升降机构(一)导向装置导向装置是由导向架、导柱、导向轮、圆柱滚子轴承、定位环、芯轴及齿轮偏心轴等组成。
为防止导柱在上下运动过程中偏斜或卡死,将四周导向轮布置为两侧间隙固定和两侧间隙可调的形式。
可调侧的导向轮则采用齿轮偏心轴与齿条啮合的安装形式来调整间隙大小。
(二)升降传动装置与传统的液压缸驱动方式及气动驱动方式不同,此升降传动装置采用电机与减速机及升降机组合的传动方式。
1.传动装置的结构组成升降传动装置(见图1)主要由升降机、升降电机、制动器、减速机等组成。
减速机是等比例传动型式。
升降电机与中间减速机连接,通过传动轴等比输出到两侧减速机,减速机再分别等比输出并直接带动两侧升降机,实现辊道升降运动。
1—升降机1;2—升降机2;3—升降电机;4—制动器;5—减速机;6—传动轴图1 升降传动装置布置图2.与其他传动方式比较与液压缸驱动形式及气缸驱动的形式相比,升降辊道中利用电机-减速机-升降机的升降传动方式,具有如下优点:(1)此传动型式能够有效地节省空间。
1780热连轧支撑辊剥落的原因分析及预防措施
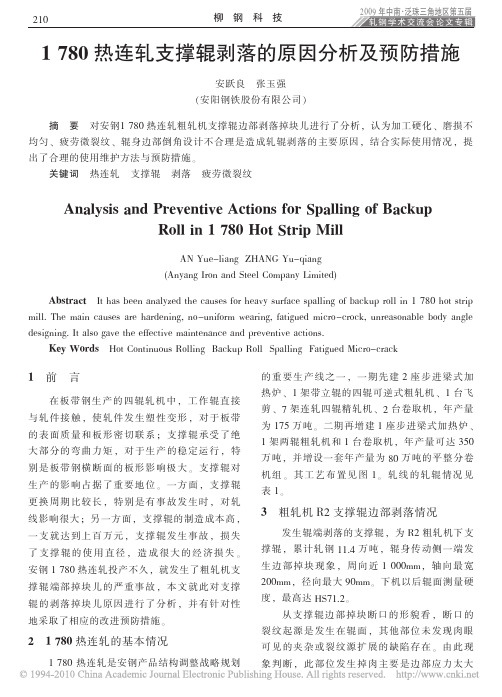
柳钢科技2009年中南·泛珠三角地区第五届1前言在板带钢生产的四辊轧机中,工作辊直接与轧件接触,使轧件发生塑性变形,对于板带的表面质量和板形密切联系;支撑辊承受了绝大部分的弯曲力矩,对于生产的稳定运行,特别是板带钢横断面的板形影响极大。
支撑辊对生产的影响占据了重要地位。
一方面,支撑辊更换周期比较长,特别是有事故发生时,对轧线影响很大;另一方面,支撑辊的制造成本高,一支就达到上百万元,支撑辊发生事故,损失了支撑辊的使用直径,造成很大的经济损失。
安钢1780热连轧投产不久,就发生了粗轧机支撑辊端部掉块儿的严重事故,本文就此对支撑辊的剥落掉块儿原因进行了分析,并有针对性地采取了相应的改进预防措施。
21780热连轧的基本情况1780热连轧是安钢产品结构调整战略规划的重要生产线之一,一期先建2座步进梁式加热炉、1架带立辊的四辊可逆式粗轧机、1台飞剪、7架连轧四辊精轧机、2台卷取机,年产量为175万吨。
二期再增建1座步进梁式加热炉、1架两辊粗轧机和1台卷取机,年产量可达350万吨,并增设一套年产量为80万吨的平整分卷机组。
其工艺布置见图1。
轧线的轧辊情况见表1。
3粗轧机R2支撑辊边部剥落情况发生辊端剥落的支撑辊,为R2粗轧机下支撑辊,累计轧钢11.4万吨,辊身传动侧一端发生边部掉块现象,周向近1000mm,轴向最宽200mm,径向最大90mm。
下机以后辊面测量硬度,最高达HS71.2。
从支撑辊边部掉块断口的形貌看,断口的裂纹起源是发生在辊面,其他部位未发现肉眼可见的夹杂或裂纹源扩展的缺陷存在。
由此现象判断,此部位发生掉肉主要是边部应力太大1780热连轧支撑辊剥落的原因分析及预防措施安跃良张玉强(安阳钢铁股份有限公司)摘要对安钢1780热连轧粗轧机支撑辊边部剥落掉块儿进行了分析,认为加工硬化、磨损不均匀、疲劳微裂纹、辊身边部倒角设计不合理是造成轧辊剥落的主要原因,结合实际使用情况,提出了合理的使用维护方法与预防措施。
轧钢机工作辊道的布置和结构
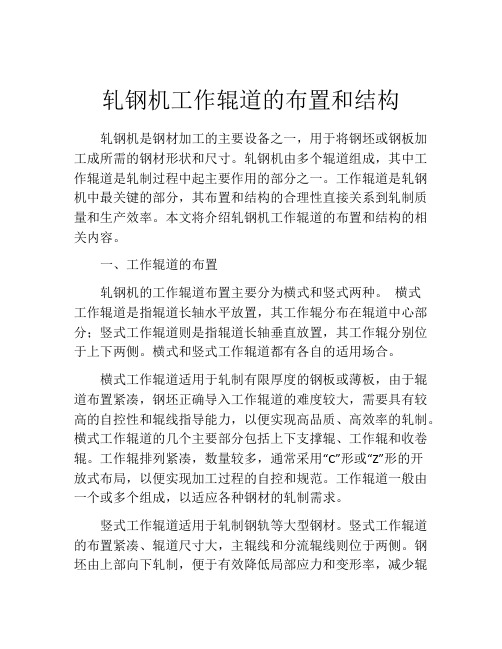
轧钢机工作辊道的布置和结构轧钢机是钢材加工的主要设备之一,用于将钢坯或钢板加工成所需的钢材形状和尺寸。
轧钢机由多个辊道组成,其中工作辊道是轧制过程中起主要作用的部分之一。
工作辊道是轧钢机中最关键的部分,其布置和结构的合理性直接关系到轧制质量和生产效率。
本文将介绍轧钢机工作辊道的布置和结构的相关内容。
一、工作辊道的布置轧钢机的工作辊道布置主要分为横式和竖式两种。
横式工作辊道是指辊道长轴水平放置,其工作辊分布在辊道中心部分;竖式工作辊道则是指辊道长轴垂直放置,其工作辊分别位于上下两侧。
横式和竖式工作辊道都有各自的适用场合。
横式工作辊道适用于轧制有限厚度的钢板或薄板,由于辊道布置紧凑,钢坯正确导入工作辊道的难度较大,需要具有较高的自控性和辊线指导能力,以便实现高品质、高效率的轧制。
横式工作辊道的几个主要部分包括上下支撑辊、工作辊和收卷辊。
工作辊排列紧凑,数量较多,通常采用“C”形或“Z”形的开放式布局,以便实现加工过程的自控和规范。
工作辊道一般由一个或多个组成,以适应各种钢材的轧制需求。
竖式工作辊道适用于轧制钢轨等大型钢材。
竖式工作辊道的布置紧凑、辊道尺寸大,主辊线和分流辊线则位于两侧。
钢坯由上部向下轧制,便于有效降低局部应力和变形率,减少辊道变形和断边现象的发生,同时也有利于轧制质量和生产效率的提高。
二、工作辊道的结构轧钢机工作辊道结构设计要考虑到钢坯的规格、材质、厚度、轧制宽度和轧制工艺等多种因素。
为了达到预期的轧制效果,还必须考虑辊道尺寸、直径、材质与表面硬度、辊道形状和滚道线速度等因素对轧制工艺的影响。
1.支撑辊的设计支撑辊是辊道中最重要的部件之一,它能够支撑工作辊的运动,防止其发生过度变形和损坏。
支撑辊应具有较高的稳定性、耐高温、耐磨损、高精度和高刚度等特点。
2.工作辊的设计工作辊是轧制过程中和钢材直接接触的部件,它需要具备耐磨损、高强度和高精度等特性。
通常采用合金工具钢或高速钢制造,表面采用镀铬、氮化或其他处理技术加强表面硬度。
(完整版)轧辊机构设计
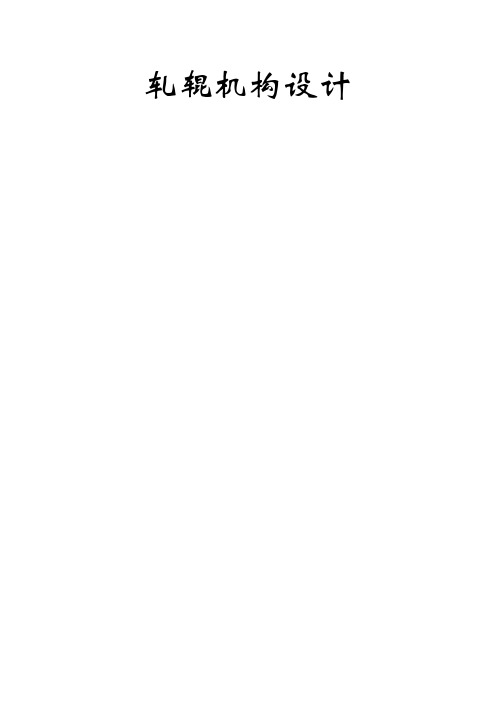
轧辊机构设计目录一、设计题目·······································二、原始设计数据和设计要求························三、运动方案选择····································四、工艺动作分析····································五、运动尺寸确定····································六、机构布置示意图··································七、参考资料········································一、设计题目轧机是由送料辊送进铸坯,由于工作辊将铸坯轧制成一定尺寸的方形、矩形或圆形截面坯料的初轧机。
机械毕业设计(论文)-轧管机轧辊侧压机构设计(全套图纸) .doc
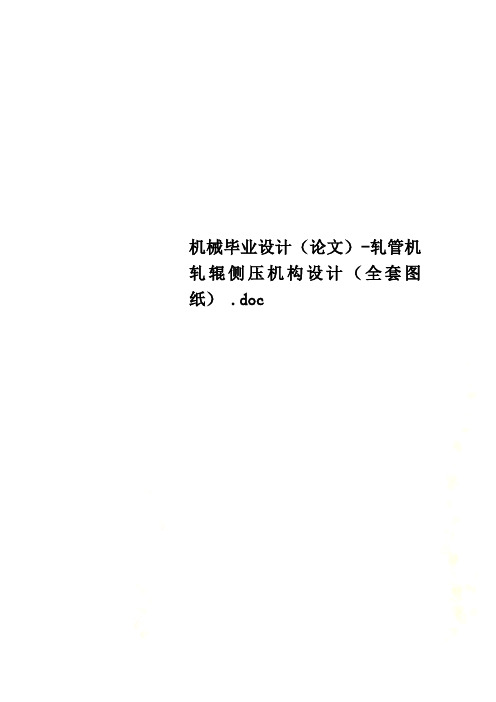
机械毕业设计(论文)-轧管机轧辊侧压机构设计(全套图纸) .doc辽宁科技大学毕业设计(论文)题目:轧管机轧辊侧压机构设计院系:机械工程与自动化学院专业班级:机设12-4班学生姓名:指导教师:2016年06月轧管机轧辊侧压机构设计摘要钢管在钢铁产品中属于经济断面、不可替代的重要品种。
轧管机作为生产无缝钢管的主要设备之一,其主要作用是对钢管进行轧制,而在轧制前,轧辊侧压装置必不可少,因为其对轧辊辊缝的调节将直接影响无缝钢管的质量。
本课题利用减速器传动、蜗轮蜗杆传动等基本原理,拟定出合理的侧压传动装置的零件图以及装配图,经过合理的计算,确定侧压装置的力能参数,然后按这些参数来选用各个零部件的规格并进行系统的结构设计来达到设计一套完整的轧辊侧压装置的目的。
该侧压装置包括减速器传动、蜗轮蜗杆传动两个传动部分,还包括液压缸平衡装置,电动机等,各个部分的设计,结构合理,强度以及寿命等都满足要求,符合实际应用的需求。
关键词:轧制压力;侧压机构;侧压电机;减速器;蜗轮蜗杆全套图纸,加153893706The Design of Mill Roll Side Pressure MechanismAbstractSteel pipe in steel products belong to economic section and irreplaceable important species.As one of the main equipment for production of steel tube mill,the main function is to rolling of steel tube ,and before rolling,roll side pressure device is necessary ,because the adjustment of roll gap will directly affect the quality of seamless steeltube.This topic using reducer drive,worm gear and worm drive,such as basic principles,work out a reasonable lateral pressure can force transmission device parameter,then according to these parameters to choose the specifications of the various parts and the structure of the system design to design a set of complete roll the purpose of the lateral pressure device.The lateral pressure device including gear reducer,worm gear and worm drive two transmission parts,including hydraulic cylinder balancing device,motor and so on,each part of the design,rational structure,strength and life all meet the requirements such as meeting the needs of practical application.Keyword:Rolling pressure;Lateral pressure institutions;Lateral pressure motor;Lateral pressure motor;Reducer;Worm gear and worm目录1绪论 (1)1.1 选题背景及目的 (1)1.2 钢管生产工艺及其国民经济中的主要地位与作用 (1)1.2.1 钢管生产方法及工艺 (1)1.2.2 钢管在国民经济中的地位与作用 (2)1.3 国内外轧管机械的发展状况 (3)1.3.1 无缝钢管生产工艺技术发展的三个阶段 (3)1.3.2 穿孔机的发展 (3)1.3.3 轧管机的发展概况 (3)1.3.4 定减径机(包括张力减径)的发展 (4)1.4 课题设计的内容和方法 (4)1.4.1 课题设计的内容 (4)1.4.2 课题设计的方法 (4)2总体方案选择 (5)2.1设计的原始参数 (5)2.2 方案的选择 (5)2.2.1 系统动力源的选择 (5)2.2.2 传动装置的选择 (5)2.2.3 执行装置的选择 (6)2.3 总体方案简图 (6)3 二辊斜轧穿孔的力参数 (8)3.1 轧制压力 (8)3.1.1 变形区长度的确定 (8)3.1.2 接触面宽度的确定 (9)3.1.3 轧制压力的计算 (11)4侧压电机的选择 (12)4.1 侧压螺丝主要尺寸的确定 (12)4.2 侧压螺丝的传动力矩 (13)4.3 侧压电机的选择 (15)4.4 电动机的校核 (16)5 侧压平衡系统的确定 (18)5.1 平衡方法的选择 (18)5.2 侧压装置平衡力的计算 (18)5.3 平衡液压缸的计算 (18)5.3.1 液压缸柱塞直径的计算 (18)5.3.2 液压缸柱塞直径的校核 (19)5.3.3 液压缸壁厚的校核 (19)6 主要零部件强度计算 (21)6.1 传动比分配及标准减速器的选取 (21)6.1.1 传动比分配 (21)6.1.2 标准减速器的选取 (21)6.1.3 标准减速器的校核 (21)6.2 蜗轮蜗杆的设计与校核 (22)6.3 减速器各轴及蜗杆动力参数计算 (27)6.4 蜗杆轴的设计 (28)6.5 蜗杆传动校核 (29)6.6 轴承的寿命计算 (33)6.7 侧压螺丝的强度计算 (34)6.8 侧压螺母的设计校核 (35)7 系统的润滑 (38)7.1 润滑剂的分类 (38)7.2 蜗轮蜗杆的润滑 (38)7.3 滚动轴承的润滑................................................................................ 错误!未定义书签。
1780轧机电动压下装置的设计计算

1780轧机电动压下装置的设计计算【摘要】详细介绍了1780轧机的轧制线调整电动压下装置中压下螺丝、压下螺母及传动电机的功率等的设计计算过程及强度校核【关键词】轧机;电动压下;设计计算;强度校核最近我公司承接了某钼业股份有限公司的一条1780mm温/冷轧钼轧制板材生产线,主要包括有前后运输辊道、六辊冷轧机、矫直机以及剪子等设备。
机组主要参数有:1. 来料的厚度≤5㎜;2. 成品的厚度:0.3~4㎜;3. 最大轧制力:30MN。
现就介绍该六辊冷轧机轧制线调整电动压下装置的设计计算及强度校核。
在以往的单台钼板轧机中,我们通常使用的轧制线调整装置的结构形式是:1. 在机架的侧面安装有四个液压缸,轧制线需要调整时用液压缸顶起支承辊的弧面垫,按照计算好的厚度把事先准备好的合适厚度的垫板塞入,以增加垫板的方式来补偿辊径变化保证轧制线的固定不变;2. 采用液压缸推动阶梯垫板的形式进行轧制线调整。
此两种方法最大的不足就是无法进行轧制线的连续调整,而且第一种方法采用的是人工加放垫板的方式,由于空间限制操作不方便,本机组是整条生产线,前后设有运输辊道,设备布置较紧凑人工加放垫板的方式就更不可能实现。
为了达到轧制线高度上可以实现连续调整,前期考虑选取用螺旋升降机驱动两个串联的斜楔进行轧制线标高调整的方案。
因为此轧机为板材轧机而不是带材轧机,在板材进入轧机和离开轧机时会产生强大的瞬时冲击力,纵向冲击力导致斜楔的水平分力会传递给螺旋升降机,为了避免螺旋升降机瞬时承受较大冲击力而损坏,后经多方论证该方案被否定。
图1最终轧制线调整装置采用电动压下的方案,如图1。
下面就该方案详细介绍一下主要技术参数的设计计算和确定。
1、压下螺丝的设计计算:通过与同类产品的类比和以往的经验初步确定压下螺丝采用B480×18,然后再对其强度进行校核。
式中:——压下螺丝中实际计算应力,MPa;P1——压下螺丝所承受的轧制力,N;d1——压下螺丝螺纹内径,m;[]——压下螺丝材料许用应力,MPa;代入P1=15×106N、d=0.44876m 得=94.84MPa;而[]=压下螺丝材质采用42CrMo,=690~840MPa,代入得n=7.3~8.8,符合n≥6的要求。
1780mm热连轧轧机机组的设计

1
No. 4 November 2019
《中国重型装备》 CHINA HEAVY EQUIPMENT
1—1#加热炉2—2#加热炉3—3#加热炉4—粗轧除鳞箱5—E1附着立辗轧机6—R1二辗可逆粗轧机组7—E2附着立辗轧机 8-R2四楹可逆粗轧机组9—保温罩10—热卷箱11—切头飞剪12—精轧除鳞箱13—F1E附着立楹轧机 14—F1 - F7四楹精轧机组15—层流冷却16—1、2、3号卷取机 图1 1780 mm热轧带钢生产线工艺布置图
成品带钢规格见表1。原料坯为连铸坯,连 铸坯规格见表2。
收稿日期:2019 -05 -15 作者简介:赵勇(1984 -),男,学士,工程师。
1.2轧线工艺布置 该轧线主要设备有:1#、2#、3#加热炉、粗轧除
鳞箱、E1附着式立辐轧机、R1二辐可逆粗轧机、 E2附着式立辐轧机、R2四辐可逆粗轧机、活动保
45 mm以下的中间坯经R2后延伸辐道,进 入热卷箱卷取成卷,进行均热、保温。卷取完成 后,带卷被送往开卷位置进行开卷,开卷后中间坯 尾部首先进入精轧机以降低头尾温差。45 mm以 上的中间坯采取直通方式,不经过热卷箱卷取。 R1粗轧机与R2粗轧机及R2粗轧机与精轧机之 间的延伸辐道上设置有保温罩,减少中间坯温降。
32.0
2轧线工艺流程简述
2.1工艺流程简述 合格的连铸板坯经上料辐道运输至入炉辐道
处定位,然后由装钢机装入加热炉,按照设定的加 热程序,钢坯在炉内加热升温和均热。
板坯经加热炉加热后,达到均匀一致的出炉 温度(根据轧制钢种的不同,出炉温度控制在 1100 - 1250T ),由出钢机出料准备进入粗轧机组 进行轧制。
- 1、下载文档前请自行甄别文档内容的完整性,平台不提供额外的编辑、内容补充、找答案等附加服务。
- 2、"仅部分预览"的文档,不可在线预览部分如存在完整性等问题,可反馈申请退款(可完整预览的文档不适用该条件!)。
- 3、如文档侵犯您的权益,请联系客服反馈,我们会尽快为您处理(人工客服工作时间:9:00-18:30)。
太原科技大学毕业设计说明书 第 1 章 概论
1.1 轧钢生产在国民经济中的主要地位与作用 轧钢生产是将钢锭及连续铸坯轧制成材的生产环节。用轧制的方法生产钢材,具有 生产率高、品种多、生产过程连续性强、易于实现自动化等优点。钢材的生产方法有轧 制、锻造、挤压、拉拔等。用轧制方法得到的钢材,具有生产过程连续性、生产效率高、 品 种多、质量好、易与机 械化、自动化等优点,因 此得到广泛的应用。目 前,约有 90 ﹪的钢都是经过轧制成材的。有色金属成材,主要也用轧制的方法。 轧钢生产在国民经济中所起的作用是十分显著的。钢铁工业生产中,除少量的钢用 铸造或铸造方法制成零件外,炼钢厂生产的钢锭与连铸坯有 85~90%以上要经过轧钢车 间轧成各种钢材,供应国民经济各部门。可见在现代钢铁企业中,作为使钢成材的轧钢 生产,在整个国民经济中占据着异常重要的地位,对促进我国经济快速发展起十分重要 的作用。 1.2 国内外轧钢机械的发展状况 十九世纪中叶轧钢机械只是轧制一些熟铁条的小型轧机,设备简陋,产量不高;有 的轧机是用原始的水轮来驱动。大上个世纪五十年代以后,钢的产量大增;各先进工业 国的铁路建设与远洋航运的发展,蒸汽驱动的中型、大型轧机先后出现了。上个世纪的 电气化使功率更大的粗轧机迅速发展起来。上个纪 50~70 年代,由于汽车、石油、天 然气的运输,电器电子工业与食品罐头工业的发展,钢材生产是以薄板占优势为特征的。 总的来说,轧钢机械向着大型、连续、高速和计算机控制方向发展。
- 1 - 太原科技大学毕业设计说明书 1.2.1 带钢热连轧机发展 带钢热轧机分为连续式带钢热轧机、四辊及多辊可逆式轧机、炉卷轧机和行星式轧 机等。 带钢热连轧机分为全连轧、1/2 连轧和 3/4 连轧机。 带钢连续式热轧机主要 是生产 1.0~16(20)毫米的热钢板卷的,其生产的品种以 普通炭钢为主。 在世界上美国首先在 1926 年采用了热连轧板机,这台轧机安装在哥伦比亚钢铁公 司,轧机规格为 1030 毫米,是 1/2 连轧,只是有一个粗轧机架,是近代热连轧机的雏形。 四十年代以前,带钢热连轧机,几乎全部集中在美国。 1961~1971 年,美国新建了 11 台辊身长度为 1473 毫米以上的热连轧机,称为“第 二代轧机”。第二代轧机具有轧制速度高、产量高、自动话程度高的特点。 我国从 1966~1970 年开始发展热连轧板机,1700 毫米 3/4 热连轧板机以投产,其 他规格的热连轧板机还有 1450 毫米半连轧、1450 毫米全连轧、750 毫米全连轧等。 这些年来,薄钢板的生产比重日趋增加,这是现代轧钢生产发展的一个趋势。热轧 钢板是汽车、造船、桥梁、电机、化工等工业不可缺少的原料,也是冷轧机的坯料,随 着焊管、冷弯型钢的发展,钢板的需要量日益增长。 现代带钢热连轧机发展趋势是提高产量、扩大品种、提高精度、提高自动化程度。 采取的主要措施有:提高轧制速度、加大带卷和坯料重量、建造宽辊身的全连轧、粗轧 机架近距离布置、采用快速换辊装置、提高产品精度和轧机刚度、采用板厚自动控制系 统、精轧机轧辊辊型控制、采用计算机控制。 90 年代以来,钢铁生产短流程迅速开发和推广,薄板坯连铸连轧工艺的出现,正在 改变着传统的热轧机市场。自 1987 年 7 月第一套薄板坯连铸连轧生产线在美国纽柯公 司投产以来,到 1997 年已建成的有 33 套。连铸连轧技术是将钢的凝固成型与变形成型 两个工序衔接起来,将连铸坯在热状态下继续送入精轧机组,直接轧制成带卷产品。德 国西马克公司的 CSP 技术、德马克公司的 ISP 技术、奥钢联开发的 Conroll 技术等都有 用户采用。 1.2.2 新型热带轧机精轧机的种类 目前,新型热带轧机主要有以下几种形式:带液压弯辊技术(WRB)的轧机,CVC
- 2 - 太原科技大学毕业设计说明书 轧机、PC 轧机、HC 轧机以及 WRS 轧机等,现分别介绍如下: (1)液压变辊技术 第一种:弯工作辊的方法(如图 1-1)。这又可以分为两种方式:①反弯力加在两工 作辊瓦座之间。即除工作辊平衡油缸以外,尚配有专门提供弯辊力的液压缸,使上下工 作辊轴承座受到与轧制压力方向相同的弯辊力 N1,结果是减小了轧制时工作辊的挠度。 这称为正弯辊。②反弯力加在两工作辊与支持辊的瓦座之间,使工作辊轴承座受到一个 与轧制压力方向相反的作用力 N1,结果是增大了轧制时工作辊的挠度,这称为负弯辊。 2 热轧薄板轧机多采用弯工作辊的方法。 第二种:弯曲支持辊的方法。这种方法是反弯力加在两支持辊之间。为此,必须延 长支持辊的辊头 ,在延长辊端上装有液压缸,使上下支持辊两端承受一个弯辊力 N2。 此力使支持辊挠度减小,即起正弯辊的作用。弯曲支持辊的方法多用于厚板轧机,它比 弯工作辊能提供较大约挠度补偿范围,且由于弯支持辊时的弯辊 挠度曲线与轧辐受轧制压力产生的挠度曲线基本相符合,故比弯工作辐更有效,对 于工作辊辊身较长(L/D 大于 4)的宽板轧机,一般以弯支持辊为宜。弯曲支持辊的方法 如图 1-2 所示。
图 1-1 弯工作辊(左图减小工作辊的挠度;右图增加工作辊的挠度) - 3 - 太原科技大学毕业设计说明书 图 1-2 弯曲支持辊
(2)CVC 轧机 CVC 轧机是 SMS 公司在 HCW 轧机的基础上于 1982 年研制成功的。CVC 轧机与 HCW 轧机的不同之处在于 CVC 轧机的工作辊原始辊型为 S 形,而 HCW 轧机的工作辊原 始辊型为平辊,其相同点都是采用工作辊轴向串动技术来控制板形。CVC 工作辊的轴向 移动量为±100mm ,其效果相当于常规磨辊凸度在 100μm 到 500μm 之间变化的效果。S 形辊的半径差仅为 273μm,上下轧辊线速度之差最大仅为 0.076% ,相当于带钢前滑值的 1%。CVC 系统的工作辊辊身比支撑辊辊身长出可移动的距离,以确保支承辊不会压到工 作辊边缘。由于工作辊具有 S 形曲线,工作辊与支承辊是非均匀接触,实践表明, 这种非 均匀接触对轧辊磨损和接触应力不会产生太大的影响。 CVC 轧机和弯辊装置配合使用可调辊缝达 600μm。CVC 在精轧机组的配置一般是, 前几个机架采用 CVC 辊主要控制凸度,后几个机架采用 CVC 辊要控制平直度。我国宝 钢 2050mm 热带钢轧机 7 个精轧机架均采用 CVC 轧机,可调凸度 400μm, F1~F5 弯辊装 置可调凸度 150μm,合计 550μm。宝钢采用 CVC 的作用是 F1~F4 改善凸度, F5~F7 改 善平直度。到目前为止, 全世界已投产近 70 台 CVC 热轧机。 CVC 轧制原理图:在轧辊末产生轴向移动时,轧辊构成具有相同高度的辊缝,其有 效凸度等于零(图 1-3(a))。如果上辊向左移动,下辊向右移动时,板材中心处两个轧辊 轮廓线 之间的辊缝变大,此时的有效凸度小于零(图 1-3(b))。 如果上辊向右移动下辊向 左 移动 时, 板材 中心 处两 个轧 辊轮 廓线 之间 的辊 缝变 小, 这时 的有 效凸 度大 于零 (图 1-3(c))。CVC 轧辊的作用与一般带凸度的轧辊相同,但其主要优点是凸度可以在最小和 最大凸度之间进行无级调整,这是通过具有 S 形曲线的轧辊作轴向移动来实现的。CVC 轧 辊辊缝 调整范围 也较大, 与弯辊 装置配合 使用时如 1700 热轧 机的辊缝 调整量 可达 600μm 左右。通过工作辊轴向移动可以获得工作辊辊缝的正负凸度的变化从而实现对带 钢凸度的控制。其凸度控制能力和工作辊轴向移动量为线性变化关系,凸度控制能力可以 达到 1.0mm。
- 4 - 太原科技大学毕业设计说明书 (a)平辊缝 (b)中凹辊缝 (c)中凸辊缝 图 1-3 CVC 轧机轧辊辊缝形状变化示意图 CVC 轧机的优点是: 板凸度控制能力强;轧机结构简单, 易改造;能实现自由轧制; 操作方便, 投资较少。CVC 轧机的缺点是: 轧辊形状复杂、特殊, 磨削要求精度高而且 困难, 必须配备专门的磨床;无边部减薄功能;带钢易出现蛇形现象。 (3)HC 轧机 HC 轧机为高性能板型控制轧机的简称。HC 轧机的主要特点有:①具有大的刚度稳 定性。即当轧制力增大时,引起的钢板横向厚度差很小,因为它也可以通过调整中间辊 的移动量来改变轧机的横向刚度,以控制工作辊的凸度,此移动量以中间辊端部与带钢 边部的距离 δ 表示,当 δ 大小合适,即当中间辊的位置适当,即在所谓 NCP 点(non control point)时,工 作辊的挠度即可 不受轧制力变化 的影响,此时的轧 机的横向刚度 可调至无 限大。②具有很好的控制性。即在较小的弯辊力作用下,就能使钢板的横向厚度差发生 显著的变化。HC 轧机还没有液压弯辊装置,由于中间辊可轴向移动,致使在同一轧机 上能控制的板宽范围增大了。③HC 轧机由于上述特点因而可以显著提高带钢的平宜度, 可以减少板、带钢边部变薄及裂边部分的宽度,减少切边损失。④压下量由于不受板形 限制而可适当提高。 (4)PC 轧机 对辊交叉(PC)轧制技术(Pair CrossRoll)。在日本新日铁公司广烟厂于 1984 年投产的 1840mm 热带连轧机的精轧机组上首次采用了工作辊交叉的轧制技术。PC 轧机的工作原 理是,通过交叉上下成对的工作辊和支撑辊的轴线形成上下工作辊间辊缝的抛物线,并 与工作辊的辊凸度等效。等效轧辊凸度 Cr 由公式表示:
2Dw 2Dw 式中 b—带材宽度; - 5 -
2 2 2 2 b tan q b q c = » (1.1)