材料力学课程设计之单缸柴油机曲轴的强度设计(doc 14页)
单缸四冲程柴油机设计及静力分析

题目二单缸四冲程柴油机设计一、机构简介及有关数据1、机构简介柴油机如图2-1所示,其中a)为机构简图,它将燃料(柴油)燃烧时所产生的热能转变为机械能。
往复式内燃机的主体机构为曲柄滑块机构,借气缸内的燃气压力推动活塞3,再通过连杆2使曲柄1作旋转运动。
往复式内燃机有两冲程和四冲程两种,本课程设计的是四冲程内燃机,即以活塞在气缸内往复移动四次(对应曲柄转两转)完成一个工作循环。
在一个工作循环中,气缸内的压力变化可通过示功图(或称容压曲线)如图2-1 b)看出,它表示气缸容积(与活塞位移s成正比)与压力的变化关系。
a) 机构简图b) 示功图图1 单缸四冲程柴油机的机构简图和示功图四冲程内燃机的工作原理如下:ϕ=→。
进气阀开,空进气冲程:活塞由上止点向下移动,对应曲柄转角000180气开始进入气缸,此时气缸内指示压力略低于1大气压力,一般以1大气压力计算,如示功图上的a b→。
ϕ=→。
此时进气完压缩冲程:活塞由下止点向上移动,对应曲柄转角00180360毕,进气阀闭,已吸入的空气受到压缩,压力渐升高,如示功图上的b c→。
膨胀(工作)冲程:在压缩冲程终了时,被压缩的空气的温度已超过柴油自燃的温度,因此,在高压下射入的柴油立刻爆炸燃烧,气缸内压力突增至最高点,此时燃气压力推动活塞由上向下移动对外作功(故又可称工作冲程),曲柄转角00ϕ=→,随着燃气的膨胀,活塞下行,气缸容积增加,压力逐渐降低,360540如示功图上的c b→。
ϕ=→。
排气阀开,废气经排排气冲程:活塞由下向上移动,曲柄转角00540720气阀门被驱除,此时气缸内压力略高于1大气压力,一般亦以1大气压力计算,如示功图上的b a →。
示功图中的a b c b a →→→→即表四个冲程气缸内的压力变化情况。
进、排气阀的启闭是由凸轮机构来控制的,图2-1 a )中y y -剖面有进、排气阀各一只(图示只画了进气凸轮)。
凸轮机构是通过曲柄轴O 上的齿轮Z 1和凸轮轴O 1的齿轮Z 2来传动的,由于一个工作循环中,曲柄转将转两转而进、排气阀则仅各启闭一次,所以齿轮的传动比1212212i n n Z Z ===。
曲轴设计课件

曲轴的8个曲柄在轴向成镜面对称,平衡块 重量相同能保证柴油机具有最小的内力矩和轴 承负荷。
6.2 工艺措施
1、圆角滚压强化:表面产生剩余压应力,抵消部分 工作拉伸应力,从而提高曲轴的疲劳强度。
2、圆角淬火强化:用热处理方法使金属发生组织相 变,体积膨胀而产生残余压应力,从而提高曲轴 疲劳强度。
4、曲轴的主要参数
依据中国农业机械出版社出版的《柴油机 设计手册》选择参数如下: 曲柄销直径:dp=0.75D=0.75×280=210 曲柄销长度:lp=0.60D=0.6×280=168 曲柄臂厚度:h=0.25D=0.25×280=70 曲柄臂宽度:b=1.1D=1.1×280=308 主轴颈直径:dj=0.9D=0.9×280=252 主轴颈长度:lj=0.4D=0.4×280=112 曲轴圆角半径:r=0.045D=0.045×280=12.6 取r=15
5、曲轴的其它结构设计
5.1 润滑油通道 主轴颈设置有中心内孔,连杆颈内有两对开油孔, 每一曲柄有2个斜油孔在连杆颈内相交,在自由端 轴颈锥面有一油孔与主轴颈油道相通。
5.2 曲轴两端轴段结构 曲轴自由端设有一段锥面,用于安装曲轴齿轮和 卷簧减震器。曲轴输出端轴段上有一整体法兰, 用于安装联轴节。
3、喷丸强化处理:与滚压强化的道理一样,属于冷 作硬化变形。
4、氮化处理:使氮气渗入零件表面,金属体积增大 而产生挤压应力。
曲轴设计
主要内容
1、总述 2、曲轴的材料和工艺 3、曲轴的结构设计 4、曲轴主要参数 5、曲轴其它结构设计 6、提高曲轴疲劳强度的措施
1、总述
曲轴是发动机 中最重要的机件之 一,它的成本大约 占整机成本的十分 之一。它的尺寸参
柴油机曲轴设计ppt资料

谢词
• 感谢童勇老师的指导和关怀 • 非常感谢同组同学在设计工作中给予的帮助、支持和鼓励 • 由衷感谢各位老师百忙中抽空参与答辩工作
曲轴X方向最大位移发生在第二连杆轴颈纵向对称面左侧, 结果如下图:
曲轴Y方向最大发生在第二连杆轴颈左端曲柄臂平衡块尾 部, 结果如下图:
曲轴Z方向最大位移发生在第二连杆轴颈上部,结果如下 图:
曲轴疲劳强度分析
• 经过计算,曲轴疲劳强度达到要求。
结论:
• 在通过VB程序,对490柴油机进行工作过程计算中得到相 关数据如下表: • 通过excel软件对490柴油机进行动力学分析得到,缸内最 大绝对压力为8.428115405,活塞最大速度为16.311,活 塞最大位移为0.99999596及其活塞位移、速度、加速度 曲线图。 • 曲轴的三维建模,强度校核,通过软件CATIA可知,曲轴 的许可绕度,L为曲轴两支承点的距离。计算可得,最大 挠度,所以曲轴的刚度满足设计要求。通过计算,曲轴疲 劳强度达到要求。
490柴油机பைடு நூலகம்轴设计
设计者:苏玉立 专业:热动(汽发) 学号:312009080501622 指导老师:童勇
设计的主要内容
• • • •
490柴油机工作过程计算 动力学分析 490柴油机曲轴基本设计 曲轴疲劳校核
1.490柴油机工作过程计算
根据VB编程计算结果如下
p v p v
经过VB程序计算,绘制图如下:
2.发动机动力学分析:
• 活塞位移图 • 活塞速度图 • 活塞加速度图
3.活塞的基本设计:
• 曲轴的结构形式; • 曲轴材料; • 曲轴主要尺寸确定和细节设计
4.曲轴疲劳强度校核
• 曲轴实体模型:
曲轴网格划分:
曲柄轴的强度设计,疲劳校核及刚度计算课程设计 刘晨

材料力学课程设计班级:机械工程系铁道车辆1班作者:刘晨(2014120892)题目:曲轴的强度设计、疲劳强度校核及刚度计算指导老师:任小平老师2016年6月9日目录一、课程设计的目的-------------------------------------------2二、课程设计的任务和要求---------------------------------3三、设计计算说明书的要求---------------------------------3四、分析讨论及说明部分的要求--------------------------4五、程序计算部分的要求------------------------------------4六、设计题目-----------------------------------------------------4七、设计内容-----------------------------------------------------5(一)画出曲柄轴的内力图-------------------------6(二)设计曲柄颈直径d,主轴颈直径D-------7(三)校核曲柄臂的强度-----------------------------8(四)校核主轴颈的疲劳强度----------------------11(五)用能量法计算A截面的转角---------------12(六)计算机程序--------------------------------------14八、设计的改进措施及方法------------------------------18九、设计体会--------------------------------------------------19十、参考文献--------------------------------------------------20一、课程设计的目的材料力学课程设计的目的是在于系统学习材料力学后,能结合工程中的实际问题,运用材料力学的基本理论和计算方法,独立地计算工程中的典型零部件,以达到综合运用材料力学的知识解决工程实际问题之目的。
材料力学课程设计——车床主轴设计共14页文档

材料力学课程设计班级:作者:题目:车床主轴设计指导老师:任小平2019.5.26一、课程设计的目的材料力学课程设计的目的是在于系统学习材料力学后,能结合工程中的实际问题,运用材料力学的基本理论和计算方法,独立地计算工程中的典型零部件,以达到综合运用材料力学的知识解决工程实际问题之目的。
同时,可以使我们将材料力学的理论和现代计算方法及手段融为一体。
既从整体上掌握了基本理论和现代的计算方法,又提高了分析问题,解决问题的能力;既把以前所学的知识综合应用,又为后继课程打下基础,并初步掌握工程中的设计思想和设计方法,对实际工作能力有所提高。
1)使所学的材料力学知识系统化,完整化。
让我们在系统全面复习的基础上,运用材料力学知识解决工程实际问题。
2)综合运用以前所学的各门课程的知识(高等数学、工程图学、理论力学、算法语言、计算机等),使相关学科的知识有机地联系起来。
3)使我们初步了解和掌握工程实践中的设计思想和设计方法,为后续课程的学习打下基础。
二、课程设计的任务和要求要系统复习材料力学课程的全部基本理论和方法,独立分析、判断设计题目的已知所求问题,画出受力分析计算简图和内力图,列出理论依据并导出计算公式,独立编制计算程序,通过计算机给出计算结果,并完成设计计算说明书。
三、设计题目某车床主轴尺寸及受力情况如图1所示。
在A、B、C三个支座的中间支座B 处,轴承与轴承座之间有间隙 ,正常工作时,B处轴承不起支撑作用,此时主轴处于A 、C 两支座下的静定状态。
当B 截面处弯曲变形大于间隙δ时,主轴处于A 、B 、C 三支座下的静不定状态。
轴截面E 处装有斜齿轮,其法向压力角为α,螺旋角为β,工作处的切削力有 、 、 (在进行强度、刚度计算时,可以不计轴向力 的影响,而以弯曲、扭转变形为主)。
轴的材料为优质碳素结构钢(45钢),表面磨削加工,氮化处理。
其他已知数据见表1。
1、试按静定梁(A 、C 支撑)的强度、刚度条件设计等截面空心圆轴外径 D(d/D 值可见数据表2),并计算这时轴上B 截面处的实际位移。
单缸四冲程柴油机机构设计 机械原理课程设计

机械原理课程设计说明书设计题目:单缸四冲程柴油机机构设计学院:机电工程学院专业:车辆工程班级: S1学号:2012126849设计者:黄通尧指导教师:王洪波提交日期:二○一四年七月1、机构简介柴油机是内燃机的一种,如图1所示。
它将柴油燃烧时所产生的热能转变为机械能。
往复式内燃机的主运动机构是曲柄滑块机构,以气缸内的燃气压力推动活塞3经连杆2而使曲柄1旋转。
图1 柴油机机构简图及示功图四冲程内燃机是以活塞在气缸内往复移动四次(对应于曲柄轴转两转)完成一个工作循环。
在一个工作循环中气缸内的压力变化可用示功器或压力传感器从气缸内测得,然后将压力与活塞位移的关系绘成曲线图,称为示功图,见图1(b)。
现将四冲程柴油机的压力变化关系作一粗略介绍:进气冲程:活塞下行,对应曲柄转角=0°—180°,进气阀开启,空气进入气缸。
汽缸内指示压力略低于1个大气压,一般可以1个大气压来计算。
进气结束时,进气阀关闭。
如示功图上的a一b段。
压缩冲程:活塞上行,对应曲柄转角=180°—360°,将进入气缸的空气压缩。
随着活塞的上移气缸内压力不断升高。
如示功图上的b一c段。
膨胀冲程:在压缩冲程结束前,被压缩空气的温度已超过柴油的自燃温度。
因此当高压油泵将柴油喷进燃烧室时,呈雾状细滴的柴油与高温空气相接触,立即爆炸燃烧,使气缸内的压力骤增至最高点。
燃气产生的高压推动活塞下行,通过连杆带动曲柄旋转对外作功。
对应曲柄转角=360°—540°,随着燃气的膨胀活塞下行气缸容积增大,气缸内压力逐渐降低,如示功图上c—d段。
排气冲程:排气阀开启,活塞上行将废气排出。
气缸内压力略高于1个大气压,一般亦以一个大气压计算。
对应曲柄转角=540°—720°,如示功图上d —a 段。
进、排气阀的开启是通过凸轮机构控制的。
凸轮机构是通过曲柄轴上的齿轮Z1和凸轮轴上的齿轮Z2来传动的。
本科毕业设计-柴油机曲轴设计

1前言1.1柴油机与曲轴1.1.1柴油机的工作原理柴油机的每个工作循环都要经历进气、压缩、做功和排气四个过程。
四行程柴油机的工作过程:柴油机在进气冲程吸入纯空气,在压缩冲程接近终了时,柴油经喷油泵将油压提高到10MPa以上,通过喷油器以雾状喷入气缸,在很短时间内与压缩后的高温空气混合,形成可燃混合气。
压缩终了时气缸内空气压力可达3.5~4.5MPa,温度高达476.85℃~726.85℃,极大地超过柴油的自燃温度,因此柴油喷人气缸后,在很短的时间内即着火燃烧,燃气压力急剧达到6~9MPa,温度升高到1726.85℃~2226.85℃。
在高压气体推动下,活塞向下运动并带动曲轴旋转做功。
废气同样经排气门、排气管等处排出。
四行程柴油机的每个工作循环均经过如下四个行程:(1)进气行程在这个行程中,进气门开启,排气门关闭,气缸与化油器相通,活塞由上止点向下止点移动,活塞上方容积增大,气缸内产生一定的真空度。
可燃混合气被吸人气缸内。
活塞行至下止点时,曲轴转过半周,进气门关闭,进气行程结束。
由于进气道的阻力,进气终了时气缸内的气体压力稍低于大气压,约为0.07~0.09MPa。
混合气进入气缸后,与气缸壁、活塞等高温机件接触,并与上一循环的高温残余废气相混合,所以温度上升到96.85℃~126.85℃。
(2)压缩行程进气行程结束后,进气门、排气门同时关闭。
曲轴继续旋转,活塞由下止点向上止点移动,活塞上方的容积缩小,进入到气缸中的混合气逐渐被压缩,使其温度、压力升高。
活塞到上止点时,压缩行程结束。
压缩终了时鼓,混合气温度约为326.85℃~426.85℃,压力一般为0.6~1.2MPa。
(3)做功行程活塞带动曲轴转动,曲轴通过转动把扭矩输出。
(4)排气行程进气口关闭,排气口打开,排除废气。
由上可知,四行程汽油机或柴油机,在一个工作循环中,只有一个行程作功,其余三个行程作为辅助行程都是为作功行程创造条件的。
因此,单缸发动机工作不平稳。
曲轴设计_??????
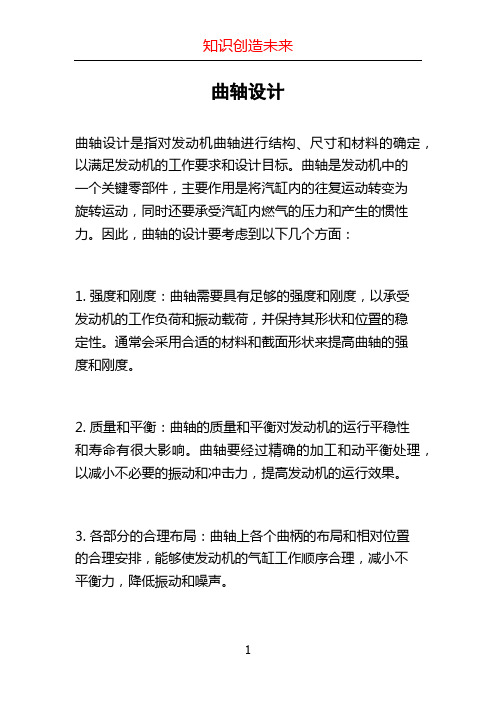
曲轴设计
曲轴设计是指对发动机曲轴进行结构、尺寸和材料的确定,以满足发动机的工作要求和设计目标。
曲轴是发动机中的
一个关键零部件,主要作用是将汽缸内的往复运动转变为
旋转运动,同时还要承受汽缸内燃气的压力和产生的惯性力。
因此,曲轴的设计要考虑到以下几个方面:
1. 强度和刚度:曲轴需要具有足够的强度和刚度,以承受
发动机的工作负荷和振动载荷,并保持其形状和位置的稳
定性。
通常会采用合适的材料和截面形状来提高曲轴的强
度和刚度。
2. 质量和平衡:曲轴的质量和平衡对发动机的运行平稳性
和寿命有很大影响。
曲轴要经过精确的加工和动平衡处理,以减小不必要的振动和冲击力,提高发动机的运行效果。
3. 各部分的合理布局:曲轴上各个曲柄的布局和相对位置
的合理安排,能够使发动机的气缸工作顺序合理,减小不
平衡力,降低振动和噪声。
4. 磨削和表面处理:曲轴的磨削和表面处理对减小摩擦损失和延长使用寿命有很大影响。
磨削工艺要尽量减小表面粗糙度,提高曲轴的表面质量,同时可以采用表面硬化等处理方法来提高曲轴的耐磨性和抗疲劳性。
总之,曲轴设计需要综合考虑发动机的工作要求、性能指标和制造工艺等因素,以确保曲轴能够满足发动机的工作需要,并具有良好的强度、刚度、平衡性和耐用性。
- 1、下载文档前请自行甄别文档内容的完整性,平台不提供额外的编辑、内容补充、找答案等附加服务。
- 2、"仅部分预览"的文档,不可在线预览部分如存在完整性等问题,可反馈申请退款(可完整预览的文档不适用该条件!)。
- 3、如文档侵犯您的权益,请联系客服反馈,我们会尽快为您处理(人工客服工作时间:9:00-18:30)。
材料力学课程设计 班级: 作者: 题目:单缸柴油机曲轴的强度设计 及刚度计算、疲劳强度校核 指导老师:
2007.11.05 一、 课程设计的目的 材料力学课程设计的目的是在于系统学习材料力学后,能结合工程中的实际问题,运用材料力学的基本理论和计算方法,独立地计算工程中的典型零部件,以达到综合运用材料力学的知识解决工程实际问题之目的。同时,可以使我们将材料力学的理论和现代计算方法及手段融为一体。既从整体上掌握了基本理论和现代的计算方法,又提高了分析问题,解决问题的能力;既把以前所学的知识综合应用,又为后继课程打下基础,并初步掌握工程中的设计思想和设计方法,对实际工作能力有所提高。 1)使所学的材料力学知识系统化,完整化。让我们在系统全面复习的基础上,运用材料力学知识解决工程实际问题。 2)综合运用以前所学的各门课程的知识(高等数学、工程图学、理论力学、算法语言、计算机等),使相关学科的知识有机地联系起来。 3)使我们初步了解和掌握工程实践中的设计思想和设计方法,为后续课程的学习打下基础。 二、课程设计的任务和要求
要系统复习材料力学课程的全部基本理论和方法,独立分析、判断设计题目的已知所求问题,画出受力分析计算简图和内力图,列出理论依据并导出计算公式,独立编制计算程序,通过计算机给出计算结果,并完成设计计算说明书。 三、 设计题目 某柴油机曲轴可以简化为下图所示的结构,材料为球墨铸铁(QT450-5)弹性常数为E、μ,许用应力为[σ],G处输入转矩为eM,曲轴颈中点受切向力tF 、径向力rF的作用,且rF=2tF。曲柄臂简化为矩形截面,1.4≤hD≤1.6,2.5≤hb≤4, 3l=1.2r,已知数据如下表:
1/lm 2/lm /EGpa /Mpa 1/Mpa 0.11 0.18 150 0.27 120 180
/PkW /(/min)nr /rm
0.05 0.78 15.5 280 0.06
(一) 画出曲轴的内力图。 (二) 设计曲轴颈直径d,主轴颈直径D。 (三) 校核曲柄臂的强度。 (四) 校核主轴颈H-H截面处的疲劳强度,取疲劳安全系数n=2。键槽为端铣 加工,主轴颈表面为车削加工。 (五) 用能量法计算A-A截面的转角y,z。 3 / 15
1、 画出曲轴的内力图
(1) 外力分析 画出曲轴的计算简图,计算外力偶矩
Me=9549pn=9549*10.5100=1003Nm
tF
=eMr=16717N
rF=2tF=8358N 计算反力 在XOY平面内:AyF=212rFlll=5188N FyF=112rFlll=3170N 在XOE平面内:AzF=212tFlll=10376N FzF=112tFlll=6341N (2) 内力分析 ①主轴颈的EG左端(1-1)截面最危险,受扭转和两向弯曲
1XM=m=1003Nm
1YM=FzF*(2l–32l)=913Nm
1ZM=FyF*(2l–32l)=456Nm
②曲柄臂DE段下端(2-2)截面最危险,受扭转、两向弯曲和压缩 2XM=m=1003Nm
2YM=FzF*(2l–32l)=913Nm
2ZM=FyF*(2l–32l)=456Nm
2NF=FyF=3170N
③曲柄颈CD段中间截面(3-3)最危险,受扭转和两向弯曲
3XM=AzF*r=623Nm
3YM=AzF*1l=1141Nm
3ZM=AyF*1l=571Nm
(1) 图如下图(不计内力弯曲切应力,弯矩图画在受压侧): (单位: 力—N 力矩—Nm) yxM768768
1141913
913
M623
10031003 NF51883170
zM384384
571456
456
1、 设计曲轴颈直径d和主轴颈直径D (1)主轴颈的危险截面为EF的最左端,受扭转和两向弯曲 根据主轴颈的受力状态,可用第三强度理论计算
3r=112222111()MxMyMz≤[]
其中11=332D 得D≥49.5mm取D=50mm (2)曲柄颈CD属于圆轴弯扭组合变形,由第三强度理论,在危险截面1-1中:
222333331rXYZMMMW 222333332XYZMMMd 2223326231141571120MPad 得 49.4dmm 故取 50dmm 1、 校核曲柄臂的强度 (1)(具体求解通过C语言可得,见附录) 由程序得h,b的最佳值为 72.32hmm,28.92bmm。
查表得 0.258,0.767 (2)曲柄臂的强度计算 曲柄臂的危险截面为矩形截面,且受扭转、两向弯曲及轴力作用(不计剪
力QF),曲柄臂上的危险截面2-2的应力分布图如下图:
根据应力分布图可判定出可能的危险点为1D,2D,3D。 8 / 15 1D点: 1D点处于单向应力状态
222222NXZXZFMMAWW
22266FyZFmMhbhbhb 50.73[]MPa 所以1D点满足强度条件。 2D点: 2D点处于二向应力状态,存在扭转切应力
222991358.50.25872.3228.9210yMMPahb 2D点的正应力为轴向力和绕z轴的弯矩共同引起的 2222NZZFMAW
226FyZFMhbhb
6293170645646.75[]72.3228.921072.3228.9210MPa
由第三强度理论
22223446.75458.5125.99[]rMPa
∵ 125.99120100%4.996%5%120 所以2D点满足强度条件。 3D点: 3D点处于二向应力状态
'0.76758.544.87MPa
2222'NXXFMAW
26FyeFMhbhb 62931706100341.30372.3228.921028.9272.3210MPa 根据第三强度理论 22223'4'41.303444.8798.789[]rMPa
所以3D点满足强度条件。 ➢ 综上,曲柄臂满足强度条件。 1、 校核主轴颈H-H截面处的疲劳强度
由题意 450bMPa 查表得 1.43K 0.9438 已知 1180MPa 0.78 0.05 2n FH处只受扭转作用
11min3391652942.104.001016xxpMMMPaDW
max0 minmaxr 所以,扭转切应力为脉动循环。 min2am
min42.1021.0522amMPa
安全系数11804.521.4321.050.0521.050.780.9438amnnK
所以,H-H截面的疲劳强度足够。
1、 用能量法计算A-A截面的转角y,z 采用图乘法分别求解A-A截面的转角y,z。 (1) 求y: 在截面A加一单位力偶矩yM。并作出单位力偶矩作用下的弯矩图
yM 与外载荷作用下的弯矩图yM如下(画在受压一侧):
10.7450.497
0.497
9139131141768
768My
由平衡方程得12113.4480.110.18AzFzFFNll B点的弯矩为3113.4480.110.0360.7452llNm E点的弯矩为323.4480.180.0360.4972EFzlMFlNm 由图乘法: 72.32hmm,28.92bmm 查表得 0.249
441294150101501045996.196464DEIEpam