连铸方坯轻压下内裂纹形成研究
第六讲 连 铸 坯 裂 纹 控 制

连 铸 坯 质 量 控 制
北 京 科 技 大 学 冶 金 学 院
3 连铸坯表面裂纹形成及防止
3.1铸坯表面裂纹类型
◆ 纵裂纹 ◆ 横裂纹 ◆ 星形裂纹 ◆ 皮下气孔
图3-1 铸坯表面裂纹示意图
连 铸 坯 质 量 控 制
北 京 科 技 大 学 冶 金 学 院
3.2表面纵裂纹
3.2.1定义 沿拉坯方向,板坯表面中心位置或距边部10~15mm处产 生的裂纹。裂纹长10~1500mm,宽0.1~3.5mm,深<5mm。 3.2.2产生原因 在结晶器弯月面区(钢液面下170mm左右),钢凝固在 固相线以下发生δ→γ转变,导致凝固厚度生长的不均匀性, 由于热收缩使坯壳产生应力梯度,在薄弱处产生应力集中, 坯壳表面形成纵向凹陷,从而形成纵向裂纹。 可以说,结晶器弯月面区凝固壳厚度不均匀性是产生表 面纵裂纹的根本原因,在二冷区铸坯裂纹进一步扩展。
连 铸 坯 质 量 控 制
北 京 科 技 大 学 冶 金 学 院
2.2 产生内裂纹的判据
内裂纹的产生主要决定于凝固面前沿所能承受的应力应 变。当凝固前沿承受的应变ε 超过临界应变ε 临值,则 产生裂纹。 不同作者实际测定ε临值如下:
C,% 0.15 0.17~0.28 0.16~0.23 0.13~0.15 0.13 0.18~0.24 0.42 ε(应变) 0.2~0.5 3.2~3.6 0.5~1.0 3.2~3.3 0.45~0.56 0.32~0.62 1.0~1.5
液面波动<±5mm,纵裂纹最少(图3-8); 液面控制方式对纵裂影响如图3-9。
图3-8 结晶器液面波动对纵裂的影响
图3-9 液面控制方式对纵裂的影响
连 铸 坯 质 量 控 制
25 安钢连铸小方坯裂纹形成的原因和预防措施

加强炉机之间的现场生产协调 ,加强对转炉 冶炼周期 、连铸钢水传递时间 、温度命中率的管 理 ,为连铸稳定拉速创造条件 ,最大限度地减少等 钢水或钢水温度高造成的低速浇铸 。根据我厂生 产条件 , 2000 年 8 月制定出转炉和连铸温度制 度 ,见表 1 。
表 1 转炉和连铸温度制度 转炉出钢 出钢后大包 吹氩 、喂丝后 中包温度 温度/ ℃ 温度/ ℃ 大包温度/ ℃ / ℃ 第一炉 1 670~1 690 1 630~1 650 1 610~1 630 1 540~1 560 连浇炉 1 640~1 660 1 600~1 620 1 580~1 600 1 520~1 540
Keywords continuous casting billet crack precautionary measure
1 前 言
裂纹是连铸坯常见缺陷之一 ,在连铸坯中裂 纹是发生在铸坯表面和凝固前沿 ,有表面裂纹和 内部裂纹之分 。但无论表面裂纹还是内部裂纹的 产生 ,均是由作用在铸坯上的应力和应变引起的 , 而产生应力和应变的因素是热负荷和机械负荷 , 对铸坯产生热负荷和机械负荷的原因是多种多样 的 ,因此 ,形成裂纹的原因也是极其复杂的 。归纳 起来主要有 :钢水成分 、连铸工艺及参数 、保护渣 、 连铸设备等 。不同的工厂 、不同的铸机在不同的 阶段 ,由于条件不同 ,每种因素对铸坯裂纹产生影 响的程度也不同 。
大方坯连铸角部纵裂纹缺陷控制技术研究

参数 组合式 等腰直角 25mm×45°
正弦 2900~3300L/Min
≥350Gs 270m3/h 0.30~0.45mPa.s 1045~1090℃ 0.50~0.90m/min
收件日期:2019-05-07 作者简介:石鹏,男,工程硕士,助理工程师,从事连铸工艺技术研究.
· 16 ·
特钢技术
Keywords: heavy rail steel, bloom, corner defects, chamfering size of mold, mould flux
引言
攀钢六机六流大方坯连铸机以生产重轨钢等 高碳钢为主,代表钢种有 U75V 和 U71Mn。最初设 计采用组合式结晶器,投产后出现频率较高的表面 缺陷,包括角部纵裂纹和凸包两类,轧制钢轨后,将 在角部对应的轨头轨底位置,演变成沿轨制方向纵 向细微裂纹,影响钢轨的抗疲劳性能,带来轨头掉 块风险。本文分析了重轨钢铸坯倒角缺陷产生的 原因,提出对倒角参数和结晶器保护渣优化的针对 性措施,取得良好效果。攀钢 1#大方坯连铸机由 奥钢联设计和制造,关键工艺设备及参数表 1。
Shi Peng
(Pangang Group Steel and Vanadium Co., Ltd.,Panzhihua,Sichuan 617022)
Abstract: Aiming at the chamfering cracks and convexity defects of high carbon steel due to improper heat transfer control of the solidified shell in the mold, the design of mold chamfering parameters and the performance of the slag were optimized. The experimental results showed that the use of an equilateral right angle with a chamfer of 10 mm × 45 ° and an improved mold mold slag with low viscosity and low melting point were beneficial to the heat transfer control and lubrication between the mold and the solidified bloom and so corner cracking defects were elimi⁃ nated, and the convexity defects were greatly reduced; the proportion of heavy rail steel with corner defects was re⁃ duced from 2.74% before improvement to 0.32%. The damage level and risk of defects were well controlled, and the cost of mold was also reduced.
连铸轻压下技术
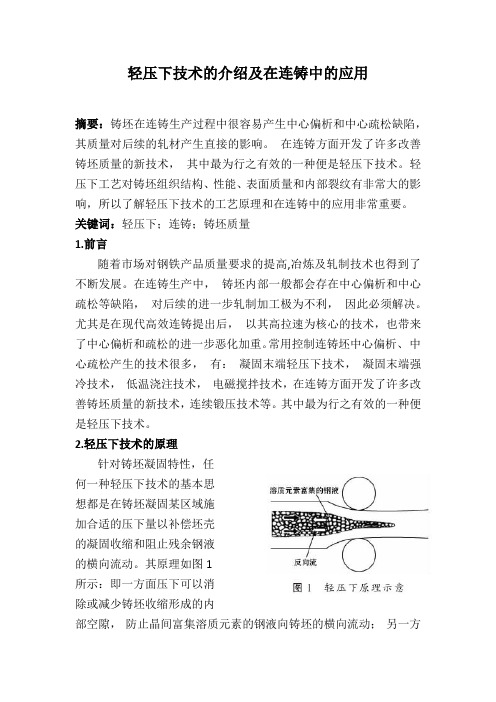
轻压下技术的介绍及在连铸中的应用摘要:铸坯在连铸生产过程中很容易产生中心偏析和中心疏松缺陷,其质量对后续的轧材产生直接的影响。
在连铸方面开发了许多改善铸坯质量的新技术,其中最为行之有效的一种便是轻压下技术。
轻压下工艺对铸坯组织结构、性能、表面质量和内部裂纹有非常大的影响,所以了解轻压下技术的工艺原理和在连铸中的应用非常重要。
关键词:轻压下;连铸;铸坯质量1.前言随着市场对钢铁产品质量要求的提高,冶炼及轧制技术也得到了不断发展。
在连铸生产中,铸坯内部一般都会存在中心偏析和中心疏松等缺陷,对后续的进一步轧制加工极为不利,因此必须解决。
尤其是在现代高效连铸提出后,以其高拉速为核心的技术,也带来了中心偏析和疏松的进一步恶化加重。
常用控制连铸坯中心偏析、中心疏松产生的技术很多,有:凝固末端轻压下技术,凝固末端强冷技术,低温浇注技术,电磁搅拌技术,在连铸方面开发了许多改善铸坯质量的新技术,连续锻压技术等。
其中最为行之有效的一种便是轻压下技术。
2.轻压下技术的原理针对铸坯凝固特性,任何一种轻压下技术的基本思想都是在铸坯凝固某区域施加合适的压下量以补偿坯壳的凝固收缩和阻止残余钢液的横向流动。
其原理如图1所示:即一方面压下可以消除或减少铸坯收缩形成的内部空隙,防止晶间富集溶质元素的钢液向铸坯的横向流动;另一方面,压下可以使液芯中溶质元素富集的钢液沿拉坯方向反向流动,使溶质元素在钢液中重新分配,从而改善中心偏析情况。
在连铸坯凝固过程中,对铸坯施加外力,补偿凝固收缩并破碎已经形成的“晶桥”,使得铸坯内的钢水可以自由地进行流动,就可以最大程度地减少中心偏析和疏松,这就是轻压下技术的工艺原理。
3.轻压下技术的发展及分类3.1轻压下技术的发展轻压下技术始于20世纪70年代末、80年代初,是在20世纪70年代辊缝收缩技术的基础上发展而来的。
目前,连铸坯的轻压下有两种含义:在铸坯凝固末端处进行的轻压下;离凝固末端较远处进行的轻压下,又称带液芯轻压下。
连铸坯角部皮下横裂纹成因分析及控制技术

连铸坯角部皮下横裂纹成因分析及控制技术【摘要】铸坯角部皮下横裂纹是常见的生产缺陷,本文结合济钢中厚板厂连铸机生产实践实际,分析了角部皮下横裂纹形成原因,研究了铸坯凝固行为、二冷工艺、Al和N元素含量等重要因素对角部裂纹率的影响作用,并提出了相应的改进措施。
【关键词】连铸角部皮下横裂纹1 前言进入二十一世纪以来,随着我国交通运输、石油化工、重型机械、海洋工程、核电军工等行业的迅猛发展,从而大力推动了低合金、高强度等微合金钢的炼钢、轧钢工艺技术发展。
我厂生产的铸坯经常出现角部皮下横裂纹,给产品质量带来及极大的影响,为此我们对各个工艺环节进行了深入地研究,通过控制好钢水的Als含量、全程做好保护浇注等措施,有效地控制了铸坯角部产生横裂纹,从而确保了产品质量。
2 铸坯皮下横裂纹的形成机理及形态2.1 铸坯皮下横裂纹的形成机理钢水在结晶器的凝固过程中,弯月面附近液渣在结晶器振动作用下缓慢流入铜板和坯壳间的气隙中,初凝坯壳在振动和钢水静压力的共同作用下开始变形,进而形成铸坯振痕。
由于铸坯坯壳角部收缩相对显著,使得铸坯角部的振痕谷底处初凝坯壳的传热速度下降,导致该区域的奥氏体晶粒长大,S、P偏析加剧,从而降低了钢的高温强度。
与此同时,钢中微合金元素(如铝、硼、铌等)极易与钢中的碳、氮元素相结合,在一定条件下,将在奥氏体晶界析出碳氮化物。
而振痕波谷处的晶粒粗大,将加剧碳氮化物的析出,当铸坯受到应力作用时,极易产生应力集中,最终形成横向裂纹。
2.2 铸坯角部皮下横裂纹的形态铸坯角部皮下横裂纹是板坯常见的一种铸坯缺陷,在铸坯上呈“跨角裂”形式。
角部横裂纹往往发生于铸坯角部的晶间,难以在线检查,只能将铸坯下线通过火焰清理的方式进行挽救。
连铸板坯角部皮下横裂纹的特点如图1所示。
3 铸坯皮下横裂纹的成因分析3.1 Als、N含量的影响钢中Al、N含量对铸坯角部皮下横裂缺陷有较大影响,Al、N含量越高,铸坯裂纹敏感性越高,角部横裂纹率越高,这是因为:在凝固的过程中Al易与N元素形成氮化物并在晶界析出,促进板坯角部横裂纹的产生,在晶界的析出物越细小,析出物体积百分比越高,对钢的热塑性恶化越严重。
连铸方坯裂纹的改善

3.2 优化和改进炼钢工艺
根据不同的结晶器短边铜板厚度设定不同的短边冷 却水流量,对窄边进行缓冷。由于原水不脱硬,造成结 晶器铜板结垢严重以及二冷喷嘴堵塞。对循环系统进行 了化学清洗,加入分散阻垢剂,并加装静电阻垢器,减 缓铜板结垢速度对污循环系统也进行了清洗和加药处理, 以改善喷嘴堵塞问题。 对温度制度进行调查分析。推行中间包温度命中率 管理,通过对炼钢、连铸过程温度、时间流的控制水平 进行调查分析,完善了各土序的温度控制基准,加强了 对钢液温度、成分、传搁时间三命中管理。
2.1 设备因素
结品器使用到后期,铜板变形会造成两边之间 的间隙过大。这样,易在间隙中挂冷钢,增加角部 的应力,产生微裂纹。结品器的锥度正常情况下应 为士 0.5 mm,但实际测量有时为 11.1 mm。由此 可以推测结品器不垂直,当浇注过程中结品器振动 不在垂直方向上时,会增加坯壳的应力,增加产生 裂纹的几率。 扇形段之间对中不良。在设备维修对弧时,发 现个别扇形段之间辊子在使用一段时间后错位达 1.0—2.0mm, 这就增加了铸坯通过时的应变,增加 裂纹发生的几率。 拉坯阻力大。由于润滑不良,辊 子不转及断辊现象时有发生,万向轴断的现象也很 多。
由于伴随包晶反应出现较大的体积变化、线 收缩、凝固收缩和钢液静压力的不均衡作用,使 薄的坯壳表面粗糙、折皱,严重时形成凹陷。凹 陷部位凝固冷却比其它部位慢,组织粗化在热应 力和钢液鼓胀力的作用下,凹陷处应力集中,产 生微裂纹 。
2 工艺与操作因素分析
2.1 2.2
设备因素 工艺因素 2.2.1 拉速的影响 2.2.2 钢液过热度
4 结论
连铸坯的裂纹都是在较高温度下发生并扩 展形成的,主要在热作用和机械作用下坯壳凝 固薄厚不均强度不大,从而在应力作用下发生 断裂。在设备改造上,对二冷水实行动态控制, 铸坯得到合理均匀的冷却,渐进矫直对控制内 裂形成的作用十分明显。在良好的设备下,物 流、物性管制的好坏直接影响连铸的稳态浇注 从而影响铸坯质量。中间包温度命中率的提高 为减少方坯裂纹创造了良好条件。
贵钢低碳高硫系易切钢连铸小方坯内裂成因

中圈分类号 : 聊
. 文献标识码 : 3 B
文章编号:1 68 (o 0 唧 10 86 2 加)6一 12—
.3 0
Th ay i f Bi e n a ti t r a a k f r L w-ar o u p u e An l s o l tCo c s e n lCr c o o c b n S l h r s l n Fr e c t n te n Gu y n p d ̄ S e l e -ut g S e l ia g S e i i te
8 I + , 围绕 8 枝 晶形成 ^ 包层 , y 构成 6 L+ 的 3 +
相界面 ; 温度继续降低 , 相 通过碳原 子在相 界面上 扩散长
大, 不断消耗 8 相和液相 , 直到全部变成 相为止 。 当发 生 8 +L一 转 变 时 , 收 缩 系 数 为 : . 线 9 8×
Ke r s f e c t n te ; tr a ca k p r e t ; e i ei ins mo l m u d l biain p w e y wo d  ̄ e ut g s li en r c ; ei ci p r e t p o t; ud; l r t o d r r i e n l t c t c o u c o
产的小方坯低碳高硫系易切钢 中 , 内裂是最主要 的质量缺陷。
经过理论及检验分析发现 , 内裂成 因是多方面 的。
l 连铸机工艺参数
铸坯断面/ ×nI 舢 1 r l
弧形半 m 流数
1~  ̄ 而未发 生 包 晶反 应 的 8 的线 收 缩 系数 为 : 0 /C, 相 2×
连铸坯角部横向裂纹的形成机理与定量评估_赵晗
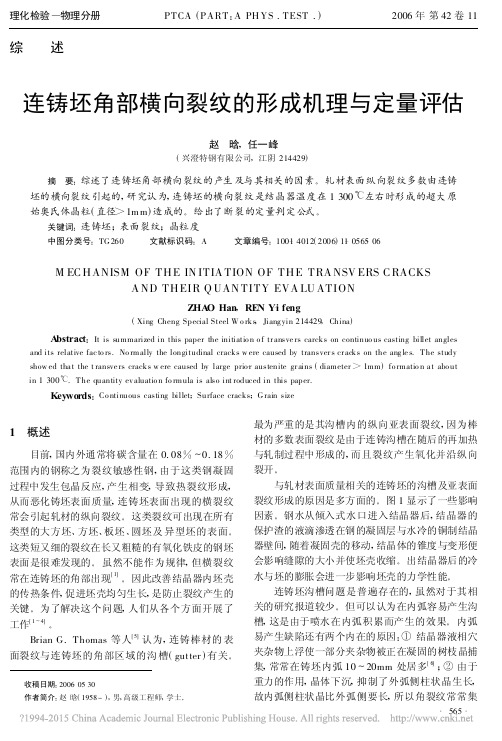
理化检验—物理分册PTCA(PART:A PH YS.TEST.)2006年第42卷11综 述连铸坯角部横向裂纹的形成机理与定量评估赵 晗,任一峰(兴澄特钢有限公司,江阴214429)摘 要:综述了连铸坯角部横向裂纹的产生及与其相关的因素。
轧材表面纵向裂纹多数由连铸坯的横向裂纹引起的,研究认为,连铸坯的横向裂纹是结晶器温度在1300℃左右时形成的超大原始奥氏体晶粒(直径>1m m)造成的。
给出了断裂的定量判定公式。
关键词:连铸坯;表面裂纹;晶粒度中图分类号:TG260 文献标识码:A 文章编号:1001-4012(2006)11-0565-06M EC HANISM OF THE IN ITIA TION OF THE TRA NSV ERS C RACKSA ND THEIR Q UAN TITY EVA LU ATIONZHA O Han,REN Yi-feng(Xing Cheng Special Steel W o rks,Jiang yin214429,China)A bstract:It is summarized in this paper the initiatio n o f tr ansve rs carcks on continuo us casting billet anglesand its relative fac to rs.No rmally the longitudinal cracks w ere caused by transver s cr acks on the ang le s.T he study show ed tha t the t ransve rs cracks w ere caused by large prio r-austenite gr ains(diameter>1mm)fo rmatio n a t abo ut in1300℃.T he quantity ev aluatio n fo rmula is also int roduced in this paper.Keywords:Co ntinuous casting billet;Surface cracks;G rain size1 概述目前,国内外通常将碳含量在0.08%~0.18%范围内的钢称之为裂纹敏感性钢,由于这类钢凝固过程中发生包晶反应,产生相变,导致热裂纹形成,从而恶化铸坯表面质量,连铸坯表面出现的横裂纹常会引起轧材的纵向裂纹。