含碳球团还原、渗碳、熔融机理的研究
球团理论与工艺-5球团矿的还原性状

400℃
主要反应 炉料预热,炉料水分的 蒸发 间接还原,结晶水的分 解 间接还原,少量的直接 还原,开始软化 间接还原,直接还原, 炉料软化 熔融、渣铁分离和渗碳
400~700℃
700~1100℃
1100~1300℃
1300~1500℃
5 球团矿的还原性状
*高炉冶炼过程概述
5 球团矿的还原性状
5.1 球团矿还原机理 5.1.3 球团断面的还原行为
球团中心至r1区域:h+m r1至r2区域:m+W r2至r3区域:W+Fe r3至rp区域:Fe
5 球团矿的还原性状
5.1 球团矿还原机理 5.1.3 球团断面的还原行为
球团中心至r1区域:赤铁矿 与磁铁矿共存 r1至r2区域:磁铁矿与浮士体 共存 r3至rp区域:单一的金属铁层
5 球团矿的还原性状
*高炉冶炼过程概述 (5)渣铁聚集区 在渣铁层间的交界面及铁滴穿 过渣层时发生渣金反应。 渣铁分层存在,焦炭浸泡其中。 主要反应: 渣铁间脱S, Si、Mn等元素还原
还原反应是高炉内的最基本反应。炉料从 高炉顶部装入后就开始还原,直到下部炉 缸,除风口回旋区外,几乎贯穿整个高炉冶 炼的始终。
5 球团矿的还原性状
(3)球团矿还原体积膨胀理论 在较高的还原速度 1)球团内气体压力增大引起异常膨胀。 )球团内气体压力增大引起异常膨胀。在较高的还原速度 下,球团内部CO2、H2O气体生成速度大于其通过气孔向外扩散 的速度时。 由于碳在铁和浮士体相界上的沉积引起 2)碳沉积膨胀理论。 )碳沉积膨胀理论。由于碳在铁和浮士体相界上的沉积引起 异常膨胀。 在低温还原条件下 CO→CO2+C(550℃) 2 2CO 形成的碳沉积在球团矿细微孔隙和晶体裂缝里导致球团矿 体积膨胀甚至粉化 在高温还原条件下(600~ 1200 ℃)碳素很少沉积
碳热还原法制锰合金

碳热还原法制锰合金碳热还原法是一种常用的方法,用于制备锰合金。
锰合金是一种重要的合金材料,具有广泛的应用领域,如冶金、化工、电力等。
碳热还原法制备锰合金的原理是利用高温条件下的化学反应。
锰矿石经过破碎、磨粉等预处理步骤后,与固体还原剂(一般为焦炭或石墨)一同进入高温电炉中。
在高温下,焦碳和锰矿石发生反应,生成锰铁合金和一定量的矽锰合金。
在反应过程中,锰矿石中的氧被焦碳还原为CO和CO2,同时,锰与焦碳反应生成锰铁合金。
碳热还原法制备锰合金具有以下特点:1.高反应温度:碳热还原法需要较高的反应温度,一般在1500-1600摄氏度之间。
高温有利于加快反应速度,并保证反应能够充分进行。
2.过程中的化学反应:碳热还原法中,锰矿石中的氧被焦碳还原为CO和CO2,并生成锰铁合金。
同时,一部分锰与硅反应生成矽锰合金。
3.过程控制:碳热还原法需要控制反应过程中的温度、还原剂的用量、矿石的粒度等因素。
不同的参数能够影响反应的速率和产物的品质。
碳热还原法制备锰合金的优点是制备过程简单、原料易得。
此外,碳热还原法能够制备出具有良好机械性能和热稳定性的锰合金。
然而,碳热还原法中也存在一些问题。
例如,反应温度较高,能耗较高;还原过程中有二氧化碳和一氧化碳等环境污染物的产生。
锰合金在不同领域有不同的应用。
在冶金行业,锰合金可用于制备不锈钢、合金钢、耐磨材料等。
在化工行业,锰合金可作为催化剂,用于有机合成和化学反应。
在电力行业,锰合金可用于制造电池、电池材料和电力设备。
总结来说,碳热还原法是一种制备锰合金的常用方法。
碳热还原法具有简单易行、原料易得的优点,可以制备出优质的锰合金。
然而,碳热还原法中也存在一些问题,如高能耗和环境污染。
锰合金具有广泛的应用领域,在冶金、化工、电力等行业中发挥着重要的作用。
熔炼过程中常见的冶金反应

热处理氮化反应是一种通过控制温度和氮气环境,以 改变金属内部结构和性能的过程。
详细描述
在热处理氮化反应中,金属被加热至高温,并暴露在 氮气环境中。通过控制温度和氮气浓度,可以改变金 属内部的晶体结构,使其变得更加稳定和强化。这种 处理方法能够显著提高金属的硬度和强度。
氮化处理过程中的反应
要点一
沉淀脱氧反应
总结词
沉淀脱氧反应是一种通过向熔融金属中加入脱氧剂,使 溶解在金属中的氧与脱氧剂反应生成不溶于金属的氧化 物,从而将氧从金属中去除的过程。
详细描述
沉淀脱氧反应通常使用如硅、锰、钛、锆等元素作为脱 氧剂。这些元素在金属中的溶解度较低,因此它们与氧 反应后生成的氧化物会以固态形式沉淀出来,从而达到 脱氧的目的。
复分解硫化反应
复分解硫化反应是指通过复分解反应生成金属硫化物的过程。
在熔炼过程中,一些金属元素可以通过与其他金属或非金属元素发生复分解反应 ,生成相应的金属硫化物。这种反应通常需要在特定的化学环境和温度下进行。 生成的金属硫化物同样具有较高的熔点和稳定性,因此在冶金工业中有广泛的应 用。
04
渗碳反应
真空脱氧反应
总结词
真空脱氧反应是一种通过降低熔融金属周围的压力,使溶解 在金属中的氧通过蒸发或化学反应的方式去除的过程。
详细描述
真空脱氧反应通常在高温和高真空条件下进行。降低压力可 以促进溶解在金属中的氧的蒸发,同时也可以使金属中的氧 化物更易于与脱氧剂发生反应。常用的脱氧剂包括碳、硅、 锰等元素。
表面渗碳反应
总结词
表面渗碳反应主要发生在金属表面,通过与渗碳介质(如煤、石油等)接触,使金属表 面含碳量增加。
详细描述
在渗碳过程中,碳原子通过扩散作用从渗碳介质中进入金属表面,使表面层的含碳量增 加。这种反应通常用于提高金属表面的硬度和耐磨性,如汽车发动机中的气缸内壁。
熔融还原炼铁技术

熔融还原炼铁技术摘要随着社会经济的发展,高炉炼铁资源短缺与环境负荷日益加重的局面已经充分显现,开发新技术逐步取代传统技术将迫在眉睫,这其中以熔融还原炼铁技术为主要开发对象。
国际钢铁界始终没有停止对熔融还原炼铁技术开发的脚步,本文对现有HIsmelt、COREX和FINEX熔融还原工艺及设备进行了分析研究和综合评价,指出了开发新熔融还原技术的原则,介绍了克服高炉炼铁及COREX、HIsmelt熔融还原法存在的缺点的LSM炼铁工艺。
我们应针对目前存在的问题,开发新的熔融还原炼铁技术。
关键词熔融还原;COREX;FINEX;HIsmelt;LSMSMELTING REDUCTION IRONMAKING TECHNOLOGYABSTRACT With the economic society developing, it fully shows that the resources shortage and environment of blast furnace ironmaking load have aggravated day by day. It is very urgent to exploit new technology to replace the traditional. The smelting reduction ironmaking technology is one of the main research fields. International Iron and Steel sector has not stopped for smelting reduction ironmaking technology development pace. The development for the smelting reduction ironmaking technology was never stopped in the world. This thesis just generates under this background.This paper analyzes and makes comprehensive evaluation of the existing HIsmelt, COREX and FINEX reduction process and equipment, points out that the principle of developing new smelting reduction technology, introduces LSM ironmaking process ,which overcomes existing shortcomings of blast furnace ironmaking and COREX, HIsmelt smelting reduction method.We should be aiming at the existing problems, develop new smelting reduction ironmaking technology.KEY WORDS smelting reduction,COREX,FINEX,HIsmelt,LSM1. 前言高炉炼铁方法从使用焦炭算起已有三百多年的历史,第二次世界大战后的50年来,钢铁冶金技术获得了重大发展。
高炉炼铁中矿石还原的机理及其影响因素

高炉炼铁中矿石还原的机理及其影响因素矿石还原在高炉炼铁过程中扮演着重要的角色,对于炼铁工艺的稳定性和炼铁产品的质量具有直接影响。
本文将探讨高炉炼铁中矿石还原的机理以及影响矿石还原的因素。
通过深入了解矿石还原的本质,我们可以更好地优化高炉操作,提高铁的产量和质量。
一、矿石还原的机理高炉炼铁过程中,矿石还原的机理是指将矿石中的金属氧化物还原为金属的化学反应过程。
在高炉中,通常使用生铁矿石作为主要原料,其中的主要成分是含有铁的氧化物,如赤铁矿(Fe2O3)。
矿石还原主要发生在高炉的还原带(还原温度约为900°C - 1150°C)。
矿石还原的主要反应可以用以下方程式表示:Fe2O3 + 3CO → 2Fe + 3CO2其中,Fe2O3代表赤铁矿,CO代表一氧化碳。
该反应是一个放热反应,反应产生的CO2会进一步参与高炉的燃烧过程,增加炉内热量。
二、影响矿石还原的因素1. 温度:矿石还原反应的速率随温度的升高而增加。
在高炉炼铁中,通过控制高炉内的温度,可以加速矿石还原的进行。
同时,温度的增加也会促进熔剂和渣的形成,有助于金属的分离。
2. 还原剂浓度:高炉炼铁中最常用的还原剂是一氧化碳(CO)。
增加CO的浓度可以提高矿石还原的速率,进而增加铁的产量。
因此,在高炉操作中,保证适当的还原剂供应非常重要。
3. 矿石性质:不同种类的矿石对于还原反应的速率会有所影响。
矿石的晶体结构、化学成分和颗粒大小等参数都可以影响矿石的还原性能。
特定的矿石还原性能需要通过实验和分析来确定,在高炉操作中选择合适的矿石非常重要。
4. 炉料层结构:高炉炼铁中,炉料层的结构对于还原反应的进行具有重要影响。
炉料层的密度和通气性会影响CO的扩散速率和矿石还原的进行。
因此,优化炉料层结构是提高高炉炼铁效率的关键一步。
5. 炉内气氛:高炉内的气氛对于矿石还原的进行有直接的影响。
在高炉操作中,保持合适的气氛可以提高矿石还原的速率,减少不必要的反应。
熔融还原新方法LSM工艺流程
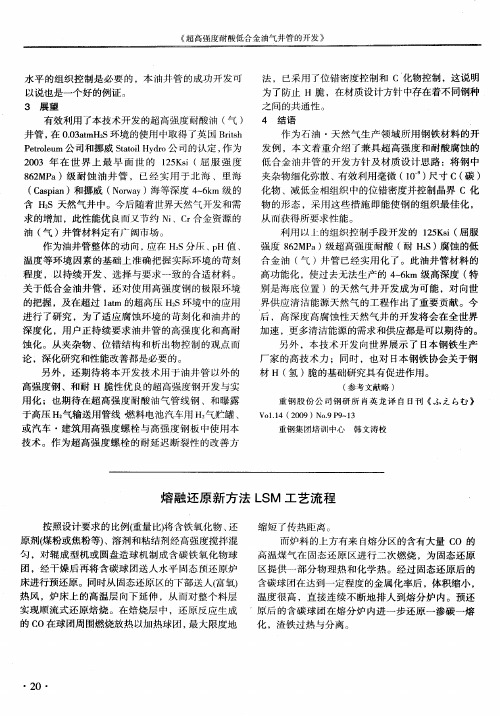
强度 82 a 6MP )级超 高强 度耐 酸 ( HS) 蚀 的低 耐 腐
合 金 油 ( )井管 已经 实用 化 了 。此油 井 管材 料 的 气
重钢 股 份 公 司钢 研 所 肖英 龙译 自 日刊 《v 之 岛 》 ; 1
Vo .4( 0 9)No9P ~1 11 2 0 . 9 3
或汽 车 ・ 筑用 高强 度 螺栓 与 高 强度 钢板 中使用 本 建 技术。作为超高强度螺栓的耐延迟断裂性 的改善方
重钢 集 团 培训 中心韩 涛 校 之 间的共 通性 。
4 结语
有 效利用 了本技 术 开发 的超高 强度 耐酸油 ( ) 气 井 管 , 00 amH S 境 的使用 中取得 了英 国 B ih 在 . t :环 3 rs t
P t lu e o m公 司和挪 威 Sa iH do 司 的认 定 , 为 re t ol y r 公 t 作
发例 ,本 文 着 重介 绍 了兼 具 超 高强 度 和耐 酸腐 蚀 的 低 合 金 油井 管 的开 发 方 针及 材质 设 计思 路 :将 钢 中 夹 杂物 细化 弥散 、有效 利用 毫微 ( 0 尺 寸 C( ) 1 ) 碳 化 物 、减 低 金相组 织 中的位 错密度 并控 制 晶界 C 化 物 的形 态 ,采用 这些 措 施 即能 使 钢 的组织 最 佳化 ,
高功能化 , 使过去无法生产的 4 6m级高深度 ( -k 特 别 是海 底 位 置 )的天然 气 井开 发 成 为可 能 ,对 向世
界 供应 清 洁 能源 天 然气 的工程 作 出 了重 要贡 献 。今
氧化球团链篦机_回转窑结圈机理的研究
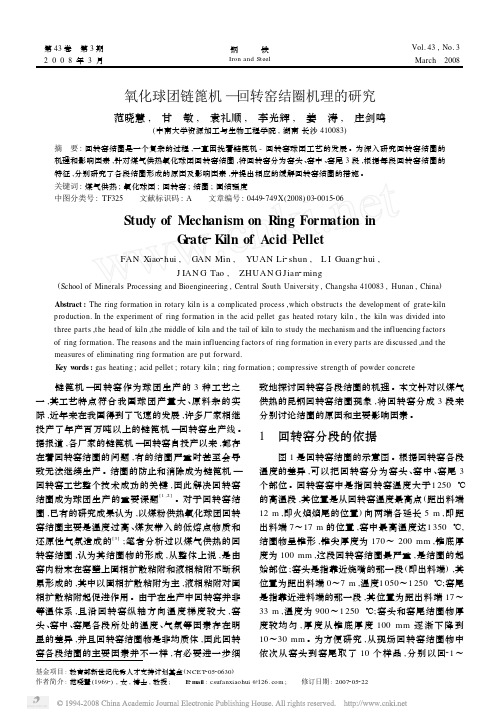
致地探讨回转窑各段结圈的机理 。本文针对以煤气 供热的昆钢回转窑结圈现象 ,将回转窑分成 3 段来 分别讨论结圈的原因和主要影响因素 。
1 回转窑分段的依据
图 1 是回转窑结圈的示意图 。根据回转窑各段 温度的差异 ,可以把回转窑分为窑头 、窑中 、窑尾 3 个部位 。回转窑窑中是指回转窑温度大于1 250 ℃ 的高温段 ,其位置是从回转窑温度最高点 (距出料端 12 m ,即火焰焰尾的位置) 向两端各延长 5 m ,即距 出料端 7~17 m 的位置 ,窑中最高温度达1 350 ℃, 结圈物呈锥形 ,锥尖厚度为 170~ 200 mm ,锥底厚 度为 100 mm ,这段回转窑结圈最严重 ,是结圈的起 始部位 ;窑头是指靠近烧嘴的那一段 (即出料端) ,其 位置为距出料端 0~7 m ,温度1 050~1 250 ℃;窑尾 是指靠近进料端的那一段 ,其位置为距出料端 17~ 33 m ,温度为 900~1 250 ℃;窑头和窑尾结圈物厚 度较均匀 , 厚度从锥底厚度 100 mm 逐渐下降到 10~30 mm 。为方便研究 ,从现场回转窑结圈物中 依次从窑头到窑尾取了 10 个样品 ,分别以回21~
结圈物中的低熔点物质主要包括橄榄石和玻璃
第3期
位置编号
橄榄石 玻璃质 渣相量
回21 3. 26 1. 34 4. 60
范晓慧等 :氧化球团链篦机 —回转窑结圈机理的研究
窑头 回22 3. 71 2. 44 6. 15
表 1 低熔点物质在回转窑各位置的分布
Table 1 Composition of low melting minerals in rings
图 2 焙烧温度对粉末固结强度的影响 Fig. 2 Effect of roast temperature on compression strength of powder
含碳球团厚料层穿流干燥的实验研究

《工业加热》 第
球团原料及粒度
TFe 68.0 0 ~ 1.4 1) (75) C 77.07 CaO 0.4 1.4 ~ 2.0 1) (10) A2) 10.18 SiO2 3.95 Al2O3 0.79
卷
年第
期
算法得到平均干燥速率回归方程、 干燥时间回归方程、 球 团表面温度变化回归方程以及瞬时干燥速率回归方程。 由 于干燥过程明显分为升速和降速两段,为了更好地描述 干燥过程,所以将瞬时干燥速率的回归方程分为升速段 和降速段两部分。 (1)平均干燥速率回归方程
为干燥终了质量;
误差分析
由表 3 可见回归方程(1)~(5)的均方差和残差 平方都在误差允许的范围内并且相关性很好。
表3
结果 均方差 残差平 方和 相关 系数
1 2
误差分析表
s j t
0.000 595 17 5.667 67 × 10 0.899 99
6
2.459
0.001 68
0.001 781 7
FENG Jun-xiao,XIE Xiao-yan,SUN Li-jia,ZHANG Da-bao (Department of Thermal Science and Energy Engineering,University of Science and Technology Beijing,Beijing 100083,China) Orthogonal experiments of cross-flow drying through thick layer carbon-containing pellets were made. The influence of different parameters, such as air temperature,air speed,initial moisture content, size and thickness of raw pellets and so on, on drying process was studied in hot air cross-flow experiment. The multi-exponent formulas which reflect the effects of the parameters listing above on average and transient drying rate,drying time and temperature in drying progresses were gained, and the precision of these formulas is high enough to be applied.So the results got from the experiments could offer reference to industry production. carbon-containing pellets;thick layer;cross-flow drying;orthogonal regression
- 1、下载文档前请自行甄别文档内容的完整性,平台不提供额外的编辑、内容补充、找答案等附加服务。
- 2、"仅部分预览"的文档,不可在线预览部分如存在完整性等问题,可反馈申请退款(可完整预览的文档不适用该条件!)。
- 3、如文档侵犯您的权益,请联系客服反馈,我们会尽快为您处理(人工客服工作时间:9:00-18:30)。
(a) Coal char(20%) + Iron ore(80%) + Bentonite(1%) (b) Coal char(20%) + Electrolytic iron(80%) + Bentonite(1%) (c) Graphite(18.2%) + Iron ore(81.8%) + Bentonite(1%) (d) Graphite(18.2%) + Electrolytic iron(81.8%) + Bentonite(1%)
heated for 9min at 1350oC.
Shell Core
Cross sectional view
Melted
Not melted
( pellet Pc,i )
( pellet Pg,i )
Fig. Outside views and a cross-section of
coal char-iron ore ( pellet Pc,i ) and graphite-iron ore ( pellet Pg,i ) composite pellets heated in N2 for 30min at 1250oC.
其他的影响要因:
1 温度 2 反应气氛
3 气体流量
4 球团内部的压力
本研究的目的
1. 考察焦粉(或者石墨)- 铁矿石混合球团在氮气中高温
加热时所发生的体积膨胀、 强度变化等各种现象。
2. 考察含碳球团通过快速升温所发生的高速还原及渗碳。 3. 球团内部球壳-球心(shell-core)构造的形成、熔融。
本研究中所用到的原料
(1) 焦粉(%) (2) 石墨粉(%)
Proximate analysis
Ash V.M
F.C
2.79 6.17 91.04
Ultimate analysis
C
H
O.N.S
88.28 0.86 8.07
Water Ash Purity <0.50 <0.05 >99.50
(3) 铁矿粉(%)
Time (s)
(a)
6 5 4 3 2 1 0 300
C,core S,core
C,shell S,shell
1350℃
420 540 660 780 Time (s)
(b)
0.07 0.06 0.05 0.04 0.03 0.02 0.01 0.00 900
1100℃
1200℃
1300℃
1350℃
Fig. Schematic internal structure of coal char-iron ore composite pellets heated for 10min at 1100-1350oC.
5min
7min
Core
Void
Shell
9min
含碳球团还原、渗碳、熔融机理的研究
东北大学 材料与冶金学院 钢铁研究所
孟繁明
含碳球团高温还原机理
反应路径
C+CO2=2CO
(1)
FenOm+mCO→nFe+mCO2 (2)
Coal(煤)→volatile matter (CO, CO2, H2, N2, etc.)+char(C) (3)
C+ H2O=CO+ H2
Melted at surface area
Fig. Photograph of a graphite-iron ore composite pellet Heated for 9min at 1250 showing melted and gathered reduced iron drops.
11min
Fig. Cross sectional views of coal char-iron ore composite pellets heated at 1350oC.
(core, ×400)
Core direction
( core, ×100)
( shell, ×100 )
Fig. Metallographic cross-sections of the shell and core of a coal char-iron ore composite pellet
(4)
FenOm+ mH2→nFe+ mH2O (5)
控制环节
氧化铁的还原反应 炭的气化反应 传热 以上个过程的组合
重要的考察对象
影响含碳球团反应速度的因素
有关原料因素的影响:
1 氧化铁以及还原剂炭的粒度
2 氧化铁以及还原剂炭的化学组成
3 粘结剂的量,
4 还原剂的添加量 5 球团的大小 6 球团的气孔率
Na2O 2.43
D
Pellet, D =18mm
1.gas cylinder
2.flow meter
7 3.furnace
4.sample
slide
5 5.magnet
8
6.cold water 7.motor
8.iron block
6
3
4
1 CO2
2
N2
1
2
CO 1
Fig. Schematic diagram of the experimental apparatus Fig. Experimental apparatus
Carbon (%) Sulfur (%) Carbon (%) Sulfur (%)
9
0.09
C,core
C,medium
8
C,shell
S,core
0.08
S,medium
S,shell
7
0.07
6
0.06
5
0.05
4
1200℃
0.04
3
0.03
2
0.02
1
0.01
0
0.00
540 600 660 720 780 840 900
7min
9min
Not melted
Melted at surface area
(1)
(2)
11min
Fig. Cross sectional views of graphite-iron ore composite pellets at 1250oC. (1) A melted and gathered drop from shell and (2) Not melted residue.
T.Fe 66.7
SiO2 1.76
Al2O3 0.35
P
S
FeO
0.05 0.005 0.68
CaO 0.06
(4) 电解铁粉(ppm) C P
S
Si
Mn
20
7
47
6
8
(5) 粘结剂 (%)
SiO2 67.52
Al2Oቤተ መጻሕፍቲ ባይዱ 12.97
Fe2O3 2.94
CaO 3.15
MgO 2.04
K2O 1.14