隧道窑烧结砖焙烧与干燥过程中的问题分析
隧道窑的焙烧
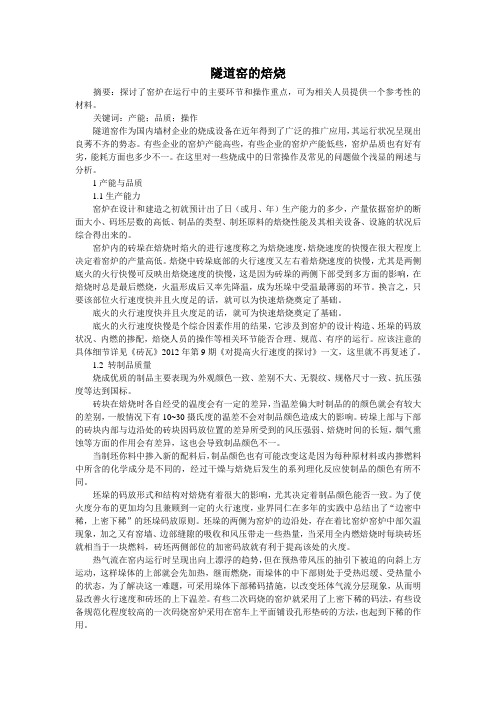
隧道窑的焙烧摘要:探讨了窑炉在运行中的主要环节和操作重点,可为相关人员提供一个参考性的材料。
关键词:产能;品质;操作隧道窑作为国内墙材企业的烧成设备在近年得到了广泛的推广应用,其运行状况呈现出良莠不齐的势态。
有些企业的窑炉产能高些,有些企业的窑炉产能低些,窑炉品质也有好有劣,能耗方面也多少不一。
在这里对一些烧成中的日常操作及常见的问题做个浅显的阐述与分析。
1产能与品质1.1生产能力窑炉在设计和建造之初就预计出了日(或月、年)生产能力的多少,产量依据窑炉的断面大小、码坯层数的高低、制品的类型、制坯原料的焙烧性能及其相关设备、设施的状况后综合得出来的。
窑炉内的砖垛在焙烧时焰火的进行速度称之为焙烧速度,焙烧速度的快慢在很大程度上决定着窑炉的产量高低。
焙烧中砖垛底部的火行速度又左右着焙烧速度的快慢,尤其是两侧底火的火行快慢可反映出焙烧速度的快慢,这是因为砖垛的两侧下部受到多方面的影响,在焙烧时总是最后燃烧,火温形成后又率先降温,成为坯垛中受温最薄弱的环节。
换言之,只要该部位火行速度快并且火度足的话,就可以为快速焙烧奠定了基础。
底火的火行速度快并且火度足的话,就可为快速焙烧奠定了基础。
底火的火行速度快慢是个综合因素作用的结果,它涉及到窑炉的设计构造、坯垛的码放状况、内燃的掺配,焙烧人员的操作等相关环节能否合理、规范、有序的运行。
应该注意的具体细节详见《砖瓦》2012年第9期《对提高火行速度的探讨》一文,这里就不再复述了。
1.2 转制品质量烧成优质的制品主要表现为外观颜色一致、差别不大、无裂纹、规格尺寸一致、抗压强度等达到国标。
砖块在焙烧时各自经受的温度会有一定的差异,当温差偏大时制品的的颜色就会有较大的差别,一般情况下有10~30摄氏度的温差不会对制品颜色造成大的影响。
砖垛上部与下部的砖块内部与边沿处的砖块因码放位置的差异所受到的风压强弱、焙烧时间的长短,烟气熏蚀等方面的作用会有差异,这也会导致制品颜色不一。
烧成窑炉、干燥窑走砖的影响因素分析

烧成窑炉、干燥窑走砖的影响因素分析作者:程建马梦兰来源:《佛山陶瓷》2020年第08期摘要:随着建陶行业产品不断更新变化,对窑炉设备的要求也愈来愈高。
本文从干燥窑、烧成窑炉两方面对走砖的影响因素进行分析,并对影响走砖稳定的窑炉技改提出了相应建议,以期与广大生产技术人员探讨,促进陶瓷烧成窑炉、干燥窑走砖稳定。
关键词:烧成窑炉;干燥窑;传动走砖;影响因素1 前言近年来,随着陶瓷大板的流行,瓷砖规格越做越大,其对生产设备也提出了更高的要求。
尤其是起着关键作用的窑炉,必须要重新投资或技改,窑炉的长度和窑炉内宽在不断地加长与加宽,对窑炉传动走砖的要求也愈来愈高。
而目前陶瓷行业的部分窑炉、干燥窑都是在21世纪前十年投入生产的,窑炉、干燥窯传动配件也相对老旧,直接影响了窑炉、干燥窑走砖的稳定性。
因此,本文从干燥窑、窑炉两方面对走砖影响因素进行分析。
2 干燥窑走砖影响因素分析干燥窑传动走砖要好,需从以下几个因素考虑:2.1 干燥窑铁棒对走砖的影响以目前行业上常见的双层干燥窑为例,一般内宽3500 mm左右,走3片800 mm×800 mm 或4片600mm×600 mm规格的瓷砖。
干燥窑投产前需做2步工作:①对铁棒进行校直。
目的是保证砖坯运行过程中,铁棒不甩动,进而保证走砖的平稳及避免砖坯相撞;②对铁棒表面进行打磨。
打磨的作用是清理铁棒上的棒钉,棒钉的存在会影响干燥砖坯的正常运行,存在发生裂砖的风险。
目前行业上的瓷砖越做越大,越做越厚,对干燥铁棒厚度要求也更大。
常规产品干燥铁棒厚度在3.8 mm左右,而生产厚砖则需加厚到4.2 mm,以满足干燥窑平稳走砖。
2.2 传动设备对走砖的影响传动安装完成后,需对干燥窑整体传动水平进行调整,以保证传动在一个水平面上平稳运行,特别是要检查每节箱体连接处的传动水平,避免因传动高低落差而造成干燥机械裂砖。
部分场地因干燥窑基础下沉,需每年对干燥传动水平进行调整,保证干燥窑走砖的平稳及减少机械裂砖。
如何控制陶瓷成型过程中的烘干和烧结速度

如何控制陶瓷成型过程中的烘干和烧结速度陶瓷是一种广泛应用于日常生活和工业生产的材料,它具有优良的耐热、耐腐蚀和电绝缘性能。
而在陶瓷制作过程中,烘干和烧结是两个至关重要的环节。
本文将探讨如何控制陶瓷成型过程中的烘干和烧结速度,以确保最终产品的质量和性能。
一、烘干速度的控制烘干是将湿陶瓷制品中的水分蒸发掉的过程,它的速度直接影响到成品的质量。
过快的烘干速度可能导致陶瓷制品表面龟裂,而过慢则会延长制作周期。
因此,控制烘干速度是非常重要的。
首先,要合理安排烘干的温度和湿度。
温度过高会导致表面过快蒸发而内部水分无法及时释放,从而引起龟裂;湿度过高则会延缓水分的蒸发速度。
因此,需要根据具体的陶瓷材料和制品形状,合理调节烘干温度和湿度,以达到最佳的烘干效果。
其次,要注意烘干的均匀性。
陶瓷制品在烘干过程中,表面和内部的水分蒸发速度可能存在差异,导致制品变形或龟裂。
为了解决这个问题,可以采取逐渐升温的方式进行烘干,让水分逐渐从内部向外部蒸发,以保持制品的形状和完整性。
二、烧结速度的控制烧结是将烘干后的陶瓷制品在高温下形成致密结构的过程,也是决定陶瓷制品性能的关键环节。
烧结速度的控制涉及到温度、时间和气氛等多个因素。
首先,要合理选择烧结温度。
烧结温度过低会导致陶瓷制品的致密性不足,性能较差;而温度过高则可能引起过烧现象,使制品变形或烧损。
因此,需要根据陶瓷材料的烧结特性和要求,选择适当的烧结温度。
其次,要控制烧结时间。
烧结时间过短会导致陶瓷制品的致密性不够,性能不稳定;而时间过长则可能造成能源浪费和制品烧损。
因此,需要根据具体情况,控制烧结时间在合理范围内。
此外,烧结过程中的气氛也对烧结速度有影响。
不同的陶瓷材料对气氛的要求不同,有些需要在氧化气氛下烧结,有些则需要在还原气氛下烧结。
因此,需要根据具体材料的要求,选择合适的气氛条件,以提高烧结速度和陶瓷制品的质量。
总之,控制陶瓷成型过程中的烘干和烧结速度是保证产品质量的关键。
烧结砖隧道窑的质量问题分析
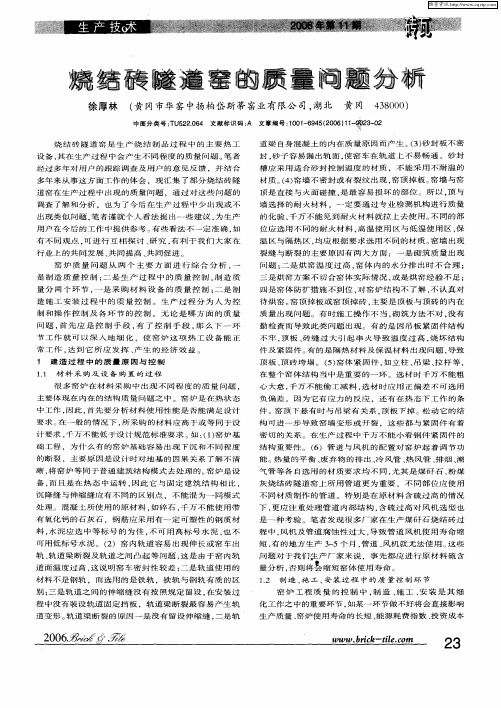
问题 : 是 烘窑温 度过高 , 体 内的水 分排 出时不合 理 ; 二 窑
三 是 烘窑 方 案不 切 合 窑 体 实 际 情 况 , 是 烘 窑 经 验 不 足 ; 或
四 是 窑 体 防 扩 措 施 不 到 位 . 窑 炉结 构 不 了解 , 认 真 对 对 不
多年 来 从 事 这 方 面工 作 的体 会 , 现 汇 集 了 部 分 烧 结 砖 隧
道 窑 在 生 产 过 程 中 出 现 的 质 量 问 题 .通 过 对 这 些 问 题 的 调 查 了 解 和 分 析 . 也 为 了 今 后 在 生 产 过 程 中 少 出 现 或 不
墙 选择 的 耐 火材 料 一 定 要 通 过专 业 检 测 机 构 进 行 质 量
维普资讯
砖 隧 道 饔 哟 量
烧 结 砖 隧 道 窑 是 生 产 烧 结 制 品 过 程 中 的 主 要 热 工 设 备 , 在 生 产 过 程 中会 产 生 不 同程 度 的质 量 问题 。 者 其 笔
经 过 多 年 对 用 户 的跟 踪 凋 查 及 用 户 的 意 见 反 馈 ,并 结 合
件 及 紧 固件 。 的 是 隔 热 材 料 及 保 温 材 料 出 现 问 题 , 致 有 导 顶板 、 砖 垮塌 。() 体紧 固件 , 立柱 、 梁 、 杆等 , 顶 5窑 如 吊 拉 在 整个 窑 体 结 构 当 中是 重 要 的一 环 。 选 材 时 千 万 不 能 粗 心 大 意 , 万 不 能 偷 工 减 料 , 材 时 应 用 正 偏 差 不 可 选 用 千 选 负 偏 差 ,因 为它 有 应 力 的 反 应 ,还有 在 热 态 下 工 作 的 条
三种一次码烧“烘烧连通窑”利弊谈(深度好文)

三种一次码烧“烘烧连通窑”利弊谈(深度好文)现代烧结砖瓦生产线必备的热工设施有干燥室(俗称干燥窑、干燥洞、烘干窑、烘干洞等)和焙烧窑,二者缺一不可。
干燥室和焙烧窑的种类很多,各具特征,优缺点并存,适用条件各异。
设计和新建一条塑性挤出成型的烧结砖瓦生产线,必须根据原料、燃料、产量、产品品种、生产装备、工艺技术及其他生产条件的不同,综合考虑各种相关因素,慎重选用相适宜的干燥和焙烧工艺,不可盲目地随意选用。
特别是对一次码烧“烘烧连通窑”的选用,更得谨而慎之。
1. 什么是一次码烧“烘烧连通窑”烧结砖瓦生产的基本工艺过程依次可分为原料制备、陈化、制坯、码坯、干燥、码窑、焙烧几个阶段。
合理的烧结砖瓦生产线,应该是通过相关的物料输送设备,例如铲运机、输送机、运坯车、摆渡车、步进机、顶车机等,把这几项生产工序按工艺要求合理的组成,形成连贯的、完整的、平衡顺畅的流水生产线。
其中对码坯、干燥、码窑、焙烧工序分别有二次码烧工艺和一次码烧工艺(含“一次半码烧”)之分。
二次码烧工艺是先把成型后的湿坯按干燥工艺要求码放在干燥车(或其他干燥设备) 上进入干燥室脱水,干燥成为干坯后,再把干坯按焙烧工艺要求,再次码放到焙烧窑焙烧成合格产品。
由于两次码坯适用的热工设备不一样(一个是干燥室,另一个是焙烧窑),码坯的方式也不一样,码坯的目的和效果也不一样,,两次码坯相应的工艺要求和工艺制度更不一样。
这种工艺流程较长,机械化自动化程度高,需用设备较多,一次性投资大,但对原料的工艺性能要求不高,可适用各种原料以及制品,更适合大块、多孔、薄壁的制品。
一次码烧工艺是按同时满足干燥工艺和焙烧工艺要求,将成型湿坯一次码放到相应的载坯设备上(比如窑车),然后将码好湿坯的载坯设备先进入干燥室脱水干燥成为干坯后,随原载坯设备脱离干燥室,再到焙烧窑进行焙烧。
一次码烧坯体的码垛方式要求必须同时满足干燥室与焙烧窑的要求,但干燥室和焙烧窑一般是两个独立分开的不连通的热工设施,各自按不同是工艺制度和生产要求独立运行。
煤矸石烧结砖隧道干燥室的干燥控制

下 一 步 等 速 干 燥 做 准 备 。等 砖 坯 内外 温 度 升 到一 定 阶段 时 , 砖坯 恰好抵 达 等速 1 二 燥 阶段 的部 位 。
1 . 2 等速 干燥 阶段
砖 坯 在预 热 阶段 主 要是 加 热坯 体 , 只有少 部分 的 自由水 排 出 , 大部 分 的 白南水 是 在等 速 十燥 阶段 排 出 的 。高 湿 的 热坯 通 过 预热 带 后 继 续 吸 收 _ _ F 燥 热风 的热 量 , 砖 坯表 面 的脱 水 速度 与砖 坯 内部 水 分 移 向表 面 的 速度 趋 向一 致 , 使 砖 坯 内外 同步 脱 水 ,
而 比 自由水 蒸 发 要 困难 的多 , 在 同一 千 燥 条什 下 ,
来, 通常分为 4 个 阶段 : 即预热、 等速干燥 、 降速 干
燥 和平 衡 干燥 四个 阶段 。各 个 阶 段 担 负着 不 同 的
干燥 速 度大 为 减慢 , f燥 收缩 此 时也 基本 停 止 。这 个 阶段 可 以 适 当提 高 热 风 温 度 , 降 低 窑 内 相 对 湿
结果引起坯体着火 , 造 成 干燥 室 顶 塌 陷 , 使 生 产 停
缩 的快 , 内层 收 缩 的慢 , 由于 内外 收缩 不 一致 , 造 成
内应 力 , 当 这 种 内应 力 大 于 泥料 的弹 性 系数 时 , 就 会 产生 干燥 裂 纹 。 因此在 预 热 阶段 升温 不 要过 快 , 此 阶 段 的 主 要 任 务是 升 温 , 而 不是 脱 水 , 升温 是 为
同步 收 缩 , 因此 不 会 产 生 裂 纹 。砖 坯 在 此 阶段 , 只
脱 水 不再 升 温 。在 这 个 阶 段 要 合理 调 整送 热 和 排
隧道窑常见问题分析探讨
工程技术科技创新导报 Science and Technology Innovation Herald431 合理的烧成制度烧成制度是隧道窑生产的核心内容,制定了合理的烧成制度不仅能够保证烧成质量,并且实现快速烧成,以达到高产、低消耗的目的。
制定烧成制度应考虑的因素:(1)根据制坯原料的化学成分和矿物成分可以判断烧成温度和烧结温度范围,以及在焙烧过程的不同温度阶段分解气体量的多少。
(2)根据差热曲线了解坯体吸热和放热情况,再通过综合判断,可确定制品各阶段极限升温速率和最大供热速度。
(3)窑炉特点结构,码窑图,燃料种类,供热体积大小以及调节的灵活性。
(4)调查了解同类原料和产品生产和实验资料。
烧结砖焙烧时间,相同原料在不同的烧成制度下,烧成周期不同。
长时间的焙烧,不仅增加了燃料及人力消耗,而且影响了窑炉及其附属设备的有效利用,牵制了生产能力的发挥。
2 降低系统内气流阻力损失系统内气流阻力损失越大,电量消耗越多。
不但要增加动力设备的能力,增加生产成本,而且限制了窑的产量。
降低系统阻力损失意味着节约电能。
降低系统阻力可采用以下措施见图1。
(1)砖坯在窑车上垛码得规范。
窑内坯垛码得规范,通道畅通,其长度方向阻力可降至约8~10 Pa/m;如果坯垛码得不规范,通道不通畅,其长度方向阻力将成倍增加。
坯垛适当稀码则空隙大、阻力小,在同样抽力下,有利于气体流过,可以快速烧成。
在这方面,机械码坯优于人工码坯。
(2)选取适当气流流速。
流速大,则气流摩擦阻力和局部阻力都相应增大;流速小,则降低烧成速度,进而影响产量。
应选取适当流速,一般用风机排烟时的流速取8~12 m/s。
另外,考虑建设成本,排烟烟囱超过60 m为宜,越高的烟囱提供的负压抽力越大。
(3)当烟道断面需要变化时,应用逐步变化代替突然变化,用圆滑转弯代替直角转弯,用缓慢转弯代替急转弯,以减少不必要的阻力损失。
(4)烟道内部光滑些可以减少气流摩擦阻力系数。
(5)尽量缩短管道长度。
技术|干燥窑常见缺陷探讨及解决
技术|干燥窑常见缺陷探讨及解决干燥窑产生的缺陷主要有开裂、滴水和落脏。
开裂有左右边裂、前后边裂和面裂3种。
一、坯体面裂产生原因:干燥高温高湿段的排湿速度过快,造成坯体中间与周边的收缩不均匀,产生面裂。
措施:减慢高温高湿段的排湿速度,缩小坯体传热造成的收缩不均。
控制要点:高温高湿段的时间、等速段的排湿速度、等速段的排湿时间。
二、坯体边裂的控制1、传动水平情况,干燥窑箱体节间传动系统的水平差异,会直接导致坯体在干燥过程中的横裂或边裂。
2、这种开裂几乎都与干燥窑的前温不够密切相关。
干燥窑的进窑温度一般在200℃左右,最高的可以升到近300℃。
3、与干燥窑窑头的湿度不够高有关。
最好用高温高湿烟气。
用一级烟气,禁止用窑炉冷却余热烟气,如果烟气湿度不够,可以考虑在总管道处喷水雾增湿。
4、干燥窑高温高湿后段的排湿段长度、温度、抽湿闸板开度不合理,很多坯体开裂都出在这一段,操作员要根据坯体的特性,结合干燥窑的特点,制定出干燥曲线。
三、坯体前后边裂采用底进风、面侧抽结构的干燥窑,干燥介质的流向与辊棒平行,决定了坯体在干燥过程中,平行辊棒的前后边产生排水快慢、收缩先后的差异,若超过一定程度,就产生开裂。
在干燥窑前部加顶抽,可以有效解决该问题。
四、干燥窑滴水滴水主要出现于生产渗花砖产品、生产微粉砖时很少出现。
产生滴水的原因:1、砖面喷水,抽到干燥窑烟气的湿度过高。
2、干燥窑集中抽湿,局部湿度过高,导致过饱和冷凝滴水。
有的烧成窑炉的窑头也会出现滴水。
解决滴水的措施:(1)采用分散抽湿方式,避免局部湿度过高。
(2)窑头烟气排空一部分,不要全部抽到干燥窑。
(3)混合部分二级烟气到干燥窑头的一级烟气中,适当降低干燥空气的湿度。
注意二级烟气的混合量,不要产生烟气过干而出现坯体开裂。
(4)加大干燥窑内气体的流速。
(5)防止干燥窑内金属件直通窑外,湿热气体泄漏产生冷凝水通过金属件滴下来。
五、干燥窑落脏产生落脏的原因:1、风机积脏;2、供热的风管积脏;3、干燥窑窑底积脏;4、滴水也会导致落脏。
建设隧道窑应关注的几个问题
建设隧道窑应关注的几个问题(1)砌筑砖瓦焙烧窑炉和修建房屋不一样,它要求窑室密不透风。
砖是不会透风的,窑室内表面也不能抹灰(抹灰要脱落),因此,在国家相关的标准中,对砖瓦焙烧窑炉砌筑时的灰缝的质量都有明确规定。
在行业标准JC982—2005《砖瓦焙烧窑炉》和国家标准GB50211—2077《工业窑炉砌筑及验收规范》中都明确规定:当采用红砖时,直墙的灰缝宽度应小于5mm,拱顶的灰缝应小于3mm。
当采用耐火砖时,砖的灰缝宽度必须小于2mm。
灰浆必须饱满,对于水平灰缝,灰浆的饱满度应大于95%,竖直灰缝应大于85%。
为了保证灰缝宽度不超标和灰浆饱满度,砌筑窑用烧结普通砖的质量必须符合GB5101—2003中规定的一级品的质量要求,砌筑时不得沿用一般砌砖时的“摆砖”,而必须按照“一挤一揉三定位”的方法操作。
在铺好灰浆砌砖时应“一挤以保证灰缝厚度不超标;”二揉“挤出泥浆中的空气保证灰浆饱满度;三定位”使砌体符合规定尺寸。
为此,砌直墙时应计算后在砌;例如:直墙高度为1500mm,烧结普通砖的厚度为53mm,按允许最大灰缝宽5mm,没层砖的总高为53+5=58mm,用1500除以58,得25.7,如用25层砖墙高仅为1450mm,显然不行,如果砌26层砖当灰缝为5mm宽时,墙高为1508mm,只多出8mm,每条灰缝压缩0.32mm,即灰缝宽为4.68mm正合适,则该窑直墙应砌26层砖。
施工时应在每个砌筑段(通常以相邻两条膨胀缝之间为1个砌筑段,长度约5~10m)的两端按计算出的砌砖层数及设计高度,各砌1个砖垛,以此为基准拉线砌筑该段中间部分。
直墙的水平方向也应先计算出每段应该用多少块砖,以控制竖向灰缝宽度。
对于拱顶则应先在拱模上“预排”,在保证圆拱下方灰缝宽度小于3mm的条件下,决定一排拱的用砖块数。
对于耐火砖,为保证灰缝宽度小于2mm,其所用泥料的粒度应小于1mm,且应抹灰挤紧,以满足灰缝宽度和竖缝泥浆饱满度的要求。
浅谈隧道窑的一些故障与基本常识
浅谈隧道窑的一些故障与基本常识先说烘干房的问题:自然排潮的烘干房如果烘不干砖的原因,不外乎两种可能,送热溫度过低或送热风量过小!而风机排潮的烘干房出现回潮、塌坯,大多是因为送风量与排风量不平衡,特别是当送风量过于大于排风量时极易出现回潮、塌坯!我相信这都是窑师傅技术方面力所能及的!而有些问题与窑体的设计或改造的不合理有客观原因,比如有很多由自然排潮改造成风机排潮,改造得不合理,有的把排潮风机装在中间段,甚至有装在烘干房出坯口的方向,有的进坯口没装窑门,有的烘干房窑内的送热孔沒有重新规划改造等,各种低级错误都有……!当然,窑师傅要能够看见出问题,并提出简捷可行的改造方案。
关于烧道炸坯,通常是砖没有烘全干,但并不是没烘干就一定会炸坯,要用技术手段降低进坯囗的溫度,重新规划高温焙烧区的位置,把预热区前面多留几个车位作烘干区用。
关于内燃卡位的高配与低配问题:除了窑师傅掌握好合适的风速,更多地取决于窑体的保温效果、码坯等等各方面的因素。
最常见的一个耗卡位的问题有水箱安装位置不合理,好多砖厂把水箱安装在出砖口方向的笫六个甚至笫七个车位,一般90米长左右,3.6断面的窑子为例,六七车位一般还有七百度左右的溫度,也就是保温区,而水箱开水的温度也只有一百度,这就好比汽车水箱的散热作用,什么高温的砖只要一进到水箱底下的位置,该车位立马降温熄火,保溫区不保温势必影响焙烧区的温度,这种情况下就耗内燃!或者同一个厂,两烧一烘,一条烧道装了这样的水箱,另一条没装,同样的卡位,产量不一样。
(水箱应该安装在出砖口的第三个车位,那里的余溫完全够热水)另外,我烧制过的最耗卡位的窑子,是外置管道从保溫区抽热到烘干房,而焙烧窑的风机直接把原本可以利用的热气从烟囱排放掉,也就是说整个烘干房的热风都是从焙烧窑保温区抽过来的,这种窑特别耗內燃,不能低于四百卡!而个别好烧的窑子仅仅三百卡就够了,依个人经验大多数隧道窑不加外燃,內燃卡位大多在三百三~三百七之间。
- 1、下载文档前请自行甄别文档内容的完整性,平台不提供额外的编辑、内容补充、找答案等附加服务。
- 2、"仅部分预览"的文档,不可在线预览部分如存在完整性等问题,可反馈申请退款(可完整预览的文档不适用该条件!)。
- 3、如文档侵犯您的权益,请联系客服反馈,我们会尽快为您处理(人工客服工作时间:9:00-18:30)。
隧道窑烧结砖焙烧与
干燥过程中的问题分析
随着我国墙材烧结砖行业不断的快速发展,隧道窑是当前烧结墙材厂家首选的热工设
备。笔者走访了很多生产厂家。了解到隧道窑干燥室运行过程中均存在不同程度的问题。在
此,笔者根据自己的工作经验提出改进办法。与同行共同商榷。
1.原料焙烧性能与隧道窑结构的关系
目前市场上隧道窑的型号各不相同。差异很大。设计建设也不规范。对隧道窑的要求。
有的投资者既想投资少,又要产量大,这对窑炉设计者来说是很大的挑战。笔者认为还应回
归到热工原理上进行分析.只有掌握窑炉的性能与结构符合科学规律.才能使热工设备进入
正常生产状态,否则就是异想天开。砖坯在热工设备焙烧过程中产生一系列的变化,主要有:
坯体中的各种组分发生分解、化合、再结晶生成新矿物。坯体的颜色、密度、吸水率发生变
化:最后变成具有一定颜色、致密坚硬、力学强度的制品。当坯体被加热时。首先排除原料
矿物中的水分,在200℃以前。坯体中残余的自由水及大气吸附水被排除出去。在400℃~
600℃时。黏土失去结构水,黏土矿物结构受到破坏。此阶段坯体强度有所下降,升温至
573℃于,坯体中的β一石英转化成仪α一石英,体积增加0.82%,此时如升温过快,坯体
易产生裂纹。600℃以后固相反应开始进衍。在650 ℃~800℃有少量易熔物存在,坯体开
始烧结,产生收缩。在600℃-900℃如果原料中含有较多的可燃物质。这些物质需要较长
氧化时间c过程中在930℃~970℃,CaCO3,分解生成CaO和CO2,,在焙烧原料中黏土
颗粒发生硅酸盐化合作用,发生不可逆的变化过程。窑体内的冷空气通过冷却带的砖垛。与
砖发生热交换过程。最后制品被冷却到20℃~40℃。砖坯冷却速度因原料而定,尤其冷却
到573℃于,游离石英由α型转变为β型,体积急剧收缩0.82%,使坯体中产生很大的内应
力。此时应缓慢冷却,否则易使制品开裂。
2.制品的干燥与烧成的关系
干燥好的砖坯在进焙烧窑前要达到含水率小于6%的要求,这项技术参数对烧成来说非
常重要。如果坯体残余含水率大于6%,这种情况将直接影响后面的烧成。如何控制好干燥
这一环节,首先要掌握干燥窑的干燥过程,了解影响干燥的因素:①坯体原料的性质和坯体
的形状大小、厚度、孔洞率;②坯体的成型含水率,残余含水率;③坯体本身的温度越高则
干燥速度越快,因此,坯体在成型时加热可以提高干燥速度;④干燥介质的温度越高则干燥
速度越快。但温度过高会使坯体开裂;⑤干燥介质的相对湿度越低,则干燥速度越快。在等
速干燥阶段此影响最明显。干燥介质的流动速度越大,干燥速度越快;⑥干燥介质与坯体的
接触面积越大,则干燥速度越快,接触面积大小主要决定于坯体的码坯形式;⑦干燥窑的结
构、送排风的形式及风机的选型;⑧干燥窑的结构上要注重4个方面的结构处理.如加热
阶段、等速干燥阶段、降速干燥阶段、平衡阶段;⑨干燥倒坯是常见的最头痛的问题.尤其
是春季南方地区的生产厂家,最为普遍;⑩干燥进车速度不均匀。干燥曲线变化无常,送热
与热分布、排潮与风速与原料的性能不适应。如何处理好这些因素将与烧成质量有直接的关
系。
3.烧成产品的质量及产量的关键环节
笔者参观了很多生产厂家,反映突出的问题有:窑炉设计参数与实际生产有差异:产
品的能耗与生产成本过高;产品的优等率过低;窑炉自身能耗高等。这些问题反映了烧成窑
结构不合理。这些结构不合理的窑炉大多出自非专业窑炉公司.他们没有资质,设计和建造
窑炉没有理论依据,拿着一张抄袭的图纸走天下。完全没有按照《烧结砖瓦工厂设计规范>
中的有关规定实施。更谈不上节能降耗。在此。我们要想解决生产过程中出现的上述问题,
就要彻底掌握热工设备上的关键结构及技术要求,从根本上改造窑炉先天不足之处,才能确
保投产后顺利达产达标,使投资人见到效益。这样才能促进墙材事业的发展。大家要清楚窑
炉是一种热工设备。而非一种建筑物,要想掌握热工设备的生产性能就必须从它的结构功能
及选材上进行全方位的了解。
4.烧结隧道窑能耗
降低窑炉热损能耗是多环节的过程.并非单项环节就能降耗。窑炉吸热较大的部位有
窑墙、窑顶、窑车、热量利用、烟囱排出、自然介质温度、材质的吸热并放热等。要全面掌
握窑体密封及合理的烧成曲线、升温与降温的时间控制、可燃物的挥发值、产品的冷去口时
间、上下火道温差、火道走向、上下火的关系,以及窑炉的蹲火等一系列情况。并将这些参
数严格控制在规范范围内,才能确保生产过程的节能降耗。
5.生产管理
笔者在走访砖厂中,发现很多较规范的专业窑炉公司承建的窑炉,其制造的窑炉质量
很好,但生产状况不尽如人意,生产现场非常杂乱,工人不懂操作规程,不善于进行窑炉保
护,不注重生产环节管理.排放物乱扔乱放,烟气、S02不处理,造成周边环境污染。一个
企业的效益关键来自管理,管理也是一门学科,如何进行规范化的管理,首先,管理者自身
一定要懂行,要从整厂的设备性能技术着手,并培养一批中层和基层技术骨干及熟练的操作
工人,宣传落实操作规范和操作流程以及整厂的管理理念。
6.窑炉操作过程中应注意的环节
一是干燥窑的性能与干燥过程。无论干燥风量风速过大亦或是干燥风温过高、周期较
短.都不利于干燥,极易造成砖坯裂纹。
二是造成砖坯裂纹的根本原因是干燥工艺不当,即干燥制度不合理造成的。一定要按
照砖坯干燥的四个阶段,即砖坯加热干燥段、等速干燥段、降速干燥段、平衡干燥段的特征
及其工艺操作方法进行操作。砖坯加热阶段是坯体随温度升高而干燥速度加快.坯体开始产
生干燥收缩。在干燥过程中,砖坯水分的外扩散速度与内扩散速度相等时,即干燥进入等速
阶段,这时,干燥进行最为强烈。如果外扩散速度远远大于内扩散速度,则坯体内外形成很
大的水分梯度,导致坯体表面收缩很大,当收缩产生的应力大于坯体强度时,坯体表面就形
成裂纹。干燥过程中,当坯体表面上的水分等于大气吸附水分时,蒸发面随着水分的减少而
逐渐缩向坯体内部的毛细孔道中,干燥速度逐渐降低。即干燥进入降速阶段。在降速阶段坯
体内只是相应增加气孔,并不发生体积收缩,所以,坯体在降速阶段不会产生干燥裂纹。在
等速干燥阶段与降速干燥阶段之间有一个分界点,即干燥临界点。此时因固体颗粒失去周围
的水分而相互靠近,直到它们互相接触并靠拢在一起,因此,砖坯水分达到临界含水率以后,
坯体即停止收缩。就是使用大风量、高温的热介质,坯体脱水速度再快.也不会产生干燥收
缩。所以,在临界点以前,要严格控制送人干燥窑的热风温度与风量,在保证坯体不产生裂
纹的情况下,提高干燥速度。临界点以后.由于干燥过程已不会使坯体产生破坏性裂纹,所
以,应该用最大的通风量和最高的热介质温度,快速地脱去坯体中的水分,提高干燥速度。
由此可见,准确地确定隧道窑干燥临界点的位置,对于隧道干燥窑的设计与生产操作都十分
重要。临界点在隧道干燥窑中的准确位置,操作者无法直接确定,只能通过调试各送风口的
风量、风温以及砖坯的干燥质量和干燥速度来摸索出一个较小的范围,如果干燥过程中窑内
经常发生塌坯现象,尤其是季节交替时,这种塌坯现象最为严重。此时必须加强干燥窑体和
顶部的保温措施和窑炉进出端的密封措施,防止冷风进入排潮口而降低排潮温度,根据天气
降温的变化情况提高入窑的风温与风量,发现塌坯车位时,加大高温热风的输入量,可在窑
的两侧及窑车台面以上部位增设进风口,采取一些其他必要措施。提高排潮口的温度,使其
必须大于50℃,这样才能有效的控制塌坯现象的出现。
三是必须要掌握窑炉在焙烧过程中的环节和注意事项。根据原料性能的不同确定最高
烧成温度、开始烧结温度、最终烧结温度、烧成温度范围、烧成曲线等参数。要有合理的升
温时间、保温时间、冷却时间。注意焙烧气氛的压力制度和窑炉送入供风量。在焙烧过程中
通常会出现产品的缺陷有:欠火或过火砖、制品裂纹、黑心和压花、面包砖、烧焦起泡砖、
制品石灰爆裂、制品泛霜、制品表面印纹、制品色差等一系列的缺陷。
总之,在砖坯烧成过程中必须掌握所有环节,在窑炉正常生产过程中,也要注重异常情况的
观察,特别是吊顶式的隧道窑和大断面的平顶窑,其窑顶吊砖及窑顶的隔热保温系统最容易
出现问题,要多加观察,烧坏的顶砖要及时更换,要掌握不停火情况下的换砖技术,确保窑
炉正常生产。