钢包下渣检测技术在济钢三炼钢的应用_黄绍伟
渣洗工艺应用实践

渣洗工艺应用实践提高精炼比是我国钢铁工业提高产品质量的重要手段之一。
业内资深专家在国内有关炼钢、连铸生产会议上曾着重指出,建立高效、低成本洁净钢生产平台,是今后几年国内钢铁企业都应努力实现的基本目标之一。
建立洁净钢生产平台不能仅注重高端产品的研发,更应努力提高量大、面广的钢材产品的质量和生产效率,降低生产成本。
近年来,有关钢铁企业在注重发挥精炼装置功效的同时,也根据钢种生产实际积极研究并采用经济实用的渣洗工艺来净化钢水,并注意处理和解决应用过程中遇到的一些具体问题,收到了降低精炼成本、优化冶炼效果、提升整体效益的效果。
据中国金属学会专家介绍,渣洗就是用预熔型渣来处理钢液的一种炉外处理方法。
渣洗是获得洁净钢的简单有效的精炼手段,以去除夹杂、净化钢液为目的。
在出钢过程中加入特殊配比的渣洗料,可有效吸附夹杂。
依靠良好的钢包底吹搅拌和钢流搅拌,可以使迅速溶化的渣洗料和钢液充分接触,液态的渣洗料液滴能立即与脱氧产物结合、吸附并快速上浮排除,实现净化钢液、提高钢水质量、改善钢水流动性的目标。
在这些方面,有关钢铁企业积极采用渣洗工艺来降低精炼运行成本,效果明显,实现了优化冶炼和降低成本同行。
德龙钢铁有限公司经过积极探索,采用直上渣洗工艺,在不经过LF精炼炉处理的情况下,开发了低成本生产低碳低硅铝镇静钢SPHC的工艺。
实践证明,直上渣洗工艺可有效解决铝镇静钢钢水流动性差的技术难题,冷轧产品性能优良,可完全满足质量要求。
华东某重点钢铁企业采用直上渣洗料,通过实施渣洗工艺来净化钢水、脱氧,在降低精炼成本的同时,经过渣洗工艺处理的钢水直接上连铸,既不改变原有的炼钢-连铸生产工艺布置,又满足了快节奏生产的需要。
江西某钢铁企业通过应用新型渣洗料和渣洗工艺,在不改变原有转炉、连铸生产节奏的情况下,经过渣洗后的钢水直接连铸,满足了降低精炼成本、适应炼钢和连铸快节奏生产的双重需要,经济效益明显。
据有关人士介绍,渣洗的主要功能如下:一是净化钢液。
声纳化渣技术

Thank You
碳素结构钢Leabharlann 碳素结构钢包括: (a) Q195; (b)Q215(A、B) (c) Q235(A、B、C); (d) Q255(A、B); (e) Q275。
钢的牌号
钢的牌号简称钢号,是对每一种具 体钢产品所取的名称,是人们了解钢 的一种共同语言。我国的钢号表示方 法,根据国家标准《钢铁产品牌号表 示方法》(GB221-79)中规定,采 用汉语拼音字母、化学元素符号和阿 拉伯数字相结合的方法表示。
目前,在较多的钢铁厂中已装 备了各种炉料的称量系统、氧气 及温度等检测装置,但对转炉炼 钢过程本身的检测系统至今仍属 空白。操作者在很大程度上仍然 耳闻目测靠经验来炼钢。因此, 研制一种能正确检测炉内情况的 技术一定会受到炼钢厂的欢迎。
随着计算机技术突飞猛进的 发展,在国内外先进经验和教训 的基础上,转炉声纳微机监控造 渣技术的研究,终于取得了突破 性的进展,获得了满意的结果。
铁皮降温;如有喷溅趋向,则加少量石灰抑制。 ③曲线位置较低或向下发展。说明枪位偏低,应逐渐提高枪位,做
应用效果
应用声纳化渣技术,为转炉造渣 提供了基本模式,改变了以往紧凭肉 眼看火的经验操作法,大大减小了喷 溅和返干的发生,喷溅和返干预警命 中率分别大于85%和90%,使金属吹 损和渣料消耗降低通过对取声装置的 改造,大大提高了设备运行完好率与 检测精度。
系统由三部分组成,分别是(1) 声处理器(主机);(2)拾 音器;(3)配水、配气系统。它们的作用分别是:
1. 声处理器对拾音器采集的信号进行放大处理,获得一 个与渣平面相对应的信号分送往工业控计算机或可编程控 制器。 2. 拾音器用来采集炉渣噪声,但因其工作在高温区域,所 以必须给它增加水冷和惰性气体(氮气)保护装置。 3. 配水、气是为探头(拾音器)保护装置配水和气的系统。
漫谈LF高效精炼技术的发展
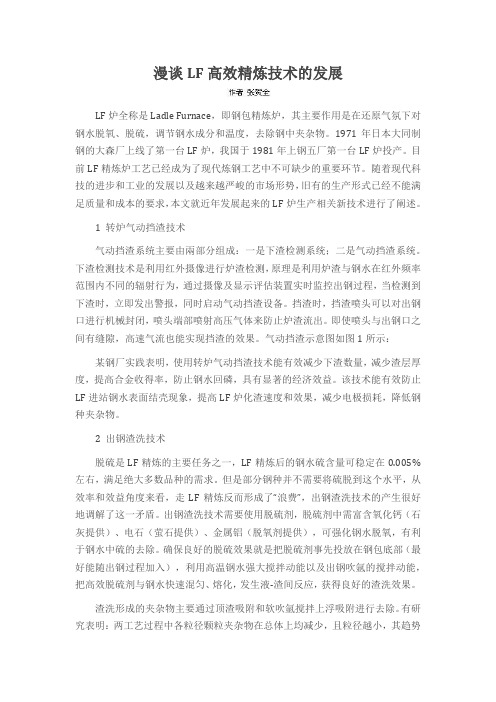
漫谈LF高效精炼技术的发展LF炉全称是Ladle Furnace,即钢包精炼炉,其主要作用是在还原气氛下对钢水脱氧、脱硫,调节钢水成分和温度,去除钢中夹杂物。
1971年日本大同制钢的大森厂上线了第一台LF炉,我国于1981年上钢五厂第一台LF炉投产。
目前LF精炼炉工艺已经成为了现代炼钢工艺中不可缺少的重要环节。
随着现代科技的进步和工业的发展以及越来越严峻的市场形势,旧有的生产形式已经不能满足质量和成本的要求,本文就近年发展起来的LF炉生产相关新技术进行了阐述。
1 转炉气动挡渣技术气动挡渣系统主要由兩部分组成:一是下渣检测系统;二是气动挡渣系统。
下渣检测技术是利用红外摄像进行炉渣检测,原理是利用炉渣与钢水在红外频率范围内不同的辐射行为,通过摄像及显示评估装置实时监控出钢过程,当检测到下渣时,立即发出警报,同时启动气动挡渣设备。
挡渣时,挡渣喷头可以对出钢口进行机械封闭,喷头端部喷射高压气体来防止炉渣流出。
即使喷头与出钢口之间有缝隙,高速气流也能实现挡渣的效果。
气动挡渣示意图如图1所示:某钢厂实践表明,使用转炉气动挡渣技术能有效减少下渣数量,减少渣层厚度,提高合金收得率,防止钢水回磷,具有显著的经济效益。
该技术能有效防止LF进站钢水表面结壳现象,提高LF炉化渣速度和效果,减少电极损耗,降低钢种夹杂物。
2 出钢渣洗技术脱硫是LF精炼的主要任务之一,LF精炼后的钢水硫含量可稳定在0.005%左右,满足绝大多数品种的需求。
但是部分钢种并不需要将硫脱到这个水平,从效率和效益角度来看,走LF精炼反而形成了“浪费”,出钢渣洗技术的产生很好地调解了这一矛盾。
出钢渣洗技术需要使用脱硫剂,脱硫剂中需富含氧化钙(石灰提供)、电石(萤石提供)、金属铝(脱氧剂提供),可强化钢水脱氧,有利于钢水中硫的去除。
确保良好的脱硫效果就是把脱硫剂事先投放在钢包底部(最好能随出钢过程加入),利用高温钢水强大搅拌动能以及出钢吹氩的搅拌动能,把高效脱硫剂与钢水快速混匀、熔化,发生液-渣间反应,获得良好的渣洗效果。
超声波检测技术在钢铁冶炼中的应用研究

超声波检测技术在钢铁冶炼中的应用研究随着钢铁产业的发展,冶炼工艺和设备不断更新迭代。
其中,超声波检测技术在钢铁冶炼中的应用,成为了当前研究的焦点之一。
本文将着重介绍超声波检测技术在钢铁冶炼中的应用及其研究进展。
一、超声波检测技术在钢铁冶炼中的应用超声波检测技术是指利用超声波对材料进行无损检测的技术,该技术在钢铁冶炼中有广泛应用。
主要分为以下几个方面。
(一)连铸过程中的应用钢铁连铸工艺中,温度和流动状态是关键的控制参数,超声波检测技术可以用于实时检测铸坯物流状态、气泡大小和数量等,帮助操作人员及时调整工艺参数,保证铸坯质量。
(二)熔铁预测采用超声波检测技术,可以通过测量炉前料层和炉后气泡来预测炉内熔铁温度,提高铁水出铁质量和效率。
(三)铁水净化过程中的应用在铁水净化过程中,超声波检测技术可以识别气泡、杂质和其他不良因素,促进铁水净化,并提高铁水质量。
同时,它还可以检测喷洒的液体流动情况,以确定铁水在净化过程中是否均匀。
二、超声波检测技术在钢铁冶炼中的研究进展随着钢铁产业的不断发展,人们对超声波检测技术在钢铁冶炼中的应用不断深入研究。
下面介绍一下近期的研究进展。
(一)超声波相控阵成像技术超声波相控阵成像技术是一种高精度的无损检测技术,可用于测量材料的几何参数、皮层厚度、裂纹等缺陷。
在钢铁冶炼中,应用超声波相控阵成像技术,可以直观地观察炉内铁水流动状态、气泡情况等,为操作人员提供重要参考。
(二)多参数超声波探头开发针对钢铁冶炼中多种不同的材料和工艺参数,研究人员正在开发多参数超声波探头,以适应更多的应用场景。
例如,针对炉前料层测量,可以开发具有高分辨率和抗干扰能力的超声波探头。
(三)基于神经网络的缺陷检测模型随着人工智能技术的不断发展,研究人员开始将神经网络算法应用于超声波检测中。
根据不同的检测场景,采用不同的神经网络结构,在钢铁冶炼中实现高精度的缺陷检测。
三、结语总之,超声波检测技术在钢铁冶炼中具有重要的应用价值,可以提高钢铁生产的效率和产品质量,降低生产成本。
钢包炉LF用预熔精炼渣的研究和应用

1253.6
1266.3
3760.3
1231.6
1239.7
1244.6
3715.9
1293.6
1269.5
1278
3841.1
1259.3
1269.5
1296.7
3825.5
1269.5
1282.5
1248
3800
1272.1
1308.9
1286.3
3867.3
1247.3
1258.6
1264.4
实验号
1 2 3 4 5 6 7 8 9 10 11 12 13 14 15 16
熔化温度(℃)
1
2
3
合计si (℃)
1295.3
1325.3
1339.5
3960.1
1322.3
1298.7
1307
3928
1303
1298.7
1303
3904.7
1293.7
1290.3
1308.7
3892.7
1240.4
R 45.225 9.041667 17.08333 19.35 22.38333
第一列(A因素) R=1307.1-1261.9=42.2 第二列(B因素) R=1290.6-1281.5=9.1 第三列(C因素) R=1295.1-1278.0=17.1 第四列(D因素) R=1295.6-1276.2=19.4 第五列(E因素) R=1296.6-1274.2=22.2
中,其在它A1因、素A2(、B、A3C、、AD4各和自E)的所1在、的2、实3验、组4 水平都分别出现了一次。把第一组实验所得 的实验数据相加,其和记作I,同理,把第 二组、第三组、第四组的数据相加分别记作 II、III和IV。
转炉下渣检测系统在南钢的应用

龙源期刊网
转炉下渣检测系统在南钢的应用
作者:朱宁岐
来源:《现代商贸工业》2012年第23期
摘要:随着低磷钢种的需求大大增加,降低钢水磷含量问题成为目前转炉炼钢的一个主要课题。
为此我们引入了下渣检测系统。
该系统使用红外线摄像头,在现场监视器上可以显示实时钢流图像。
当出钢期间下渣时,通过画面色彩明显改变及声光报警。
提示出钢操作工钢流中存在夹渣或下渣。
从而既能够保证钢水最大限度的出尽,又能最大限度的减少下渣量,减少钢水回磷,避免磷超标准的事故发生。
关键词:钢水磷含量;转炉;下渣检测
中图分类号:TB文献标识码:A文章编号:1672-3198(2012)23-0229-02
1前言
近年来,用户对高等级别的钢种,尤其是低磷钢种的需求大大增加,如高等级管线钢、石油储罐用钢等,这些高等级别产品对钢中磷含量要求很严。
因此降低钢水磷含量问题成为目前炼钢工作者的一个主要工作内容。
降低钢水磷含量的主要渠道是减少转炉出钢时的下渣。
在转炉出钢过程中进行有效的挡渣操作,可以减少钢水回磷;提高钢水收得率;还能减少钢水中夹杂物;提高钢水清洁度;减少合金元素的使用量,提高合金回收率;并可减少钢包粘渣,延长钢包使用寿命。
与此同时亦可减少耐材消耗,相应提高转炉出钢口耐火材料的使用寿命,还可为钢水精炼提供良好的条件。
2目前常用的挡渣方法。
板坯连铸大包下渣自动检测技术探索与实践
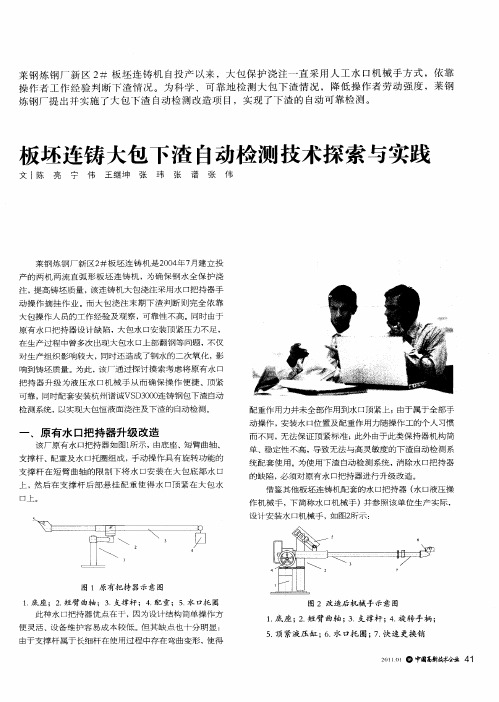
注 , 高 铸 坯 质 量 , 连 铸 机 大 包 浇 注 采 用 水 口把 持 器 手 提 该 动 操 作 摘 挂 作 业 。而 大 包 浇 注 末 期 下 渣 判 断 则 完 全 依 靠 大 包 操 作 人 员 的 工 作 经 验 及 观 察 ,可 靠 性 不 高 。同 时 由 于
原有 水 口把持 器设计缺 陷 , 大包 水 口安装顶 紧压 力不 足 ,
振 动来 完成 检测 。该 系统可 有效控 制杜 绝原 有人工 下 渣
检 测带 来的 种种 弊 端 。
三 、下渣 自动检测 系统工作原理
VS O O 铸 钢 包 下 渣 自动 监 测 系 统 通 过 感 受 机 械 D3 0 连 操 作 臂 的 振 动 来 检 测 连 铸 过 程 中的 下 渣 。在 钢 水 浇 注 过 程 中 , 水 流 经 长 水 口注 入 中 间 包 时 , 水 冲 击 长 水 口壁 钢 钢
在 生 产 过 程 中 曾 多次 出现 大 包 水 口上 部 翻 钢 等 问题 ,不 仅 对 生 产 组 织 影 响 较 大 ,同时 还 造 成 了 钢 水 的 二 次 氧 化 , 影
响 到 铸 坯 质 量 。为 此 , 厂 通 过 探 讨 摸 索 考 虑 将 原 有 水 口 该 把 持 器 升 级 为 液 压 水 口机 械 手 从 而 确 保 操 作 便 捷 、顶 紧 可 靠 ,同时 配 套 安 装 杭 州 谱 诚 VS 0 0 铸 钢 包 下 碴 自动 D3 0 连 检 测 系统 ,以实 现 大 包 恒 液 面 浇 注 及 下 渣 的 自动 检 测 。
比 重 相 差 较 大 , 动 粘 度 也 不 相 同 , 以 在 混 有 钢 渣 的 钢 流 所
流 穿过 长 水 口时 会 表 现 出 不 同 的振 动 特 性 系统 的 传 感 器
炼钢精炼炉钢包底吹控制系统改造分析

71C omputer automation计算机自动化炼钢精炼炉钢包底吹控制系统改造分析沈江珠(酒钢集团榆中钢铁有限公司,甘肃 兰州 730104)摘 要:随着当前炼钢行业的不断发展进步,其冶炼工艺技术基于创新手段,极大的提高了冶炼产品质量和生产效率。
而钢包底吹作为冶炼工艺中的重要环节,现有炼钢精炼炉钢包底吹控制系统已经不能完全满足现代化工艺生产需求,必须要对原有控制系统进行一定的优化和改造,保障钢包底吹控制系统具有良好的实施效果,提高氩气流量控制的合理性。
因此本文从硬件配置以及PLC 编程角度出发,在原有控制系统管理基础上,对其进行优化改造,旨在更好的促进炼钢精炼炉钢包底吹控制系统满足生产工艺要求,进一步提高生产效率和效益。
关键词:炼钢精炼炉;钢包底吹;控制系统;改造中图分类号:TF769 文献标识码:A 文章编号:11-5004(2020)16-0071-2收稿日期:2020-08作者简介:沈江珠,男,生于1987年, 汉族, 甘肃临夏回族自治州人,本科,助工,研究方向:冶金工程。
钢包底吹是炼钢精炼炉在生产成品钢时,不可或缺的重要工艺手段。
其主要作用是通过搅拌和气洗钢水,以防止出现钢水氧化。
通常情况下,在开展钢包底吹工艺时,对精炼钢水质量影响最大的因素即是氩气流量的控制。
如氩气流量相对较大,则会导致穿液面发生严重的喷溅现象,从而致使钢水出现裸露氧化,致使夹杂物大量增加。
而如果吹氩气的流量较小,则会造成流量不够稳定、无法开展快速搅拌,不能完全的去除气体和夹杂物,影响炼钢过程的质量。
1 钢包底吹控制系统的原理炼钢精炼炉的钢包底吹控制系统改造的前提是了解和掌握其具体的工作原理。
一般情况下,钢包底吹控制系统是由两套氩气控制阀而组成,分别控制两组钢包底吹工艺的开展。
同时配备流量调节电磁阀,当其打开时,会产生对应的流量值。
而电磁阀的动作则是根据氩气流量工艺的实际要求而决定的,即是在HMI 设定炼钢工艺所需输出的流量值,通过计算后,能够准确得到电磁阀的动作状态,打开相应的阀而关闭其他无关阀。
- 1、下载文档前请自行甄别文档内容的完整性,平台不提供额外的编辑、内容补充、找答案等附加服务。
- 2、"仅部分预览"的文档,不可在线预览部分如存在完整性等问题,可反馈申请退款(可完整预览的文档不适用该条件!)。
- 3、如文档侵犯您的权益,请联系客服反馈,我们会尽快为您处理(人工客服工作时间:9:00-18:30)。
钢包下渣检测技术在济钢三炼钢的应用ApplicationofSlagCarry-overDetectionSystemforLadleinNo.1CCMofJisteel
黄绍伟(济南钢铁集团总公司第三炼钢厂,山东济南250101)
摘 要:本文叙述了济钢第三炼钢厂1#连铸采用的电磁法下渣检测的原理及使用效果,钢包下渣检测已成为现代连铸生产和质量控制的重要技术之一,它对防止钢包过量下渣、提高钢水纯净度,提高连铸钢水浇铸收得率、改善大包操作工的劳动强度和工作环境均有明显的效果,使用钢包下渣检测技术不仅提高了连铸生产的自动化水平,同时可以获得明显的经济效益。关键词:连铸;钢包;下渣检测
1 引言在连续铸钢的生产过程中,当钢包中含氧化铁,氧化锰和氧化硅的炉渣流入中间包以后,会造成钢水中铝和钛等易氧化合金元素的烧损,并产生氧化铝夹杂物,影响钢水的纯净度,并最终造成冷轧钢板的表面质量问题,此外钢水中的氧化铝夹杂还会造成水口堵塞,影响结晶器内的流场以及中间包连浇炉数。为了避免钢包中的炉渣进入中间包,在生产对钢质纯净度要求非常严格的钢种如汽车板时有些钢厂采用钢包留钢操作,这样虽然满足了质量要求,但钢水的收得率低。传统的通过目视来判定钢包下渣的方法误差大,由于每个操作工的经验都不一样,有的明显提早关闭滑板,有的在明显下渣时才关闭滑板,这样钢水质量波动大。为了有效控制连铸过程的钢包下渣,国外一些公司开发了钢包下渣自动检测装置,比较有代表性是德国AMEPA公司开发的电磁感应法下渣检测技术和美国ADVENT公司开发的声振法下渣检测技术。目前工业大生产中应用的下渣检测装置中90%以上采用的是AMEPA公司的电磁感应法下渣检测技术。济钢第三炼钢厂1#连铸机投产后即使用AMEPA公司的下渣自动检测技术。1 电磁感应法下渣检测的原理电磁法下渣检测技术就是在大包包底上水口外围装上传感器(一级和二级线圈),当钢液通过接交流电的线圈时,就会产生涡流,这些涡流可改变磁场的强度,由于炉渣的电导率显著低于钢液的电导率,仅为钢液电导率的千分之一,如果钢流中含有少量炉渣,涡流就会减弱,而磁场就会增强,如图1所示,磁场强度的变化可通过二级线圈产生的电压来检测。这种低电压信号经放大处理后,可以显示出带渣量的多少,达到报警的设定值时系统就会产生报警并关闭钢包滑动水口。传感器的灵敏度、传感器安装精度以及系统的抗干扰能力是获得稳定的下渣信号的关键。只有获得稳定的下渣信号,才能确保系统工作的可靠性和精度。
图1 电磁法下渣检测的原理2 下渣检测系统的构成下渣检测系统的组成部分及其它们之间的相互关系的框图如图2所示。
图2 下渣检测系统框图系统的工作过程大致如下:传感器实际上是一组同心线圈,它包括一个初级回路(或称发射部分)和一个次级回路(或称接收部分),它将由于不同感应电流而产生的电压信号送往前置放大器PA100,该电压信号在前置放大器中被放大并转换成一个比例电流信号,带微处理器的中央处理器MCU100对比例电流信号进行处理,并将处理后的值分别送往接口单元IFI和外围(就地)显示和控制单元PICU100。渣信号连续地与设定的报警极限值进行比较,如果检测到“渣信号”,系统便立即报警并通过接口单元控制滑动水口;若“渣信号”不在报警范围内,系统便不被“激活”。
48 《计量与测试技术》2008年第35卷第8期济钢第三炼钢厂是2003年投产的大型全连铸转炉炼钢厂,装采用了当代连铸领域内的多项先进技术,如全密封保护浇铸、结晶器液面自动控制、结晶器在线调宽及软夹紧、漏钢预报、二冷水自动控制等。配备大包下渣检测装置,其设备随铸机一起从国外成套引进。该系统的测量周期流程如图3所示。图3 测量周期流程图一旦系统启动,测量周期便连续运行,运行的前提条件是系统通过自检并确认无故障。来自传感器的信号通过微处理器中计算机进行处理,当检测到渣信息时,在中央处理单元和就地控制单元以光柱的形式显示,同时控制大包滑动水口关闭,本次浇铸结束。该装置投运以来,对三炼钢厂的生产起到了积极的作用,主要表现在以下几个方面:(1)按照预报响应时间不大于315s的要求,使大包中的残余钢水量减少,提高了钢水的收得率。(2)由于流入到中间包的渣量减少,使钢水的洁净度得到改善,铸坯“夹渣”现象减少,坯质量有了较大的提高。(3)渣量的减少,减小了对耐火材料的侵蚀程度,延长中间罐的使用铸命,增加连浇炉数,提高了铸机的作业率。3 影响下渣检测信号的因素下渣信号的强弱与钢流中的带渣量以及渣在钢流中的分布有关,渣在钢流中的分布状态有3种类型如图4所示,一是渣位于钢流的中央,二是渣在钢流中均匀分布,三是渣分布在钢流的表面,图2中列出了3种状态下渣信号与渣的比例的关系,可以看出不管在哪种状态下随着渣的比例的增加,下渣信号也随之增强,也就是说,渣信号与钢流中的带渣量是明显相关的,同时也不难发现,状态三的下渣是最容易检测的,很少下渣比例就会产生很强的下渣信号,状态二与状态三相比下渣信号略差一些,最难检测的是状态一,下渣比例为20%时才能产生约5%的下渣信号。据报道,渣在钢流中的分布是很复杂的,不同的钢厂、不同的钢包、不同的工艺条件均可能产生不同的分布状态,因此要精确定量测量出钢流中渣的比例几乎是不可能的。事实上,渣的比例从0%上升至100%只有几秒钟时间,因此报警值设定在多少已不是特别重要了,重要的是钢包滑动水口的关闭速度。在钢包浇铸过程中,由于温度的上升,线圈的电压和电流会逐渐变小,但变化的幅度最大不会超过20%,如果变化过大,说明有故障存在如绝缘不良、插头接触不好等。当钢包水口内结瘤时会导致下渣信号变弱,有时下渣信号甚至达不到设定值。另外如果人工提前关闭钢包滑板,也不可能出现下渣信号。有时会过早发生下渣报警,影响因素有:钢渣异常卷入钢流、周围环境的其他信号干扰以及接触不良造成的信号波动等。
图4 渣在钢流中的不同分布对渣信号的影响4 增加钢包下渣检测装置的运行效果自2003年9月第三炼钢厂1#连铸钢包下渣检测装置正常投入大生产应用后,对于纯净度要求较高的钢种在大包浇铸末期不用留钢操作了,完全由下渣检测装置自动判定并关闭滑动水口,带来的最明显的效果就是连铸收得率的提高,收得率平均比以前提高0.4%,平均每炉钢可减少留钢约1t。中间包连浇8炉后,渣层厚度不超过50mm。同时减轻了大包操作工的劳动强度,改善了操作工的工作环境。5 结语钢包下渣检测已成为现代连铸生产和质量控制的重要技术之一,它对防止钢包过量下渣、提高钢水纯净度,提高连铸钢水浇铸收得率、改善大包操作工的劳动强度和工作环境均有明显的效果,使用下渣检测技术不仅提高了连铸生产的自动化水平,同时可以获得明显的经济效益.济钢三炼钢1#连铸应用钢包下渣检测装置后,收得率平均提高了约0.4%。参考文献[1]DLWalker,SDawson,NDGMountford.Thedevelopmentoful-trosonicsensorsfortheearlydetectionofslagcarryover[J].IronandSteel-maker,1990,23(9):59264.[2]李培玉,赵明祥.连铸下渣检测方法的研究与进展[J].炼钢,2003,19(3):16222.[3]邱东明.300t连铸钢包下渣检测系统的研制.仪器计仪表学报,1998,19(1).
黄绍伟:钢包下渣检测技术在济钢三炼钢的应用
49 汞柱式血压计常见故障及排除方法探讨DiscussionintheCommonBreakdownsandSolutionsoftheMercurySphygmomanormeter
董万科(陕西省宝鸡市计量测试所,陕西宝鸡721000)
摘 要:本文对汞柱式血压计常见故障进行了分析,并给出了故障维修方法。关键词:汞柱式血压计;常见故障;维修方法
汞柱式血压计由于价格便宜,计量性能稳定,便于维修等特点,深受各医疗机构和个人家庭的欢迎,也是目前常见血压计中使用最为普遍的一种,结合本人实际工作经验现将该类血压计的常见故障及排除方法加以探讨,谨供同行参考。1 灵敏度差原因分析:汞柱式血压计在快速造压停止或快速降压停止时,汞柱都会上下波动,这表明该血压计的灵敏度较高,如果不产生波动则说明该血压计灵敏度差。这是由于血压计玻璃管上端的气孔堵塞或玻璃管内壁太脏所致。有时玻璃管装反也会产生这种情况。排除方法:更换气孔上的网垫或清洗玻璃管内壁,故障即可消除。在拆装玻璃管时应将有字的一端装在下面。2 汞柱不连续(有气泡)原因分析:血压计在造压过程中,汞柱不连续(有气泡产生),其原因有两种:一是因使用不当(不使用时忘记关闭汞瓶开关或打压过大)水银溢出。二是玻璃管内壁或水银太脏。排除方法:如在无压情况下汞柱低于零位,则说明缺少水银,用医用注射器从玻璃管上端气孔加入适量水银,使汞柱复位到零即可。如果汞柱不低于零位,则需要清洗玻璃管或水银。在清洗玻璃管时应先关闭汞瓶开关,再拆卸玻璃管,以防水银溢出。清洗水银时不必完全拆下玻璃管,让上压板压住玻璃管的边沿,使管口露出,然后打开汞瓶开关,把水银倒入一容器中,用酒精棉球擦拭水银上的脏物,然后用橡皮球打气,用气吹净汞瓶中的灰尘即可。3 漏水银原因分析:出现这种故障要细心观察,看水银是从何处漏出。如果水银是从玻璃管和汞瓶的接口处漏出,说明橡胶垫有问题,由于长期使用,使玻璃管与汞瓶之间的胶垫老化损坏;如从汞瓶底部漏出,说明在安装时螺钉拧得太紧使汞瓶裂缝。排除方法:如橡胶垫有问题,需进行更换。如汞瓶有裂缝,用“502”胶粘合或更换新汞瓶。4 汞柱无法稳定原因分析:出现这种情况说明胶管、气袋和铅阀有漏气现象。要分步进行检查,打压到高位,先将气袋以前的胶管夹住,看是否漏气,如漏气,说明胶管或胶管与汞瓶接口处漏气。如不漏气,再夹住气袋以后的胶管,这时漏气,说明是气袋漏气。还如果不漏,就是铜阀有漏气现象,最常见的是铜阀内的小胶管切口处有脏物,铜阀关闭不严也会出现这一现象。排除方法:如是胶管或气袋漏气,用“鱼皮胶”粘补或更换新气袋。如是铜阀有漏气现象,对铜阀内的小胶管切口处有脏物进行清理,故障即可消除。如果橡皮球和后气阀出现问题会影响造压,和漏气无关。以上是本人在实际工作中常碰到的一些故障,经过以上方法一般可以解决。在汞柱式血压计的检修过程中,只要注意细心观察,勤于思考,一般故障均能得以顺利解决。
作者简介:董万科,男,工程师。工作单位:宝鸡市计量测试所。通讯地址:721000陕西省宝鸡市胜利桥北。收稿时间:2008-04-22
[4]徐红,张红,茅洪洋.转炉炉渣自动检测技术及其应用.冶金设备,1999(2).[5]孙巧玲,袁伟霞.采用振动测量法检测钢包至中间包的下渣.钢铁研究,1994(3).作者简介:黄绍伟,男,助理工程师。工作单位:济南钢铁集团总公司第三炼钢厂。通讯地址:250101济南市济钢第三炼钢厂电气车间。收稿时间:2008-04-24