微合金化技术的开发与应用
铌钛微合金化汽车大梁板510L开发

铌钛微合金化汽车大梁板510L开发
范敬国;赵征志;赵爱民
【期刊名称】《热加工工艺》
【年(卷),期】2009()8
【摘要】在实验室试制了低碳高强度汽车大梁板510L;利用Gleeble 2000热模拟试验机研究了汽车大梁板在不同连续冷却工艺条件下的组织变化情况,并绘制了试验条件下动态CCT曲线;通过拉伸试验和光学显微镜研究了试制钢板显微组织与力学性能之间的关系。
结果表明:钢板的连续冷却相变温度随冷速的提高而降低,随冷速的提高,实验钢组织细化,铁素体形貌从多边形逐渐向针状转变,当冷却速率大于10℃/s时,试样显微组织中出现部分贝氏体。
【总页数】4页(P21-24)
【关键词】微合金钢;相变;CCT曲线;显微组织
【作者】范敬国;赵征志;赵爱民
【作者单位】武汉钢铁股份有限公司生产技术部;北京科技大学冶金工程研究院【正文语种】中文
【中图分类】TG142.1
【相关文献】
1.通钢TG510L铌钛微合金化汽车大梁钢工艺研发 [J], 于川;李春雷
2.铌钛微合金化汽车大梁钢BM510L的开发 [J], 万兰凤;冷祥贵
3.涟钢CSP流程铌微合金化生产汽车大梁板 [J], 刘跃飞
4.铌钛微合金化汽车大梁用热轧板带BM510L的开发 [J], 万兰凤;冷祥贵
5.Ti微合金化汽车大梁钢510L的组织性能 [J], 陈其源;周晓光;刘振宇;吴思炜因版权原因,仅展示原文概要,查看原文内容请购买。
新型VTiB微合金化调质Q690E钢板的开发
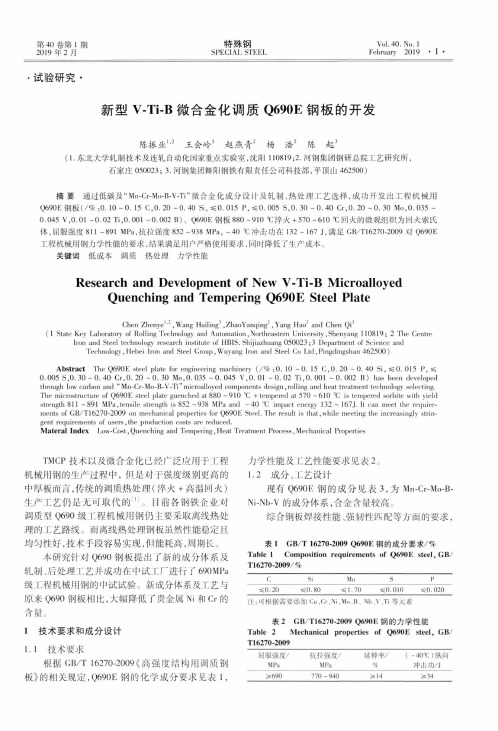
本研究 针 对 Q690钢 板 提 … j,新 的成 分 体 系 及 轧制 、后 处理工 艺 并成功 【{I试 J 厂进 行 r 690MPa 级 l 程机 械用钢 的中试试 验 。新 成分 体系 及_ 1 艺与 原 来 Q690钢 板 卡l】比 ,大幅 降低 J 炙金属 Ni和 Cr的 含 }
Ihrough low carbon and “M n—CI-一Mo—B—V—Ti”microalhwed ('oHlp()nenls design.rolling all(1 heat treatment technology selecting.
l、he nlieroslructure of Q690E st ̄ PI plate guenche ̄l at 880~9l0 +tenlpere(1 at 570~6lO ℃ is[em1)et·P(1 sorbite with vield stren ̄h 8 1 l~89 l MPa.tensile strength is 852~938 MPa all(1 —4O ℃ impat·t energ ̄ l 32 ~l 67J.11('all nleel the require— illents of GB/Tl6270—2009 Oil lne(·hani ̄-al properties fi)r Q690E St( e1. Fhe result is that,while meeti z1g tile jncreasingly strin—
铌在特殊钢中的应用
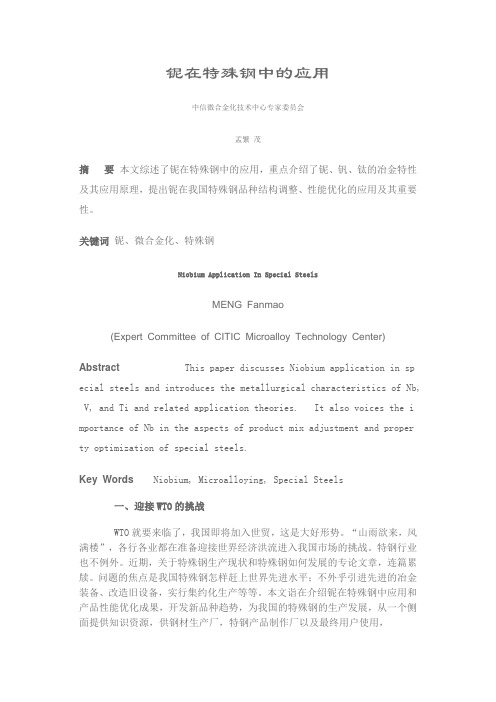
铌在特殊钢中的应用中信微合金化技术中心专家委员会孟繁茂摘要本文综述了铌在特殊钢中的应用,重点介绍了铌、钒、钛的冶金特性及其应用原理,提出铌在我国特殊钢品种结构调整、性能优化的应用及其重要性。
关键词铌、微合金化、特殊钢Niobium Application In Special SteelsMENG Fanmao(Expert Committee of CITIC Microalloy Technology Center)Abstract This paper discusses Niobium application in sp ecial steels and introduces the metallurgical characteristics of Nb, V, and Ti and related application theories. It also voices the i mportance of Nb in the aspects of product mix adjustment and proper ty optimization of special steels.Key Words Niobium, Microalloying, Special Steels一、迎接WTO的挑战WTO就要来临了,我国即将加入世贸,这是大好形势。
“山雨欲来,风满楼”,各行各业都在准备迎接世界经济洪流进入我国市场的挑战。
特钢行业也不例外。
近期,关于特殊钢生产现状和特殊钢如何发展的专论文章,连篇累牍。
问题的焦点是我国特殊钢怎样赶上世界先进水平;不外乎引进先进的冶金装备、改造旧设备,实行集约化生产等等。
本文诣在介绍铌在特殊钢中应用和产品性能优化成果,开发新品种趋势,为我国的特殊钢的生产发展,从一个侧面提供知识资源,供钢材生产厂,特钢产品制作厂以及最终用户使用,开发新产品参考应用。
二、现代钢特点现代钢生产的三大技术是材质纯净化,晶粒细化,尺寸精确化。
屈强比

工程结构用钢屈强比问题的探讨添加日期:9/13/2009 阅读500次工程结构用钢屈强比问题的探讨东涛付俊岩中信微合金化技术中心,专家委员会随着钢的微合金化技术、热机械处理技术(TMCP)、以及新型的低合金高强度钢(微合金化钢)的开发和应用,随着强度的提高, 作为工程结构用钢材的主体微合金化钢的屈强比高于传统的热轧低合金钢和热处理类型的低合金钢是高强度钢发展的必然趋势。
由于国内的钢材使用客户在安全性设计时,明显地趋于保守,钢的高屈强比已成为不安全的同义词。
但是,在国内钢铁业装备得到了普遍的技术改造的基础上,钢的洁净度已大大提高,按微合金化强韧化机制,并采用热机械处理的优化工艺流程生产的新型高强度钢材不断涌现,工程结构设计中对钢的屈强比的认识也应当有所调整,从经济性和安全性两个角度向国际规范靠拢,积极采用较高屈强比并具有高韧性的高强度微合金化钢,以推动我国工程结构设计和制造业发展现代化。
1、屈强比的物理涵义和工程价值钢的抗拉强度,一般称之为强度极限,是普通意义上评价和区分钢材等级的依据。
钢的屈服强度是指在应力不增加的情况下,塑性变形继续增加并可至某个数值,对于脆性材料,几乎极小塑性变形,在达到极限强度后瞬间发生断裂,而对于多数工程结构用的延性材料,则在超过屈服强度后,将出现“缩颈”,而导致承载能力下降,所以更多地把屈服强度作为承载构件的工程设计的主要依据。
钢的屈强比是在屈服强度与抗拉强度之比值,自然把屈强比表征材料均匀变形的能力,由塑性变形至最后断裂过程的形变容量。
在船舶、桥梁、容器、管线、建筑等工程结构设计中,无不重视钢的屈强比这一参数,而且在相应规范中都限定屈强比在某个范围。
表1 各规范对屈强比的要求标准名称或编号对屈强比的规定API Spec 5L X80 扩径管YR≤0.93,其它无要求ISO 3183-2 X42~X52 YR≤0.85,X60~X80 YR≤0.90ISO 3183-3 X42~X52 YR≤0.90,X60~X80 YR≤0.92GB 9711.1 无要求CAN3-Z245.1-M86 无要求TransCanada P-04 YR 无要求,但要求均匀伸长率δb>10Snampragetti Spc/TB-F-700 高于X65 扩径管YR≤0.90,其余YR≤0.85SHELL GROUP L-3-2/3 YR≤0.90PEMEX TSA-001 YR≤0.85DNV 海上钢管安装规范对扩径管YR≤0.90,一般要求YR≤0.85ARCO 4957-ALC-SS-L-1001 YR≤0.90俄75-86 对X65 YR≤0.902在一定的抗拉强度水平下,提高钢的屈服强度,亦即提高钢的屈强比,可增加材料的使用应力,挖掘材料的潜力,以油气输送管线用钢为例,各规范对屈强比有不同的规定,见表1,在0.85~0.92 范围之内。
《微合金元素在钢》课件

此外,随着实验设备和测试技术的不 断进步,对微合金元素在钢中的行为 和作用机理的认识也更加深入。
近年来,研究者们通过深入研究微合 金元素的原子结构、相变机制和微观 组织演化,进一步揭示了微合金元素 在钢中的作用机制。
微合金元素的发展和应用 推动了钢铁工业的技术进 步,促进了相关领域的发 展。
02
微合金元素在钢中的分布与存在形式
微合金元素在钢中的分布
01
碳、氮、氧等元素
这些元素在钢中以固溶形式存在 ,主要分布在铁素体和奥氏体中 。
02
铬、镍、锰等元素
03
硅、磷、硫等元素
这些元素在钢中以置换形式存在 ,主要分布在铁素体和奥氏体中 。
分类
碳氮间隙元素(如钛、铌、锆)、碳 氮化物形成元素(如钒、铬、钼)和 晶界强化元素(如硼、磷、砷)。
微合金元素在钢中的作用
01
02
03
细化钢的晶粒
通过形成碳氮化物或氮化 物,微合金元素可以阻碍 奥氏体晶粒的长大,从而 细化钢的晶粒。
改善钢的韧性
某些微合金元素可以改变 钢的韧性,例如钛和铌可 以增加钢的低温韧性。
微合金元素对钢强度的影响
显著增强
微合金元素可以与钢中的碳形成碳化物,这些碳 化物在钢中起到“钉扎”作用,抑制奥氏体晶粒 长大,从而在冷却过程中获得更细小的铁素体晶 粒,提高强度。
微合金元素如钛、钒、铌等可以细化钢的晶粒, 从而提高其强度。
通过微合金元素的加入,可以实现仅通过热处理 工艺即达到提高强度和改善韧性之间的平衡。
同时,随着人工智能和大数 据技术的应用,对微合金元 素在钢中的研究将更加智能 化和精细化,有望实现更加 精准和高效的钢材性能调控
铌微合金化高强度钢在轻量化商用车列车上的应用

铌微合金化高强度钢在轻量化商用车列车上的应用
随着环保意识的不断增强以及节能减排的需求,轻量化商用车列车的
发展越来越得到重视。
而铌微合金化高强度钢作为一种优良的材料,其具
有高强度、低成本、良好的可焊性和耐腐蚀性等优点,适合用于轻量化商
用车列车上。
首先,在车身结构方面,铌微合金化高强度钢可以用于车身构件的制造,如前支架、引擎罩、车门等。
这种钢材质轻、强度高,能够减少车身
重量和燃料消耗,提高车辆的整体性能。
其次,在底盘系统方面,铌微合金化高强度钢可以用于制造悬挂系统、制动系统等零部件。
这种钢材制作的车轮可以提升车辆的抗拉强度和承载
能力,同时还可以延长车轮寿命,降低使用成本。
最后,在安全性方面,铌微合金化高强度钢的强度和耐腐蚀性可以带
来更好的安全性能。
当车辆遭受碰撞或进入恶劣环境时,这种钢材可以提
供更强的抗压和耐腐蚀性能,有效保障驾驶员和乘客的搭乘安全。
总之,铌微合金化高强度钢在轻量化商用车列车上的应用可以显著降
低车辆的重量和燃料消耗,提高车辆的整体性能和安全性能。
未来,随着
材料制造技术的不断创新和升级,相信这种材料在轻量化商用车列车上的
应用将会越来越广泛。
《高Nb微合金钢中NbC的析出对组织与硬度的影响》范文
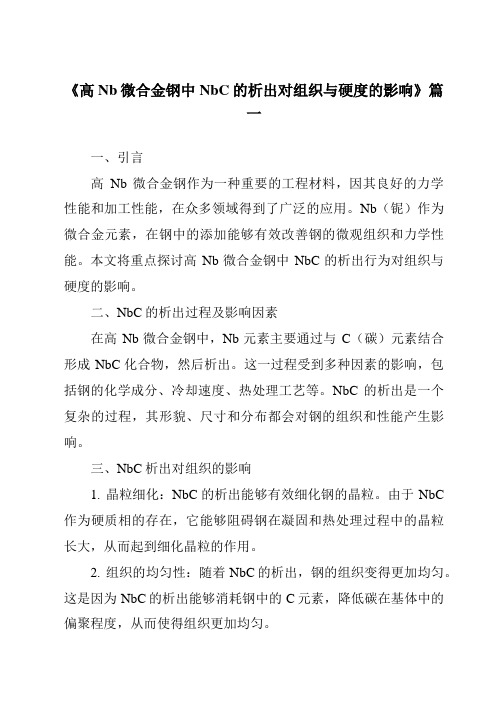
《高Nb微合金钢中NbC的析出对组织与硬度的影响》篇一一、引言高Nb微合金钢作为一种重要的工程材料,因其良好的力学性能和加工性能,在众多领域得到了广泛的应用。
Nb(铌)作为微合金元素,在钢中的添加能够有效改善钢的微观组织和力学性能。
本文将重点探讨高Nb微合金钢中NbC的析出行为对组织与硬度的影响。
二、NbC的析出过程及影响因素在高Nb微合金钢中,Nb元素主要通过与C(碳)元素结合形成NbC化合物,然后析出。
这一过程受到多种因素的影响,包括钢的化学成分、冷却速度、热处理工艺等。
NbC的析出是一个复杂的过程,其形貌、尺寸和分布都会对钢的组织和性能产生影响。
三、NbC析出对组织的影响1. 晶粒细化:NbC的析出能够有效细化钢的晶粒。
由于NbC 作为硬质相的存在,它能够阻碍钢在凝固和热处理过程中的晶粒长大,从而起到细化晶粒的作用。
2. 组织的均匀性:随着NbC的析出,钢的组织变得更加均匀。
这是因为NbC的析出能够消耗钢中的C元素,降低碳在基体中的偏聚程度,从而使得组织更加均匀。
3. 第二相的形成:NbC的析出还会形成第二相,这些第二相能够有效地提高钢的强度和韧性。
四、NbC析出对硬度的影响1. 硬度的提高:由于NbC具有较高的硬度,因此其析出会显著提高钢的硬度。
随着NbC的析出量和尺寸的增加,钢的硬度也会相应提高。
2. 硬度的均匀性:由于NbC的均匀析出,使得钢的硬度分布更加均匀。
这有利于提高钢的力学性能和加工性能。
五、实验研究及结果分析通过实验研究,我们发现高Nb微合金钢中NbC的析出对组织和硬度的影响是显著的。
随着Nb含量的增加,NbC的析出量也相应增加,钢的晶粒得到细化,组织更加均匀,硬度也有所提高。
此外,我们还发现适当的热处理工艺能够促进NbC的析出,进一步提高钢的性能。
六、结论高Nb微合金钢中NbC的析出对组织和硬度具有显著影响。
通过控制Nb的含量和热处理工艺,可以有效地调控NbC的析出行为,从而改善钢的微观组织和力学性能。
控轧控冷

关于对控轧控冷与正火的认识1、TMCP技术TMCP(Thermo Mechanical Controlled Processing: 热机械控制工艺)技术是以控制轧制和控制冷却技术相结合的特点,也就是低温轧制和在线热处理的综合处理手段,在控制形变组织的基础上,又控制随后的冷却速度,获得理想的相变组织。
其要点是将连铸坯低温加热到1000℃左右,在具有较小晶粒的奥氏体区开始轧制,在适当的Ar3温度附近的亚稳态奥氏体区或γ+α两相区变形。
随后控制冷却,使加工后未再结晶组织进行恒温转变,通过晶粒内变形带上形成的大量晶核,实现细晶铁素体的转变。
在同样的变形量下,恒温转变温度越低,铁素体的形核率越高,组织晶粒越细。
TMCP技术的实质就是传统的形变热处理工艺在轧制生产中在线完成,从而得到高强度化及高韧性化。
各种轧制程序的模式图,如图1—1所示:(1)控制轧制的类型[3]控制轧制(Controlled Rolling)是通过严格控制热轧工艺参数,充分发挥微合金元素的作用,以达到细化晶粒、改善钢的组织结构和机械性能的目的,从而可直接轧制成材和取消一些热处理工序,取得节能降耗的效果。
最初的控制轧制是在奥氏体低温区进行大的压下量,它是指在比常规轧制温度稍低的条件下,采用强化压下和控制冷却措施来提高热轧钢材的强度和韧性等综合性能的一种轧制方法。
现在人们对控制轧制广义地解释为是通过微合金化处理,从轧前的加热到最终轧制道次结束为止的整个轧制过程实行最佳控制的全新工艺,以控制奥氏体状态和相变产物的组织状态,达到改变钢板的综合机械性能的目的。
控制轧制技术多用于结构钢生产中,因为对结构钢的要求是高强度、高韧性和良好的焊接性能。
而为使结构钢获得最佳综合性能,最好的方法是使钢的晶粒细化,主要是细化铁素体晶粒,它可以通过两种途径来完成:一种是细化奥氏体晶粒,然后通过相变得到细化的铁素体晶粒;另一种是直接细化铁素体晶粒。
这两种方法的机理是不同的,细化奥氏体的机理首先要细化原始奥氏体晶粒,即从加热温度、加热时间和加入微量合金元素这三方面入手,然后采用形变再结晶的方法。
- 1、下载文档前请自行甄别文档内容的完整性,平台不提供额外的编辑、内容补充、找答案等附加服务。
- 2、"仅部分预览"的文档,不可在线预览部分如存在完整性等问题,可反馈申请退款(可完整预览的文档不适用该条件!)。
- 3、如文档侵犯您的权益,请联系客服反馈,我们会尽快为您处理(人工客服工作时间:9:00-18:30)。
微合金化技术的开发与应用 中信微合金化技术中心专家委员会 王祖滨 (2000年11月)
1. 开发微合金化技术的重要意义 在不久前召开的第四届国际低合金高强度钢会议(HSLA Steel '2000)的一篇特邀报告(W.B.Morrison)中写道,过去半世纪中,钢铁材料最重要的发展无疑要数低合金高强度钢。在1984年,有人估计世界低合金高强度钢的产量约为5千万吨,并将以每年5%的速度增长。而目前的估计约为8千万吨,相当于世界钢产量的十分之一,这与当时的预测是很接近的。作者认为,低合金高强度钢普及之快的原因在微合金元素Nb、V、Ti的合理和经济的使用。虽然并不是所有的低合金高强度钢都进行微合金化,但是由于微合金化对提高低碳结构钢强度的显著作用,在不少场合往往把微合金钢和低合金高强度钢等同起来。应该指出,目前微合金化已经不仅用于以板带材为主,以供应状态直接供用户使用的低合金高强度钢,而且在线材、钢筋、钢轨以及锻材方面广泛应用。专家预测,在即将到来的21世纪中,微合金化的低合金高强度钢不仅在用量上有大幅度增长以及在广阔的用途上取代碳素钢,而且微合金化可以作为一种能降低成本,符合可持续发展要求又能促进技术进步的手段来开发综合性能更好的钢铁产品。 2. 微合金化技术的原理 众所周知,传统的低合金高强度钢采用固溶强化机制,加入的合金元素Mn、Si、Ni、Cu、Cr等元素大约在百分之一、二的数量级。增加含量不仅不能提高强度,而且使其他性能恶化。根据文献资料,V、Ti等元素在本世纪初即已开始使用,而Nb在本世纪中发现有较大储量后也开始用于钢铁产品。它们的加入量分别在千分之一、二甚至万分之几的数量级。数量虽小,但是由于它们的作用机制不清楚,产品性能不稳定,甚至牺牲塑性、韧性这样一些重要结构材料性能,而未受到重视。这个局面直到进行了大量研究工作,对微合金钢的物理冶金有了深入的理解以后才有根本变化。理解这些问题的关键是Petch发现的晶粒尺寸与强度及断裂性能之间的定量关系。这个关系式能区分微合金化元素的不同作用并加以定量化,而且早期的研究即已表明,主要是碳化物及氮化物的形成而引起晶粒细化和析出强化,这是这些微合金化元素强烈影响性能的原因所在。 用Al来细化钢的晶粒从而改善钢的强、韧性,已有半个多世纪的历史。从广泛意义上讲,微合金元素有七、八种,但是,研究得最多、用得最广的是Nb、V、Ti。微合金元素与钢中的C、N、O、S形成多种化合物,从而对性能产生多种影响。微合金元素能够影响的显微组织参数是晶粒尺寸和形状;各种尺寸的析出物;位错密度;织构演变;非金属夹杂物的尺寸和形状。对微合金钢来说主要是晶粒细化和析出强化。 晶粒细化是不同强化机制中唯一的既能提高强度又能降低脆性韧性温度的方法。微合金元素通过析出质点在从冶炼凝固过程到焊接加热、冷却过程中影响晶粒成核和晶界迁移来影响晶粒尺寸。对在加热过程中抑制奥氏体晶粒长大最为强烈的是Ti,依次为Nb、Al和V。但是从加入量来说,在控轧和正火钢中Nb用比较低的含量,即现在常用的0.03%左右即能起显著的作用。Nb对晶粒细化的独特影响表现在它对奥氏体再结晶有强烈的延迟作用。用0.03%Nb即可将完全再结晶所需的最低温度提高到950℃左右,从而显著降低控轧对轧机负荷的要求。由于Ti在连铸冷却条件下生成弥散的TiN,对阻止奥氏体晶粒细化有很强的效果,80年代初,开发了一种V-Ti-N微合金钢,适合在高温区细化晶粒的再结晶控轧工艺,为不能进行低温轧制的老式低轧制力的轧机进行控轧开辟了途径。最近的研究表明Nb-Mo系钢也适合此种工艺。近年来,在钢板,特别是厚板的焊接中,为了提高效率,广泛使用大线能量。这种措施对焊接热影响区韧性极为不利。由于TiN熔点很高,在焊接热影响区都能抑制晶粒长大,所以加微量Ti0.03%能显著改善热影响区韧性。 微合金元素的另一重要作用是析出强化。这种最有效的强化是由在奥氏体转变成铁素体过程中或转变之后随即生成的碳氮化物引起的,它们在铁的晶格中对位错运动起了阻碍作用。强度的提高与析出质点的体积分数及尺寸大小成比例。在微合金化钢中,由析出引起的强化可能非常显著。这是由于析出质点非常细,通常小于10nm。在多数钢中V比Nb更易溶解。因此加钒由于质点体积分数较大,析出强化作用更为显著。 析出强化与晶粒细化不同,在提高强度的同时也提高脆性转折温度。当两种机制叠加时,在不同钢种中的影响就大不一样。Nb的强度增量主要靠晶粒细化,而且在0.04%以下增加很快,而V的强度增加主要靠析出强化,强化的分量很小。Ti的作用居中,特别是0.08%以下靠晶粒细化,超过0.08%,析出强化起主要作用。由于晶粒细化能降低转折温度,而析出强化提高转折温度,综合影响的结果是,Nb在0.03-0.04%以下,Ti在0.08%以下降低脆性转折温度,但是V不论含量多少都将提高脆性转折温度。 还应指出,微合金元素都能收集间隙原子C、N,这个原理已被用于开发无间隙原子(IF)钢,其中含Ti或Ti-Nb的带钢具有特别好的冲压性能,而且适宜进行连续退火和热镀锌。最近又开发了一种含Ti+V的IF钢,由于VC在铁素体中具有高的溶解度,使它具有优良的烘烤硬化性。Ti作为N的收集元素在其他类型钢中也起一定作用。当Ti加入铌处理的HSLA钢中发现有若干益处。轧钢时在奥氏体中富N的NbCN析出要少,使轧制力降低,而且可以提供更多Nb,从而增加析出强化。而另一方面,Ti加入到V处理钢中时,析出强化的份量看来要降低,除非有意地加N以抵消上述作用。 微合金元素的复合加入被证明对性能的影响要比单个元素加入的影响之数学相加要大得多。例如,为了开发屈服强度达到700Mpa的热轧带钢,采用了多种合金元素和微合金元素,集合了晶粒细化、固溶强化、析出强化和位错强化(相变强化)多种强化机制。为了开发现代的高强度钢经常综合多种强化机制以期获得多种性能的最佳配合。 3.应用微合金化技术要与优化工艺过程相结合 微合金化技术采用千分之几到万分之几的微合金元素就能显著影响钢的性能的事实受到广泛的重视,这是理所当然的。但是要用好微合金化技术必须与优化工艺过程相结合,却往往没有受到应有的重视,这是值得注意的。这里所指优化工艺过程的含意有两个方面。第一,正是由于微合金元素用量相对较少,而且它们影响性能的机制对工艺参数比较敏感,因此,对成分和工艺参数的控制应该有比采用一般合金元素更严格的要求,也就是说控制在比较窄的范围内,并保证在由钢水到钢材的全过程中,尽可能均匀一致。第二,鉴于微合金元素的某些独特作用,只有在一定的工艺条件下才能实现,必须创造必要的工艺条件和研究工艺参数的优化。 1990年,J.M.Gray在北京第二届国际低合金高强度钢会议报告中对1960-1990年期间钢铁冶金生产工艺技术的变革以及与钢材品种质量有关的特性进行了归纳。笔者对以后的发展又作了相应的补充(见表1)。为了更好发挥微合金化技术的作用,需要不断优化工艺过程,向现代生产工艺靠拢,即高炉 —— 铁水预处理——转炉顶底复合吹炼或超高功率电弧炉冶炼——钢包喷粉、喂丝——真空除气——板坯或方坯连铸。多种多样的钢包冶金工艺的开发为优化生产流程创造了有利条件。
表1 钢铁冶金生产工艺的变革 生产流程 1960年 1990年 1995年 特性 炼铁 高炉 高炉与铁水预处理 高炉及铁水预处理 去除P、S、Si 炼钢 平炉、电炉、kaldo 顶底复吹转炉 顶底复吹转炉、超高功率 降低C 电弧炉 钢包冶金 无 RHOB、VAD、VOD、 RHOB、LFV、喷粉、 去除S、P、O、 CAB等 喂丝等 N、C 浇注 钢锭 连铸 连铸及薄板坯连铸 控制偏析与显 微组织、弥散 TIN质点 轧钢 重新加热 热装热送,控轧 热装热送、控轧 合金元素充分溶解 轧后处理 空冷或热处理 加速冷却或直接淬火 加速冷却或直接淬火 合金元素充分溶解
对于微合金钢,目前需要对连铸和控轧控冷两个环节给予特别关注。 现在,几乎所有的低合金高强度钢种,包括微合金钢,都可用连铸生产。为了得到无缺陷和化学成分及内部组织均匀的连铸坯,需采用现代工艺技术所能提供的一切可能措施。如采用钢流保护系统,以防止浇注过程中钢水吸氧和氮。采取浸入式水口或氩气保护,有效地防止氧化烧损。必须妥善选择钢包用耐火材料,以保证钢液的纯净度。 微合金钢连铸需注意的主要问题是铸坯表面在弯曲和随后矫直过程中容易产生横裂。这是由于奥氏体中的析出使热塑性低谷的宽度和深度增加所引起的。为防止裂纹,从化学成分上需把铌、铝这样的元素降低到为获得最终性能所需的最低含量,从工艺上需调整二次冷却,使板坯在变曲时的表面和边部的温度避开钢的热塑性低谷区。 近所来,连铸微钛处理钢引起人们的特殊兴趣。由于连铸冷却的特殊条件,能够生成弥散的TIN夹杂物,对阻止奥氏体晶粒细化有很强的效果。 薄板坯连铸连轧新工艺正逐渐成熟。快速冷却有诸如减少偏析、改变夹杂物性质及形态和抑制某些析出等特点。有必要针对这些特点开展相应的研究和开发工作。 虽然人们早已看到降低轧制终了温度能够提高钢材强度和改善韧性,但由于低温轧制时轧机需承受较大的载荷,而且冷却到一定的低轧制温度时,需要增加道次间的停留时间,因而这一工艺未获得广泛应用。由于微量铌对奥氏体再结晶有强烈的抑制作用,使含铌钢在相对较高的温度下进行控制轧制,从而使这项工艺得到有效的应用,而且打开了应用铌钢的局面。轧后加速冷却或所谓控制冷却工艺不仅影响转变温度,而且能够抑制转变前的奥氏体晶体粒长大,可以进一步减小晶粒。控制冷却主要是控制析出温度,使其在较低温度进行,因此,终冷温度十分关键。控制冷却速度和终冷温度可以得到不同的显微组织,从而获得不同的强韧性的配合。铌、钒、钛或者复合微合金化的钢都可利用这个原理。 由上所述,微合金钢的生产决不是在碳素钢基础上加点合金就能收到改善质量,提高性能的效果,没有相应的工艺,优化的制度,就不可能收到预期的效果,甚至带来不良的影响。要根据工厂的装备条件,根据微合金化原理,选择并优化工艺制度,这是当前推广微合金化技术过程中需要遵循的原则。