FDFCC-Ⅲ重油催化裂化工艺
催化裂化、催化裂解、热裂解技术对比

催化裂化.催化裂解、催化重整.加氢精制与裂解.芳桂抽提技术总结DCC (催化裂解)DCC的操作有两种不同的方式:最大量生产丙烯(工型)以及最大量生产异构DCC-I510-5S0 'C伟创石油化工设计有限公司,如有问题请加qql503261405中国石化石油化工科学研究院达到60%目前国内已经开匚生产的MCC有两套,还有一套装置年内也要开匸。
上海河图石化丄程有限公司的技术•简单地说多产烯烧并不准确•汽油提升管主要功能是将催化汽油中的r⅛碳烯烧转换成低碳烯烧•提r⅛液化气产址和碳三、碳四烯烧收率。
另一个功能是汽油沉降湍的待生催化剂循环至重油提升管降低催化剂温度从而提r⅛重油提升管的剂油比。
山东齐旺达集团海仲石化有一套60万吨的HCC.生产液化气.干气、轻芳烧、中芳烧联产芳烧的催化裂化技术(MCC)以重油加石脑油进料,联产丙稀.芳烧(苯、甲苯和二甲苯)和溶剂油~~DCC工艺是常规FeC操作与蒸汽裂解的组合。
其工艺条件比FCC苛刻,深度催化装化(DCC)匚艺又称催化裂解工艺,它可看作是常规FCC操作与蒸汽裂解的组合。
DCC装宜在538-582Γx 10%-30%蒸汽条件下操作,而FCC装宜在 493~549<∖ 1%~3%蒸汽条件下操作。
DCC操作采用分子筛催化剂选择性地生产丙烯、乙烯和富芳烧石脑油。
该技术最大址生产丙烯(工型)使用RlPP开发的专利沸石催化剂QCC(匸型)丄艺可生产20%丙烯,而FCC匸艺的丙烯产率为5%左右.MGG J:艺也是RIPP研究开发的一项藝产液化气和汽汕的催化转化工艺,采用具有特殊反应性能的RMG催化剂,在反应温度DCC-I 510-580、C DCe-II500-530 'C反应压力0.15 - 0.35MPA的条件下,丙烯产率可达9%(质).RIPP在DCC和MGG丄艺的基础上开发f MlO工艺,该匸艺可最大量生产界构烯烧和商辛烷值汽油,兰炼釆用MK)工艺后,丙烯产率达Iwo(质),异丁烯和异戊烯的产率可达10%(质)∙RIP],与长炼合作开发了以一 1助气剂,以一 1助气剂具有强度高,适应性强,产气量大,气体烯炷度和异构化程度高及汽油辛烷值增加的特点,长炼两套頊油催多)•但前者不产汽油.重油加石脑油重油(减压馆分油.焦化抽油.常圧渣油.以及减压饰分油掺减压渣油)■也可加I •轻油(石脑汕、柴油以及C4、CS轻烧)因产乙烯较少,基本改为CPP工艺,这样同时产乙烯和丙烯1、丙烯(产率20%)为主的气体烯矩(含乙烯较少八2.兼产∣⅛辛烷值优质汽油?芳烧多少?4、液化气?5、焦炭?丙烯20. 5%乙烯6・1丁烯11. 3%,其中另一•种为非质子酸中心•(即L酸中心)。
fcc催化裂化

fcc催化裂化FCC催化裂化技术(Fluid Catalytic Cracking,以下简称FCC)是一种重要的石油炼制工艺,用于将重质石油馏分转化为高附加值的轻质烃类产品。
本文将从FCC技术的原理、工艺流程、催化剂以及应用领域等方面进行介绍。
一、FCC技术的原理FCC技术是利用催化剂在高温条件下对重质石油馏分进行裂化反应,将较长的烷烃链分子裂解为较短的烷烃链分子。
这种裂化反应是在流化床反应器中进行的,床层内的催化剂与石油馏分混合后形成流化床,在催化剂的作用下进行裂化反应。
裂化反应生成的烃类产品经过分离和处理后,可以得到汽油、液化气等高附加值的产品。
二、FCC技术的工艺流程FCC技术的工艺流程主要包括进料预处理、裂化反应、分离和处理等环节。
进料预处理主要是对原料进行加热、脱盐、脱水等操作,以提高裂化反应的效果。
裂化反应是FCC技术的核心环节,通过将预处理过的原料与催化剂混合后送入流化床反应器,经过高温和催化剂的作用,使原料分子发生裂化反应。
分离和处理环节主要是通过一系列的分离设备,如分馏塔、冷凝器等,将裂化反应产生的混合物进行分离和纯化,得到目标产品。
三、FCC技术的催化剂催化剂是FCC技术中起着至关重要作用的物质。
常用的FCC催化剂主要是硅铝酸盐基催化剂,其具有良好的活性和稳定性。
催化剂的选择对于裂化反应的效果具有重要影响,不同的催化剂可以调控反应的产物分布和性质。
此外,催化剂的再生和补充也是FCC技术中必要的工艺环节,通过对催化剂进行再生和补充,可以保持反应的稳定性和持续性。
四、FCC技术的应用领域FCC技术广泛应用于石油炼制工业中,特别是在汽油生产领域有着重要地位。
通过FCC技术可以将重质的石脑油、渣油等转化为高辛烷值的汽油,满足不同地区和需求的汽油标准。
此外,FCC技术还可以生产液化气、煤油、柴油等产品,具有较高的经济效益和社会效益。
总结起来,FCC催化裂化技术是一种重要的石油炼制工艺,通过催化剂在高温条件下对重质石油馏分进行裂化反应,将其转化为高附加值的轻质烃类产品。
催化裂化、催化裂解、热裂解技术对比

催化裂化、催化裂解、催化重整、加氢精制与裂解、芳烃抽提技术总结
MGG是以减压渣油、掺渣油和常压渣油等为原料的最大量生产富含烯烃的液态烃,同时最大生产高辛烷值汽油的工艺技术,与其他同类工艺的差别在于它在多产液态烃下还能有较高的汽油产率,并且可以用重油作原料(包括常压渣油)。
反应温度在510~540℃时,液化气产率可达25%~35%(摩尔比),汽油产率40%~55%(摩尔比)。
液化气加汽油产率为70%~80%。
汽油RON 一般为91~94,诱导期为500~900 min。
这一技术是以液化气富含烯烃、汽油辛烷值高和安定性好为特点的,现已有多套装置应用。
MIO技术是以掺渣油为原料,较大量地生产异构烯烃和汽油为目的产物的工艺技术。
1995年3-6月在中国兰州炼化总厂实现了工业化。
以石蜡基为原料时,缩短反应时间和采取新的反应系统,异构烯烃的产率高达15%(摩尔比)。
催化结焦原因分析及措施
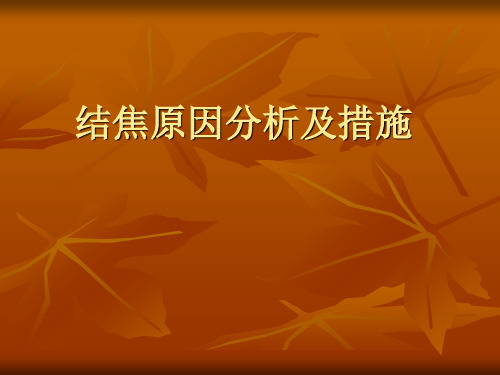
b) 沉降器单级旋分在本次改造中选用的是国产PV 沉降器单级旋分在本次改造中选用的是国产PV 型旋分,其设计与制造技术在国内已成型,主要起 到分离反应油气和催化剂的作用。影响旋分效果的 主要参数有:入口油气的粉尘浓度,粉尘的颗粒度、 入口油气线速以及旋分的本身设计尺寸等。 c) 从旋分的尺寸来看,其入口面积、筒体直径、 沉降高度、排尘口直径以及升气管高度是影响旋分 效率与压降的关键尺寸。一般来说,在入口气量保 持一定的情况下(入口面积保持一定),筒体直径 越大,分离效率越高,压降越低,另外沉降高度越 大,分离效率越高,压降也增加不大,但旋分的直 径和高度直径受制于沉降器的大小,因此设计时根 据气量。沉降器尺寸等因素确定合适的高径比。
谢谢大家!!
每一次紧急停工容易引发如催化剂跑损,大型 机组故障,结焦加剧和脱落等次生事故的发生,特 别是结焦和脱落直接影响装置产品的分布和二次停 工抢修,避免生焦难达到,但是可以控制焦炭的生 成速度和防止焦块的脱落
四,防结焦技术改造内容
1,沉降器的防焦蒸汽由1.0Mpa蒸汽改为 ,沉降器的防焦蒸汽由1.0Mpa蒸汽改为 3.5Mpa 以提高蒸汽在沉降器的温度,减缓油气冷凝 结焦;同时在沉降器底部增设1.0Mpa松动蒸汽,在 结焦;同时在沉降器底部增设1.0Mpa松动蒸汽,在 沉降器藏量超高时进行松动。 2,沉降器单旋升气筒增设导流片,目的是防止此部分 结焦后的焦炭因工艺操作变化或紧急事故状态温度 突变而脱落,堵塞料腿导至非计划停工。 3,沉降器粗旋升气筒与单旋入口直连,单旋直连分配 器与粗旋出口集合管通过活动插口实现直连和吸收 热位移,粗旋出口下端设引流锥,将气提后的油气 导入进入单旋入口:同时将沉降器内的防焦蒸汽和 飘散在内的零星油气导入单旋。
三,结焦原因分析
重质油催化裂化工艺
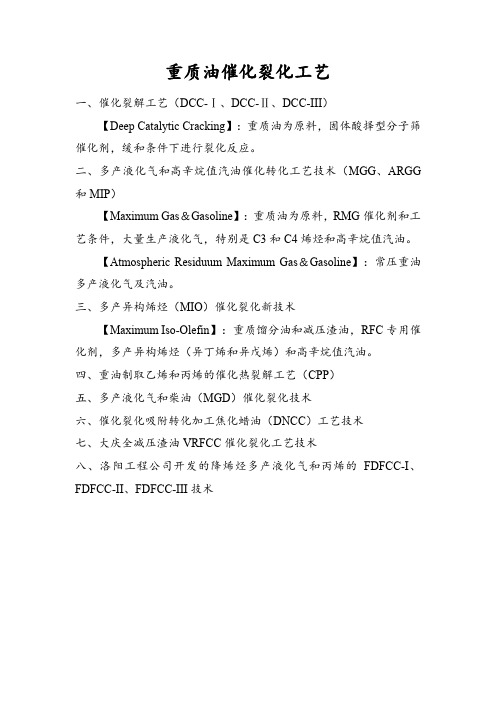
重质油催化裂化工艺
一、催化裂解工艺(DCC-Ⅰ、DCC-Ⅱ、DCC-III)
【Deep Catalytic Cracking】:重质油为原料,固体酸择型分子筛催化剂,缓和条件下进行裂化反应。
二、多产液化气和高辛烷值汽油催化转化工艺技术(MGG、ARGG 和MIP)
【Maximum Gas&Gasoline】:重质油为原料,RMG催化剂和工艺条件,大量生产液化气,特别是C3和C4烯烃和高辛烷值汽油。
【Atmospheric Residuum Maximum Gas&Gasoline】:常压重油多产液化气及汽油。
三、多产异构烯烃(MIO)催化裂化新技术
【Maximum Iso-Olefin】:重质馏分油和减压渣油,RFC专用催化剂,多产异构烯烃(异丁烯和异戊烯)和高辛烷值汽油。
四、重油制取乙烯和丙烯的催化热裂解工艺(CPP)
五、多产液化气和柴油(MGD)催化裂化技术
六、催化裂化吸附转化加工焦化蜡油(DNCC)工艺技术
七、大庆全减压渣油VRFCC催化裂化工艺技术
八、洛阳工程公司开发的降烯烃多产液化气和丙烯的FDFCC-I、FDFCC-II、FDFCC-III技术。
FDFCC工艺中汽油提升管催化裂化反应动力学模型研究

采 用 的温度 , 利 于汽 油 烯 烃 的转 化 , 而 在产 物 有 从 分 布 中有大 量裂 化产 物液 化气 产生 ; 另外 产 物 中还
有 少量 柴油 组分 , 这可 能 与在操 作 中采用 多 产柴油 催 化剂 C 一OD有 关 。 C2 —
表 1 原 料 性 质 项 目 原 料 1 原 料 2 原 料 3 原 料 4 原料 5
对 于催 化裂 化 反应 体 系 的模 型研 究 大 多采 用
比较 成熟 的集 总理 论 方 法 。催 化 裂 化 集 总 反 应 动 力学 模 型 的 发 展 已 经 历 了 从 三 集 总 l 、 集 8 六 J 总[ 十集 总l 十一集 总[ 1 、 l 、 1 副的 历 程 , 轻 馏 分 对
密 度 (0℃) g・ m 。0 7 75 . 4 0 7 0 7 . 2 0 7 45 2 / c . 2 0 7 75 . 4 0 7 51 . 3
馏程/ ℃
初 馏 点
3 O 5 0 7 0
3 . 10
7 . 1 5 9 . 6 5 1 4 5 2 .
3 . 25
( 烯烃体积分 数高 达 4 ~6 ) 大 幅度 降低 催化 o o ,
裂化汽 油中的烯烃含量是 我 国实现 汽油 清洁化 的当
务之急 。为此 , 内出现 了不 少 降低催 化 裂化 汽 油 国
烯烃 含量 的工艺 , : P MGD 2, D C [ 如 MI u , J l F F C3 , J “ TS C [ 等 , 些工 艺都 以抑 制 汽油 中的 烯烃 生 RF C5 这
艺 汽 油 提 升 管 内 的催 化 反 应 行 为 。 根 据 集 总 原 则 , 汽 油 提 升 管 内反 应 系 统 的 原 料 和 产 品 按 馏 程 将 及 烃族 组 成 划 分 为 九 个集 总 组 分 , 过 合 理 简 化反 应 网络 , 立 九集 总反 应 动 力学 模 型 , 求 取 2 组 通 建 并 5 反 应 动 力 学 参 数 , 对 不 同 性 质 原 料 在 不 同操 作 条 件 下 的 产 品 分 布进 行 验 证 。结 果 表 明 , 模 型 能 并 该 较 好 预 测 汽 油 产 品组 成 及 液化 气 中 高 附 加 值 的丙 烯 产 率 。
fcc工艺

fcc工艺FCC工艺简介FCC工艺,即流化催化裂化工艺(Fluid Catalytic Cracking),是炼油行业中常用的一种重要的转化工艺。
它是利用催化剂在高温下使重质石油馏分在流化床中进行裂化反应的过程,将重质石油馏分转化为较轻质的石油产品,如汽油、柴油等,从而提高石油产品的产率和质量。
一、FCC工艺的原理FCC工艺的核心是流化床反应器。
在反应器中,催化剂以固体颗粒的形式悬浮在流化床中,形成一种类似于流体的状态,因此又称为流化床催化裂化工艺。
石油馏分经过加热后与催化剂接触,发生裂化反应。
在高温下,长链烃分子断裂成较短的链烃分子,同时释放出大量的热量。
裂化反应生成的碳氢化合物经过分离、冷却和净化等步骤后,得到各种石油产品。
二、FCC工艺的优势1. 产率高:FCC工艺能够将重质石油馏分转化为较轻质的石油产品,提高产率。
同时,还可以通过优化工艺条件和催化剂的选择,进一步提高产品产率。
2. 产品多样:FCC工艺不仅可以生产汽油和柴油等常见的石油产品,还可以生产液化石油气(LPG)、石油饮料和石油化工原料等多种产品,具有较高的经济效益。
3. 能源节约:FCC工艺中释放出的热量可以用于加热石油馏分,减少了外部能源的消耗,提高了能源利用效率。
4. 环保性好:FCC工艺中采用的催化剂可以有效地降低石油产品中的硫含量,减少对环境的污染。
此外,FCC工艺还能够有效地处理催化剂中的焦炭,降低废催化剂的排放量。
三、FCC工艺的应用FCC工艺广泛应用于炼油行业,是炼油厂中最重要的转化工艺之一。
它可以处理各种不同种类和来源的石油原料,包括重质原油、蜡油、渣油等。
在炼油厂中,FCC装置通常位于蒸馏装置之后,能够将蒸馏装置无法进一步转化的重质石油馏分转化为有价值的产品。
四、FCC工艺的发展趋势随着能源需求的增长和石油质量的下降,FCC工艺受到了越来越多的关注。
未来,FCC工艺的发展趋势主要包括以下几个方面:1. 提高产品质量:通过改进催化剂的性能和结构,降低产品中的硫含量和芳烃含量,提高产品的抗爆性能和清洁度。
fcc工艺

fcc工艺FCC工艺简介FCC工艺,即流化催化裂化工艺(Fluid Catalytic Cracking),是一种广泛应用于石油炼制行业的重要工艺。
该工艺通过在高温、高压和催化剂的作用下,将重质石油馏分转化为轻质石油产品,如汽油和石脑油,以满足市场需求。
工艺原理FCC工艺的核心是催化裂化反应,通过将重质石油馏分与催化剂混合并在高温下进行反应,使得长链烃分子断裂为短链烃分子。
这一过程中,催化剂起到了非常重要的作用,它能够提供活性位点,并加速烃分子的裂解反应。
催化剂通常由沸石类物质构成,具有良好的孔隙结构和催化活性。
工艺流程FCC工艺的主要流程包括进料预热、催化剂再生、反应装置等。
首先,进料经过预热,使其达到适宜的反应温度。
然后,进入催化裂化反应器,与催化剂进行接触反应。
反应产物进一步进入分离装置,通过分馏和其他处理步骤,得到不同品位的石油产品。
工艺优势FCC工艺具有许多优势,使其成为炼油行业的重要工艺之一。
首先,它能够将重质石油馏分转化为更多的汽油和石脑油,适应了市场对这些产品的需求。
其次,该工艺具有较高的石油转化率,能够充分利用原料资源。
此外,FCC工艺还能够降低石油产品中的硫含量,减少对环境的污染。
工艺挑战与改进尽管FCC工艺具有许多优势,但也面临一些挑战。
首先,催化剂在反应过程中会受到热力学和动力学的限制,导致催化剂活性降低。
此外,催化剂的再生也是一个关键的环节,需要耗费大量能源。
为了克服这些挑战,研究人员一直在努力改进FCC工艺。
例如,开发更活性和稳定的催化剂,优化反应条件,提高产品选择性等。
FCC工艺的应用由于其独特的优势,FCC工艺广泛应用于石油炼制行业。
特别是在汽油需求大幅增加的情况下,FCC工艺能够有效地提高汽油产量,满足市场需求。
此外,FCC工艺还可以与其他工艺相结合,如石脑油加氢装置,进一步提高产品质量和增加附加值。
总结FCC工艺作为一种重要的石油炼制工艺,通过催化裂化反应将重质石油馏分转化为轻质石油产品。
- 1、下载文档前请自行甄别文档内容的完整性,平台不提供额外的编辑、内容补充、找答案等附加服务。
- 2、"仅部分预览"的文档,不可在线预览部分如存在完整性等问题,可反馈申请退款(可完整预览的文档不适用该条件!)。
- 3、如文档侵犯您的权益,请联系客服反馈,我们会尽快为您处理(人工客服工作时间:9:00-18:30)。
FDFCC-Ⅲ重油催化裂化工艺 FDFCC-Ⅲ工艺特有的技术特点: (1)开发了实现“低温接触、大剂油比”高效催化技术(HECT)。即利用汽油提升管待生剂相对较低的温度和较高的剩余活性,将汽油提升管待生剂引入重油提升管底部与再生剂混合,降低干气和焦炭产率,提高丙烯收率,改善产品分布。 (2)采用双提升管、双沉降器和双分馏塔工艺流程,即分别设置重油提升管和汽油提升管,两根提升管后均设有沉降器和分馏塔,从而充分利用汽油提升管的改质效果,使催化汽油的烯烃含量直接满足欧Ⅲ标准。 4. 采用了带预混合管的烧焦罐高效再生技术,具有较高的烧焦强度和较低的再生剂含炭。为降低再生系统压降2007年FDFCC技术改造取消了预混合管和大孔分布板。 5. 采用了可调性强的下流式外取热器,取出两器热平衡多余的热量。 6. 能量回收机组采用了烟气轮机-轴流式主风机-汽轮机-电动/发电机四机组同轴新设备,回收了能量,降低了装置能耗。烟气轮机轮盘和叶片使用的是国内研制的新型高温合金和喷涂材料。 7. 设有余热锅炉回收系统,回收热量,降低能耗,为防止省煤器炉管低温腐蚀,在烟气低温位置采用了20G钢炉管,过热器高温段采用12CrMo材质。 8. 选用了高效旋风器和电液冷壁滑阀等设备。 生产原理 1. 反应—再生部分 重油催化裂化提升管和汽油提升管用的催化剂为分子筛催化剂。原料油与高温催化剂在提升管内接触,在一定的压力和温度下发生一系列化学反应,主要有裂化、异构化、氢转移、芳构化、缩合等反应,生成包括干气、液化气、汽油、柴油、回炼油、油浆馏份的高温油气和焦炭,生成的焦炭附着在催化剂上。在沉降器内反应油气和催化剂分离,反应油气到主、副分馏塔内进行分离,重油反应器附有焦炭的催化剂经汽提段汽提直接回到再生器,汽油反应器内附有焦炭的催化剂经汽提后一路直接回到再生器烧焦一路返回重油提升管底部与重反再生剂混合。再生器内催化剂在一定的温度、压力及通入主风的条件下,烧去催化剂上的积炭(即催化剂的再生过程)。催化剂活性、选择性恢复后回提升管循环使用。焦炭燃烧放出的热量除满足工艺需要外,多余的热量由外取热器取出,焦炭燃烧后生成的高温烟气经烟气轮机和余热炉后排入大气。 2. 分馏部分 重油催化分馏部分的作用是把从反应器来的高温油气混合物按沸点范围分割成为富气、汽油、轻柴油、回炼油及油浆馏分,并保证各个馏分的质量符合产品要求。此外分馏系统还完成原料预热及热量回收的任务。催化分馏塔与常减压装置的常压塔原理基本相同。不同之处在于: (1).催化分馏塔的进料是过热气相进料。 (2).催化分馏塔气相进料中携带了一部分催化剂颗粒。 因此,催化分馏塔除了按分馏原理完成一般的产品分割外,还设有油浆循环以完成脱过热(将高温过热油气冷却到饱和状态)并和回炼油返塔一起洗涤反应油气中的催化剂。 3. 吸收稳定部分 吸收稳定部分由吸收塔、解吸塔、再吸收塔、稳定塔、容器、冷换及机泵等组成。吸收稳定部分的任务是加工来自分馏塔顶油气分离器的粗汽油和富气(富气经气压机压缩),从中分离出干气(C3≯3%(V)),液化气(C2≯3%(V),C5≯1.0%(V))和稳定汽油,并要求稳定汽油的蒸汽压合格(冬季≯88kpa,夏季≯74kpa)。吸收、解吸、再吸收塔主要解决C2与C3馏份的分离,是吸收和解吸过程;其原理是利用气体混合物中各组分在液体中溶解度的不同来分离气体混合物。 稳定塔完成C3、C4馏份与汽油馏份的分离,是精馏过程;其原理是利用液体混合物各组分的挥发度不同进行分离。 4. 柴油碱洗 碱洗就是利用碱溶液(非加氢精制剂DF-01)和油品中的酸性非烃化合物起反应,生成相应的盐类,而以碱渣的形式排掉,碱洗能除去硫化氢、酚、低分子硫醇、环烷酸等非烃化合物,提高柴油质量。 5. 四机组及气压机 四机组: 80万吨/年重油催化裂化装置设置的四机组由烟气轮机、主风机、蒸汽轮机、电动/发电机组成。 烟气轮机—主风机—汽轮机—变速箱—电动/发电机 四机组主要完成反应—再生烧焦供风和多余能量的回收。 各机组的作用; (1)烟气轮机:主要回收高温烟气的压力能和部分热能,在设计负荷下的实际回收功率大约在7000kw左右。 (2)汽轮机:采用背压型式,利用蒸汽的焓降做功,额定功率3920kw。 (3)主风机:前五级静叶可调的轴流式压缩机,主要目的是压缩空气,供给反应—再生烧焦用风。 (4)电动/发电机;为汽轮机,烟气轮机的功率之和小于主风机消耗功率时,处于电动状态:反之,处于发电状态。正常情况下,电动/发电机处于发电状态,发电量一般在3900kw—4200kw之间。 四机组的同轴转数正常情况下是随电网的周波变化而变化。 6. 气压机 富气压缩机是由冷凝式蒸汽轮机带动的,正常情况下通过调整气压机转数来改变压缩机负荷。 气压机作用主要有以下几点: (1)调节反应压力,通过气压机转数来调节富气压缩量从而改变反应压力。 (2)提高富气压力,提高烃类沸点,为富气吸收分离创造条件。 7. 余热回收 本单元主要将装置内多余的热量,通过传热过程,将热量传递给水,使水变为具有一定温度和压力的蒸汽。 本装置余热热源:高温催化剂、油浆及高温烟气产3.5MPa过热蒸汽、分馏塔一中,二中回流产0.6MPa蒸汽。 工艺流程说明 1.反应—再生部分 重油提升管反应器(T-101)的进料由新鲜原料,回炼油和油浆三部分组成。新鲜原料的渣油和蜡油分别由系统进入装置,经过原料油混合器(混-202)混合均匀后,进入原料油缓冲罐(R-202),用原料油泵(P-201/1.2)抽出。开工时经H-212/1、2加热,正常生产时,与分馏塔顶循环回流(H-202/1~4),轻柴油(H-204/1.2)和油浆(H-208/1.2)换热后进入混合器(混-201)。回炼油由泵(P-206/1.2)自回炼油罐(R-203)抽出,在混201入口与新鲜原料混合。回炼油浆用泵(P-207/1.2)自分馏塔(T-201)底部抽出,与混-201来的油品混合,混合后分四路经原料油雾化喷嘴进入重油提升管反应器下部,与来自重油提升管底部催化剂混合器的的高温催化剂接触,完成原料的升温、汽化及反应。 重油提升管反应器进料与来自再生器(T-102)的再生剂接触立即汽化并反应,产生的反应油气携带催化剂通过提升管向上流动,在提升管出口经粗旋使催化剂与油气迅速分离,油气及夹带的一部分催化剂经两组单级旋风分离器分离,分离出的油气去分馏塔,回收下来的催化剂经料腿流入汽提段,在汽提段底部通入水蒸汽,使沉积有焦炭并吸附了一定量油气的催化剂与蒸汽逆流接触,除去催化剂所吸附的油气,然后经待生滑阀进入烧焦罐。 汽油提升管原料油为来自2#催化裂化装置的粗汽油,由粗汽油泵升压后,经副分馏塔中段油-粗汽油换热器换热、升温至135.5℃左右后分四路经粗汽油雾化喷嘴进入汽反提升管反应器下部,与来自再生器的高温催化剂接触,完成原料的升温、汽化及反应。 反应后的油气与待生催化剂在汽反提升管出口经粗旋迅速分离,气体经升气管进入汽反沉降器单级旋风分离器,进一步除去携带的催化剂细粉后,反应油气离开汽反沉降器,进入副分馏塔。 积炭的汽反待生催化剂经汽反粗旋料腿进入汽反汽提段,在此与汽提蒸汽逆流接触,以汽提催化剂中所携带的油气。汽提后的催化剂一路经汽反待生斜管、汽反待生滑阀后进入烧焦罐下部。汽提段料位由汽反待生滑阀调节。另一路返回重油提升管底部与重反再生剂混合。 重反和汽反的待生催化剂在烧焦罐下部与二密相床返回的高温再生催化剂充分混合,以提高烧焦起始温度,汇同外取热器返回的催化剂一同在烧焦罐内烧焦, 再生器烧焦主风由主风机(机—101)升压,一路经增压机增压后分别作为外取热器及二密床流化风;另一路经辅助燃烧室(F—101)进入烧焦罐。循环斜管、待生斜管、外取热器及汽油待生斜管下来的催化剂进入烧焦罐,烧焦后的催化剂与烟气并流向上进入稀相管,稀相管出口的4组倒L快分将烟气和催化剂分离,分离后的烟气进入再生器6组两级旋风分离器,进一步分离催化剂。旋风分离器分离下来的再生催化剂落入第二密相床,二密相的再生催化剂分四路:一路经再生斜管、再生滑阀至重油提升管反应器,其催化剂量由反应温度控制再生滑阀的开度来实现;第二路经再生斜管、再生滑阀至汽油提升管反应器,其催化剂量由反应温度控制再生滑阀的开度来实现;第三路进外取热器,取走再生烧焦过程的过剩热量;第四路经外循环管和循环管滑阀补充进烧焦管底部,以提高烧焦起始温度。 从再生器顶部出来的高温烟气进入三级旋风分离器,进一步将烟气中携带的催化剂分离出来,以满足烟气轮机对烟气中催化剂粉尘浓度和粒度的要求。正常生产时,绝大部分烟气通过烟气轮机膨胀作功,回收烟气的压力能和部分热能,然后进入余热炉。开工初期及非正常生产时(烟机故障),大部分烟气可以经烟气旁路直接进入余热炉,尔后排入大气。余热炉分省煤器和过热器两部分,过热器设有烟气旁路蝶阀,用来调节过热蒸汽温度,余热炉设有烟气旁路,非正常情况下,烟气可不经余热炉,直接排入大气。为了保证经三旋分出的催化剂正常下料,设有烟气临界流速喷咀,携带催化剂的烟气经四旋旋分后,经临界流速喷咀后直接排入大气。 除氧水由除氧器经泵(P-503/1. 3)抽出,经低温省煤器、高温省煤器升压升温后进入汽包(R-501),汽包(R-501)内饱和水分别由泵(P-501/1.3 ;P-505/1.2)抽出。泵(P-501/1.3 )出口饱和水分四路,第一路去外取热器(T-103)取热管束,第二路去油浆—蒸汽发生器(H-209),,第三、四路去余热锅炉强制蒸发段;泵(P-505/1.2 )出口饱和水去低温省煤器联箱。饱和水换热后,汽水混合物回汽包分离;饱和蒸汽由汽包(R-501)顶部引出后,进入过热器与烟气换热,过热后的中压蒸汽并入3.5MPa蒸汽管网。