镁合金半固态压铸缺陷分析与防止
镁合金压铸及机加工过程中的安全与防护范文(4篇)

镁合金压铸及机加工过程中的安全与防护范文镁合金的压铸和机加工过程涉及诸多安全隐患,因此,在进行这些操作时必须妥善采取安全措施和防护措施。
本文将阐述针对镁合金压铸和机加工过程中的安全与防护的内容。
首先,我们将介绍镁合金在压铸和机加工过程中的安全要求。
然后,我们将重点探讨镁合金压铸和机加工过程中的安全措施和防护措施。
最后,我们将总结本文的主要观点。
1. 镁合金压铸和机加工的安全要求镁合金压铸和机加工过程中,必须满足一系列的安全要求。
首先,操作人员必须了解镁合金的特性和危险性,并且具备相关的操作技能和知识。
其次,所有设备和设施必须符合相关的安全标准和规定,并经过定期的检验和维护。
此外,操作人员必须佩戴个人防护装备,如安全帽、防护眼镜、防护手套等。
还应该设置明显的警示标志和禁止标志,以提醒人们注意安全。
2. 镁合金压铸和机加工的安全措施在镁合金压铸和机加工过程中,为了确保操作人员和设备的安全,必须采取一系列的安全措施。
首先,对于镁合金的存储和运输,必须遵循相关的规定。
镁合金在接触空气时会产生易燃易爆的气体,因此,在存储和运输过程中必须保持良好的通风和防火措施。
其次,在镁合金压铸和机加工现场,必须设置专门的安全区域,并限制非相关人员的进入。
操作人员必须接受必要的培训,了解相关的操作规程和安全措施。
同时,所有设备和设施必须经过严格的检验和测试,确保其在运行过程中的安全性能。
此外,应及时清理和处理废弃物和污染物,以保持工作环境的清洁和安全。
3. 镁合金压铸和机加工的防护措施在镁合金压铸和机加工过程中,除了上述的安全措施外,还必须采取一系列的防护措施。
首先,为了防止镁合金的火灾和爆炸,必须提供足够的火灾防护设备,如灭火器、泡沫灭火系统等。
此外,还应该确保工作区域的通风良好,以及设置必要的防火帘、隔离措施和防护设备。
其次,在进行镁合金压铸和机加工操作时,操作人员必须佩戴个人防护装备,如防护眼镜、面具、防护手套等。
压铸产品质量缺陷分析及解决对策

龚春2011-09-30 龚春
压铸产品质量缺陷分析及解 决对策
分类: 分类: 冷隔、拉伤、裂纹、变形、花纹、 冷隔、拉伤、裂纹、变形、花纹、 斑点、网状毛刺、凹陷、欠铸、 斑点、网状毛刺、凹陷、欠铸、夹 外观类) 皮(外观类) 气孔、缩孔、气泡、夹杂( 气孔、缩孔、气泡、夹杂(内在组 织缺陷) 织缺陷)等
TU5JP4进排气浇口直冲型芯有被冲凹陷的立即进行更换以减少变形
上模时压铸机上的4根推杆一定要长度一样, 公差在0.5mm内,以保证顶出平稳
开模后静模弹簧推杆没有出来,说明已经卡死不 起作用了,需修模
DUG:977机框下抽芯
变形:
1. 铸件几何形状与图纸不符 2. 整体变形或局部变形 产生的原因: 产生的原因: 1. 铸件结构设计不良,引起不均匀收缩 铸件结构设计不良, 2. 开模过早,铸件刚性不够 开模过早, 3. 顶杆设置不当,顶出时受力不均匀 顶杆设置不当, 4. 切除浇口方法不当 5. 由于模具表面粗糙造成举报阻力大而引起顶出时变形 改进措施 (检查分析判断是开模变形还是顶出变形\收缩变形) 检查分析判断是开模变形还是顶出变形\收缩变形) 1. 改进铸件结构,比如机体人为增加倒拔,倒钩平衡包紧力, 改进铸件结构,比如机体人为增加倒拔,倒钩平衡包紧力,人为增 加渣包等。 加渣包等。 2. 调整开模时间 3. 合理设置顶杆位置及数量,有必要加6 合理设置顶杆位置及数量,有必要加6根推杆 4. 选择合适的切除浇口方法比如热切边 选择合适的切除浇口方法比如热切边 5. 加强模具型腔表面抛光0.4 减少脱 加强模具型腔表面抛光0.4,减少脱模阻力 0.4, 6、上模时推杆配平 7、更换断推杆 8、检查有无倒拔,及时消除 检查有无倒拔,
镁合金压铸及机加工过程中的安全与防护(4篇)

镁合金压铸及机加工过程中的安全与防护一、引言镁合金具有优异的物理性能、低密度、高比强度等特点,因此广泛应用于航空航天、汽车、电子等领域。
然而,在镁合金压铸及机加工过程中,存在一些安全与防护问题,需要给予足够的重视和措施。
本文将就镁合金压铸及机加工过程中的安全与防护进行探讨。
二、镁合金压铸过程中的安全与防护1. 选用适当的压铸机和工艺参数在镁合金压铸过程中,选择适当的压铸机和合理的工艺参数是保证安全的重要环节。
首先,压铸机的选用要符合国家相关标准,并经过专业人员维护和检测;其次,根据镁合金的性质和零件的要求,确定合适的铸造工艺参数,避免因过高温度或过大压力而产生意外情况。
2. 使用合适的模具和工装在镁合金的压铸过程中,模具和工装起到重要的作用。
因此,选择合适的模具和工装,并确保其质量和稳定性十分重要。
应定期检查模具和工装的磨损情况,以免因损坏而造成安全隐患。
3. 合理的操作规程和流程严格遵循操作规程和流程是保证安全的基本要求。
操作人员应经过专业培训,了解镁合金压铸的操作要点和安全注意事项。
在操作过程中,应严格按照指导书进行,避免因操作不当而导致事故发生。
4. 防止镁合金燃烧镁合金具有易燃的特性,因此应采取相应措施防止燃烧事故的发生。
首先,要做好防火工作,对压铸车间进行防火处理,严禁在车间内吸烟或使用明火。
其次,要进行良好的通风和排烟,保持压铸车间的空气流通。
此外,还应配备灭火器材,并定期进行维护和检测。
三、镁合金机加工过程中的安全与防护1. 使用合适的切削工具和刀具在镁合金的机加工过程中,使用合适的切削工具和刀具是保证安全的前提。
切削工具和刀具要选用质量可靠、适合材料的产品,并保持其良好的状态。
使用过程中,切削工具和刀具的破损情况要及时检查和更换,以免产生切削事故。
2. 控制切削速度和切削深度在机加工过程中,要合理控制切削速度和切削深度,避免因速度过快或深度过大而引发事故。
操作人员应根据具体情况,选择适当的切削参数,并进行试切试验,确保安全。
镁合金压铸常常遇到的问题
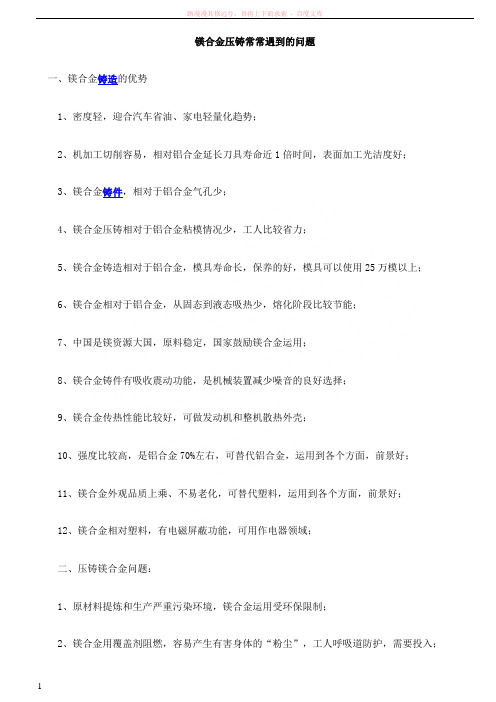
镁合金压铸常常遇到的问题一、镁合金铸造的优势1、密度轻,迎合汽车省油、家电轻量化趋势;2、机加工切削容易,相对铝合金延长刀具寿命近1倍时间,表面加工光洁度好;3、镁合金铸件,相对于铝合金气孔少;4、镁合金压铸相对于铝合金粘模情况少,工人比较省力;5、镁合金铸造相对于铝合金,模具寿命长,保养的好,模具可以使用25万模以上;6、镁合金相对于铝合金,从固态到液态吸热少,熔化阶段比较节能;7、中国是镁资源大国,原料稳定,国家鼓励镁合金运用;8、镁合金铸件有吸收震动功能,是机械装置减少噪音的良好选择;9、镁合金传热性能比较好,可做发动机和整机散热外壳;10、强度比较高,是铝合金70%左右,可替代铝合金,运用到各个方面,前景好;11、镁合金外观品质上乘、不易老化,可替代塑料,运用到各个方面,前景好;12、镁合金相对塑料,有电磁屏蔽功能,可用作电器领域;二、压铸镁合金问题:1、原材料提炼和生产严重污染环境,镁合金运用受环保限制;2、镁合金用覆盖剂阻燃,容易产生有害身体的“粉尘”,工人呼吸道防护,需要投入;3、镁合金用覆盖剂阻燃,容易产生HCL气体,和水蒸气结合,产生腐蚀性极强的稀盐酸,对工厂人员、设备和厂房基建有损害,厂房顶棚行车支撑等需要防腐蚀;4、镁合金用SF6混合气体阻燃,SF6气体由于制造混有有毒杂质,如HF等,所以需要严格管理;SF6是温室气体,在我国使用会受到限制;5、镁合金容易燃烧,熔化、保温、运输防止燃烧,有技术门槛;6、镁合金容易燃烧,熔化炉、保温炉的合金残渣清理工作量大;7、镁合金容易燃烧,如果设备比较老,机器外泄漏情况频繁,合金保温炉不密封,液压油请使用不燃油,防止火灾,生产现场易燃易爆气体和液体不要存放;8、镁合金容易燃烧,机器和熔化炉边上需要放(一大缸)黄沙放置易燃镁渣,(一大桶)阻燃覆盖剂,作为熄灭压铸过程中零星逃料产生的火情;9、镁合金的粉尘会自燃,高温镁渣也会燃烧,需要集中特殊处理;10、镁合金作为结构材料,容易受潮氧化,需要做表面处理,镀铬和阳极氧化污染环境镁合金作为结构材料,螺栓连接处因电化学腐蚀和蠕变,造成紧固件松动;11、镁合金铸件热强度低,容易产生热裂纹,造成铸件漏气和断裂;12、镁合金比热容低,热量损失快,需要模具一般需要设计加热装置;13、镁合金遇油燃烧,遇水爆炸;大块的镁合金失控燃烧,火势难以控制,以预防为主;。
镁合金熔炼铸造易出现的缺陷

镁合金熔炼铸造易出现的缺陷:由于镁合金的铸造性能较差,在镁合金的铸件生产中容易出现多种缺陷,并且较难消除,造成生产成本高。
常见的缺陷有疏松,夹渣,裂纹,气孔等。
我们必须从原辅材料开始控制质量,模具,设备,工序都要严格的控制和检验。
现做问题的分析处理,跟足去验证;1,疏松;(包跨表面脱层,明显熔合位等。
)该缺陷容易在内浇口及热节处出现。
这种缺陷一般在铸件的内部,肉眼不可见。
通过X 射线检查能检测出,由于浇口及热节部位则由于长时间处于过热状态,擬固过程中温度较高导致产生该缺陷。
防此这类缺陷要做好以下几方面的工作:(1),从工艺的角度合理设计好浇口系统,经反复实验确定直浇道,横浇道与浇口的截面积最佳之比为1:3:3;并合理进行冒口尺寸的改善,强化冒口的补缩作用,形成铸件有顺序的擬固;(2),充分利用冷铁的激冷效果帮助热节处补缩,一般冷铁是与冒口配合使用的;(3),在有疏松的位置使用暗冒口补缩,如果效果不好时,应适当增大冒口的体积或使用保温冒口,而在不易清理冒口的地方做成易割冒口。
以上的操作,实验证明都是有效的。
2,夹渣;(包跨常说的熔剂点,结疤,等等。
)该缺陷在铸件酸洗处理后,有的表面或铸件尖角处,暴露出黑斑夹杂物。
肉眼可见。
黑斑由一个接近圆形的浅色区所包围。
并以一个更黑的环为边界。
这种夹渣物一般是溶剂造成的,不但会降低铸件的力学性能,并且溶剂中的MgCl2直接降低铸件的抗腐蚀能力,镁和镁合金及易氧化,特别是ZM系列合金,更易氧化。
为防此镁合金在熔炼时氧化燃烧,而在熔炼中要加一定的溶剂,使之不与空气接触,由于溶剂的性能不好或操作不当,浇注工具上的溶剂容易进入到金属液中;舀取金属液不当,将溶剂带入到金属液中;由于浇注不槙,浇包上面浮着的溶剂进入到模腔中。
更可能是浇注温度较高,镁合金液在型腔中与泥芯放出的气体反应燃烧,产生二次氧化夹渣所致。
要消除这种缺陷。
具体方法如下:(1),使用带节流管的茶壶式浇包时,要磕掉粘附着的熔剂,浇包和坩埚底部少量的熔液不能浇入型腔,从坩埚中舀取金属液前,必须用浇包底部拨开液面的熔剂及氧化层。
压铸产品质量缺陷分析及解决对策

龚春2011-09-30
整理课件
压铸产品质量缺陷分析及解 决对策
分类: 冷隔、拉伤、裂纹、变形、花纹、 斑点、网状毛刺、凹陷、欠铸、夹 皮(外观类) 气孔、缩孔、气泡、夹杂(内在组 织缺陷)等
整理课件
压铸件缺陷产生的机理
压铸件在高温、高速、高压条件下成形,在理想条件下,压 铸充型过程大致可分为三个阶段Ⅲ。第一阶段是合金液被压射人 型腔,直接冲击到对面型腔,并沿边壁向各个方向迅速扩展生成 壳体;第二阶段是随后进入型腔的合金液继续沉积充满型腔;第 三阶段是型腔内的合金液在高压下压实冷却。但实际情况表明, 由于压铸件的几何形状千差万别、合金液在型腔不同部位温度和 粘度的变化等因素的影响,使得实际的充型过程比理想状态下的 三阶段充填过程复杂得多,型腔的充填过程其实包含着热力学和 流体力学的复合,并随充填过程中温度、速度、压力的变化呈非 常复杂的流态在合金液被压射入型腔直接冲击对面型腔并沿边壁 向各个方向迅速扩展生成壳体的过程中,存在有飞溅、涡流、裹 气现象,若浇注系统设计不当、压射速度选用过大,这一现象还 会加重。压铸件的几何形状越复杂,充型过程中合金液流相互碰 撞的机会就越多,型腔内残留的气体就越多,合金液温度降低得 就越多。这些残留的气体留在压铸件内就形成了气孔类缺陷,而 温度较低的合金液流在交汇处就形成了成形类缺陷。
加渣包等。
2. 调整开模时间
3. 合理设置顶杆位置及数量,有必要加6根推杆
4. 选择合适的切除浇口方法比如热切边
5. 加强模具型腔表面抛光0.4,减少脱模阻力
6、上模时推杆配平
7、更换断推杆
8、检查有无倒拔,及时消除
整理课件
花纹、流痕
整理课件
221机体上方流痕、花纹
镁合金压铸缺陷

第七章鎂合金壓鑄缺陷7.1 缺陷分類鎂合金壓鑄缺陷主要區分為三種類型。
分別為表面缺陷、形狀缺陷與內部缺陷。
各種缺陷常見的表象如下:1. 表面缺陷:表面缺陷包括˙裂紋˙起泡˙縮陷˙變色˙冷接紋˙拉模˙流紋˙黏模2. 形狀缺陷:形狀缺陷包括˙毛邊˙充填不良˙變形與翹曲˙尺寸不良3. 內部缺陷˙夾雜˙連續孔˙縮孔˙氣孔7.2 表面缺陷7.2.1 裂紋7.2.1.1 缺陷的外觀裂紋是鑄件的平滑表面上產生了不規則線狀的縫隙,它深入鑄件內,有時甚至穿透整個鑄件。
較常見的裂紋有兩種,一種是受外力破壞而產生的破壞裂紋,另一種是鑄件收縮時產生的收縮裂紋。
收縮裂紋通常沿著晶粒界面而行,其顏色在顯微鏡下顯得有點黯淡。
而破壞裂紋則可能穿透晶粒破壞,其顏色在顯微鏡下顯得光亮。
7.2.1.2 缺陷發生的原因˙熔湯內含不純物˙保護氣體供應量不足˙模具溫度過低˙離型劑種類不當˙模具元件幾何形狀受損˙頂出面與配置不當˙鑄件突出物的幾何形狀設計不良鎂合金常會因充填不良而引起裂紋,流紋就成為潛在發生裂紋的原因,當收縮或頂出時,鑄件一受力就沿著接合不良的地方裂開。
圖7.1即是鑄件沿著流紋裂開的情形。
圖7.1 沿著鑄件流紋裂開之裂紋有的裂縫看起來像裂紋缺陷,但實際上是流動不良引起的未密合情形,這類的裂縫寬度通常較寬。
如圖7.2所示。
a.疑是裂紋缺陷的裂縫鑄件b.裂縫切面放大後是流動不良圖7.2 疑是裂紋缺陷的裂縫及其切面放大7.2.2 縮陷7.2.2.1 缺陷的外觀縮陷是在平滑的鑄件表面產生局部的凹陷。
它常發生於厚薄不均的鑄件上肉厚較厚的部分。
7.2.2.2 缺陷發生的原因˙增壓壓力不足˙模具溫度分布不當˙增壓反應時間太慢˙離型劑用量過多˙熔湯溫度過高˙鑄件設計不當˙模具溫度過高(局部過高)7.2.3 冷接紋7.2.3.1 缺陷外觀冷接紋發生在鑄件表面上,一般有三種外觀。
一種是接合線呈現直線狀,另外一種呈現雲狀,第三種呈現漩渦。
不論何類,都是由於熔湯在充填過程中產生凝固的現象。
镁合金铸造缺陷

镁合金铸造缺陷资料来源:国营3017厂陈德洪《X光透视检验中常见的镁合金铸造缺陷》镁合金铸件中的圆形气泡和梨形气泡常分布在铸件的表面或靠铸型的一面,或者靠型芯的一面,有时也分布在铸件出气冒口的部位镁铝合金(ZM-5)铸件中的成组侵入气孔铸型或芯型中发出的气体在其压力大于金属液对气体的阻力时,侵入金属液体没有逸出型外而形成,常见于铸件的局部地区,常常可在吹砂之后和机械加工时发现。
造成这种缺陷的原因如型芯过紧、型芯烘干不够、型芯的通气孔堵塞等导致气体来不及排除,形成高压,进而侵入金属液中。
应当注意控制型砂和芯砂中发气物质的含量、湿型的含水量、铸型和芯型的烘干质量以及烘干后停放时间(防止返潮),改善和控制型砂的透气性,如合理夯实型砂,防止局部过紧,在转角部位应有气眼帮助排气,保证芯型通气孔道的畅通等等。
适当提高浇注温度、放置出气冒口,有利于侵入金属液的气体上浮逸出等也有利于防止侵入气孔的产生。
镁铝合金(2M-5)铸件中的气孔镁合金铸件中的块状夹渣镁合金铸件中的片状连续性夹渣镁合金铸件中的夹渣主要指氧化物夹渣,其主要来源于浇注操作不当,例如浇注时产生涡流、搅动和卷入气体。
多分布在铸件表面或铸件转接部分以及铸件内部的各部分。
夹渣表面通常是粗糙而形状不规则的孔洞,在X光底片上表现为外形不定而轮廓较清晰的黑斑,其摄影密度深浅不一,有块状或片状连续性。
目视、断口检查或机械加工时可发现其外观颜色呈灰暗色,有时呈黄色或带绿色。
防止氧化物夹渣常用措施:在熔炼过程中加入溶剂精炼,使溶剂吸收各种非金属物质(如氧化物、氮化物等),其后将在静置过程中沉于坩埚底部。
浇注时勿使金属液断流;在铸型的浇口设置撇渣装置(如过滤网和集渣包);浇注系统的设计应保证横浇道和内浇道以最小的搅动将金属液引入型腔内。
镁合金铸件中的条状疏松镁合金铸件中的云状疏松镁合金铸件中的疏松在X光底片上呈现为黑色条状纹路或黑色云状斑块,其摄影密度不大,边缘不规则且不大明显。
- 1、下载文档前请自行甄别文档内容的完整性,平台不提供额外的编辑、内容补充、找答案等附加服务。
- 2、"仅部分预览"的文档,不可在线预览部分如存在完整性等问题,可反馈申请退款(可完整预览的文档不适用该条件!)。
- 3、如文档侵犯您的权益,请联系客服反馈,我们会尽快为您处理(人工客服工作时间:9:00-18:30)。
F
铸造
oundry
热加工
热处理/锻压/铸造2011年第13期
69
镁合金半固态压铸缺陷分析与防止
浙江机电职业技术学院(杭州310053)王瑞权
【摘要】
针对镁合金半固态压铸生产中出现的各种缺陷的特征,从形成机理、影响因素等方面进行
分析,并提出了具体的预防与控制措施。通过调整压铸工艺参数,改善铸型设计,提高镁合金的熔炼质量
,
可取得满意的效果
。
在镁合金半固态压铸过程中铸件存在气孔、缩
孔、缩松、氧化夹杂、冷隔、充型不良、毛刺和飞边等缺陷。下面对上述各种缺陷产生的原因和防止方法进行论述。一、气孔缺陷气孔属气体作用而形成,一般尺寸较大,肉眼可见,内孔光滑(如图1所示)。图1铸件中的气孔金相1.产生的原因(1)当半固态浆料的液相率较高,飞溅严重,容易形成漩涡包住空气。(2)内浇道处金属浆料充填速度较高,造成紊流,卷入气体。(3)排气不良,溢流排气道太小。(4)模具温度过低,脱模剂未干。2.防止措施(1)选择合理工艺参数,调整半固态浆料的液相率。(2)增加内浇道和溢流槽面积,使内浇道处金属液流充填速度降低,并加大内浇道与铸件之间的
过渡圆角
。
(3)增设排气槽、溢流槽,充分排气,
及时清
除排气槽上的油污、废料
。
(4)
减少脱模剂的用量
。
二、缩孔、缩松缺陷
铸件凝固次序的一般规律是:较薄处及合金液
最先停止流动处往往最先凝固,较厚处及合金液体
流过时间最长及最后充型处往往最后凝固,而缩孔
与缩松的缺陷最易集中在铸件最后凝固的部位
。
镁合金液的凝固方式为结晶温度范围比较宽的
层状凝固,即由表及里逐层凝固。随着凝固的进行
,
金属的收缩也在不断地进行,结壳厚度不断增加
,
外部压力的作用越来越小,最后使铸件内部压力低
于外部压力造成内部真空,从而形成缩孔与缩松
缺陷
。
压铸件中大而集中的孔洞为缩孔,小而分散的
孔洞为缩松,缩松和缩孔的孔洞形状不规则、不光
滑,表面呈暗色(如图2所示),而气孔具有光滑的
表面,形状为圆形
。
1.
产生的原因
(1)铸件在凝固过程中,
因产生收缩且得不到
金属液补偿而造成空穴
。
(2)压射比压低,增压压力过低。
(3)模具设计不合理,
不能够建立合理的凝固
顺序
。
F
铸造
oundry
70
2011年第13期热处理/锻压/
铸造
热加工
图2铸件中的缩孔和缩松金相
(4)内浇道较薄、面积过小,过早凝固,
不利
于压力传递和金属液补缩
。
2.
防止措施
(1)降低浇注温度,减少收缩量。
(2)提高压射比压及增压压力。
(3)合理设计模具,建立顺序凝固条件,
使缩
孔与缩松排除于铸件外
。
(4)改变铸件结构,减少金属积聚,
使壁厚尽
可能均匀
。
三、夹杂
外形尺寸稍大,且不规则。用放大镜或肉眼有
时可明显观察到状态不规则,以及大小、颜色、高
度不同的夹杂物(见图
3)。
图3铸件中的夹杂扫描
1.
产生的原因
(1)熔炼不洁净,混入杂质太多。
(2)保温温度高且持续时间长,造成氧化夹杂。
(3)
石墨坩埚或涂料中含有石墨脱落混入金属
液中
。
2.
防止措施
(1)使用洁净的炉料,合金熔液需精炼除气,
将熔渣清除干净
。
(2)控制半固态浆料制备过程的保温温度,
减
少保温时间
。
(3)及时清理压室、型腔。
四、冷隔和充型不良
压铸件表面有明显的、不规则的、下陷线型纹
路和充型不满的现象
。
1.
冷隔和充型不良产生的原因
(1)填充速度低,压射比压低。
(2)半固态浆料固相率太高。
(3)内浇道横截面积太小。
(4)浇注位置不当或流路过长。
(5)合金液吸气,氧化夹杂物含量高,
使其质
量差而降低流动性
。
2.
防止措施
(1)正确选择填充速度和压射比压,
提高合金
的流动性
。
(2)
适当提高半固态浆料的制备温度,减少固
相率
。
(3)
加大内浇道的横截面积
。
(4)改善排气、填充条件。
(5)提高合金液的质量。
五、毛刺飞边
压铸件在分型面上出现的金属薄片
。
1.
产生的原因
(1)分型面上有杂物。
(2)
锁型力不够
。
(3)压射速度过高,形成压力过高。
(4)
半固态浆料的液相率过高
。
2.
防止措施
(1)清洁型腔和分型面。
(2)检查锁型力和增压情况,调整工艺参数。
(3)选择适当的压射速度。
(4)适当降低半固态浆料的制备温度,
减小其
液相率
。
六、结语
总之,镁合金半固态压铸件的质量与压铸设备的性
能、压铸工艺参数、铸型设计,以及镁液熔炼的质量有
关。如果压铸成形工艺参数选择不当,铸件易出现气
孔、冷隔、浇不足、裂纹、夹渣和性脆等铸造缺陷,我
们可以通过改善工艺、调整模具、合理设计、严格管理
等来减少缺陷,提高铸件的力学性能
。
(20110119)